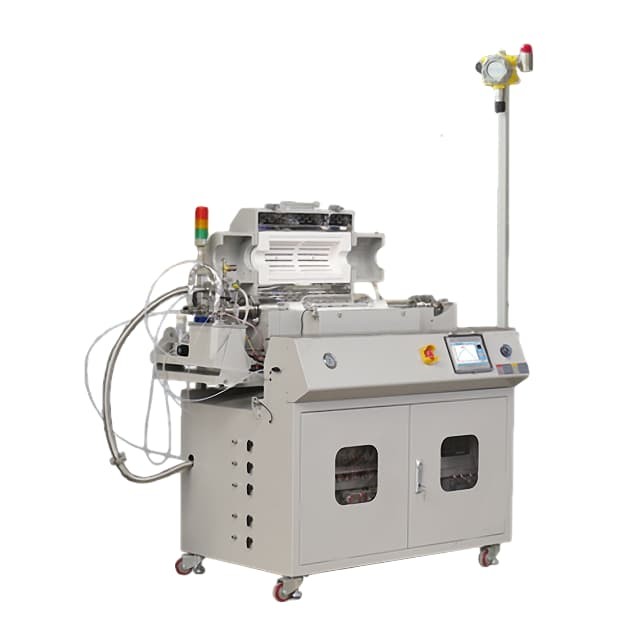
CVD & PECVD Furnace
Customer Made Versatile CVD Tube Furnace Chemical Vapor Deposition Chamber System Equipment
Item Number : KT-CTF16
Price varies based on specs and customizations
- Max. temperature
- 1600 ℃
- Constant work temperature
- 1550 ℃
- Furnace tube diameter
- 60 mm
- Heating zone
- 3x300 mm
- Heating rate
- 0-10 ℃/min
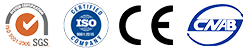
Shipping:
Contact us to get shipping details Enjoy On-time Dispatch Guarantee.
Why Choose Us
Reliable PartnerEasy ordering process, quality products, and dedicated support for your business success.
Introduction
The CVD Tube Furnace is a high-temperature furnace used for chemical vapor deposition (CVD) processes. It features multiple heating zones that allow for precise temperature control, a high vacuum pump that creates a vacuum environment for CVD processes, and a mass flow gas control station that mixes and inputs gases into the furnace tube. The furnace is capable of reaching temperatures up to 1200°C and has an ultimate vacuum rate of 10^-7 torr. It is commonly used in the semiconductor industry for depositing thin films of various materials, including insulating materials, metallic materials, and metal alloy materials.
Applications
Multi-Zone CVD Tube Furnaces are widely used in various research and industrial applications, including:
- Nanomaterial Synthesis: The CVD tube furnace is ideal for the growth of nanowires and the preparation of nanofilms, which are crucial for developing advanced materials with unique properties.
- Coating Technologies: It is widely used for the deposition of metal films, ceramic films, and composite films, which are essential for enhancing the surface properties of various materials.
- Battery Material Processing: The furnace is suitable for the drying and sintering of battery materials, which is a critical step in the production of high-performance energy storage devices.
- High-Temperature Sintering: It is employed in high-temperature atmosphere sintering and atmosphere reduction processes, which are necessary for the densification of materials.
- Vacuum Coating: The high vacuum capabilities of the furnace make it perfect for vacuum coating applications, where the purity and quality of the coating are paramount.
- Research and Development: Universities and scientific research institutes utilize this equipment for a wide range of experiments in the field of material science, including CVD/CVI (Chemical Vapor Infiltration) studies.
- Industrial Applications: In industrial settings, the CVD tube furnace is used for processes that require precise temperature control and gas management, such as in the semiconductor industry.
- Plasma Cleaning and Etching: The versatility of the equipment allows for the expansion of functionalities to include plasma cleaning and etching, which are essential for preparing substrates before deposition.
Features
CVD Tube Furnace is a versatile and high-performance furnace that is ideal for a variety of applications in research and industry. With its advanced features and capabilities, this furnace can help you achieve the best possible results in your work.
- Multi-zone temperature control:This furnace features multi-zone temperature control, which allows you to precisely control the temperature in different zones of the furnace. This is essential for applications where you need to create a specific temperature profile or gradient.
