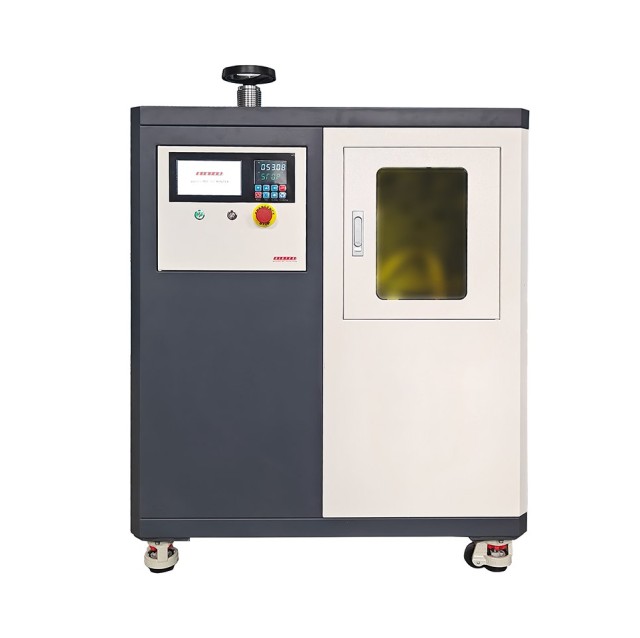
Isostatic Press
Warm Isostatic Press for Solid State Battery Research
Item Number : PCIH
Price varies based on specs and customizations
- Working Pressure
- 0-60 T
- Cylinder Stroke
- 50 mm
- Isostatic Pressure
- 0-500 MPa
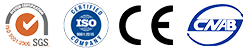
Shipping:
Contact us to get shipping details Enjoy On-time Dispatch Guarantee.
Why Choose Us
Reliable PartnerEasy ordering process, quality products, and dedicated support for your business success.
Introduction
Warm Isostatic Press (WIP) for Solid State Battery is a specialized equipment used for laminating processes in the semiconductor industry, featuring controlled temperatures (50-100°C) and high-pressure capabilities. Designed according to ASME standards, WIP systems include components like high-pressure pumps, pressure vessels, and reservoir tanks, ensuring safety and accuracy. This technology is essential for creating laminates in various electronic components, enhancing strength and stability through heat and pressure. Applications span hybrid chips, MLCC, Bluetooth components, fuel cells, and medical electronics, among others.
Applications
The Warm Isostatic Press (WIP) from Kintek is a versatile piece of equipment designed for various applications in the semiconductor industry and beyond. It is particularly renowned for its lamination processes, which enhance the properties of materials through multiple layers. Below are the main application areas of the WIP, along with related long-tail keywords that highlight its versatility and effectiveness in different industries.
- Hybrid Chips: The WIP is used for laminating hybrid chips, which are essential in modern electronic devices.
- MLCC Lamination: Multi-Layer Ceramic Capacitors (MLCC) benefit from the precise lamination processes enabled by the WIP.
- Bluetooth Components: The WIP ensures the high-quality lamination of components used in Bluetooth technology.
- Fuel Cells: The equipment supports the production of fuel cells, which are crucial for renewable energy applications.
- Medical Electronics & Implants: The WIP is used in the fabrication of medical electronics and implants, ensuring high reliability and performance.
- Multilayer PZTs: The WIP is employed in the production of Multilayer Piezoelectric Transducers (PZTs), which are used in various sensing and actuating applications.
- LTCCs (Low Temperature Co-fired Ceramics): The WIP aids in the manufacturing of LTCCs, which are widely used in electronic packaging and substrate technologies.
- Varistors: The equipment is used for laminating varistors, which protect electronic circuits from voltage surges.
- Other Laminated Electronic Components: The WIP is versatile enough to be used in a wide range of laminated electronic components, enhancing their strength, stability, and appearance.
These applications demonstrate the WIP's ability to improve material properties through precise lamination, making it an indispensable tool in the semiconductor and electronic industries.
