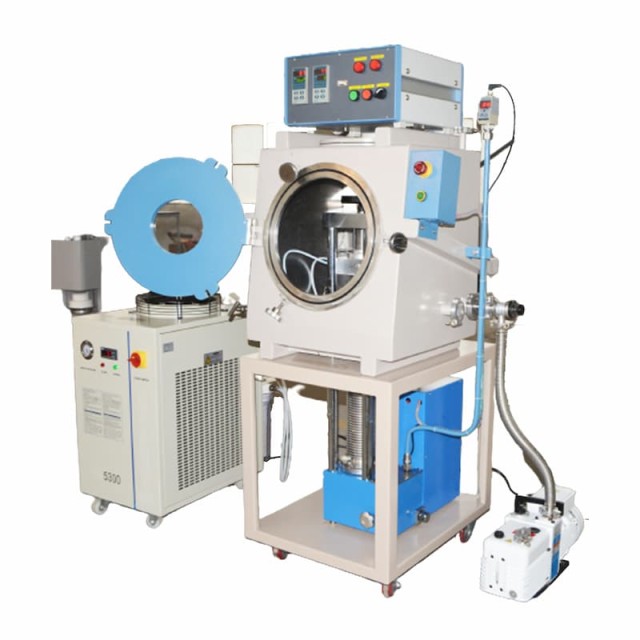
Vacuum Hot Press Furnace
Vacuum Hot Press Furnace Machine for Lamination and Heating
Item Number : KT-VLP
Price varies based on specs and customizations
- Plates travel distance
- 30-40 mm
- Heating temperature
- <500 ℃
- Vacuum pressure
- -0.1Mpa
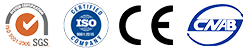
Shipping:
Contact us to get shipping details Enjoy On-time Dispatch Guarantee.
Why Choose Us
Reliable PartnerEasy ordering process, quality products, and dedicated support for your business success.
Introduction
Vacuum lamination press is a multi-functional machine that combines hydraulic press, electric heating, and a vacuum glove box. With electric heating plates embedded in the hydraulic press plate, thermal insulation, and circulating water cooling, the high temperature of the hydraulic press structure can be prevented. The pressing plates are located inside the vacuum glove box, which can generate a vacuum and a clean environment for oxygen-sensitive processing products.
Vacuum lamination presses are commonly used for wafer bonding, thin-film transformations, and LCP lamination. They are particularly useful in applications where a vacuum and a clean environment are required to prevent oxidation or contamination of the materials being processed.
Applications
Vacuum lamination press finds its applications in diverse industries, including:
- Wafer bonding
- Thin-film transformations
- LCP lamination
- Decorative engineered laminates for aircraft interior panels
- Vacuum clamping
- Vacuum chucking
- Veneering
- Vacuum forming for clay pottery
- Vacuum clamping & template routing
Features
The Vacuum Lamination Press is a specialized hydraulic compression press designed to cater to a wide range of industries including electronics, printed circuit boards, decorative laminates, and honeycomb panels. This press stands out with its advanced features that not only enhance the lamination process but also ensure high-quality results. Here are the key benefits of the Vacuum Lamination Press:
- Precise Temperature and Pressure Controls: Equipped with multiple openings, this press allows for exact adjustments of temperature and pressure, ensuring optimal bonding conditions for various materials. This precision is crucial for maintaining the integrity and quality of the laminates.
- Versatile Heating Options: The platens can be heated using electric heaters, steam, or hot oil, providing flexibility to match the heating requirements of different materials and applications. This versatility ensures that the press can be adapted to a wide range of industrial needs.
- Internal Cooling System: For applications requiring rapid processing, the platens are internally cooled. This feature significantly reduces the cooling time, thereby increasing the overall productivity of the press.
- Vacuum Environment: The hot pressing plate is placed in a vacuum negative pressure box, which is ideal for applications requiring a controlled environment free from air pockets and contaminants. This vacuum setting is particularly beneficial for delicate materials and high-precision products.
- Wide Range of Applications: From straight and curved veneer panels to carbon fiber work and vacuum infusion, the Vacuum Lamination Press is capable of handling a multitude of tasks. This makes it an invaluable tool for industries that require sophisticated lamination processes.
