Introduction to Solid-State Batteries and Pressurization Needs
Challenges in Solid-State Battery Production
Solid-state batteries present a unique set of manufacturing challenges due to their requirement for dense stacking of materials to achieve a robust solid-solid contact interface. This necessitates the use of specialized pressurization equipment, such as isostatic presses, to apply pressures exceeding 100 MPa. The high pressures are essential to eliminate microscopic gaps between the stacked layers, which can otherwise lead to poor electrical conductivity and reduced battery performance.
Traditional pressing methods, such as hot pressing and roller pressing, fall short in this regard as they provide limited and uneven pressure distribution. This inconsistency can result in suboptimal battery performance and reliability. In contrast, isostatic presses leverage Pascal's principle to ensure uniform pressure distribution in all directions, addressing the critical need for precision in solid-state battery production.
The application of isostatic pressing in solid-state batteries is not without its complexities. For instance, the cold isostatic press (CIP) operates at room temperature, which is advantageous for creating strong "green bodies" that can withstand subsequent processing stages. However, the warm isostatic press (WIP) and hot isostatic press (HIP) introduce additional variables such as controlled heating and elevated temperatures, which must be meticulously managed to avoid compromising material integrity.
Moreover, the integration of isostatic pressing technology into solid-state battery production lines requires significant investment in equipment and expertise. Companies like Samsung SDI have already adopted WIP technology, demonstrating the potential for enhanced material densification and battery performance. However, the broader industry faces ongoing challenges in optimizing temperature and pressure control, surface management, and overall production efficiency.
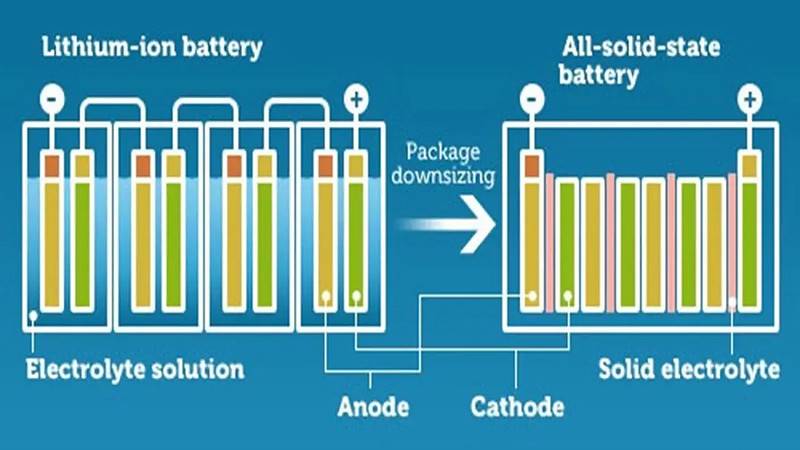
In summary, while isostatic pressing offers a promising solution to the pressing challenges of solid-state battery production, its successful implementation hinges on overcoming technical hurdles and refining production processes.
Limitations of Traditional Pressing Methods
Traditional hot pressing and roller pressing solutions present significant limitations in the context of solid-state battery production. These methods often struggle to provide uniform pressure across the battery's components, leading to inconsistent densification and material properties. This uneven pressure distribution can result in suboptimal solid-solid contact interfaces, which are critical for maintaining the battery's structural integrity and performance.
Moreover, the variability in pressure applied by traditional methods can lead to a range of issues, including:
- Inconsistent Energy Density: Uneven pressure can cause some regions of the battery to be more densely packed than others, resulting in inconsistent energy storage capabilities.
- Increased Internal Resistivity: Poorly pressed areas can exhibit higher internal resistance, which can reduce the overall efficiency and lifespan of the battery.
- Quality Variability: The lack of uniform pressure can lead to significant quality variations between different batches of batteries, complicating quality control processes.
Issue | Impact on Solid-State Batteries |
---|---|
Inconsistent Energy Density | Reduced performance and reliability |
Increased Internal Resistivity | Lower efficiency and shorter lifespan |
Quality Variability | Difficulty in maintaining consistent quality |
These limitations underscore the need for more advanced pressing technologies, such as isostatic pressing, which can provide the necessary uniformity and precision to overcome the challenges posed by traditional methods.
Isostatic Pressing Technology
Pascal's Principle and Isostatic Pressing
Isostatic pressing technology is deeply rooted in the foundational principle proposed by the French scientist Blaise Pascal, which states, "A change in the pressure of an enclosed incompressible fluid is conveyed undiminished to every part of the fluid and the surface of its container." This principle is pivotal in ensuring that the pressure applied during the pressing process is uniformly distributed across all directions. The process begins with powder materials being sealed within a forming mold with low deformation resistance, such as a rubber bag, to facilitate the application of liquid pressure. Subsequently, the molded body undergoes uniform compression across its entire surface area as the liquid pressure is transmitted through the pressure vessel.
