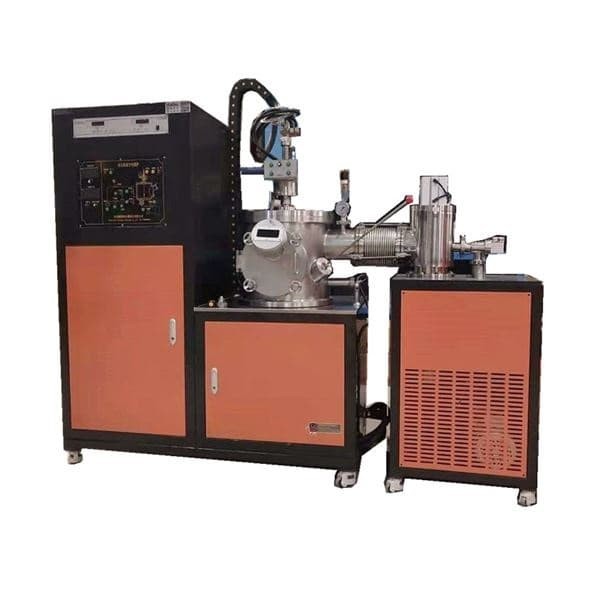
Vacuum Furnace
Vacuum Arc Induction Melting Furnace
Item Number : KT-VA
Price varies based on specs and customizations
- Capacity
- 1-200 kg
- Working voltage
- 20-40 V
- Vacuum pressure
- 1.3-1.3x10-2
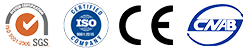
Shipping:
Contact us to get shipping details Enjoy On-time Dispatch Guarantee.
Why Choose Us
Reliable PartnerEasy ordering process, quality products, and dedicated support for your business success.
Applications
Vacuum arc furnace is mainly used to melt active metals such as titanium, niobium, zirconium and refractory metals such as tungsten and molybdenum. In addition, it is also used to melt iron base, nickel base, cobalt base and other alloy materials.
Vacuum arc furnace is characterized by high temperature, high speed melting, remarkable degassing effect, free of refractory contamination of molten metal, and able to reduce non-metallic inclusions in metal.
Vacuum arc furnace is widely used in the smelting and purification of ultra-high temperature metal materials, high entropy alloy materials, parent alloy materials, refractory metal materials, rare and precious metal materials in schools, research institutes and institutions. It can effectively remove oxygen and impurities.
Detail & Parts
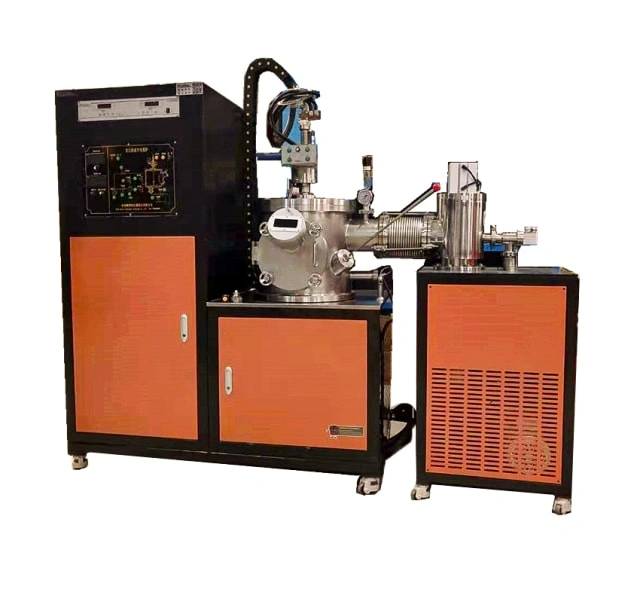
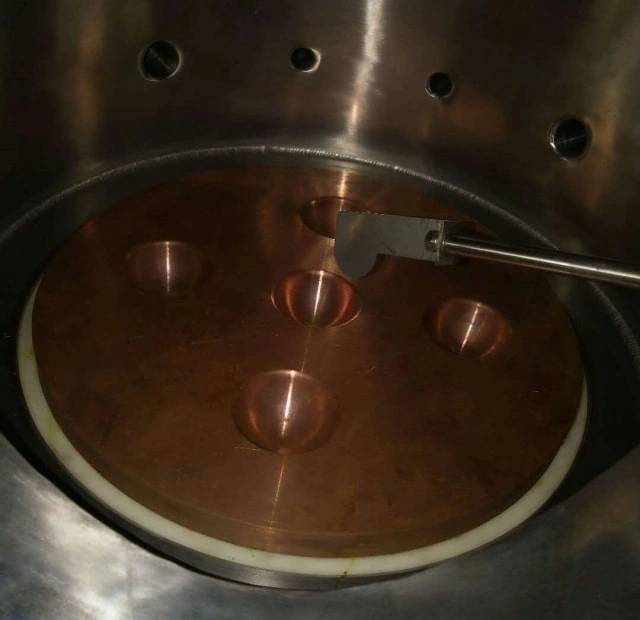
Feature
- The furnace body is all stainless steel, with beautiful appearance and no rust.
