Introduction to Isostatic Pressing
Isostatic pressing is a manufacturing process used to shape and consolidate materials by applying equal pressure from all directions. The technique involves placing a material in a pressure vessel and applying hydrostatic pressure to the material. This pressure is applied uniformly from all directions, allowing the material to be compacted into a desired shape. Isostatic pressing is commonly used to create high-density materials, such as ceramics, metals, and composites. The process can be performed at room temperature (cold isostatic pressing) or at elevated temperatures (hot isostatic pressing). Isostatic pressing is a versatile and efficient manufacturing process that can produce complex shapes with high precision and consistency.
Table of Contents
Overview of Isostatic Pressing Technology
Isostatic pressing technology is a widely used process in the field of materials science and engineering. It is used to produce high-quality parts with uniform density and minimal porosity. The process involves using a fluid medium, such as oil or gas, to apply pressure evenly in all directions to a powder-filled mold. Keep pressure until desired shape is achieved.
Types of isostatic pressing
Isostatic pressing can be carried out by two methods: cold isostatic pressing or hot isostatic pressing. In cold isostatic pressing, the material is processed at room temperature, while in hot isostatic pressing, the material is heated before pressing. Both methods have advantages and disadvantages depending on the type of material being processed.
Advantages of isostatic pressing
Isostatic forming offers several advantages over other forming technologies, including the ability to produce complex shapes with excellent surface finish and consistency. It is also a cost-effective process as it reduces the need for post-processing steps such as machining or grinding. Understanding the basics of isostatic pressing is crucial for anyone working with laboratory equipment, as it can help select the appropriate equipment and optimize the process for a specific application.
hot isostatic pressing
Hot isostatic pressing (HIP) is a process technology that uses high temperature and high pressure to subject metal or ceramic products to equal pressure in all directions, so that the parts can be sintered and densified. The hot isostatic pressing densification process is to put the product into a closed container, input high-pressure argon gas into the container through a compressor, and heat it through a heating furnace in the container, so that the product is densified under the action of high temperature and high pressure at the same time. After hot isostatic pressing treatment, the wear resistance, corrosion resistance and mechanical properties of the material will be greatly improved, and the fatigue life can be increased by 10 to 100 times.
cold isostatic pressing
Cold isostatic pressing (CIP) is a molding method that utilizes the incompressibility of liquid media and uniform pressure transfer. This method can apply pressure to all directions of the blank at the same time, so the pressed blank has good uniformity. Mold production is more convenient, has long service life, lower cost, and can use less or no binder. Divided into wet and dry isostatic pressing. Wet isostatic pressing is to encapsulate the pre-pressed blank in an elastic rubber mold or plastic mold, and then place it in a high-pressure container to apply high-pressure liquid. The molding pressure of the blank is usually above 100MPa. Compared with wet isostatic pressing, dry isostatic pressing is that the mold is not entirely in the liquid, but semi-fixed. Adding the blank and taking out the blank are both in dry operation, so it is called dry isostatic pressing.
In summary, isostatic forming technology is an important process in materials science and engineering and has several advantages over other forming technologies. Two isostatic pressing methods, cold pressing and hot pressing, are used to process materials at different temperatures. Hot isostatic pressing uses high temperature and high pressure to subject metal or ceramic products to equal pressure in all directions, while cold isostatic pressing uses the incompressible and uniformly transmitted pressure of the liquid medium to apply pressure to all directions of the product at the same time.
Hot isostatic pressing process
Hot isostatic pressing (HIP) is a process used to increase the density, mechanical properties and overall quality of various materials. The process involves heating the material to high temperatures and applying high pressure to it while in an inert gas pressure vessel.
Stage 1: Internal imperfections and pores are destroyed
In the first stage of the HIP process, internal defects and pores are destroyed. The external pressure is greater than the high-temperature strength of the material, causing plastic deformation of the material and destroying defects and pores. This creates internal surface contact between the material particles.
