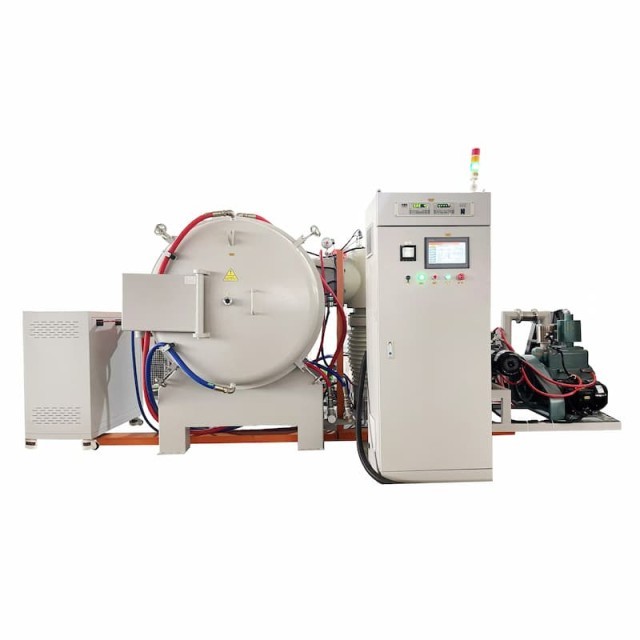
Vacuum Furnace
Molybdenum Vacuum Heat Treat Furnace
Item Number : KT-VM
Price varies based on specs and customizations
- Max. temperature
- 1400 ℃
- Constant work temperature
- 1300 ℃
- Heating rate
- 0-10 ℃/min
- Effective volume
- 4.5-253 L
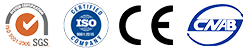
Shipping:
Contact us to get shipping details Enjoy On-time Dispatch Guarantee.
Why Choose Us
Reliable PartnerEasy ordering process, quality products, and dedicated support for your business success.
Introduction
A molybdenum vacuum furnace is a type of high-temperature heat treatment equipment used in various industrial applications. It utilizes molybdenum foil as a heating element and provides a vacuum environment to prevent contamination of the heated materials. This furnace exhibits high-temperature stability, excellent vacuum performance, efficient heat transfer, and high durability. It is commonly employed in fields such as vacuum sintering and vacuum brazing, where high-purity and vacuum requirements are crucial.
Applications
The molybdenum vacuum furnace finds applications in various fields, including:
- Vacuum sintering
- Vacuum brazing
- Sapphire crystal growth
- Special brazing
- Heat treatment
- Casting aircraft components
- Refining high purity metals and alloys
- Electrodes for remelting
- Powder roasting
- Ceramic sintering
- High-temperature experiments
- Material treatment
- High-temperature atmosphere sintering
- Ceramic glue discharge
- Flue gas treatment
- Annealing and sintering
Detail & Parts

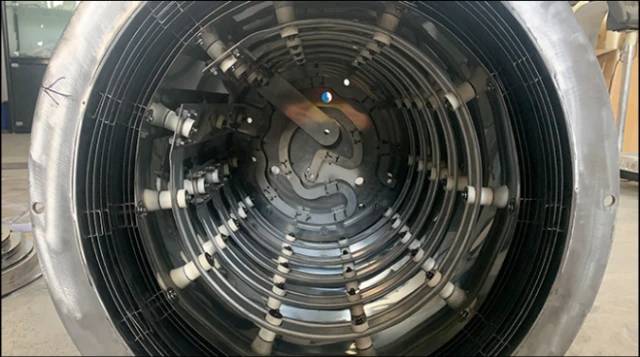
Small thermal expansion;High melting point;High thermal conductivity.
Features
The molybdenum foil vacuum furnace provides various benefits that cater to specific customer needs:
- High-temperature stability: Guarantees consistent heating temperatures for reliable heat treatment processes, even under demanding conditions.
- Excellent vacuum performance: Maintains a high vacuum level and prevents contamination, ensuring the integrity of heated materials.
- Efficient heat transfer: Facilitates faster heating rates and improved thermal uniformity, enhancing process efficiency.
- High durability: Resists high temperatures and oxidation, ensuring prolonged usage without performance degradation.
