Introduction to Molybdenum Vacuum Furnaces
Molybdenum vacuum furnaces are pivotal in high-temperature applications, leveraging the unique properties of molybdenum to excel in demanding environments. These advanced systems are not only essential for high-temperature atmosphere sintering but also for vacuum sintering of various materials, showcasing their versatility and critical role in modern industrial processes. This article delves into the intricate features, construction, and applications of molybdenum vacuum furnaces, providing insights into their advanced control systems and maintenance strategies, essential for ensuring optimal performance and longevity.
Key Features and Purposes of Molybdenum Vacuum Furnaces
Molybdenum vacuum furnaces are specialized pieces of equipment designed for high-temperature processing in a controlled, vacuum environment. These furnaces are particularly renowned for their use in high-temperature atmosphere sintering and vacuum sintering of various materials, which includes ceramics, metals, and composites. The unique properties of molybdenum, such as its high melting point, excellent thermal conductivity, and resistance to thermal shock, make it an ideal material for heating elements in these furnaces.
High-Temperature Stability and Efficiency
One of the primary features of molybdenum vacuum furnaces is their ability to maintain high-temperature stability. Molybdenum can operate at temperatures up to 1700°C, which is crucial for processes like sintering where precise temperature control is essential. The high thermal conductivity of molybdenum ensures efficient heat transfer, allowing for rapid heating and uniform temperature distribution within the furnace chamber. This efficiency is particularly important in industrial applications where time and energy costs are significant factors.
Vacuum Performance and Contamination Control
Molybdenum vacuum furnaces are designed to operate in a vacuum or controlled atmosphere, which is essential for preventing contamination of the materials being processed. The vacuum environment eliminates the presence of oxygen and other gases that could react with the materials at high temperatures, thereby preserving their purity and integrity. This feature is particularly beneficial in the processing of high-purity materials and in applications where trace contamination levels must be kept to a minimum.
Versatility in Applications
The versatility of molybdenum vacuum furnaces extends to a wide range of applications beyond sintering. These include heat treatment, brazing, annealing, and the processing of advanced materials such as transparent ceramics and metal matrix composites. Each of these applications benefits from the precise temperature control and the contamination-free environment provided by the furnace.
Structural Components and Design
The design of a molybdenum vacuum furnace incorporates several key components that ensure its functionality and efficiency. These include:
- Furnace Body and Lid: Constructed from high-grade stainless steel, the furnace body and lid are designed to maintain a high vacuum and are often water-cooled to handle the high temperatures.
- Heating Elements: Made from high-purity molybdenum, these elements are crucial for achieving and maintaining the required temperatures.
- Insulation Screens: These are used to minimize heat loss and ensure uniform temperature distribution within the furnace chamber.
- Vacuum System: Comprising pumps, valves, and gauges, the vacuum system is essential for maintaining the vacuum environment and controlling the atmosphere within the furnace.
- Control System: Advanced control systems, often including PLC and computer interfaces, allow for precise control over the furnace parameters, ensuring reproducibility and safety in operation.
Maintenance and Precautions
While molybdenum vacuum furnaces offer numerous advantages, they also require careful maintenance and operation to ensure longevity and performance. Molybdenum is sensitive to oxidation and contamination, so the furnaces must be operated under strictly controlled conditions. Regular maintenance, including the inspection and replacement of heating elements and seals, is crucial to prevent failures and ensure the furnace operates at peak efficiency.
In conclusion, molybdenum vacuum furnaces are indispensable tools in high-temperature processing, offering high-temperature stability, efficient heat transfer, and a contamination-free environment. Their versatility and precision make them a key component in the advancement of materials science and industrial processing technologies.
Construction and Composition of Molybdenum Vacuum Furnaces
Molybdenum vacuum furnaces are sophisticated pieces of equipment designed for high-temperature applications under vacuum or controlled atmospheres. These furnaces are crucial for processes such as sintering, heat treatment, and brazing, where maintaining a pristine environment is essential. The construction of these furnaces involves several key components, each designed to function seamlessly under extreme conditions.
