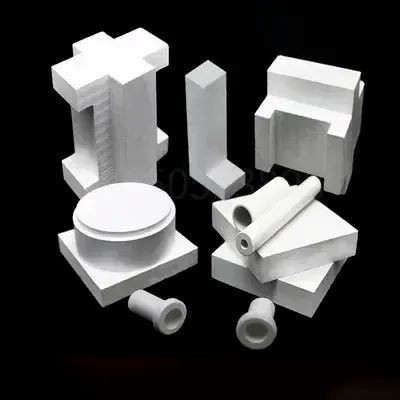
fine ceramics
Advanced Engineering Fine Ceramics Boron Nitride (BN) Ceramic Parts
Item Number : KM-P01
Price varies based on specs and customizations
- Material
- Boron nitride (BN)
- Specification
- Customizable
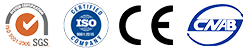
Shipping:
Contact us to get shipping details Enjoy On-time Dispatch Guarantee.
Why Choose Us
Reliable PartnerEasy ordering process, quality products, and dedicated support for your business success.
Application
Boron nitride (BN) is a compound with equal numbers of boron and nitrogen atoms. An advanced synthetic ceramic material available in powder, solid, liquid or aerosol form. It has excellent temperature resistance, dielectric strength and thermal conductivity. Due to these various properties, boron nitride is an easy-to-process material. To obtain sintered boron nitride, boron nitride powder needs to be pressed at very high temperatures. Because of these lubricating abilities and good thermal conductivity, boron nitride is comparable to graphite, although it is white and has very good electrical insulating capabilities.
- Ion implantation equipment: BN components are used for ion source brackets, wafer chucks, crucibles and other components.
- Vacuum system: BN acts as an insulator in a vacuum system to provide electrical insulation and prevent arcing.
- Glass Melting: BN gaskets seal glass melting furnace components, maintaining operating conditions.
- High voltage equipment: BN components enable efficient power transmission and insulation.
- PVD, MOCVD, MBE system: BN parts can withstand high temperature and corrosive environment in thin film deposition.
- Thermocouple Protection: BN protects thermocouples in high temperature environments.
- Casting Tool Protection: BN coating prevents molten metal from adhering to molds and cores.
- High temperature electrical insulation: BN insulates electrical systems in high temperature environments.
- Melting and Sintering Crucibles: BN crucibles handle high temperature molten materials.
- Resistor support: BN supports the resistance, dissipates heat and prevents conduction.
- Solar energy and photovoltaic industry: BN is used in furnace bodies, pipes, insulating sleeves and coatings.
- Furnace body structure: BN is used for pipes and insulation sleeves, which has good high temperature stability.
- Brazing: Boron nitride parts such as nozzles and brackets are used in brazing applications.
Detail & Parts
The produce we show are available in different sizes and custom sizes are available on request.
Advantages
- High thermal conductivity
- Low thermal expansion
- Excellent Dielectric Resistance
- Microwave transparency
- Easy to process
- Low wettability to molten metal
- Relatively high thermal conductivity and low thermal expansion
- High thermal shock resistance compared to other ceramics
- Extremely high operating temperature with proper inert gas protection (>3000C documented).
FAQ
What Are The Applications Of Boron Nitride Ceramic Parts?
What Are Advanced Ceramics?
What Are The Main Applications Of Fine Ceramics?
What Are Engineering Ceramics?
What Are The Advantages Of Using Boron Nitride Ceramic Parts?
What Are The Main Types Of Advanced Ceramics?
What Are The Main Types Of Fine Ceramics?
What Are The Main Types Of Engineering Ceramics?
What Considerations Should Be Made When Selecting Boron Nitride Ceramic Parts?
What Are The Applications Of Advanced Ceramics?
What Is The Principle Behind Fine Ceramics?
What Are The Applications Of Engineering Ceramics?
What Manufacturing Processes Are Used To Produce Boron Nitride Ceramic Parts?
How Are Advanced Ceramics Manufactured?
What Are The Advantages Of Using Fine Ceramics?
How Do Engineering Ceramics Differ From Traditional Ceramics?