Detail & Parts
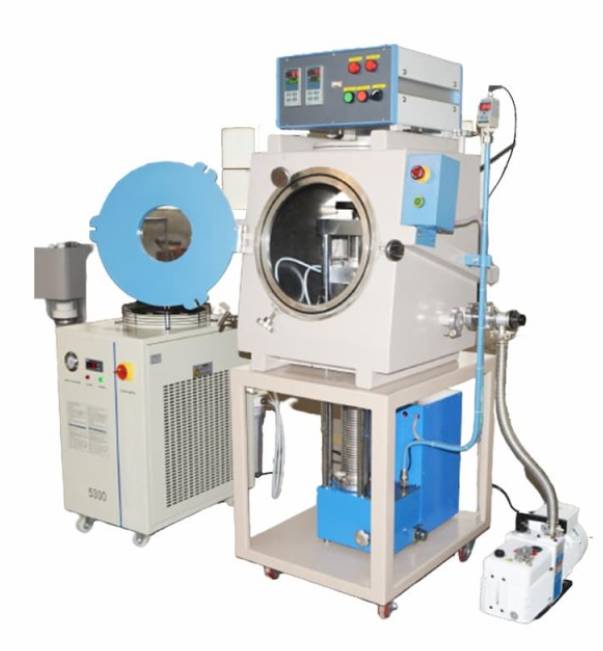
Principle
Vacuum Lamination Press is a type of hydraulic press that is used to bond two or more layers of material together. The press uses a vacuum to remove air from between the layers, which creates a strong bond. The press also uses heat to soften the materials, which makes them easier to bond together.
Vacuum Lamination Presses are used in a variety of industries, including the automotive, aerospace, and electronics industries. They are used to bond a variety of materials, including metals, plastics, and composites.
Advantages
- Vacuum glove box provides a vacuum and clean environment for oxygen-sensitive processing products.
- Integrated features of hydraulic press, electric heating, and vacuum glove box.
- Precise temperature and pressure controls ensure optimal bonding results.
- Electric heating plates prevent high temperatures from affecting the hydraulic press structure.
- Suitable for a wide range of applications, including wafer bonding, thin-film transformations, and LCP lamination.
- Ideal for heat-sensitive materials as the vacuum membrane system forms the heated laminate without glossing or texture washout.
- Capable of forming and bonding laminates into deep recesses without popping or bubbling.
- Versatile machine that combines multiple functionalities for efficient and effective lamination processes.
Dimensions | Over-all: 775mm(L) x 550mm(W) x 1325mm(H) |
---|---|
Structure |
|
Hydraulic Pump |
|
Temperature control and Pressure Display |
|
Vacuum Charmber |
|
Technical parameters
Model | KT-VLP100 | KT-VLP300 | KT-VLP400 |
---|---|---|---|
Heating plate size | 100x100mm | 300x300mm | 400x400mm |
Plates travel distance | 30mm | 40mm | 40mm |
Working pressure | 30T during heating/40Tin the cold state | ||
Pressure gauge | Digital pressure gauge | ||
Heating temperature | <500℃ | ||
Temperature control | Touch screen with PID thermal controller | ||
Vacuum chamber | 304 Stainless steel | ||
Vacuum pump | Rotary vane vacuum pump | ||
Vacuum pressure | -0.1Mpa | ||
Power supply | AC110-220V, 50/60HZ |
Warnings
Operator safety is the top important issue! Please operate the equipment with cautions. Working with inflammable& explosive or toxic gases is very dangerous, operators must take all necessary precautions before starting the equipment. Working with positive pressure inside the reactors or chambers is dangerous, operator must fellow the safety procedures strictly. Extra caution must also be taken when operating with air-reactive materials, especially under vacuum. A leak can draw air into the apparatus and cause a violent reaction to occur.
Designed for You
KinTek provide deep custom made service and equipment to worldwide customers, our specialized teamwork and rich experienced engineers are capable to undertake the custom tailoring hardware and software equipment requirements, and help our customer to build up the exclusive and personalized equipment and solution!
Would you please drop your ideas to us, our engineers are ready for you now!
FAQ
What Is A Vacuum Furnace Used For?
What Is The Purpose Of A Vacuum Hot Press Furnace?