Detail&Parts
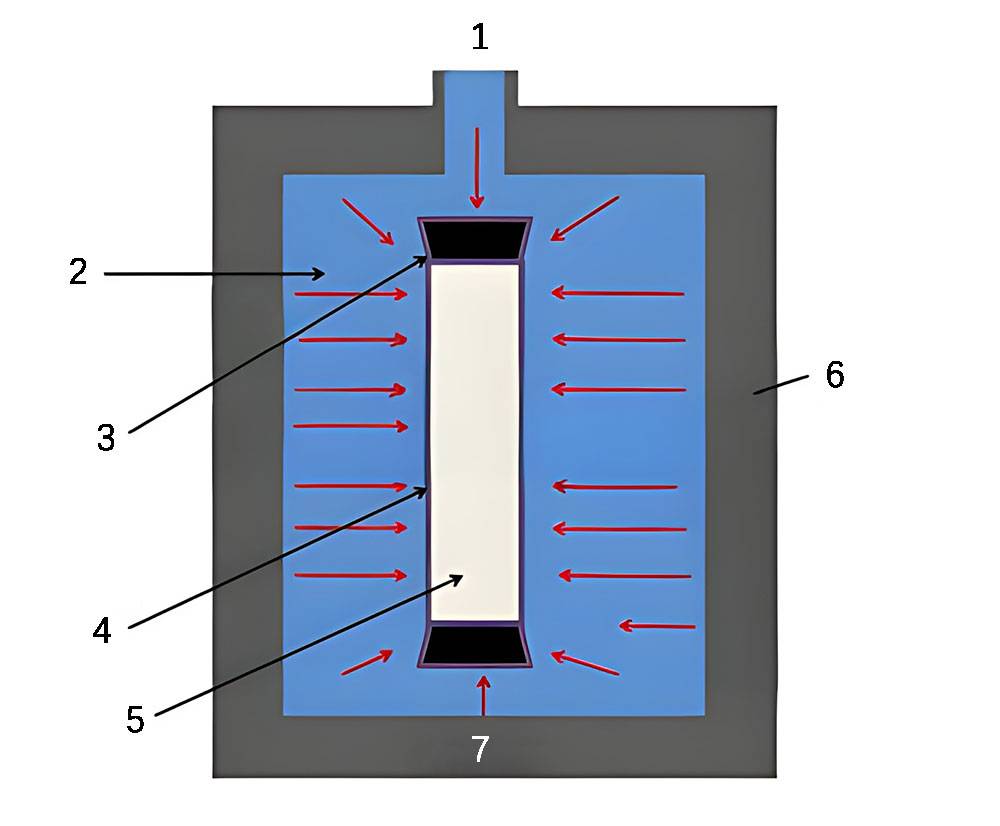
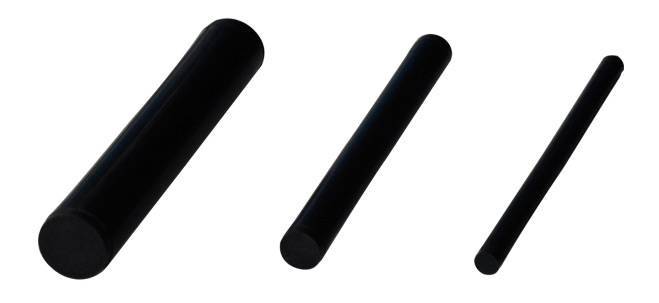
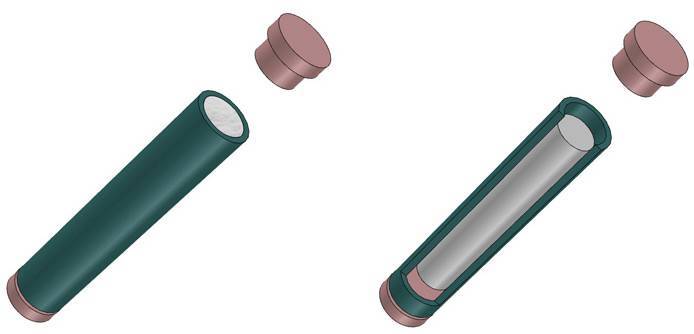
Sample preparation and mold release
technical specifications
Instrument model | PCIH-20T | PCIH-40T | PCIH-60T | PCIH-100T |
---|---|---|---|---|
Pressure Range | 0-20T | 0-40T | 0-60.0 tons | 0-100 tons |
Piston diameter | 130mm (d) in chrome plated oil cylinder | 150mm (d) in chrome plated oil cylinder | 200mm (d) in chrome plated oil cylinder | 220mm (d) in chrome plated oil cylinder |
Pressurization process | Program pressurization - Program holding-Timed pressure relief | |||
Hold time | 1 second to 999 minutes | 1 second to 999 minutes | 1 second to 999 minutes | 1 second to 999 minutes |
Pressure conversion | The program automatically converts the pressure borne by the sample | |||
Display | 7 inch LCD screen | 7 inch LCD screen | 7 inch LCD screen | 7 inch LCD screen |
Heating temperature | Room temperature-200.0C | Room temperature-200.0C | Room temperature-200.0C | Room temperature-200.0C |
Isostatic pressure | 300MPa | 300MPa | 300MPa | 500MPa |
Isostatic chamber size | Φ30×150mm(M×N) | Φ40×150mm(M×N) | Φ×50×150 (M×N) | Φ×50×150 (M×N) |
Piston stroke (T) | 50mm | 50mm | 50mm | 50mm |
Principle
The Warm Isostatic Press (WIP) operates by applying uniform pressure and controlled low temperatures (up to 100°C) to compact parts. Unlike traditional heated platen presses, WIP ensures consistent pressure on all surfaces, minimizing dimensional variations. This method is widely used in the electronics industry for laminating processes, producing high-quality multilayer ceramic components such as MLCC, LTCC, and hybrid chips.
