Introduction to Metal Mold Pressing
Metal mold pressing stands as a cornerstone in industrial manufacturing, shaping materials with precision and efficiency. This comprehensive guide delves into the intricate world of metal mold pressing, exploring its fundamental principles, the diverse equipment utilized, and its extensive applications across various sectors. From the basic mechanics of operation to the sophisticated machinery involved, we will unravel the step-by-step process, material considerations, and the critical aspects of quality control. Join us as we navigate through the advantages, challenges, and future trends of this pivotal manufacturing technique.
Types of Metal Mold Pressing Equipment
Metal mold pressing is a critical process in the manufacturing industry, particularly in the production of intricate metal components. This method involves the compression of metal powders within a confined space defined by a metal mold and punches. The equipment used for this process is diverse, ranging from single-acting to double-acting presses, each tailored to specific applications and production needs.
Single-Acting Presses
Single-acting presses are fundamental in metal mold pressing. In this setup, the powder is filled into a cavity formed by the metal mold and a fixed lower punch. The compression is achieved by moving the upper punch downwards, thereby reducing the volume of the cavity and compacting the powder into a solid form. This method is straightforward and commonly used for simple shapes where uniform density is not critical. However, due to the friction between the powder and the mold walls, the resulting density can vary, with the lower part of the molded body typically having a lower density than the upper part.
Double-Acting Presses
Double-acting presses offer a more sophisticated approach to metal mold pressing. Unlike single-acting presses, double-acting presses use two separate mechanisms to control both the upper and lower punches. This dual action allows for more precise control over the compression process, enabling the production of parts with more uniform density and complex geometries. The initial compression is often facilitated by the lower punch, pushing the powder upwards, followed by the upper punch compressing from above. This method is particularly beneficial for applications requiring high precision and uniform density, such as in the aerospace and automotive industries.
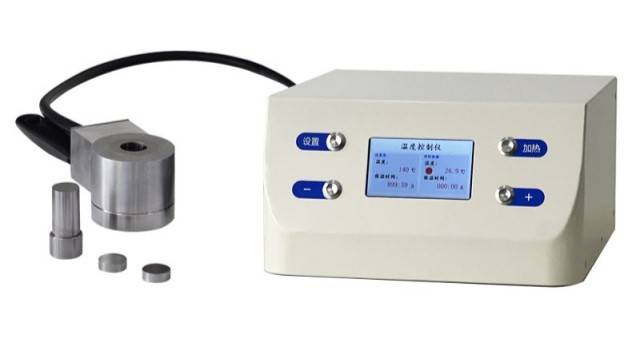
Cylindrical Lab electric heating Press Mold
Hydraulic Presses
Hydraulic presses are versatile and widely used in metal mold pressing due to their ability to generate high compressive forces. These presses operate by using hydraulic fluid to amplify the force applied by a small piston, which is then transferred to the metal mold. Hydraulic presses can be designed to accommodate various sizes and shapes of molds, making them suitable for a wide range of applications. They are also capable of maintaining consistent pressure throughout the pressing cycle, ensuring uniform compaction of the metal powder.
Mechanical Presses
Mechanical presses operate on a different principle, utilizing a flywheel to store energy and release it during the pressing cycle. This type of press is known for its high speed and efficiency, making it ideal for high-volume production environments. Mechanical presses are typically used for simpler pressing tasks where the consistency of the pressing force is less critical.
Hot Pressing Equipment
Hot pressing equipment introduces an additional element of heat to the pressing process. By heating the mold and punches, these machines facilitate the compaction of metal powders at elevated temperatures. This method is particularly useful in powder metallurgy, where the sintering process is enhanced by the application of heat. Hot pressing can result in denser and stronger metal components, making it essential for applications requiring high mechanical integrity.
Applications of Metal Mold Pressing Equipment
The applications of metal mold pressing equipment are extensive and span various industries. In the automotive sector, these presses are used to manufacture engine parts, transmission components, and structural elements. In the aerospace industry, they are crucial for producing lightweight yet strong components for aircraft structures. Additionally, metal mold pressing is employed in the production of household appliances, hardware tools, and many other products where precision metal components are required.