Structural Components
Furnace Body and Lid: The furnace body is typically constructed from stainless steel, known for its resistance to corrosion and high-temperature deformation. The inner and outer shells are often made from 304 stainless steel, with the outer surface mirror-polished to enhance durability and aesthetics. The lid, which is detachable, includes a water-cooling mechanism in its middle section to prevent overheating and ensure a tight seal when closed.
Bottom and Vacuum System: The bottom of the furnace, similar to the lid, incorporates water cooling and features ports for electrodes, thermocouples, and other monitoring instruments. The vacuum system is integral to the operation of the furnace, consisting of a combination of vacuum pumps, valves, and gauges. These components work together to achieve and maintain the necessary vacuum levels, crucial for preventing oxidation and contamination of the materials being processed.
Heating Elements and Insulation Screen: The heart of the furnace lies in its heating elements, often made from high-purity molybdenum. Molybdenum is chosen for its excellent resistance to high temperatures and its ability to maintain structural integrity up to 1700°C. The heating elements are designed to operate at high power densities, ensuring rapid and uniform heating. The insulation screen, typically made from materials like tungsten and stainless steel, helps in maintaining the temperature within the furnace and reducing heat loss.
Operational Considerations
Material Handling and Control Systems: Molybdenum vacuum furnaces are equipped with advanced control systems that allow for precise temperature management and process control. These systems can be automated, using PLC and touch screen interfaces, enabling operators to monitor and adjust parameters in real-time. The inclusion of computerized control not only enhances efficiency but also ensures repeatability and safety in high-temperature processes.
Cooling and Safety Features: Given the high operational temperatures, cooling systems are crucial for the longevity of the furnace components. Water-cooled jackets around the furnace body, lid, and bottom help dissipate heat and prevent structural damage. Safety features such as pressure relief valves and emergency stop functions are also integrated to protect both the equipment and the operators.
Applications and Benefits
Molybdenum vacuum furnaces are versatile tools, used in a variety of industries including metallurgy, ceramics, and electronics. Their ability to operate under vacuum or controlled atmospheres makes them ideal for processes that require high purity and minimal contamination. The use of molybdenum heating elements ensures efficient and reliable heating, contributing to the overall quality and consistency of the end products.
In conclusion, the construction and composition of molybdenum vacuum furnaces are meticulously designed to meet the demands of high-temperature, high-purity applications. Each component, from the furnace body to the heating elements, plays a critical role in ensuring the furnace operates efficiently and safely, making it an indispensable tool in advanced manufacturing and research environments.
Control Systems in Molybdenum Vacuum Furnaces
Molybdenum vacuum furnaces are integral to high-temperature processing and material synthesis, employing advanced control systems to ensure precision and efficiency. These control systems, which include computer automatic control and programmable logic controller (PLC) systems, are pivotal in managing complex processes and maintaining optimal furnace operations.
Computer Automatic Control Systems
Computer automatic control systems in molybdenum vacuum furnaces are designed to handle intricate logic control functions, continuous monitoring of process parameters, and data management. These systems utilize dedicated computer hardware and software to oversee operations such as remelting rates, arc gap control, and data acquisition. An operator interface PC (OIP) serves as the primary interface between the operator and the furnace process, providing real-time process visualization, parameter adjustments, and recipe management. The OIP can also be equipped with an Ethernet network interface for seamless data transfer to other networked computers, enhancing system integration and data accessibility.
Programmable Logic Controllers (PLCs)
PLCs have revolutionized the control of vacuum furnaces by replacing traditional relay-based systems with more reliable and efficient digital controls. Originally introduced to simplify the management of multiple control instruments, PLCs are now indispensable in modern vacuum furnace systems. They reduce operator involvement, ensure consistent product quality, and minimize furnace downtime. In contemporary molybdenum vacuum furnaces, PLCs are typically integrated with touch panel interfaces, allowing operators to load and unload the furnace, select process recipes, and initiate operations with a simple push of a button.
Control System Features and Benefits
The integration of advanced control systems in molybdenum vacuum furnaces offers several key benefits:
-
Precision and Consistency: Advanced control systems enable precise adjustments of furnace parameters, ensuring uniform heat distribution and consistent processing outcomes. This precision is crucial for high-value applications where material properties must be tightly controlled.
