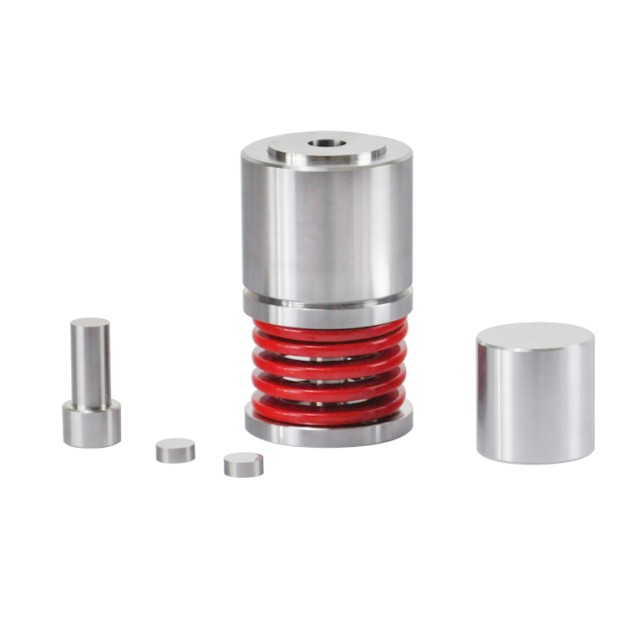
Molds & Accessories
Round Bidirectional Press Mold for Lab
Item Number : PMSY
Price varies based on specs and customizations
- Die material
- Alloy tool steel : Cr12MoV
- Indenter hardness
- HRC60-HRC62
- Sample size
- Φ12、Φ13、Φ15、Φ18、Φ20mm(M)
- Cavity depth
- 40mm (N)
- Dimensions
- Φ88*175mm(L*H)
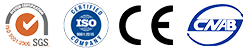
Shipping:
Contact us to get shipping details Enjoy On-time Dispatch Guarantee.
Why Choose Us
Reliable PartnerEasy ordering process, quality products, and dedicated support for your business success.
Introduction
The round bidirectional press mold is a specialized tool used in high-pressure molding processes, particularly for creating intricate shapes from metal powders. This mold is designed to accommodate various shapes, including round, square, rectangular, and hexagonal, by utilizing different mold inserts. The process involves hydraulically applying pressure to a liquid-filled chamber containing the metal powder, which results in the mechanical bonding of the powder particles to form a solid green body. This technique is essential for producing components with large cross-sectional areas or requiring high pressures. The mold also features electric heating capabilities to facilitate the heating process within the tablet, enhancing the molding efficiency and product quality.
Applications
The round bidirectional press mold is versatile in various industrial applications, particularly in the fields of powder metallurgy, rubber molding, and diffusion bonding. This equipment is essential for creating precise shapes with high pressure and uniform heating, making it suitable for a wide range of products and processes.
- Powder Metallurgy: Used for molding powders into complex shapes with large cross-sectional areas under high pressure.
- Rubber Molding: Employed in compression molding, transfer molding, and injection molding processes to shape rubber products.
- Diffusion Bonding: Utilized in large-scale bonding of metal parts, ensuring uniform pressure distribution across extensive surfaces.
- Ceramic Molding: Applicable for pressing ceramic powders into intricate shapes, requiring high pressure and precise temperature control.
- Pharmaceutical Tableting: Used for compressing pharmaceutical powders into tablets, involving electric heating of molds for uniform heating during the tabletting process.
- Advanced Materials Processing: Essential for manufacturing advanced materials where precise pressure and temperature control are critical.
These applications highlight the versatility and critical role of round bidirectional press molds in various high-pressure and high-temperature industrial processes.
Detail & Parts
Technical specifications
Instrument model | PMSY |
---|---|
Sample shape | ![]() |
Die material | Alloy tool steel : Cr12MoV |
Indenter hardness | HRC60-HRC62 |
Sample size | Φ12、Φ13、Φ15、Φ18、Φ20mm(M) |
Cavity depth | 40mm (N) |
Dimensions | Φ88*175mm(L*H) |
Weight | 3.0Kg |
Diagram of hydraulic powder press size | ![]() |
Operation steps
Two way pressurized cylindrical open mold is suitable for samples with high density requirements for powder pressing.