Principle
The molybdenum vacuum furnace utilizes the high-temperature resistance and excellent vacuum performance of molybdenum foil as the heating element and furnace liner. It operates by creating a high-temperature vacuum environment through resistive heating of the molybdenum foil, which effectively isolates the heated materials from external contaminants and enables precise temperature control. This unique design allows for high-temperature heat treatment processes in a clean and controlled atmosphere, making it ideal for applications such as vacuum sintering and vacuum brazing.
Advantages
- High-temperature stability: The molybdenum foil vacuum furnace exhibits remarkable temperature stability, maintaining a consistent heating temperature and ensuring a reliable heat treatment process under high-temperature conditions.
- Excellent vacuum performance: The molybdenum foil material possesses exceptional sealability and corrosion resistance, enabling the furnace to maintain a high vacuum level and prevent contamination of the heated materials.
- Efficient heat transfer: Utilizing molybdenum foil material, the vacuum furnace facilitates efficient heat transfer, resulting in faster heating rates and improved thermal uniformity.
- High durability: The molybdenum foil material exhibits excellent resistance to high temperatures and oxidation, allowing for prolonged usage at elevated temperatures without failure.
Safety Advantage
- Kindle Tech vacuum furnace owns over current protection, over temperature alarming function, furnace will turn off the power automatically
- Furnace build in thermal couple detecting function, furnace will stop heating and alarm will be on once broken or failure detected
- Power failure restarting function,furnace will resume the furnace heating program when power is incoming after failure
Technical specifications
Furnace model | KT-VM | ||
Max. temperature | 1400 ℃ | ||
Constant work temperature | 1300 ℃ | ||
Chamber insulation material | molybdenum heat shied | ||
Heating element | Molybdenum Strip | ||
Heating rate | 0-10℃/min | ||
Temperature sensor | Build in S type thermal couple | ||
Temperature controller | Touch screen PID controller with PLC | ||
Temperature control accuracy | ±1℃ | ||
Temperature uniformity | ±5℃ | ||
Electric power supply | AC110-440V,50/60HZ | ||
Standard Chamber Sizes Stocks | |||
Chamber size (mm) | Effective volume (L) | Chamber size (mm) | Effective volume (L) |
150x150x200 | 4.5 | 400x400x500 | 80 |
200x200x300 | 12 | 500x500x600 | 125 |
300x300x400 | 36 | 600x600x700 | 253 |
Customer design sizes and volume is accepted |
Optional Setup
- Independent furnace temperature monitoring and recording
- RS 485 communication port for PC remote control and data exporting
- Optional pneumatic vacuum valve linkage with temperature controller
- Touch screen temperature controller with versatile operator friendly functions
- Cold water circulation cooling machine for furnace shell jacket cooling system
Precautions and maintenance
The molybdenum foil vacuum furnace consists of key components such as the furnace chamber, molybdenum strips, vacuum gauge, vacuum system, and water cooler. The following precautions and maintenance guidelines should be observed:
Furnace Chamber |
|
|
---|---|---|
Molybdenum Strips Heater |
|
|
Pirani Gauge and Ionisation Gauge |
|
|
Mechanical Pump |
|
|
Roots Pump |
|
|
Diffusion Pump |
|
|
Water Cooler |
|
In summary, the molybdenum foil vacuum furnace is an efficient, stable, durable, and safe device. However, it requires regular vacuum maintenance, safe operation, and diligent maintenance practices to ensure its long-term stable operation.
Warnings
Operator safety is the top important issue! Please operate the equipment with cautions. Working with inflammable& explosive or toxic gases is very dangerous, operators must take all necessary precautions before starting the equipment. Working with positive pressure inside the reactors or chambers is dangerous, operator must fellow the safety procedures strictly. Extra caution must also be taken when operating with air-reactive materials, especially under vacuum. A leak can draw air into the apparatus and cause a violent reaction to occur.
Designed for You
KinTek provide deep custom made service and equipment to worldwide customers, our specialized teamwork and rich experienced engineers are capable to undertake the custom tailoring hardware and software equipment requirements, and help our customer to build up the exclusive and personalized equipment and solution!
Would you please drop your ideas to us, our engineers are ready for you now!
4.9
out of
5
The molybdenum vacuum furnace from KINTEK SOLUTION is a game-changer for our laboratory. It's efficient, precise, and incredibly durable.