Feature
The Warm Isostatic Press (WIP) from Kintek Autoclave is a cutting-edge piece of equipment designed specifically for the laminating processes in the semiconductor industry. This innovative system offers a range of features that not only enhance the efficiency and precision of your operations but also ensure safety and convenience for users. Below are the key features and their benefits:
- Temperature Control (50 ~ 100℃): The integrated heater in the reservoir tank allows for precise temperature control, which is crucial for achieving optimal lamination conditions. This feature ensures consistent results and improves the overall quality of the laminated materials.
- High Pressure Pump and Pressure Vessel: The WIP series is equipped with a high-pressure pump and a pressure vessel designed according to ASME standards, ensuring both safety and accuracy. This design allows for high densification and low density variation, which are essential for producing high-quality laminates.
- Pressure and Temperature Sensors: The inclusion of pressure sensors and thermocouples provides real-time monitoring and control, allowing for precise adjustments and ensuring that the process remains within the desired parameters.
- Pin Closure Type: The pin closure type design enhances user convenience by simplifying the operation and maintenance processes, making it easier to handle and use.
- Customizable Modes: For applications requiring special functions, the WIP unit offers customizable modes, ensuring that it can be adapted to meet the specific needs of various research and production environments.
- Touch Screen with Graphical Operation: The touch screen interface, combined with computer-based graphical operation, provides an intuitive and user-friendly control system, making it easier for operators to manage the process.
- Wide Range of Applications: The WIP system is versatile and can be used in a variety of applications, including hybrid chips, MLCC lamination, Bluetooth components, fuel cells, medical electronics, multilayer PZTs, LTCCs, varistors, and other laminated electronic components.
- Dry State Processing: Unlike general press machines, the WIP can process materials in a dry state, offering excellent temperature uniformity and strength, which are critical for achieving high-quality laminates.
- Adaptability and Flexibility: The WIP system's design allows for strong adaptability, enabling the processing of multiple bags at once and accommodating small batch production and large, complex parts.
These features collectively make the Warm Isostatic Press (WIP) an indispensable tool for industries requiring precise and reliable lamination processes, ensuring high-quality output and operational efficiency.
Advantages
- Enhanced Temperature Control: The Warm Isostatic Press (WIP) offers precise temperature control (50~100℃) through its integrated heater in the reservoir tank. This feature is crucial for achieving consistent lamination in semiconductor and electronic component manufacturing, ensuring improved product quality and reliability.
- Uniform Pressure Distribution: Unlike cold isostatic pressing, WIP ensures uniform pressure distribution across the material, leading to uniform density and strength. This results in minimal density variation and superior material properties, which are essential for applications like MLCC, LTCC, and hybrid chips.
- High Densification: The WIP system achieves high densification rates, which are critical for the production of high-performance electronic components. This densification minimizes porosity and enhances the mechanical and electrical properties of the final product.
- Versatility in Applications: WIP is versatile and can be used for a wide range of applications, including MLCC lamination, hybrid chips, fuel cells, medical electronics, and multilayer PZTs. Its ability to process materials in a dry state makes it suitable for various research and production needs.
- Safety and Compliance: The pressure vessel of the WIP series is designed and manufactured in accordance with ASME codes, ensuring safety and accuracy. The inclusion of pressure sensors and thermocouples further enhances operational safety and user convenience.
- User-Friendly Interface: The WIP system features a touch screen with computer-based graphical operation, making it easy to use and control. The standard interface allows for seamless integration into existing production lines, reducing the learning curve for operators.
- Customizability: For specialized applications, the WIP system can be customized to meet specific requirements. This flexibility ensures that the equipment can be tailored to the unique needs of different research and production environments.
- Improved Green Strength: The materials processed using WIP exhibit high green strength, allowing for faster sintering and machining processes. This reduces production time and increases overall efficiency in the manufacturing workflow.
