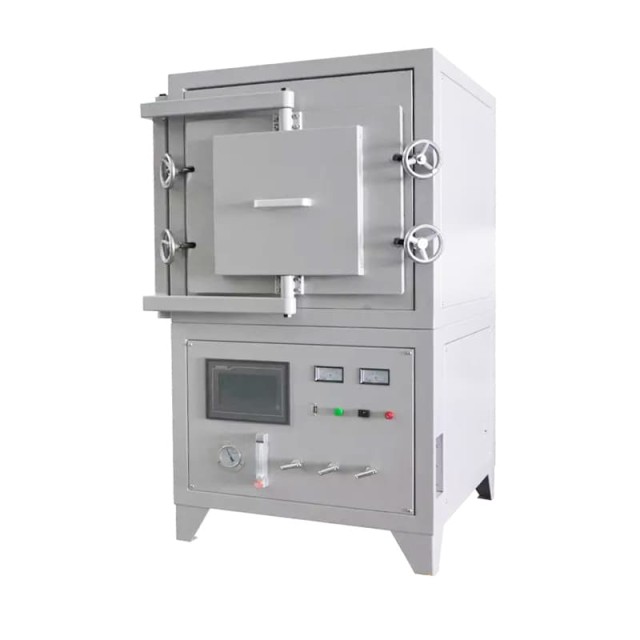
Atmosphere Furnace
1200℃ Controlled Atmosphere Furnace Nitrogen Inert Atmosphere Furnace
Item Number : KT-12A
Price varies based on specs and customizations
- Max. temperature
- 1200 ℃
- Constant work temperature
- 1100 ℃
- Vacuum pressure
- 0.1 Mpa
- Heating rate
- 0-30 ℃/min
- Effective volume
- 1-512 L
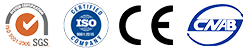
Shipping:
Contact us to get shipping details Enjoy On-time Dispatch Guarantee.
Why Choose Us
Reliable PartnerEasy ordering process, quality products, and dedicated support for your business success.
Introduction
A controlled atmosphere furnace is a type of furnace that allows for the introduction of one or more gases into the heating chamber, which react with the heated material, protecting it from the action of oxygen and water vapor contained in the air. These furnaces are used for a variety of applications, including heat treating, brazing, soldering, and annealing.
Controlled atmosphere furnaces are typically used when the material being heated is sensitive to oxidation or other reactions with the air. By introducing an inert or active gas into the heating chamber, the furnace can create an atmosphere that prevents these reactions from occurring. This can help to improve the quality of the finished product and reduce the risk of defects.
Controlled atmosphere furnaces are available in a variety of sizes and configurations, and can be used for a wide range of applications. They are typically more expensive than conventional furnaces, but the benefits they offer can often justify the additional cost.
Controlled atmosphere furnaces are widely used in various fields, including:
Application
The 1200℃ Controlled Atmosphere Furnace is a versatile and efficient tool designed for various high-temperature processes requiring precise atmosphere control. This furnace, equipped with advanced features such as temperature controller and a polycrystalline alumina fibre chamber, is ideal for applications in industrial settings, scientific research institutes, and universities. Its ability to pre-vacuum and handle gases like H2, Ar, N2, O2, CO, and NH3 makes it suitable for a range of specialized processes.
- Atmosphere Protection Sintering: Ideal for sintering materials under controlled atmospheres to prevent oxidation and enhance material properties.
- Atmosphere Reducing Processes: Used in processes that require a reduction in the presence of oxygen, such as in the production of certain alloys or ceramics.
- Material Research and Development: Essential for researchers studying the effects of controlled atmospheres on material properties and behaviors.
- Small Batch Production: Particularly useful in the production of semiconductors, silicon nitride, and other sensitive materials where atmosphere control is critical.
- Educational Purposes: Provides hands-on experience for students in materials science and engineering, demonstrating the practical aspects of controlled atmosphere furnaces.