In conclusion, metal mold pressing equipment is a cornerstone of modern manufacturing, offering a versatile and efficient means of producing high-quality metal components. The choice of press type—whether single-acting, double-acting, hydraulic, mechanical, or hot pressing—depends on the specific requirements of the application, including the desired part geometry, density, and production volume. Each type of press brings its unique advantages to the pressing process, ensuring that manufacturers can meet the diverse needs of their customers.
Process of Metal Mold Pressing
Metal mold pressing is a critical process in the manufacturing of various metal components, involving several meticulous steps from powder filling to the final removal of the molded body. This process leverages the precision of punches and dies to shape metal powders into intricate forms, ensuring uniformity and structural integrity.
Powder Preparation and Filling
The initial step in metal mold pressing involves the preparation of the metal powder. This typically includes blending the metal powder with a matrix material to enhance its properties. The mixture is then meticulously poured into a mold within the press. The mold is designed to replicate the exact shape of the desired final product, ensuring that the powder fills every crevice and corner.
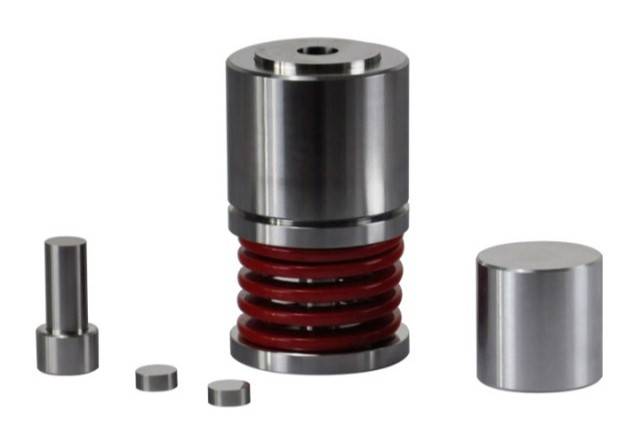
Round bidirectional press mold
Application of Pressure
Once the mold is filled, the pressing process begins. The press applies a significant amount of force to the powder mixture, causing it to compact and conform to the shape of the mold. This phase is crucial as it determines the density and structural integrity of the final product. The use of punches and dies in this process is essential. The upper punch, often referred to as the ejector, and the lower punch, or the core, work in tandem to apply uniform pressure from both ends, ensuring that the metal powder is compressed evenly.
Removal and Post-Processing
After the pressure is released and the metal has taken its shape, the molded body is carefully removed from the mold. This step requires precision to avoid any damage to the delicate structure of the newly formed metal piece. Post-pressing processes such as heat treatment are often employed to enhance the mechanical properties of the metal, including its strength, hardness, and durability.
Types of Presses and Their Applications
Metal mold pressing can be executed using different types of presses, each designed for specific applications and outcomes. For instance, double-acting hydraulic presses are commonly used due to their ability to apply pressure from both the top and bottom, ensuring a more uniform compression. Monostatic isostatic presses, with their single-cavity structures, are ideal for smaller, more precise components, while densomatic isostatic presses, featuring multi-cavity designs, are suited for high-volume production where multiple pieces can be pressed simultaneously.
Industrial Automation and Quality Control
In industrial settings, metal mold pressing is often integrated with a series of automated processes that streamline operations from powder filling to the final removal of the molded body. This automation not only increases efficiency but also enhances the consistency and quality of the final products. Quality control measures are rigorously applied throughout the process to ensure that each component meets the specified standards, including dimensional accuracy and material integrity.
Conclusion
The process of metal mold pressing is a testament to the precision and control achievable in modern manufacturing. By meticulously controlling each step from powder preparation to the final product, manufacturers can produce high-quality metal components that meet the stringent requirements of various industries. The use of advanced presses and automation further ensures that this process is both efficient and reliable, making it a cornerstone in the production of metal goods across the globe.