4.7
out of
5
We've been using the molybdenum vacuum furnace for over a year now, and it's been a fantastic investment. It's reliable, easy to use, and produces high-quality results.
4.8
out of
5
The molybdenum vacuum furnace from KINTEK SOLUTION is a top-notch piece of equipment. It's well-built, easy to operate, and delivers exceptional performance.
4.9
out of
5
We recently upgraded to the molybdenum vacuum furnace from KINTEK SOLUTION, and we're thrilled with the results. It's faster, more efficient, and produces better-quality products.
4.7
out of
5
The KINTEK SOLUTION molybdenum vacuum furnace is a great choice for labs that demand precision and reliability. It's a well-made, high-quality product that delivers consistent results.
4.8
out of
5
We've been using the molybdenum vacuum furnace for several months now, and it's exceeded our expectations. It's easy to use, maintains temperature accurately, and produces high-quality results.
4.9
out of
5
The molybdenum vacuum furnace from KINTEK SOLUTION is a fantastic addition to our lab. It's user-friendly, efficient, and produces excellent results. We highly recommend it.
4.7
out of
5
We're very impressed with the molybdenum vacuum furnace from KINTEK SOLUTION. It's a well-built, reliable piece of equipment that delivers exceptional performance.
4.8
out of
5
The molybdenum vacuum furnace from KINTEK SOLUTION is a great investment for any lab. It's efficient, accurate, and produces high-quality results. We're very happy with our purchase.
REQUEST A QUOTE
Our professional team will reply to you within one business day. Please feel free to contact us!
Related Products
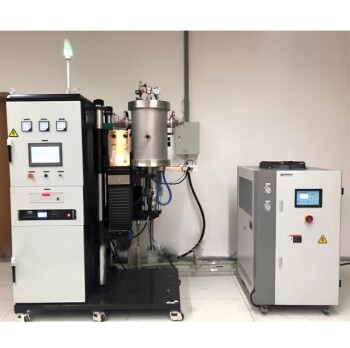
Vacuum Heat Treat and Molybdenum Wire Sintering Furnace for Vacuum Sintering
A vacuum molybdenum wire sintering furnace is a vertical or bedroom structure, which is suitable for withdrawal, brazing, sintering and degassing of metal materials under high vacuum and high temperature conditions. It is also suitable for dehydroxylation treatment of quartz materials.
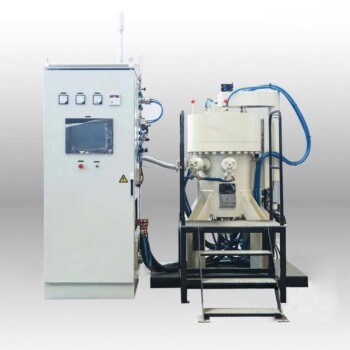
Vacuum Heat Treat and Sintering Furnace with 9MPa Air Pressure
The air pressure sintering furnace is a high-tech equipment commonly used for the sintering of advanced ceramic materials. It combines vacuum sintering and pressure sintering techniques to achieve high-density and high-strength ceramics.
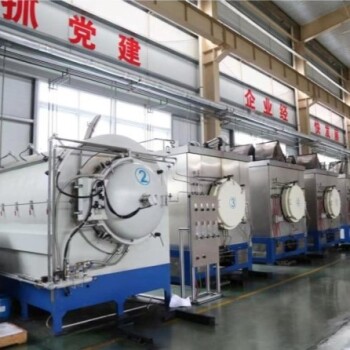
Vacuum Heat Treat Sintering Brazing Furnace
A vacuum brazing furnace is a type of industrial furnace used for brazing, a metalworking process that joins two pieces of metal using a filler metal that melts at a lower temperature than the base metals. Vacuum brazing furnaces are typically used for high-quality applications where a strong, clean joint is required.
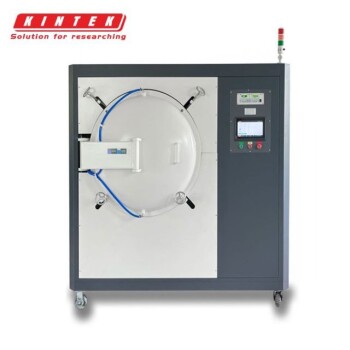
Vacuum Heat Treat Furnace with Ceramic Fiber Liner
Vacuum furnace with polycrystalline ceramic fiber insulation liner for excellent heat insulation and uniform temperature field. Choose from 1200℃ or 1700℃ max. working temperature with high vacuum performance and precise temperature control.