What Is The Process Of A Vacuum Furnace?
What Are The Advantages Of A Vacuum Hot Press Furnace?
What Gas Is Used In A Vacuum Furnace?
How Does A Vacuum Hot Press Furnace Work?
What Is The Heating Element Used In A Vacuum Furnace?
What Are The Common Applications Of Vacuum Hot Press Furnaces?
What Factors Should Be Considered When Selecting A Vacuum Hot Press Furnace?
4.9
out of
5
I've been using the Vacuum Lamination Press for a few months now, and it has been an excellent investment. It's easy to use and has helped me create some beautiful pieces of art.
4.7
out of
5
I'm a laboratory manager, and I've been using the Vacuum Lamination Press for over a year now. It's a great machine that has helped me produce high-quality laminates for my research.
4.8
out of
5
I'm very impressed with the Vacuum Lamination Press. It's a versatile machine that can be used for a variety of applications. I've used it to create laminates for my research, and I've also used it to repair some damaged furniture.
4.6
out of
5
The Vacuum Lamination Press is a great machine. It's easy to use and produces high-quality laminates. I've been using it for a few months now, and I've been very happy with the results.
4.9
out of
5
I'm a laboratory manager, and I've been using the Vacuum Lamination Press for over a year now. It's a great machine that has helped me produce high-quality laminates for my research. I would highly recommend it to anyone looking for a vacuum lamination press.
4.7
out of
5
I'm very impressed with the Vacuum Lamination Press. It's a versatile machine that can be used for a variety of applications. I've used it to create laminates for my research, and I've also used it to repair some damaged furniture. I would highly recommend it to anyone looking for a vacuum lamination press.
4.8
out of
5
The Vacuum Lamination Press is a great machine. It's easy to use and produces high-quality laminates. I've been using it for a few months now, and I've been very happy with the results. I would highly recommend it to anyone looking for a vacuum lamination press.
4.6
out of
5
I'm a laboratory manager, and I've been using the Vacuum Lamination Press for over a year now. It's a great machine that has helped me produce high-quality laminates for my research. I would highly recommend it to anyone looking for a vacuum lamination press.
Products
Vacuum Hot Press Furnace Machine for Lamination and Heating
REQUEST A QUOTE
Our professional team will reply to you within one business day. Please feel free to contact us!
Related Products
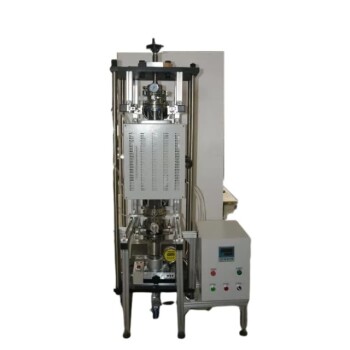
Vacuum Hot Press Furnace Heated Vacuum Press Machine Tube Furnace
Reduce forming pressure & shorten sintering time with Vacuum Tube Hot Press Furnace for high-density, fine-grain materials. Ideal for refractory metals.
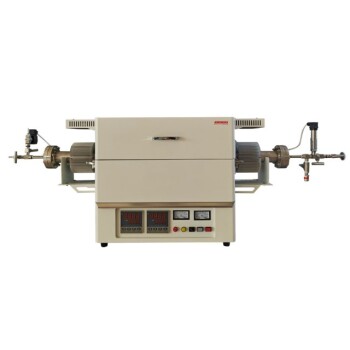
High Pressure Laboratory Vacuum Tube Furnace Quartz Tubular Furnace
KT-PTF High Pressure Tube Furnace: Compact split tube furnace with strong positive pressure resistance. Working temp up to 1100°C and pressure up to 15Mpa. Also works under controller atmosphere or high vacuum.
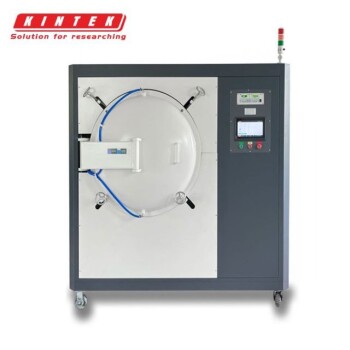
Vacuum Heat Treat Furnace with Ceramic Fiber Liner
Vacuum furnace with polycrystalline ceramic fiber insulation liner for excellent heat insulation and uniform temperature field. Choose from 1200℃ or 1700℃ max. working temperature with high vacuum performance and precise temperature control.