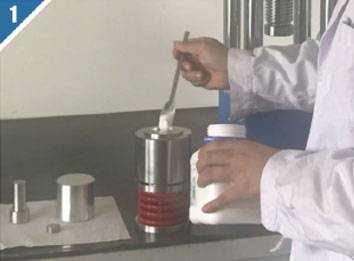
1.Assemble the die according to the operation diagram and install the sample in the cavity.
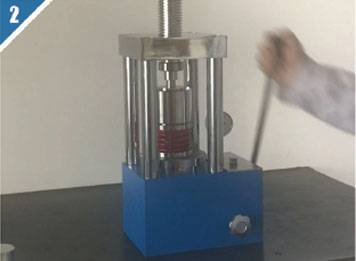
2.Put the die in the center of the hydraulic press and pressurize to required pressure.

3.Assemble the die according to the release diagram ,eject the sample out of the die bushing with the screw rod.
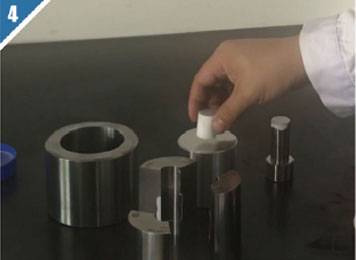
4.Take out the die from the hydraulic press , and remove the sample gently.
Advantages
- Enhanced Pressure Distribution: The round bidirectional press mold utilizes a multi-cylinder system with large pressing plates, ensuring uniform pressure across the entire surface. This is particularly beneficial for large parts, up to approximately 3 feet x 4 feet, which is significant for diffusion bonding processes.
- Independent Cylinder Control: Each hydraulic cylinder can be controlled independently, allowing for precise adjustments based on pressure transducer readings. This feature ensures that even over large areas, the pressure remains consistent, minimizing defects such as flow lines, blisters, or unfilled parts.
- Improved Stability and Uniformity: The bidirectional pressing method compacts the sample from both sides, resulting in enhanced stability and uniformity. This is crucial for subsequent processing stages and ensures the integrity of the final product.
- Versatility in Part Sizes: The press mold can accommodate a wide range of part sizes, making it versatile for various applications. This flexibility is particularly advantageous in industries where parts of different dimensions are commonly used.
- Reduced Dimensional Variability: Although initial setup may require some trial and error, the process once established becomes highly repeatable. This is beneficial for producing parts with specific dimensions, such as long aspect ratio pellets used in industries like automotive (e.g., spark plugs).
FAQ
What Is A Lab Press?
What Is A Round Bidirectional Press Mold Used For?
How Does The Mold Ensure Even Distribution Of Pressure?
Can Custom Molds Be Designed And Produced?
What Happens If There Is Uneven Pressure During The Molding Process?
What Is A Press Mold?
What Is The Purpose Of A Hydraulic Press In Lab?
What Is Press Mould In Ceramics?
What Are Different Type Of Lab Presses?
How Are Pellet Molds Used?
What Types Of Materials Can Be Pelletized Using Pellet Molds?
How Can One Select The Appropriate Pellet Mold For Their Specific Application?
4.8
out of
5
Incredible precision and durability. A game-changer for our lab!
4.7
out of
5
Fast delivery and top-notch quality. Highly recommend!
4.9
out of
5
Exceptional value for money. Our lab productivity soared!
4.8
out of
5
Technologically advanced and user-friendly. A must-have!
4.7
out of
5
Reliable and efficient. Perfect for our high-pressure needs.
4.9
out of
5
Outstanding durability. Handles our toughest projects with ease.
4.8
out of
5
Impressive technological advancements. Enhances our lab's capabilities.
4.7
out of
5
Great value and performance. Our lab couldn't be happier!
4.9
out of
5
Superb quality and reliability. A key asset to our operations.