What Are The Advantages Of Using Advanced Ceramics?
What Are The Advantages Of Using Alumina Ceramics?
What Is The Difference Between Alumina And Zirconia Ceramics?
Why Are Zirconia Ceramics Preferred In Certain Applications?
Why Are Silicon Carbide Ceramics Used In High-temperature Applications?
What Makes Silicon Carbide Ceramics Suitable For High-temperature Applications?
What Makes Boron Nitride Ceramics Unique?
How Are Boron Nitride Ceramics Used In Electronics?
How Do Advanced Ceramics Contribute To Energy Efficiency?
What Is The Manufacturing Process Of Engineering Ceramics?
Can Engineering Ceramics Be Customized For Specific Applications?
4.9
out of
5
The Boron Nitride ceramic parts from KINTEK SOLUTION are a game-changer for our lab. Their exceptional quality and durability have significantly improved our research outcomes.
4.8
out of
5
KINTEK SOLUTION's Boron Nitride ceramic parts are a testament to their commitment to innovation. They offer unmatched performance and reliability, making them an invaluable asset to our laboratory.
4.7
out of
5
The prompt delivery and excellent customer service from KINTEK SOLUTION were the icing on the cake. Their Boron Nitride ceramic parts are a fantastic addition to our lab's equipment.
4.9
out of
5
KINTEK SOLUTION's Boron Nitride ceramic parts are worth every penny. Their exceptional quality and durability have saved us both time and money in the long run.
4.8
out of
5
The technological advancements incorporated into KINTEK SOLUTION's Boron Nitride ceramic parts are truly remarkable. They have revolutionized our research capabilities.
4.7
out of
5
KINTEK SOLUTION's Boron Nitride ceramic parts are a testament to their commitment to excellence. They have exceeded our expectations in terms of quality, performance, and durability.
4.9
out of
5
The Boron Nitride ceramic parts from KINTEK SOLUTION are a game-changer for our lab. Their exceptional quality and durability have significantly improved our research outcomes.
4.8
out of
5
KINTEK SOLUTION's Boron Nitride ceramic parts are a testament to their commitment to innovation. They offer unmatched performance and reliability, making them an invaluable asset to our laboratory.
4.7
out of
5
The prompt delivery and excellent customer service from KINTEK SOLUTION were the icing on the cake. Their Boron Nitride ceramic parts are a fantastic addition to our lab's equipment.
4.9
out of
5
KINTEK SOLUTION's Boron Nitride ceramic parts are worth every penny. Their exceptional quality and durability have saved us both time and money in the long run.
4.8
out of
5
The technological advancements incorporated into KINTEK SOLUTION's Boron Nitride ceramic parts are truly remarkable. They have revolutionized our research capabilities.
4.7
out of
5
KINTEK SOLUTION's Boron Nitride ceramic parts are a testament to their commitment to excellence. They have exceeded our expectations in terms of quality, performance, and durability.
4.9
out of
5
The Boron Nitride ceramic parts from KINTEK SOLUTION are a game-changer for our lab. Their exceptional quality and durability have significantly improved our research outcomes.
Products
Advanced Engineering Fine Ceramics Boron Nitride (BN) Ceramic Parts
REQUEST A QUOTE
Our professional team will reply to you within one business day. Please feel free to contact us!
Related Products
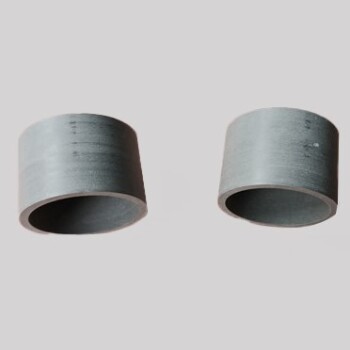
Conductive Boron Nitride BN Ceramics Composite for Advanced Applications
Due to the characteristics of boron nitride itself, the dielectric constant and dielectric loss are very small, so it is an ideal electrical insulating material.