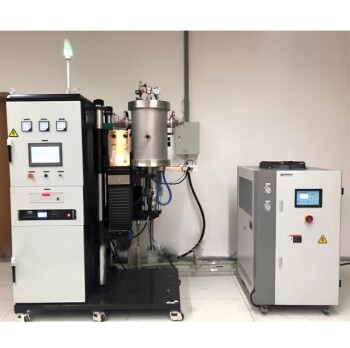
Vacuum Heat Treat and Molybdenum Wire Sintering Furnace for Vacuum Sintering
A vacuum molybdenum wire sintering furnace is a vertical or bedroom structure, which is suitable for withdrawal, brazing, sintering and degassing of metal materials under high vacuum and high temperature conditions. It is also suitable for dehydroxylation treatment of quartz materials.
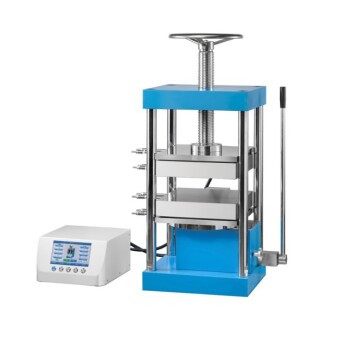
Heated Hydraulic Press Machine with Heated Plates Split Manual Laboratory Hot Press
Efficiently prepare your samples with our Split Manual Heated Lab Press. With a pressure range up to 40T and heating plates up to 300°C, it's perfect for various industries.
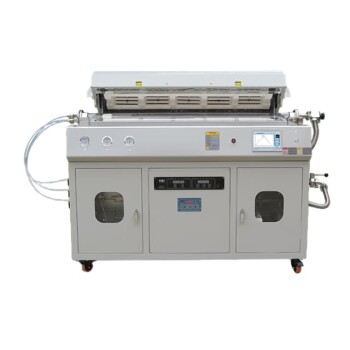
Multi Heating Zones CVD Tube Furnace Machine Chemical Vapor Deposition Chamber System Equipment
KT-CTF14 Multi Heating Zones CVD Furnace - Precise Temperature Control and Gas Flow for Advanced Applications. Max temp up to 1200℃, 4 channels MFC mass flow meter, and 7" TFT touch screen controller.
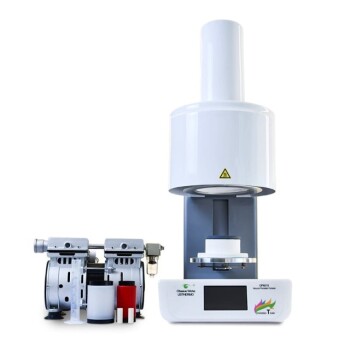
Dental Porcelain Zirconia Sintering Ceramic Vacuum Press Furnace
Get precise dental results with Dental Vacuum Press Furnace. Automatic temperature calibration, low noise tray, and touch screen operation. Order now!
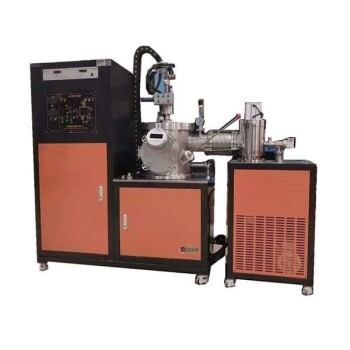
Vacuum Arc Induction Melting Furnace
Discover the power of Vacuum Arc Furnace for melting active & refractory metals. High-speed, remarkable degassing effect, and free of contamination. Learn more now!
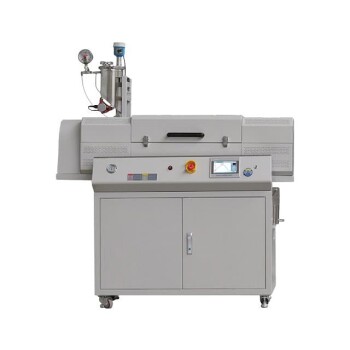
Laboratory Vacuum Tilt Rotary Tube Furnace Rotating Tube Furnace
Discover the versatility of Laboratory Rotary Furnace: Ideal for calcination, drying, sintering, and high-temperature reactions. Adjustable rotating and tilting functions for optimal heating. Suitable for vacuum and controlled atmosphere environments. Learn more now!
