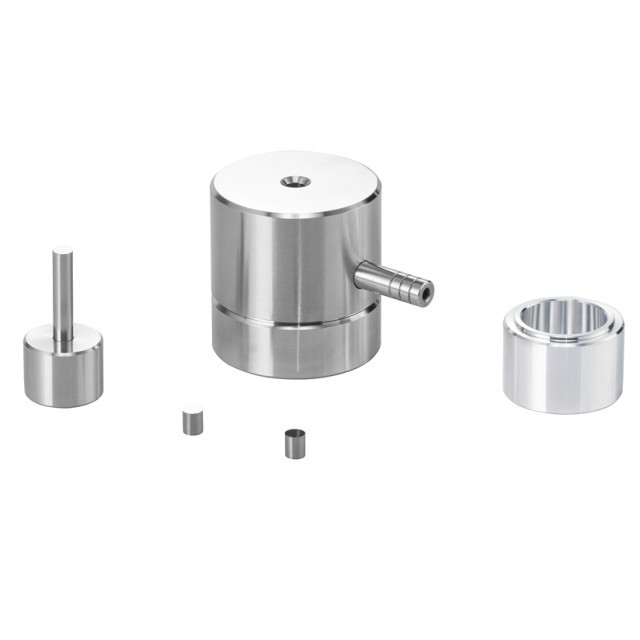
Molds & Accessories
Cylindrical Press Mold for Lab Applications
Item Number : PMC
Price varies based on specs and customizations
- Cavity depth
- 20-65 mm
- Indenter hardness
- HRC68-HRC70 / HRC60-HRC62
- Material
- ASSAB+17 / Cr12MoV
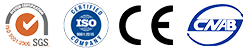
Shipping:
Contact us to get shipping details Enjoy On-time Dispatch Guarantee.
Why Choose Us
Reliable PartnerEasy ordering process, quality products, and dedicated support for your business success.
Applications
Cylindrical press molds can be used for forming and testing most samples, we have a complete range of mold sizes, The accessories are interchangeable.
The mold is widely used in battery, superconductor, cement, ceramics, catalysis, silicate, powder metallurgy, sea mud analysis, biochemical analysis and new material sample preparation research and development. In addition, the product can also be used with calcium iron, infrared, X-ray fluorescence and other testing instruments.
The mold is made of Japanese high-speed steel, high hardness, no deformation, long service life.
Special sizes press molds can be customized according to customer requirements.
Detail & Parts
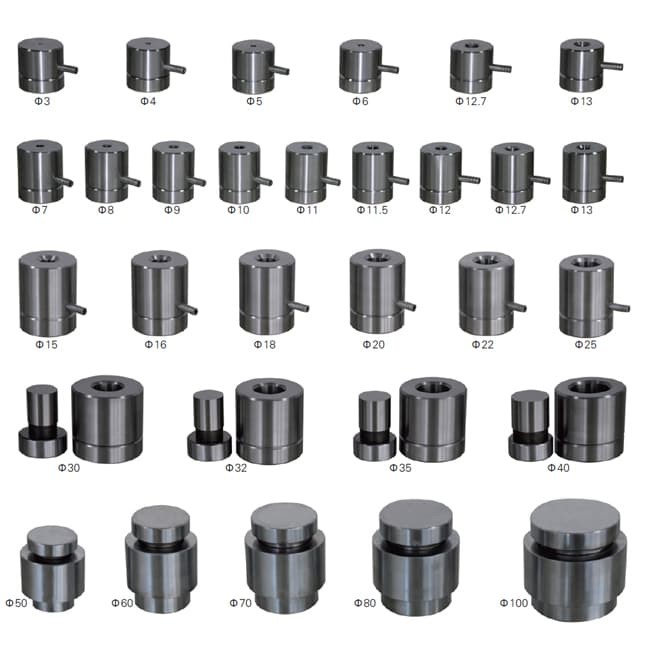