Stage 2: Material undergoes high-temperature creep
In the second stage of the HIP process, the external pressure is lower than the high-temperature strength of the material. Materials undergo high-temperature creep, and contact between material particles leads to interpenetration and diffusion bonding. This completely eliminates defects and porosity, allowing the density of the material to approach the theoretical density.
Thin wall prestressed winding unit
The use of thin-walled prestressed winding units in the HIP process enables a uniform and rapid cooling process, increasing productivity by 70% compared to the natural cooling process.
Advantages of hot isostatic pressing
The main advantages of hot isostatic pressing technology are increased product density, improved mechanical properties, increased productivity, reduced scrap and losses, and the ability to form metallurgical bonds between dissimilar materials.
Applications of hot isostatic pressing
Hot isostatic pressing is currently used not only for the processing of castings, powder metallurgy and the ceramic industry, but also for the manufacture of porous materials, near net shapes, material bonding, plasma spraying and high-end graphite.
In conclusion
HIP processes are an important part of materials science and are used to manufacture aerospace components, medical implants, and other advanced materials. The process helps improve the quality and performance of a variety of materials and components by eliminating porosity, increasing density and enhancing the material's mechanical properties. The success of the HIP process depends on several factors, including the temperature, pressure and duration of the process, as well as the type of material being pressed.
Cold isostatic pressure explained
Cold isostatic pressing (CIP) is a manufacturing process that involves compacting powdered materials into a solid uniform mass prior to processing or sintering. This process, also known as hydrostatic pressing, is used to produce high-integrity blanks or preforms that exhibit little deformation or cracking when fired.
Wet bag and dry bag isostatic pressing
There are two types of cold isostatic pressing methods: wet bag and dry bag. Wet bag isostatic pressing is a method very similar to the theoretical concept of isostatic pressing, whereby equal hydrostatic pressure is applied to all external powder surfaces simultaneously. The resulting compact has a uniform density and low clamping stress, allowing it to be processed in the green state. There is little distortion when fired, reducing or eliminating machining, which is difficult and expensive and requires the use of diamond tools. The dry bag isostatic pressing process, on the other hand, is suitable for pressing relatively long compacts at high productivity. The process can be used for simple shapes where the powder-filled mold is sealed and compression occurs between the mold and the pressure vessel.
How cold isostatic pressing works
Compared to cold pressing, isostatic pressing applies pressure evenly over the entire surface of the mold. There is no die wall friction that has a significant impact on the density distribution of cold pressed parts, so a more uniform density is achieved. Eliminating die wall lubricant also allows for higher pressing densities and eliminates problems associated with lubricant removal before or during final sintering. Additionally, if necessary, air can be removed from the loose powder before compaction. Therefore, isostatic pressing provides higher, more uniform density at a given compaction pressure and is relatively free of density defects when applied to brittle or fine powders. Because the compaction pressure is uniform, the cross-section to height ratio of the part is not as limiting a factor as it is with uniaxial pressing. Additionally, cold isostatic pressing can be used to compact more complex shapes compared to uniaxial pressing.
Advantages and Disadvantages of Cold Isostatic Pressing
The advantages of cold isostatic pressing are many and can be summarized as follows:
- Low distortion during firing
- Consistent shrinkage during firing
- Parts can be fired without drying
- Most green (unfired) briquettes can be processed
- Compact structure and low internal stress during pressing
- Large pressed part capabilities (wet bags)
- Low mold cost (wet bag)
- Density higher than achievable by mechanical pressing at a given pressing pressure
- Capable of pressing very high aspect ratio (>200) compacts
- Ability to press parts with internal shapes including threads, splines, serrations and tapers
- Ability to press long and thin-walled parts
- Able to suppress weak powders
- It is possible to press compacts having two or more layers of powders with different properties.
The disadvantages of cold isostatic pressing are:
- The pressed surfaces adjacent to flexible bags are less precise than mechanical pressing or extrusion and often require subsequent processing
- Fully automatic dry bag presses typically require relatively expensive spray-dried powders
- Productivity is lower than extrusion or die compaction.