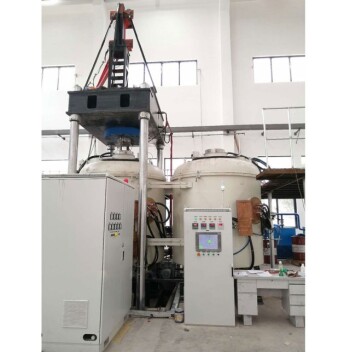
600T Vacuum Induction Hot Press Furnace for Heat Treat and Sintering
Discover the 600T Vacuum Induction Hot Press Furnace, designed for high-temperature sintering experiments in vacuum or protected atmospheres. Its precise temperature and pressure control, adjustable working pressure, and advanced safety features make it ideal for nonmetal materials, carbon composites, ceramics, and metal powders.
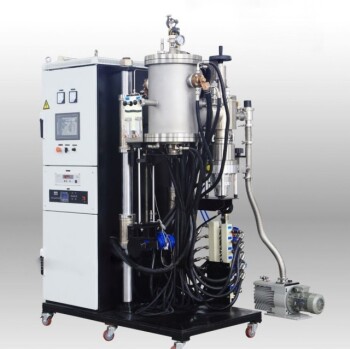
Small Vacuum Heat Treat and Tungsten Wire Sintering Furnace
The small vacuum tungsten wire sintering furnace is a compact experimental vacuum furnace specially designed for universities and scientific research institutes. The furnace features a CNC welded shell and vacuum piping to ensure leak-free operation. Quick-connect electrical connections facilitate relocation and debugging, and the standard electrical control cabinet is safe and convenient to operate.
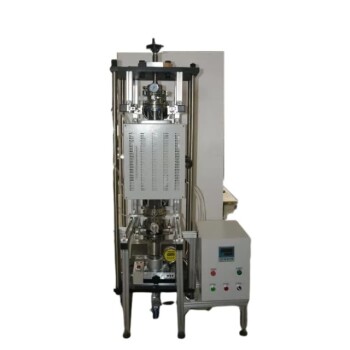
Vacuum Hot Press Furnace Heated Vacuum Press Machine Tube Furnace
Reduce forming pressure & shorten sintering time with Vacuum Tube Hot Press Furnace for high-density, fine-grain materials. Ideal for refractory metals.
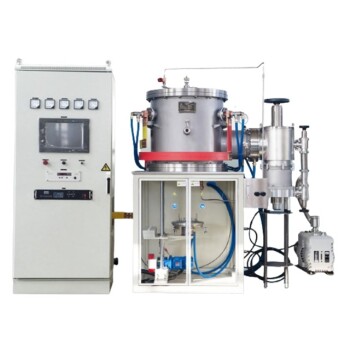
2200 ℃ Tungsten Vacuum Heat Treat and Sintering Furnace
Experience the ultimate refractory metal furnace with our Tungsten vacuum furnace. Capable of reaching 2200℃, perfect for sintering advanced ceramics and refractory metals. Order now for high-quality results.
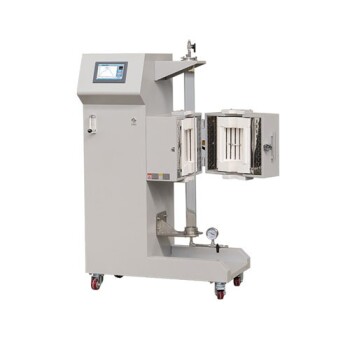
Vertical Laboratory Quartz Tube Furnace Tubular Furnace
Elevate your experiments with our Vertical Tube Furnace. Versatile design allows for operation under various environments and heat treatment applications. Order now for precise results!
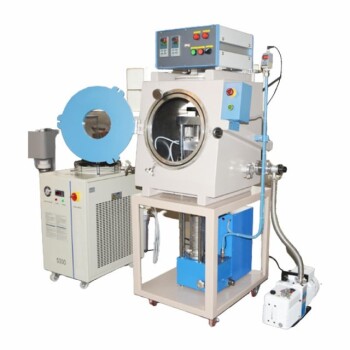
Vacuum Hot Press Furnace Machine for Lamination and Heating
Experience clean and precise lamination with Vacuum Lamination Press. Perfect for wafer bonding, thin-film transformations, and LCP lamination. Order now!