4.8
out of
5
Excellent product and service. Delivered exactly as promised.
4.7
out of
5
Highly durable and efficient. Boosts our lab's efficiency significantly.
Products
Round Bidirectional Press Mold for Lab
REQUEST A QUOTE
Our professional team will reply to you within one business day. Please feel free to contact us!
Related Products
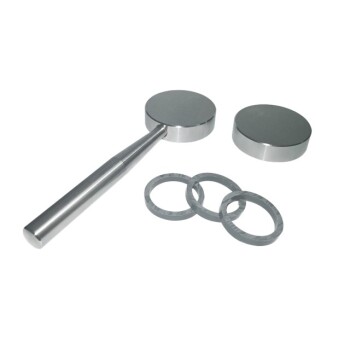
XRF & KBR plastic ring lab Powder Pellet Pressing Mold for FTIR
Get precise XRF samples with our plastic ring lab powder pellet pressing mold. Fast tableting speed and customizable sizes for perfect molding every time.
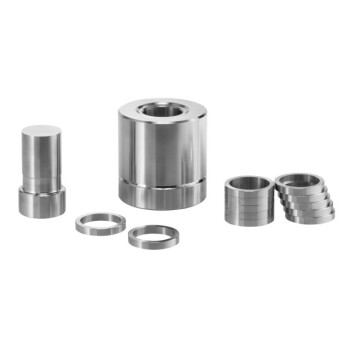
XRF & KBR steel ring lab Powder Pellet Pressing Mold for FTIR
Produce perfect XRF samples with our steel ring lab powder pellet pressing mold. Fast tableting speed and customizable sizes for accurate molding every time.
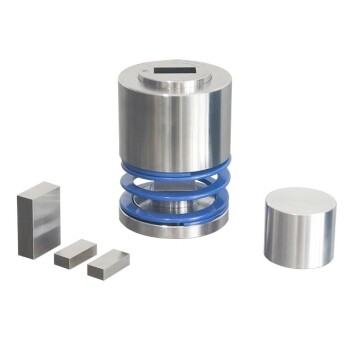
Square Bidirectional Pressure Mold for Lab Use
Discover precision in molding with our Square Bidirectional Pressure Mold. Ideal for creating diverse shapes and sizes, from squares to hexagons, under high pressure and uniform heating. Perfect for advanced material processing.
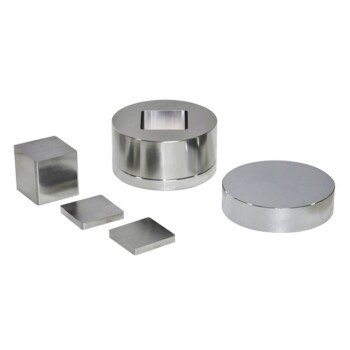
Square Lab Press Mold for Laboratory Applications
Create uniform samples easily with Square Lab Press Mold - available in various sizes. Ideal for battery, cement, ceramics, and more. Custom sizes available.
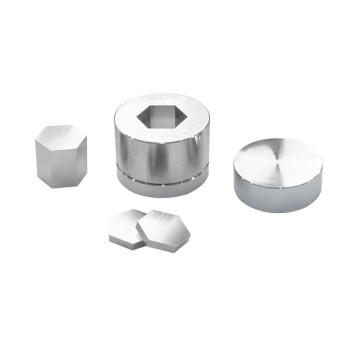
Discover precision polygon press molds for sintering. Ideal for pentagon-shaped parts, our molds ensure uniform pressure and stability. Perfect for repeatable, high-quality production.
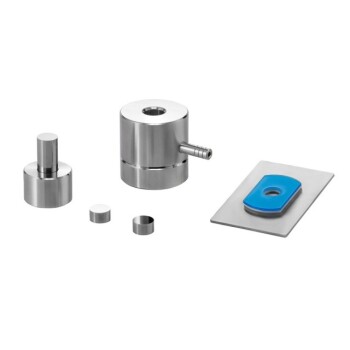
Easily release samples from our lab infrared press mold for accurate testing. Ideal for battery, cement, ceramics, and other sample preparation research. Customizable sizes available.