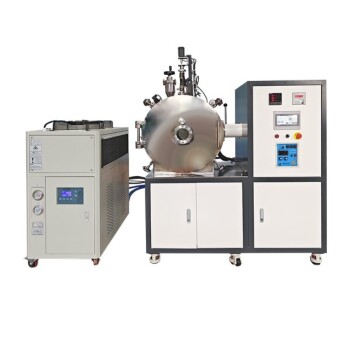
Lab-Scale Vacuum Induction Melting Furnace
Get precise alloy composition with our Vacuum Induction Melting Furnace. Ideal for aerospace, nuclear energy, and electronic industries. Order now for effective smelting and casting of metals and alloys.
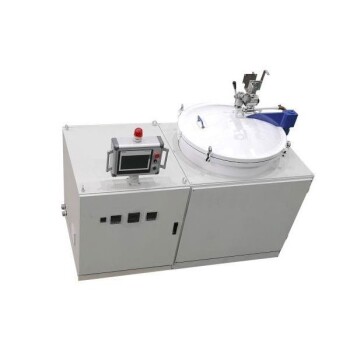
Graphite Vacuum Furnace IGBT Experimental Graphitization Furnace
IGBT experimental graphitization furnace, a tailored solution for universities and research institutions, with high heating efficiency, user-friendliness, and precise temperature control.
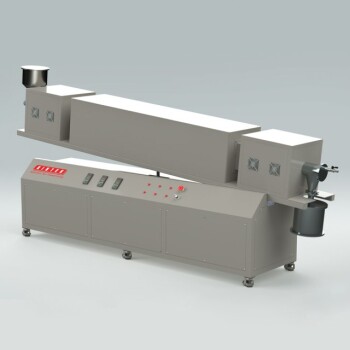
Vacuum Sealed Continuous Working Rotary Tube Furnace Rotating Tube Furnace
Experience efficient material processing with our vacuum-sealed rotary tube furnace. Perfect for experiments or industrial production, equipped with optional features for controlled feeding and optimized results. Order now.
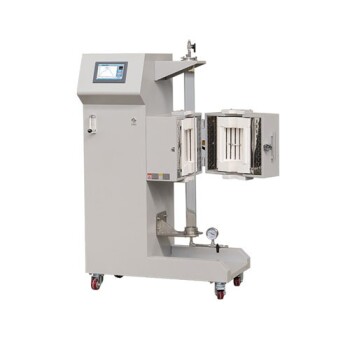
Vertical Laboratory Quartz Tube Furnace Tubular Furnace
Elevate your experiments with our Vertical Tube Furnace. Versatile design allows for operation under various environments and heat treatment applications. Order now for precise results!
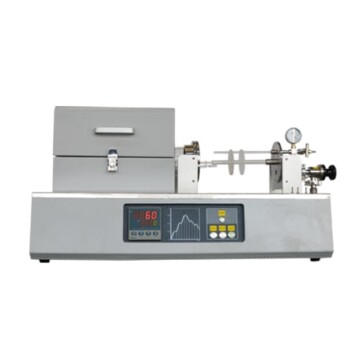
Laboratory Quartz Tube Furnace Tubular RTP Heating Furnace
Get lightning-fast heating with our RTP Rapid Heating Tube Furnace. Designed for precise, high-speed heating and cooling with convenient sliding rail and TFT touch screen controller. Order now for ideal thermal processing!
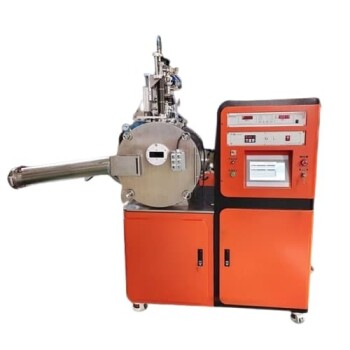
Vacuum Induction Melting Spinning System Arc Melting Furnace
Develop metastable materials with ease using our Vacuum Melt Spinning System. Ideal for research and experimental work with amorphous and microcrystalline materials. Order now for effective results.