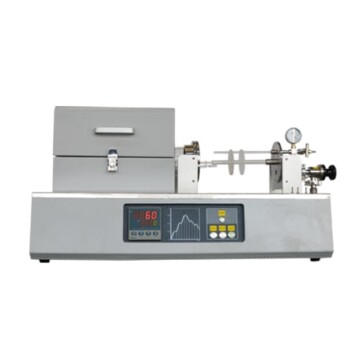
Laboratory Quartz Tube Furnace Tubular RTP Heating Furnace
Get lightning-fast heating with our RTP Rapid Heating Tube Furnace. Designed for precise, high-speed heating and cooling with convenient sliding rail and TFT touch screen controller. Order now for ideal thermal processing!
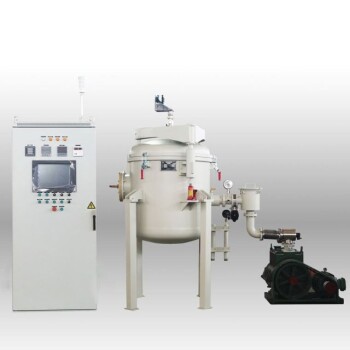
Ultra-High Temperature Graphite Vacuum Graphitization Furnace
The ultra-high temperature graphitization furnace utilizes medium frequency induction heating in a vacuum or inert gas environment. The induction coil generates an alternating magnetic field, inducing eddy currents in the graphite crucible, which heats up and radiates heat to the workpiece, bringing it to the desired temperature. This furnace is primarily used for graphitization and sintering of carbon materials, carbon fiber materials, and other composite materials.
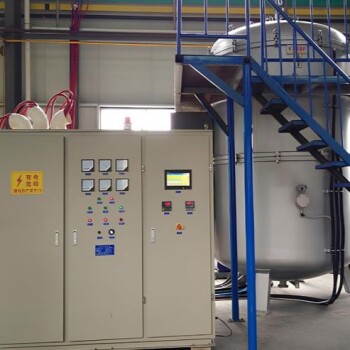
Large Vertical Graphite Vacuum Graphitization Furnace
A large vertical high-temperature graphitization furnace is a type of industrial furnace used for the graphitization of carbon materials, such as carbon fiber and carbon black. It is a high-temperature furnace that can reach temperatures of up to 3100°C.

Graphite Vacuum Furnace Bottom Discharge Graphitization Furnace for Carbon Materials
Bottom-out graphitization furnace for carbon materials, ultra-high temperature furnace up to 3100°C, suitable for graphitization and sintering of carbon rods and carbon blocks. Vertical design, bottom discharging, convenient feeding and discharging, high temperature uniformity, low energy consumption, good stability, hydraulic lifting system, convenient loading and unloading.
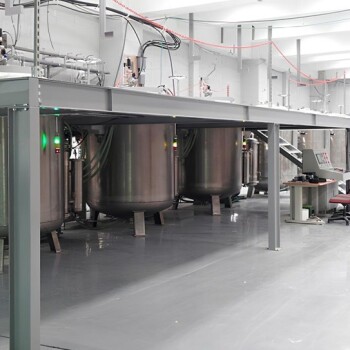
Graphite Vacuum Furnace Negative Material Graphitization Furnace
Graphitization furnace for battery production has uniform temperature and low energy consumption. Graphitization furnace for negative electrode materials: an efficient graphitization solution for battery production and advanced functions to enhance battery performance.
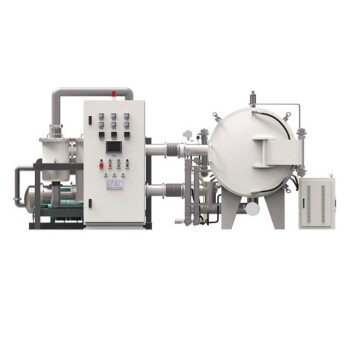
Horizontal High Temperature Graphite Vacuum Graphitization Furnace
Horizontal Graphitization Furnace: This type of furnace is designed with the heating elements placed horizontally, allowing for uniform heating of the sample. It's well-suited for graphitizing large or bulky samples that require precise temperature control and uniformity.