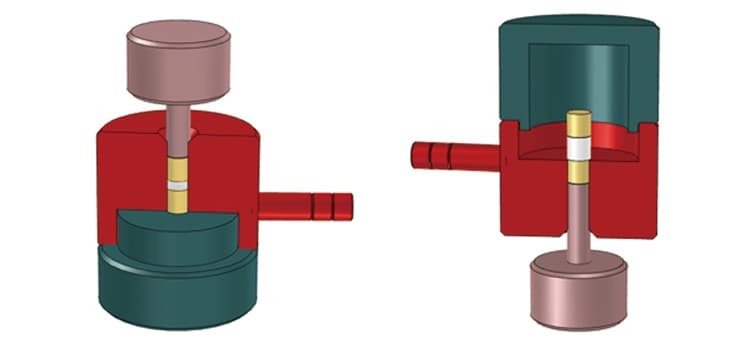
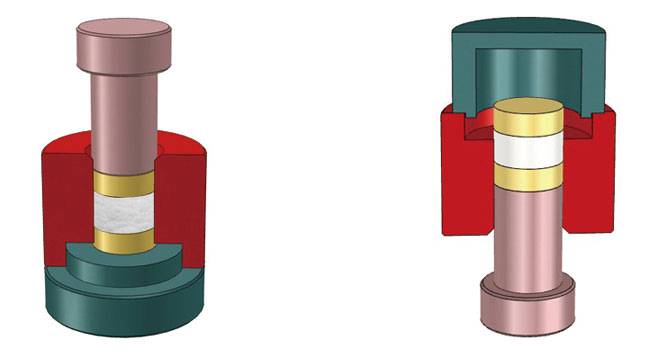
1)Sample Preparation Process 2)Release Process
Technical specifications
Instrument model | PMC-A | PMC-B | PMC-C | PMC-D | PMC-E | PMC-F | PMC-G |
---|---|---|---|---|---|---|---|
Die material | High-speed tool steel ASSAB +17 | Alloy tool steel :Cr12MoV | |||||
Indenter hardness | HRC68-HRC70 | HRC60-HRC62 | |||||
Sample size | Φ3、Φ4、Φ5、Φ6 mm ((M) | Φ7、8、9、10、11、11.5、12、12.7、13 mm(M) | Φ15、Φ16、Φ18、Φ20、Φ22、Φ25mm (M) | Φ28、Φ30、Φ32、Φ35、Φ40mm (M) | Φ50、Φ60、Φ70mm (M) | Φ80、Φ90、Φ100mm (M) | Φ120、Φ150(M) |
Cavity depth | 20mm (N) | 30mm (N) | 40mm (N) | 45mm (N) | 55、60、65mm(N) | 65mm(N) | 65mm(N) |
Dimensions | Φ43 * 78mm (L*H) | Φ43*93mm(L*H) | Φ53*120mm(L*H) | Φ73*133mm(L*H) | Φ88*150mm、Φ98*180mm、Φ108*180mm(L*H) | Φ118*150mm、Φ128*180mm、Φ138*180mm(L*H) | Φ168*180mm、Φ218*180mm(L*H) |
Weight | 0.55Kg | 0.67Kg | 1.34Kg | 2.9Kg | 5.1Kg、7.3Kg、9Kg | 11.5Kg、14Kg、20Kg | 30Kg、40Kg |
Other sizes can be customized |
Operation steps
The cylindrical die can be used for molding and testing of most samples. The structure is simple and the cost is low.
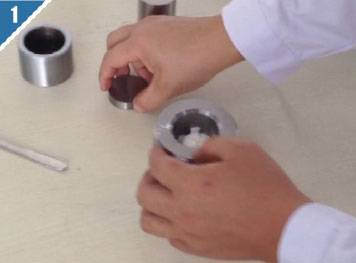
Step 1: Assemble the die according to the operation diagram and install the sample in the cavity.
