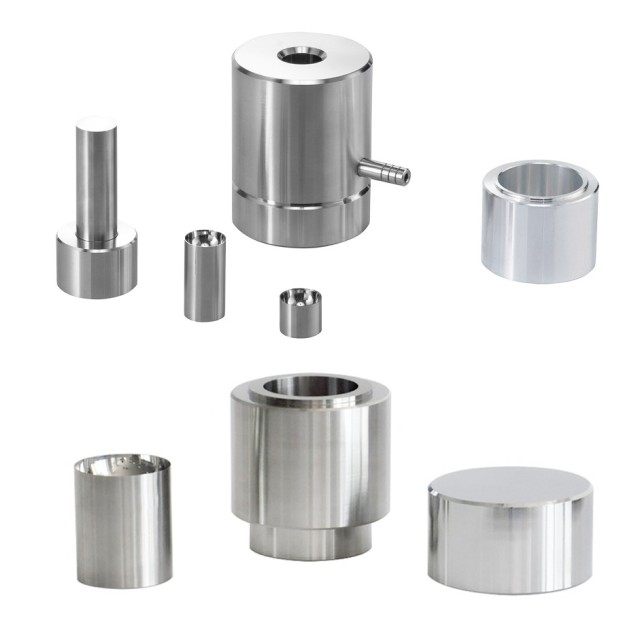
Molds & Accessories
Ball Press Mold for Lab
Item Number : PMQ
Price varies based on specs and customizations
- Die heating
- Alloy tool steel :Cr12MoV
- Indenter hardness
- HRC60-HRC62
- Sample size
- Φ6-Φ50 mm (M)
- Cavity depth
- 40mm (N)-60mm (N)
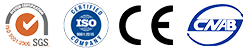
Shipping:
Contact us to get shipping details Enjoy On-time Dispatch Guarantee.
Why Choose Us
Reliable PartnerEasy ordering process, quality products, and dedicated support for your business success.
Introduction
Ball press molds are specialized tools used in high-pressure applications to shape metal powders into various forms such as round, square, or hexagonal shapes. These molds are often used in conjunction with large tonnage machines to achieve the necessary pressure for molding large cross-sectional areas. The process involves electric heating of the mold and the use of hydraulic systems to control pressure and ensure uniform compression of the powder. This technique is crucial in industries requiring precise and durable metal components, enhancing mechanical bonding and structural integrity.
Applications
Ball press molds are versatile tools used in various industries for the compaction and shaping of materials under high pressure. These molds are particularly essential in powder metallurgy, ceramic production, and rubber processing, where precise shaping and high-density products are required. The ability to produce different shapes and sizes, coupled with the option for electric heating, makes ball press molds a critical component in advanced manufacturing processes.
- Powder Metallurgy: Used for compacting metal powders into desired shapes before sintering, ensuring high density and strength in the final product.
- Ceramic Manufacturing: Essential for creating intricate ceramic pieces with uniform density, suitable for high-performance applications like insulators and advanced ceramics.
- Rubber Processing: Employed in the production of rubber products through hydraulic vulcanization, ensuring uniform heating and shaping of rubber materials.
- Pharmaceutical Industry: Used for tablet manufacturing, where precise pressure and shape are crucial for dosage accuracy and product integrity.
- Advanced Materials Research: Involved in the development of new materials and composites, where controlled pressure and shape are necessary for research and prototyping.