- Adopt vertical cylindrical vacuum chamber
- Equipped with a large diameter observation window, the smelting situation in the furnace can be observed in real time
- The smelting temperature is high, the temperature can be above 3500 degrees,
- A special melting power supply for arc melting is adopted.
- Equipped with an operation simulation screen, the control data is intuitively displayed, and the operation is intuitive and simple
- High vacuum design, the vacuum degree can reach 5x10E-4Pa and above
- Use over-temperature protection and add filter glass to protect eyes
- The water-cooled copper electrode can be moved 360 degrees, and the operation is flexible. At the same time, the water-cooled crucible is small and replaceable, and can be customized.
- With material turning device, to overcome the situation of uneven melting on one side of the material
- Casting station with vacuum suction casting
- Efficiency of equipment: Most metal materials are heated and remelted for one minute or less.
Technical specifications
Model | KT-VA1 | KT-VA5 | KT-VA25 | KT-VA200 |
Capacity (Kg) | 1 | 5-15 | 25 | 200 |
Working voltage (V) | 20-40 | |||
Working current (A) | 1000A | 3000A | 6000A | 12000A |
Vacuum pressure (Pa) | 1.3-1.3x10-2 | |||
Electrode size (mm) | Φ25-40 x 400 | Φ10-45x1200 | Φ30-60x1350 | Φ56-150x1745 |
Ingot size (mm) | Φ60x100 | Φ80x135 | Φ100x400mm | Φ200x670mm |
Dimensions (m) | 0.8x0.35x1.8 | 3.81x3.0x5.21 | 4.43x3.33x4.93 | 7.4x3.4x6.72 |
Warnings
Operator safety is the top important issue! Please operate the equipment with cautions. Working with inflammable& explosive or toxic gases is very dangerous, operators must take all necessary precautions before starting the equipment. Working with positive pressure inside the reactors or chambers is dangerous, operator must fellow the safety procedures strictly. Extra caution must also be taken when operating with air-reactive materials, especially under vacuum. A leak can draw air into the apparatus and cause a violent reaction to occur.
Designed for You
KinTek provide deep custom made service and equipment to worldwide customers, our specialized teamwork and rich experienced engineers are capable to undertake the custom tailoring hardware and software equipment requirements, and help our customer to build up the exclusive and personalized equipment and solution!
Would you please drop your ideas to us, our engineers are ready for you now!
FAQ
What Is A Vacuum Induction Furnace And How Does It Work?
What Is A Vacuum Furnace Used For?
What Is CVD Furnace?
Chemical vapor deposition (CVD) is a technology that uses various energy sources such as heating, plasma excitation or light radiation to chemically react gaseous or vapor chemical substances on the gas phase or gas-solid interface to form solid deposits in the reactor by means of chemical reaction.To put it simply, two or more gaseous raw materials are introduced into a reaction chamber, and then they react with each other to form a new material and deposit it on the substrate surface.
CVD furnace is one combined furnace system with high temperature tube furnace unit,gases control unit, and vacuum unit, it is widely used for experiment and production of composite material preparation, microelectronics process, semiconductor optoelectronic, solar energy utilization, optical fiber communication, superconductor technology, protective coating field.
What Are The Main Applications Of Vacuum Induction Furnaces?
How Does A Vacuum Induction Melting Furnace Work?
What Is Vacuum Arc Melting Process?
What Is The Process Of A Vacuum Furnace?
How Does CVD Furnace Work?
CVD furnace system consists of high temperature tube furnace unit, reacting gas source precise control unit, vacuum pump station and corresponding assembling parts.
Vacuum pump is to remove the air from the reacting tube,and make sure there is no unwanted gases inside the reaction tube, after that the tube furnace will heat the reaction tube to a target temperature, then reacting gas source precise control unit can introduce different gases with a set ratio into the furnace tube for the chemical reaction, the chemical vapor deposition will be formed in the CVD furnace.
What Are The Advantages Of Using A Vacuum Induction Furnace?
What Are The Advantages Of Vacuum Induction Melting?
What Is VAR Vacuum Arc Remelting (VAR)Furnace?
What Gas Is Used In A Vacuum Furnace?
Which Gas Is Used In CVD Process?
There are tremendous gas sources can be used in the CVD process, the common chemical reactions of CVD includes Pyrolysis, photolysis, reduction, oxidation, redox,so the gases involved in these chemical reactions can be used in the CVD process.
We take CVD Graphene growth for an example, the gases used in the CVD process will be CH4,H2,O2 and N2.
