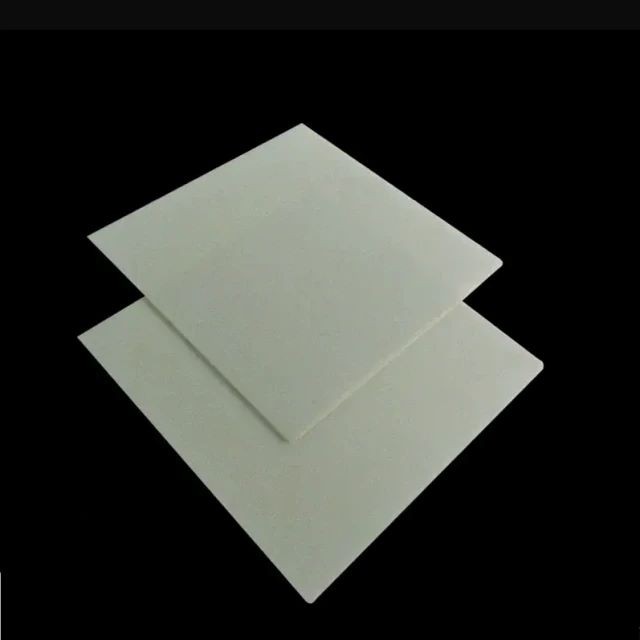
fine ceramics
Precision Machined Silicon Nitride (SiN) Ceramic Sheet for Engineering Advanced Fine Ceramics
Item Number : KM-DG04
Price varies based on specs and customizations
- Material
- Silicon nitride
- Specification
- See the form
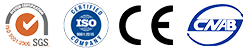
Shipping:
Contact us to get shipping details Enjoy On-time Dispatch Guarantee.
Why Choose Us
Reliable PartnerEasy ordering process, quality products, and dedicated support for your business success.
Application
Silicon nitride ceramic is an inorganic material that maintains its shape during sintering and has uniform properties at high temperatures. It is a commonly used ceramic material in the metallurgical industry. Silicon nitride plates have excellent thermal shock resistance due to their microstructure. Silicon nitride also has excellent creep and oxidation resistance, as well as its low thermal conductivity and high wear resistance, making it an excellent material capable of withstanding the conditions of most industrial applications.
- Hybrid integrated circuit interconnection substrate: used as the substrate for the interconnection of electronic components in hybrid integrated circuits.
- Microwave Devices: Silicon nitride substrates are used in the manufacture of microwave components.
- Optoelectronic Communications: For the production of optoelectronic devices used in communication systems.
- Sensing applications: Silicon nitride substrates are used to manufacture sensors in various industries.
- Power electronics substrates: Silicon nitride's high flexural strength, fracture toughness and good thermal conductivity make it ideal for power electronics substrates.
Detail & Parts
Technical specifications
10*10*0.35mm | 20*20*0.35mm | 140*190*0.32mm | 114*114*0.35mm | 114*114*0.75mm |
The produce we show are available in different sizes and custom sizes are available on request.
Advantages
- High mechanical strength at high temperature.
- Excellent wear resistance and self-lubrication properties, including high load capacity and abrasive environments.
- Low thermal expansion and high thermal conductivity ensure dimensional stability and efficient heat dissipation.
- High fracture toughness, not easy to crack or break.
- The high hardness makes silicon nitride one of the hardest substances known.
- Good thermal shock resistance, enabling it to withstand sudden temperature changes without damage.
- Good chemical and oxidation resistance, making it suitable for use in corrosive environments.
FAQ
What Are The Main Applications Of Fine Ceramics?
What Are Advanced Ceramics?
What Are Engineering Ceramics?
Comparison Of Si3N4 And Other Ceramics.
What Are The Main Types Of Fine Ceramics?
What Are The Main Types Of Advanced Ceramics?
What Are The Main Types Of Engineering Ceramics?
What Is The Principle Behind Fine Ceramics?
What Are The Applications Of Advanced Ceramics?
What Are The Applications Of Engineering Ceramics?
What Are The Advantages Of Using Fine Ceramics?