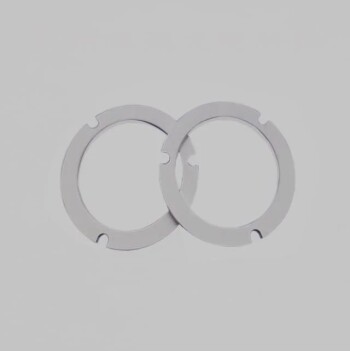
Hexagonal Boron Nitride HBN Ceramic Ring
Boron nitride ceramic (BN) rings are commonly used in high temperature applications such as furnace fixtures, heat exchangers and semiconductor processing.
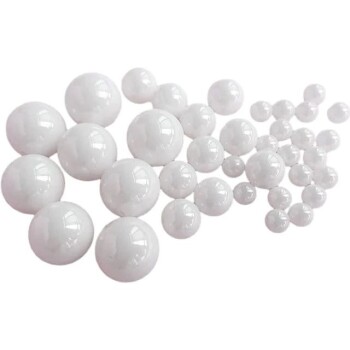
Precision Machined Zirconia Ceramic Ball for Engineering Advanced Fine Ceramics
zirconia ceramic ball have the characteristics of high strength, high hardness, PPM wear level, high fracture toughness, good wear resistance, and high specific gravity.
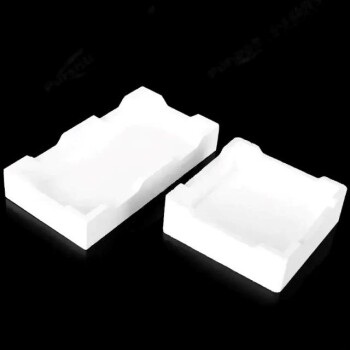
Advanced Engineering Fine Ceramics Alumina Ceramic Saggar for Fine Corundum
Alumina sagger products have the characteristics of high temperature resistance, good thermal shock stability, small expansion coefficient, anti-stripping, and good anti-powdering performance.
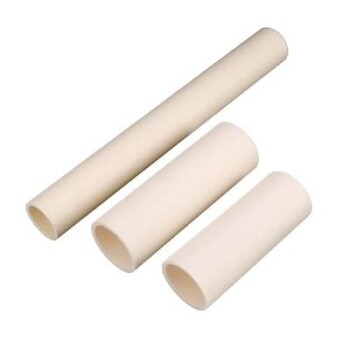
High Temperature Alumina (Al2O3) Furnace Tube for Engineering Advanced Fine Ceramics
High temperature alumina furnace tube combines the advantages of high hardness of alumina, good chemical inertness and steel, and has excellent wear resistance, thermal shock resistance and mechanical shock resistance.

Zirconia Ceramic Gasket Insulating Engineering Advanced Fine Ceramics
Zirconia insulating ceramic gasket has high melting point, high resistivity, low thermal expansion coefficient and other properties, making it an important high temperature resistant material, ceramic insulating material and ceramic sunscreen material.
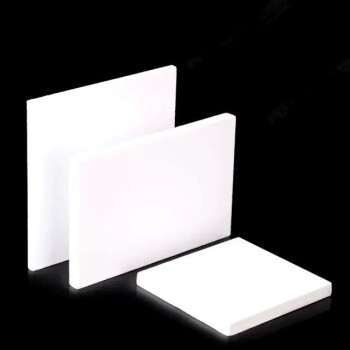
High Temperature Wear-Resistant Alumina Al2O3 Plate for Engineering Advanced Fine Ceramics
High temperature wear-resistant insulating alumina plate has excellent insulation performance and high temperature resistance.
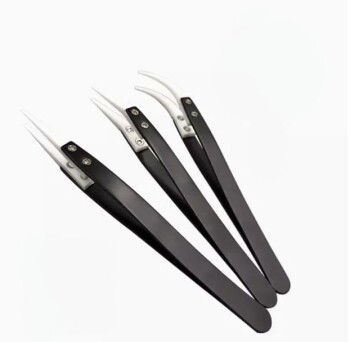
Engineering Advanced Fine Ceramics Head Tweezers with Pointed Elbow Zirconia Ceramic Tip
Zirconia ceramic tweezers are a high-precision tool made of advanced ceramic materials, especially suitable for operating environments that require high precision and corrosion resistance. This type of tweezers not only has excellent physical properties, but is also popular in the medical and laboratory fields because of its biocompatibility.

