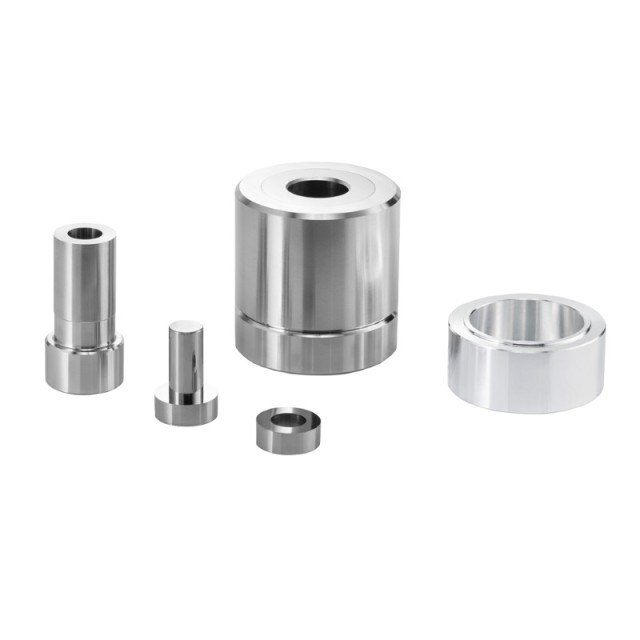
Molds & Accessories
Ring Press Mold for Lab Applications
Item Number : PMO
Price varies based on specs and customizations
- Die heating
- Alloy tool steel :Cr12MoV
- Indenter hardness
- HRC60-HRC62
- Sample size
- Φ7-3——Φ20-10 mm (M)
- Cavity depth
- 40mm (N)、45 (d)
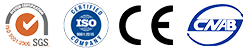
Shipping:
Contact us to get shipping details Enjoy On-time Dispatch Guarantee.
Why Choose Us
Reliable PartnerEasy ordering process, quality products, and dedicated support for your business success.
Applications
Ring Press Dies, also known as Circular Pellet Press Die Sets, are integral components in various industrial and laboratory processes. These dies are designed to create round pellets with high precision, ranging from very thin to over 2 inches in length. The versatility and precision of these dies make them essential in multiple sectors. Below are the main application areas of Ring Press Dies, highlighting their use in different industries and processes:
- Material Testing: Used to create uniform pellets for material testing in laboratories, ensuring consistent results in hardness, tensile strength, and other properties.
- Automotive Industry: Essential in the manufacturing of various components through die punch press processes, contributing to the precision and quality of automotive parts.
- Forging Processes: Particularly in hubbing, where patterns are pressed into die cavities, commonly used in the production of silverware and other metal articles.
- Coin Production: Involved in the manufacturing of coins and other small metal articles, utilizing the precision and controlled compression rates of press forging.
- Industrial Applications: Used in high-volume production settings where the creation of any size and shape is required with minimal scrap and draft.
- Research and Development: In research settings, these dies are used to prepare samples for various analyses, ensuring uniformity and accuracy in experimental results.
These applications underscore the critical role of Ring Press Dies in achieving precision and efficiency in both industrial production and laboratory research.
Detail & Parts
![Ring mold [Φ3-40mm]](https://image.kindle-tech.com/images/products/581/9958a17c9caae87365b4d9f1049d996567bc2411db4c1.jpg)
![Ring mold [Φ41-80mm]](https://image.kindle-tech.com/images/products/581/37291f5f82bd040c7f7a77a1f30855b367bc23d444e81.jpg)
Technical specifications
Instrument model | PMQ | |
---|---|---|
Sample shape | ![]() |
|
Die heating | Alloy tool steel :Cr12MoV | |
Indenter hardness | HRC60-HRC62 | |
Sample size | Φ7-3、Φ10-5、Φ20-10 mm M) | Φ30-10、Φ50-20mm (d) |
Cavity depth | 40mm (N) | 45 (d) |
Dimensions | Φ53*120mm (L*H) | Φ72*100mm、Φ88*120(D*L) |
Weight | 1.4Kg | 3.5kg、5kg |
Diagram of hydraulic powder press size | ![]() |
![]() |
Operation steps
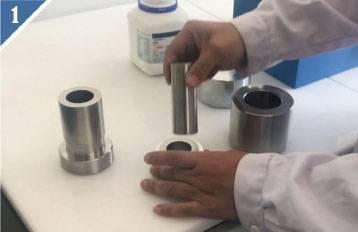
1.Assemble the die.
