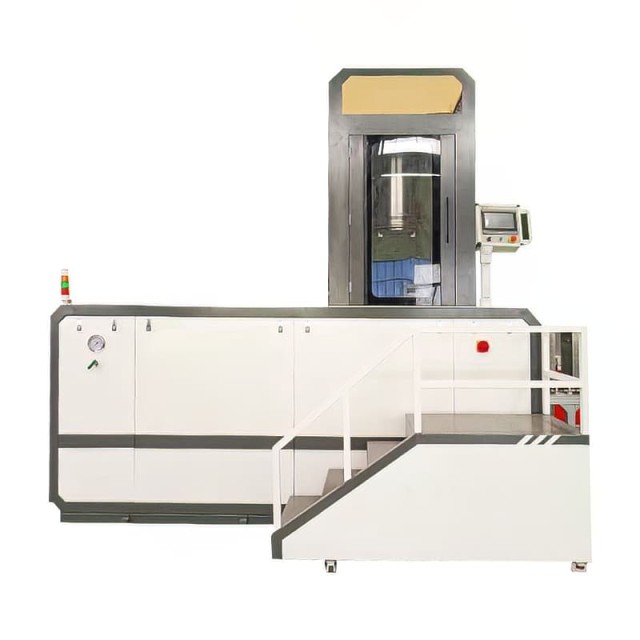
Isostatic Press
Warm Isostatic Press WIP Workstation 300Mpa for High Pressure Applications
Item Number : PCIW
Price varies based on specs and customizations
- Cylinder inner diameter
- Ø150-Ø1000 mm
- Cylinder inner height
- 300-3000 mm
- Maximum pressure
- 300 MPa
- Maximum temperature
- (heat transfer oil)≤ 250℃
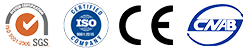
Shipping:
Contact us to get shipping details Enjoy On-time Dispatch Guarantee.
Why Choose Us
Reliable PartnerEasy ordering process, quality products, and dedicated support for your business success.
Warm isostatic pressing (WIP) is a variant of cold isostatic pressing (CIP) that includes a heating element. It employs warm water or a similar medium to apply uniform pressure to powdered products from all directions.
Warm isostatic pressing (WIP) is a cutting-edge technology that enables isostatic pressing at a temperature that does not exceed the boiling point of the liquid medium. This process typically involves utilizing flexible materials as a jacket mold and hydraulic pressure as a pressure medium to shape and press the powder material.
The Warm isostatic pressing process typically involves heating the liquid medium first and then continuously injecting the heated liquid medium into a sealed pressing cylinder through a booster source. To ensure the accuracy of temperature control, the pressing cylinder is equipped with a heating element.
Applications
Warm isostatic pressing is commonly used for powders, binders, and other materials that have special temperature requirements or cannot be molded at room temperature. This technology has revolutionized the manufacturing industry and has enabled the production of complex parts and components with precision and efficiency.
Detail & Parts
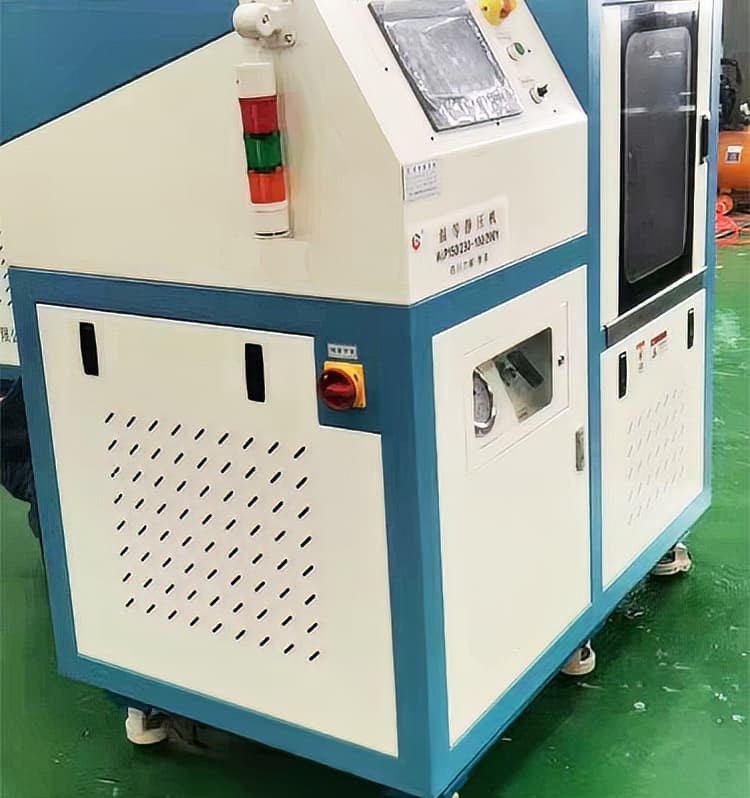
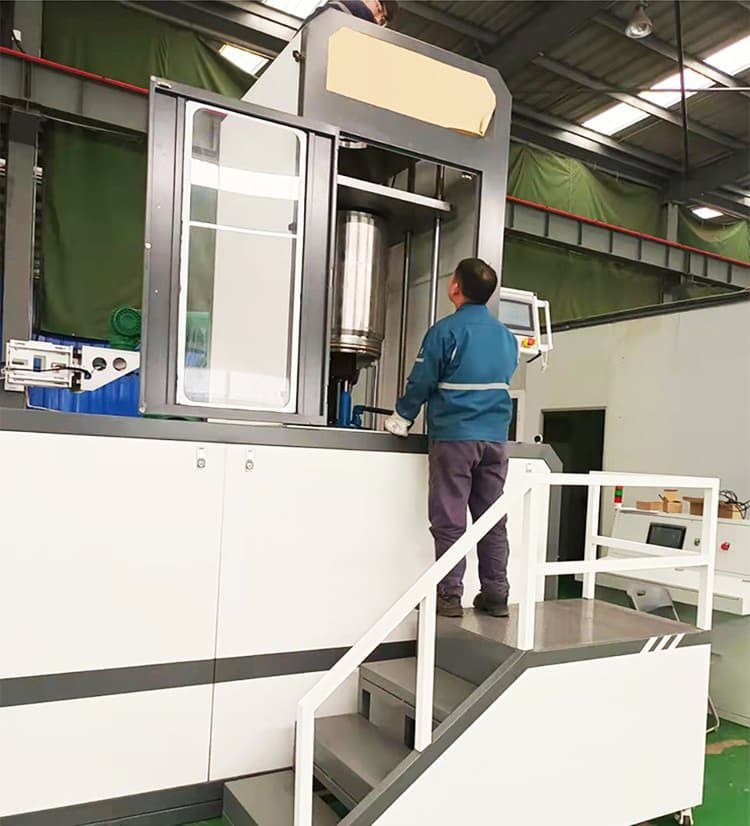
- Thick wall high pressure cylinder
- Pressure boost module
- Movable operation plateform
Warm Isostatic Press structure types
Warm isostatic presses can be categorized into three types of structures: bolt structure, moment tooth structure, and wire winding structure.