Applications of Metal Mold Pressing
Metal mold pressing technology has revolutionized the manufacturing sector, enabling the production of high-quality, complex parts across various industries. This process involves the compression of metal powders within a mold to create parts with precise dimensions and properties. The versatility and efficiency of metal mold pressing have made it indispensable in sectors such as automotive, aerospace, and consumer goods.
Automotive Industry
In the automotive sector, metal mold pressing is pivotal for manufacturing lightweight and durable components. The technology supports the production of intricate parts that are critical for modern vehicle designs, enhancing both performance and fuel efficiency. According to industry reports, the adoption of metal mold pressing in automotive manufacturing has led to a significant reduction in part weight, contributing to overall vehicle weight reduction and improved fuel economy. For instance, components like gears, sprockets, and structural parts are commonly produced using this method, showcasing its role in advancing automotive engineering.
Aerospace Industry
The aerospace industry benefits immensely from metal mold pressing due to its ability to produce high-strength, lightweight components. These components are crucial for aircraft structures, engines, and landing gear, where reliability and performance are paramount. The precision and consistency offered by metal mold pressing ensure that aerospace parts can withstand extreme conditions and high stress levels. Recent advancements in the technology have also enabled the production of parts with reduced material usage, further enhancing cost-effectiveness and sustainability in aerospace manufacturing.
Consumer Goods
Beyond heavy industries, metal mold pressing finds extensive application in the production of consumer goods. From household appliances to electronic devices, the technology is used to manufacture parts that require high precision and durability. The ability to produce complex geometries with minimal material waste makes metal mold pressing an economical choice for consumer goods manufacturers. Additionally, the high throughput and repeatability of the process ensure consistent quality and reliability in consumer products.
Technological Advancements
The continuous evolution of metal mold pressing technology has led to the development of advanced systems that enhance productivity and part quality. Modern presses incorporate sophisticated controls and automation, allowing for precise control over pressing parameters such as pressure, temperature, and time. These advancements have enabled the production of parts with superior mechanical properties and tighter dimensional tolerances. Furthermore, the integration of digital technologies like IoT and AI in metal mold pressing equipment has paved the way for predictive maintenance and real-time process optimization, further boosting efficiency and reducing downtime.
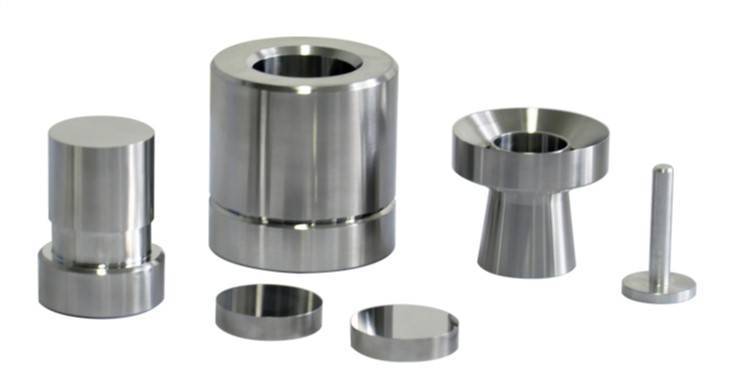
XRF Boric Acid lab Powder Pellet Pressing Mold
Environmental Impact
Sustainability is a growing concern across all industries, and metal mold pressing offers several advantages in this regard. The process minimizes material waste and energy consumption compared to traditional manufacturing methods. Additionally, the recyclability of metal powders used in pressing contributes to a circular economy, where materials are reused and repurposed effectively. As industries increasingly focus on reducing their environmental footprint, metal mold pressing stands out as a sustainable manufacturing solution.
In conclusion, metal mold pressing technology plays a crucial role in modern manufacturing, offering unparalleled precision, efficiency, and sustainability. Its applications span across diverse industries, from automotive and aerospace to consumer goods, highlighting its versatility and importance. As technology continues to advance, the potential of metal mold pressing is set to expand even further, driving innovation and efficiency in manufacturing processes worldwide.