What Types Of Materials Can Be Processed In A Vacuum Induction Furnace?
How Does Vacuum Help In Induction Melting Furnace?
How Does Vacuum Arc Melting Furnace Work?
What Is The Heating Element Used In A Vacuum Furnace?
What Is The Advantage Of CVD System?
- Wide range of films can be produced, metal film, nonmetal film and multi-component alloy film as required. At the same time, it can prepare high-quality crystals that are difficult to obtain by other methods, such as GaN, BP, etc.
- The film forming speed is fast, usually several microns per minute or even hundreds of microns per minute. It is possible to simultaneously deposit large quantities of coatings with uniform composition, which is incomparable to other film preparation methods, such as liquid phase epitaxy (LPE) and molecular beam epitaxy (MBE).
- The working conditions are carried out under normal pressure or low vacuum conditions, so the coating has good diffraction, and the workpieces with complex shapes can be uniformly coated, which is much superior to PVD.
- Due to the mutual diffusion of reaction gas, reaction product and substrate, a coating with good adhesion strength can be obtained, which is crucial for preparing surface strengthened films such as wear-resistant and anti-corrosion films.
- Some films grow at a temperature far lower than the melting point of the film material. Under the condition of low temperature growth, the reaction gas and reactor wall and impurities contained in them almost do not react, so a film with high purity and good crystallinity can be obtained.
- Chemical vapor deposition can obtain a smooth deposition surface. This is because compared with LPE, chemical vapor deposition (CVD) is carried out under high saturation, with high nucleation rate, high nucleation density, and uniform distribution on the whole plane, resulting in a macroscopic smooth surface. At the same time, in chemical vapor deposition, the average free path of molecules (atoms) is much larger than LPE, so the spatial distribution of molecules is more uniform, which is conducive to the formation of a smooth deposition surface.
- Low radiation damage, which is a necessary condition for manufacturing metal oxide semiconductors (MOS) and other devices
How Does The Vacuum Environment In A Vacuum Induction Furnace Improve Material Properties?
What Is Vacuum Induction Melting Furnace?
What Are The Applications Of Vacuum Arc Melting Furnaces?
What Does PECVD Stand For?
PECVD is a technology that uses plasma to activate reaction gas, promote chemical reaction on the surface of substrate or near surface space, and generate solid film. The basic principle of plasma chemical vapor deposition technology is that under the action of RF or DC electric field, the source gas is ionized to form a plasma, the low-temperature plasma is used as the energy source, an appropriate amount of reaction gas is introduced, and the plasma discharge is used to activate the reaction gas and realize chemical vapor deposition.
According to the method of generating plasma, it can be divided into RF plasma, DC plasma and microwave plasma CVD, etc...
What Are The Advantages Of Using Vacuum Arc Melting Furnaces?
What Is The Difference Between CVD And PECVD?
The difference between PECVD and traditional CVD technology is that the plasma contains a large number of high-energy electrons, which can provide the activation energy required in the chemical vapor deposition process, thus changing the energy supply mode of the reaction system. Since the electron temperature in the plasma is as high as 10000K, the collision between electrons and gas molecules can promote the chemical bond breaking and recombination of the reaction gas molecules to generate more active chemical groups, while the whole reaction system maintains a lower temperature.
So compared to the CVD process, PECVD can carry out the same chemical vapor deposition process with a lower temperature.
What Safety Precautions Should Be Followed When Using A Vacuum Arc Melting Furnace?
4.8
out of
5
Vacuum arc furnace is a great tool for melting active metals and preparing bulk amorphous materials by vacuum suction casting.
4.9
out of
5
The vacuum induction furnace allows for the smelting of refractory metals and the production of special corrosion-resistant and heat-resistant alloys.
4.7
out of
5
Vacuum induction melting furnace has the advantages of no air and vacuum induction furnace slag pollution, pure alloy, and low gas content.
4.8
out of
5
The vacuum induction furnace is widely used in the smelting and purification of various metal materials in schools, research institutes, and institutions.
4.9
out of
5
Vacuum arc furnace is characterized by high temperature, high speed melting, remarkable degassing effect, and free of refractory contamination of molten metal.
4.7
out of
5
The vacuum induction melting furnace is mainly composed of a furnace shell, inductor, crucible, furnace tilting mechanism, mold mechanism, power supply device, and a water cooling system.
4.8
out of
5
The vacuum arc furnace is mainly used to melt active metals such as titanium, niobium, zirconium and refractory metals such as tungsten and molybdenum.
4.9
out of
5
Vacuum induction melting technology and induction smelting technology have been applied in different occasions.
4.7
out of
5
The development and progress of vacuum induction furnace are mainly reflected in the gradual improvement of the overall structure of the equipment, the increasingly obvious trend of modularization and the more intelligent control system.