- High temperature capability:This furnace can reach temperatures up to 1200°C, making it ideal for a wide range of applications. This high temperature capability makes it possible to perform demanding processes such as CVD, diffusion, and other thermo-treatments.
- Vacuum or atmosphere protection: This furnace can be used under vacuum or atmosphere protection, making it suitable for a variety of applications. This versatility makes it possible to perform processes that require a specific atmosphere or vacuum environment.
- Easy to use:This furnace is easy to use, with a user-friendly interface and intuitive controls. This makes it easy to set up and operate the furnace, even for users with limited experience.
- Compact design: This furnace is compact and lightweight, making it easy to install and use in a variety of spaces. This compact design makes it ideal for use in laboratories and other space-constrained environments.
Principle
Chemical Vapor Deposition (CVD) is a thin film deposition technique in which a solid material is deposited onto a substrate from a gas phase. The substrate is heated to a high temperature, and a gas containing the desired material is introduced into the chamber. The gas reacts with the substrate, and the desired material is deposited onto the surface.
CVD Tube Furnaces are used for CVD processes. The furnace consists of a heated tube, which is typically made of quartz or alumina. The substrate is placed inside the tube, and the gas is introduced into the tube. The gas flows through the tube and reacts with the substrate, depositing the desired material onto the surface.