The uniform pressure distribution achieved through Pascal's principle is critically important for several reasons. Firstly, it effectively eliminates any gaps or voids within the material, which are common issues in traditional pressing methods. By ensuring that every part of the material is subjected to the same pressure, isostatic pressing significantly enhances the overall conductivity of solid-state batteries. This uniformity is not just a technical advantage but a necessity for achieving the high-performance standards required in modern battery technology. The consistent pressure ensures that the material properties are uniform throughout, leading to batteries with superior performance and reliability.

Moreover, the application of isostatic pressing in solid-state batteries addresses the inherent challenges of achieving dense stacking and solid-solid contact interfaces, which are essential for optimal battery performance. The technology's ability to apply pressures exceeding 100MPa ensures that the materials are compressed to their maximum potential, resulting in batteries with higher energy densities and reduced internal resistivity. This not only enhances the battery's efficiency but also simplifies the production process, making it a preferred method for mass production of solid-state batteries.
Types of Isostatic Presses
Isostatic presses are classified into three primary types: cold, warm, and hot isostatic presses, each designed to operate under distinct temperature and pressure regimes to cater to specific manufacturing requirements.
Cold Isostatic Presses (CIP)
Cold isostatic presses function at ambient temperatures, making them ideal for applications where maintaining material integrity without thermal degradation is critical. By applying high pressures at room temperature, CIPs facilitate the creation of dense, uniform structures, which are essential for the initial stages of solid-state battery production, such as forming "green bodies" that can be further processed.
Warm Isostatic Presses (WIP)
Warm isostatic presses incorporate controlled heating to enhance the densification of materials. This type of press is particularly useful in advanced manufacturing processes, such as those employed by companies like Samsung SDI in their solid-state battery production lines. The combination of moderate temperatures and high pressures allows for greater material consolidation and improved mechanical properties.
Hot Isostatic Presses (HIP)
Hot isostatic presses operate at elevated temperatures, leveraging both high heat and pressure to achieve uniform material properties. HIPs offer superior controllability and versatility, making them indispensable in the production of solid-state batteries. The high temperatures and pressures ensure that the materials achieve optimal densification and homogeneity, which are crucial for enhancing the performance and longevity of solid-state batteries.
Each type of isostatic press brings unique advantages, such as uniform strength and density, shape flexibility, and the ability to tailor processes to specific material needs, all of which contribute to the efficient and effective production of solid-state batteries.
Application of Isostatic Pressing in Solid-State Batteries
Cold Isostatic Press
Cold isostatic presses are indispensable in the production of solid-state batteries, primarily due to their capability to exert substantial pressure at ambient temperatures. This process aids in the formation of robust "green bodies," which are essential precursors for subsequent manufacturing stages. The versatility of cold isostatic pressing extends to a wide array of materials, including metals, ceramics, plastics, and composites, making it a commercially viable option for creating complex and large-scale components.
The pressing mechanism involves compacting powders within elastomeric molds, using either wet or dry bag processes. These molds, typically made from materials like urethane, rubber, or polyvinyl chloride, can withstand pressures ranging from less than 5,000 psi to over 100,000 psi (34.5 to 690 MPa). The fluid medium, usually oil or water, facilitates uniform pressure distribution, ensuring that the powder achieves a very uniform density.
However, one notable drawback of this process is the reduced geometric accuracy due to the flexible nature of the molds. Despite this limitation, the green compacts produced by cold isostatic pressing are typically sintered conventionally to achieve the final desired part. This dual-step process underscores the critical role of cold isostatic presses in solid-state battery manufacturing, where precision and uniformity are paramount.
Warm Isostatic Press
Warm isostatic presses operate by applying controlled heating and hydraulic pressure to enhance material densification. This technique involves heating the liquid medium to a temperature below its boiling point, ensuring that the pressure is evenly distributed across the powder material within the high-pressure container. The process is facilitated by a flexible envelope die, which allows for precise shaping and pressing of the material.
The warm isostatic press is typically heated to the desired temperature before the liquid medium is continuously injected into the sealed pressing cylinder. This cylinder is equipped with a heat generator to maintain the accuracy of temperature control, which is crucial for achieving consistent material properties. The operating temperatures for these presses can range from 0°C to 240°C, with ambient temperatures typically being between 10°C and 35°C. The static pressure applied can reach up to 240MPa, ensuring that the material is subjected to uniform and high pressures necessary for densification.
This method is particularly suited for materials that require specific temperature conditions or cannot be formed at room temperature, such as powders and binders. Companies like Samsung SDI employ warm isostatic presses in their solid-state battery production lines to achieve high precision and uniformity in material processing, which is essential for enhancing the performance and reliability of solid-state batteries.