-
Energy Efficiency: Modern control systems optimize energy usage by dynamically adjusting heating cycles and cooling rates based on real-time data. This not only reduces operational costs but also minimizes environmental impact.
-
Remote Monitoring and Control: With the ability to operate from remote locations, these systems enhance operational flexibility and safety. Remote access allows for real-time monitoring and adjustments, reducing the need for on-site personnel during critical phases of operation.
-
Data Management and Analysis: Advanced control systems facilitate comprehensive data logging and analysis, which is essential for process improvement and compliance with quality standards. Historical data can be used to refine processes and troubleshoot issues proactively.
-
Enhanced Safety: Automated control systems include safety protocols that prevent operator errors and protect against equipment malfunctions. This is particularly important in high-temperature and vacuum environments where safety risks are elevated.
Applications and Future Trends
Molybdenum vacuum furnaces equipped with advanced control systems are used in a variety of high-temperature applications, including sintering, heat treatment, and material synthesis. As technology advances, future trends in control systems are likely to focus on further integration with artificial intelligence and machine learning algorithms to predict and optimize furnace performance, enhance predictive maintenance, and improve overall process efficiency.
In conclusion, the advanced control systems in molybdenum vacuum furnaces represent a significant leap forward in precision, efficiency, and safety. These systems are essential for meeting the stringent requirements of modern high-temperature processing and material synthesis, ensuring that molybdenum vacuum furnaces remain at the forefront of advanced manufacturing technologies.
Material Properties and Performance of Molybdenum Heating Elements
Molybdenum, a refractory metal known for its high-temperature resistance and excellent electrical conductivity, is widely used in various heating elements across industrial and laboratory settings. Its ability to maintain structural integrity and performance at extreme temperatures makes it a preferred choice for applications requiring durability and reliability.
Material Properties of Molybdenum
Molybdenum exhibits several key properties that make it suitable for heating elements:
- High Melting Point: Molybdenum has a melting point of approximately 2623°C (4753°F), which is significantly higher than many other metals. This high melting point allows molybdenum heating elements to operate at temperatures up to 1700°C (3100°F) without structural failure.
- Good Electrical Conductivity: Molybdenum is a very good conductor of electricity, which is crucial for efficient heat generation in heating elements.
- Resistance to Creep: At high temperatures, molybdenum shows minimal deformation over time, known as creep resistance. This property ensures that the heating elements maintain their shape and performance under prolonged high-temperature exposure.
- Low Thermal Expansion: Molybdenum has a relatively low coefficient of thermal expansion, which helps in reducing stress and warping during rapid heating and cooling cycles.
Performance in High-Temperature Environments
In high-temperature environments, molybdenum heating elements demonstrate exceptional performance:
- Oxidation Resistance: Molybdenum forms a protective layer of molybdenum trioxide (MoO3) when exposed to high temperatures in oxidizing atmospheres. This layer helps in preventing further oxidation and extends the lifespan of the heating elements.
- Strength and Durability: Despite its high-temperature operation, molybdenum retains its strength and does not become brittle unless exposed to temperatures above 1700°C (3100°F). This ensures that the heating elements can withstand mechanical stresses and thermal shocks.
- Efficient Heat Distribution: Molybdenum's good thermal conductivity ensures uniform heat distribution, which is essential for consistent heating in industrial and laboratory furnaces.
Alloying Effects on Molybdenum
Alloying molybdenum with other elements enhances its properties and extends its operational range:
- TZM Alloy: The addition of titanium and zirconium to molybdenum forms the TZM alloy, which has improved strength, higher recrystallization temperature, and better resistance to creep. TZM can operate at element temperatures up to 1400°C (2552°F).
- Lanthanated Molybdenum (MoLa): Incorporating lanthanum trioxide into molybdenum results in a fine "stacked fiber" grain structure that significantly enhances resistance to recrystallization and high-temperature warpage. MoLa can be used at element temperatures up to 2000°C (3632°F).
- Molybdenum Disilicide (MoSi2): This compound offers low resistivity, positive resistance-temperature characteristics, and excellent high-temperature oxidation resistance. MoSi2 heating elements can operate under very high watt loads and maintain constant performance throughout their lifespan.