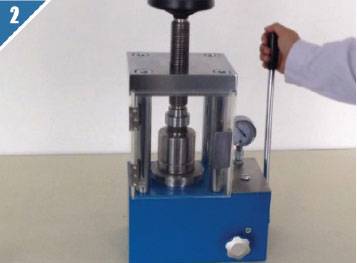
Step 2: Put the die in the center of the hydraulic press and pressurize to required pressure.
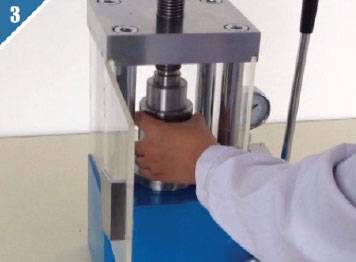
Step 3: Assemble the die according to the release diagram , eject the sample out of the die bushing with the screw rod.
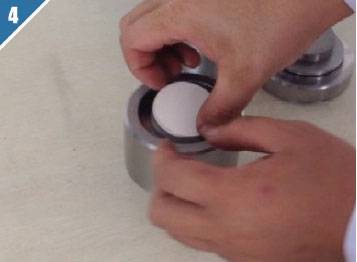
Step 4: Take out the die from the hydraulic press ,and remove the sample gently.
Precautions for mold maintenance
To ensure accurate test results, clean the mold surface with dust-free paper before each use to avoid the anti-rust oil from affecting the sample. Avoid exceeding the maximum pressure when applying pressure. Clean the mold and samples after use to prevent corrosion. Apply anti-rust oil and store the mold in a dry environment if not used for a long time to prevent damage.
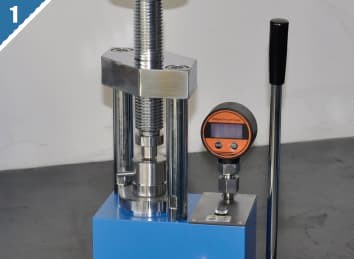
Step 1: Placing the Mold.
To begin, place the mold in the center of the tablet press. It is important to note that the maximum pressure of the mold cannot be exceeded when pressurized. This will prevent any damage to the mold and ensure accurate test results.
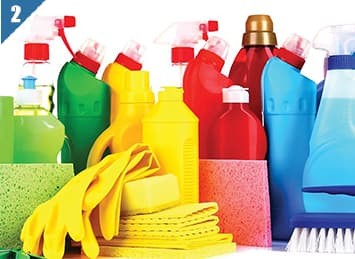
Step 2: Cleaning the Mold.
After each use, it is essential to clean the mold to prevent any contamination of the sample. Using dust-free paper, wipe the surface of the mold clean. If there are sample residues on the surface that cannot be removed, please do not use chemical reagents to clean and soak. This could potentially damage the mold and impact the accuracy of the test results.
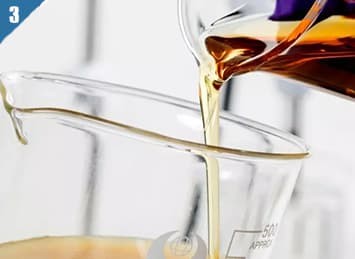
Step 3: Applying Anti-Rust Oil.
If the mold is not used for an extended period, it is recommended to apply anti-rust oil on the surface of the mold to prevent rusting. This step will help prolong the life of the mold and ensure that it remains in good condition for future use.
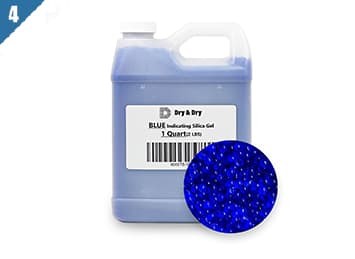
Step 4: Storing the Mold.
Lastly, if the mold is not used for a long time, it needs to be stored in a dry environment. This will prevent any moisture from accumulating on the mold and causing damage.
Full range of lab press types
Click to view our full range of lab press products.
Any question? Our experts have helped many laboratories choose their lab press, contact us now!