Electric Rotary Kiln Continuous Working Small Rotary Furnace Heating Pyrolysis Plant
Efficiently calcine and dry bulk powder and lump fluid materials with an electric heating rotary furnace. Ideal for processing lithium ion battery materials and more.
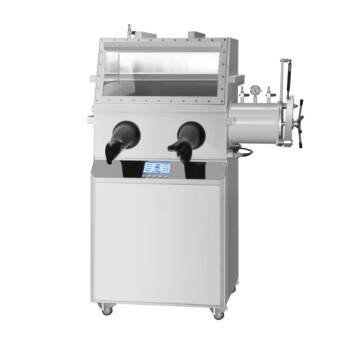
Laboratory Hydraulic Press Lab Pellet Press Machine for Glove Box
Controlled environment lab press machine for glove box. Specialized equipment for material pressing and shaping with high precision digital pressure gauge.
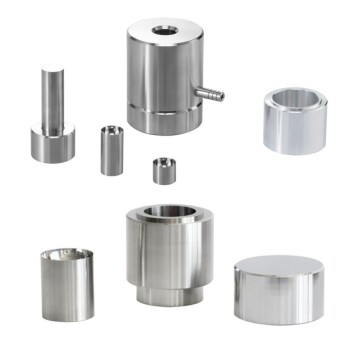
Explore versatile Hydraulic Hot Press molds for precise compression molding. Ideal for creating various shapes and sizes with uniform stability.
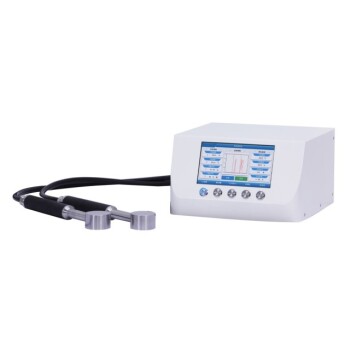
Infrared Heating Quantitative Flat Plate Press Mold
Discover advanced infrared heating solutions with high-density insulation and precise PID control for uniform thermal performance in various applications.
Related Articles
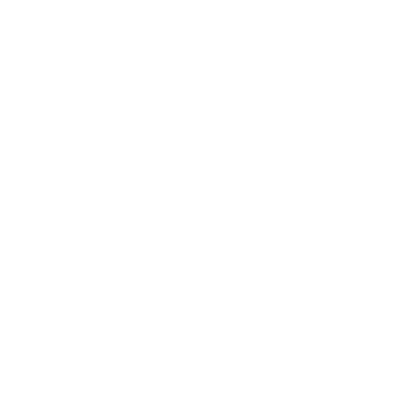
Comprehensive Guide to Vacuum Hot Press Furnace Application
The Vacuum Hot Press Furnace is a versatile tool especially suited for sintering experiments involving non-metallic materials, carbon composites, ceramic materials and metal powder materials.
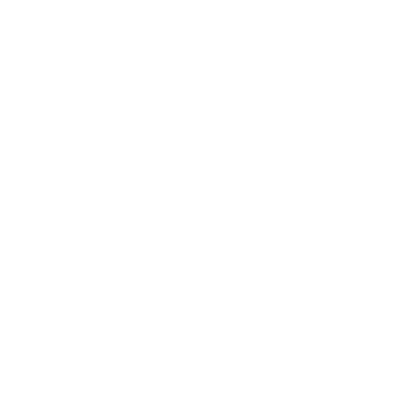
Vacuum Hot Press Furnace: A Comprehensive Guide
Gain in-depth knowledge of Vacuum Hot Press Furnaces, their components, benefits, and applications in various industries. Explore how these furnaces revolutionize material processing and achieve exceptional results.