Applications of Molybdenum Heating Elements
Molybdenum heating elements are extensively used in various applications, including:
- Vacuum Furnaces: Due to its resistance to oxidation and high melting point, molybdenum is ideal for vacuum furnaces used in heat treatment processes such as hardening and brazing.
- Industrial and Laboratory Furnaces: Molybdenum's ability to withstand high temperatures and uniform heat distribution makes it suitable for a wide range of industrial and laboratory furnaces.
- High-Temperature Oxidation Environments: The formation of a protective oxide layer on molybdenum heating elements ensures their longevity and reliability in high-temperature oxidizing atmospheres.
In conclusion, molybdenum and its alloys are crucial materials for heating elements due to their exceptional high-temperature performance, strength, and durability. Through careful selection and alloying, these materials can be tailored to meet the specific requirements of various industrial and laboratory applications, ensuring efficient and reliable heating processes.
Maintenance and Long-Term Performance of Molybdenum Vacuum Furnaces
Maintaining the long-term performance of molybdenum vacuum furnaces is crucial for ensuring consistent and reliable operation. These furnaces are designed to operate under extreme conditions, and proper maintenance can prevent issues such as hardening, collapse, and loss of strength in heating elements at high temperatures. Here are detailed guidelines to help preserve the integrity and efficiency of your molybdenum vacuum furnace.
Heating Element Maintenance
Molybdenum heating elements are critical components of vacuum furnaces. They must be maintained carefully to prevent damage and ensure longevity. After each use, inspect the heating elements for any signs of damage. Check the connections for tightness to prevent electrical issues. If a heating element is damaged, it may be possible to repair it. Molybdenum elements can typically be repaired up to three times per element band, but this requires special precautions due to the brittleness of molybdenum and the potential release of toxic molybdenum dioxide vapors during the repair process.
Conditioning New Heating Elements
New molybdenum heating elements should be conditioned to enhance their performance and longevity. This involves heating the empty furnace to 1550°C and holding it at that temperature for one hour. This process helps to apply a thin, protective glass layer to the elements, which can prevent premature degradation. If the furnace needs to operate for extended periods at temperatures below 800°C, recondition the surfaces using the initial firing procedure to maintain their integrity.
Controlling Heating Rates
The heating rate is a critical factor in maintaining the structural integrity of the heating elements. Rapid heating can lead to thermal expansion and deformation of the heat shield. It is recommended to use a slow heating rate, especially in the high-temperature stage. For instance, reducing the ramp rate for temperatures 100-200°C below the maximum rated furnace temperature to 60-100°C per hour can prevent undue stress on the heating elements.
Vacuum and Leakage Checks
Before initiating the heating process, it is essential to check the vacuum leakage rate and the ultimate vacuum degree. Ensuring a proper vacuum environment is crucial for the efficient operation of the furnace. When the equipment is not in use, store it in a vacuum state. If there are volatile substances inside the furnace, it should be dried to prevent contamination and potential damage to the heating elements.
Handling Products and Controlling Impurities
When handling products, be cautious to avoid dropping them onto the surface of the molybdenum heating elements, as this can cause damage. Products containing iron elements with lower melting points must not volatilize onto the molybdenum belt in the furnace, as this can lead to melting over time. Hold products firmly with both hands or use mechanical objects to prevent accidental drops. Additionally, strictly control the impurity content of products to prevent contamination of the heating elements.
Electrical Connections and Cooling Systems
The electrical connection to the heating elements is typically accomplished via a water-cooled feed-through. This sealed connection contains the conductor that carries the current to the heating element. Feed-throughs are available in various current ratings, including high-capacity designs. Water-cooling prevents overheating, and it is essential to use a closed-loop, grounded cooling system with non-conductive coolants such as deionized water or ethylene glycol. Cooling lines should be constructed of nonconductive materials like polypropylene tubing to prevent the coolant from becoming part of the circuit.