Principle
A controlled atmosphere furnace is a type of furnace that allows for the introduction of one or more gases into the heating chamber. This creates a controlled atmosphere that can protect the heated material from the action of oxygen and water vapor in the air. The gases used in controlled atmosphere furnaces can be inert, such as nitrogen and argon, or active, such as hydrogen, endothermic gas, exothermic gas, or a mixture of these gases. The specific gas or gas mixture used depends on the desired outcome of the heating process.
Detail & Parts
Features
The 1200°C Controlled Atmosphere Muffle Furnace is a sophisticated piece of equipment designed for advanced heat treatment processes in industrial and research settings. This furnace offers a range of features that not only enhance its functionality but also ensure efficient and safe operation. Key benefits include precise temperature control, rapid heating and cooling capabilities, and the ability to handle various atmospheres, making it ideal for sintering and reducing processes under controlled conditions.
- Double Layer Housing and Wind Cooling System: The furnace features a double-layer housing with a wind cooling system, facilitating rapid heating and cooling. This design not only improves efficiency but also maintains low surface temperatures, ensuring safety during operation.
- -Sealed Housing and Atmosphere Control: With a sealed housing, silicon gel sealed cover, and a door equipped with a silicon gel gasket, the furnace maintains a tight seal, crucial for controlled atmosphere processes. The inclusion of a water cooling system and gas flow management through flow meters ensures precise control over the atmosphere inside the chamber.
- Versatile Atmosphere Handling: The furnace is capable of pre-vacuuming and handling a variety of gases including H2, Ar, N2, O2, CO, and NH3. Multiple gas inlets and outlets, along with a burning mouth, allow for complex atmosphere manipulations, essential for advanced materials processing.
- Advanced Insulation and Heating Elements: Utilizing Kantal resistance wire heating elements and polycrystalline alumina fibre chamber, the furnace ensures optimal temperature uniformity and energy efficiency. This setup supports high-temperature applications up to 1200°C, making it suitable for a wide range of industrial and research applications.
Advantages
- Heavy-duty vacuum chamber structure design with excellent sealing performance: Ensures a controlled atmosphere environment with minimal gas leakage.
- Scientifically designed control panel for vacuum suction and inert gas pressure and flow: Allows precise regulation of the atmosphere within the furnace chamber.
- Double furnace shell design with forced air flow cooling: Effectively controls the surface temperature of the furnace, ensuring operator safety and reducing energy consumption.
- PID programmable temperature control with high accuracy: Provides precise temperature control and uniformity, optimizing the heat treatment process.
- Ceramic polycrystalline fiber insulation liner: Minimizes heat loss and improves energy efficiency.
- Professional heating element configuration: Optimizes heat radiation properties and ensures extended service life.
- Safety interlock system: Automatically shuts off power in case of furnace door opening, over-temperature, or sensor failure, ensuring operator safety.
- 7-inch TFT smart touch screen controller (KT-12A Pro): User-friendly interface for easy program setting and historical data analysis.
Safety Advantage
- Kindle Tech controlled atmosphere furnace owns over current protection, over temperature alarming function, furnace will turn off the power automatically
- Furnace build in thermal couple detecting function, furnace will stop heating and alarm will be on once broken or failure detected
- KT-12M Pro support power failure restarting function,furnace will resume the furnace heating program when power is incoming after failure
Technical specifications
Furnace model | KT-12A | ||
---|---|---|---|
Max. temperature | 1200℃ | ||
Constant work temperature | 1100℃ | ||
Vacuum pressure | 0.1Mpa | ||
Vacuum valve | Needle valve | ||
Furnace tube material | High purity quartz | ||
Chamber material | Japan alumina fiber | ||
Heating element | Cr2Al2Mo2 wire coil | ||
Heating rate | 0-30℃/min | ||
Temperature sensor | Build in K type thermal couple | ||
Temperature controller | Digital PID controller/Touch screen PID controller | ||
Temperature control accuracy | ±1℃ | ||
Temperature uniformity | ±5℃ | ||
Electric power supply | AC110-220V,50/60HZ | ||
Standard Chamber Sizes Stocks | |||
Chamber size (mm) | Effective volume (L) | Chamber size (mm) | Effective volume (L) |
100x100x100 | 1 | 300x300x400 | 36 |
150x150x150 | 3.4 | 400x400x400 | 64 |
150x150x200 | 4.5 | 500x500x500 | 125 |
200x200x200 | 8 | 600x600x600 | 216 |
200x200x300 | 12 | 800x800x800 | 512 |
Customer design sizes and volume is accepted |
Standard Package
No. | Description | Quantity |
---|---|---|
1 | Furnace | 1 |
2 | Thermal block | 1 |
3 | Crucible tong | 1 |
4 | Heat resistant glove | 1 |
5 | Operation manual | 1 |
Optional Setup
- Independent furnace temperature monitoring and recording
- RS 485 communication port for PC remote control and data exporting
- Insert gases port,exhaust output port,observation window port
- Touch screen temperature controller with versatile operator friendly functions
Warnings
Operator safety is the top important issue! Please operate the equipment with cautions. Working with inflammable& explosive or toxic gases is very dangerous, operators must take all necessary precautions before starting the equipment. Working with positive pressure inside the reactors or chambers is dangerous, operator must fellow the safety procedures strictly. Extra caution must also be taken when operating with air-reactive materials, especially under vacuum. A leak can draw air into the apparatus and cause a violent reaction to occur.
