Introduction to CVD Furnace Technology
Chemical vapor deposition (CVD) furnace technology is a widely used method for growing carbon nanotubes. It involves the use of a heated substrate material, which is placed inside a furnace chamber along with a source of carbon and a catalyst. The carbon source is typically a hydrocarbon gas such as methane or ethylene, while the catalyst is often a metal such as iron or nickel. The furnace is heated to a high temperature, causing the carbon to decompose and deposit onto the substrate in the form of carbon nanotubes. CVD furnace technology is a highly effective method for producing high-quality carbon nanotubes with a high degree of control over their properties.
Table of Contents
- Introduction to CVD Furnace Technology
- Importance of Carbon Nanotubes
- Understanding CVD Growth Process
- Types of Carbon Nanotube Growth Mechanisms
- Advantages of CVD furnace for carbon nanotube growth
- Key Components of CVD Furnace
- Factors Affecting Carbon Nanotube Growth
- Applications of Carbon Nanotubes
- Future of CVD Furnace Technology
Importance of Carbon Nanotubes
Carbon nanotubes (CNTs) are one of the most exciting materials in the field of nanotechnology. They possess unique mechanical, electrical, and thermal properties, which make them ideal for a wide range of applications. This section highlights the importance of CNTs and their potential applications.
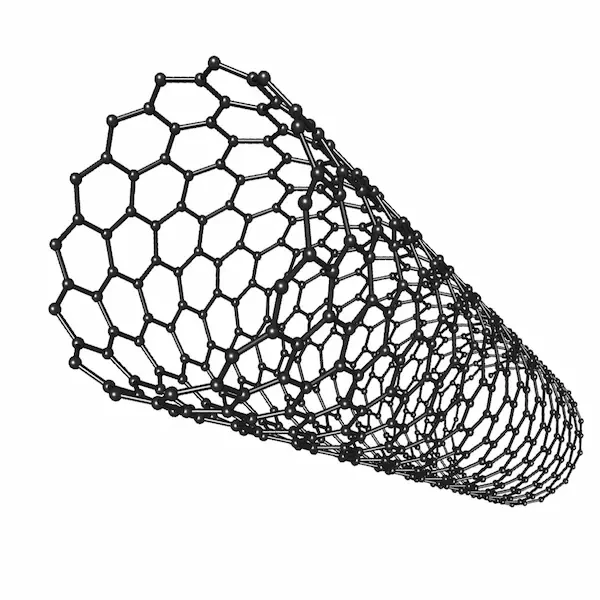
Mechanical Strength
CNTs have a high mechanical strength that is many times stronger than steel or other industrial fibers. This property makes them ideal for use in a wide range of applications, including composites for structural materials, sports equipment, yachts, armor vests, aerospace components, automotive parts, spark protection, lightning protection, and others.
Electrical Properties
CNTs have excellent electrical properties, which make them ideal for use in electronics, including transistors, sensors, and conductive films. They are also used in energy storage, including batteries and supercapacitors.
Thermal Properties
CNTs have excellent thermal properties, which make them ideal for use in thermal management, including heat sinks and thermal interface materials.
Biomedical Applications
CNTs have potential applications in biomedical engineering, including drug delivery, imaging, and biosensors. They also have potential applications in tissue engineering, including scaffolds for tissue regeneration.
Industrial-Scale Production
The demand for CNTs has increased in recent years due to their unique properties and potential applications. Chemical vapor deposition (CVD) is one of the most common methods for producing CNTs, and a CVD furnace is a critical piece of equipment for researchers and manufacturers working with CNTs. By using a CVD furnace, researchers can precisely control the growth conditions to produce CNTs with specific properties, such as diameter, length, and chirality, which can be tailored for different applications. In addition, CVD furnaces can be used to produce large quantities of CNTs, making them an essential tool for industrial-scale production.
In summary, CNTs possess unique mechanical, electrical, and thermal properties that make them ideal for a wide range of applications, including electronics, energy storage, and biomedical engineering. CVD furnaces play a crucial role in the production and development of CNTs, providing the high temperatures and controlled environment necessary for the growth of high-quality nanotubes.