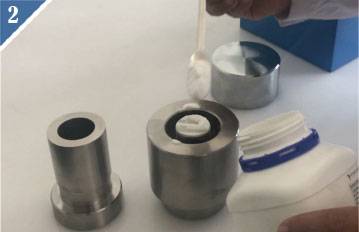
2.The sample is loaded into the die cavity.
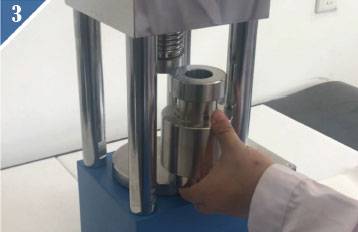
3.Place the die in the tablet press
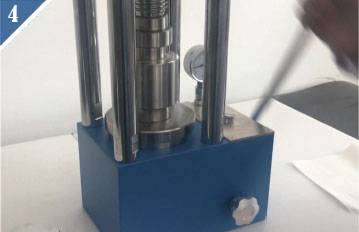
4.Push the pressure to the pressure we need.
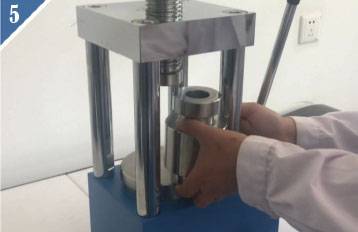
5.Remove the die.
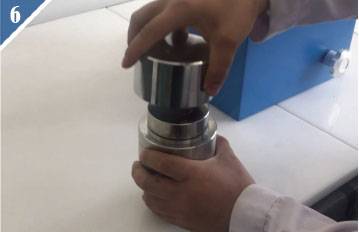
6.Install the demoulding tool.
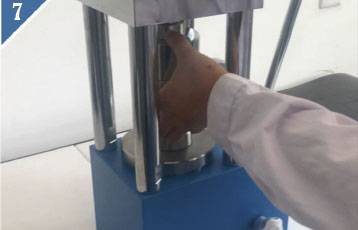
5.The sample is ejected with a tablet press.
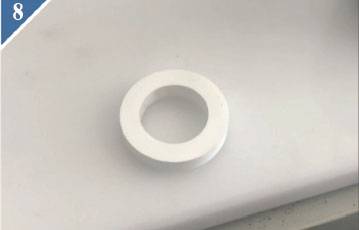
6.Take out the pressed sample.
Features of Ring Press Dies
Ring Press Dies are essential components in various industrial applications, particularly in the automotive and manufacturing sectors. These dies are designed to create precise, round pellets with diameters ranging from very thin to over 2 inches. The features of Ring Press Dies not only enhance the quality of the pellets but also improve the efficiency and flexibility of the production process.
- Precision Machining: Each die is meticulously machined from high-quality materials, ensuring accuracy in pellet dimensions and consistency in production. This precision is crucial for applications where uniformity is essential, such as in the automotive industry.
- Versatile Diameter Options: The ability to produce pellets with a wide range of diameters makes these dies adaptable to various project requirements. This versatility is beneficial for industries that require different sizes of pellets for different applications.
- Enhanced Production Efficiency: The use of Ring Press Dies can streamline the production process, reducing the need for multiple dies or machines. This efficiency is particularly advantageous in transfer press stamping operations, where a single die can handle a series of tasks, thereby saving time and resources.