- Bolt structure is suitable for small and medium-sized isostatic pressing equipment. It features high temperature control accuracy, good uniformity in the hot zone, and a compact structure. It generates no noise and doesn't cause oil or water pollution on the site.
- Moment tooth structure is suitable for medium and large isostatic pressing equipment. It shares the same characteristics as the bolt structure: high temperature control accuracy, good uniformity in the hot zone, and a compact structure. It also generates no noise and doesn't cause oil or water pollution on the site.
- Steel wire winding structure is suitable for large-scale warm isostatic pressing equipment. This structure is typically utilized in warm isostatic pressing equipment with a cylinder diameter greater than 400mm and a working pressure exceeding 250MPa. It features high temperature control accuracy, good uniformity in the hot zone, and a compact structure. It generates low noise and doesn't cause oil or water pollution on the site.
Advantages
- Temperature controlling accuracy of ±1℃
- We have the capability to provide customized design and manufacturing for WIP (water isostatic press) with a pressure capacity of up to 450 MPa.
- The pressing cylinder is equipped with a heating device to ensure precise temperature control of the liquid medium.
- High temperature control accuracy
- The warm isostatic press uses a program-controlled, multi-stage automatic boosting and depressurization process, which can be customized with manual or automatic flow control to meet various pressing process requirements.
- The ultra-high pressure treatment process is relatively simple, thanks to the fast and uniform pressure transmission speed, and the absence of a pressure gradient.
- The design of the warm isostatic press adheres to international standards to reduce production and maintenance costs.
- The valve group design is highly integrated, which reduces the number of high-pressure pipelines, improves equipment safety, and minimizes fault maintenance and repair time.
Safety guarantee
- The warm isostatic press features a prestressed steel wire winding structure in both the pressing cylinder and the pressure-bearing frame, eliminating the risk of explosion and ensuring a safer and more reliable operation with a service life of over 200,000 cycles.
