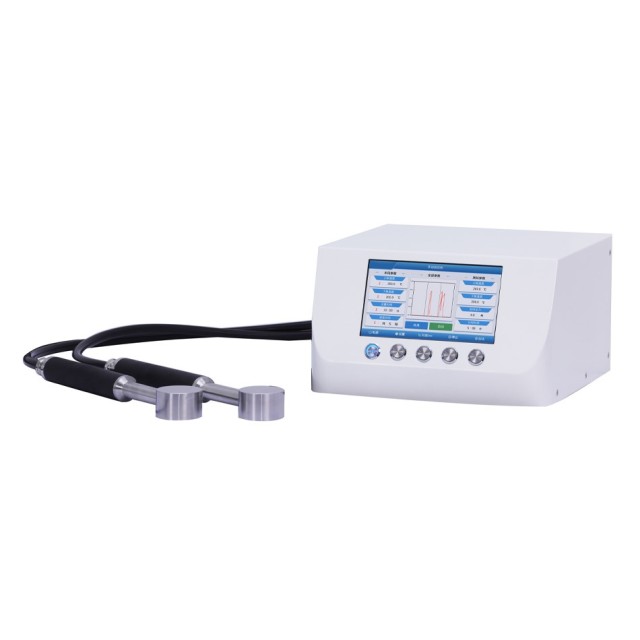
Molds & Accessories
Infrared Heating Quantitative Flat Plate Press Mold
Item Number : PMHD
Price varies based on specs and customizations
- Die heating
- 0.0℃-300.0℃
- Die material
- Alloy tool steel :Cr12MoV
- Sample size
- Φ25mm (d)/Φ50mm (d)
- Dimensions
- 200*60mm (D*H)
- Weight
- 220V/300W
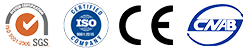
Shipping:
Contact us to get shipping details Enjoy On-time Dispatch Guarantee.
Why Choose Us
Reliable PartnerEasy ordering process, quality products, and dedicated support for your business success.
Introduction
Infrared heating quantitative flat plate mold technology utilizes advanced materials and precise temperature control to achieve uniform heat distribution. The insulation layers, including high-temperature ceramic fiber boards and zirconia fiber blankets, ensure effective thermal management. The integrated PID controller with SCR power control and auto-tune functions enhances precision and safety. This design, featuring a one-piece platen heater with a swaged tubular element, optimizes heat conduction and simplifies assembly. The use of ceramic and quartz materials in infrared heaters provides stability at high temperatures, making them suitable for various industrial applications.