Designed for You
KinTek provide deep custom made service and equipment to worldwide customers, our specialized teamwork and rich experienced engineers are capable to undertake the custom tailoring hardware and software equipment requirements, and help our customer to build up the exclusive and personalized equipment and solution!
Would you please drop your ideas to us, our engineers are ready for you now!
4.9
out of
5
The furnace's temperature uniformity is remarkable, leading to consistent results.
4.8
out of
5
The customer service was exceptional, answering all my queries promptly and efficiently.
4.7
out of
5
The construction is solid, indicating its durability and longevity.
4.9
out of
5
The programmable segments allow for precise temperature control, enhancing experimental accuracy.
4.6
out of
5
The delivery was remarkably fast, arriving within days of placing the order.
4.8
out of
5
The value for money is outstanding, considering the furnace's capabilities and performance.
4.7
out of
5
The temperature control accuracy is impressive, ensuring consistent and reliable results.
4.9
out of
5
The vacuum sealing technology ensures an excellent controlled atmosphere environment, enhancing experimental outcomes.
4.8
out of
5
The PID intelligent temperature microprocessor offers exceptional control accuracy, simplifying experimental procedures.
4.7
out of
5
The safety features, such as over-temperature alarming and power failure restarting, provide peace of mind during operation.
4.9
out of
5
The versatility of the furnace allows for various applications, making it a valuable asset in our laboratory.
4.8
out of
5
The compact design saves valuable lab space, while still delivering exceptional performance.
4.7
out of
5
The easy-to-use interface and intuitive controls make operating the furnace a breeze.
4.9
out of
5
The furnace's ability to handle various gases, such as H2, Ar, N2, and O2, expands its experimental capabilities.
4.8
out of
5
The remote control and centralized control options enhance the convenience and flexibility of operation.
4.7
out of
5
The furnace's energy efficiency contributes to cost savings and sustainability in our laboratory.
Products
1200℃ Controlled Atmosphere Furnace Nitrogen Inert Atmosphere Furnace
REQUEST A QUOTE
Our professional team will reply to you within one business day. Please feel free to contact us!
Related Products
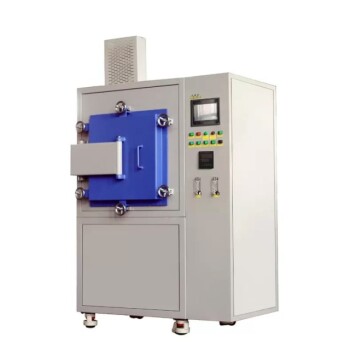
Controlled Nitrogen Inert Hydrogen Atmosphere Furnace
KT-AH Hydrogen atmosphere furnace - induction gas furnace for sintering/annealing with built-in safety features, dual housing design, and energy-saving efficiency. Ideal for lab and industrial use.