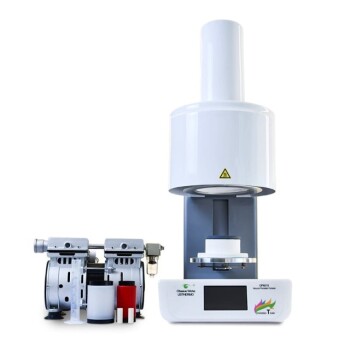
Dental Porcelain Zirconia Sintering Ceramic Vacuum Press Furnace
Get precise dental results with Dental Vacuum Press Furnace. Automatic temperature calibration, low noise tray, and touch screen operation. Order now!
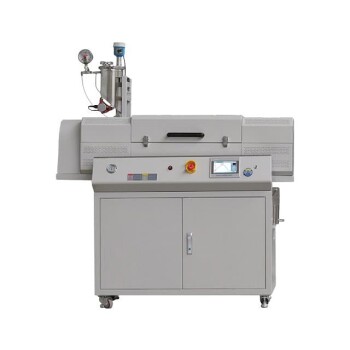
Laboratory Vacuum Tilt Rotary Tube Furnace Rotating Tube Furnace
Discover the versatility of Laboratory Rotary Furnace: Ideal for calcination, drying, sintering, and high-temperature reactions. Adjustable rotating and tilting functions for optimal heating. Suitable for vacuum and controlled atmosphere environments. Learn more now!
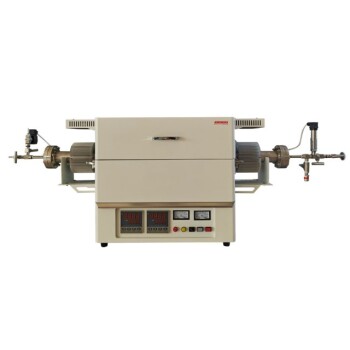
High Pressure Laboratory Vacuum Tube Furnace Quartz Tubular Furnace
KT-PTF High Pressure Tube Furnace: Compact split tube furnace with strong positive pressure resistance. Working temp up to 1100°C and pressure up to 15Mpa. Also works under controller atmosphere or high vacuum.
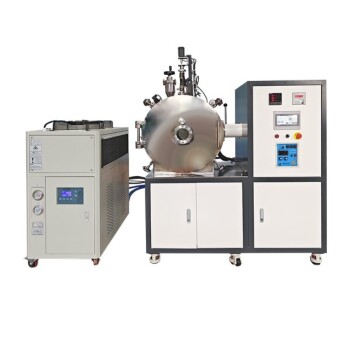
Lab-Scale Vacuum Induction Melting Furnace
Get precise alloy composition with our Vacuum Induction Melting Furnace. Ideal for aerospace, nuclear energy, and electronic industries. Order now for effective smelting and casting of metals and alloys.
Related Articles
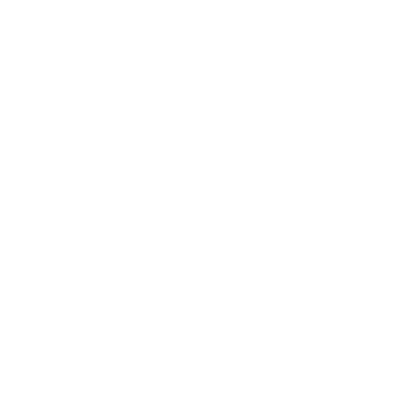
How Vacuum Induction Melting Powers Superior Material Performance in Critical Industries
Discover how Vacuum Induction Melting (VIM) ensures 99.99% pure alloys for aerospace and medical industries, boosting performance and compliance.
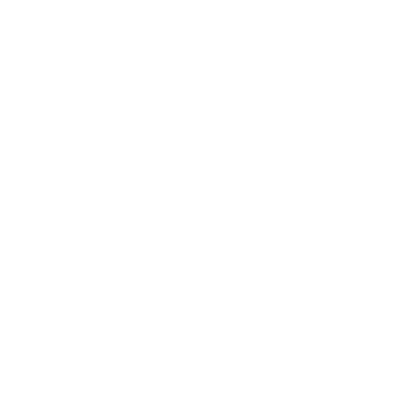
How Vacuum Induction Melting Ensures Unmatched Reliability in Critical Industries
Vacuum induction melting (VIM) ensures metallurgical purity, durability, and efficiency in aerospace, nuclear, and critical industries. Learn why VIM outperforms traditional methods.