Applications
Infrared heating quantitative flat plate molds are versatile tools with a wide range of applications, particularly in industries that require precise and efficient heating processes. These applications are often characterized by their need for rapid energy transfer and the ability to control heating zones effectively.
Detail & Parts
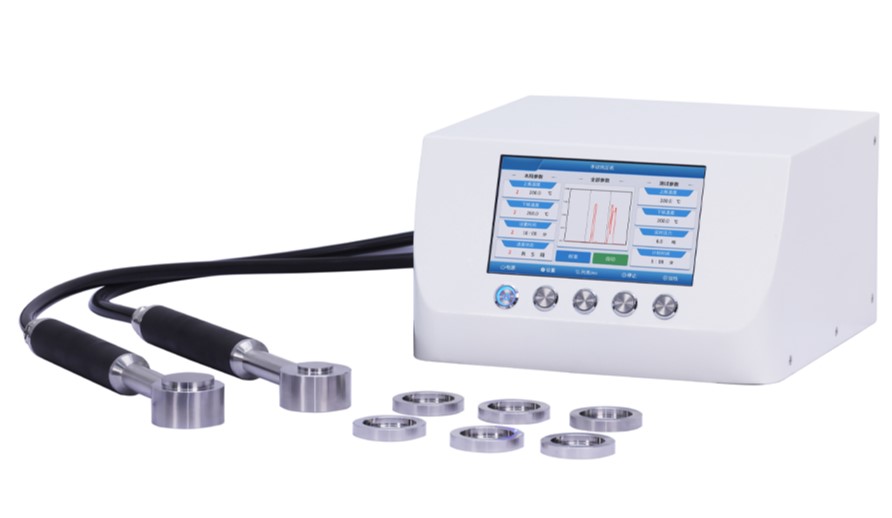
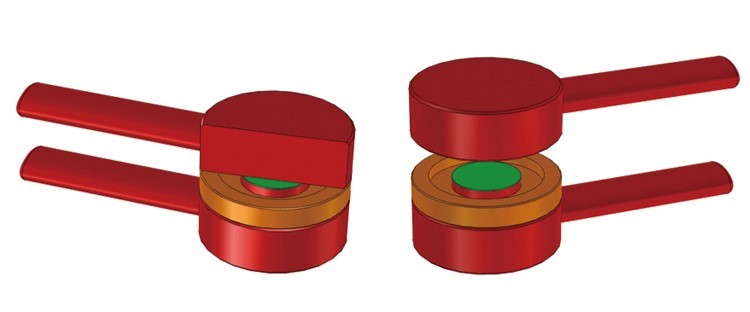
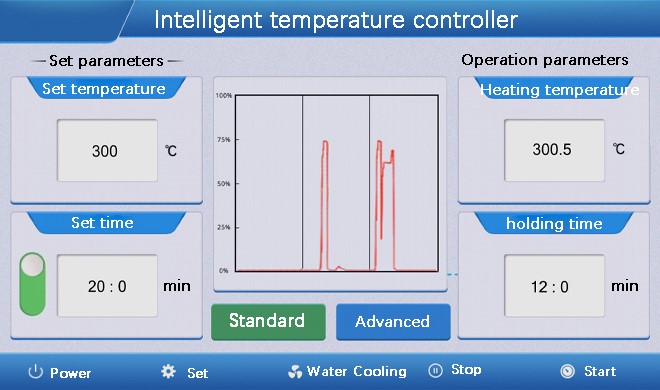
- Standard interface: You can set the mold heating temperature and constant temperature time separately in this interface.
- Water cooling button: The water cooling machine power supply is connected to the thermostat, and the thermostat can control the opening and closing of the water cooling machine.
- Heating button: You can start heating the mold.
- Stop button: You can stop the heating of the mold.
- Timing switch: You can turn the timing function on and off.
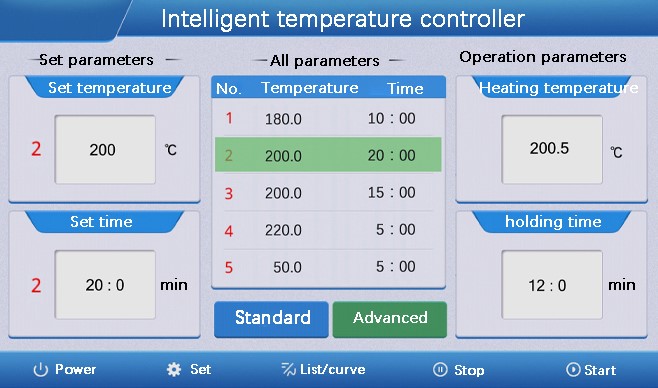
- Start button: You can heat up according to the multi-stage heating program.
- Stop button: During the heating process, you can stop the heating process.
- List curve: You can switch the current display state, list and curve chart.