- Improved Setup Flexibility: With the option to employ a single die or a series of dies, these press dies offer a high degree of flexibility in setup. This adaptability allows for the accommodation of diverse project needs without the need for extensive modifications.
- Automation Compatibility: Modern Ring Press Dies are designed to integrate seamlessly with automatic transfer systems, further enhancing the efficiency of the stamping process. This automation reduces the reliance on manual labor, minimizing errors and increasing productivity.
Overall, Ring Press Dies are a critical investment for industries seeking to enhance their production capabilities through precision, versatility, and efficiency.
Principle
Ring Press Dies, also known as Circular Pellet Press Die Sets, function by precisely compressing materials into round pellets of various diameters and lengths. The process involves the coordinated movement of upper and lower punches within a middle die, facilitated by a rotating turntable. This mechanism ensures uniform pressure distribution, creating pellets with consistent shape and density. The dies are meticulously machined from high-quality materials to maintain accuracy and durability in each pressing operation.
Advantages
- Precision Machining: Circular Pellet Press Die Sets are meticulously machined to ensure precise diameters, ranging from very thin to over 2 inches in length, making them ideal for a wide range of applications.
- High Throughput: Equipped with advanced peripheral devices, these die sets can independently control the weight, thickness, and hardness of pellets, enabling the production of up to 1,000,000+ pellets per hour, depending on the press size and tooling configurations.
- Cost Efficiency: Compared to single punch presses, rotary presses offer greater cost efficiency, making them a preferred choice for high-volume production in various industries including pharmaceutical, nutraceutical, confectionery, and veterinary applications.
- Versatility: These die sets are not only used for traditional tablet production but also for creating catalysts, ceramics, powdered metals, and other compressible materials, showcasing their versatility in different sectors.
- Remote Monitoring and Data Archiving: With the ability to interface with in-house network systems, these die sets support remote monitoring and data archiving, enhancing operational efficiency and data management.
- Quality Materials: Each die set is made from high-quality materials, ensuring durability and longevity, which is crucial for maintaining consistent pellet quality over extended periods of use.
FAQ
What Are The Applications Of Pellet Presses?
What Is A Press Mold?
How Does A Pellet Press Work?
What Is Press Mould In Ceramics?
What Are The Benefits Of Using A Pellet Press?
How Are Pellet Molds Used?
What Factors Should Be Considered When Selecting A Pellet Press?
What Types Of Materials Can Be Pelletized Using Pellet Molds?
How Can One Select The Appropriate Pellet Mold For Their Specific Application?
4.7
out of
5
Exceptional precision and durability. A game-changer for our lab's material testing.
4.8
out of
5
Incredible value for money. Streamlined our automotive part production significantly.
4.9
out of
5
Top-notch quality and efficiency. Perfect for our high-volume coin production needs.
4.7
out of
5
Technologically advanced and reliable. Essential for our research and development.
4.8
out of
5
Fast delivery and excellent customer service. Highly recommend for industrial applications.
4.9
out of
5
Outstanding versatility and precision. A must-have for any laboratory setting.
4.7
out of
5
Durable and efficient. Simplified our forging processes remarkably.
4.8
out of
5
Highly satisfied with the technological advancements. Boosted our production capabilities.
REQUEST A QUOTE
Our professional team will reply to you within one business day. Please feel free to contact us!
Related Products
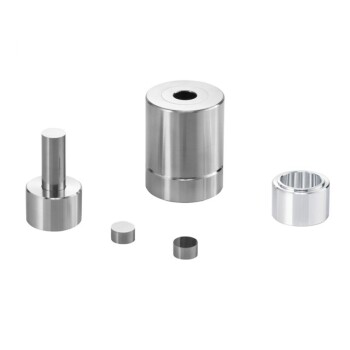
Carbide Lab Press Mold for Laboratory Applications
Form ultra-hard samples with Carbide Lab Press Mold. Made of Japanese high-speed steel, it has a long service life. Custom sizes available.