Silicon Carbide (SIC) Ceramic Sheet Wear-Resistant Engineering Advanced Fine Ceramics
Silicon carbide (sic) ceramic sheet is composed of high-purity silicon carbide and ultra-fine powder, which is formed by vibration molding and high-temperature sintering.
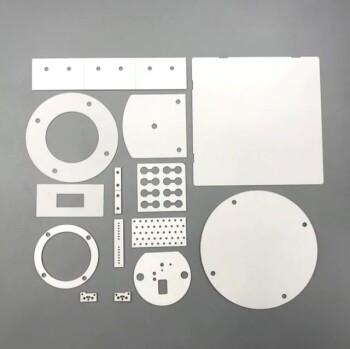
Alumina ceramics have good electrical conductivity, mechanical strength and high temperature resistance, while zirconia ceramics are known for their high strength and high toughness and are widely used.
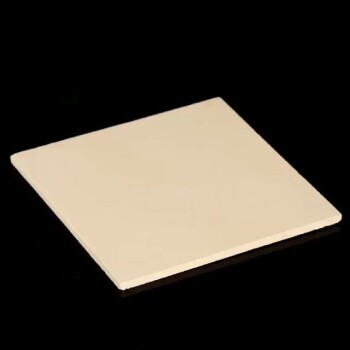
Precision Machined Yttria Stabilized Zirconia Ceramic Plate for Engineering Advanced Fine Ceramics
Yttrium-stabilized zirconia has the characteristics of high hardness and high temperature resistance, and has become an important material in the field of refractories and special ceramics.
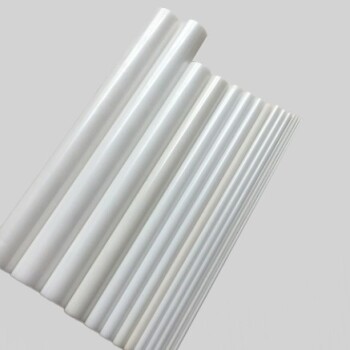
Precision Machined Yttrium Stabilized Zirconia Ceramic Rod for Engineering Advanced Fine Ceramics
Zirconia ceramic rods are prepared by isostatic pressing, and a uniform, dense and smooth ceramic layer and transition layer are formed at high temperature and high speed.
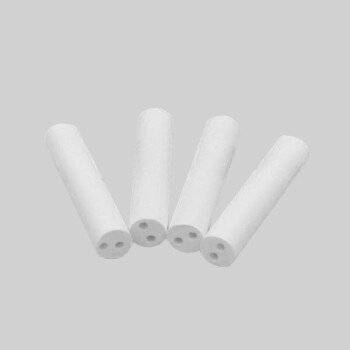
Hexagonal Boron Nitride HBN Thermocouple Protection Tube
Hexagonal boron nitride ceramics is an emerging industrial material. Because of its similar structure to graphite and many similarities in performance, it is also called "white graphite".
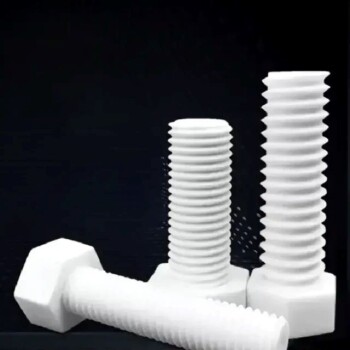
Alumina ceramic screws are fastening components made of 99.5% alumina, ideal for extreme applications requiring excellent thermal resistance, electrical insulation and chemical resistance.
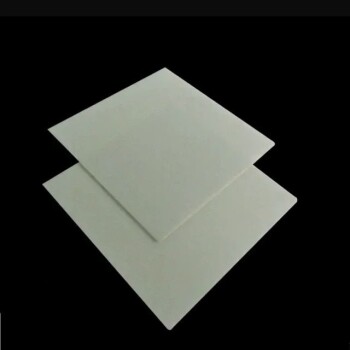
Precision Machined Silicon Nitride (SiN) Ceramic Sheet for Engineering Advanced Fine Ceramics
Silicon nitride plate is a commonly used ceramic material in the metallurgical industry due to its uniform performance at high temperatures.