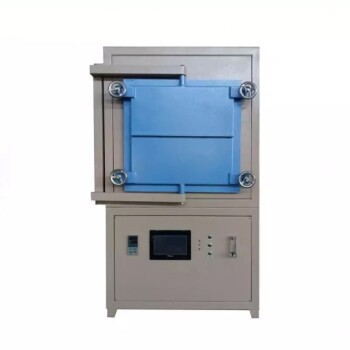
1400℃ Controlled Atmosphere Furnace with Nitrogen and Inert Atmosphere
Achieve precise heat treatment with KT-14A controlled atmosphere furnace. Vacuum sealed with a smart controller, it's ideal for lab and industrial use up to 1400℃.
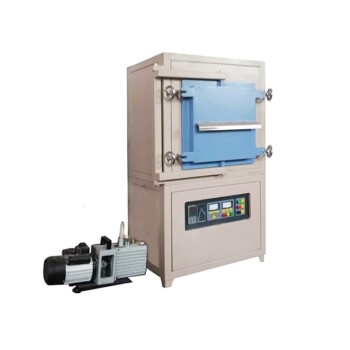
1700℃ Controlled Atmosphere Furnace Nitrogen Inert Atmosphere Furnace
KT-17A Controlled atmosphere furnace: 1700℃ heating, vacuum sealing technology, PID temperature control, and versatile TFT smart touch screen controller for laboratory and industrial use.
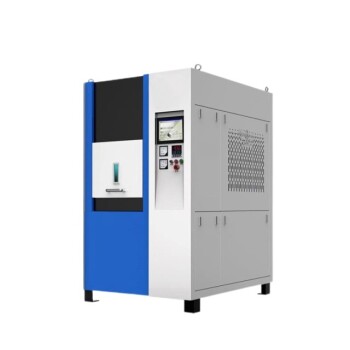
Spark Plasma Sintering Furnace SPS Furnace
Discover the benefits of Spark Plasma Sintering Furnaces for rapid, low-temperature material preparation. Uniform heating, low cost & eco-friendly.
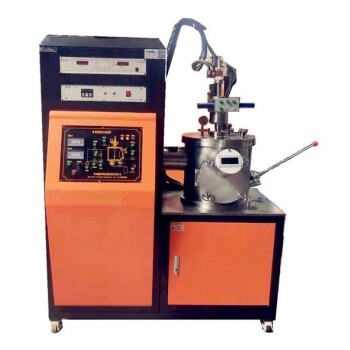
Non Consumable Vacuum Arc Induction Melting Furnace
Explore the benefits of Non-Consumable Vacuum Arc Furnace with high melting point electrodes. Small, easy to operate & eco-friendly. Ideal for laboratory research on refractory metals & carbides.
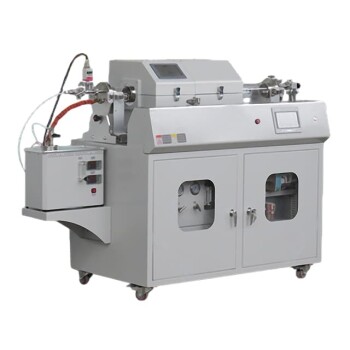
KT-PE12 Slide PECVD System: Wide power range, programmable temp control, fast heating/cooling with sliding system, MFC mass flow control & vacuum pump.
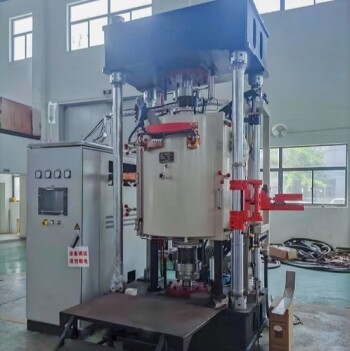
Vacuum Heat Treat and Pressure Sintering Furnace for High Temperature Applications
Vacuum pressure sintering furnaces are designed for high temperature hot pressing applications in metal and ceramic sintering. Its advanced features ensure precise temperature control, reliable pressure maintenance, and a robust design for seamless operation.