4.8
out of
5
Vacuum arc furnace is suitable for scientific research and small batch preparation of new vacuum metallurgy materials in universities and scientific research institutes.
4.9
out of
5
The vacuum induction furnace is widely used in the smelting and purification of ultra-high temperature metal materials, high entropy alloy materials, parent alloy materials, refractory metal materials, rare and precious metal materials.
4.7
out of
5
The vacuum arc furnace can effectively remove oxygen and impurities.
4.8
out of
5
The vacuum induction furnace is mainly used to melt active metals, such as titanium alloy, etc.
4.9
out of
5
The vacuum induction furnace can prevent melting of metals and alloys, and react with non-metallic inclusions.
4.7
out of
5
The vacuum induction furnace can remove the harmful dissolved gases and pollutants in molten metals.
4.8
out of
5
The vacuum induction furnace has the advantages of no air and vacuum induction furnace slag pollution, pure alloy, and low gas content.
4.9
out of
5
The vacuum arc furnace is widely used in the smelting and purification of various metal materials in schools, research institutes, and institutions.
4.7
out of
5
The vacuum induction melting furnace is mainly composed of a furnace shell, inductor, crucible, furnace tilting mechanism, mold mechanism, power supply device, and a water cooling system.
REQUEST A QUOTE
Our professional team will reply to you within one business day. Please feel free to contact us!
Related Products
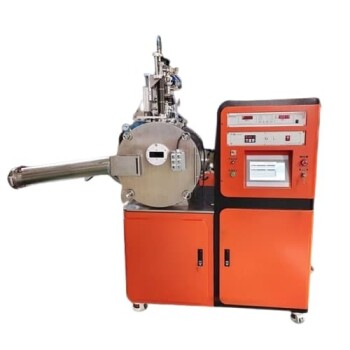
Vacuum Induction Melting Spinning System Arc Melting Furnace
Develop metastable materials with ease using our Vacuum Melt Spinning System. Ideal for research and experimental work with amorphous and microcrystalline materials. Order now for effective results.
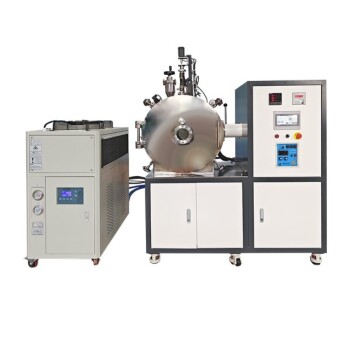
Lab-Scale Vacuum Induction Melting Furnace
Get precise alloy composition with our Vacuum Induction Melting Furnace. Ideal for aerospace, nuclear energy, and electronic industries. Order now for effective smelting and casting of metals and alloys.
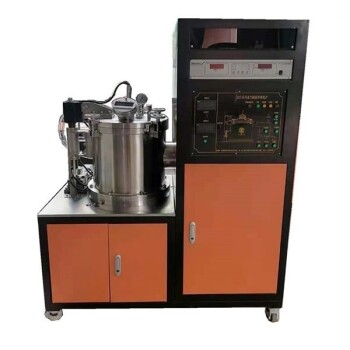
Vacuum Heat Treat Furnace and Levitation Induction Melting Furnace
Experience precise melting with our Vacuum Levitation Melting Furnace. Ideal for high melting point metals or alloys, with advanced technology for effective smelting. Order now for high-quality results.
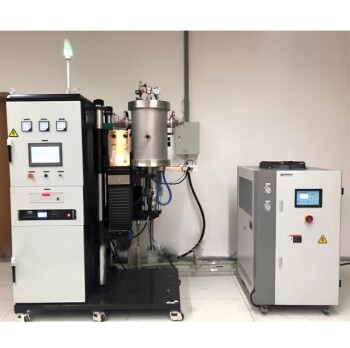
Vacuum Heat Treat and Molybdenum Wire Sintering Furnace for Vacuum Sintering
A vacuum molybdenum wire sintering furnace is a vertical or bedroom structure, which is suitable for withdrawal, brazing, sintering and degassing of metal materials under high vacuum and high temperature conditions. It is also suitable for dehydroxylation treatment of quartz materials.
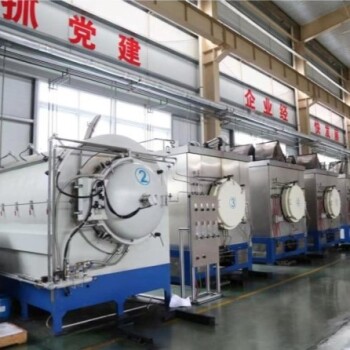
Vacuum Heat Treat Sintering Brazing Furnace
A vacuum brazing furnace is a type of industrial furnace used for brazing, a metalworking process that joins two pieces of metal using a filler metal that melts at a lower temperature than the base metals. Vacuum brazing furnaces are typically used for high-quality applications where a strong, clean joint is required.