Material Considerations in Metal Mold Pressing
Metal mold pressing is a critical process in the manufacturing industry, particularly for creating intricate shapes from various materials. This process involves the compression of materials within a metal mold, which can be made from metals, plastics, composites, and other substances. Understanding the properties and behaviors of these materials under pressure is essential for achieving optimal results in metal mold pressing.
Types of Materials Used in Metal Mold Pressing
Metals: Metals are the most traditional and widely used materials in metal mold pressing. They offer excellent mechanical properties such as high strength, ductility, and thermal conductivity. Common metals used include steel, aluminum, and titanium. Each metal has its unique properties that influence the pressing process and the final product's characteristics. For instance, steel is known for its strength and durability, making it suitable for high-stress applications, while aluminum offers a lighter weight and better corrosion resistance.
Plastics: Plastics are increasingly used in metal mold pressing due to their versatility and cost-effectiveness. They can be engineered to have specific properties such as high impact resistance, thermal stability, and chemical resistance. Thermoplastics like polyethylene and polypropylene are commonly pressed using metal molds. The pressing process for plastics involves heating the material to its melting point, pressing it into the mold, and then cooling it to solidify the shape.
Composites: Composites are materials made from two or more constituent materials with significantly different physical or chemical properties. They are designed to have characteristics superior to those of the individual components. Common composites used in metal mold pressing include carbon fiber-reinforced polymers and metal matrix composites. These materials offer a combination of strength, light weight, and durability. The pressing process for composites often involves mixing the components, placing them in a mold, and applying high pressure and temperature to bond the materials together.
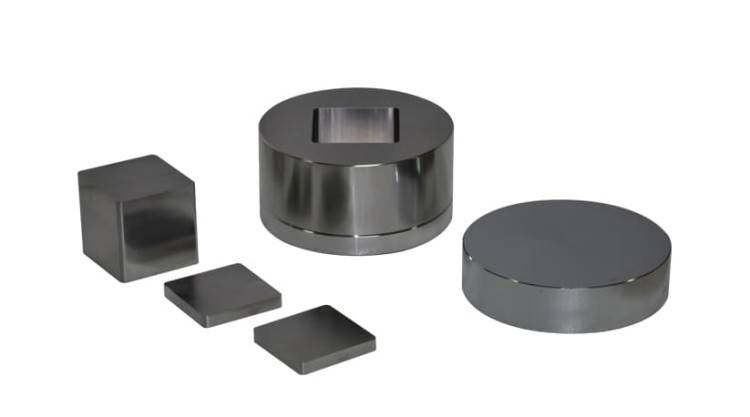
Properties of Materials in Metal Mold Pressing
The properties of materials play a crucial role in determining the success of the metal mold pressing process. Key properties to consider include:
- Density: The density of the material affects the pressure required for pressing and the final product's weight.
- Strength: The material's strength determines its ability to withstand forces during the pressing process and in the final application.
- Ductility: Ductility allows the material to deform under stress without fracturing, which is essential for complex shapes.
- Thermal Conductivity: This property is crucial for materials that require heating or cooling during the pressing process.
- Chemical Resistance: Materials used in corrosive environments must have high chemical resistance to ensure longevity.
Process Considerations
The metal mold pressing process involves several steps, including material preparation, pressing, and post-pressing treatments. The choice of material significantly influences these steps. For example, metals may require preheating to facilitate pressing, while plastics need precise temperature control to avoid degradation. Composites often involve complex mixing and curing processes to achieve the desired properties.
Conclusion
Selecting the appropriate material for metal mold pressing is a critical decision that impacts the quality, performance, and cost of the final product. By understanding the properties and behaviors of metals, plastics, and composites under pressure, manufacturers can optimize the pressing process and achieve superior results. Continuous research and development in material science are essential for advancing the capabilities of metal mold pressing and expanding its applications across various industries.
Quality Control and Testing in Metal Mold Pressing
Quality control is a critical aspect of metal mold pressing, ensuring that the final products meet the required standards of performance and durability. This process involves rigorous testing and meticulous monitoring of various stages of production. One of the key tools in this endeavor is the hydraulic press, which plays a significant role in material testing and sample preparation.