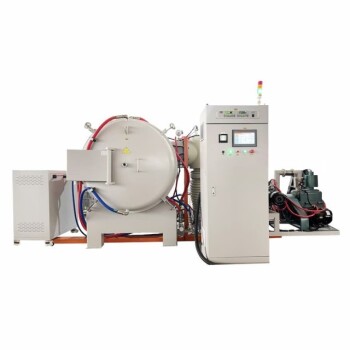
Molybdenum Vacuum Heat Treat Furnace
Discover the benefits of a high-configuration molybdenum vacuum furnace with heat shield insulation. Ideal for high-purity, vacuum environments like sapphire crystal growth and heat treatment.
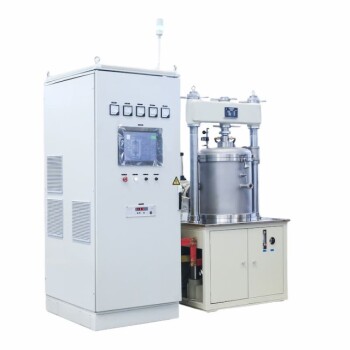
Vacuum Hot Press Furnace Machine Heated Vacuum Press
Discover the advantages of Vacuum Hot Press Furnace! Manufacture dense refractory metals & compounds, ceramics, and composites under high temp and pressure.
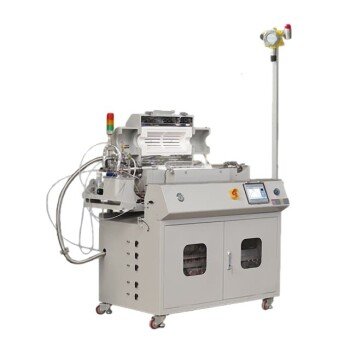
Customer Made Versatile CVD Tube Furnace Chemical Vapor Deposition Chamber System Equipment
Get your exclusive CVD furnace with KT-CTF16 Customer Made Versatile Furnace. Customizable sliding, rotating, and tilting functions for precise reactions. Order now!
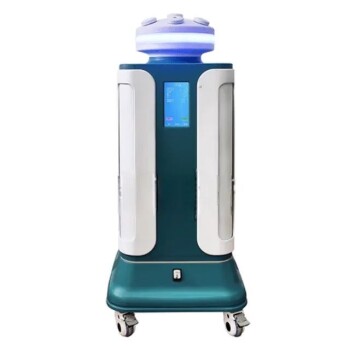
VHP Sterilization Equipment Hydrogen Peroxide H2O2 Space Sterilizer
A hydrogen peroxide space sterilizer is a device that uses vaporized hydrogen peroxide to decontaminate enclosed spaces. It kills microorganisms by damaging their cellular components and genetic material.
Related Articles
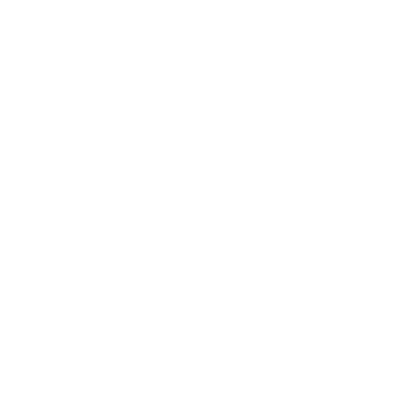
Controlled Atmosphere Furnace: Comprehensive Guide to Advanced Heat Treatment
Explore the advanced features and applications of controlled atmosphere furnaces in heat treatment processes. Learn about key components, operational techniques, and benefits for precise material processing.
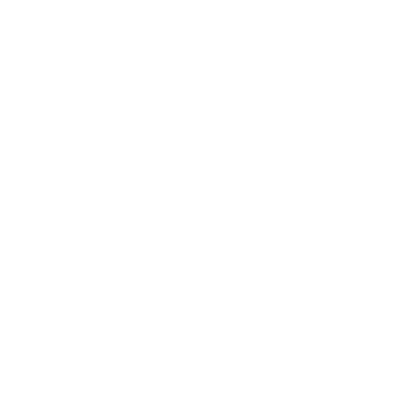
The Benefits of Controlled Atmosphere Furnaces for Sintering and Annealing Processes
They are essential in preventing oxidation, reducing the risk of contamination, and improving the properties of the materials being treated.