Detail & Parts
![Spherical mold [Φ3-40mm]](https://image.kindle-tech.com/images/products/580/8b618dc02c68e0cf9573dbc49162049067bd63aae503f.jpg)
![Spherical mold [Φ41-80mm]](https://image.kindle-tech.com/images/products/580/4def416915ba85927e8a1efd9d3e24a267bd63d41ae8c.jpg)
Technical specifications
Instrument model | PMQ | |
---|---|---|
Sample shape | ![]() |
|
Die heating | Alloy tool steel :Cr12MoV | |
Indenter hardness | HRC60-HRC62 | |
Sample size | Φ6、Φ8、Φ10、Φ15、Φ20mm (M) | Φ30、Φ40、Φ50 mm (M) |
Cavity depth | 40mm (N) | 60 mm (N) |
Dimensions | Φ53*120mm (L*H) | Φ88*150 mm (L*H) |
Weight | 1.4kg | 5.8kg |
Diagram of hydraulic powder press size | ![]() |
![]() |
Features
The ball press mold feature offers a versatile and efficient method for achieving high compact densities in metal and ceramic powder compaction. This process is particularly beneficial for producing intricate shapes and high-quality parts with uniform pressure and enhanced density. Here are the key features and their benefits:
-
Versatile Shapes and Sizes: The ball press mold allows for the production of various shapes including round, square, rectangular, circular, hexagonal, and flat shapes. This versatility is crucial for industries requiring diverse part geometries.
-
High and Uniform Pressure: The isostatic pressing process ensures high and uniform pressure distribution, eliminating die wall friction. This results in higher compact densities and improved part quality.
-
Precision Dimensions: The inner diameter of pressed shapes achieves higher precision compared to the outer diameter, making it ideal for applications requiring tight dimensional tolerances.
-
Efficient Production: The dry bag isostatic pressing method simplifies the production process by integrating rubber tooling into the apparatus, reducing the need for separate immersion and removal steps. This leads to faster production rates and ease in automation.
-
Heat Integration: The hydraulic hot press rubber process incorporates heat to facilitate the flow of stock and fill the mold cavity, ensuring complete filling and reducing defects such as flow lines and blisters.
-
Large Tonnage Capability: The large tonnage machine is suitable for molding large cross-sectional areas and requires greater pressure, making it adaptable to various industrial needs.
-
Energy Storage and Control: The circuit principle of the ball press mold involves storing energy through high-pressure oil, allowing for precise control and immediate unloading when needed, enhancing operational efficiency.
These features collectively make the ball press mold an essential tool for industries seeking high-quality, precise, and versatile powder compaction solutions.
Operation steps
The spherical mold is used in the pharmaceutical industry and small batch testing.
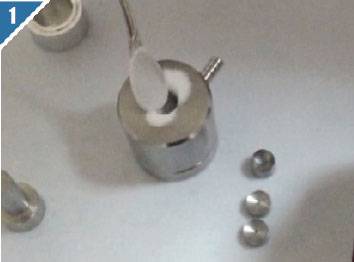
1.Assemble the die according to the operation diagram and install the sample in the cavity.
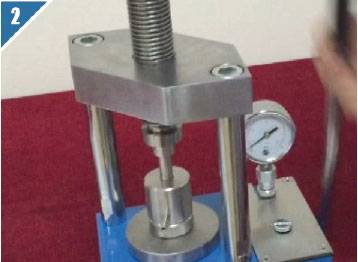
2.Put the die in the center of the hydraulic press and pressurize to required pressure.
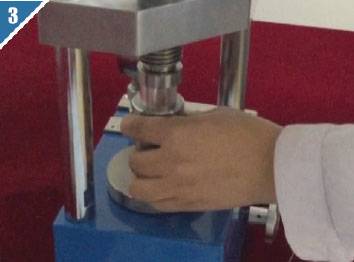
3.Assemble the die according to the release diagram ,eject the sample out of the die bushing with the screw rod.
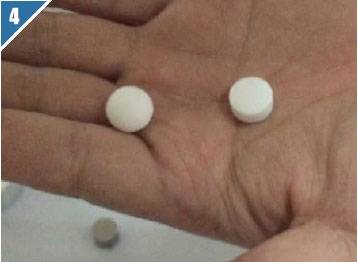
4.Take out the die from the hydraulic press , and remove the sample gently.
FAQ
What Is A Lab Press?
What Is The Purpose Of A Hydraulic Press In Lab?
What Are Different Type Of Lab Presses?