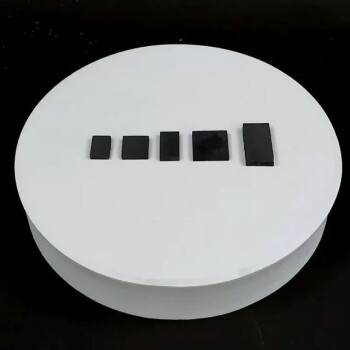
Glassy Carbon Sheet RVC for Electrochemical Experiments
Discover our Glassy Carbon Sheet - RVC. Perfect for your experiments, this high-quality material will elevate your research to the next level.
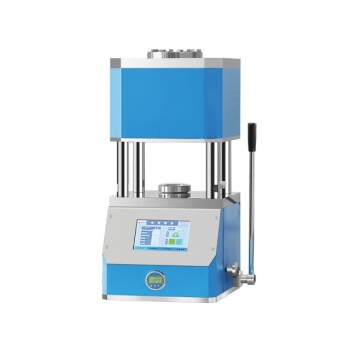
Manual High Temperature Heated Hydraulic Press Machine with Heated Plates for Lab
The High Temperature Hot Press is a machine specifically designed for pressing, sintering and processing materials in a high temperature environment. It is capable of operating in the range of hundreds of degrees Celsius to thousands of degrees Celsius for a variety of high temperature process requirements.
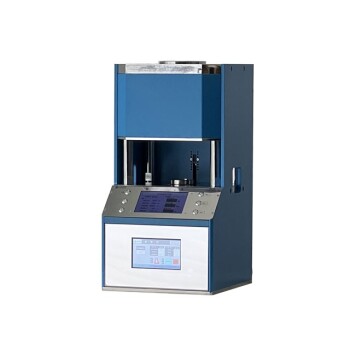
Automatic High Temperature Heated Hydraulic Press Machine with Heated Plates for Lab
The High Temperature Hot Press is a machine specifically designed for pressing, sintering and processing materials in a high temperature environment. It is capable of operating in the range of hundreds of degrees Celsius to thousands of degrees Celsius for a variety of high temperature process requirements.
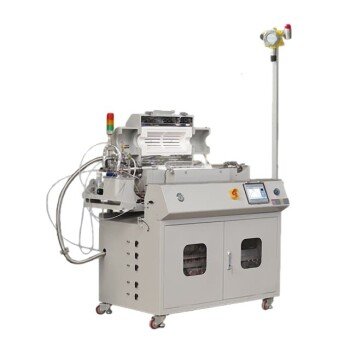
Customer Made Versatile CVD Tube Furnace Chemical Vapor Deposition Chamber System Equipment
Get your exclusive CVD furnace with KT-CTF16 Customer Made Versatile Furnace. Customizable sliding, rotating, and tilting functions for precise reactions. Order now!
Related Articles
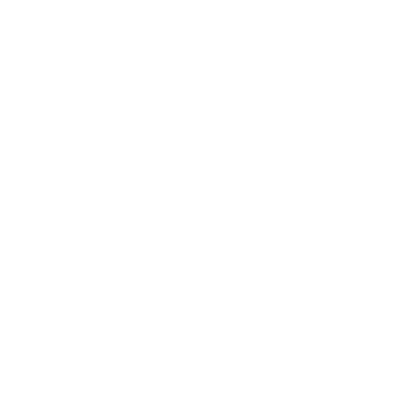
Ceramic Isostatic Pressing Mold Technology
Exploring the design and factors affecting ceramic isostatic pressing molds.
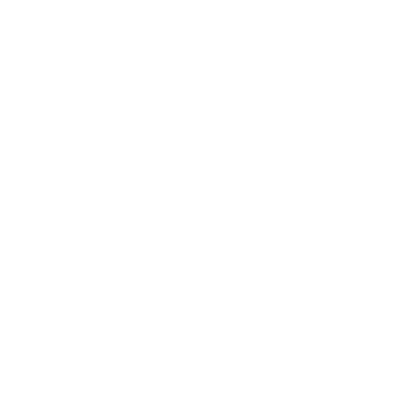
Comprehensive Guide to Metal Mold Pressing: Techniques, Equipment, and Applications
Explore the detailed process of metal mold pressing, including equipment, techniques, and applications. Learn how hydraulic presses shape materials like metal and rubber efficiently.