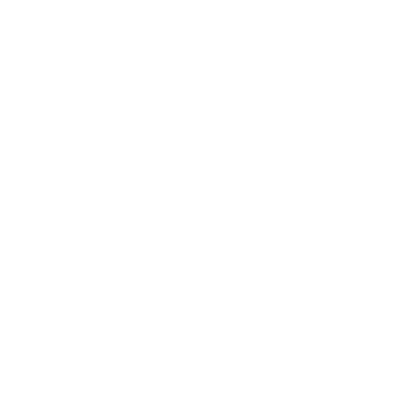
Hydrogen Atmosphere Furnaces: Applications, Safety, and Maintenance
Explore the comprehensive guide on hydrogen atmosphere furnaces, including their applications in high-end alloy sintering, safety measures, and maintenance tips. Learn about the types, components, and operational considerations for optimal performance.
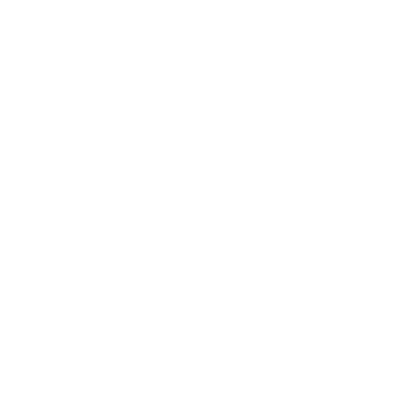
How Controlled Atmosphere Furnaces Improve Quality and Consistency in Heat Treatment
Controlled atmosphere furnaces play a vital role in heat treatment processes.
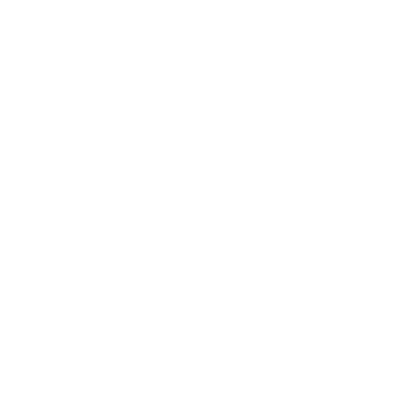
Atmosphere Furnaces: Comprehensive Guide to Controlled Heat Treatment
Explore the advanced world of atmosphere furnaces with our detailed guide. Learn about their operation, applications, and benefits in various industries. Perfect for those seeking in-depth knowledge on controlled heat treatment.
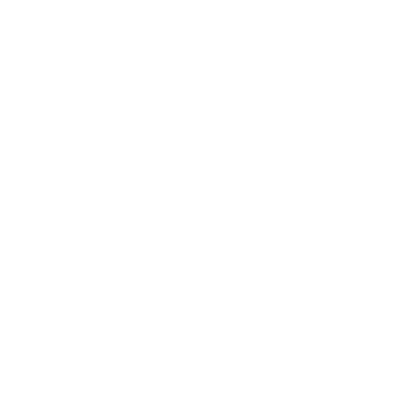
Muffle Furnace: Unraveling the Secrets of Uniform Heating and Controlled Atmosphere
Discover the intricacies of a muffle furnace, an indispensable tool for material processing and analysis. Learn about its working principle, applications, types, features, and benefits, empowering you to make informed decisions for your laboratory or industrial needs.
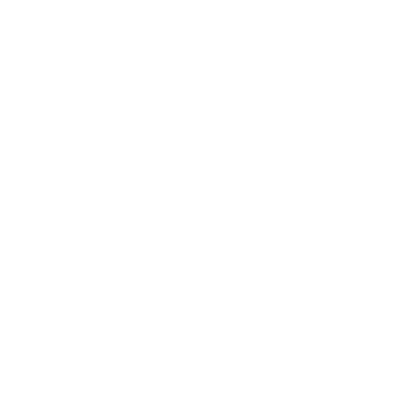
Comprehensive Guide to Atmosphere Furnaces: Types, Applications, and Benefits
Explore the world of atmosphere furnaces with our detailed guide. Learn about their types, applications in metallurgy and beyond, and the benefits they offer for precise material heat treatment.