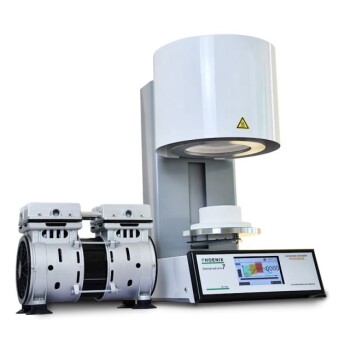
Vacuum Dental Porcelain Sintering Furnace
Get precise and reliable results with KinTek's Vacuum Porcelain Furnace. Suitable for all porcelain powders, it features hyperbolic ceramic furnace function, voice prompt, and automatic temperature calibration.
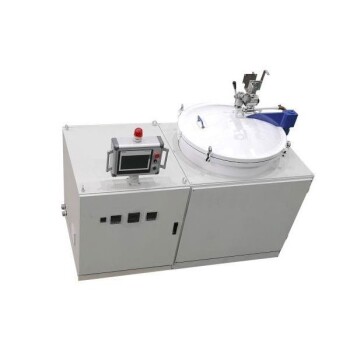
Graphite Vacuum Furnace IGBT Experimental Graphitization Furnace
IGBT experimental graphitization furnace, a tailored solution for universities and research institutions, with high heating efficiency, user-friendliness, and precise temperature control.
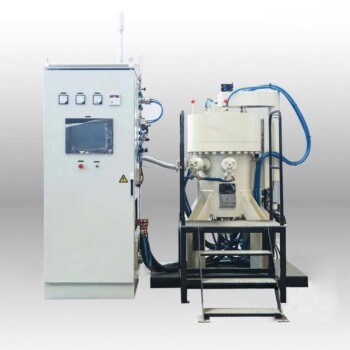
Vacuum Heat Treat and Sintering Furnace with 9MPa Air Pressure
The air pressure sintering furnace is a high-tech equipment commonly used for the sintering of advanced ceramic materials. It combines vacuum sintering and pressure sintering techniques to achieve high-density and high-strength ceramics.
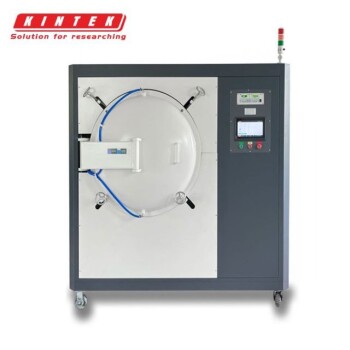
Vacuum Heat Treat Furnace with Ceramic Fiber Liner
Vacuum furnace with polycrystalline ceramic fiber insulation liner for excellent heat insulation and uniform temperature field. Choose from 1200℃ or 1700℃ max. working temperature with high vacuum performance and precise temperature control.
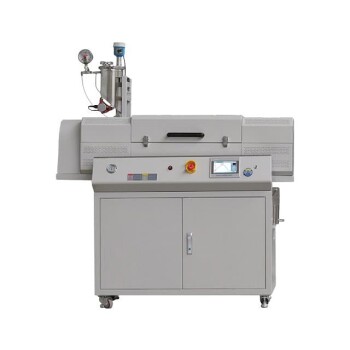
Laboratory Vacuum Tilt Rotary Tube Furnace Rotating Tube Furnace
Discover the versatility of Laboratory Rotary Furnace: Ideal for calcination, drying, sintering, and high-temperature reactions. Adjustable rotating and tilting functions for optimal heating. Suitable for vacuum and controlled atmosphere environments. Learn more now!
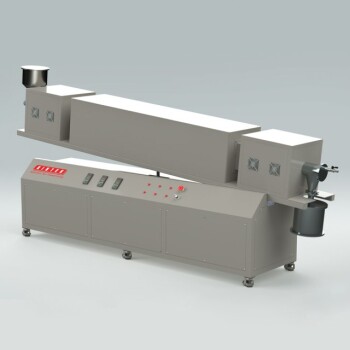
Vacuum Sealed Continuous Working Rotary Tube Furnace Rotating Tube Furnace
Experience efficient material processing with our vacuum-sealed rotary tube furnace. Perfect for experiments or industrial production, equipped with optional features for controlled feeding and optimized results. Order now.
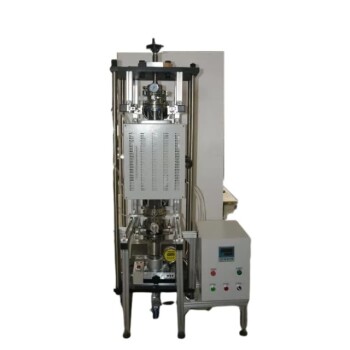
Vacuum Hot Press Furnace Heated Vacuum Press Machine Tube Furnace
Reduce forming pressure & shorten sintering time with Vacuum Tube Hot Press Furnace for high-density, fine-grain materials. Ideal for refractory metals.
