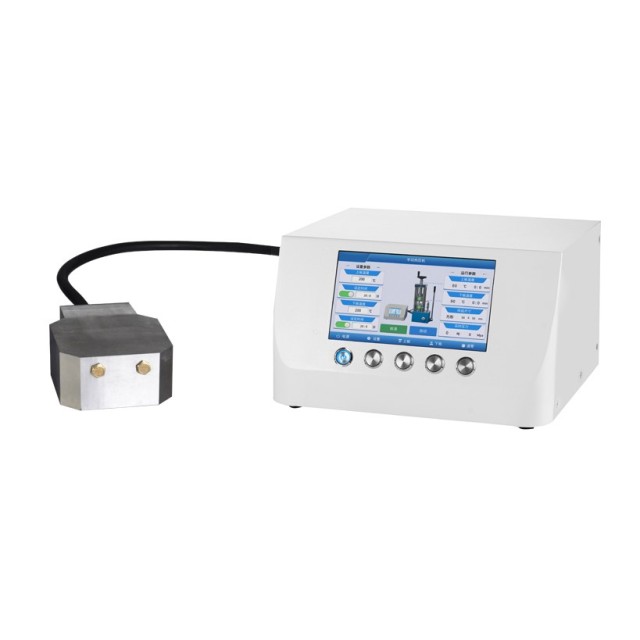
Molds & Accessories
Double Plate Heating Press Mold for Lab
Item Number : PMD
Price varies based on specs and customizations
- Heating temperature
- Room temperature-300C
- Sample size
- <Φ180mm (M)
- sample thickness
- 0.02-0.1mm(N)
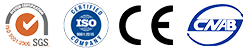
Shipping:
Contact us to get shipping details Enjoy On-time Dispatch Guarantee.
Why Choose Us
Reliable PartnerEasy ordering process, quality products, and dedicated support for your business success.
Introduction
The double plate heating mold features a split design with separate upper heating and lower cooling zones. The upper heating plate utilizes multiple electric heat pipes for stable heating, while the lower cooling plate incorporates a serpentine water cooling pipe for rapid cooling. This integrated system offers versatility in various applications. The hydraulic system includes automatic pressure compensation and optimized electro-hydraulic drive design to enhance efficiency and reduce energy consumption. The electrical control system adheres to strict standards, ensuring precise temperature, time, and pressure control.
Applications
Double plate heating molds, particularly those utilizing inductive heating and high-quality machining, find extensive use across various industries due to their ability to provide precise and uniform heating. These molds are essential in processes that require controlled thermal conditions, ensuring the integrity and quality of the final product. Below are some of the main application areas where double plate heating molds are utilized:
- Laboratory Equipment: Used in laboratory settings for precise heating applications, ensuring consistent results in experiments and research.
- 3D Printer Heated Beds: Essential for maintaining the temperature necessary for successful 3D printing, particularly with materials like ABS and PLA.
- Food Processing: Employed in griddles, waffle irons, and other cooking appliances where uniform heating is crucial for food preparation.
- Industrial Heating: Used in various industrial processes that require heat treatment, such as annealing and heat sealing.
- Automotive Applications: Help in deicing and defogging car windshields and side mirrors, ensuring safety and visibility.
- Electronics Manufacturing: Used in the production of electronic components where precise temperature control is necessary.
- Medical Devices: Employed in the manufacturing of medical equipment that requires sterilization and precise heating.
- Textile Industry: Used in clothes irons and steamers, ensuring fabric smoothness and quality.
These applications highlight the versatility and importance of double plate heating molds in maintaining precise and uniform heating across different sectors.