By combining these advantages, the Warm Isostatic Press (WIP) stands out as a superior choice for high-precision lamination and densification processes in the semiconductor and electronic component industries.
FAQ
What Is A Warm Isostatic Press?
What Is The Warm Isostatic Press (WIP) Used For?
What Are Some Applications Of The WIP?
What Are The Key Components Of The WIP?
What Are The Applications Of A Warm Isostatic Press?
What Is Isostatic Pressing?
What Are The Benefits Of Isostatic Pressing?
What Is The Working Principle Of A Warm Isostatic Press?
What Are The Types Of Isostatic Pressing?
There are two main types of isostatic pressing:
- Hot Isostatic Pressing (HIP): This type of isostatic pressing uses high temperature and high pressure to consolidate and strengthen the material. The material is heated in a sealed container and then subjected to equal pressure from all directions.
- Cold Isostatic Pressing (CIP): In this type of isostatic pressing, the material is compacted at room temperature using hydraulic pressure. This method is commonly used to form ceramic and metal powders into complex shapes and structures.
What Are The Advantages Of Using A Warm Isostatic Press?
What Type Of Isostatic Pressing Equipment Do You Have?
What Is The Operating Temperature Range Of A Warm Isostatic Press?
What Are The Wet Bag Process And The Dry Bag Process?
The CIP molding process is divided into two methods: the wet bag process and the dry bag process.
Wet bag process:
In this method, the powder material is placed in a flexible mold bag and placed in a pressure vessel filled with high-pressure liquid. This process is ideal for producing multi-shaped products and is suitable for small to large quantities, including large-sized parts.
Dry bag process:
In the dry bag process, a flexible membrane is integrated into the pressure vessel and is used throughout the pressing process. This membrane separates the pressure fluid from the mold, creating a "dry bag." This method is more hygienic as the flexible mold does not get contaminated with wet powder and requires less cleaning of the vessel. It also features fast cycles, making it ideal for mass producing powder products in an automated process.
What Types Of Materials Can Be Processed Using A Warm Isostatic Press?
How Long Is Your Delivery Time? If I Want To Customize The Instrument, How Long Does It Take?
4.9
out of
5
This HIP system delivers precise and reliable results. It's easy to use and the digital controls provide excellent precision.
4.8
out of
5
The HIP equipment is top-notch. It offers remarkable uniformity and consistency in material processing, leading to high-quality products.
4.7
out of
5
The lab HIP press stands out for its exceptional performance. It effectively eliminates voids and enhances material density, resulting in superior product quality.
4.9
out of
5
The HIP unit's ability to handle complex geometries is impressive. It allows us to produce intricate shapes with remarkable precision and accuracy.
4.8
out of
5
The HIP system's versatility is truly impressive. It seamlessly processes various materials, making it an invaluable asset in our lab.
4.7
out of
5
The HIP press's user-friendly interface makes operation a breeze. The intuitive controls and clear display ensure efficient and effortless processing.
4.9
out of
5
The HIP equipment's construction is exceptional. The durable materials and meticulous craftsmanship guarantee longevity and reliability even under demanding conditions.
4.8
out of
5
The HIP system's speed and efficiency are remarkable. It significantly reduces processing time, enabling us to meet tight deadlines and increase productivity.
4.7
out of
5
The HIP press's value for money is unbeatable. It offers exceptional performance and reliability at a competitive price, making it an excellent investment for any lab.
4.9
out of
5
The HIP unit's technological advancements are truly groundbreaking. It incorporates cutting-edge features that enhance processing capabilities and deliver superior results.
4.8
out of
5
The HIP equipment's durability is commendable. It withstands rigorous use and maintains its exceptional performance even after prolonged operation.
4.7
out of
5
The HIP press's compact design is remarkable. It occupies minimal space in the lab, making it an excellent choice for facilities with limited area.
4.9
out of
5
The HIP unit's ease of maintenance is a huge plus. Its simple design and accessible components make upkeep a breeze, minimizing downtime and ensuring uninterrupted operation.
4.8
out of
5
The HIP press's exceptional customer service is commendable. The prompt response, technical expertise, and dedication of the support team are truly outstanding.
4.7
out of
5
The HIP equipment's extensive documentation is highly valuable. The comprehensive manuals, tutorials, and technical support resources provide invaluable guidance and ensure smooth operation.
4.9
out of
5
The HIP system's ability to integrate seamlessly with our existing lab setup is exceptional. It effortlessly communicates with other instruments and software, enhancing workflow efficiency and data management.
Products
Warm Isostatic Press for Solid State Battery Research
REQUEST A QUOTE
Our professional team will reply to you within one business day. Please feel free to contact us!