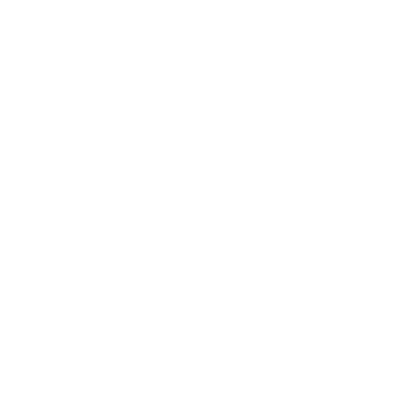
How Vacuum Induction Melting (VIM) Transforms High-Performance Alloy Production
Discover how Vacuum Induction Melting (VIM) enhances alloy purity for aerospace, medical, and nuclear industries, reducing defects and costs.
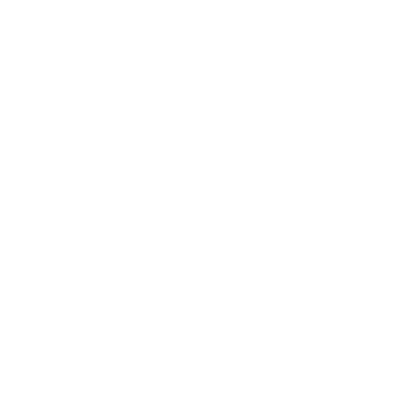
How Vacuum Induction Melting Outperforms Traditional Methods in Advanced Alloy Production
Discover how vacuum induction melting (VIM) outperforms traditional methods in advanced alloy production, offering precision, purity, and cost savings.
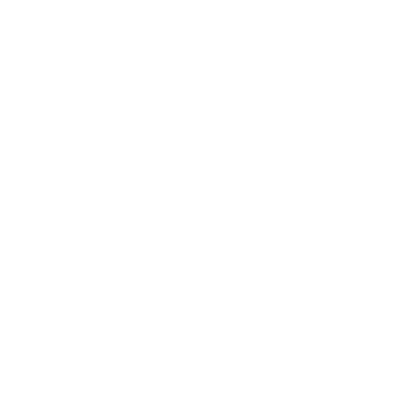
How Vacuum Induction Melting Elevates High-Performance Alloy Production
Discover how Vacuum Induction Melting (VIM) enhances alloy purity, reduces defects, and optimizes costs for aerospace and energy sectors.
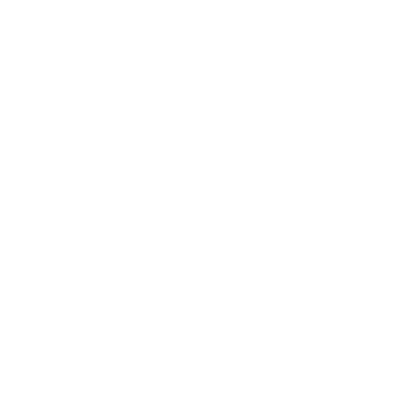
How Vacuum Induction Melting Prevents Catastrophic Material Failures in Critical Components
Discover how Vacuum Induction Melting (VIM) prevents material failures in aerospace, nuclear, and EV components by eliminating atomic-level contamination.
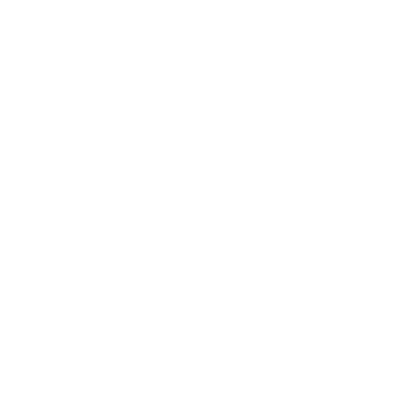
How to Choose Crucible Materials That Prevent Chemical Degradation in Vacuum Induction Melting
Learn how to choose crucible materials for vacuum induction melting to prevent chemical degradation and optimize alloy purity. Essential guide for industrial applications.