Detail & Parts
![Double plate heating mold [300℃]](https://image.kindle-tech.com/images/products/577/6fd251bc837e402f09b4fc75c4bdbec967bd790be7109.jpg)
![Double plate heating mold [500℃]](https://image.kindle-tech.com/images/products/577/6b9c8fbd66a78ff3d36b62d24e92c8b867bd78dc57240.jpg)
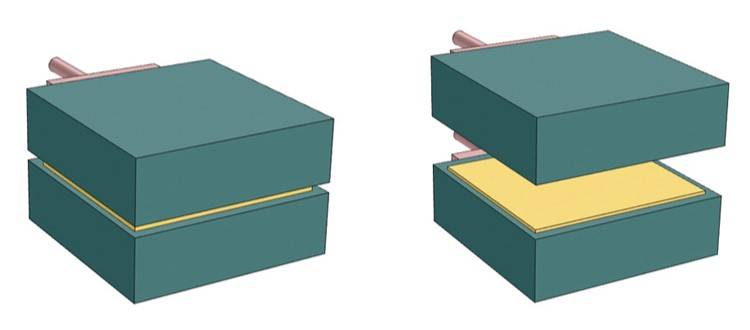
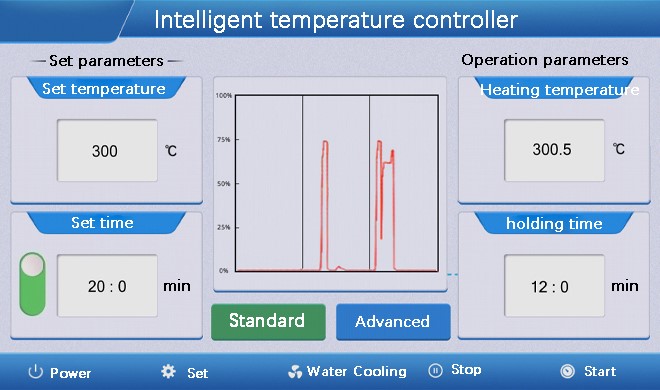
- Standard interface: You can set the heating temperature and constant temperature time of the mold separately in this interface.
- Water cooling button: The power supply of the water cooler is connected to the thermostat, and the thermostat can control the opening and closing of the water cooler.
- Heating button: You can start heating the mold.
- Stop button: You can stop the heating of the mold.
- Timer switch: You can turn the timer function on and off.
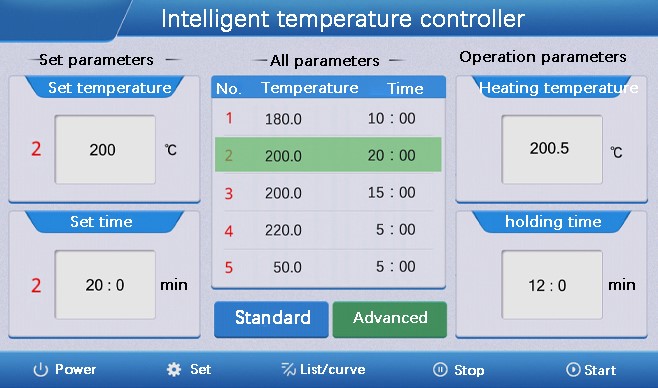
- Start button: You can heat up according to the multi-stage heating program.
- Stop button: During the heating process, you can stop the heating process.
- List curve: You can switch the current display state, list and curve chart.
Technical specifications
Instrument model | PMD |
---|---|
Press the shape of the sample | ![]() |
Heating temperature | Room temperature-300C |
Mold material | Alloy tool steel:Cr12MoV |
Indenter hardness | HRC60-HRC62 |
Sample size | |
Sample thickness | 0.02-0.1mm(N) |
External dimension 1 | 180*180*130mm(L*W*H) |
External dimension 2 | 200*200*130mm(L*XW*H) |
External dimension 3 | 300*300*130mm(L*W*H) |
Mold weight | 32Kg38Kg88Kg |
Dimensional diagram | ![]() |
Operation steps
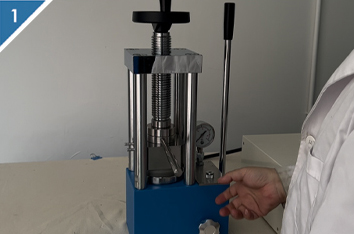
1. Place the sample in the mold.
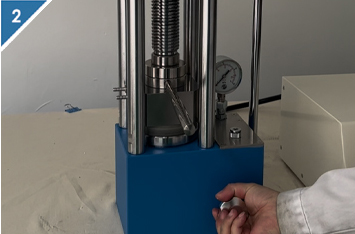
2.Put the mold into the hot press.