Material Testing with Hydraulic Presses
Hydraulic presses are indispensable in the analysis of material performance during manufacturing. They are used to test various properties of materials, such as blocking resistance, which measures a material's ability to resist adherence to itself under pressure. This is particularly important for materials that are stored in stacks or subjected to mechanical stress.
To conduct a blocking resistance test, a sample of the material is placed between two plates, and the pressure is gradually increased until the sample can no longer be displaced. This point, known as the 'blocking point', serves as an indicator of potential shape deformations during storage or use.
Sample Preparation for X-ray Fluorescence Spectroscopy (XRF)
In a laboratory setting, hydraulic presses are also utilized for sample preparation, particularly for X-ray fluorescence spectroscopy (XRF). XRF is a non-destructive analytical technique that quantifies the fluorescent X-rays emitted from a sample excited by a primary X-ray source. Hydraulic presses compress powder mixtures into pellets, which are then used for XRF analysis. This process requires precise control over the pressure and uniformity in pellet density, ensuring accurate and reliable analytical results.
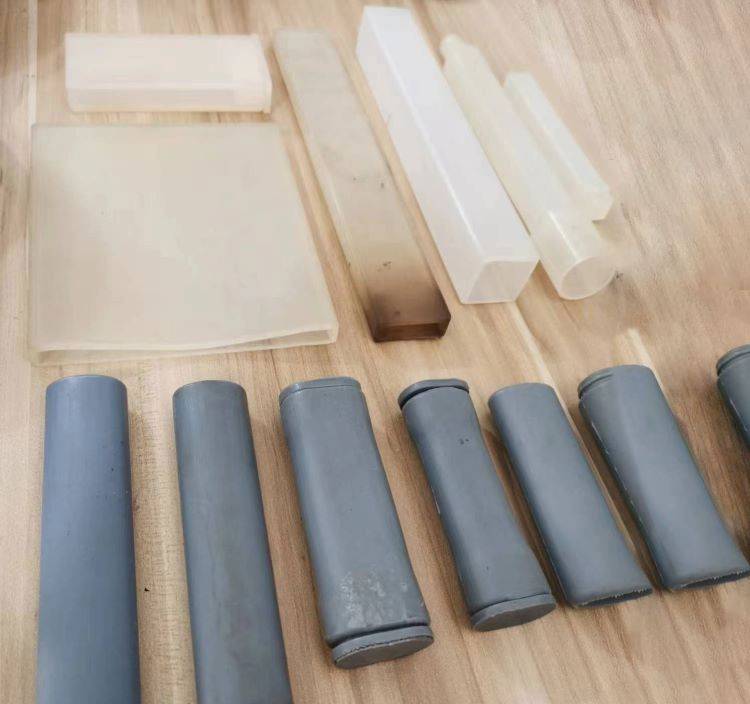
Metal Mold Pressing Process
Metal mold pressing is a method where powder materials are filled into a space enclosed by a metal mold and compressed by narrowing the distance between the upper and lower punches. This process is similar to cold isostatic pressing (CIP) but differs in the application of force and the mold's structure. Industrial metal mold pressing equipment automates the processes from powder filling to the removal of the molded body, enhancing efficiency and consistency.
In single-acting pressing, the lower punch remains fixed while the upper punch compresses the powder. This method can result in a density gradient within the molded body, with the lower part having a lower density than the upper part due to friction between the powder and the metal mold or punches, and among the powder particles themselves.
Quality Control in Metal Mold Pressing
Quality control in metal mold pressing involves several steps, starting with the blending of the desired metal powder with a matrix material. The mixture is then placed in a mold within the press, where force is applied to compact the mixture into the desired shape. Once the correct shape is achieved, the press is released, and the composite is removed from the mold. The final step involves heat treatment to enhance the composite's strength and other properties.