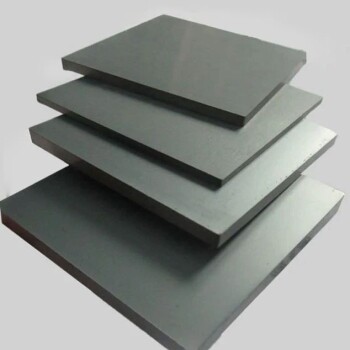
Silicon Carbide (SIC) Ceramic Plate for Engineering Advanced Fine Ceramics
Silicon nitride (sic) ceramic is an inorganic material ceramic that does not shrink during sintering. It is a high-strength, low-density, high-temperature-resistant covalent bond compound.
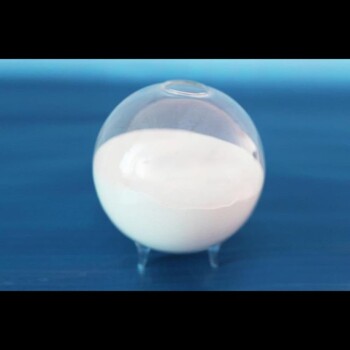
High Purity Alumina Granulated Powder for Engineering Advanced Fine Ceramics
Ordinary alumina granulated powder is alumina particles prepared by traditional processes, with a wide range of applications and good market adaptability. This material is known for its high purity, excellent thermal stability and chemical stability, and is suitable for a variety of high-temperature and conventional applications.
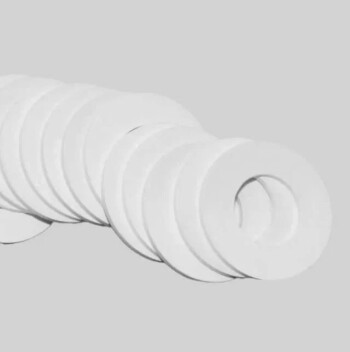
Hexagonal Boron Nitride HBN Spacer Cam Profile and Various Spacer Types
Hexagonal boron nitride (HBN) gaskets are made from hot-pressed boron nitride blanks. Mechanical properties similar to graphite, but with excellent electrical resistance.
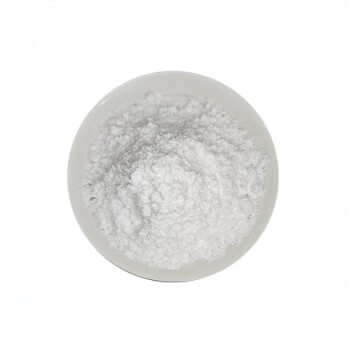
Advanced Engineering Fine Ceramics Low Temperature Alumina Granulation Powder
Low temperature alumina granulation powder is a kind of alumina particles produced by a special low temperature process, designed to meet the needs of temperature sensitive applications. This material has excellent low temperature performance and good processing characteristics, suitable for a variety of industries that require low temperature processing and treatment.
Related Articles
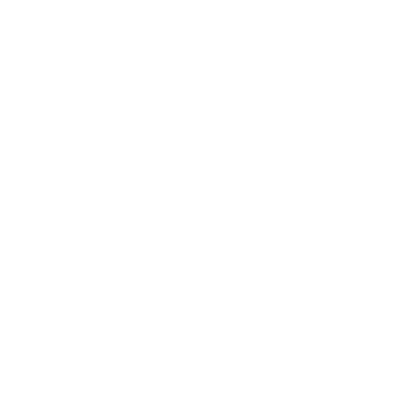
CVD furnace for the growth of carbon nanotubes
Chemical vapor deposition (CVD) furnace technology is a widely used method for growing carbon nanotubes.