- The warm isostatic press also incorporates a long-life and low-maintenance sealing structure design, which enhances equipment reliability.
- To ensure the safety of personnel and equipment, the warm isostatic press is equipped with automatic and manual safety protection functions. It also boasts multiple mechanical and electrical safety protection and warning designs, meeting the requirements of safe production.
Technical specifications
Model | Cylinder inner diameter (mm) | Cylinder inner height (mm) | Maximum pressure (MPa) | Maximum temperature |
PCIW150 | Ø150 | 300~500 | 300 |
(Deionized water) ≤ 90℃ (heat transfer oil)≤ 250℃ |
PCIW200 | Ø200 | 500-1000 | ||
PCIW250 | Ø250 | |||
PCIW300 | Ø300 | |||
PCIW350 | Ø350 | 500-1500 | ||
PCIW400 | Ø400 | 500~2000 | ||
PCIW450 | Ø450 | |||
PCIW500 | Ø500 | 1000~3000 | ||
PCIW630 | Ø630 | |||
PCIW710 | Ø710 | |||
PCIW800 | Ø800 | |||
PCIW910 | Ø910 | |||
PCIW1000 | Ø1000 |
Warnings
Operator safety is the top important issue! Please operate the equipment with cautions. Working with inflammable& explosive or toxic gases is very dangerous, operators must take all necessary precautions before starting the equipment. Working with positive pressure inside the reactors or chambers is dangerous, operator must fellow the safety procedures strictly. Extra caution must also be taken when operating with air-reactive materials, especially under vacuum. A leak can draw air into the apparatus and cause a violent reaction to occur.
Designed for You
KinTek provide deep custom made service and equipment to worldwide customers, our specialized teamwork and rich experienced engineers are capable to undertake the custom tailoring hardware and software equipment requirements, and help our customer to build up the exclusive and personalized equipment and solution!
Would you please drop your ideas to us, our engineers are ready for you now!
FAQ
What Is A Warm Isostatic Press?
What Are The Applications Of A Warm Isostatic Press?
What Is Isostatic Pressing?
What Are The Benefits Of Isostatic Pressing?
What Is The Working Principle Of A Warm Isostatic Press?
What Are The Types Of Isostatic Pressing?
There are two main types of isostatic pressing:
- Hot Isostatic Pressing (HIP): This type of isostatic pressing uses high temperature and high pressure to consolidate and strengthen the material. The material is heated in a sealed container and then subjected to equal pressure from all directions.
- Cold Isostatic Pressing (CIP): In this type of isostatic pressing, the material is compacted at room temperature using hydraulic pressure. This method is commonly used to form ceramic and metal powders into complex shapes and structures.
What Are The Advantages Of Using A Warm Isostatic Press?
What Type Of Isostatic Pressing Equipment Do You Have?
What Is The Operating Temperature Range Of A Warm Isostatic Press?
What Are The Wet Bag Process And The Dry Bag Process?
The CIP molding process is divided into two methods: the wet bag process and the dry bag process.
Wet bag process:
In this method, the powder material is placed in a flexible mold bag and placed in a pressure vessel filled with high-pressure liquid. This process is ideal for producing multi-shaped products and is suitable for small to large quantities, including large-sized parts.
Dry bag process:
In the dry bag process, a flexible membrane is integrated into the pressure vessel and is used throughout the pressing process. This membrane separates the pressure fluid from the mold, creating a "dry bag." This method is more hygienic as the flexible mold does not get contaminated with wet powder and requires less cleaning of the vessel. It also features fast cycles, making it ideal for mass producing powder products in an automated process.
What Is Warm Isostatic Pressing (WIP)?
Warm isostatic pressing (WIP) is a variant of cold isostatic pressing (CIP) that includes a heating element. It employs warm water or a similar medium to apply uniform pressure to powdered products from all directions.
Since the powder shaping occurs at a specified temperature, WIP is utilized when it is essential to minimize forming inconsistencies caused by changes in seasons.
What Types Of Materials Can Be Processed Using A Warm Isostatic Press?
What Types Of Structures Does Warm Isostatic Pressing (WIP) Have?
Warm isostatic presses can be categorized into three types of structures: bolt structure, moment tooth structure, and wire winding structure.
- Bolt structure is suitable for small and medium-sized isostatic pressing equipment. It features high temperature control accuracy, good uniformity in the hot zone, and a compact structure. It generates no noise and doesn't cause oil or water pollution on the site.