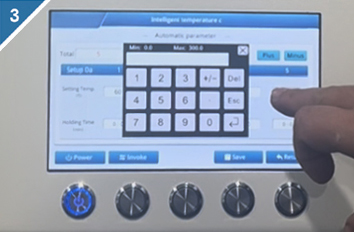
3. Set the required temperature.
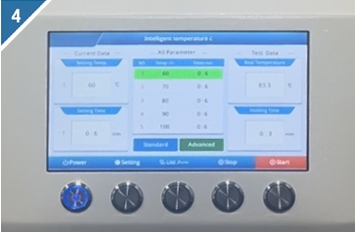
4. Start heating the sample.
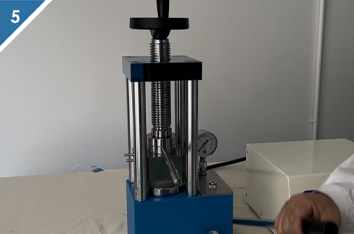
5. Pressurize the sample.
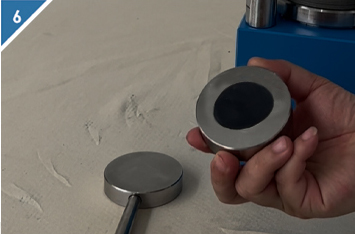
6. Take out the pressed sample.
Principle
Double plate heating molds utilize a combination of inductive and indirect resistance heating methods to achieve uniform temperature distribution. The mold, typically made of graphite or steel, is subjected to a high-frequency electromagnetic field generated by an induction coil. This induces heat within the mold material, which is then further distributed through channels filled with a heating medium like thermo-oil, water, or steam. The precision of this setup ensures steady and controlled heating, essential for maintaining consistent temperatures across the mold surface.
Features
The Double Plate Heating Mold is a versatile and efficient tool designed for precise temperature control and rapid cooling, making it ideal for a variety of industrial applications. This product integrates advanced heating and cooling technologies to ensure optimal performance and durability.
- Dual Zone Temperature Control: The mold features separate upper heating and lower cooling zones. This dual-zone design allows for precise temperature management, ensuring that materials are heated and cooled according to specific process requirements.
- Stable and Reliable Heating: The upper heating plate is equipped with multiple electric heat pipes, providing stable and reliable heating. This ensures uniform heat distribution and prevents hot spots, which is crucial for maintaining the integrity of the materials being processed.
- Quick and Effective Cooling: The lower cooling plate includes a snake-like water cooling pipe, enabling rapid and forceful cooling. This feature is essential for processes that require quick temperature reduction, enhancing overall productivity and efficiency.
- Energy-Efficient Design: The hydraulic system includes automatic pressure compensation and optimized electro-hydraulic drive, reducing energy consumption while improving efficiency. This design not only lowers operational costs but also contributes to environmental sustainability.
- High-Quality Electrical Control: The electrical control system adheres to strict standards (CE or higher), ensuring safety and reliability. Temperature, time, and pressure can be accurately set and displayed, providing precise control over the molding process.
- Customizable Options: On request, the plates can be annealed after welding to eliminate internal tensions, ensuring a smooth working surface and enhancing the longevity of the mold.
These features collectively make the Double Plate Heating Mold an excellent choice for industries requiring precise temperature control and rapid cooling cycles, ensuring high-quality output and operational efficiency.
FAQ
What Is The Main Advantage Of The One-piece Platen Heater Over Conventional Designs?
What Are The Temperature Capabilities Of The One-piece Platen Heater?
How Is The Material Heated Evenly In The One-piece Platen Heater?
How Does The One-piece Platen Heater Simplify Installation?
What Is A Press Mold?
What Is Press Mould In Ceramics?
How Are Pellet Molds Used?
What Types Of Materials Can Be Pelletized Using Pellet Molds?
How Can One Select The Appropriate Pellet Mold For Their Specific Application?
4.8
out of
5
Exceptional heating uniformity, perfect for our lab's precision needs.
4.7
out of
5
Quick cooling feature saves us hours in processing time, brilliant!
4.9
out of
5
High-quality materials ensure durability, worth every penny.
4.8
out of
5
Energy-efficient design has significantly cut our operational costs.
4.7
out of
5
User-friendly controls make operation a breeze, even for new staff.
4.9
out of
5
The dual-zone temperature control is a game-changer for our experiments.
4.8
out of
5
Reliable heating system ensures consistent results, every time.
4.7
out of
5
Customizable options allow us to tailor the mold to our specific needs.
4.9
out of
5
The rapid cooling feature is a standout, enhancing our overall efficiency.
Products
Double Plate Heating Press Mold for Lab
REQUEST A QUOTE
Our professional team will reply to you within one business day. Please feel free to contact us!