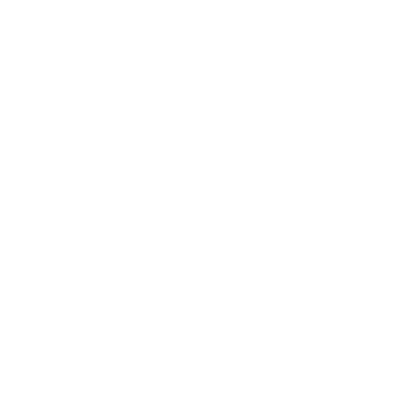
A Comprehensive Guide to Hot Press Machines: Functionality, Application, Features, Principles, Classification, and Technical Requirements
The hot Lab Press is a versatile and efficient tool used in material research, pharmacy, catalytic reactions, ceramics, and electronics. Its compact design allows for mobility in vacuum environments, making it ideal for research labs. Additionally, it can perform hot pressing functions, adding to its versatility in sample preparation.
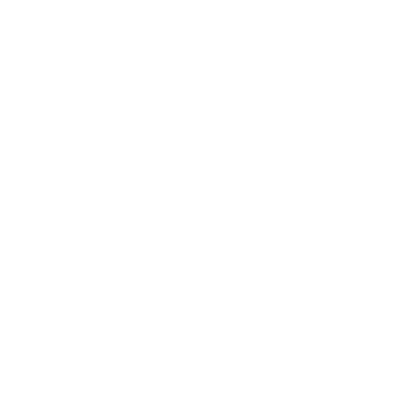
Unveiling the World of Heated Lab Presses: A Comprehensive Guide
Discover the versatility of heated lab presses in various applications, from sample preparation to material testing. Explore key factors to consider when purchasing a lab press, including pressure, temperature, platen size, and control options.
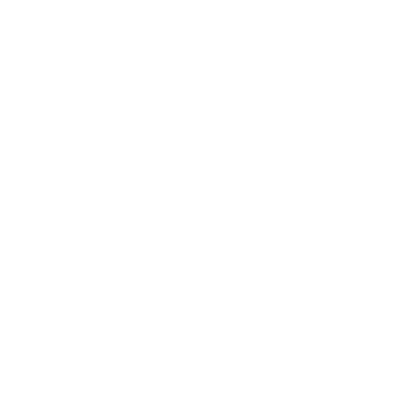
WIP – Warm Isostatic Press Equipment: Design, Features, and Benefits
KinTek specializes in designing and building Warm Isostatic Presses (WIP) for various applications. These systems can be either gas or liquid pressurized and are commonly used for plastics and laminated products. WIPs are custom-built to accommodate different pressure levels, ranging from low pressure to extreme pressures.
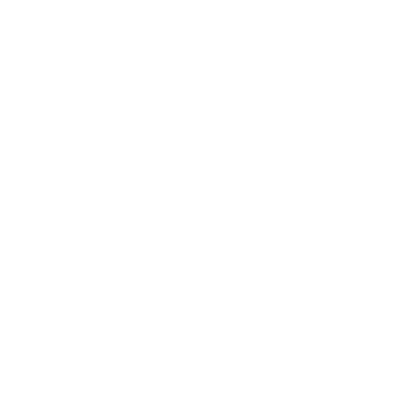
Comprehensive Guide to Heat Press Machines
A heat press is a machine designed to imprint a design or graphic on a substrate, such as a t-shirt, using heat and pressure for a specific duration. It is not limited to fabric applications; specialized heat presses can also imprint designs on mugs, plates, jigsaw puzzles, caps, and other products. Essentially, a heat press heats and presses materials, making it a valuable and versatile tool for any printing business.
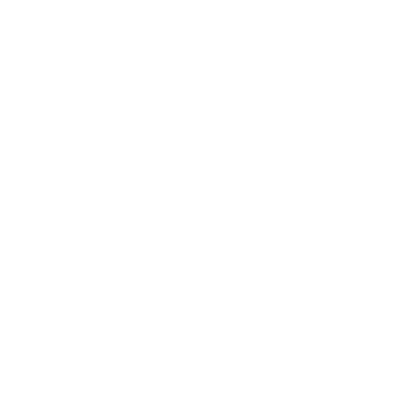
Comprehensive Guide to Hydraulic Hot Press: Function, Features and Applications
Hydraulic hot press is equipped with advanced electronic controls that allow for precise temperature selection and technical control. This enables the machine to automatically carry out processes such as stage temperature adjustment and film pressure control.