- Moment tooth structure is suitable for medium and large isostatic pressing equipment. It shares the same characteristics as the bolt structure: high temperature control accuracy, good uniformity in the hot zone, and a compact structure. It also generates no noise and doesn't cause oil or water pollution on the site.
- Steel wire winding structure is suitable for large-scale warm isostatic pressing equipment. This structure is typically utilized in warm isostatic pressing equipment with a cylinder diameter greater than 400mm and a working pressure exceeding 250MPa. It features high temperature control accuracy, good uniformity in the hot zone, and a compact structure. It generates low noise and doesn't cause oil or water pollution on the site.
How Long Is Your Delivery Time? If I Want To Customize The Instrument, How Long Does It Take?
4.8
out of
5
Kintek's Warm Isostatic Press exceeded my expectations. The 300Mpa Workstation is a game-changer for our laboratory's research.
4.9
out of
5
The WIP 300Mpa Workstation is a testament to Kintek's commitment to quality and innovation. It has revolutionized our materials testing process.
4.7
out of
5
Our lab recently purchased the WIP 300Mpa Workstation, and it's been a worthwhile investment. The machine is user-friendly and provides accurate results.
4.6
out of
5
The WIP 300Mpa Workstation has significantly improved our workflow. The machine is reliable and has helped us meet our research deadlines.
4.8
out of
5
Kintek's WIP 300Mpa Workstation is a valuable asset to our lab. It's easy to operate and has helped us achieve consistent results in our experiments.
4.9
out of
5
The WIP 300Mpa Workstation is a well-built machine that delivers precise results. Kintek's customer service is also top-notch.
4.7
out of
5
Kintek's WIP 300Mpa Workstation is an excellent choice for labs that demand accuracy and efficiency. It's a valuable addition to our research equipment.
4.6
out of
5
The WIP 300Mpa Workstation has helped us streamline our research process. It's a reliable machine that produces high-quality results.
4.8
out of
5
Kintek's WIP 300Mpa Workstation is a great investment for any lab. It's easy to use and provides consistent results.
4.9
out of
5
The WIP 300Mpa Workstation is a powerful tool that has helped us achieve breakthroughs in our research. It's a must-have for any lab.
4.7
out of
5
Kintek's WIP 300Mpa Workstation is user-friendly and delivers accurate results. It's a valuable addition to our laboratory.
4.6
out of
5
The WIP 300Mpa Workstation has exceeded our expectations. It's a reliable machine that has helped us improve our research efficiency.
Products
Warm Isostatic Press WIP Workstation 300Mpa for High Pressure Applications
REQUEST A QUOTE
Our professional team will reply to you within one business day. Please feel free to contact us!
Related Products
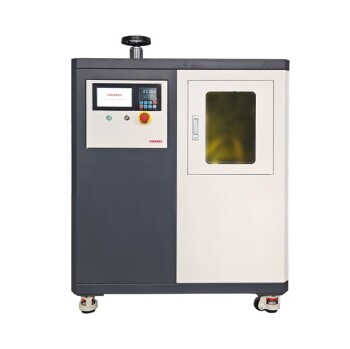
Warm Isostatic Press for Solid State Battery Research
Discover the advanced Warm Isostatic Press (WIP) for semiconductor lamination. Ideal for MLCC, hybrid chips, and medical electronics. Enhance strength and stability with precision.
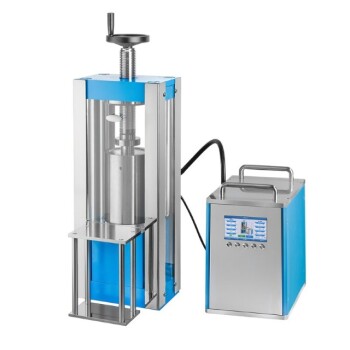
Electric Split Lab Cold Isostatic Press CIP Machine for Cold Isostatic Pressing
Split cold isostatic presses are capable of providing higher pressures, making them suitable for testing applications that require high pressure levels.
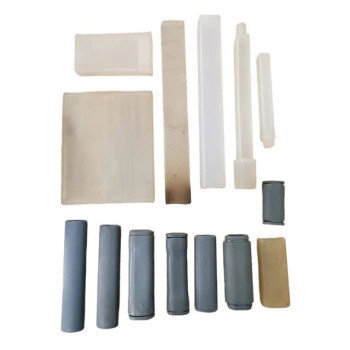
Isostatic Molding Pressing Molds for Lab
Explore high-performance isostatic pressing molds for advanced material processing. Ideal for achieving uniform density and strength in manufacturing.