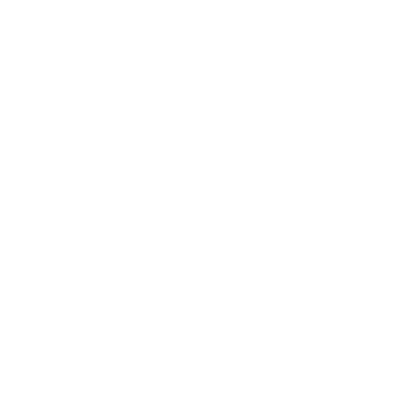
Isostatic Pressing A Low Distortion Alternative to Extrusion
Isostatic pressing is a manufacturing process that uses high pressure to compress powdered materials into a specific shape or form.
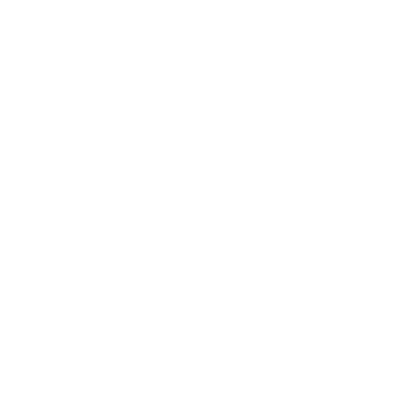
Hexagonal Boron Nitride: Enhancing Performance in Composite Ceramic Materials
Explores the role of h-BN in various composite ceramics, highlighting its properties and applications.
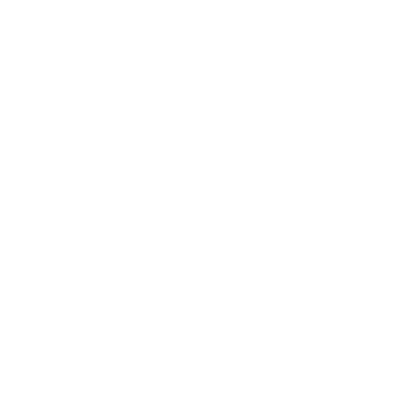
The Future of Lab Presses in Research and Development
Lab presses are an essential tool in research and development for a wide range of industries, including pharmaceuticals, materials science, and electronics.
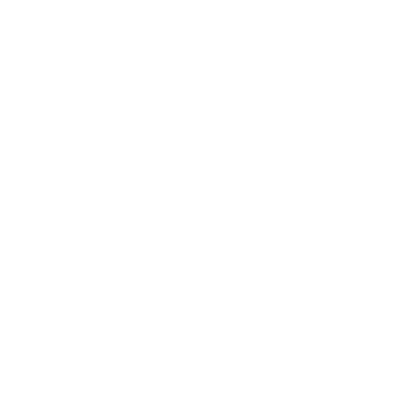
Comparison of Pyrolytic Graphite and Pyrolytic Boron Nitride Crucibles
A detailed comparison of pyrolytic graphite and pyrolytic boron nitride crucibles, focusing on their preparation processes, characteristics, and applications.
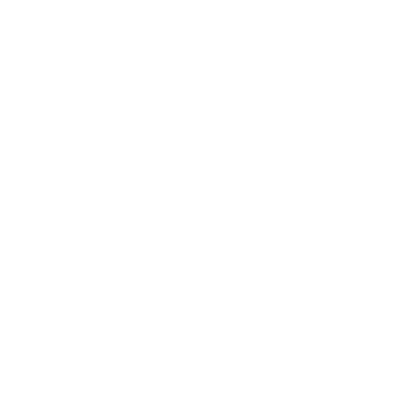
Guidelines for the Use of Boron Nitride Crucibles
Instructions on the proper use, precautions, and compatibility of boron nitride crucibles.
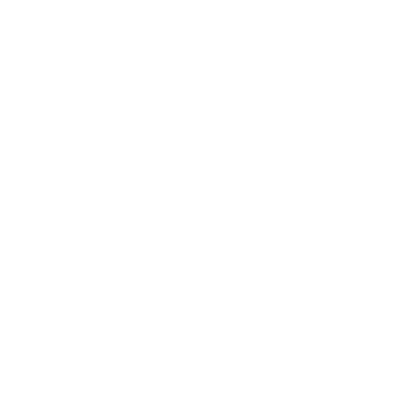
Applications and Advances in Vacuum Hot Press Sintering Furnaces for Precision Ceramics
Explores the use of vacuum hot press sintering for advanced ceramics, metal/ceramic welding, and industry trends.