Related Products
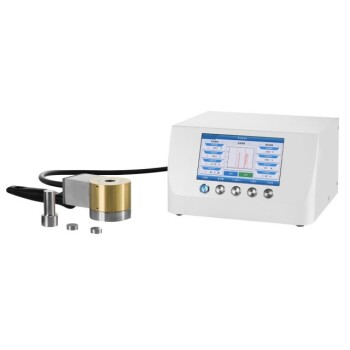
Cylindrical Lab Electric Heating Press Mold for Laboratory Applications
Efficiently prepare samples with Cylindrical Lab Electric Heating Press Mold. Fast heating, high temp & easy operation. Custom sizes available. Perfect for battery, ceramic & biochemical research.
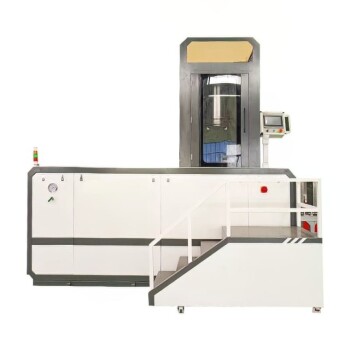
Warm Isostatic Press WIP Workstation 300Mpa for High Pressure Applications
Discover Warm Isostatic Pressing (WIP) - A cutting-edge technology that enables uniform pressure to shape and press powdered products at a precise temperature. Ideal for complex parts and components in manufacturing.
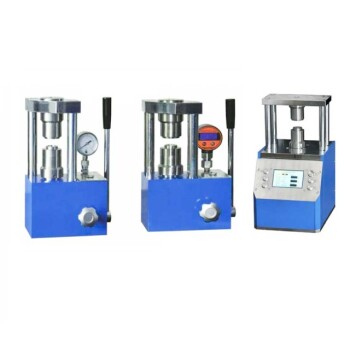
Laboratory Hydraulic Press Lab Pellet Press for Button Battery
Efficiently prepare samples with our 2T Button Battery Press. Ideal for material research labs and small-scale production. Small footprint, lightweight, and vacuum-compatible.
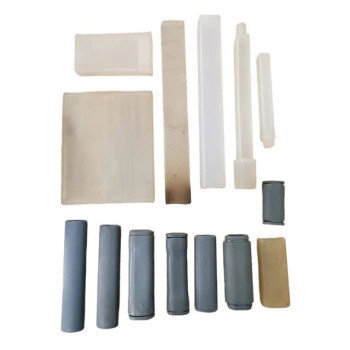
Isostatic Molding Pressing Molds for Lab
Explore high-performance isostatic pressing molds for advanced material processing. Ideal for achieving uniform density and strength in manufacturing.
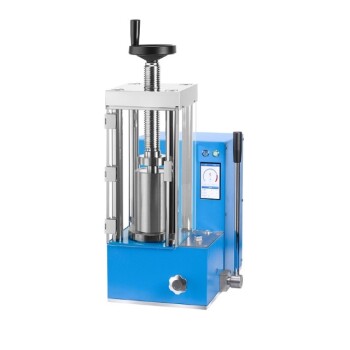
Electric Lab Cold Isostatic Press CIP Machine for Cold Isostatic Pressing
Produce dense, uniform parts with improved mechanical properties with our Electric Lab Cold Isostatic Press. Widely used in material research, pharmacy, and electronic industries. Efficient, compact, and vacuum-compatible.
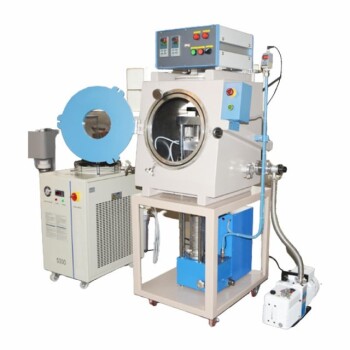
Vacuum Hot Press Furnace Machine for Lamination and Heating
Experience clean and precise lamination with Vacuum Lamination Press. Perfect for wafer bonding, thin-film transformations, and LCP lamination. Order now!
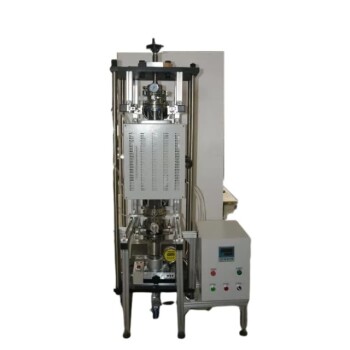
Vacuum Hot Press Furnace Heated Vacuum Press Machine Tube Furnace
Reduce forming pressure & shorten sintering time with Vacuum Tube Hot Press Furnace for high-density, fine-grain materials. Ideal for refractory metals.