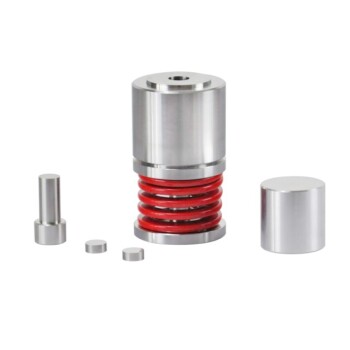
Round Bidirectional Press Mold for Lab
The round bidirectional press mold is a specialized tool used in high-pressure molding processes, particularly for creating intricate shapes from metal powders.

Special Shape Press Mold for Lab
Discover high-pressure special shape press molds for diverse applications, from ceramics to automotive parts. Ideal for precise, efficient molding of various shapes and sizes.
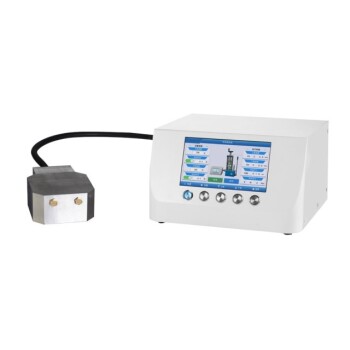
Double Plate Heating Press Mold for Lab
Discover precision in heating with our Double Plate Heating Mold, featuring high-quality steel and uniform temperature control for efficient lab processes. Ideal for various thermal applications.
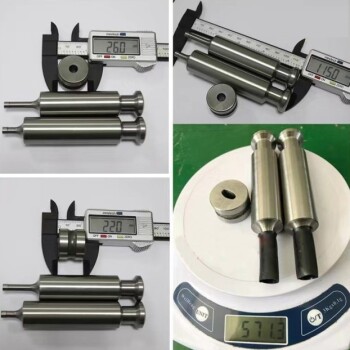
Multi-Punch Rotary Tablet Press Mold Ring for Rotating Oval and Square Molds
The multi-punch rotary tablet press mold stands as a pivotal component in pharmaceutical and manufacturing industries, revolutionizing the process of tablet production. This intricate mold system comprises multiple punches and dies arranged in a circular fashion, facilitating rapid and efficient tablet formation.
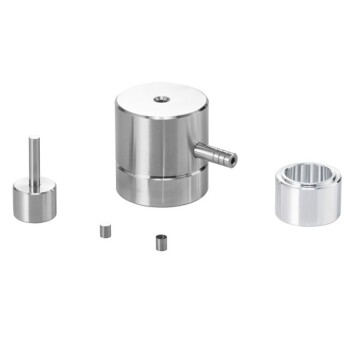
Cylindrical Press Mold for Lab Applications
Efficiently form and test most samples with Cylindrical Press Molds in a range of sizes. Made of Japanese high-speed steel, with long service life and customizable sizes.
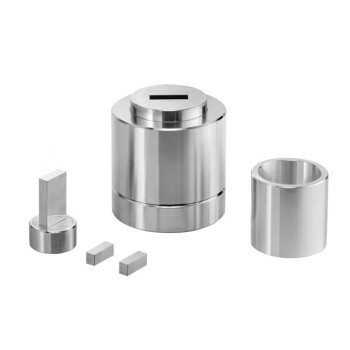
Assemble Square Lab Press Mold for Laboratory Applications
Achieve perfect sample preparation with Assemble Square Lab Press Mold. Quick disassembly eliminates sample deformation. Perfect for battery, cement, ceramics, and more. Customizable sizes available.
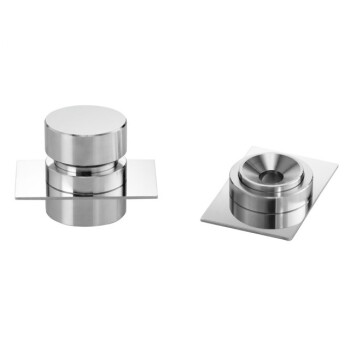
No Demolding Lab Infrared Press Mold for Laboratory Applications
Effortlessly test your samples with no demolding required using our lab infrared press mold. Enjoy high transmittance and customizable sizes for your convenience.