Designing Heating Elements for Strength
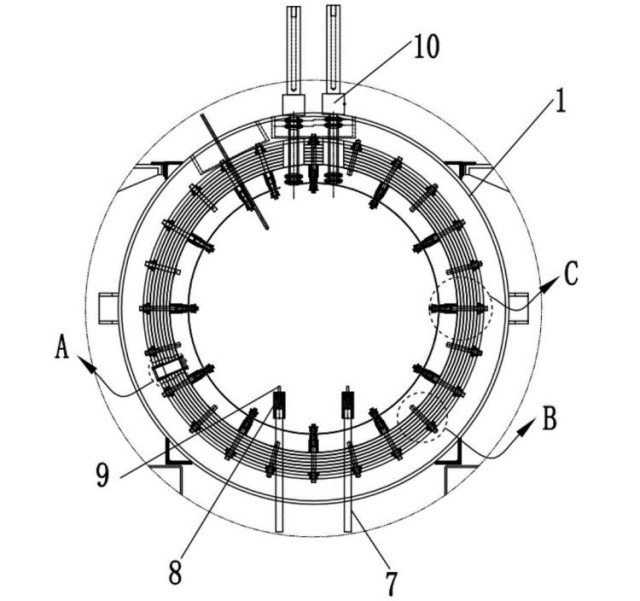
To ensure the heating wire of the vacuum furnace maintains necessary strength at high temperatures and prevents hardening, collapse, or sag, the construction size of the heating wire should be carefully designed. This includes using spiral resistance wire and paying attention to the bending diameter, pitch, and middle diameter of the heating element. The heating body should be secured against the vacuum furnace insulation lining, with 95 ceramic pieces placed in the insulation lining to provide appropriate expansion space. During use, position the heating elements suitably, generally at intervals of 100-200mm, and securely hook them to prevent the resistance wire from lying flat. Additionally, avoid direct contact between the furnace wires to prevent short circuits, typically by using isolation sheets.
By following these comprehensive maintenance and design guidelines, you can ensure the long-term performance and reliability of your molybdenum vacuum furnace, extending its service life and maintaining optimal operational efficiency.
Applications of Molybdenum Vacuum Furnaces in Industry
Molybdenum vacuum furnaces play a crucial role in various industrial sectors due to their ability to operate under high temperatures and vacuum conditions, ensuring precise control over the heating process without oxidation or contamination. This section explores the diverse applications of molybdenum vacuum furnaces in industries such as ceramics, metallurgy, electronics, and special material treatments.
Ceramics Industry
In the ceramics industry, molybdenum vacuum furnaces are essential for producing high-quality, dense ceramics with uniform properties. These furnaces enable the sintering of advanced ceramics at temperatures up to 2400°C, which is crucial for achieving the desired mechanical, electrical, and thermal properties. The vacuum environment prevents the oxidation of ceramic powders, leading to products with enhanced purity and performance. Applications include the production of technical ceramics used in electronics, aerospace, and medical devices.
Metallurgy
The metallurgy sector extensively utilizes molybdenum vacuum furnaces for melting and heat treatment of metals. These furnaces are ideal for processing refractory metals like tungsten, molybdenum, and tantalum, which require high melting points and resist oxidation. Vacuum melting helps in removing volatile impurities and gases, resulting in metals with superior purity and mechanical properties. Additionally, these furnaces are used for the heat treatment of high-strength steels, stainless steels, and tool steels to achieve desired hardness, toughness, and wear resistance.
Electronics
In the electronics industry, molybdenum vacuum furnaces are employed for the production of semiconductor devices and integrated circuits. The furnaces are used for processes such as sintering, annealing, and diffusion, which require precise temperature control and a contamination-free environment. The high-temperature capabilities of molybdenum furnaces enable the processing of advanced materials like silicon carbide and gallium nitride, which are critical for next-generation electronic devices.
Special Material Treatments
Molybdenum vacuum furnaces are also utilized for specialized material treatments in various industries. These include:
- Brazing and Soldering: Vacuum furnaces provide an ideal environment for brazing and soldering operations, ensuring high-quality joints with minimal oxidation and porosity. This is particularly important in the aerospace and automotive industries, where reliability and performance are critical.
- Nuclear Fuel Processing: Molybdenum furnaces are used for the fabrication of nuclear fuel pellets, ensuring high purity and density. The vacuum environment helps in removing volatile impurities and gases, which is essential for nuclear safety and performance.