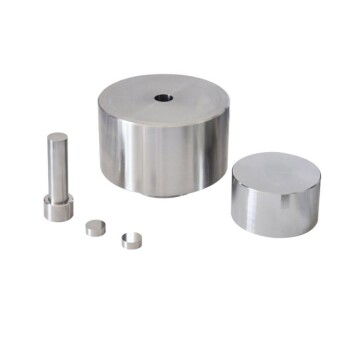
Anti-Cracking Press Mold for Lab Use
The anti-cracking press mold is a specialized equipment designed for molding various shapes and sizes of film using high pressure and electric heating.
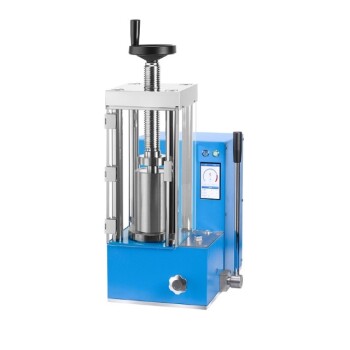
Electric Lab Cold Isostatic Press CIP Machine for Cold Isostatic Pressing
Produce dense, uniform parts with improved mechanical properties with our Electric Lab Cold Isostatic Press. Widely used in material research, pharmacy, and electronic industries. Efficient, compact, and vacuum-compatible.
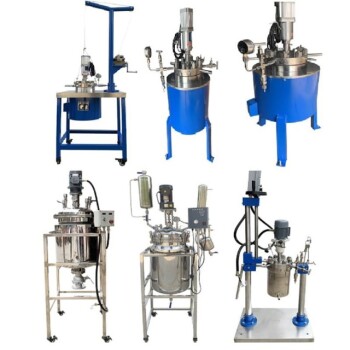
Stainless High Pressure Autoclave Reactor Laboratory Pressure Reactor
Discover the versatility of Stainless High Pressure Reactor - a safe and reliable solution for direct and indirect heating. Built with stainless steel, it can withstand high temperatures and pressures. Learn more now.
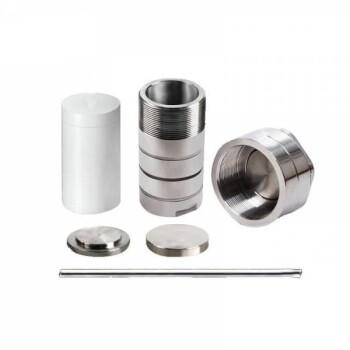
High Pressure Laboratory Autoclave Reactor for Hydrothermal Synthesis
Discover the applications of Hydrothermal Synthesis Reactor - a small, corrosion-resistant reactor for chemical labs. Achieve rapid digestion of insoluble substances in a safe and reliable way. Learn more now.
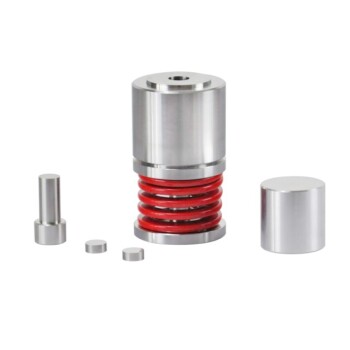
Round Bidirectional Press Mold for Lab
The round bidirectional press mold is a specialized tool used in high-pressure molding processes, particularly for creating intricate shapes from metal powders.
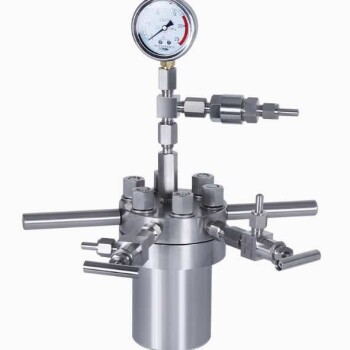
Customizable High Pressure Reactors for Advanced Scientific and Industrial Applications
This laboratory-scale high-pressure reactor is a high-performance autoclave engineered for precision and safety in demanding research and development environments.
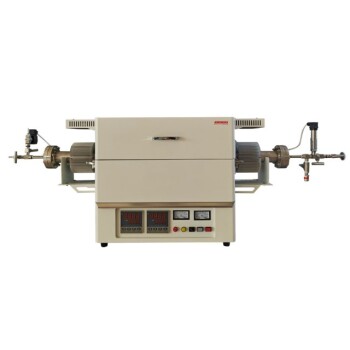
High Pressure Laboratory Vacuum Tube Furnace Quartz Tubular Furnace
KT-PTF High Pressure Tube Furnace: Compact split tube furnace with strong positive pressure resistance. Working temp up to 1100°C and pressure up to 15Mpa. Also works under controller atmosphere or high vacuum.