How Are Advanced Ceramics Manufactured?
How Do Engineering Ceramics Differ From Traditional Ceramics?
What Are The Advantages Of Using Advanced Ceramics?
What Are The Advantages Of Using Alumina Ceramics?
What Is The Difference Between Alumina And Zirconia Ceramics?
Why Are Zirconia Ceramics Preferred In Certain Applications?
Why Are Silicon Carbide Ceramics Used In High-temperature Applications?
What Makes Silicon Carbide Ceramics Suitable For High-temperature Applications?
What Makes Boron Nitride Ceramics Unique?
How Are Boron Nitride Ceramics Used In Electronics?
How Do Advanced Ceramics Contribute To Energy Efficiency?
What Is The Manufacturing Process Of Engineering Ceramics?
Can Engineering Ceramics Be Customized For Specific Applications?
4.7
out of
5
The delivery was super fast! I received it within a few days of ordering.
4.8
out of
5
I've been using this product for a while now and I can say that it's definitely worth the money. It's made of high-quality materials and it's very durable.
4.9
out of
5
This product is simply amazing! It's so easy to use and it works perfectly. I highly recommend it!
4.8
out of
5
I was really impressed with the quality of this product. It's very well-made and it's clear that a lot of thought went into its design.
4.7
out of
5
This product is exactly what I was looking for. It's perfect for my needs and it's made of high-quality materials.
4.9
out of
5
I'm so glad I found this product. It's made my work so much easier and I'm really happy with the results.
4.8
out of
5
This product is a real lifesaver! It's so easy to use and it's made such a difference in my work.
4.7
out of
5
I was really impressed with the customer service I received from this company. They were very helpful and answered all of my questions.
4.9
out of
5
This product is a game-changer! It's so much better than the other products I've tried.
4.8
out of
5
I'm really happy with this product. It's made a big difference in my work and I would definitely recommend it to others.
Products
Precision Machined Silicon Nitride (SiN) Ceramic Sheet for Engineering Advanced Fine Ceramics
REQUEST A QUOTE
Our professional team will reply to you within one business day. Please feel free to contact us!
Related Products
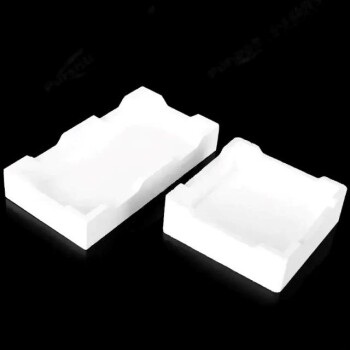
Advanced Engineering Fine Ceramics Alumina Ceramic Saggar for Fine Corundum
Alumina sagger products have the characteristics of high temperature resistance, good thermal shock stability, small expansion coefficient, anti-stripping, and good anti-powdering performance.
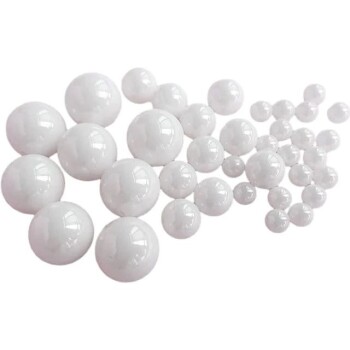
Precision Machined Zirconia Ceramic Ball for Engineering Advanced Fine Ceramics
zirconia ceramic ball have the characteristics of high strength, high hardness, PPM wear level, high fracture toughness, good wear resistance, and high specific gravity.

Silicon Carbide (SIC) Ceramic Sheet Wear-Resistant Engineering Advanced Fine Ceramics
Silicon carbide (sic) ceramic sheet is composed of high-purity silicon carbide and ultra-fine powder, which is formed by vibration molding and high-temperature sintering.