Hot Isostatic Press
Hot isostatic presses (HIP) are advanced manufacturing tools that employ both high temperatures and isostatic gas pressure to achieve uniform material properties. This process is instrumental in eliminating porosity and increasing the density of materials such as metals, ceramics, polymers, and composites. By doing so, it significantly enhances the mechanical properties and workability of these materials.
In the context of solid-state battery production, HIP offers strong controllability and wide applicability. The primary function of HIP in this domain is to consolidate powders and facilitate diffusion bonding, which is often referred to as cladding. This technique is crucial for the elimination of microshrinkage in castings, ensuring that the final product has consistent and high-quality material properties.
The operation of a hot isostatic press involves using a mold material, typically sheet metal with a high melting point to withstand the elevated temperatures and pressures. In some specialized applications, ceramic molds are employed. The pressurization is achieved using an inert gas like argon, or in certain cases, a glass-like fluid. A typical operating condition for HIP involves pressures up to 15,000 lb/in² (100 MPa) at temperatures around 2000°F (1100°C).
These conditions are optimized to ensure that the material undergoes uniform densification, which is essential for the performance of solid-state batteries. The uniform pressure distribution, facilitated by Pascal's principle, ensures that there are no gaps or inconsistencies in the material, thereby enhancing the overall conductivity and reliability of the battery.
In summary, hot isostatic pressing is a critical technology in the production of solid-state batteries. It not only ensures uniform material properties but also addresses the challenges of porosity and microshrinkage, leading to higher quality and performance in the final product.
Benefits and Challenges of Isostatic Pressing in Solid-State Batteries
Advantages of Isostatic Pressing
Isostatic pressing technology offers a multitude of benefits that significantly enhance the performance and production efficiency of solid-state batteries. One of the primary advantages is its ability to enhance energy density. By applying uniform pressure in all directions, isostatic pressing ensures that the battery materials are densely packed, thereby maximizing the energy storage capacity. This uniform compaction is achieved without the need for lubricants, which is a key factor in maintaining high and consistent material density.
Moreover, isostatic pressing reduces internal resistivity. The uniform pressure distribution helps in eliminating gaps and voids within the battery structure, which are common sources of internal resistance in traditional battery production methods. This reduction in resistivity directly translates to improved conductivity and overall battery efficiency.
The technology also ensures consistent quality across the production line. Unlike traditional pressing methods that apply pressure unidirectionally, isostatic pressing removes many of the constraints that limit the geometry and consistency of the parts. This results in a more uniform product with fewer defects, which is crucial for maintaining the reliability and longevity of solid-state batteries.

In addition to these benefits, isostatic pressing simplifies production processes. The ability to compact difficult-to-handle materials such as superalloys, titanium, and stainless steel with high efficiency streamlines the manufacturing process. This simplification not only reduces production time but also lowers costs, making it a more economical choice for large-scale battery production.
Benefit | Description |
---|---|
Enhanced Energy Density | Uniform pressure in all directions maximizes energy storage capacity. |
Reduced Internal Resistivity | Eliminates gaps and voids, improving conductivity. |
Consistent Quality | Uniform pressure ensures uniform product with fewer defects. |
Simplified Production | Efficiently compacts difficult materials, streamlining the manufacturing process. |
These advantages make isostatic pressing an indispensable technology for the mass production of solid-state batteries, offering a robust solution to the challenges faced in traditional battery production methods.
Challenges and Future Prospects
While isostatic pressing is a well-established technology, its application in solid-state batteries remains in a state of dynamic evolution. This transition is marked by several critical challenges that need to be addressed to fully harness its potential. One of the primary hurdles is the precise control of both temperature and pressure during the pressing process. Achieving uniform pressure distribution across all directions, as mandated by Pascal's principle, is essential but complex, especially when dealing with the diverse material properties of solid-state batteries.
Surface management is another significant issue. The integrity and uniformity of the battery's surface are crucial for optimal performance and longevity. Any inconsistencies can lead to inefficiencies and potential safety hazards. Additionally, enhancing production efficiency remains a focal point for researchers and manufacturers. The balance between maintaining high-quality standards and increasing output rates is a delicate one, requiring continuous innovation and optimization.
Looking ahead, the future prospects of isostatic pressing in solid-state batteries hinge on overcoming these challenges. Advances in sensor technology and automation could provide solutions for better temperature and pressure control, ensuring more precise and consistent outcomes. Innovations in material science might also offer new ways to manage surfaces more effectively, reducing inconsistencies and improving overall battery performance. As these technologies evolve, the integration of isostatic pressing into the mainstream production of solid-state batteries is expected to become more seamless and efficient.
CONTACT US FOR A FREE CONSULTATION
KINTEK LAB SOLUTION's products and services have been recognized by customers around the world. Our staff will be happy to assist with any inquiry you might have. Contact us for a free consultation and talk to a product specialist to find the most suitable solution for your application needs!