CVD Tube Furnaces can be used to deposit a wide variety of materials, including metals, oxides, nitrides, and carbides. The process is used in the manufacture of semiconductors, solar cells, and other electronic devices.
Different temperature and setup CVD systems available
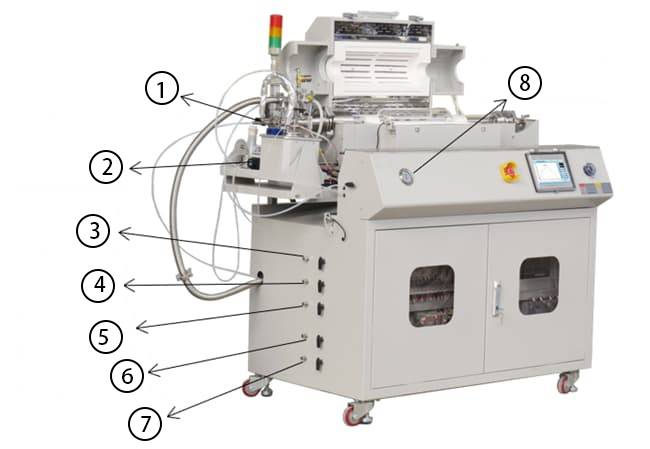
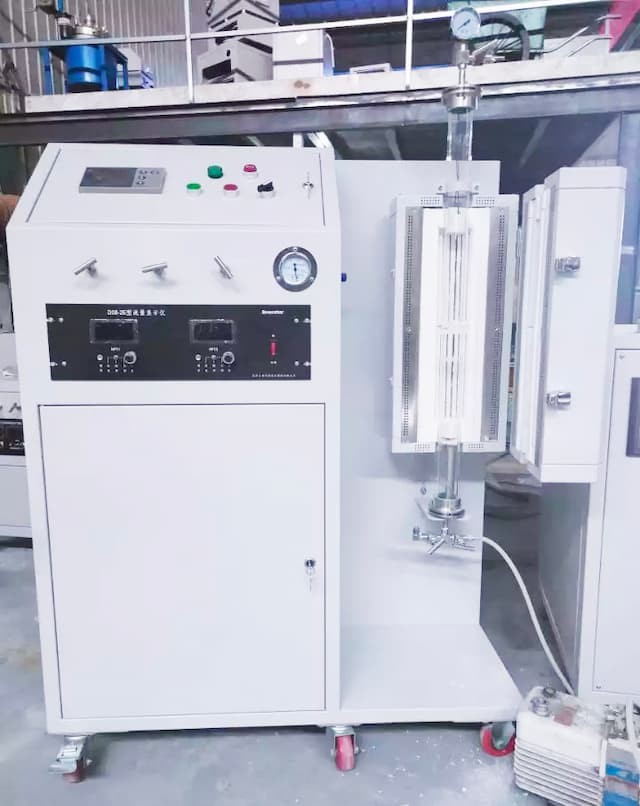
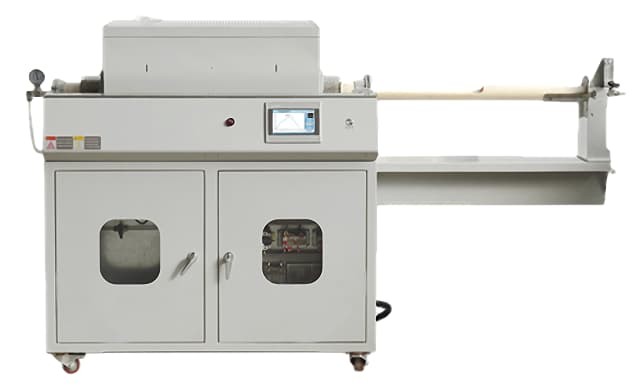
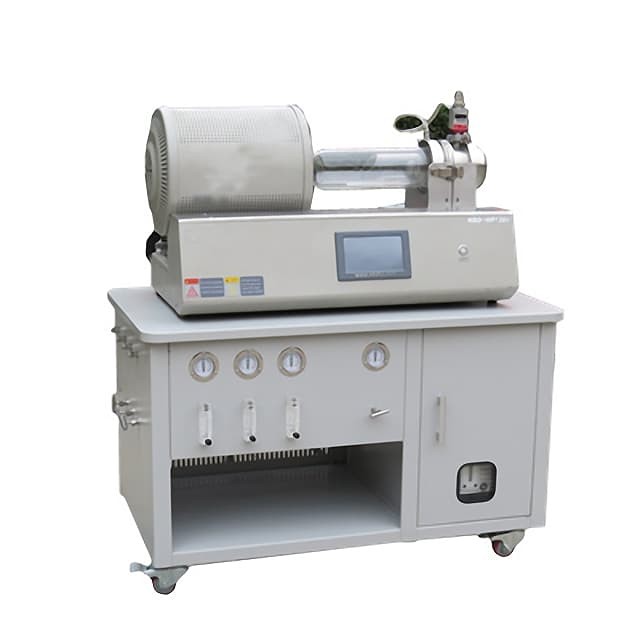
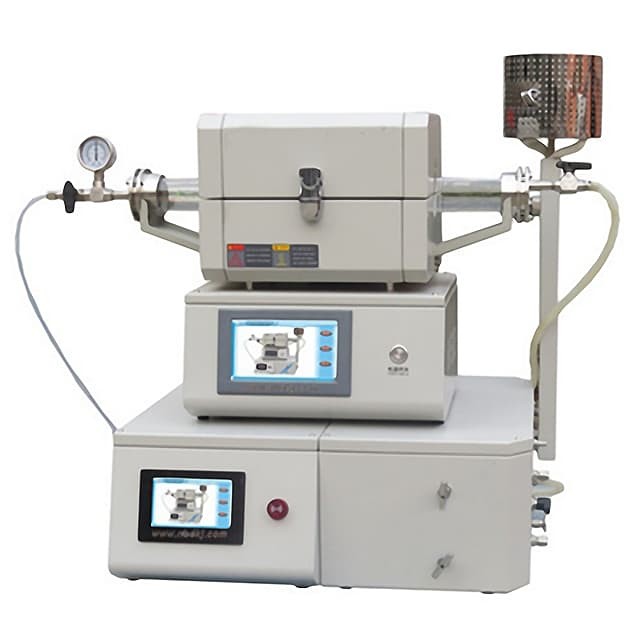
Principle
The CVD tube furnace operates on the principle of chemical vapor deposition, utilizing a high vacuum system and precise mass flow controllers to facilitate the deposition of various films under controlled conditions. It employs radio frequency glow technology for high deposition rates and advanced heating techniques for uniform film distribution.
Advantages
- High temperature uniformity:The multi-zone design ensures that the temperature is evenly distributed throughout the furnace, which is critical for CVD processes.
- Precise temperature control: The digital temperature controller allows for precise control of the furnace temperature, which is essential for repeatable and reliable results.
- High vacuum capability: The ultimate vacuum rate of 10^-7 torr allows for the removal of contaminants from the reaction chamber, which is necessary for high-quality CVD films.
- Easy to use:The user-friendly interface makes the furnace easy to operate, even for inexperienced users.
- Versatile: The furnace can be used for a wide variety of CVD processes, including metal deposition, semiconductor processing, and carbon nanotube synthesis.