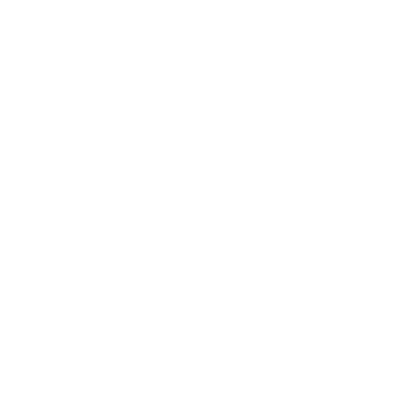
Molybdenum Vacuum Furnace: High-Temperature Sintering and Heat Treatment
Explore the advanced features and applications of molybdenum vacuum furnaces in high-temperature sintering and heat treatment. Learn about their construction, control systems, and maintenance tips.
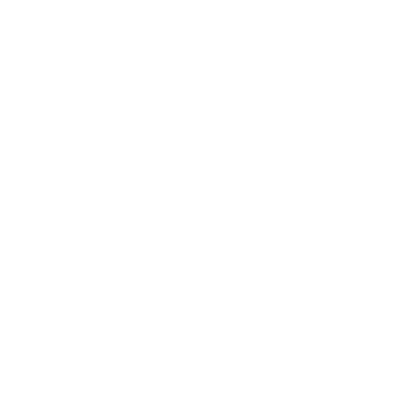
Molybdenum Vacuum Furnace: High-Temperature Sintering and Advanced Applications
Explore the advanced features and applications of molybdenum vacuum furnaces in high-temperature sintering and material treatment. Learn about their construction, control systems, and maintenance tips.
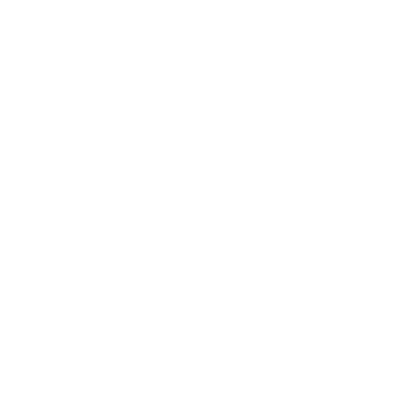
Vacuum Induction Melting Furnace: Principle, Advantages, and Applications
Discover the Vacuum Induction Melting Furnace, a specialized equipment that employs vacuum and induction heating to refine metals and alloys, ensuring high purity and precise composition control. Explore its principle, advantages, applications, and components in this comprehensive guide.
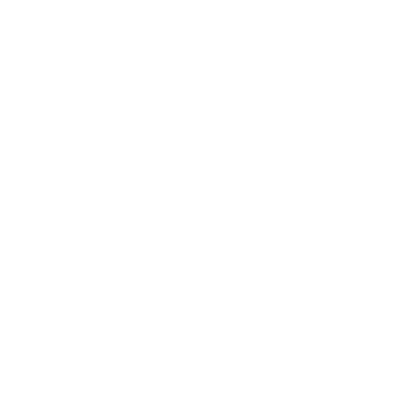
Dos and don'ts during the installation of molybdenum disilicide (MoSi2) heating element
Precautions when installing MoSi2 heating elements
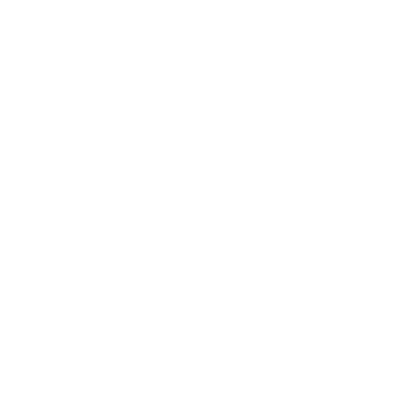
Vacuum Induction Furnace Fault Inspection: Essential Procedures and Solutions
Discover the essential procedures for inspecting and troubleshooting common faults in vacuum induction furnace. Learn how to troubleshoot electrical failures, conduct post-operation inspections, maintain records, and monitor the furnace's operation. Take corrective actions to ensure the furnace's optimal performance. Find expert solutions for temperature abnormalities, vacuum level deviations, and furnace chamber inspections.