Understanding CVD Growth Process
Chemical vapor deposition (CVD) is a widely used technique for depositing materials as thin films onto substrates by utilizing the chemical reactions between vapor species. CVD furnaces play a crucial role in the growth of carbon nanotubes (CNTs), which have a wide range of potential applications in fields such as electronics, materials science, and medicine.
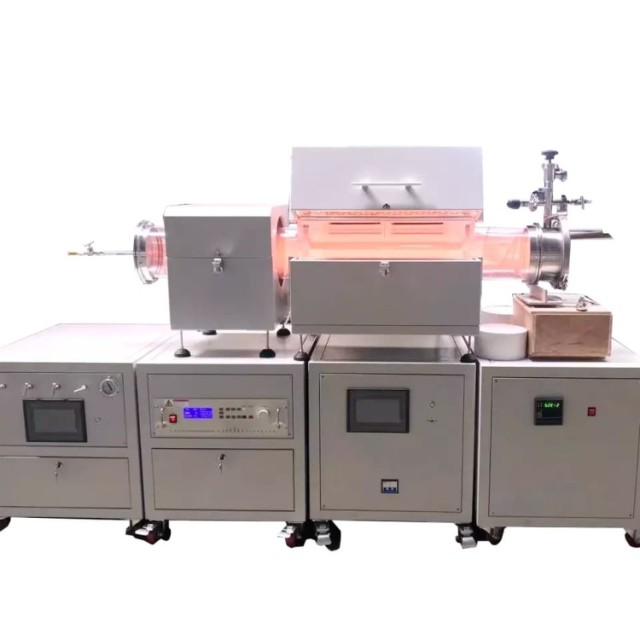
CVD Growth Process
The CVD growth process involves introducing a hydrocarbon gas into the furnace at high temperatures, typically around 800-1000°C, and allowing it to react with a catalyst such as iron or nickel to form CNTs. The growth rate, diameter, and alignment of the CNTs can be controlled by varying the temperature, gas flow rate, and catalyst properties. The growth process is driven by kinetics rather than thermodynamics.
Factors Influencing CVD Growth
The process and types of the various possible chemical reactions that occur in a CVD reactor are governed by many complex factors, including the system setup, reactor configuration, gas feedstock, gas ratios, both reactor pressure and gas partial pressures, reaction temperature, growth time, temperature, etc. CVD is an extensively used bottom-up approach for the synthesis of few-layer and single-layer graphene films.
Alternative CVD Methods
Researchers are also exploring alternative CVD methods, such as plasma-enhanced CVD and hot-wire CVD, which offer advantages in terms of scalability, cost, and control over the CNT properties. The most widely used carbon precursor is in gaseous form, such as methane (CH4) gas, which is introduced to the reaction chamber by a gas delivery system.
Importance
Understanding the CVD growth process is important for optimizing the quality and yield of CNTs, as well as for developing new applications and materials based on these unique structures. Moreover, in consideration of both ecological and cost factors, the CVD approach is among the best available routes for the synthesis of graphene-based materials.
In conclusion, the CVD furnace is a vital piece of equipment in the growth of carbon nanotubes and other nanostructures. The CVD growth process involves introducing a hydrocarbon gas into the furnace at high temperatures and allowing it to react with a catalyst such as iron or nickel to form CNTs. Understanding this process is essential for optimizing the quality and yield of CNTs, as well as for developing new applications and materials based on these unique structures.
Types of Carbon Nanotube Growth Mechanisms
Carbon nanotubes are grown using chemical vapor deposition (CVD) method, which involves introducing a carbon-containing gas into a high-temperature furnace, where it decomposes and forms carbon nanotubes on a substrate. There are two primary types of carbon nanotube growth mechanisms in CVD: the base-growth mechanism and the tip-growth mechanism.
Base-Growth Mechanism
In the base-growth mechanism, carbon nanotubes nucleate on the substrate and grow vertically upwards. The diameter of the carbon nanotubes can be controlled by adjusting the size of the catalyst particles. In this mechanism, the temperature and the concentration of the carbon-containing gas play a crucial role in determining the quality and quantity of the carbon nanotubes.