4.7
out of
5
Exceptional quality and durability, perfect for our lab's needs.
4.8
out of
5
Fast delivery and excellent value for money, highly recommend!
4.9
out of
5
Technologically advanced, makes our pressing process much smoother.
4.7
out of
5
Durable and efficient, saves us time and resources.
4.8
out of
5
Great product, enhances our lab's productivity significantly.
4.9
out of
5
Impressive technology, very satisfied with the results.
4.7
out of
5
Reliable and high-quality, exactly what we needed.
4.8
out of
5
Quick delivery and top-notch quality, very pleased.
4.9
out of
5
Advanced features make our work more efficient, highly recommend.
4.7
out of
5
Durable and user-friendly, perfect for our lab setup.
4.8
out of
5
Excellent value, enhances our pressing process tremendously.
4.9
out of
5
Highly advanced and reliable, very satisfied with our purchase.
4.7
out of
5
Fast and efficient, exactly what our lab needed.
REQUEST A QUOTE
Our professional team will reply to you within one business day. Please feel free to contact us!
Related Products

Special Shape Press Mold for Lab
Discover high-pressure special shape press molds for diverse applications, from ceramics to automotive parts. Ideal for precise, efficient molding of various shapes and sizes.
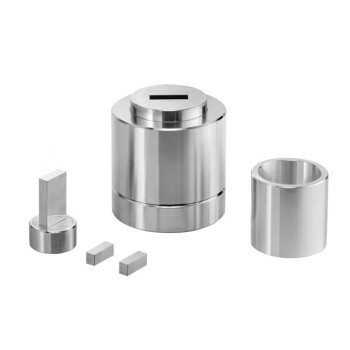
Assemble Square Lab Press Mold for Laboratory Applications
Achieve perfect sample preparation with Assemble Square Lab Press Mold. Quick disassembly eliminates sample deformation. Perfect for battery, cement, ceramics, and more. Customizable sizes available.
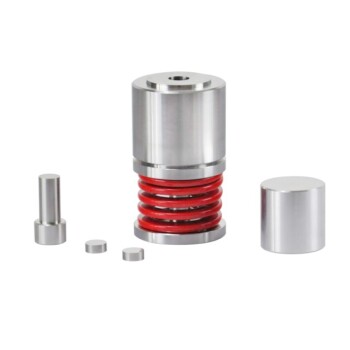
Round Bidirectional Press Mold for Lab
The round bidirectional press mold is a specialized tool used in high-pressure molding processes, particularly for creating intricate shapes from metal powders.
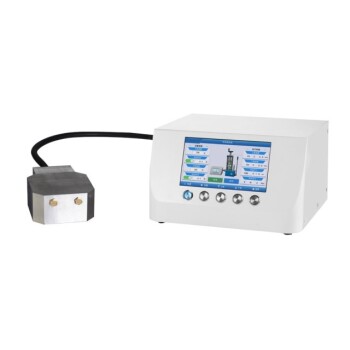
Double Plate Heating Press Mold for Lab
Discover precision in heating with our Double Plate Heating Mold, featuring high-quality steel and uniform temperature control for efficient lab processes. Ideal for various thermal applications.
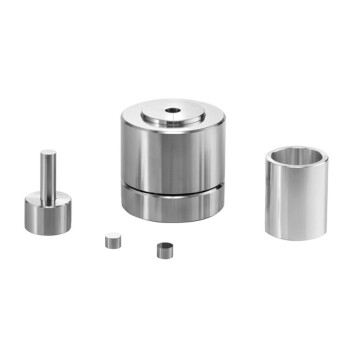
Assemble Lab Cylindrical Press Mold
Get reliable and precise molding with Assemble Lab Cylindrical Press Mold. Perfect for ultra-fine powder or delicate samples, widely used in material research and development.