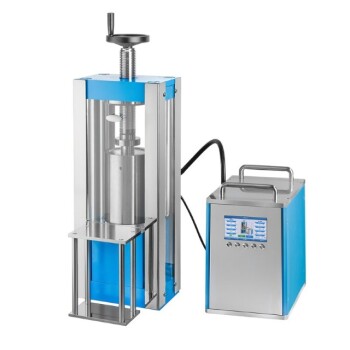
Electric Split Lab Cold Isostatic Press CIP Machine for Cold Isostatic Pressing
Split cold isostatic presses are capable of providing higher pressures, making them suitable for testing applications that require high pressure levels.
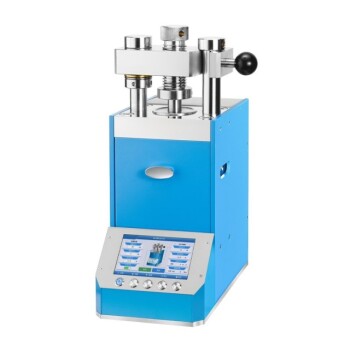
Automatic Lab Cold Isostatic Press CIP Machine Cold Isostatic Pressing
Efficiently prepare samples with our Automatic Lab Cold Isostatic Press. Widely used in material research, pharmacy, and electronic industries. Provides greater flexibility and control compared to electric CIPs.
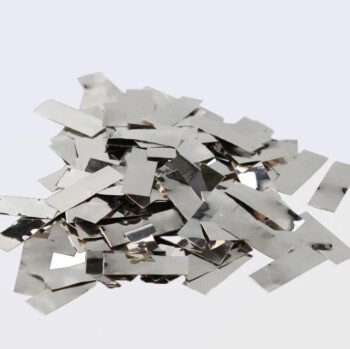
Platinum Sheet Electrode for Battery Lab Applications
Platinum sheet is composed of platinum, which is also one of the refractory metals. It is soft and can be forged, rolled and drawn into rod, wire, plate, tube and wire.
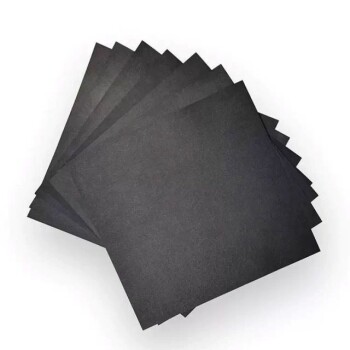
Hydrophilic Carbon Paper TGPH060 for Battery Lab Applications
Toray carbon paper is a porous C/C composite material product (composite material of carbon fiber and carbon) that has undergone high-temperature heat treatment.
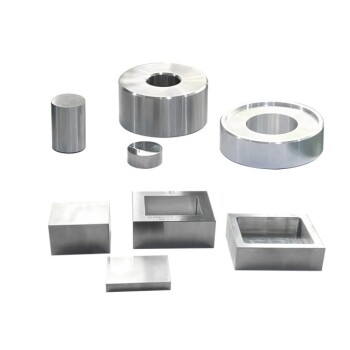
Special Heat Press Mold for Lab Use
Square, round and flat plate forming dies for hot presses.
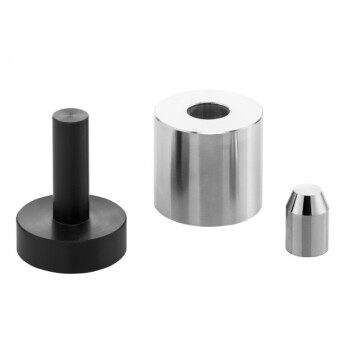
Button Battery Tablet Press Sealing Mold for Lab Use
The sealing die is essential for assembling button batteries, ensuring components like the anode, cathode, and electrolyte are securely enclosed.
Related Articles
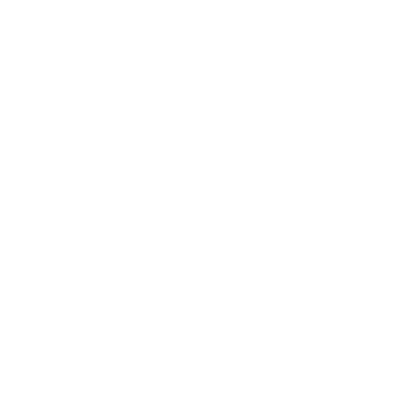
How Isostatic Presses Improve the Efficiency of Material Processing
Isostatic pressing is a manufacturing process that uses high pressure to compact and shape materials. It can be done at room temperature (cold isostatic pressing) or at high temperatures (hot isostatic pressing).