Tip-Growth Mechanism
The tip-growth mechanism involves the growth of carbon nanotubes from a catalyst particle on the substrate, with the nanotube extending outwards from the catalyst particle. The diameter of the nanotube is determined by the size of the catalyst particle, and the length of the nanotube depends on the duration of the growth process. This mechanism is preferred when high-quality, long, and aligned carbon nanotubes are required.
The choice of growth mechanism depends on the desired properties of the carbon nanotubes, as well as the specific requirements of the application. For example, the base-growth mechanism is preferred when a large quantity of carbon nanotubes is required, and the tip-growth mechanism is used when high-quality, long, and aligned carbon nanotubes are required.
In summary, understanding the different types of carbon nanotube growth mechanisms in CVD is crucial for the development of high-quality, functional nanotubes for use in a wide range of fields. The base-growth mechanism is preferred when a large quantity of carbon nanotubes is required, and the tip-growth mechanism is used when high-quality, long, and aligned carbon nanotubes are required. The diameter of the nanotube is determined by the size of the catalyst particle, and the length of the nanotube depends on the duration of the growth process.
Advantages of CVD furnace for carbon nanotube growth
The Chemical Vapor Deposition (CVD) furnace is a versatile piece of equipment for the growth of carbon nanotubes (CNTs). Here are some of the advantages of using a CVD furnace for CNT growth:
Precise control of temperature and gas flow
The CVD process allows for the precise control of temperature and gas flow, which is essential for the formation of high-quality CNTs. This means that the furnace can be operated at high temperatures, up to 1200°C, which is necessary for the synthesis of multi-walled CNTs. The CVD method is highly efficient and can be scaled up for large-scale production of CNTs.
Uniform CNTs with high aspect ratio
The CVD furnace produces uniform CNTs with a high aspect ratio, which is important for applications such as nanoelectronics and energy storage. The furnace allows for the synthesis of different types of CNTs, including single-walled, double-walled, and multi-walled CNTs, with varying diameters and lengths.
High efficiency
The CVD method is highly efficient, and the furnace can be scaled up for large-scale production of CNTs. The highly efficient nature of the CVD furnace allows for the growth of high-quality CNTs in a short period.
Low cost
The CVD furnace is a low-cost method of producing CNTs. The cost of the CVD furnace is much lower than other methods of producing CNTs such as laser ablation and arc discharge.
Versatility
The CVD furnace is a versatile tool for the growth of high-quality CNTs. The furnace can be used to grow CNTs on a variety of substrates, including silicon, glass, and metal.
In conclusion, the CVD furnace is a versatile and reliable tool for the growth of high-quality CNTs. The furnace offers several advantages over other methods of CNT growth, including precise control of temperature and gas flow, the production of uniform CNTs with a high aspect ratio, high efficiency, low cost, and versatility. These advantages make the CVD furnace a critical component in the field of nanotechnology.
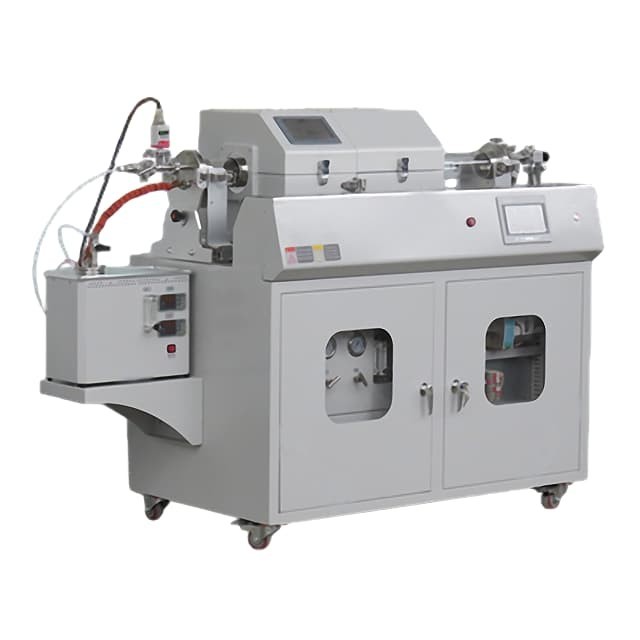
Key Components of CVD Furnace
A CVD furnace is an essential tool for the growth of carbon nanotubes. The furnace is composed of several key components that work together to create the necessary conditions for the deposition of carbon nanotubes on a substrate surface.
