Introduction
Table of Contents
When it comes to producing high-quality ceramic components, one of the most crucial processes is isostatic pressing. This technique ensures the uniformity and precision required for manufacturing ceramics used in various industries. Isostatic pressing involves carefully selecting the pressing powders and controlling the tools to achieve the desired uniformity. Another key factor in this process is the optimization of the sintering process, which greatly influences the physical properties of the ceramics. By understanding the process of isostatic pressing, manufacturers can ensure the production of ceramics that meet the strict standards of dimensional accuracy and performance.
The Process of Semi-Isostatic Pressing
Importance of Pressing Uniformity
In the semi-isostatic pressing process, products are placed in a closed container filled with liquid and subjected to equal pressure on all surfaces. This high-pressure environment increases the density of the products and gives them the required shapes. Semi-isostatic presses are widely used in the forming of high-temperature refractory, ceramics, cemented carbide, lanthanum permanent magnets, carbon materials, and rare metal powders.
Role of Careful Selection of Pressing Powders and Tool Controls
Semi-isostatic pressing relies on careful selection of pressing powders and tool controls to ensure the desired outcome. Unlike other powder metallurgy processes, semi-isostatic pressing offers several benefits, including equal compaction in all directions and a more uniform final component density. However, manufacturers must carefully characterize the properties of the metal powder used in the process to achieve optimal final component properties. Material characterization is crucial to ensure the desired quality and performance of the end product.
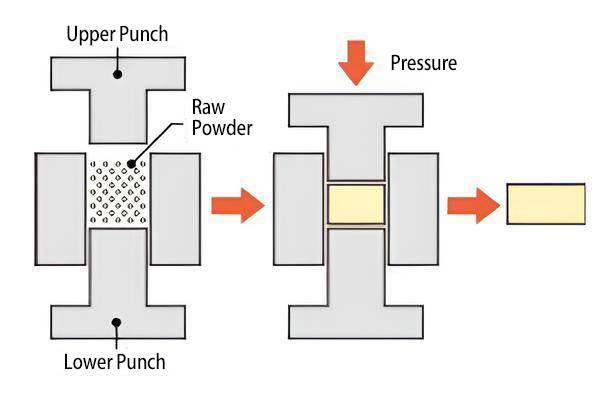
Influence of Optimized Sintering Process on Physical Properties
The optimized sintering process plays a significant role in determining the physical properties of the semi-isostatically pressed components. Isostatic pressing enables the production of various types of materials from powder compacts by reducing the porosity of the powder mixture. The powder mixture is compacted and encapsulated using isostatic pressure, which applies pressure equally from all directions. This confinement of the metal powder within a flexible membrane or hermetic container ensures uniform compaction and density within the compacted part.
The isostatic pressing process has evolved over the years and is now widely used in various industries, including ceramics, metals, composites, plastics, and carbon. It offers unique benefits for ceramic and refractory applications, allowing for precise shaping of products and reducing the need for costly machining. The all-around pressure exerted during isostatic pressing ensures uniform compaction and density, addressing concerns about density variation in conventional processing methods. Isostatic pressing is particularly suitable for producing larger parts, parts with high thickness to diameter ratios, and parts requiring superior material properties.
There are two main categories of isostatic pressing: cold isostatic pressing (CIP) and hot isostatic pressing (HIP). CIP involves applying isostatic pressure to the loose powder at room temperature, while HIP applies isostatic pressure to the powder when it is heated in a package. HIP utilizes an inert gas as the pressure transfer medium. The hot isostatic pressing process involves placing the powder into a high-pressure vessel, subjecting it to high temperature and balanced pressure, and sintering it into compact parts. Compared to other methods like hot pressing, hot isostatic pressing offers lower sintering temperatures and higher product density.
In conclusion, the semi-isostatic pressing process offers unique advantages in terms of pressing uniformity and final component density. Careful selection of pressing powders and tool controls, as well as the optimization of the sintering process, are crucial for achieving the desired physical properties. The isostatic pressing process has become a valuable tool in various industries, allowing for the production of high-quality components with precise shapes and superior material properties.