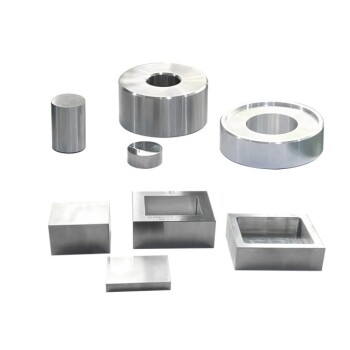
Special Heat Press Mold for Lab Use
Square, round and flat plate forming dies for hot presses.
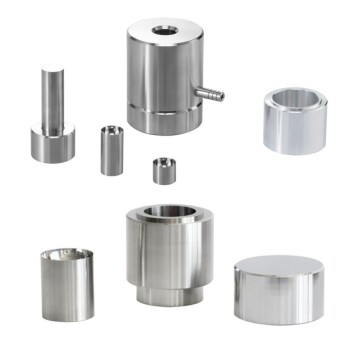
Explore versatile Hydraulic Hot Press molds for precise compression molding. Ideal for creating various shapes and sizes with uniform stability.
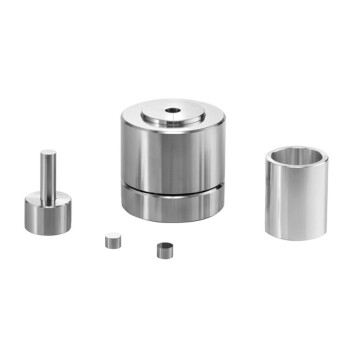
Assemble Lab Cylindrical Press Mold
Get reliable and precise molding with Assemble Lab Cylindrical Press Mold. Perfect for ultra-fine powder or delicate samples, widely used in material research and development.
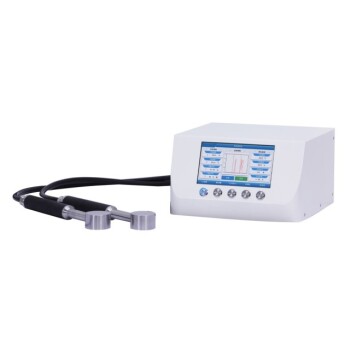
Infrared Heating Quantitative Flat Plate Press Mold
Discover advanced infrared heating solutions with high-density insulation and precise PID control for uniform thermal performance in various applications.
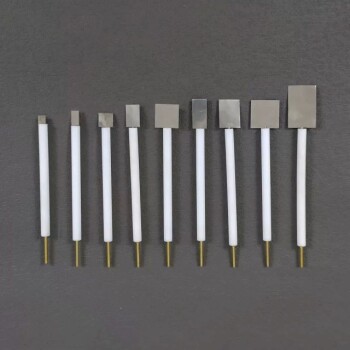
Platinum Sheet Electrode for Laboratory and Industrial Applications
Elevate your experiments with our Platinum Sheet Electrode. Crafted with quality materials, our safe and durable models can be tailored to fit your needs.
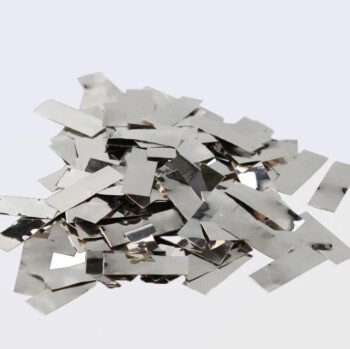
Platinum Sheet Electrode for Battery Lab Applications
Platinum sheet is composed of platinum, which is also one of the refractory metals. It is soft and can be forged, rolled and drawn into rod, wire, plate, tube and wire.