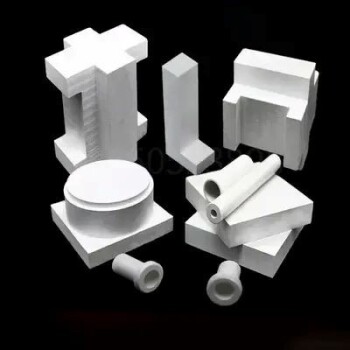
Advanced Engineering Fine Ceramics Boron Nitride (BN) Ceramic Parts
Boron nitride ((BN) is a compound with high melting point, high hardness, high thermal conductivity and high electrical resistivity. Its crystal structure is similar to graphene and harder than diamond.
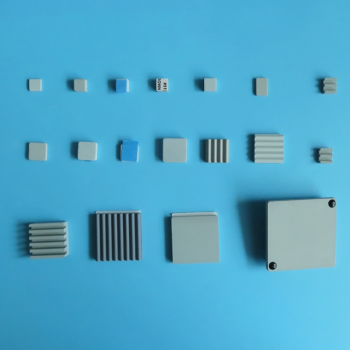
Silicon Carbide (SIC) Ceramic Sheet Flat Corrugated Heat Sink for Engineering Advanced Fine Ceramics
Silicon carbide (sic) ceramic heat sink not only does not generate electromagnetic waves, but also can isolate electromagnetic waves and absorb part of electromagnetic waves.

Zirconia Ceramic Gasket Insulating Engineering Advanced Fine Ceramics
Zirconia insulating ceramic gasket has high melting point, high resistivity, low thermal expansion coefficient and other properties, making it an important high temperature resistant material, ceramic insulating material and ceramic sunscreen material.
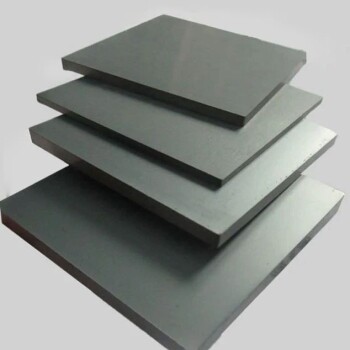
Silicon Carbide (SIC) Ceramic Plate for Engineering Advanced Fine Ceramics
Silicon nitride (sic) ceramic is an inorganic material ceramic that does not shrink during sintering. It is a high-strength, low-density, high-temperature-resistant covalent bond compound.
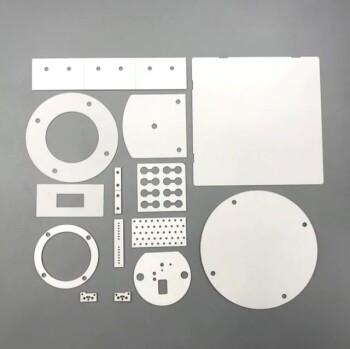
Alumina ceramics have good electrical conductivity, mechanical strength and high temperature resistance, while zirconia ceramics are known for their high strength and high toughness and are widely used.
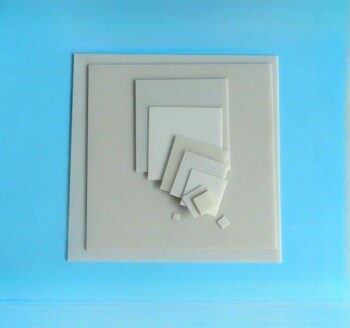
Advanced Engineering Fine Ceramics Aluminum Nitride (AlN) Ceramic Sheet
Aluminum nitride (AlN) has the characteristics of good compatibility with silicon. It is not only used as a sintering aid or reinforcing phase for structural ceramics, but its performance far exceeds that of alumina.
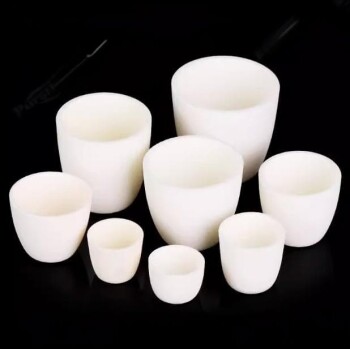
In the journey of scientific exploration and industrial production, every detail is crucial. Our arc-shaped alumina ceramic crucibles, with their excellent high temperature resistance and stable chemical properties, have become a powerful assistant in laboratories and industrial fields. They are made of high-purity alumina materials and manufactured through precision processes to ensure excellent performance in extreme environments.