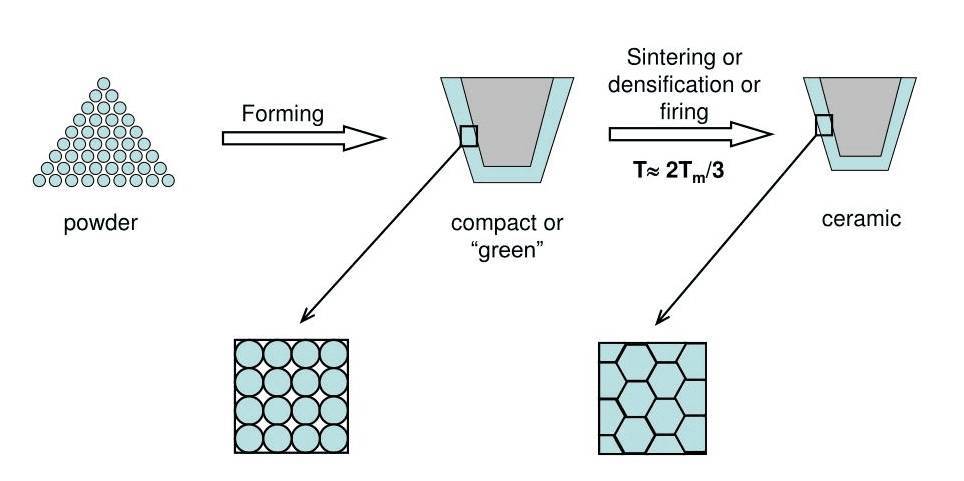
Role of Tailored Sintering Techniques
Achieving Linearity and Concentricity
Sintering is a crucial process in the manufacturing of ceramic components. Tailored sintering techniques play a vital role in achieving linearity and concentricity in these components.
One advantage of room temperature sintering is that it allows for the production of large-sized targets without being limited by equipment size. This method also offers low equipment investment, low production cost, high production efficiency, excellent target performance, and easy industrial production. It is particularly suitable for the performance requirements of coated targets for high-end displays.
However, room temperature sintering does have its weaknesses. It is considered the most difficult sintering method compared to others. To achieve a dense sintered body, a sintering aid is often added. But removing the sintering aid from the sintered body can be challenging, resulting in lower product purity. Additionally, strict requirements regarding the shape, particle size, and particle size distribution of the powder must be met. Powder processing techniques such as ball milling, jet milling, and sedimentation classification are commonly used to meet these requirements. Finally, the targets produced through room temperature sintering are generally thin.
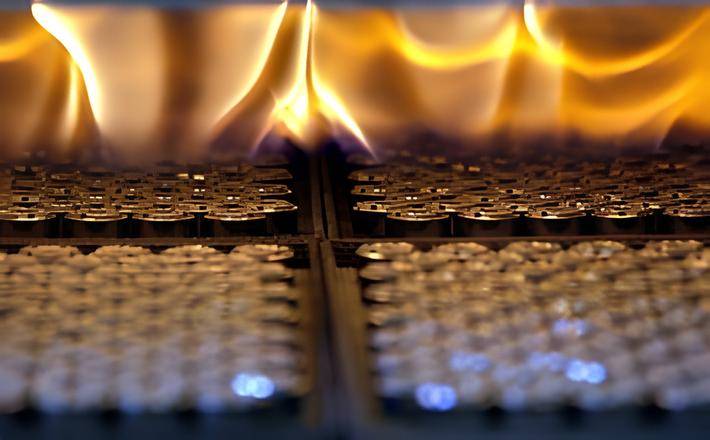
Suitability for Manufacturing Various Ceramic Components
Sintering is a versatile process that offers several advantages in the manufacturing of ceramic components. Here are some key benefits:
-
Complex shapes: Metal sintering allows for the creation of complex shapes that would be difficult or impossible to produce using other methods. This capability opens up possibilities for innovative designs and functional components.
-
High dimensional precision: Sintering offers high dimensional accuracy, ensuring that the finished product closely matches the desired shape. This precision is crucial in applications where tight tolerances are required.
-
Reliability and repeatability of large-scale production: Sintering is a reliable process, producing consistent finished products. This makes it ideal for large-scale production runs, where consistency and uniformity are essential.
-
Self-lubrication: Sintering can create parts with self-lubricating properties. The compacted powder forms a dense bond between particles, reducing friction and wear. This property is valuable in applications where lubrication is challenging or undesirable.
-
Unique and isotropic materials: Sintering is used to create unique isotropic materials, meaning they possess the same properties in all directions. These materials are highly durable and exhibit excellent strength, making them suitable for applications that require robustness.