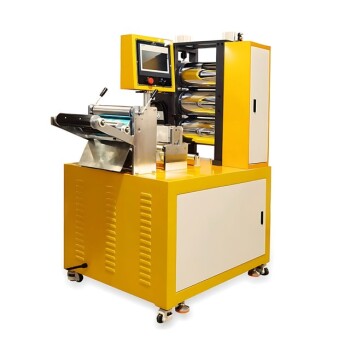
Small Lab Rubber Calendering Machine
Small lab rubber calendering machine is used for producing thin, continuous sheets of plastic or rubber materials. It is commonly employed in laboratories, small-scale production facilities, and prototyping environments to create films, coatings, and laminates with precise thickness and surface finish.
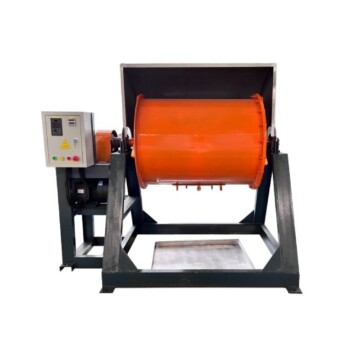
Stainless Steel Laboratory Ball Mill for Dry Powder and Liquid with Ceramic Polyurethane Lining
Discover the versatile stainless steel dry powder/liquid horizontal ball mill with ceramic/polyurethane lining. Ideal for ceramic, chemical, metallurgical, and building materials industries. High grinding efficiency and uniform particle size.
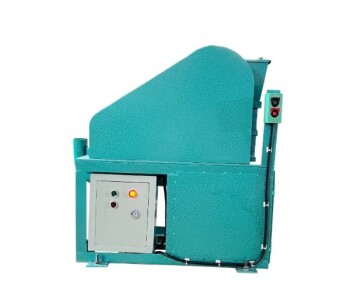
Sealed Jaw Crusher High Efficiency Environmental Protection Safe and Reliable
Discover our Sealed Jaw Crusher: High efficiency, environmental protection, Safe and reliable crushing for labs, mines, and more.
Related Articles
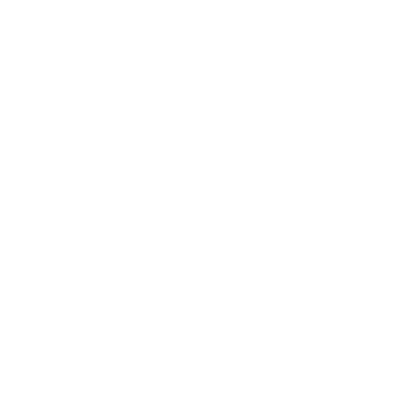
Ceramic Isostatic Pressing Mold Technology
Exploring the design and factors affecting ceramic isostatic pressing molds.
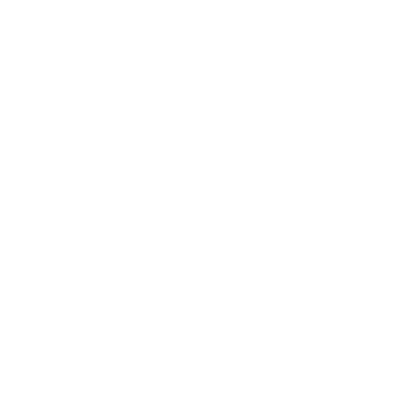
Manual Pellet Press: A Comprehensive Guide to Efficient Lab Pelletizing
Explore the intricacies of manual pellet presses, including operation, safety, and maintenance tips. Learn how to choose the right press, understand force gauges, and optimize pellet quality for your lab experiments.