Related Products
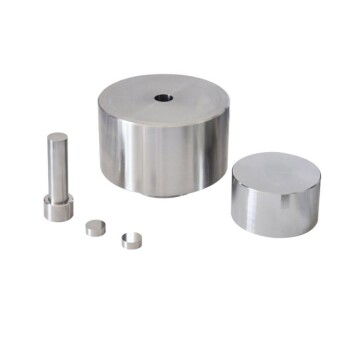
Anti-Cracking Press Mold for Lab Use
The anti-cracking press mold is a specialized equipment designed for molding various shapes and sizes of film using high pressure and electric heating.
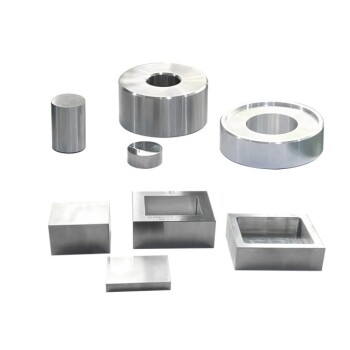
Special Heat Press Mold for Lab Use
Square, round and flat plate forming dies for hot presses.
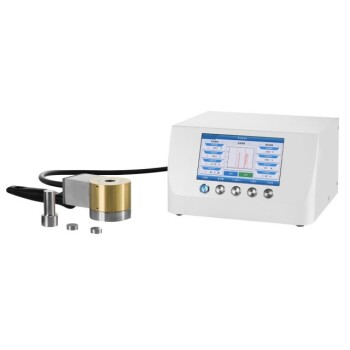
Cylindrical Lab Electric Heating Press Mold for Laboratory Applications
Efficiently prepare samples with Cylindrical Lab Electric Heating Press Mold. Fast heating, high temp & easy operation. Custom sizes available. Perfect for battery, ceramic & biochemical research.
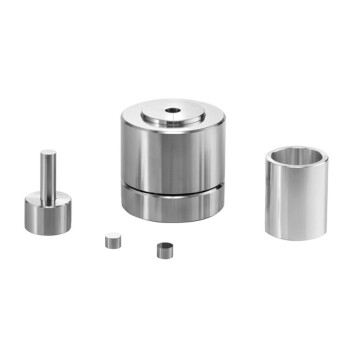
Assemble Lab Cylindrical Press Mold
Get reliable and precise molding with Assemble Lab Cylindrical Press Mold. Perfect for ultra-fine powder or delicate samples, widely used in material research and development.
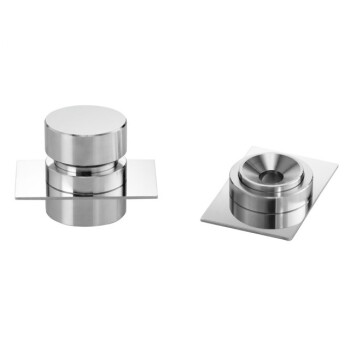
No Demolding Lab Infrared Press Mold for Laboratory Applications
Effortlessly test your samples with no demolding required using our lab infrared press mold. Enjoy high transmittance and customizable sizes for your convenience.
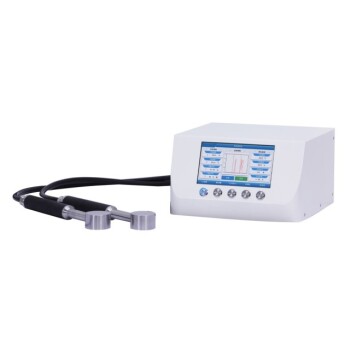
Infrared Heating Quantitative Flat Plate Press Mold
Discover advanced infrared heating solutions with high-density insulation and precise PID control for uniform thermal performance in various applications.
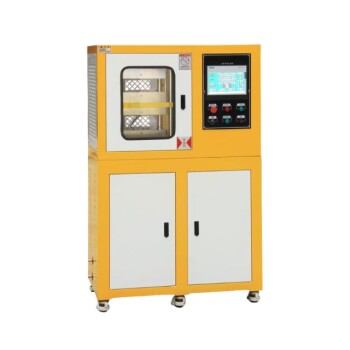
Rubber Vulcanizer Vulcanizing Machine Plate Vulcanizing Press for Lab
The Plate vulcanizing press is a kind of equipment used in the production of rubber products, mainly used for the vulcanization of rubber products. Vulcanization is a key step in rubber processing.