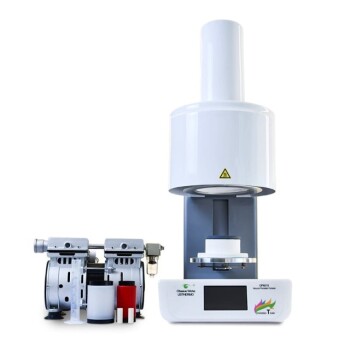
Dental Porcelain Zirconia Sintering Ceramic Vacuum Press Furnace
Get precise dental results with Dental Vacuum Press Furnace. Automatic temperature calibration, low noise tray, and touch screen operation. Order now!
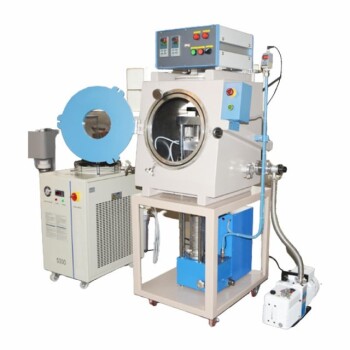
Vacuum Hot Press Furnace Machine for Lamination and Heating
Experience clean and precise lamination with Vacuum Lamination Press. Perfect for wafer bonding, thin-film transformations, and LCP lamination. Order now!
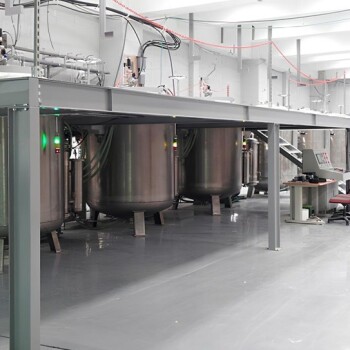
Graphite Vacuum Furnace Negative Material Graphitization Furnace
Graphitization furnace for battery production has uniform temperature and low energy consumption. Graphitization furnace for negative electrode materials: an efficient graphitization solution for battery production and advanced functions to enhance battery performance.

Graphite Vacuum Furnace Bottom Discharge Graphitization Furnace for Carbon Materials
Bottom-out graphitization furnace for carbon materials, ultra-high temperature furnace up to 3100°C, suitable for graphitization and sintering of carbon rods and carbon blocks. Vertical design, bottom discharging, convenient feeding and discharging, high temperature uniformity, low energy consumption, good stability, hydraulic lifting system, convenient loading and unloading.
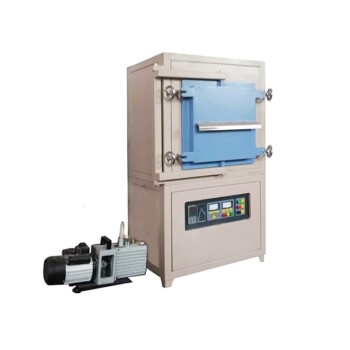
1700℃ Controlled Atmosphere Furnace Nitrogen Inert Atmosphere Furnace
KT-17A Controlled atmosphere furnace: 1700℃ heating, vacuum sealing technology, PID temperature control, and versatile TFT smart touch screen controller for laboratory and industrial use.
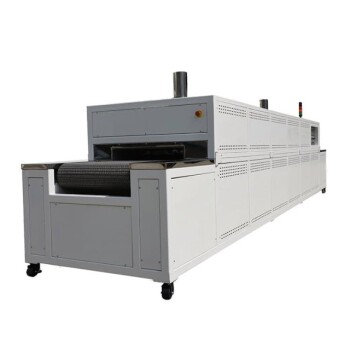
Mesh belt controlled atmosphere furnace
Discover our KT-MB mesh belt sintering furnace - perfect for high-temperature sintering of electronic components & glass insulators. Available for open air or controlled atmosphere environments.
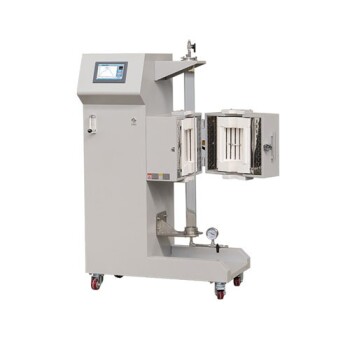
Vertical Laboratory Quartz Tube Furnace Tubular Furnace
Elevate your experiments with our Vertical Tube Furnace. Versatile design allows for operation under various environments and heat treatment applications. Order now for precise results!