- Compact design: The compact design of the furnace makes it ideal for use in space-constrained laboratories.
- Affordable: The furnace is competitively priced, making it an excellent value for the money.
Technical specifications
Furnace model | KT-CTF16-60 |
---|---|
Max. temperature | 1600℃ |
Constant work temperature | 1550℃ |
Furnace tube material | High purity Al2O3 tube |
Furnace tube diameter | 60mm |
Heating zone | 3x300mm |
Chamber material | Alumina polycrystalline fiber |
Heating element | Silicon Carbide |
Heating rate | 0-10℃/min |
Thermal couple | S type |
Temperature controller | Digital PID controller/Touch screen PID controller |
Temperature control accuracy | ±1℃ |
Gas precise control unit | |
Flow meter | MFC mass flow meter |
Gas channels | 3 channels |
Flow rate | MFC1: 0-5SCCM O2 MFC2: 0-20SCMCH4 MFC3: 0- 100SCCM H2 MFC4: 0-500 SCCM N2 |
Linearity | ±0.5% F.S. |
Repeatability | ±0.2% F.S. |
Pipe line and valve | Stainless steel |
Maximum Operating Pressure | 0.45MPa |
Flow meter controller | Digital Knob controller/Touch screen controller |
Standard vacuum unit(Optional) | |
Vacuum pump | Rotary vane vacuum pump |
Pump flow rate | 4L/S |
Vacuum suction port | KF25 |
Vacuum gauge | Pirani/Resistance silicon vacuum gauge |
Rated vacuum pressure | 10Pa |
High vacuum unit(Optional) | |
Vacuum pump | Rotary vane pump+Molecular pump |
Pump flow rate | 4L/S+110L/S |
Vacuum suction port | KF25 |
Vacuum gauge | Compound vacuum gauge |
Rated vacuum pressure | 6x10-5Pa |
Above specifications and setups can be customized |
Standard Package
No. | Description | Quantity |
---|---|---|
1 | Furnace | 1 |
2 | Quartz tube | 1 |
3 | Vacuum flange | 2 |
4 | Tube thermal block | 2 |
5 | Tube thermal block hook | 1 |
6 | Heat resistant glove | 1 |
7 | Precise gas control | 1 |
8 | Vacuum unit | 1 |
9 | Operation manual | 1 |
Optional Setup
- In tube gases detecting and monitoring,like H2, O2 and so on
- Independent furnace temperature monitoring and recording
- RS 485 communication port for PC remote control and data exporting
- Insert gases feeding flow rate control,like mass flowmeter and float flowmeter
- Touch screen temperature controller with versatile operator friendly functions
- High vacuum pump station setups, like vane vacuum pump,molecular pump,diffusion pump
Warnings
Operator safety is the top important issue! Please operate the equipment with cautions. Working with inflammable& explosive or toxic gases is very dangerous, operators must take all necessary precautions before starting the equipment. Working with positive pressure inside the reactors or chambers is dangerous, operator must fellow the safety procedures strictly. Extra caution must also be taken when operating with air-reactive materials, especially under vacuum. A leak can draw air into the apparatus and cause a violent reaction to occur.
Designed for You
KinTek provide deep custom made service and equipment to worldwide customers, our specialized teamwork and rich experienced engineers are capable to undertake the custom tailoring hardware and software equipment requirements, and help our customer to build up the exclusive and personalized equipment and solution!
Would you please drop your ideas to us, our engineers are ready for you now!
4.9
out of
5
KT-CTF16 is a great furnace, it offers high-quality CVD processing with precise temperature control and customizable setups. The customer service is also top-notch, highly recommended!
4.8
out of
5
The furnace is very versatile and can be used for a variety of applications. The temperature control is accurate and the overall performance is excellent. I highly recommend this furnace to anyone who needs a reliable and versatile CVD system.
4.7
out of
5
The furnace has been a great addition to our lab. It's easy to use and maintain, and the results have been excellent. We've been able to produce high-quality materials with ease.
4.9
out of
5
The KT-CTF16 is a fantastic furnace. It's easy to use and the temperature control is very precise. We've been able to produce high-quality materials with ease. I would highly recommend this furnace to anyone who needs a reliable and versatile CVD system.