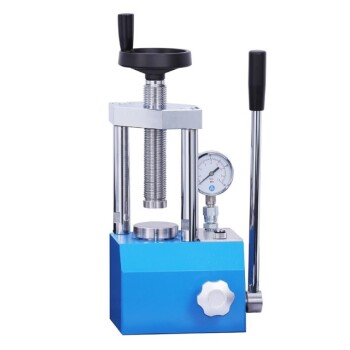
Laboratory Manual Hydraulic Pellet Press for Lab Use
Efficient Manure Lab Hydraulic Press with Safety Cover for sample preparation in material research, pharmacy, and electronic industries. Available in 15T to 60T.
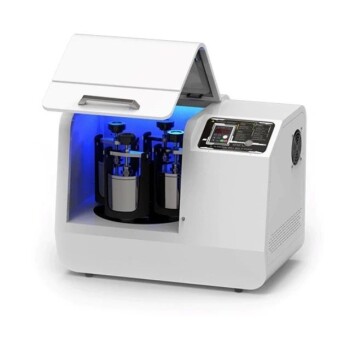
High Energy Planetary Ball Mill Milling Machine for Laboratory
The biggest feature is that the high energy planetary ball mill can not only perform fast and effective grinding, but also has good crushing ability
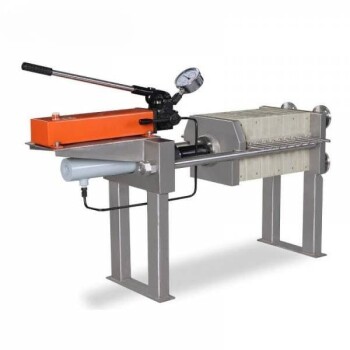
Hydraulic Diaphragm Lab Filter Press for Laboratory Filtration
Hydraulic diaphragm lab press filter is one type lab scale filter press, it takes small footprint, and higher pressing power.
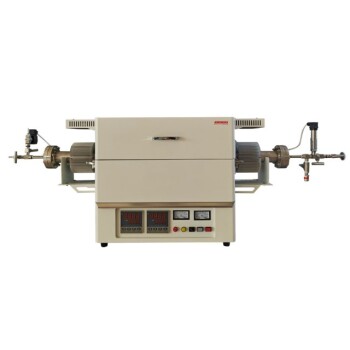
High Pressure Laboratory Vacuum Tube Furnace Quartz Tubular Furnace
KT-PTF High Pressure Tube Furnace: Compact split tube furnace with strong positive pressure resistance. Working temp up to 1100°C and pressure up to 15Mpa. Also works under controller atmosphere or high vacuum.
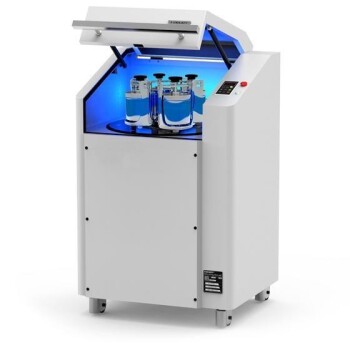
Laboratory Planetary Ball Mill Cabinet Planetary Ball Milling Machine
The vertical cabinet structure combined with ergonomic design enables users to obtain the best comfortable experience in standing operation. The maximum processing capacity is 2000ml, and the speed is 1200 revolutions per minute.
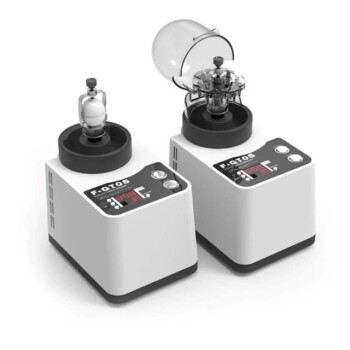
Laboratory Micro Tissue Grinding Mill Grinder
KT-MT10 is a miniature ball mill with a compact structure design. The width and depth are only 15X21 cm, and the total weight is only 8 kg. It can be used with a minimum 0.2ml centrifuge tube or a maximum 15ml ball mill jar.