- Glass Melting: In the glass industry, molybdenum vacuum furnaces are used for melting high-purity glasses and creating technical ceramics. The high temperatures and controlled atmosphere enable the production of specialty glasses with unique optical and mechanical properties.
Advantages of Molybdenum Vacuum Furnaces
The use of molybdenum vacuum furnaces offers several advantages, including:
- High Temperature Capabilities: Molybdenum heating elements can withstand temperatures up to 2400°C, making them suitable for processing high-temperature materials.
- Controlled Atmosphere: The vacuum environment prevents oxidation and contamination, ensuring high-quality products with consistent properties.
- Energy Efficiency: Vacuum furnaces are designed to be energy-efficient, reducing operational costs and environmental impact.
- Versatility: Molybdenum vacuum furnaces can be configured for various applications, making them a versatile tool in multiple industries.
In conclusion, molybdenum vacuum furnaces are indispensable in modern industry, enabling the production of high-quality materials and components with precise control and minimal contamination. Their applications span across ceramics, metallurgy, electronics, and special material treatments, highlighting their critical role in advancing technological and industrial processes.
Future Trends and Innovations in Molybdenum Vacuum Furnace Technology
The field of molybdenum vacuum furnace technology is poised for significant advancements and innovations that will enhance efficiency and expand applications across various industries. As the demand for high-quality materials and precise heat treatment processes increases, the development of advanced molybdenum vacuum furnaces is becoming crucial.
Efficiency Improvements
One of the primary focuses in the evolution of molybdenum vacuum furnace technology is the enhancement of operational efficiency. Innovations in heating elements, insulation materials, and control systems are expected to reduce energy consumption and improve temperature uniformity. For instance, the integration of advanced insulation materials like ceramic fibers and multilayer insulation can significantly reduce heat losses, thereby improving the overall energy efficiency of the furnace.
Moreover, the development of smart control systems that utilize artificial intelligence and machine learning algorithms can optimize heating cycles, predict maintenance needs, and adjust operational parameters in real-time. These systems can analyze vast amounts of data collected from sensors within the furnace to ensure optimal performance and minimal downtime.
New Applications
The versatility of molybdenum vacuum furnaces is opening new avenues for applications in emerging fields such as additive manufacturing, advanced ceramics, and semiconductor processing. The ability to control the atmosphere and temperature with high precision makes these furnaces ideal for processing advanced materials that require specific environmental conditions.
In the field of additive manufacturing, molybdenum vacuum furnaces can be used for post-processing of metal parts, ensuring that they are free from impurities and have the desired mechanical properties. Similarly, in the production of advanced ceramics, these furnaces can facilitate the sintering of complex shapes and compositions that are not possible with conventional methods.
Material Innovations
The development of new molybdenum alloys and composites is another area of innovation. By incorporating elements like titanium, zirconium, and rare earth metals, researchers are creating molybdenum alloys with improved high-temperature strength, corrosion resistance, and thermal conductivity. These advanced materials can extend the operational temperature range of molybdenum heating elements and enhance their durability.
Furthermore, the use of nanotechnology in the production of molybdenum heating elements can lead to significant improvements in their performance. Nanostructured coatings can enhance the emissivity of the elements, allowing for more efficient heat transfer and reduced power consumption.
Environmental Considerations
As environmental regulations become more stringent, the design of molybdenum vacuum furnaces is also evolving to minimize their ecological footprint. Innovations in furnace design that reduce waste generation and improve recycling capabilities are being explored. Additionally, the development of energy-efficient furnaces that comply with international standards for energy consumption is becoming a priority for manufacturers.
Conclusion
The future of molybdenum vacuum furnace technology is bright, with numerous innovations on the horizon that will drive efficiency improvements and expand applications. By leveraging advancements in materials science, control systems, and environmental sustainability, the industry is set to meet the growing demands for high-quality, precision-engineered materials. As these technologies continue to evolve, they will play a crucial role in shaping the future of various industries, from aerospace and automotive to electronics and healthcare.
CONTACT US FOR A FREE CONSULTATION
KINTEK LAB SOLUTION's products and services have been recognized by customers around the world. Our staff will be happy to assist with any inquiry you might have. Contact us for a free consultation and talk to a product specialist to find the most suitable solution for your application needs!