Related Articles
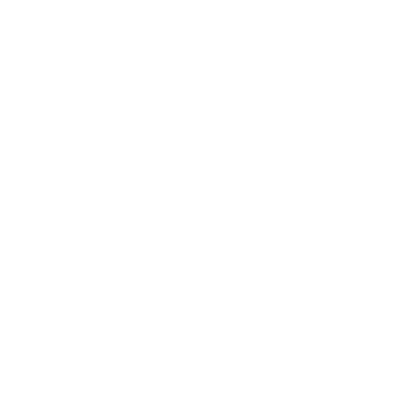
Application of Hot Isostatic Pressing Technology in Nickel-Based Casting High-Temperature Alloys
Explores the use of hot isostatic pressing to enhance the properties of nickel-based casting high-temperature alloys in aerospace applications.
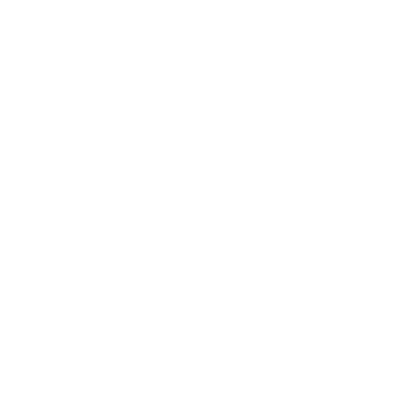
Vacuum Induction Melting Furnace: Principle, Advantages, and Applications
Discover the Vacuum Induction Melting Furnace, a specialized equipment that employs vacuum and induction heating to refine metals and alloys, ensuring high purity and precise composition control. Explore its principle, advantages, applications, and components in this comprehensive guide.
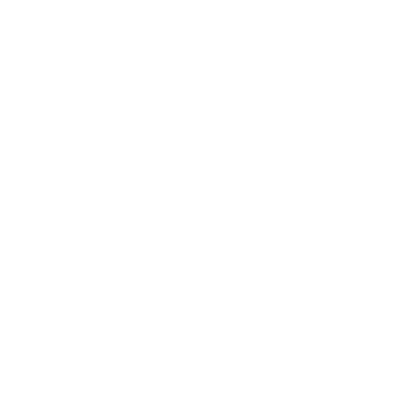
Vacuum Induction Melting Furnace vs Arc Melting Furnace: Choosing the Right Equipment for Your Process
Learn about the key differences between vacuum induction melting furnaces and arc melting furnaces, including their advantages and applications, to help you choose the best equipment for your specific needs.
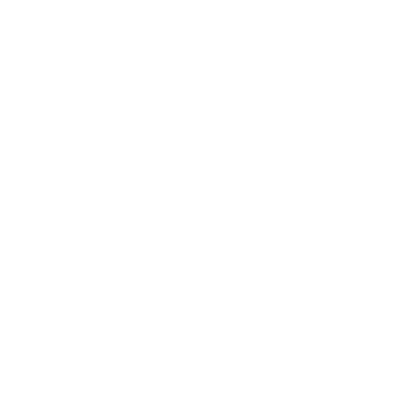
Vacuum Melting Furnace: A Comprehensive Guide to Vacuum Induction Melting
Discover the intricacies of vacuum induction melting furnaces, their components, operation, advantages, and applications. Explore how these furnaces revolutionize metal processing and achieve exceptional material properties.
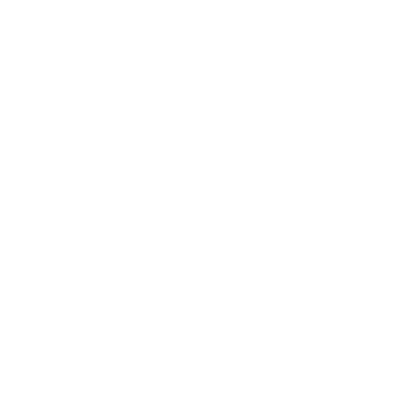
Melting process and maintenance of vacuum induction melting furnace
Melting process and maintenance of vacuum induction melting furnace
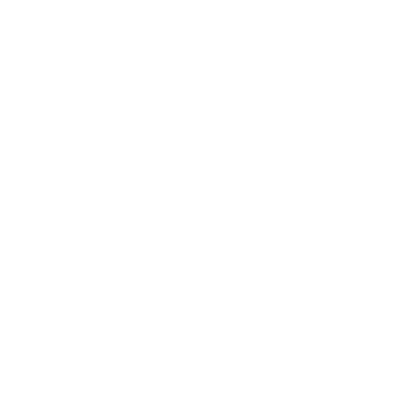
Exploring Tungsten Vacuum Furnaces: Operation, Applications, and Advantages
Discover the operation, applications, and benefits of tungsten vacuum furnaces in laboratory settings. Learn about KinTek's advanced features, control mechanisms, and the use of tungsten in high-temperature environments.