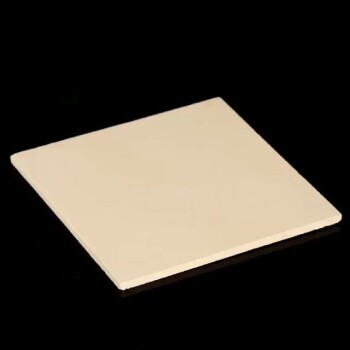
Precision Machined Yttria Stabilized Zirconia Ceramic Plate for Engineering Advanced Fine Ceramics
Yttrium-stabilized zirconia has the characteristics of high hardness and high temperature resistance, and has become an important material in the field of refractories and special ceramics.
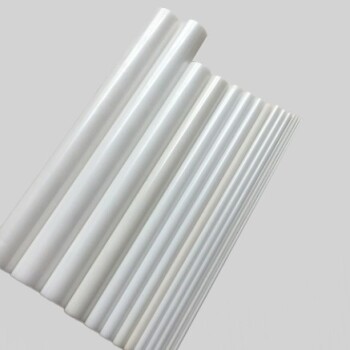
Precision Machined Yttrium Stabilized Zirconia Ceramic Rod for Engineering Advanced Fine Ceramics
Zirconia ceramic rods are prepared by isostatic pressing, and a uniform, dense and smooth ceramic layer and transition layer are formed at high temperature and high speed.
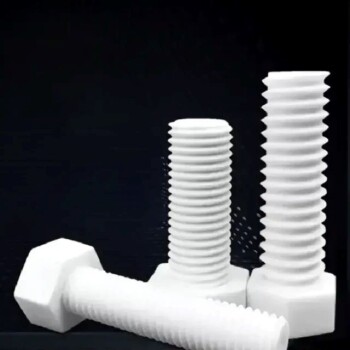
Alumina ceramic screws are fastening components made of 99.5% alumina, ideal for extreme applications requiring excellent thermal resistance, electrical insulation and chemical resistance.
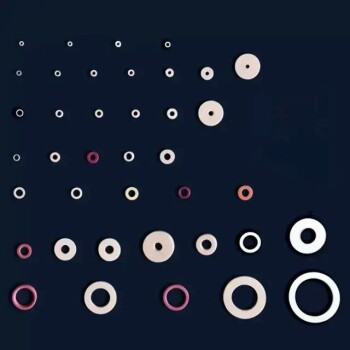
Alumina wear-resistant ceramic washer are used for heat dissipation, which can replace aluminum heat sinks, with high temperature resistance and high thermal conductivity.
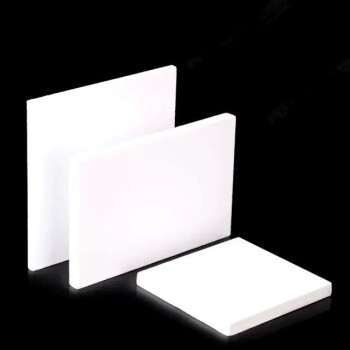
High Temperature Wear-Resistant Alumina Al2O3 Plate for Engineering Advanced Fine Ceramics
High temperature wear-resistant insulating alumina plate has excellent insulation performance and high temperature resistance.
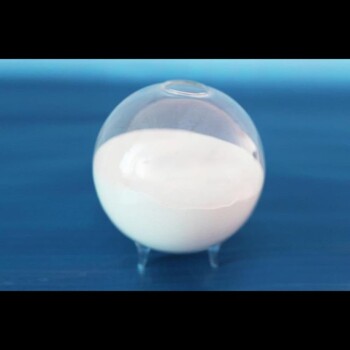
High Purity Alumina Granulated Powder for Engineering Advanced Fine Ceramics
Ordinary alumina granulated powder is alumina particles prepared by traditional processes, with a wide range of applications and good market adaptability. This material is known for its high purity, excellent thermal stability and chemical stability, and is suitable for a variety of high-temperature and conventional applications.