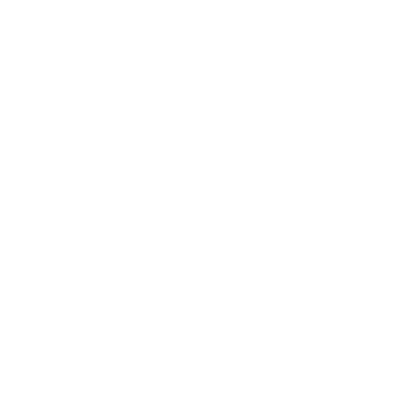
Exploring the Using a Chamber Furnace for Industrial and Laboratory Applications
A laboratory chamber furnace is a type of heating equipment that is specifically designed for use in a laboratory setting. It is typically used for applications that require precise temperature control and uniformity, such as ashing or heat treatment of materials.
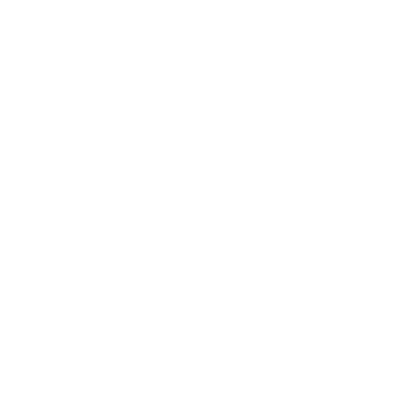
Inert Atmosphere Ovens for Research A Comprehensive Guide
Inert atmosphere ovens are designed to create a controlled environment that is free of oxygen and moisture.
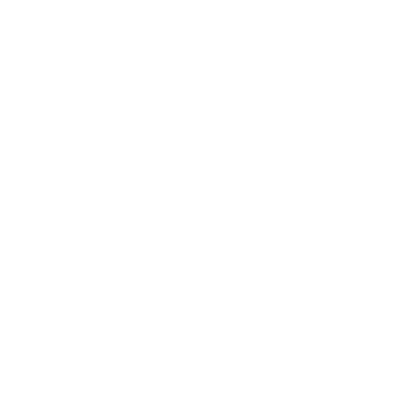
Materials Science with the Lab Vacuum Furnace
A vacuum furnace is a specialized type of furnace that is designed to operate in a vacuum environment. This means that the furnace is sealed and the air inside is pumped out, creating a low pressure or vacuum inside.
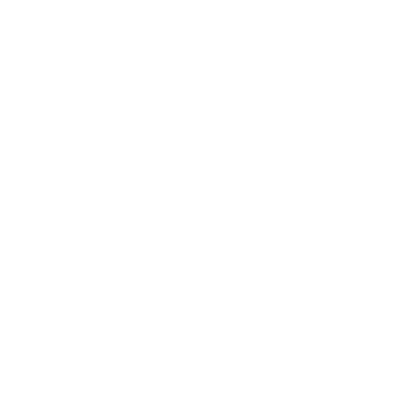
How to Choose Right Muffle Furnace for Your Laboratory?
A few other important considerations for your muffle furnace include the desired maximum temperature, process cycle time, and loading or unloading method. In order to choose the best muffle furnace for your needs, it is important to first consider the design specifications required for your desired production or application. This includes factors such as the crucible size, chamber size, and input voltage. Once you have a good understanding of the basics, you can then move on to other important considerations such as the maximum temperature, process cycle time, and loading or unloading method. By taking all of these factors into account, you can be sure to choose the best muffle furnace for your particular needs.
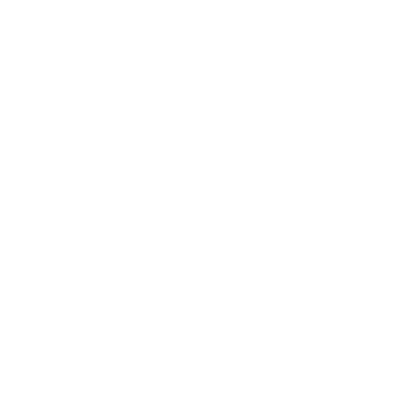
The Importance of Inert Atmosphere Gases in Furnace Atmospheres
Furnace atmospheres play an essential role in the heat treatment process of materials.