Related Articles
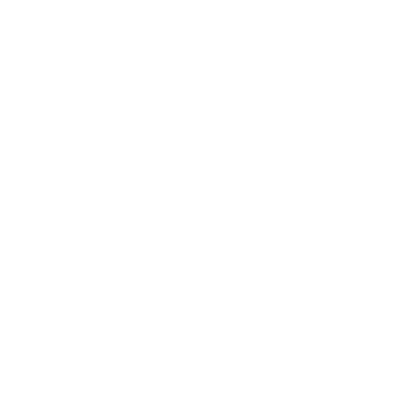
Comprehensive Guide to Cylindrical Lab Electric Heating Press Mold: Technology and Applications
Explore the advanced features and applications of cylindrical lab electric heating press molds. Learn about their working principles, types of heating technologies, and key benefits for precise sample preparation.
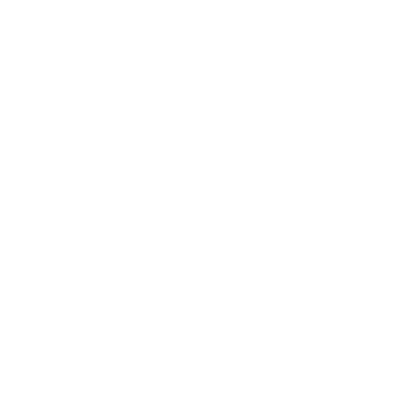
Infrared Press Mold Techniques for Non-Demolding Applications
Explore advanced infrared press mold techniques without demolding. Learn about the benefits, applications, and best practices for non-demolding lab processes.
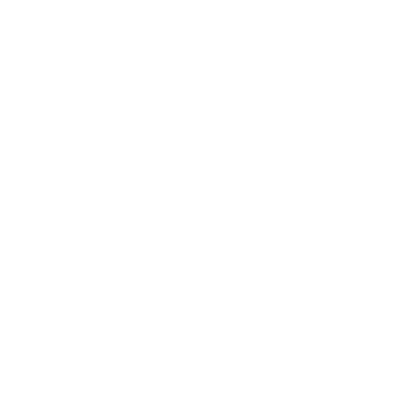
Exploring the Multifunctional Electrolytic Cell Water Bath: Applications and Benefits
Discover the versatile applications of multifunctional electrolytic cell water baths in various industries. Learn about their benefits, components, and how they facilitate chemical reactions and temperature control.
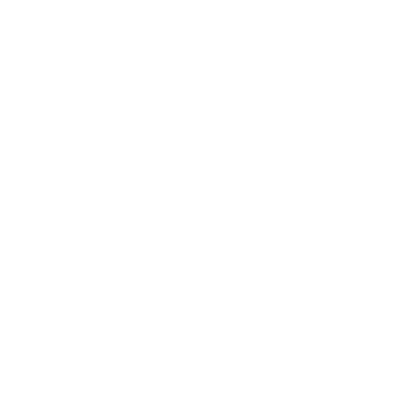
Comprehensive Overview of Commonly Used Heat Treatment Equipment
This article discusses various heat treatment equipment, their classifications, structures, and applications.
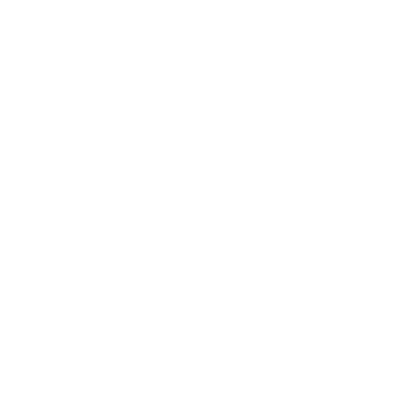
13 Tips on Induction Technology and Sustainable Heat Treatment
Expert tips on maintaining induction coils, improving vacuum furnace efficiency, and sustainable heat treatment methods.
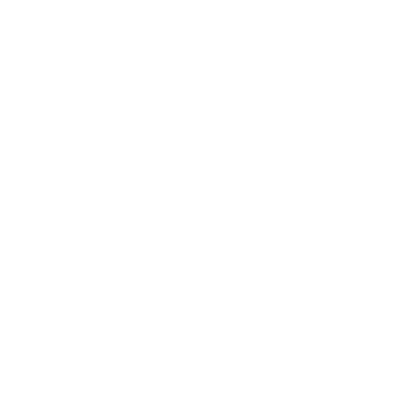
Choosing the Right Heating Method for Laboratory Experiments
Discusses different heating methods in labs and their suitability for various experiments.