Reaction Chamber
The reaction chamber is the heart of the CVD furnace. It is typically made of quartz or alumina and designed to withstand high temperatures and corrosive gases. The chamber provides a controlled environment where the carbon-containing gas reacts with a substrate at high temperatures, resulting in the deposition of carbon nanotubes on the substrate surface.
Gas Delivery System
The gas delivery system is responsible for regulating the flow and composition of the precursor gases, such as methane or ethylene, into the reaction chamber. The gas delivery system must be precise to ensure that the correct amount of gas is delivered at the right time.
Heating System
The heating system is responsible for maintaining a uniform and precise temperature throughout the reaction chamber. The heating system keeps the reaction chamber at a high temperature, which is necessary for the growth of carbon nanotubes. The temperature needs to be monitored and adjusted regularly to ensure that it remains within the range necessary for the specific CVD process.
Vacuum System
The vacuum system creates a low-pressure environment in the reaction chamber, which is necessary to remove unwanted gases and impurities from the reaction chamber. The vacuum system must be capable of maintaining a consistent level of pressure throughout the process, which is critical for the growth of high-quality carbon nanotubes.
Cooling System
The cooling system is responsible for removing heat from the reaction chamber and the substrate after the CVD process is complete. The cooling system must be precise and efficient to prevent the substrate and the carbon nanotubes from being damaged during the cooling process.
Gas Exhaust System
The gas exhaust system is responsible for removing the waste gases produced during the CVD process. It must be able to safely and effectively remove the waste gases, which can be corrosive and harmful to human health.
Control System
The control system is responsible for monitoring and adjusting various parameters, such as temperature, pressure, and gas flow rate during the CVD process. It ensures that the CVD process runs smoothly and efficiently, and that the resulting carbon nanotubes are of high quality.
In conclusion, the CVD furnace is a complex equipment that comprises several key components, including the reaction chamber, gas delivery system, heating system, vacuum system, cooling system, gas exhaust system, and control system. These components work together to create the necessary conditions for the growth of high-quality carbon nanotubes, and their precise control is critical to the success of the CVD process.
Factors Affecting Carbon Nanotube Growth
Carbon nanotubes are widely used in various fields, including electronics, energy, and materials science. The growth of carbon nanotubes in CVD furnaces is a complex process that involves several critical factors.
Temperature
One of the most important factors that affect the growth of carbon nanotubes is temperature. High temperatures are required for the formation of carbon nanotubes, and the optimal temperature range is between 600°C and 1000°C. The temperature must be carefully controlled to achieve high-quality carbon nanotube growth.
Pressure
The pressure within the furnace is also a critical factor that affects the growth of carbon nanotubes. It is necessary to maintain a low-pressure environment to prevent unwanted reactions. The pressure must be carefully controlled to achieve high-quality carbon nanotube growth.
Gas Composition
The gas composition is also crucial for the growth of carbon nanotubes. Carbon-containing gases such as methane or ethylene are required for the growth of carbon nanotubes. The flow rate of these gases also plays a significant role in the growth of carbon nanotubes.
Substrate
The type of substrate used can also affect the growth of carbon nanotubes. The choice of substrate can influence the nucleation and growth of carbon nanotubes, with some materials being more conducive to growth than others. The substrate must be carefully chosen to achieve high-quality carbon nanotube growth.
Catalyst
The catalyst used in the CVD process can also affect the growth of carbon nanotubes. The catalyst can influence the nucleation and growth of carbon nanotubes, with some materials being more conducive to growth than others. The catalyst must be carefully chosen to achieve high-quality carbon nanotube growth.