Technical specifications
Instrument model | PMHD-A | PMHD-B |
---|---|---|
Sample shape | ![]() |
|
Die heating | 0.0℃-300.0℃ | 0.0℃-300.0℃ |
Die material | Alloy tool steel :Cr12MoV | Alloy tool steel :Cr12MoV |
Sample size | Φ50mm (d) | Φ25mm (d) |
Sample thickr | 15-100μm | 25、50、100、250、500μm(6 measuring loops) |
Dimensions | 200*60mm (D*H) | 200*60mm(D*H) |
Weight | 220V/300W | 220V/300W |
Diagram of hydraulic powder press size | ![]() |
![]() |
Operation steps
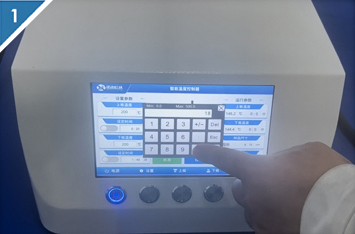
1. Set the temperature for heating the upper and lower molds.
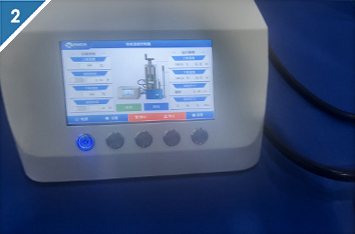
2. Click the upper and lower plates to start heating.
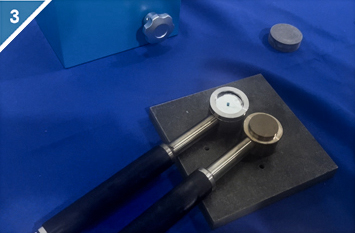
3. Put the sample into the mold first.
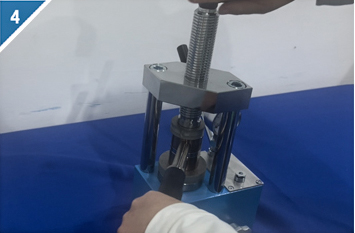
4. Put the mold into the tablet press for pre-compression.
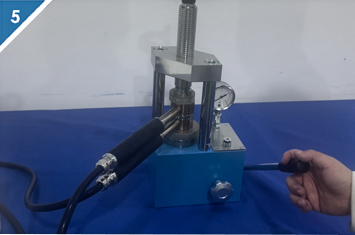
5. When the temperature reaches the set temperature, start pressurizing the mold.
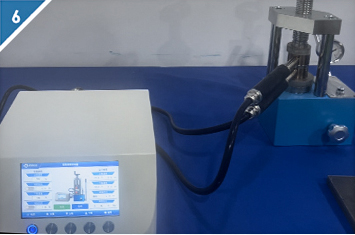
6. Turn off the heating function and let the sample cool.
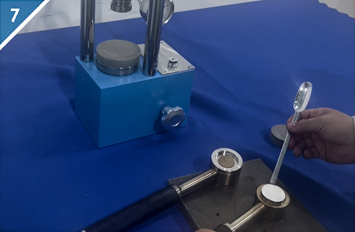
7. Remove the heated mold.
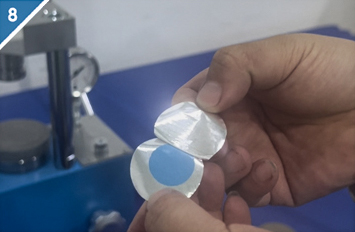
8. Take out the pressed sample.
FAQ
What Is The Principle Of Tablet Press Molds?
What Is A Press Mold?
What Are The Main Types Of Tablet Press Molds?
What Is Press Mould In Ceramics?
What Are The Advantages Of Using Tablet Press Molds?
How Are Pellet Molds Used?
What Are The Applications Of Tablet Press Molds?
What Types Of Materials Can Be Pelletized Using Pellet Molds?
How Can One Select The Appropriate Pellet Mold For Their Specific Application?
4.7
out of
5
Exceptional precision and durability, a game-changer for our lab!
4.8
out of
5
Incredible value for money, highly efficient and reliable.
4.9
out of
5
Technologically advanced, simplifies complex processes effortlessly.
4.7
out of
5
Fast delivery, top-notch quality, couldn't be happier!
4.8
out of
5
Durable and user-friendly, perfect for our research needs.
4.9
out of
5
Revolutionary tech, saves time and boosts productivity.
4.7
out of
5
Outstanding performance, highly recommend for any lab.
4.8
out of
5
Efficient, cost-effective, and easy to operate.
4.9
out of
5
Best investment for our lab, precise and durable.
4.7
out of
5
Speedy delivery, excellent quality, highly satisfied.
Products
Infrared Heating Quantitative Flat Plate Press Mold
REQUEST A QUOTE
Our professional team will reply to you within one business day. Please feel free to contact us!