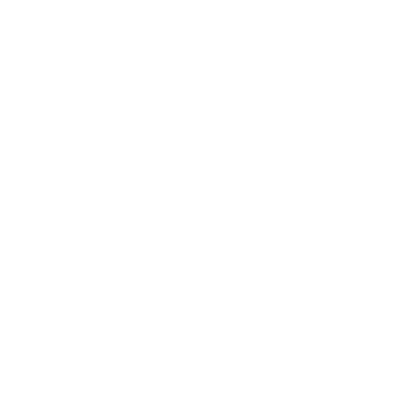
Choosing the Right Heating Method in Laboratory Experiments
Understanding the differences between metal bath, water bath, and thermostat heating methods for various lab experiments.
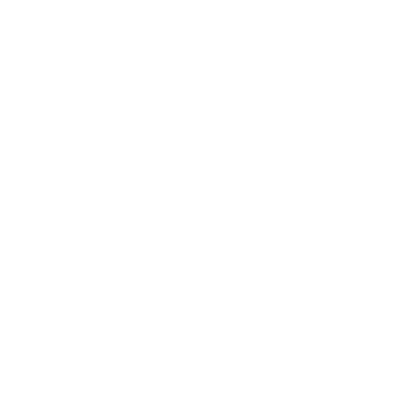
Basic Constant Temperature Heating Equipment in Laboratories
Overview of various constant temperature heating devices used in laboratories.
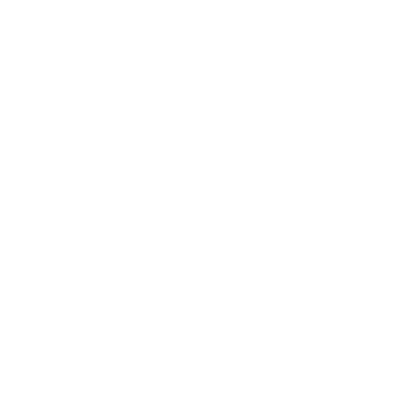
Common Laboratory Melting Methods
An overview of three primary laboratory melting techniques: Arc Melting, Induction Melting, and Suspension Melting.
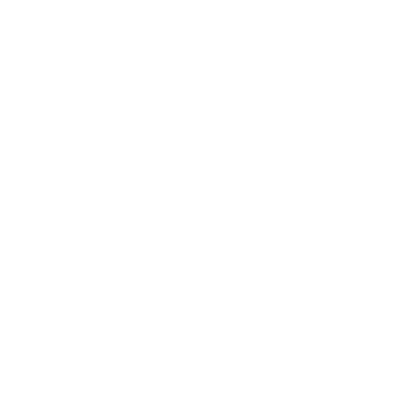
Chip Manufacturing: Comprehensive Guide to the Annealing Process
Detailed exploration of the annealing process in semiconductor fabrication, its types, key parameters, and applications.
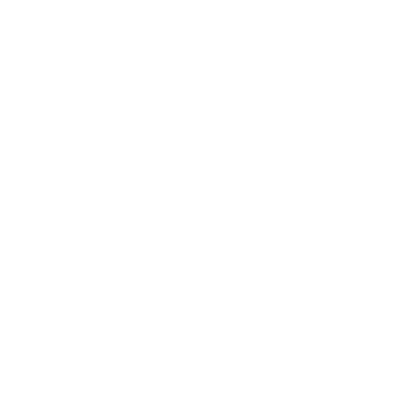
Temperature Control Requirements for Laboratory Small High-Temperature Resistance Furnaces
Exploring the precision, stability, and safety aspects of temperature control in laboratory small high-temperature resistance furnaces.
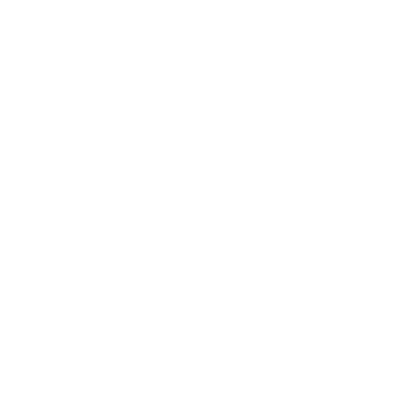
Selection of Muffle Furnace: Key Considerations
Guidelines for selecting a muffle furnace based on experimental needs, heating methods, temperature control, safety, and more.