In conclusion, the growth of carbon nanotubes using CVD furnace is a complex process that requires careful control of several factors. The temperature, pressure, gas composition, substrate, and catalyst are all critical factors that affect the growth of carbon nanotubes. By carefully controlling these factors, high-quality carbon nanotube growth can be achieved.
Applications of Carbon Nanotubes
Carbon nanotubes (CNTs) are highly versatile materials with a wide range of applications in various fields. The exceptional electrical, mechanical, and thermal properties of CNTs make them highly sought after in research and development. Here are some of the most promising applications of CNTs.
Electronics
CNTs have exceptional electrical conductivity, which makes them ideal for use in electronics. They have been used as transistors, interconnects, and sensors due to their electrical properties. The high aspect ratio of CNTs makes them ideal for use in field emission displays and CRTs. Researchers are exploring the use of CNTs in flexible electronics, where their high flexibility can be utilized to create flexible and stretchable circuits.
Energy Storage
CNTs' high surface area and electrical conductivity make them ideal for use in energy storage devices. They have been used as electrodes in supercapacitors and batteries, where they have shown promising results. CNTs are also being explored as a potential material for fuel cells, where their high conductivity can be utilized to improve efficiency.
Biomedicine
CNTs have shown great potential as a material for drug delivery, imaging, and biosensors in biomedicine. The high aspect ratio and biocompatibility of CNTs make them ideal for use in drug delivery systems, where they can be used to target specific cells. CNTs are also being explored as imaging agents, where their high contrast can be utilized to improve imaging techniques.
Materials Science
CNTs' exceptional mechanical, thermal, and electrical properties make them ideal for use in materials science. They have been used to improve the mechanical properties of composites, where they can be added to improve strength and stiffness. CNTs are also being explored as a potential material for thermal management, where their high thermal conductivity can be utilized to improve heat dissipation.
In conclusion, the exceptional properties of CNTs make them highly versatile materials with a wide range of applications in various fields. The potential applications of CNTs are diverse, including electronics, energy storage, biomedicine, and materials science. As research continues to advance, it is likely that even more applications for CNTs will be discovered in the future.
Future of CVD Furnace Technology
CVD furnaces are the backbone of carbon nanotube production and their future lies in improving the efficiency and scalability of CNT production. Here are some promising areas of development for CVD furnace technology:
Multi-Zone Furnaces
One promising area of development is the use of multi-zone furnaces. These furnaces allow for better control over the temperature and gas flow during CNT growth. This can improve the uniformity of CNTs and reduce defects, leading to higher quality materials.
Alternative Carbon Sources
Researchers are exploring the use of alternative carbon sources, such as carbon dioxide and carbon monoxide. These sources could potentially reduce the environmental impact of CNT production and make the process more sustainable.
Portable CVD Systems
Another area of focus is the development of portable CVD systems. These systems could enable on-site production of CNTs for various applications. This could have significant benefits for industries that require CNTs but don't have easy access to them.
Improved Efficiency and Scalability
Overall, the continued development of CVD furnace technology is essential for advancing the field of CNTs and realizing their potential in various industries. Efforts are being made to improve the efficiency and scalability of CNT production. This includes optimizing the growth rate of CVD diamond and getting perfect diamond crystals.
Synthetic Diamond
Synthetic diamond of large single crystal and nanometer diamond films are also areas of development. Synthetic diamond of large single crystal has the same excellent properties as natural diamond and can achieve ultra-precision machining by using tools of this diamond material. Nanometer diamond has properties of nanometer materials and diamond materials and can be used as a tool coating material to improve efficiency and extend tool life.
The future of CVD furnace technology is exciting and holds great promise for the advancement of various industries.
CONTACT US FOR A FREE CONSULTATION
KINTEK LAB SOLUTION's products and services have been recognized by customers around the world. Our staff will be happy to assist with any inquiry you might have. Contact us for a free consultation and talk to a product specialist to find the most suitable solution for your application needs!