Full range of types of laboratory press molds
We have a full range of molds for you to choose from, and the molds fit the body perfectly.
If you need molds with special shapes, we can also customize them for you.
Warnings
Operator safety is the top important issue! Please operate the equipment with cautions. Working with inflammable& explosive or toxic gases is very dangerous, operators must take all necessary precautions before starting the equipment. Working with positive pressure inside the reactors or chambers is dangerous, operator must fellow the safety procedures strictly. Extra caution must also be taken when operating with air-reactive materials, especially under vacuum. A leak can draw air into the apparatus and cause a violent reaction to occur.
Designed for You
KinTek provide deep custom made service and equipment to worldwide customers, our specialized teamwork and rich experienced engineers are capable to undertake the custom tailoring hardware and software equipment requirements, and help our customer to build up the exclusive and personalized equipment and solution!
Would you please drop your ideas to us, our engineers are ready for you now!
4.8
out of
5
I'm thrilled with the durability and precision of this mold. It's a game-changer for my research!
4.9
out of
5
The mold's versatility is remarkable! It accommodates various sample sizes and thicknesses, making it a must-have for my lab.
4.7
out of
5
The mold's high-speed steel construction ensures longevity and resistance to deformation. It's a worthwhile investment!
4.8
out of
5
I highly recommend this mold for its ease of use and consistent sample quality. It simplifies sample preparation!
4.9
out of
5
The mold's adaptability is exceptional. It seamlessly integrates with my existing equipment, making it a seamless addition to my lab.
4.7
out of
5
The mold's customizable sizes cater to my specific research needs. I appreciate the flexibility it offers!
4.8
out of
5
The mold's precision and accuracy in sample preparation are remarkable. It's a valuable asset to my laboratory.
4.9
out of
5
The mold's swift delivery exceeded my expectations. I received it promptly, allowing me to continue my research without delay.
4.7
out of
5
The mold's value for money is unbeatable. It's an affordable solution that doesn't compromise on quality.
4.8
out of
5
The mold's technological advancements are impressive. It streamlines my research process and enhances the accuracy of my results.
4.9
out of
5
The mold's durability is exceptional. It withstands repeated use without compromising its integrity.
4.7
out of
5
The mold's versatility allows me to explore a wide range of sample types and sizes. It's a versatile tool that meets my diverse research needs.
4.8
out of
5
The mold's adaptability to various testing instruments enhances its functionality and makes it a valuable addition to my laboratory.
4.9
out of
5
The mold's customizable sizes cater to my specific research requirements. It's a flexible solution that accommodates my evolving needs.
4.7
out of
5
The mold's high-quality construction ensures reliable and consistent sample preparation. It's a dependable tool that I can count on.
4.8
out of
5
The mold's user-friendly design simplifies the sample preparation process. It's easy to assemble and operate, saving me time and effort.
4.9
out of
5
The mold's compatibility with various sample types makes it a versatile addition to my lab. It's a valuable tool for a wide range of research applications.
4.7
out of
5
The mold's durability is exceptional. It withstands the rigors of daily use without compromising its performance.
4.8
out of
5
The mold's technological advancements enhance the efficiency of my research. It's a cutting-edge tool that sets new standards in sample preparation.
Products
Cylindrical Press Mold for Lab Applications
REQUEST A QUOTE
Our professional team will reply to you within one business day. Please feel free to contact us!
Related Products
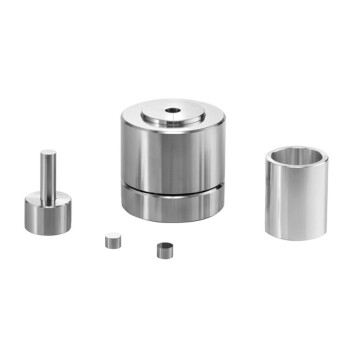
Assemble Lab Cylindrical Press Mold
Get reliable and precise molding with Assemble Lab Cylindrical Press Mold. Perfect for ultra-fine powder or delicate samples, widely used in material research and development.