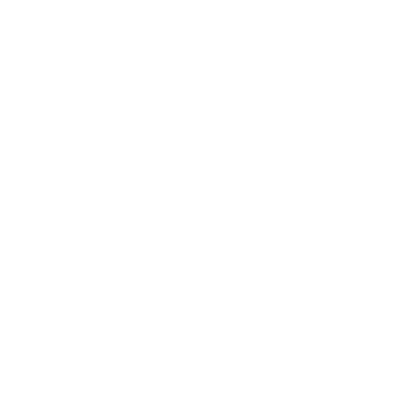
Comprehensive Overview of Warm Isostatic Press and Its Applications
Warm isostatic pressing (WIP) is a variant of cold isostatic pressing (CIP) that includes a heating element. It employs warm water or a similar medium to apply uniform pressure to powdered products from all directions. WIP is a cutting-edge technology that enables isostatic pressing at a temperature that does not exceed the boiling point of the liquid medium.
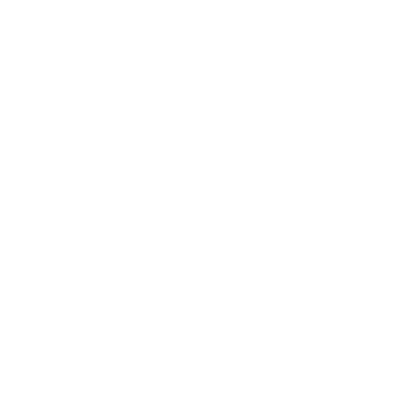
Comprehensive Guide to Heat Press Machine and Essential Supplies
Many people are familiar with using iron-on logos or graphics to customize apparel and other products. While iron-ons can be effective, using a heat press offers more consistent heat and pressure, resulting in higher-quality results. Heat presses also allow you to use transfer products that require higher temperatures and pressures than what can be achieved with an iron.
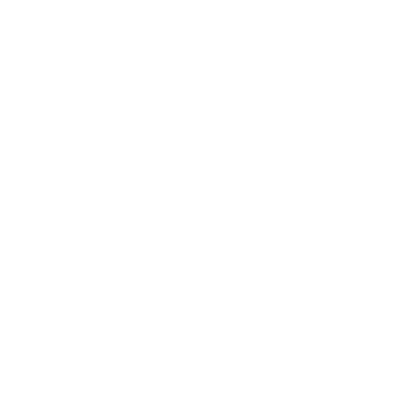
Comprehensive Overview of Cold Isostatic Pressing Services
Cold Isostatic Pressing (CIP) services play a crucial role in various industries, providing solutions for sterilization and compacting powders. These services offer a wide range of capabilities, ensuring the highest quality and efficiency.
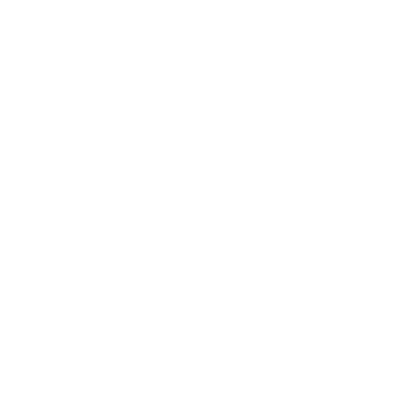
Isostatic Pressing A Low Distortion Alternative to Extrusion
Isostatic pressing is a manufacturing process that uses high pressure to compress powdered materials into a specific shape or form.
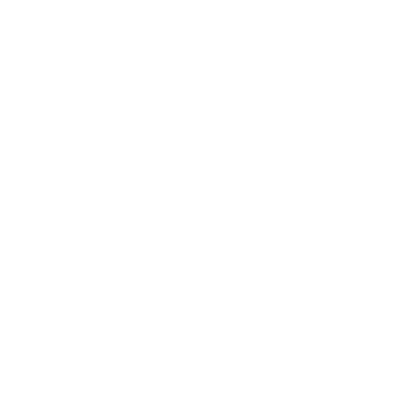
A Comprehensive Guide to Vacuum Coating: Enhancing Performance and Aesthetics
Discover the world of vacuum coating, a process that creates protective and aesthetic layers on metal and plastic surfaces. Explore its types, uses, and benefits, including enhanced performance, extended lifespan, and improved aesthetics.