-
Green technology: Sintering is considered a green technology as it does not produce harmful emissions. This makes it an environmentally friendly choice for companies aiming to reduce their environmental impact.
-
Damping vibration: Sintering can produce parts with vibration damping properties. The compacted powder forms a dense bond, reducing vibrations and noise. This attribute is beneficial in applications where vibration control is crucial.
Various ceramic parts
Metal sintering finds application in various industries, including electrical components, semiconductors, and optical fibers. It enhances the strength, conductivity, and translucency of metals, making them suitable for these industries.
In ceramic sintering, the process is used to manufacture ceramic objects, including pottery. It involves the consolidation of the material, reducing porosity and increasing density. Ceramic raw materials often require organic additives before sintering to improve plasticity. High temperatures, pressure, or electrical currents drive the sintering process.
Modern methods of powder shape forming, such as isostatic pressing, slipcasting, extruding, tapecasting, and 3D printing, have been developed for making green bodies of ceramics and metals. The green body is then heated through a sintering process, reducing porosity and increasing density.
Sintering processes are controlled by thermally activated solid-state diffusion mechanisms. These mechanisms can be quantified by developing sintering models using instruments like push rod dilatometers.
Microwave sintering equipment is widely used in industrial applications for sintering various high-quality ceramics, including lithium cobalt oxide, silicon nitride, silicon carbide, aluminum oxide, aluminum nitride, zirconium oxide, magnesium hydroxide, aluminum, zinc, kaolin, cobalt sulfate, cobalt oxalate, and vanadium oxide. It is also used in sintering electronic ceramic devices like PZT piezoelectric ceramics and varistors.
Overall, tailored sintering techniques play a crucial role in achieving linearity and concentricity in ceramic components. They offer numerous advantages, including the ability to manufacture complex shapes, high dimensional precision, reliability in large-scale production, self-lubrication, unique isotropic materials, green technology, and damping vibration. Metal sintering finds applications in various industries, while ceramic sintering is used in pottery and other ceramic manufacturing processes. Microwave sintering equipment is widely used in industrial applications for sintering various ceramics and electronic ceramic devices.
Dimension Capabilities and Precision
Standard range of dimension capabilities
The dimension capabilities of a deposition system play a crucial role in determining its suitability for various applications. In R&D environments, flexibility is a key factor. The system should be able to handle different materials, substrate sizes, temperature ranges, ion flux, deposition rates, frequencies, endpoints, and pressure operating regimes. This allows for experimentation and adaptation to changing priorities. Additionally, budget considerations also come into play, as the cost of systems can vary significantly depending on the technology options.
Precision in as-fired condition
Precision is a critical factor when it comes to deposition systems. For example, in the case of micro-machining or ultra-precision applications, diamond is often used as a tool material due to its extreme hardness and dimensional stability. When considering precision in the as-fired condition, it is important to note that the internal diameter can have a tolerance of +/- 0.02 mm with a repeatability of less than 10 µm within the same batch of production.
Precision after diamond-grinding
Diamond grinding is a process that can significantly enhance precision in machining applications. After diamond-grinding, the length of the workpiece can have a tolerance of +/- 0.03 mm, while the external diameter can have a tolerance of +/- 0.01 mm. Additionally, the minimum wall thickness achievable is 0.3 µm. These levels of precision ensure high-quality workpiece results.
Diamond cutting tools can be created using either massive diamond (monocrystal, CVD diamond, PCD) or diamond coatings. Standard diamond abrasive tools are made by bonding diamond monocrystals onto a base body. Alternatively, there is a new grinding layer technology that involves chemical vapour-deposited microcrystalline diamond layers with sharp crystallite tips. These sharp edges contribute to the effectiveness of the grinding process.