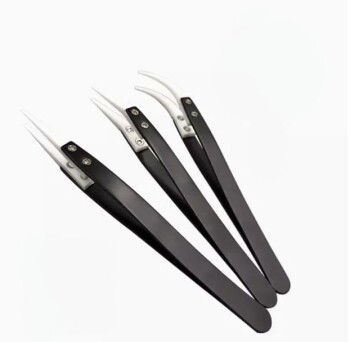
Engineering Advanced Fine Ceramics Head Tweezers with Pointed Elbow Zirconia Ceramic Tip
Zirconia ceramic tweezers are a high-precision tool made of advanced ceramic materials, especially suitable for operating environments that require high precision and corrosion resistance. This type of tweezers not only has excellent physical properties, but is also popular in the medical and laboratory fields because of its biocompatibility.
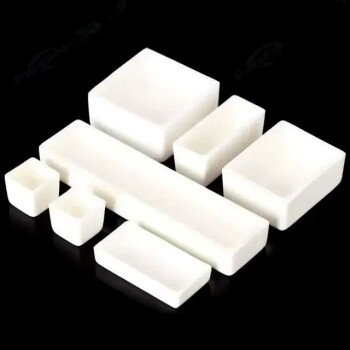
Engineering Advanced Fine Alumina Al2O3 Ceramic Crucible for Laboratory Muffle Furnace
Alumina ceramic crucibles are used in some materials and metal melting tools, and flat-bottomed crucibles are suitable for melting and processing larger batches of materials with better stability and uniformity.
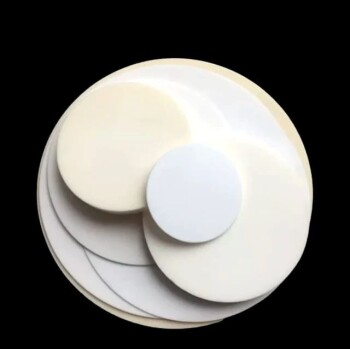
Engineering Advanced Fine Ceramics Aluminum Oxide Al2O3 Heat Sink for Insulation
The hole structure of the ceramic heat sink increases the heat dissipation area in contact with the air, which greatly enhances the heat dissipation effect, and the heat dissipation effect is better than that of super copper and aluminum.
Related Articles
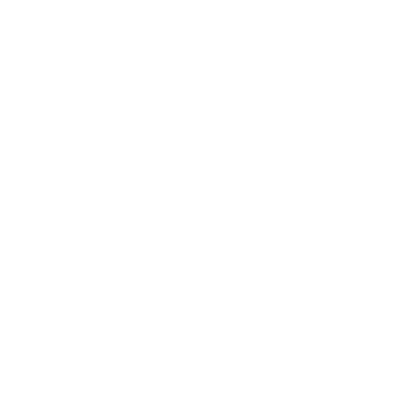
Precautions for installing silicon carbide stick
Precautions for installing silicon carbide stic.
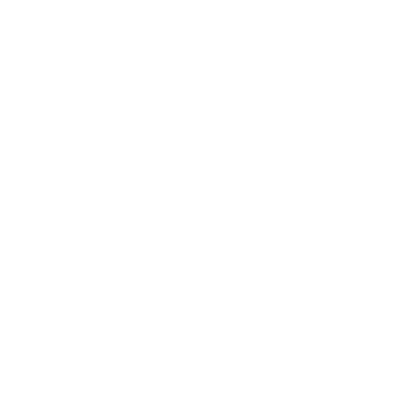
Optical Quartz Plate: A Comprehensive Guide to Applications, Specifications, and Usage
Discover the versatility of optical quartz plates, exploring their uses in various industries, key specifications, and factors that differentiate them from glass. Gain insights into their applications in ultraviolet transmission, precision optics, and more.