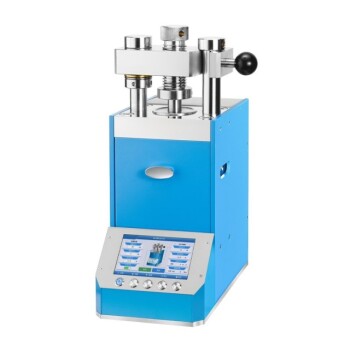
Automatic Lab Cold Isostatic Press CIP Machine Cold Isostatic Pressing
Efficiently prepare samples with our Automatic Lab Cold Isostatic Press. Widely used in material research, pharmacy, and electronic industries. Provides greater flexibility and control compared to electric CIPs.
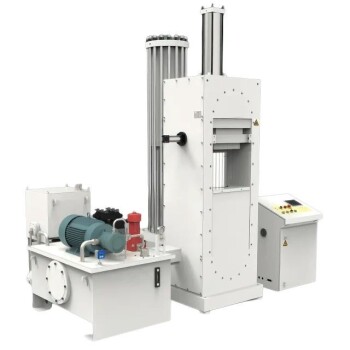
Cold Isostatic Pressing Machine CIP for Small Workpiece Production 400Mpa
Produce uniformly high-density materials with our Cold Isostatic Press. Ideal for compacting small workpieces in production settings. Widely used in powder metallurgy, ceramics, and biopharmaceutical fields for high-pressure sterilization and protein activation.
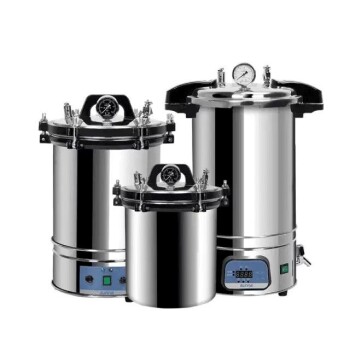
Portable High Pressure Laboratory Autoclave Steam Sterilizer for Lab Use
Portable autoclave sterilization pressure is a device that uses pressure saturated steam to quickly and effectively sterilize items.
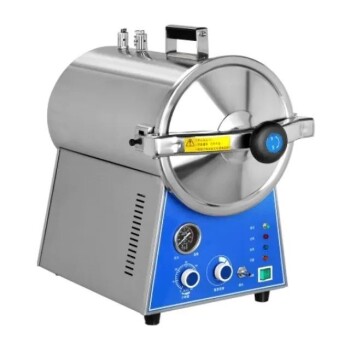
Desktop Fast High Pressure Laboratory Autoclave Sterilizer 16L 24L for Lab Use
The desktop fast steam sterilizer is a compact and reliable device used for rapid sterilization of medical, pharmaceutical, and research items.
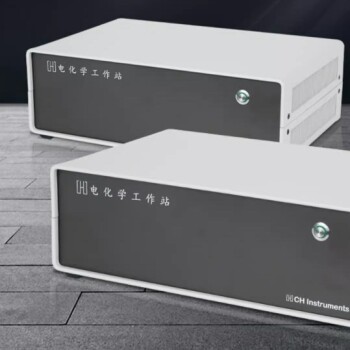
Lab Electrochemical Workstation Potentiostat for Laboratory Use
Electrochemical workstations, also known as laboratory electrochemical analyzers, are sophisticated instruments designed for precise monitoring and control in various scientific and industrial processes.
Related Articles
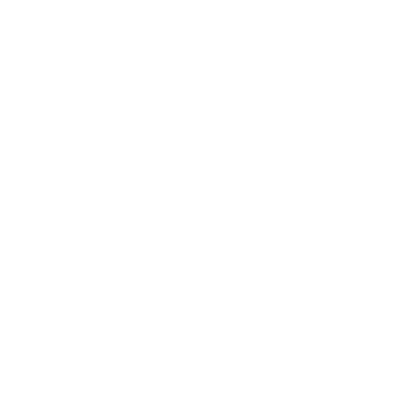
How Isostatic Presses Improve the Efficiency of Material Processing
Isostatic pressing is a manufacturing process that uses high pressure to compact and shape materials. It can be done at room temperature (cold isostatic pressing) or at high temperatures (hot isostatic pressing).