Related Products
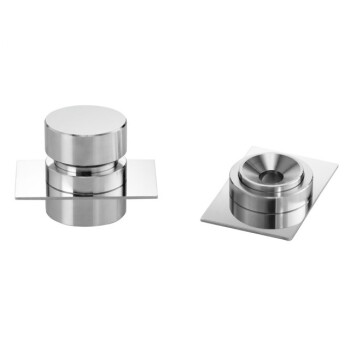
No Demolding Lab Infrared Press Mold for Laboratory Applications
Effortlessly test your samples with no demolding required using our lab infrared press mold. Enjoy high transmittance and customizable sizes for your convenience.
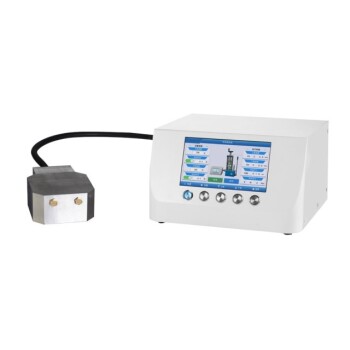
Double Plate Heating Press Mold for Lab
Discover precision in heating with our Double Plate Heating Mold, featuring high-quality steel and uniform temperature control for efficient lab processes. Ideal for various thermal applications.
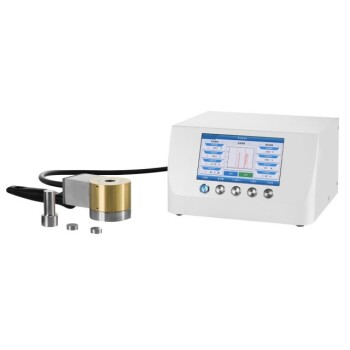
Cylindrical Lab Electric Heating Press Mold for Laboratory Applications
Efficiently prepare samples with Cylindrical Lab Electric Heating Press Mold. Fast heating, high temp & easy operation. Custom sizes available. Perfect for battery, ceramic & biochemical research.
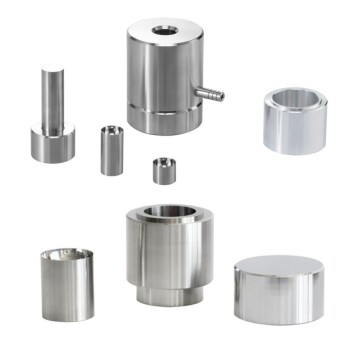
Explore versatile Hydraulic Hot Press molds for precise compression molding. Ideal for creating various shapes and sizes with uniform stability.
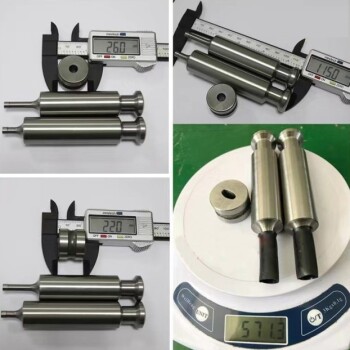
Multi-Punch Rotary Tablet Press Mold Ring for Rotating Oval and Square Molds
The multi-punch rotary tablet press mold stands as a pivotal component in pharmaceutical and manufacturing industries, revolutionizing the process of tablet production. This intricate mold system comprises multiple punches and dies arranged in a circular fashion, facilitating rapid and efficient tablet formation.
Related Articles
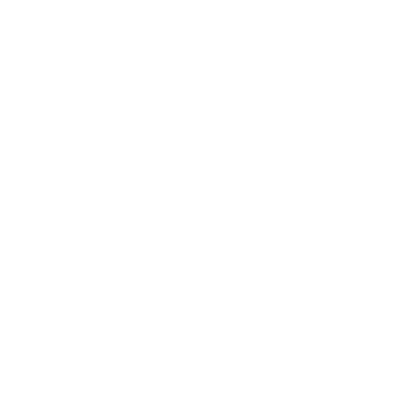
Infrared Press Mold Techniques for Non-Demolding Applications
Explore advanced infrared press mold techniques without demolding. Learn about the benefits, applications, and best practices for non-demolding lab processes.