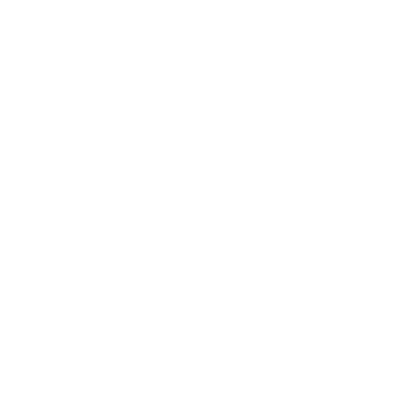
Why PECVD is Essential for Microelectronic Device Fabrication
PECVD (Plasma-Enhanced Chemical Vapor Deposition) is a popular thin film deposition technique used in microelectronics device fabrication.
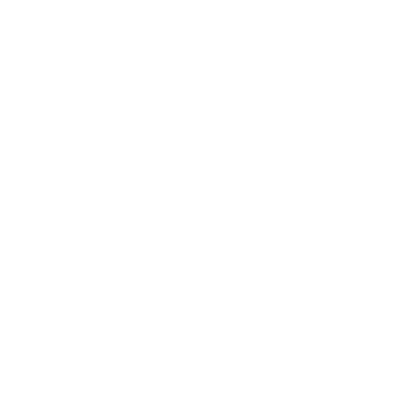
Isostatic Pressing of Ceramics: Process and Precision
When it comes to producing high-quality ceramic components, one of the most crucial processes is isostatic pressing. This technique ensures the uniformity and precision required for manufacturing ceramics used in various industries. Isostatic pressing involves carefully selecting the pressing powders and controlling the tools to achieve the desired uniformity. By understanding the process of isostatic pressing, manufacturers can ensure the production of ceramics that meet the strict standards of dimensional accuracy and performance.
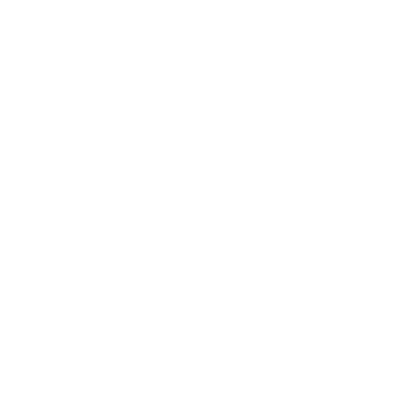
The Role of Plasma in PECVD Coatings
PECVD (Plasma Enhanced Chemical Vapor Deposition) is a type of thin film deposition process that is widely used for creating coatings on various substrates. In this process, a plasma is used to deposit thin films of various materials onto a substrate.
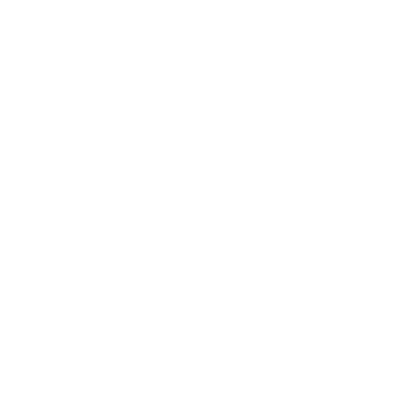
Unveiling the Exceptional Properties and Applications of Optical Quartz Plates
Discover the remarkable characteristics and diverse applications of optical quartz plates, including their superior ultraviolet transmission, thermal stability, and use in lenses, lighting devices, and semiconductor manufacturing.
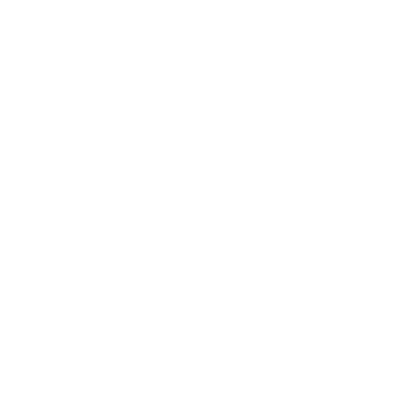
The Benefits of Cold Isostatic Pressing
Cold Isostatic Pressing (CIP) is a process used to compact powders into a specific shape or size. This method involves subjecting the powders to high pressure, typically between 100 and 200 MPa, in a liquid medium.