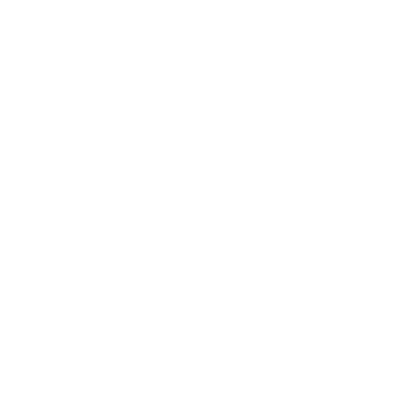
Essential Equipment for Mass Production of Solid-State Batteries: Isostatic Press
Discusses the role of isostatic pressing technology in enhancing solid-state battery performance and production efficiency.
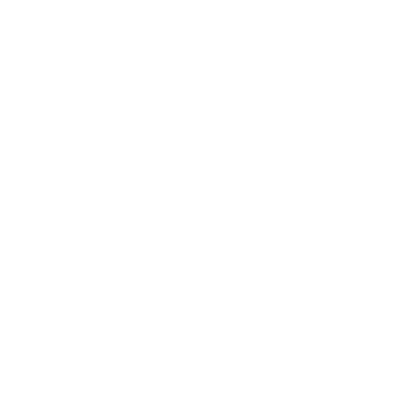
Isostatic Pressing Technology for Solid-State Batteries
Focus on isostatic pressing to commercialize next-gen batteries.
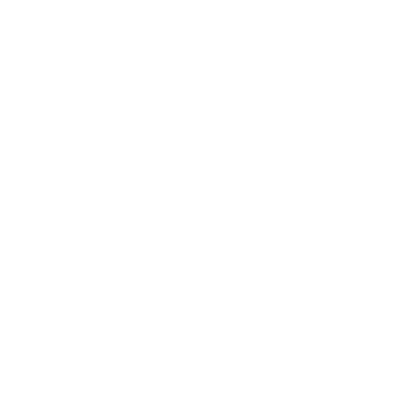
How Isostatic Presses Help Eliminate Defects in Materials
Isostatic pressing is a manufacturing process that is used to eliminate defects in materials.
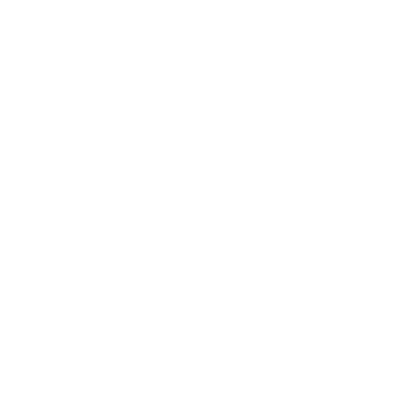
How to replace the rubber ring of isostatic press and what precautions should be taken
How to replace the rubber ring of isostatic press and matters needing attention.
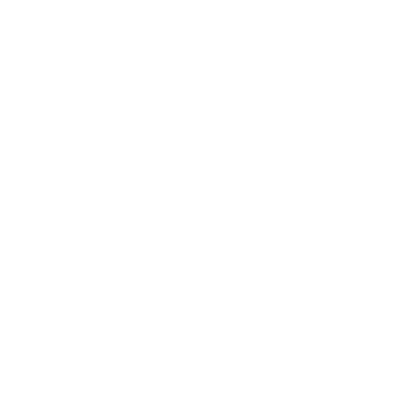
The Benefits of Using Isostatic Pressing in Manufacturing
sostatic pressing is a manufacturing process that involves applying uniform pressure to a material to achieve a specific shape or density. The process can be performed at room temperature (cold isostatic pressing or CIP) or at high temperatures (hot isostatic pressing or HIP).
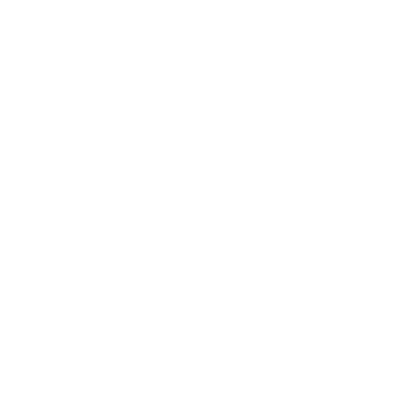
Understanding the Basics of Isostatic Pressing
Isostatic pressing is a manufacturing process used to shape and consolidate materials by applying equal pressure from all directions. The technique involves placing a material in a pressure vessel and applying hydrostatic pressure to the material.