4.8
out of
5
This furnace is an excellent choice for anyone who needs a versatile and reliable CVD system. It's easy to use and maintain, and the results have been consistent and of high quality. I highly recommend this furnace.
4.7
out of
5
The KT-CTF16 is a great furnace for a variety of applications. It's easy to use and maintain, and the results have been excellent. We've been able to produce high-quality materials with ease.
4.9
out of
5
This furnace is a great investment. It's well-made and has a lot of features that make it easy to use. The customer service is also excellent. I would definitely recommend this furnace to anyone who needs a reliable and versatile CVD system.
4.8
out of
5
The furnace arrived quickly and was easy to set up. It's been working great so far and I'm very happy with it. The customer service has also been excellent.
4.7
out of
5
This furnace is a great value for the price. It's well-made and has a lot of features that make it easy to use. The customer service is also excellent. I would definitely recommend this furnace to anyone who needs a reliable and versatile CVD system.
4.9
out of
5
The KT-CTF16 is a great furnace. It's easy to use and the temperature control is very precise. We've been able to produce high-quality materials with ease. I would highly recommend this furnace to anyone who needs a reliable and versatile CVD system.
4.8
out of
5
This furnace is an excellent choice for anyone who needs a versatile and reliable CVD system. It's easy to use and maintain, and the results have been consistent and of high quality. I highly recommend this furnace.
4.7
out of
5
The KT-CTF16 is a great furnace for a variety of applications. It's easy to use and maintain, and the results have been excellent. We've been able to produce high-quality materials with ease.
4.9
out of
5
This furnace is a great investment. It's well-made and has a lot of features that make it easy to use. The customer service is also excellent. I would definitely recommend this furnace to anyone who needs a reliable and versatile CVD system.
4.8
out of
5
The furnace arrived quickly and was easy to set up. It's been working great so far and I'm very happy with it. The customer service has also been excellent.
4.7
out of
5
This furnace is a great value for the price. It's well-made and has a lot of features that make it easy to use. The customer service is also excellent. I would definitely recommend this furnace to anyone who needs a reliable and versatile CVD system.
4.9
out of
5
The KT-CTF16 is a great furnace. It's easy to use and the temperature control is very precise. We've been able to produce high-quality materials with ease. I would highly recommend this furnace to anyone who needs a reliable and versatile CVD system.
Products
Customer Made Versatile CVD Tube Furnace Chemical Vapor Deposition Chamber System Equipment
REQUEST A QUOTE
Our professional team will reply to you within one business day. Please feel free to contact us!
Related Products
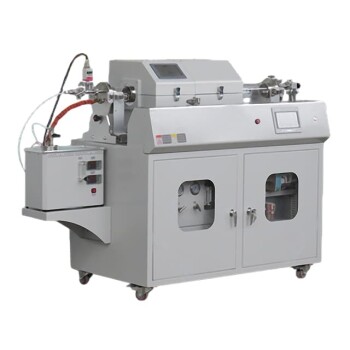
KT-PE12 Slide PECVD System: Wide power range, programmable temp control, fast heating/cooling with sliding system, MFC mass flow control & vacuum pump.
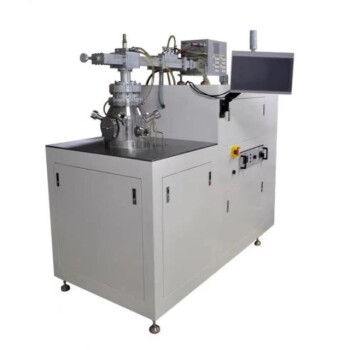
Learn about Cylindrical Resonator MPCVD Machine, the microwave plasma chemical vapor deposition method used for growing diamond gemstones and films in the jewelry and semi-conductor industries. Discover its cost-effective advantages over traditional HPHT methods.
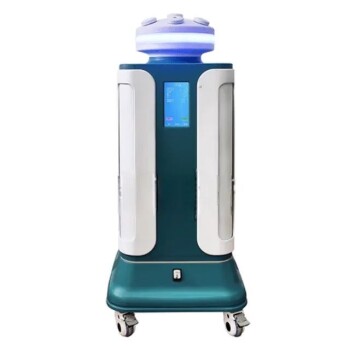
VHP Sterilization Equipment Hydrogen Peroxide H2O2 Space Sterilizer
A hydrogen peroxide space sterilizer is a device that uses vaporized hydrogen peroxide to decontaminate enclosed spaces. It kills microorganisms by damaging their cellular components and genetic material.