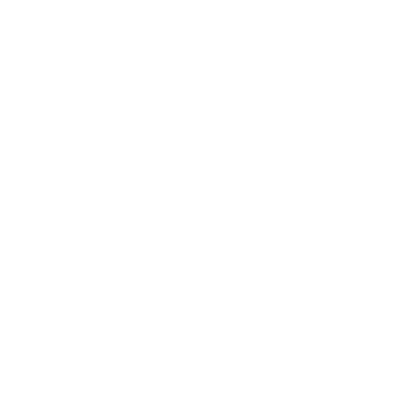
Infrared Press Mold Techniques for Non-Demolding Applications
Explore advanced infrared press mold techniques without demolding. Learn about the benefits, applications, and best practices for non-demolding lab processes.
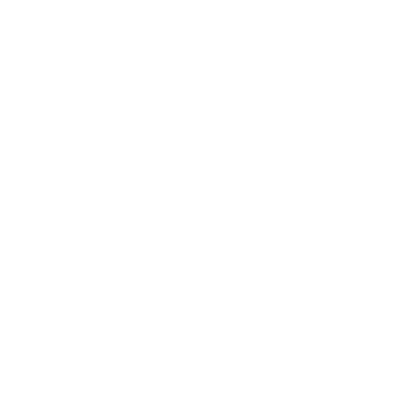
Comprehensive Guide to Isostatic Pressing Molds: Types, Processes, and Applications
Explore the detailed world of isostatic pressing molds, including types like wet bag and dry bag, their processes, and applications. Learn how these molds ensure uniform density and high-strength products.
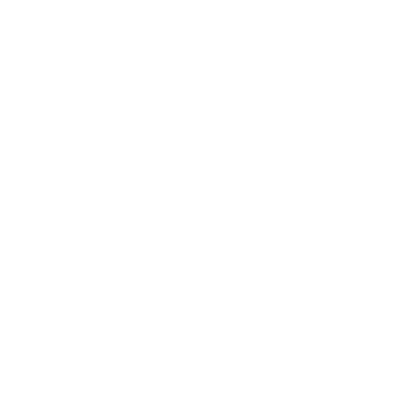
Comprehensive Guide to Cylindrical Lab Electric Heating Press Mold: Technology and Applications
Explore the advanced features and applications of cylindrical lab electric heating press molds. Learn about their working principles, types of heating technologies, and key benefits for precise sample preparation.
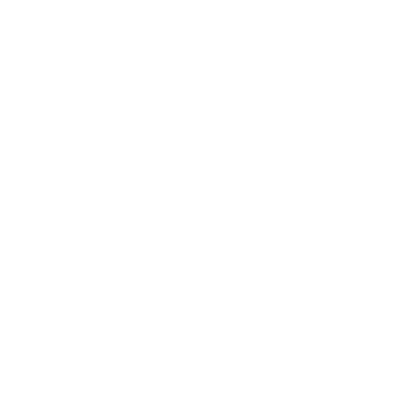
Infrared Heating Quantitative Flat Plate Mold: Design, Applications, and Benefits
Explore the advanced design and applications of infrared heating quantitative flat plate molds. Learn about their benefits in achieving uniform heat distribution and efficient processing.
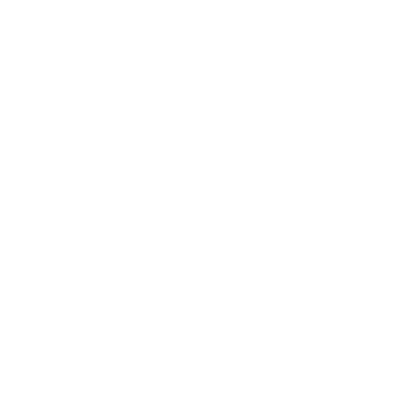
Manual Pellet Press: A Comprehensive Guide to Efficient Lab Pelletizing
Explore the intricacies of manual pellet presses, including operation, safety, and maintenance tips. Learn how to choose the right press, understand force gauges, and optimize pellet quality for your lab experiments.