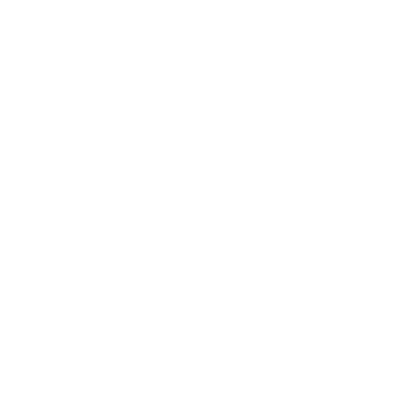
Comprehensive Guide to Cylindrical Lab Electric Heating Press Mold: Technology and Applications
Explore the advanced features and applications of cylindrical lab electric heating press molds. Learn about their working principles, types of heating technologies, and key benefits for precise sample preparation.
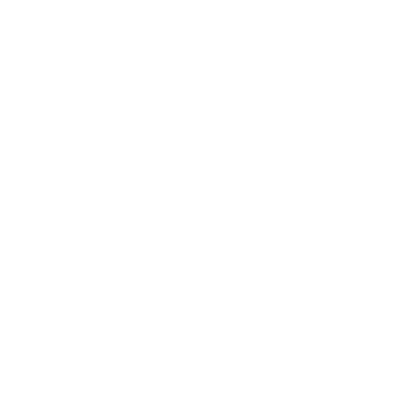
Comprehensive Overview of Commonly Used Heat Treatment Equipment
This article discusses various heat treatment equipment, their classifications, structures, and applications.
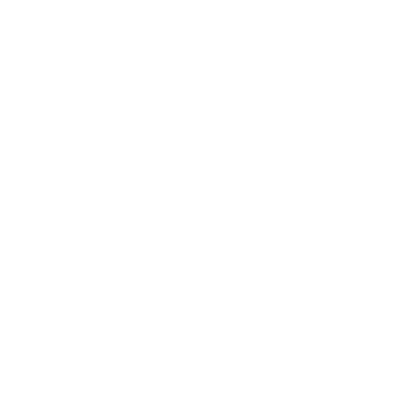
13 Tips on Induction Technology and Sustainable Heat Treatment
Expert tips on maintaining induction coils, improving vacuum furnace efficiency, and sustainable heat treatment methods.
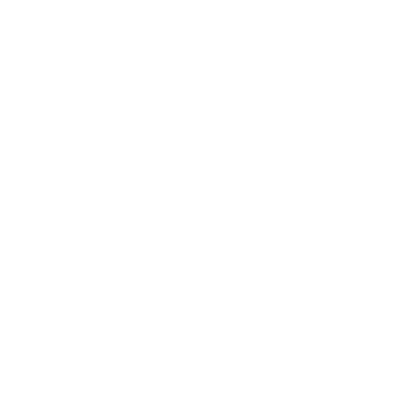
Infrared Spectroscopy Sample Preparation Operation Guide
A comprehensive guide on preparing samples for infrared spectroscopy analysis, covering gas, liquid, and solid samples.
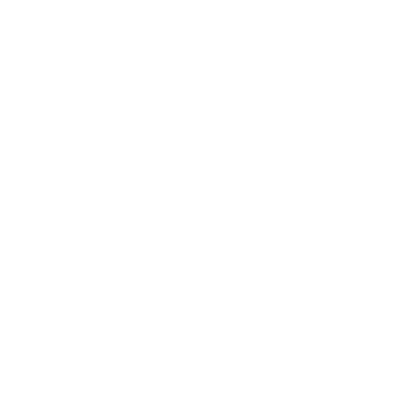
Choosing the Right Heating Method in Laboratory Experiments
Understanding the differences between metal bath, water bath, and thermostat heating methods for various lab experiments.