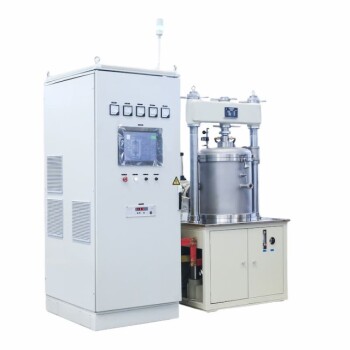
Vacuum Hot Press Furnace Machine Heated Vacuum Press
Discover the advantages of Vacuum Hot Press Furnace! Manufacture dense refractory metals & compounds, ceramics, and composites under high temp and pressure.
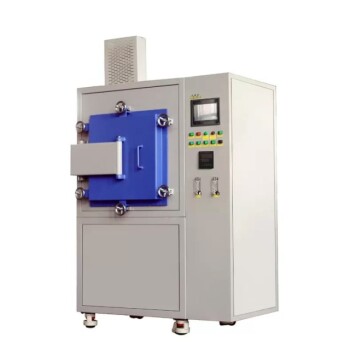
Controlled Nitrogen Inert Hydrogen Atmosphere Furnace
KT-AH Hydrogen atmosphere furnace - induction gas furnace for sintering/annealing with built-in safety features, dual housing design, and energy-saving efficiency. Ideal for lab and industrial use.
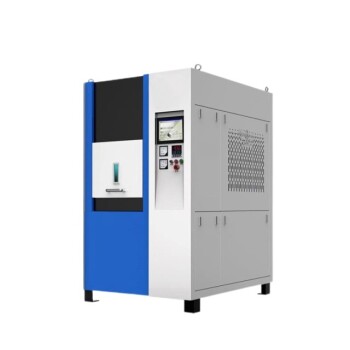
Spark Plasma Sintering Furnace SPS Furnace
Discover the benefits of Spark Plasma Sintering Furnaces for rapid, low-temperature material preparation. Uniform heating, low cost & eco-friendly.
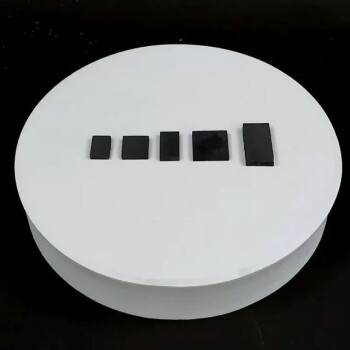
Glassy Carbon Sheet RVC for Electrochemical Experiments
Discover our Glassy Carbon Sheet - RVC. Perfect for your experiments, this high-quality material will elevate your research to the next level.
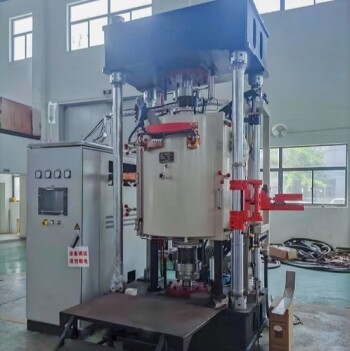
Vacuum Heat Treat and Pressure Sintering Furnace for High Temperature Applications
Vacuum pressure sintering furnaces are designed for high temperature hot pressing applications in metal and ceramic sintering. Its advanced features ensure precise temperature control, reliable pressure maintenance, and a robust design for seamless operation.
Related Articles
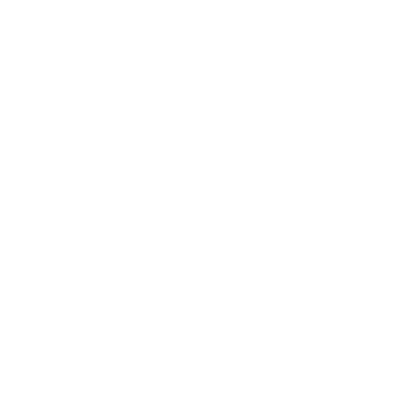
Advantages of Using CVD Tube Furnace for Coating
CVD coatings have several advantages over other coating methods, such as high purity, density, and uniformity, making them ideal for many applications in various industries.