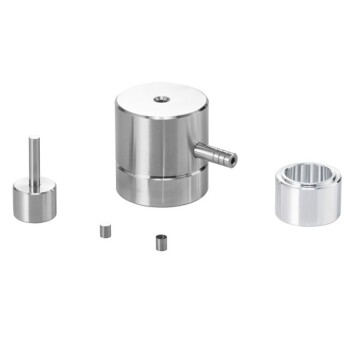
Cylindrical Press Mold for Lab Applications
Efficiently form and test most samples with Cylindrical Press Molds in a range of sizes. Made of Japanese high-speed steel, with long service life and customizable sizes.
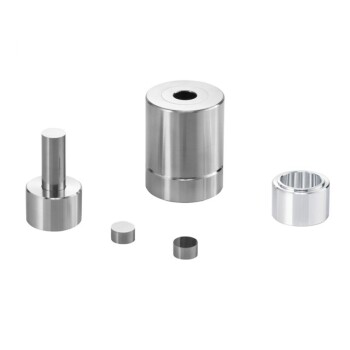
Carbide Lab Press Mold for Laboratory Applications
Form ultra-hard samples with Carbide Lab Press Mold. Made of Japanese high-speed steel, it has a long service life. Custom sizes available.
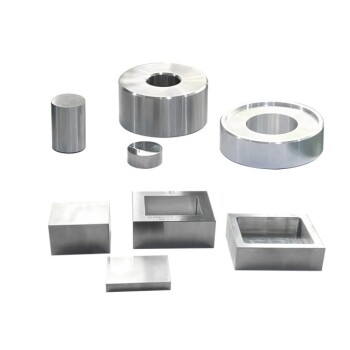
Special Heat Press Mold for Lab Use
Square, round and flat plate forming dies for hot presses.
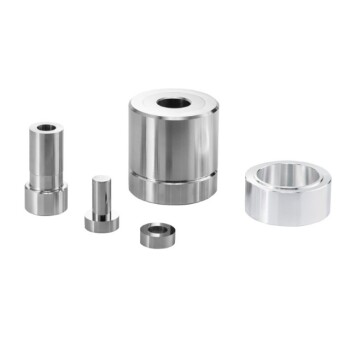
Ring Press Mold for Lab Applications
Ring Press Dies, also known as Circular Pellet Press Die Sets, are integral components in various industrial and laboratory processes.
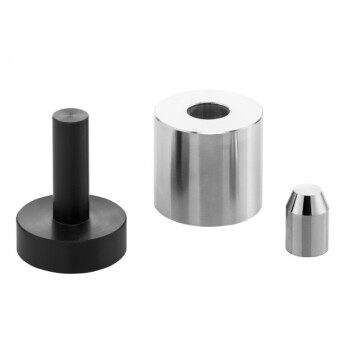
Button Battery Tablet Press Sealing Mold for Lab Use
The sealing die is essential for assembling button batteries, ensuring components like the anode, cathode, and electrolyte are securely enclosed.
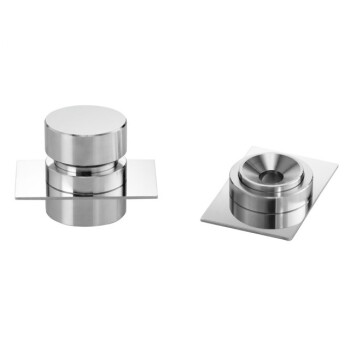
No Demolding Lab Infrared Press Mold for Laboratory Applications
Effortlessly test your samples with no demolding required using our lab infrared press mold. Enjoy high transmittance and customizable sizes for your convenience.
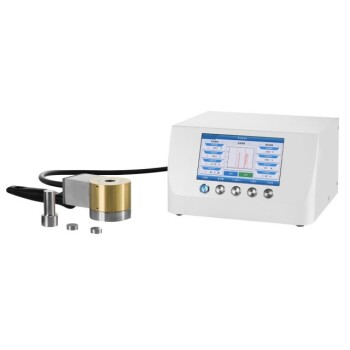
Cylindrical Lab Electric Heating Press Mold for Laboratory Applications
Efficiently prepare samples with Cylindrical Lab Electric Heating Press Mold. Fast heating, high temp & easy operation. Custom sizes available. Perfect for battery, ceramic & biochemical research.