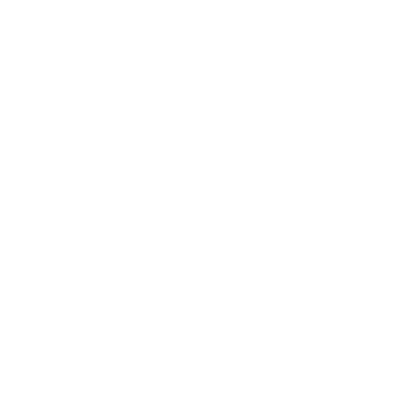
Choosing the Right Heating Method for Laboratory Experiments
Discusses different heating methods in labs and their suitability for various experiments.
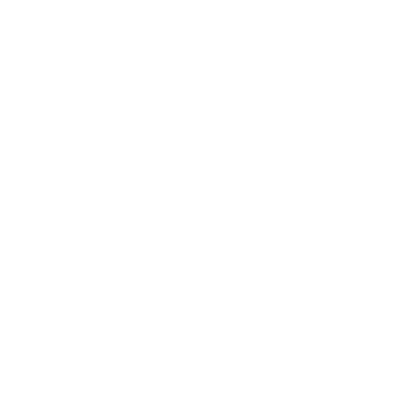
IR (Tablet Pressing Method) Operation
Detailed guide on the IR tablet pressing method, including instruments, reagents, sample preparation, and testing procedures.
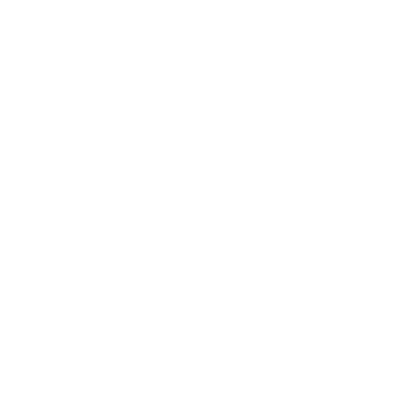
Common Laboratory Melting Methods
An overview of three primary laboratory melting techniques: Arc Melting, Induction Melting, and Suspension Melting.
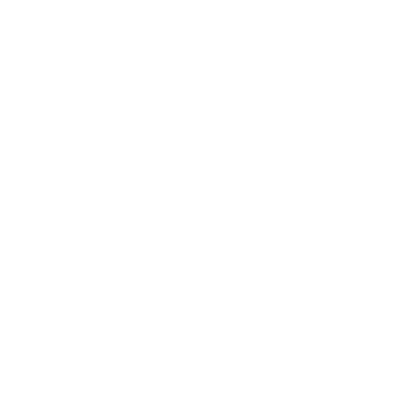
Infrared Spectroscopy Sample Preparation and Handling
Detailed guide on preparing and handling solid, liquid, and gas samples for infrared spectroscopy.
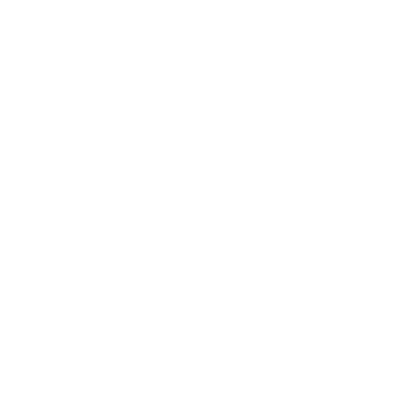
Chip Manufacturing: Comprehensive Guide to the Annealing Process
Detailed exploration of the annealing process in semiconductor fabrication, its types, key parameters, and applications.
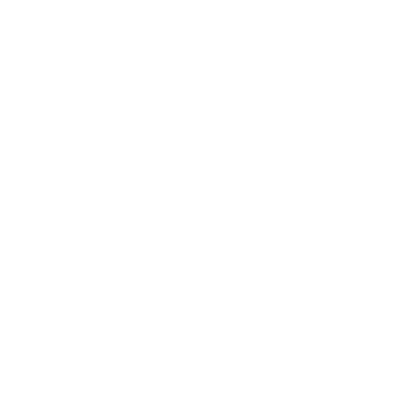
Preparation Techniques for Solid Samples in Infrared Spectroscopy
A detailed guide on various methods for preparing solid samples for infrared spectroscopy, including plate pressing, paste, and thin film methods.