Hydraulic presses are also used to create test substances for material testing, providing insights into the material's performance during manufacturing. This testing is crucial for identifying any potential issues before mass production, ensuring that the final products meet the stringent quality standards required by the industry.
Conclusion
In conclusion, quality control and testing in metal mold pressing are essential for producing high-quality, durable products. Hydraulic presses play a pivotal role in this process, from material testing to sample preparation and the actual pressing of metal molds. By ensuring that each step of the process is meticulously monitored and controlled, manufacturers can guarantee the reliability and performance of their products, meeting the high expectations of their customers and the industry at large.
Advantages and Challenges of Metal Mold Pressing
Metal mold pressing technology offers a range of advantages and faces several challenges, particularly in terms of efficiency, cost-effectiveness, and the complexities involved in the process. This technology is closely related to compacting in powder metallurgy, where metal powders are compressed into a mold to form desired shapes.
Advantages of Metal Mold Pressing
-
Efficiency in Shape Formation: Metal mold pressing allows for the creation of complex shapes that are difficult to achieve through traditional sintering methods. This is particularly beneficial in industries where intricate designs are crucial, such as in the automotive and aerospace sectors.
-
Uniformity of Components: Unlike traditional powder metallurgy, where components can vary in density due to friction between the powder and tooling, metal mold pressing ensures a more uniform density throughout the component. This uniformity enhances the mechanical properties and reliability of the final product.
-
Scalability: While metal mold pressing can be more expensive for small parts, it becomes cost-effective for larger-scale production. The process can be automated, reducing labor costs and increasing throughput, making it suitable for mass production scenarios.
Challenges of Metal Mold Pressing
-
High Initial Costs: The setup for metal mold pressing involves significant initial investment in molds and pressing equipment. Molds can be costly and have a limited lifespan, which can be a deterrent for small-scale manufacturers or those producing low-volume products.
-
Technical Expertise Required: The process of metal mold pressing requires a high level of technical skill. Operators must carefully control parameters such as temperature, pressure, and the timing of heating and cooling cycles to avoid defects in the final product. This necessitates ongoing training and skilled labor, which can increase operational costs.
-
Size and Shape Limitations: Although metal mold pressing can handle complex shapes, there are inherent limitations in the size and geometry of the parts that can be produced. Larger parts require larger molds and equipment, which can be prohibitively expensive. Additionally, very complex shapes can be challenging to mold uniformly, affecting the quality of the final product.
-
Environmental and Safety Considerations: The process involves handling metal powders, which can pose environmental and safety risks if not managed properly. Dust generation and the potential for explosions require stringent safety protocols and environmental controls, adding to the operational complexity and cost.
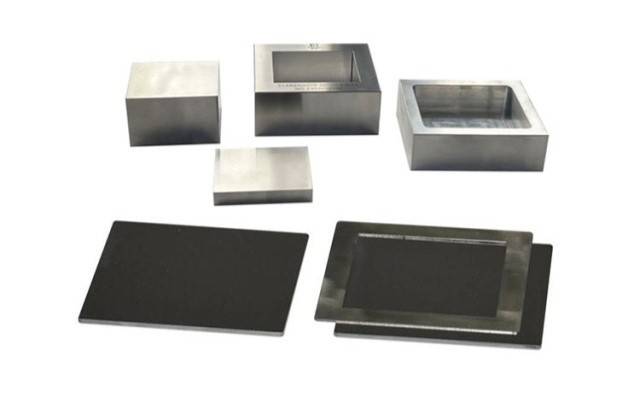
Special mold for heat press
Conclusion
Metal mold pressing technology stands out for its ability to produce complex, high-quality parts efficiently and uniformly. However, it requires significant upfront investment and technical expertise to manage the process effectively. As technology advances, overcoming the current limitations in size, shape, and operational costs will be crucial for expanding the applications of metal mold pressing in various industries. Future developments in automation and mold technology could potentially address these challenges, making metal mold pressing an even more attractive option for manufacturers seeking high precision and quality in their products.