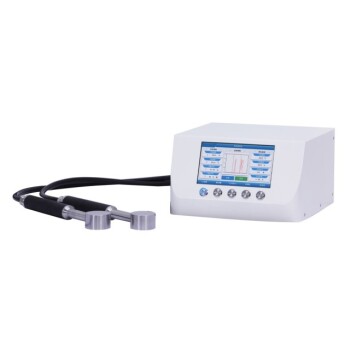
Infrared Heating Quantitative Flat Plate Press Mold
Discover advanced infrared heating solutions with high-density insulation and precise PID control for uniform thermal performance in various applications.
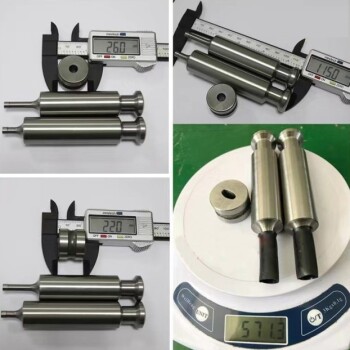
Multi-Punch Rotary Tablet Press Mold Ring for Rotating Oval and Square Molds
The multi-punch rotary tablet press mold stands as a pivotal component in pharmaceutical and manufacturing industries, revolutionizing the process of tablet production. This intricate mold system comprises multiple punches and dies arranged in a circular fashion, facilitating rapid and efficient tablet formation.
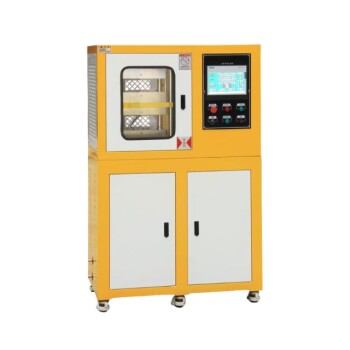
Rubber Vulcanizer Vulcanizing Machine Plate Vulcanizing Press for Lab
The Plate vulcanizing press is a kind of equipment used in the production of rubber products, mainly used for the vulcanization of rubber products. Vulcanization is a key step in rubber processing.
Related Articles
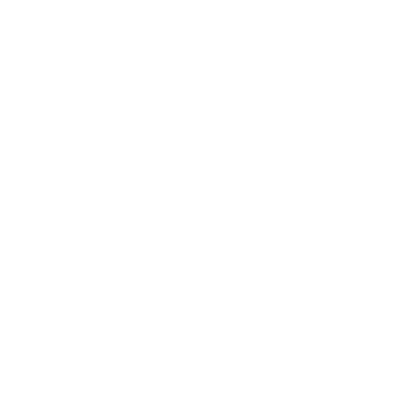
Comprehensive Guide to Metal Mold Pressing: Techniques, Equipment, and Applications
Explore the detailed process of metal mold pressing, including equipment, techniques, and applications. Learn how hydraulic presses shape materials like metal and rubber efficiently.
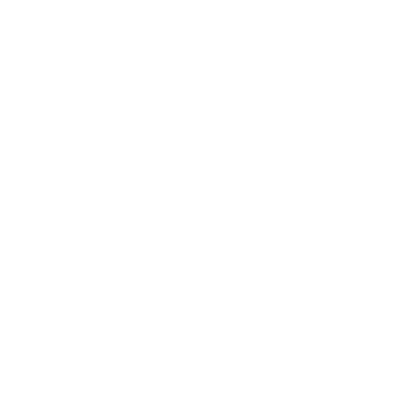
Manual Lab Hydraulic Pellet Press: Comprehensive Guide to High-Quality Pellet Preparation
Explore the detailed guide on using a Manual Lab Hydraulic Pellet Press for high-quality pellet preparation in spectral analyses. Learn about features, operation, and maintenance for optimal performance.