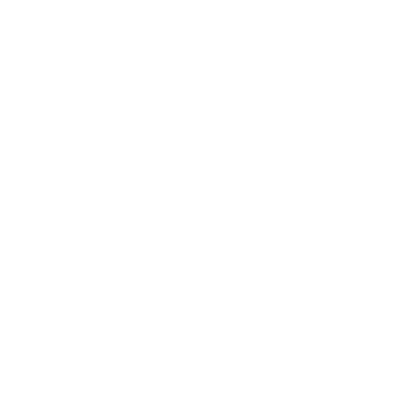
Nine Precision Molding Processes of Zirconia Ceramics
An overview of nine advanced molding processes for zirconia ceramics, including dry and wet methods.
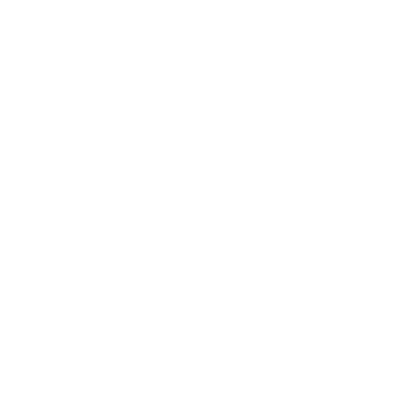
Advanced Ceramics Hot Press Sintering Technology and Equipment
Explores the hot press sintering process for advanced ceramics, its methods, advantages, equipment, and applications.
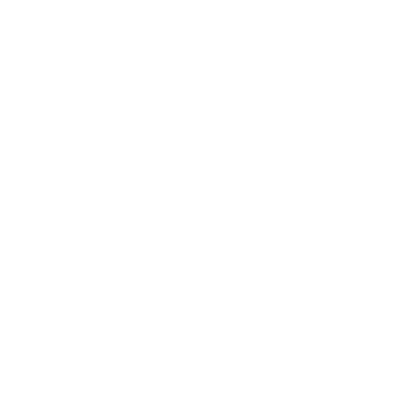
Issues with Poor Demoulding in Manual Tablet Presses
Analyzes the causes of poor demoulding in manual tablet presses, focusing on powder, mold, machine body, and operator factors.
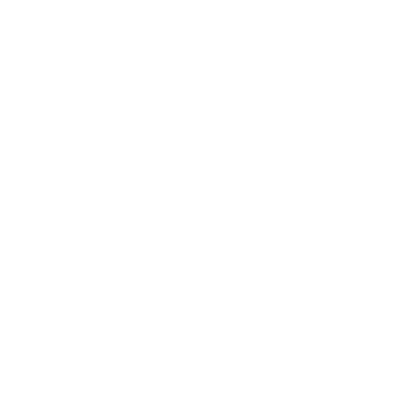
Precision Ceramic Injection Molding: Key Processes
An in-depth look at the stages of precision ceramic injection molding, focusing on grouting, holding pressure, cooling, and demolding.
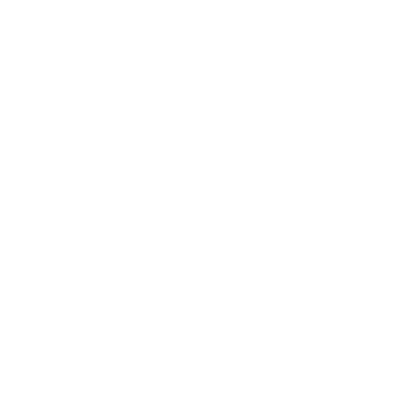
Application of Vacuum Heat Treatment Technology
Exploring the evolution and benefits of vacuum heat treatment in metal processing.