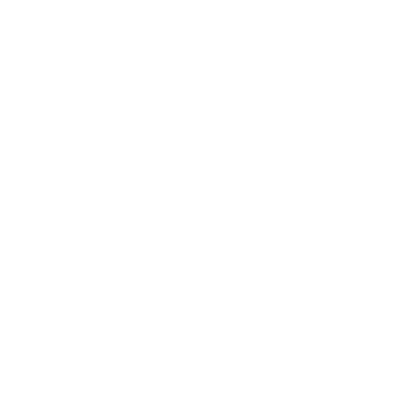
What is Isostatic Pressing Machine
Isostatic molding is a molding method that uses the incompressibility of a liquid medium and the uniform transfer of pressure. It is suitable for powder dense parts with equal pressure in all directions. The principle is to fill the mold with a liquid medium, such as water, and then subject the mold to uniform pressure. The pressure is applied by a piston or a flexible membrane.
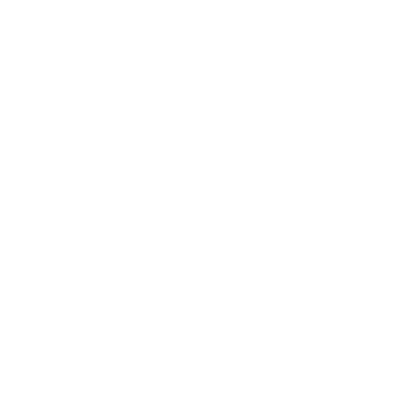
Isostatic Pressing Technology in Solid-State Battery Production
Exploring the role of isostatic pressing technology in manufacturing solid electrolytes for next-generation solid-state batteries.
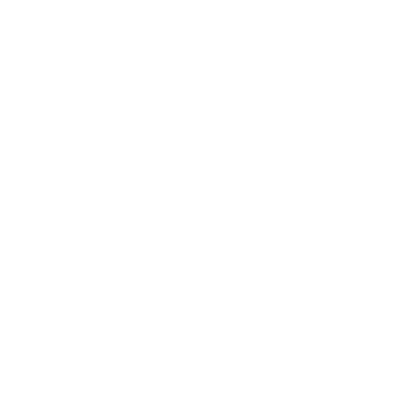
Understanding the Isostatic Pressing Process and its Types
Isostatic pressing, a technique that applies hydrostatic pressure to a material to improve its density and mechanical strength, has seen significant growth and development over the years. Isostatic pressing is commonly used for the consolidation of powders and defect healing of castings, making it a versatile process for a range of materials including ceramics, metals, composites, plastics, and carbon.
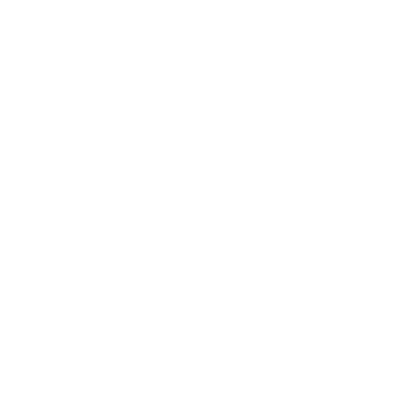
Comprehensive Guide to Isostatic Pressing: Types, Processes, and Features(3)
Isostatic pressing is a versatile manufacturing process that is widely used in various industries. It involves subjecting a material to equal pressure from all directions to achieve uniform density and shape. Isostatic pressing offers numerous advantages, such as the ability to produce complex shapes, uniformity in material properties, and high precision.
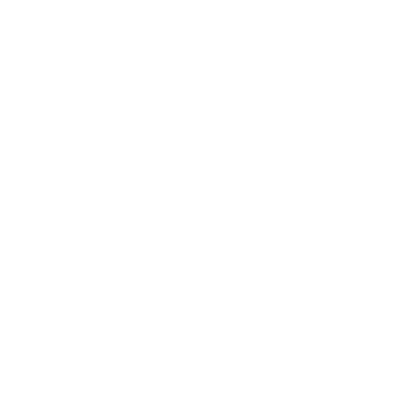
Comprehensive Guide to Isostatic Pressing:Processes, and Features
Isostatic pressing is a versatile manufacturing process that is widely used in various industries. It involves subjecting a material to equal pressure from all directions to achieve uniform density and shape. Isostatic pressing offers numerous advantages, such as the ability to produce complex shapes, uniformity in material properties, and high precision. This comprehensive guide will delve into the different types of isostatic pressing, including cold, warm, and hot pressing. We will explore the processes, features, and applications of each type, providing you with a thorough understanding of this essential manufacturing technique. So let's dive in!