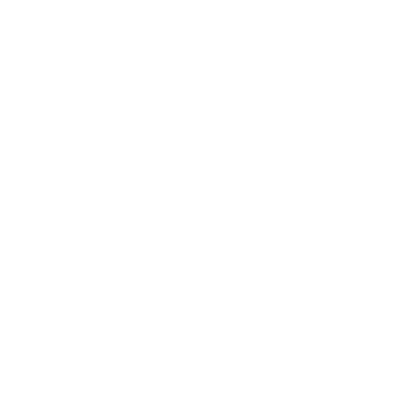
Infrared Press Mold Techniques for Non-Demolding Applications
Explore advanced infrared press mold techniques without demolding. Learn about the benefits, applications, and best practices for non-demolding lab processes.
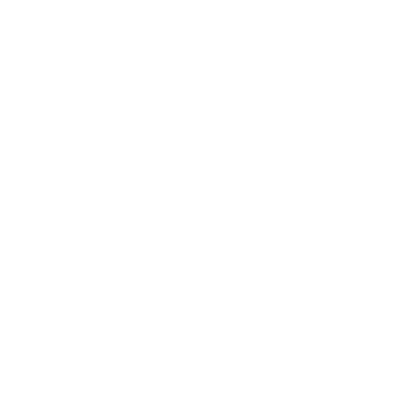
Manual Pellet Press: A Comprehensive Guide to Efficient Lab Pelletizing
Explore the intricacies of manual pellet presses, including operation, safety, and maintenance tips. Learn how to choose the right press, understand force gauges, and optimize pellet quality for your lab experiments.
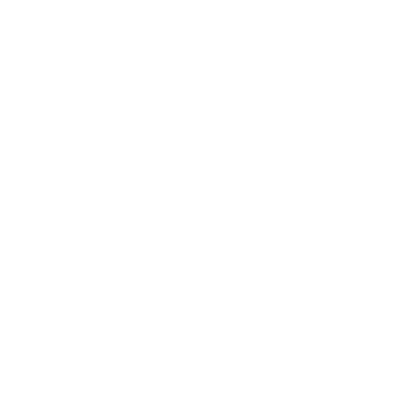
Hydraulic Tablet Press: Comprehensive Guide to Design, Operation, and Applications
Explore the advanced features, operational principles, and diverse applications of hydraulic tablet presses in various industries. Learn how these machines ensure high-quality tablet production with detailed insights.
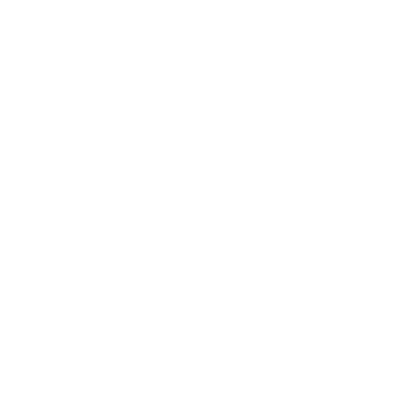
Infrared Heating Quantitative Flat Plate Mold: Design, Applications, and Benefits
Explore the advanced design and applications of infrared heating quantitative flat plate molds. Learn about their benefits in achieving uniform heat distribution and efficient processing.
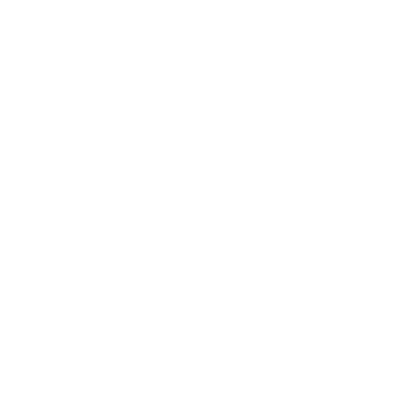
Comprehensive Guide to Cylindrical Lab Electric Heating Press Mold: Technology and Applications
Explore the advanced features and applications of cylindrical lab electric heating press molds. Learn about their working principles, types of heating technologies, and key benefits for precise sample preparation.