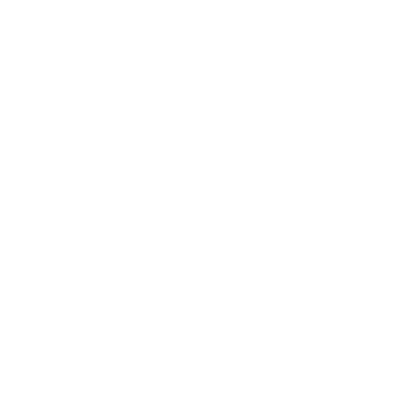
CVD furnace for the growth of carbon nanotubes
Chemical vapor deposition (CVD) furnace technology is a widely used method for growing carbon nanotubes.
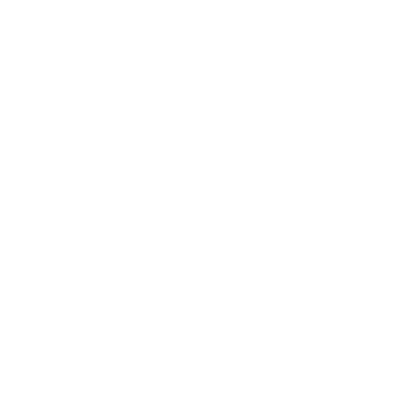
Introducing the Lab Vacuum Tube Furnaces
A vacuum tube furnace is a type of furnace that uses vacuum to isolate the process atmosphere from the external atmosphere.
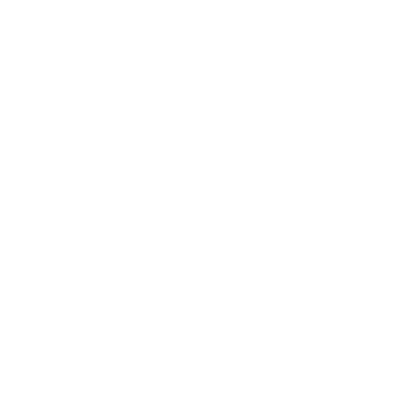
An Introduction to Chemical Vapor Deposition (CVD)
Chemical vapor deposition, or CVD, is a coating process that involves the use of gaseous reactants to produce thin films and coatings of high quality.
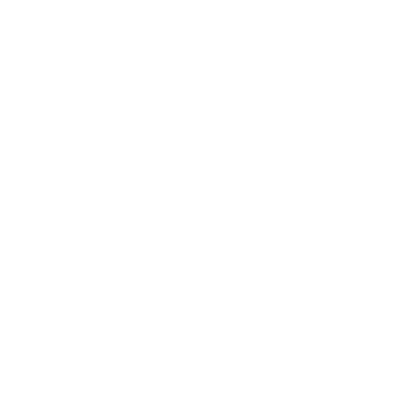
Advantages and Disadvantages of Chemical Vapor Deposition (CVD)
Chemical vapor deposition (CVD) is a versatile thin-film deposition technique widely used in various industries. Explore its advantages, disadvantages, and potential new applications.
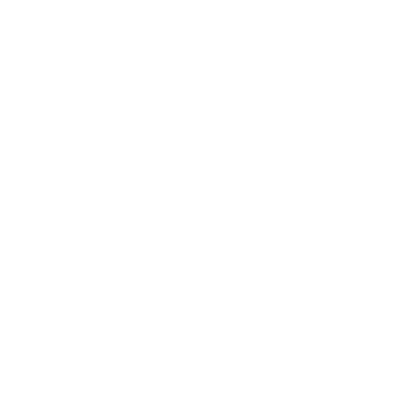
Exploring the Functions and Advantages of Rotary Tube Furnaces
Discover how rotary tube furnaces work and why they are used in advanced materials processing. Learn about the basic technique of rotary furnaces and their customizable features. Explore the advantages of rotary tube furnaces over other furnace types.
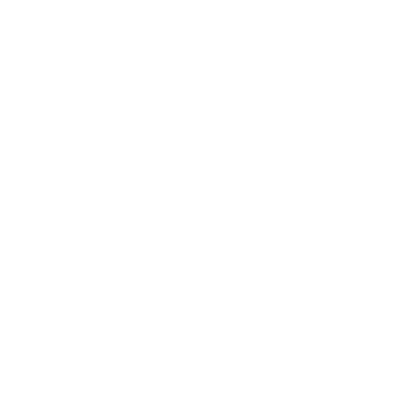
PECVD Furnace A Low-Power and Low-Temperature Solution for Soft Matter
PECVD (Plasma Enhanced Chemical Vapor Deposition) furnaces have become a popular solution for the deposition of thin films on soft matter surfaces.