In summary, cold isostatic pressing is an effective method for producing high-quality materials with excellent strength and durability. It is a reliable and cost-effective process that is widely adopted by manufacturers across a wide range of industries. Understanding the basics of cold isostatic pressing can help researchers and engineers develop new materials and improve existing ones. By utilizing this process, manufacturers can create products that are stronger, more durable, and more resistant to wear and tear.
Advantages of hot isostatic pressing
Hot isostatic pressing (HIP) is a manufacturing process that offers several advantages for producing high-performance materials. The process involves applying high pressure and temperature to the material simultaneously, resulting in densification and sintering in a single step. Here are some of the advantages of hot isostatic pressing:
Improve mechanical properties
One of the significant advantages of HIP is that it can improve the mechanical properties of materials. The simultaneous application of high temperature and pressure helps eliminate internal porosity, thereby improving impact resistance, ductility and fatigue strength. This process enables the material to achieve the same or better mechanical properties as forged materials.
Isotropic properties
HIP also enables fine grain structure and uniformity, resulting in isotropy. This uniformity in material properties enhances the predictability of part life due to reduced variation in mechanical properties.
Wear and corrosion resistance
HIP can also help improve the material's resistance to wear and corrosion. The process enables cladding and extended alloying possibilities, controls grain size and shape, and produces a uniform microstructure in the material. This improves wear and corrosion resistance, making it ideal for the aerospace, medical and automotive industries.
Diffusion bonding
HIP is capable of diffusion bonding similar and dissimilar materials in powder or solid form. This process eliminates the need for additional welding and related inspections, thereby reducing production time and costs.
Reduce expensive materials
With cladding, components are molded using premium or expensive materials only in critical areas, reducing the overall cost of materials used in production.
In summary, hot isostatic pressing is a versatile manufacturing process that offers multiple advantages for producing high-performance materials. The ability to produce near-net shape parts, improved material properties, and reduced production costs have made HIP a popular choice within the industry. The process helps improve the material's mechanical properties, wear and corrosion resistance, and enables diffusion bonding of similar and dissimilar materials.
Types of Isostatic Pressing: Wet Bags and Dry Bags
Isostatic pressing is a method of applying uniform pressure to a material from all directions, resulting in a highly dense and uniform product. There are two main types of isostatic pressing: wet bag and dry.
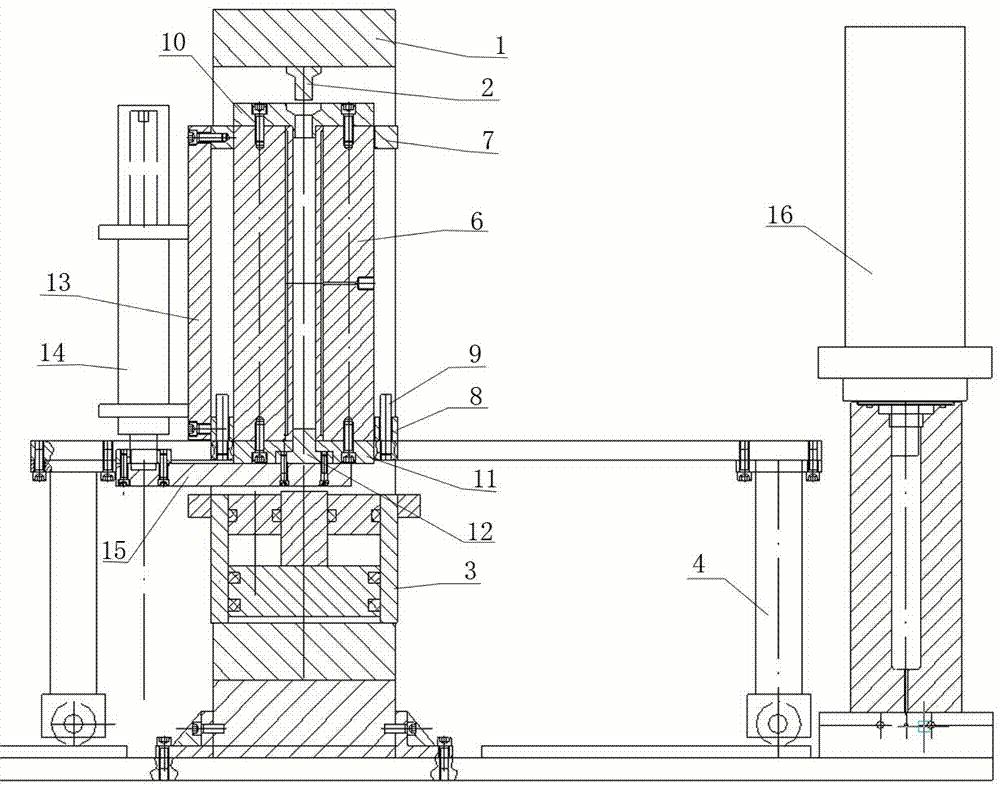
Wet bag isostatic pressing