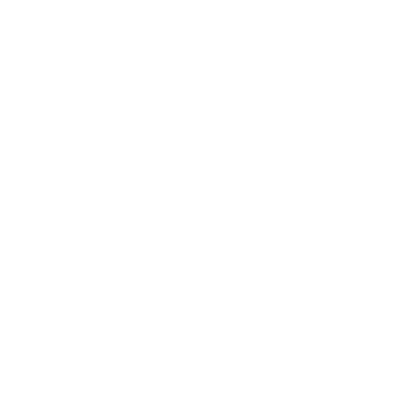
Manual Hydraulic Presses for Laboratory Use: A Comprehensive Guide
Explore the intricacies of manual hydraulic presses in labs, including operation, benefits, and comparison with automatic models. Ideal for those seeking detailed insights on sample preparation and cost-effectiveness.
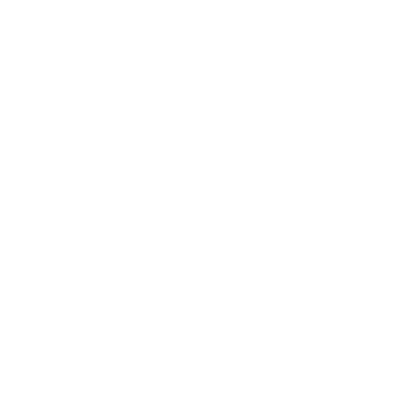
Defects and Solutions for Isostatically Pressed Ceramic Balls
This article discusses various defects in isostatically pressed ceramic balls and provides solution strategies for each type of defect.
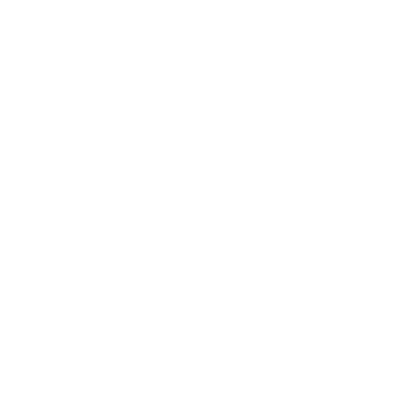
Ceramic Isostatic Pressing Mold Technology
Exploring the design and factors affecting ceramic isostatic pressing molds.
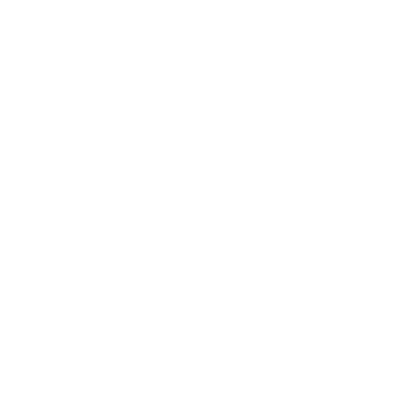
Issues with Poor Demoulding in Manual Tablet Presses
Analyzes the causes of poor demoulding in manual tablet presses, focusing on powder, mold, machine body, and operator factors.
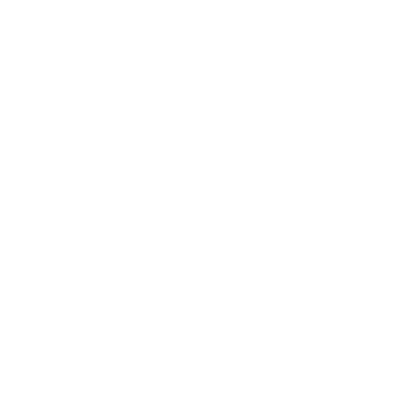
Nine Precision Molding Processes of Zirconia Ceramics
An overview of nine advanced molding processes for zirconia ceramics, including dry and wet methods.