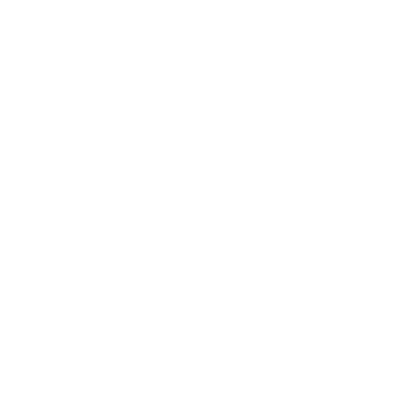
Precision Ceramics in Semiconductor Applications
Exploring the use of precision ceramics in semiconductor equipment, their properties, and manufacturing processes.
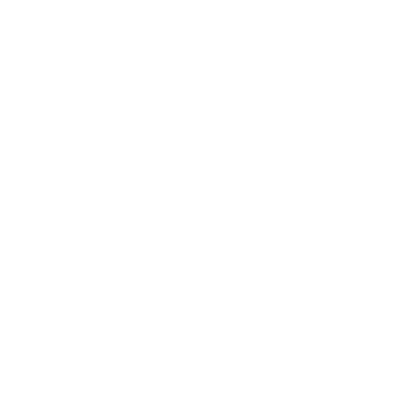
Precision Ceramic Materials for Energy Conversion Applications
Overview of various ceramic materials used in energy conversion technologies, including heaters, piezoelectric ceramics, and solid oxide fuel cells.
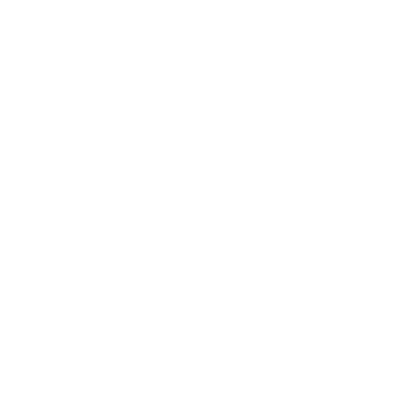
Defects and Solutions for Isostatically Pressed Ceramic Balls
This article discusses various defects in isostatically pressed ceramic balls and provides solution strategies for each type of defect.
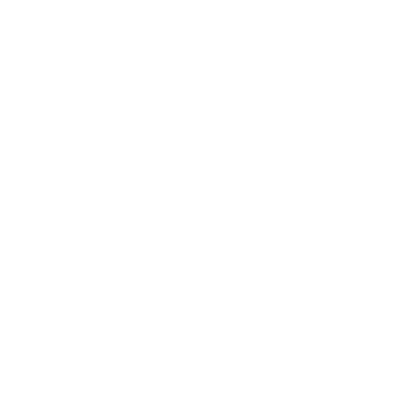
The 5 Hottest Advanced Ceramic Powders Currently Available!
An overview of the top 5 advanced ceramic powders: High Purity Aluminum Oxide, Boehmite, Aluminum Nitride, Silicon Nitride, and Spherical Alumina, highlighting their applications and market trends.
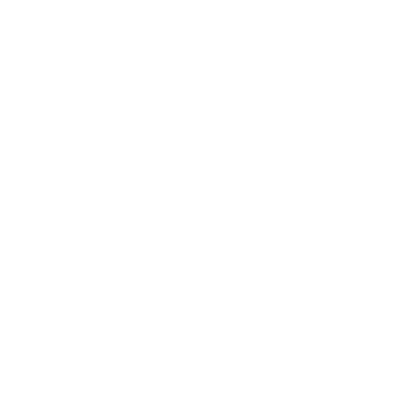
Engineering Ceramic Materials: Applications in Aerospace, Electronic Information, New Energy, and Environmental Protection
This article explores the diverse applications of engineering ceramic materials across aerospace, electronic information, new energy, and environmental protection sectors.