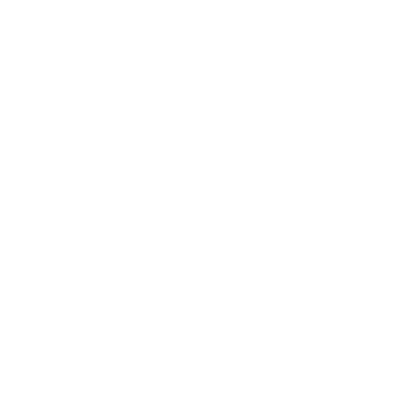
Essential Equipment for Mass Production of Solid-State Batteries: Isostatic Press
Discusses the role of isostatic pressing technology in enhancing solid-state battery performance and production efficiency.
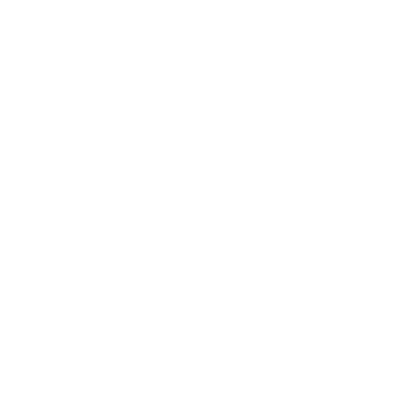
Isostatic Pressing Technology for Solid-State Batteries
Focus on isostatic pressing to commercialize next-gen batteries.
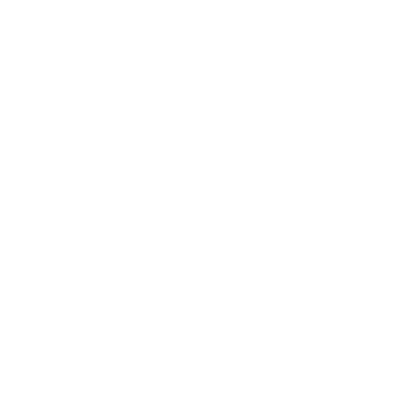
How Isostatic Presses Help Eliminate Defects in Materials
Isostatic pressing is a manufacturing process that is used to eliminate defects in materials.
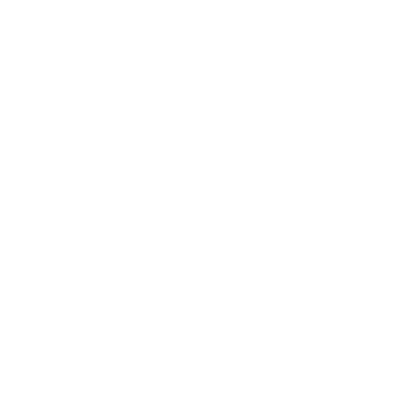
How to replace the rubber ring of isostatic press and what precautions should be taken
How to replace the rubber ring of isostatic press and matters needing attention.
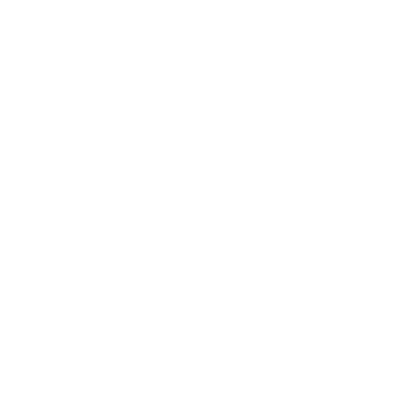
Understanding the Basics of Isostatic Pressing
Isostatic pressing is a manufacturing process used to shape and consolidate materials by applying equal pressure from all directions. The technique involves placing a material in a pressure vessel and applying hydrostatic pressure to the material.
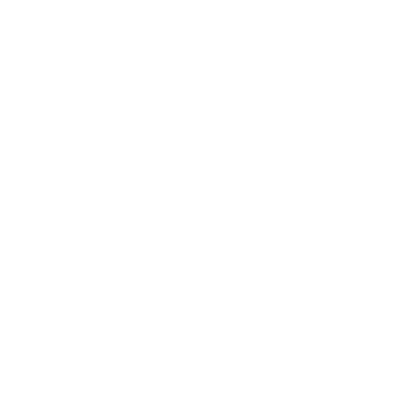
The Benefits of Using Isostatic Pressing in Manufacturing
sostatic pressing is a manufacturing process that involves applying uniform pressure to a material to achieve a specific shape or density. The process can be performed at room temperature (cold isostatic pressing or CIP) or at high temperatures (hot isostatic pressing or HIP).