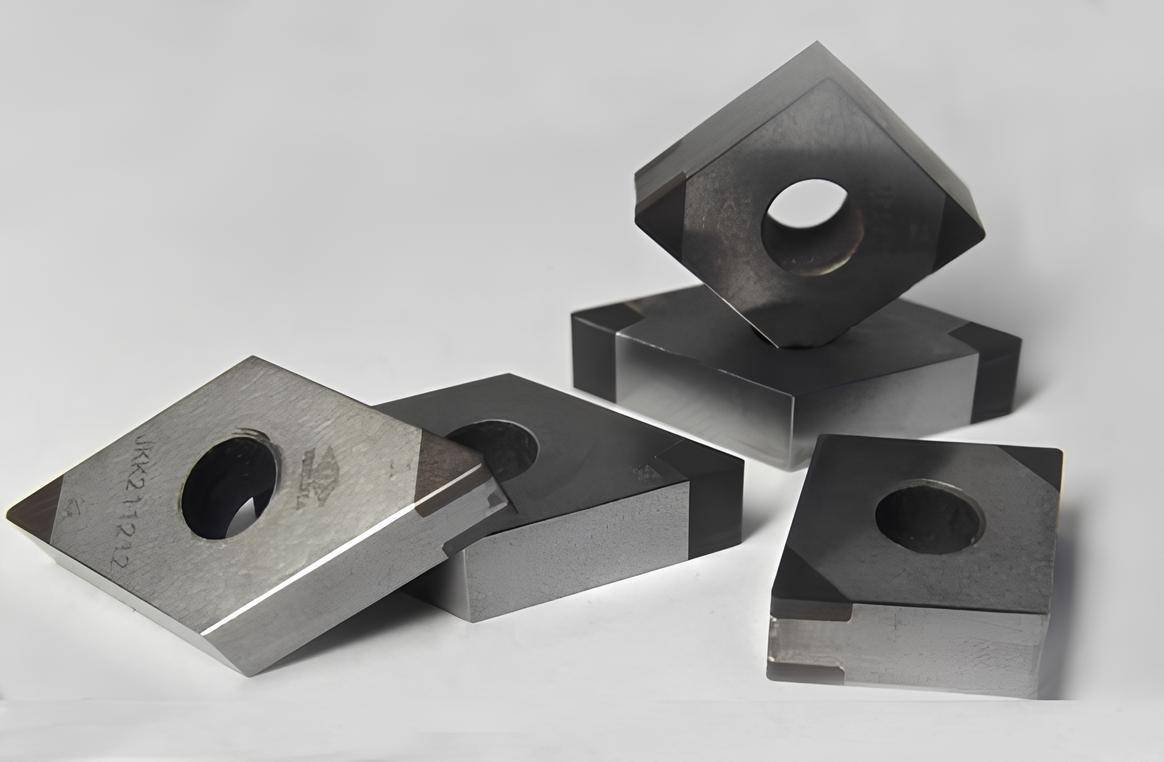
Micro grinding tools, such as abrasive pencils and burrs, can also be produced using the same coating technology. Even very small tools with diameters of 50 mm have been successfully tested.
In conclusion, the dimension capabilities and precision of a deposition system are crucial factors to consider in R&D environments. The system should offer flexibility, allowing for experimentation and adaptation to changing priorities. Diamond grinding can greatly enhance precision in machining applications, ensuring high-quality results. Whether it's a standard range of dimension capabilities or precision after diamond-grinding, these factors contribute to the overall effectiveness and efficiency of the deposition system.
Conclusion
In conclusion, isostatic pressing is a crucial process in ceramic manufacturing that ensures the uniformity and precision of ceramic components. By carefully selecting the pressing powders and controlling the tools, manufacturers can achieve the desired uniformity in the pressed ceramics. Additionally, optimizing the sintering process further enhances the physical properties of the ceramics. Tailored sintering techniques play a vital role in achieving linearity and concentricity in the final product, making it suitable for various applications. Moreover, the dimension capabilities and precision of ceramics can be standardized, and any necessary adjustments can be made through diamond grinding. Overall, isostatic pressing and tailored sintering techniques are essential for producing high-quality and precise ceramic components.
If you are interested in our products, please visit our company website:https://kindle-tech.com/product-categories/isostatic-press, where innovation has always been a priority. Our R&D team consists of experienced engineers and scientists who closely follow industry trends and are constantly pushing the boundaries of what is possible. Our laboratory equipment incorporates the latest technology to ensure that you can obtain accurate and repeatable results during your experiments. From high-precision instruments to intelligent control systems, our products will provide you with unlimited possibilities for your experimental work.
CONTACT US FOR A FREE CONSULTATION
KINTEK LAB SOLUTION's products and services have been recognized by customers around the world. Our staff will be happy to assist with any inquiry you might have. Contact us for a free consultation and talk to a product specialist to find the most suitable solution for your application needs!