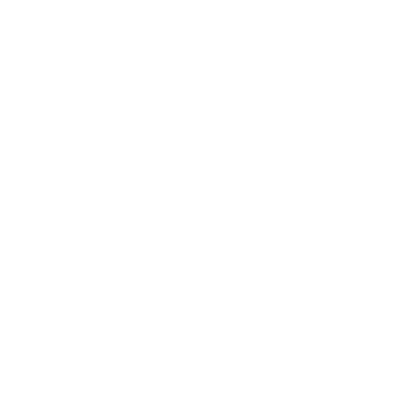
Optimizing Laboratory Analysis with Split Automatic Heated Lab Pellet Press
Explore the advanced features and benefits of split automatic heated lab pellet presses for precise pellet preparation in various analytical applications. Ideal for high-throughput laboratories.
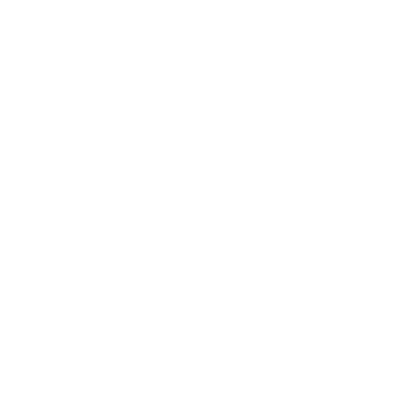
Comprehensive Guide to Isostatic Pressing Molds: Types, Processes, and Applications
Explore the detailed world of isostatic pressing molds, including types like wet bag and dry bag, their processes, and applications. Learn how these molds ensure uniform density and high-strength products.
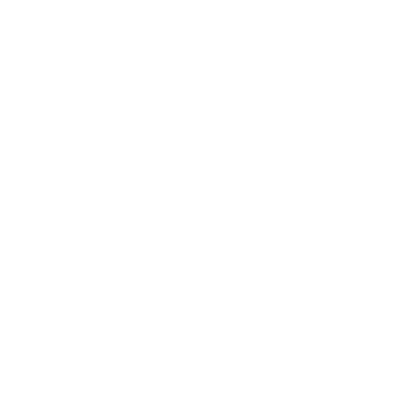
Manual Lab Hydraulic Pellet Press: Comprehensive Guide to High-Quality Pellet Preparation
Explore the detailed guide on using a Manual Lab Hydraulic Pellet Press for high-quality pellet preparation in spectral analyses. Learn about features, operation, and maintenance for optimal performance.
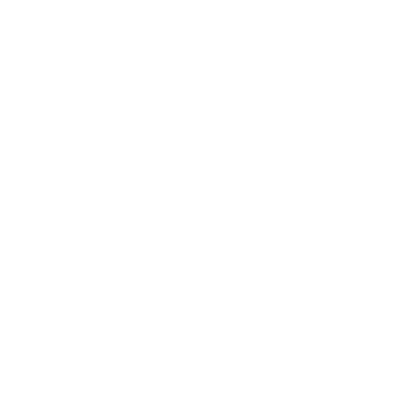
Comprehensive Guide to Integrated Manual Heated Lab Pellet Presses
Explore the features and applications of integrated manual heated lab pellet presses. Learn about customization options, capacities, and benefits for spectroscopy and analysis.
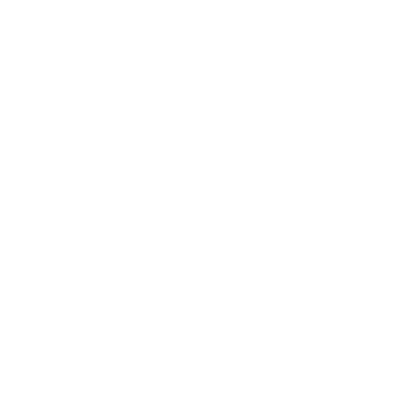
Issues with Poor Demoulding in Manual Tablet Presses
Analyzes the causes of poor demoulding in manual tablet presses, focusing on powder, mold, machine body, and operator factors.