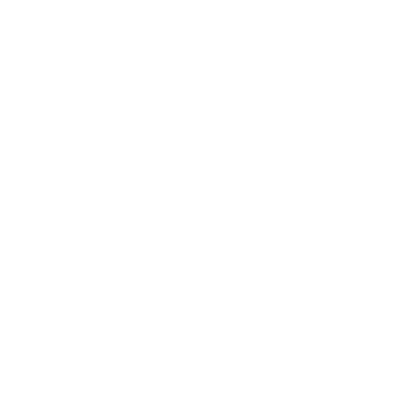
Vacuum Induction Furnace Fault Inspection: Essential Procedures and Solutions
Discover the essential procedures for inspecting and troubleshooting common faults in vacuum induction furnace. Learn how to troubleshoot electrical failures, conduct post-operation inspections, maintain records, and monitor the furnace's operation. Take corrective actions to ensure the furnace's optimal performance. Find expert solutions for temperature abnormalities, vacuum level deviations, and furnace chamber inspections.
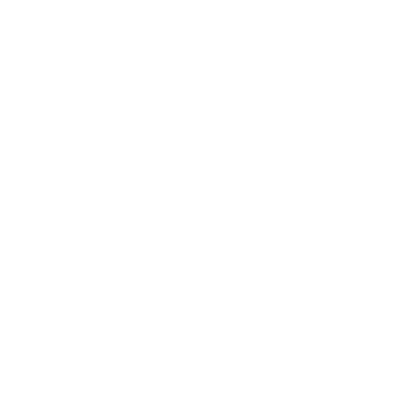
Unlocking the Potential: Vacuum Levitation Induction Melting Furnace Explained
Discover the working principles, applications, and advantages of vacuum levitation induction melting furnaces. Learn how this technology revolutionizes metal smelting, ensuring purity, efficiency, and environmental friendliness.
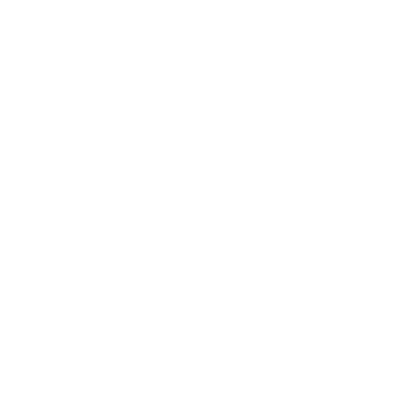
Vacuum Laboratory Furnaces in Advanced Materials Research
In addition to size, there are several other key differences between industrial-scale and laboratory vacuum furnaces
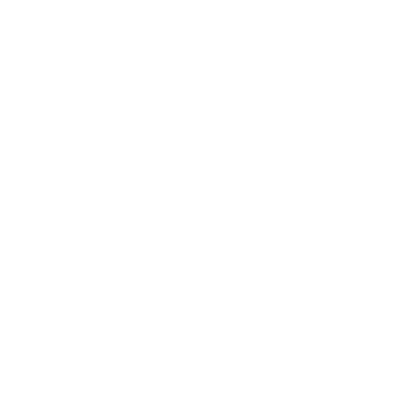
Materials Science with the Lab Vacuum Furnace
A vacuum furnace is a specialized type of furnace that is designed to operate in a vacuum environment. This means that the furnace is sealed and the air inside is pumped out, creating a low pressure or vacuum inside.
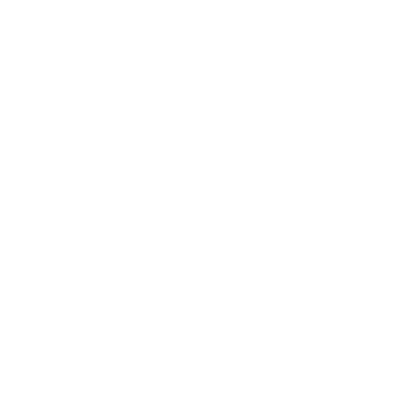
Evaluating the Pros and Cons of External Vacuum Heat Treatment Furnaces
we evaluate the pros and cons of using external vacuum heat treatment furnaces to help manufacturers determine if it is the right choice for their specific process.
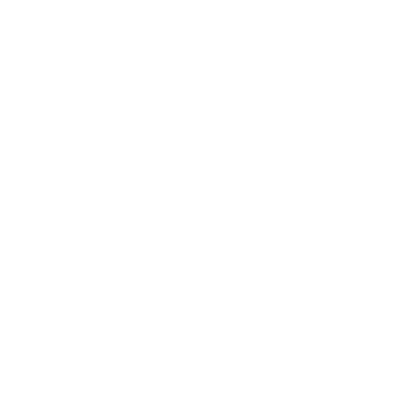
Exploring the Benefits of Using Tungsten for Furnace Heating
Tungsten has a number of properties that make it well-suited for use in high-temperature furnaces.