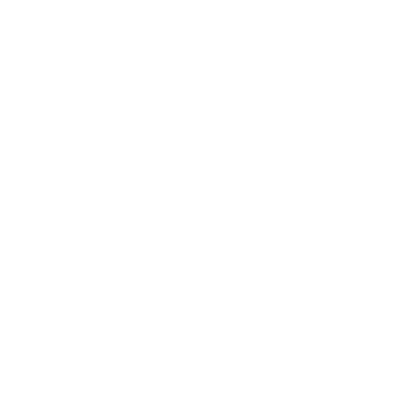
CVD Machines for Thin Film Deposition
Chemical Vapor Deposition (CVD) is a widely used technique for deposition of thin films on various substrates.
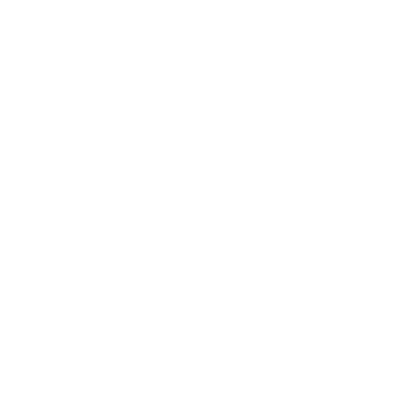
The Versatility of Tube Furnaces: A Guide to Their Applications and Benefits
A laboratory tube furnace is a specialized heating device used in scientific and industrial labs for a variety of applications.
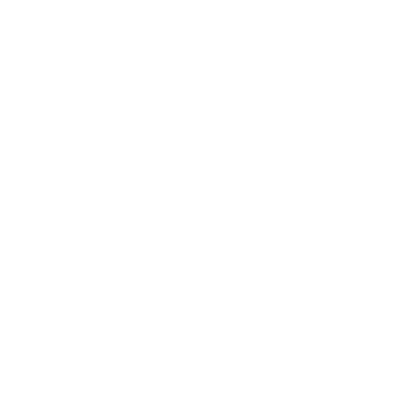
Exploring the Key Characteristics of Tube Heating Furnaces
A tube heating furnace is a specialized type of industrial furnace that is used in various industries to heat substances through the use of fuel combustion.
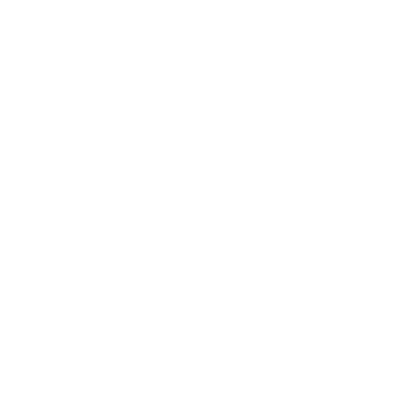
Exploring Rotary Tube Furnaces: A Comprehensive Guide
Discover the workings of rotary tube furnaces, their diverse applications, and key advantages. Explore how these furnaces operate, their suitability for different processes, and factors to consider when selecting one. Find out why rotary tube furnaces are favored in advanced materials processing.
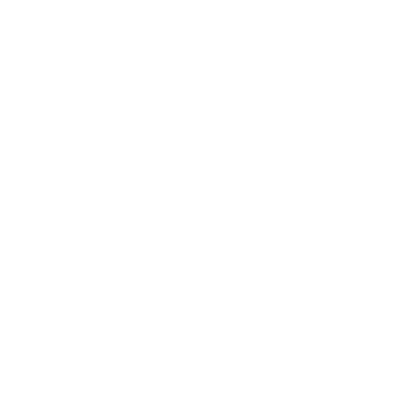
Plasma Enhanced Chemical Vapor Deposition (PECVD): A Comprehensive Guide
Learn everything you need to know about Plasma Enhanced Chemical Vapor Deposition (PECVD), a thin film deposition technique used in the semiconductor industry. Explore its principles, applications, and benefits.