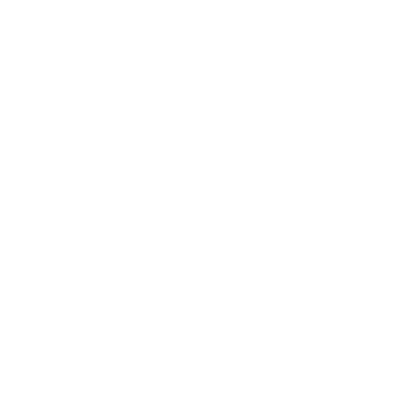
Mastering XRF Sample Preparation: 7 Proven PRESS Strategies for Optimal Results
Elevate your XRF analysis with 7 advanced PRESS strategies. Learn expert tips for successful XRF pellet pressing, optimal sample preparation, and consistent results.
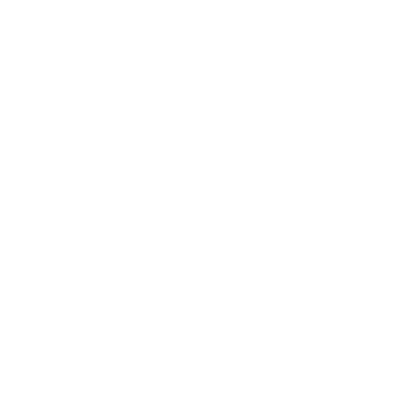
X-Ray Fluorescence Spectrometer: Powder Compression Method for Sample Preparation
This article discusses the powder compression method in XRF spectral analysis, focusing on sample preparation techniques and equipment.
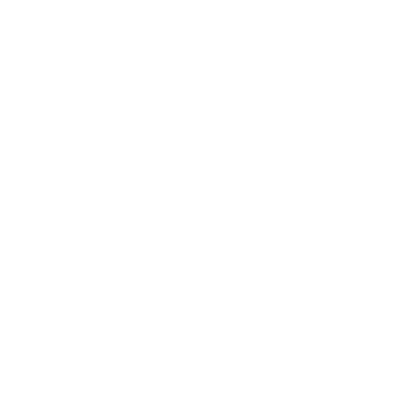
Zirconia Ceramic Rod Production Processes: Isostatic Pressing vs. Dry Pressing
A comparison of isostatic pressing and dry pressing in zirconia ceramic rod production, highlighting differences and advantages.
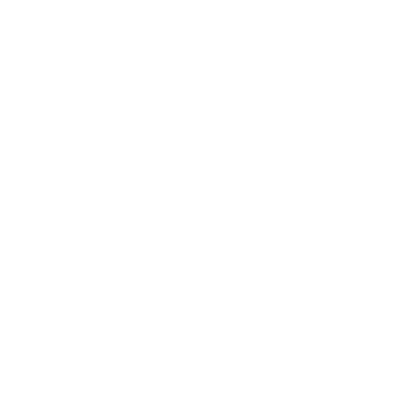
How to replace the rubber ring of isostatic press and what precautions should be taken
How to replace the rubber ring of isostatic press and matters needing attention.
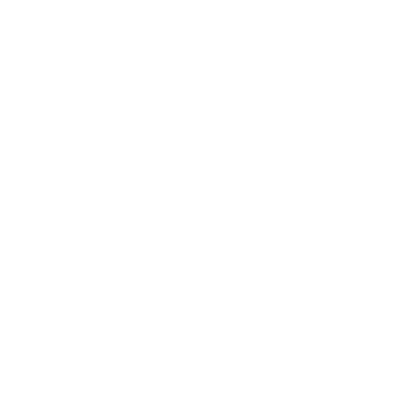
Understanding Isostatic Pressing: Cold and Hot Techniques
Isostatic pressing is a powder processing technique that uses fluid pressure to compact the part. It involves placing metal powders in a flexible container, which acts as a mold for the part. Fluid pressure is exerted over the entire outside surface of the container, causing the powder to be formed into the desired geometry. Unlike other processes that exert force on the powder through an axis, isostatic pressing applies pressure equally from all directions.