In wet-bag isostatic pressing, the material to be pressed is placed in a flexible bag containing a liquid pressure-transmitting medium, such as oil or water. The bag is placed in a pressure vessel and subjected to high pressure from all directions. Wet bag isostatic pressing is best suited for difficult-to-handle materials such as powders, fibers and whiskers. Common shapes produced by this method are axisymmetric open or closed ends, hollow shapes, such as tubes.
Wet bag isostatic pressing is a versatile option for achieving high densities from metal and ceramic powders. The geometry and volume of the mold cavity are designed to achieve the target final size. The inner diameter of this pressed shape will have higher accuracy than the outer diameter. Another option is an expansion tool, which forces pressurized fluid into the interior surface of the object; the powder is pressed outward from the inner elastic mold walls against the outer rigid shell. This process provides a way to produce high uniform pressure and high density due to the elimination of die wall friction.
Dry bag isostatic pressing
Dry bag isostatic pressing, on the other hand, involves the use of a rigid container, such as a rubber or metal mold, to hold the material in place. The container is then placed into a pressure vessel and subjected to high pressure from all directions. Dry bag isostatic pressing is suitable for materials that are easy to form, such as ceramics and metals.
Dry bag isostatic pressing is a highly efficient production method for small parts with axially symmetrical shapes. Since the rubber tool is integrated into the device, separate dipping and disassembly steps are not required, simplifying automation and rapid production. However, there is friction on one side of the mold and is not compressed by the pressurized liquid. Likewise, there are more shape and size restrictions in the dry bag process. Spark plugs, for example, require green machining to develop the required surface features.
Pros and cons
Isostatic pressing is often chosen to achieve high density and process shapes that cannot be compacted by a single-axis press. If needed, some complex shapes can be designed into the elastic mold. The wet bag variant is better suited for the production of large parts compared to the dry bag process. However, loading and unloading of molds can reduce productivity and limit the automation of wet bag presses. Likewise, wet bag processes are also more dense because they involve very little friction. The dry bag version offers advantages in terms of automation and productivity. For both types of isostatic pressing, the mold cost and process complexity are higher than those for uniaxial pressing.
In summary, understanding the basics of isostatic pressing and the types of isostatic pressing available will help manufacturers choose the most appropriate process for their application. Wet bag isostatic pressing is best suited for materials that are difficult to process, such as powders, fibers, and whiskers, while dry bag isostatic pressing is suitable for materials that are easily formed, such as ceramics and metals.
CONTACT US FOR A FREE CONSULTATION
KINTEK LAB SOLUTION's products and services have been recognized by customers around the world. Our staff will be happy to assist with any inquiry you might have. Contact us for a free consultation and talk to a product specialist to find the most suitable solution for your application needs!