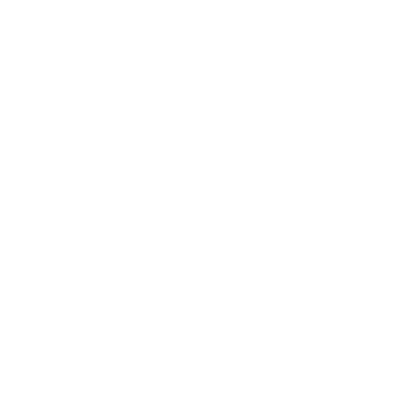
Understanding Cold Isostatic Pressing: Process, Advantages and Types
Cold Isostatic Pressing (CIP), also known as cold isostatic compaction, is a materials processing technique that involves subjecting a material to uniform pressure from all sides. This is achieved by immersing the material in a high-pressure fluid medium and applying hydraulic pressure. CIP is particularly effective for shaping and consolidating powdered materials, allowing for the creation of intricate shapes and achieving high green density.
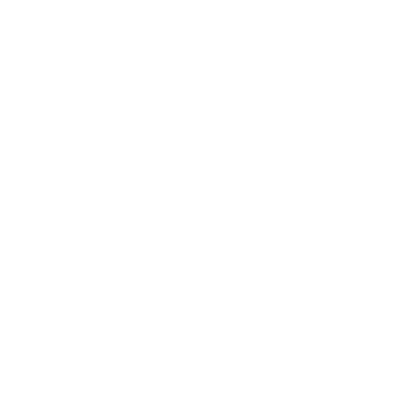
The Future of Lab Presses in Research and Development
Lab presses are an essential tool in research and development for a wide range of industries, including pharmaceuticals, materials science, and electronics.
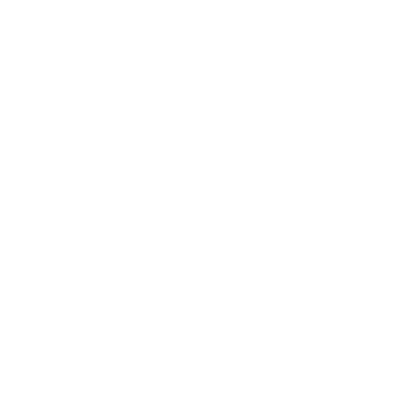
Cold Isostatic Pressing for Medical Applications Challenges and Solutions
Cold Isostatic Pressing (CIP) is a process used to compact and densify powders, ceramics, and metals. This process uses high-pressure fluids, usually water or oil, to apply uniform pressure to the material from all directions.
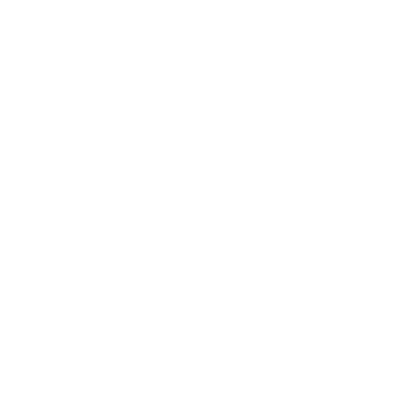
A Guide to Choosing the Right Temperature for Warm Isostatic Press
Warm Isostatic Pressing (WIP) is a process used to eliminate porosity and improve the mechanical properties of materials. In this process, the material is subjected to high pressure and temperature in an inert gas environment.
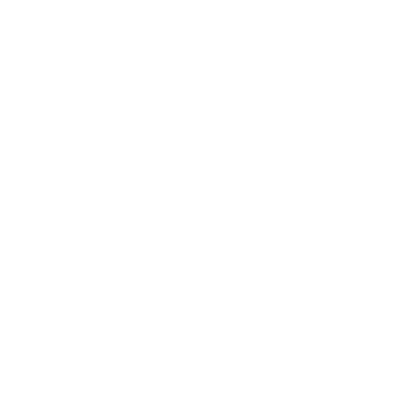
Dos and don'ts during the installation of molybdenum disilicide (MoSi2) heating element
Precautions when installing MoSi2 heating elements