Future Trends in Metal Mold Pressing
The field of metal mold pressing is poised for significant advancements, driven by innovations in automation, material science, and additive manufacturing technologies. As industries continue to seek more efficient and cost-effective manufacturing processes, metal mold pressing stands to benefit greatly from these developments.
Advancements in Automation
Automation in metal mold pressing has been a focal point for enhancing productivity and precision. Modern metal mold pressing equipment now features fully automated processes, from powder filling to the removal of the molded body. This automation not only reduces labor costs but also minimizes human error, leading to more consistent product quality. For instance, the use of robotic arms and advanced control systems ensures precise alignment and movement of punches, thereby improving the density uniformity of the pressed parts.
Moreover, the integration of IoT (Internet of Things) and AI (Artificial Intelligence) in metal mold pressing machinery allows for real-time monitoring and predictive maintenance. This proactive approach to equipment maintenance can significantly reduce downtime and extend the lifespan of pressing equipment.
Material Science Innovations
The evolution of material science has also played a crucial role in the future of metal mold pressing. New materials and alloys are being developed that offer superior mechanical properties, corrosion resistance, and thermal stability. These materials are particularly beneficial in industries such as aerospace, automotive, and medical, where high performance and reliability are critical.
For example, the development of advanced ceramic composites and metal matrix composites has opened up new possibilities for creating lightweight yet robust components. These materials can withstand extreme temperatures and pressures, making them ideal for high-performance applications.
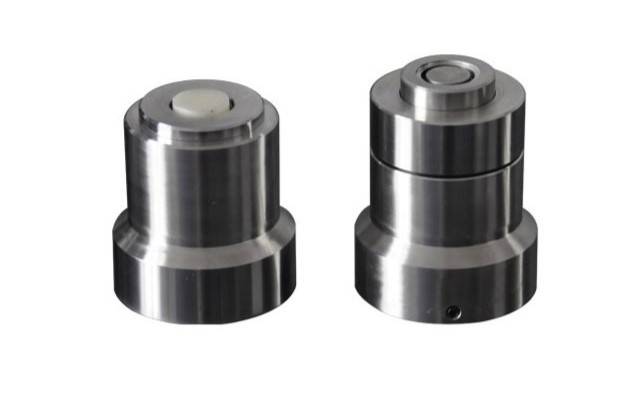
Integration with Additive Manufacturing
The convergence of metal mold pressing with additive manufacturing technologies, such as Metal Injection Molding (MIM) and Binder Jetting (BJ), is another promising trend. These technologies allow for the production of complex geometries that were previously unattainable with traditional pressing methods. The ability to create intricate parts directly from CAD designs reduces the need for multiple manufacturing steps, thereby lowering costs and lead times.
The falling costs of 3D printers and the elimination of geometric limitations have made additive manufacturing an attractive option for many industries. The ability to produce multiple versions of the same product without varying the cost of production and the drastic reduction in processing waste are additional benefits that enhance the sustainability of manufacturing processes.
Applications and Market Trends
The applications of metal mold pressing are expanding rapidly, driven by the need for high-performance components in various sectors. In the aerospace industry, for instance, metal mold pressing is used to manufacture critical parts such as turbine blades and structural components. The automotive industry benefits from metal mold pressing in the production of engine parts, transmission components, and braking systems.
In the medical field, metal mold pressing is utilized for creating implants and surgical instruments with high precision and biocompatibility. The increasing demand for personalized medical devices further underscores the importance of advanced metal mold pressing technologies.
Conclusion
The future of metal mold pressing is bright, with significant advancements in automation, material science, and additive manufacturing driving its evolution. These developments not only enhance the efficiency and quality of manufacturing processes but also expand the applications of metal mold pressing across various industries. As technology continues to advance, we can expect even more innovative solutions that will further propel the field of metal mold pressing into new frontiers.
CONTACT US FOR A FREE CONSULTATION
KINTEK LAB SOLUTION's products and services have been recognized by customers around the world. Our staff will be happy to assist with any inquiry you might have. Contact us for a free consultation and talk to a product specialist to find the most suitable solution for your application needs!