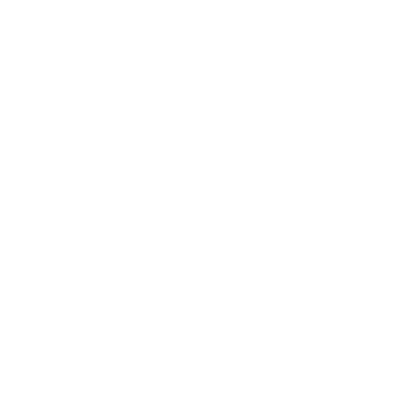
What is Isostatic Pressing Machine
Isostatic molding is a molding method that uses the incompressibility of a liquid medium and the uniform transfer of pressure. It is suitable for powder dense parts with equal pressure in all directions. The principle is to fill the mold with a liquid medium, such as water, and then subject the mold to uniform pressure. The pressure is applied by a piston or a flexible membrane.
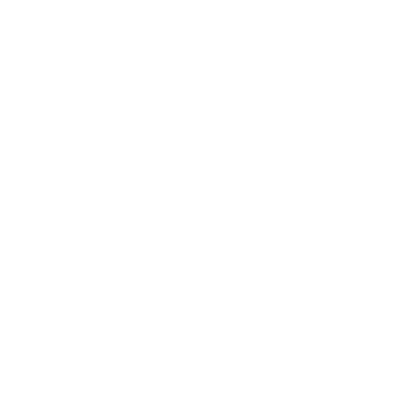
Isostatic Pressing Technology in Solid-State Battery Production
Exploring the role of isostatic pressing technology in manufacturing solid electrolytes for next-generation solid-state batteries.
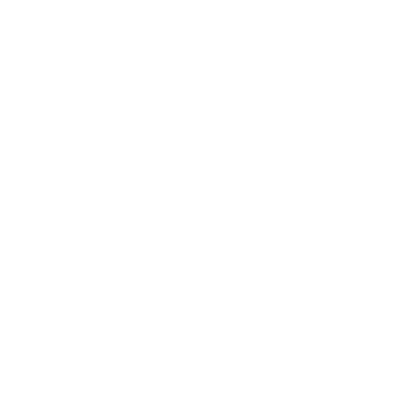
Zirconia Ceramic Rod Production Processes: Isostatic Pressing vs. Dry Pressing
A comparison of isostatic pressing and dry pressing in zirconia ceramic rod production, highlighting differences and advantages.
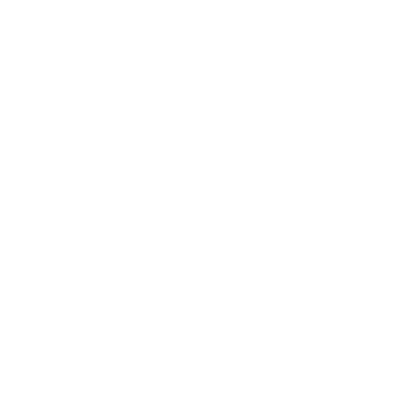
Understanding the Isostatic Pressing Process and its Types
Isostatic pressing, a technique that applies hydrostatic pressure to a material to improve its density and mechanical strength, has seen significant growth and development over the years. Isostatic pressing is commonly used for the consolidation of powders and defect healing of castings, making it a versatile process for a range of materials including ceramics, metals, composites, plastics, and carbon.
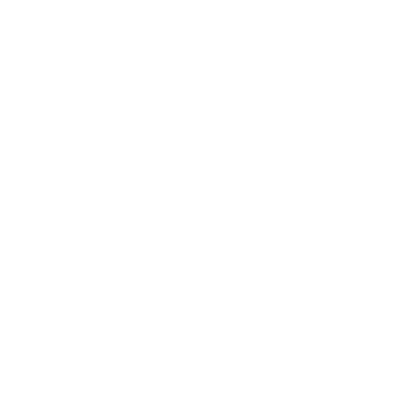
Comprehensive Guide to Isostatic Pressing:Processes, and Features
Isostatic pressing is a versatile manufacturing process that is widely used in various industries. It involves subjecting a material to equal pressure from all directions to achieve uniform density and shape. Isostatic pressing offers numerous advantages, such as the ability to produce complex shapes, uniformity in material properties, and high precision. This comprehensive guide will delve into the different types of isostatic pressing, including cold, warm, and hot pressing. We will explore the processes, features, and applications of each type, providing you with a thorough understanding of this essential manufacturing technique. So let's dive in!