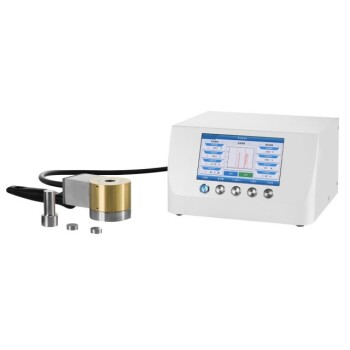
Cylindrical Lab Electric Heating Press Mold for Laboratory Applications
Efficiently prepare samples with Cylindrical Lab Electric Heating Press Mold. Fast heating, high temp & easy operation. Custom sizes available. Perfect for battery, ceramic & biochemical research.

Special Shape Press Mold for Lab
Discover high-pressure special shape press molds for diverse applications, from ceramics to automotive parts. Ideal for precise, efficient molding of various shapes and sizes.
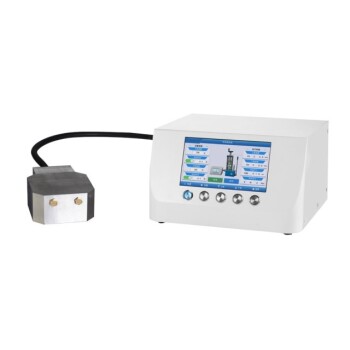
Double Plate Heating Press Mold for Lab
Discover precision in heating with our Double Plate Heating Mold, featuring high-quality steel and uniform temperature control for efficient lab processes. Ideal for various thermal applications.
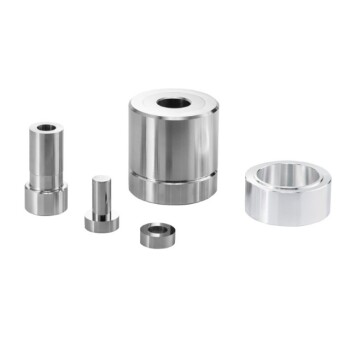
Ring Press Mold for Lab Applications
Ring Press Dies, also known as Circular Pellet Press Die Sets, are integral components in various industrial and laboratory processes.
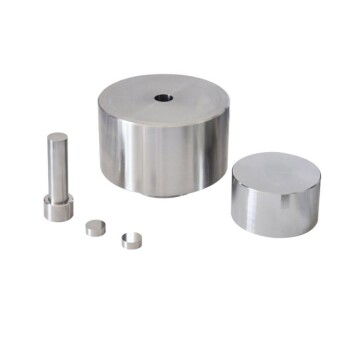
Anti-Cracking Press Mold for Lab Use
The anti-cracking press mold is a specialized equipment designed for molding various shapes and sizes of film using high pressure and electric heating.
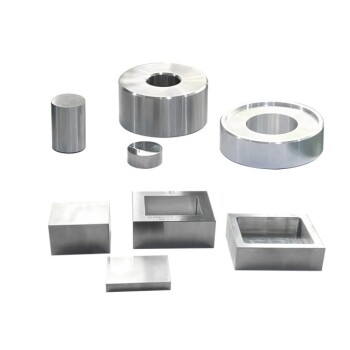
Special Heat Press Mold for Lab Use
Square, round and flat plate forming dies for hot presses.
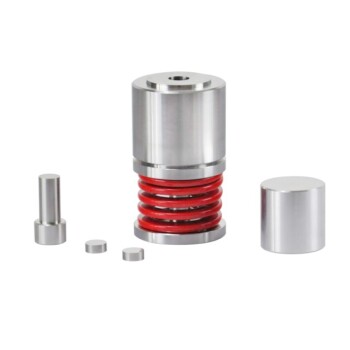
Round Bidirectional Press Mold for Lab
The round bidirectional press mold is a specialized tool used in high-pressure molding processes, particularly for creating intricate shapes from metal powders.
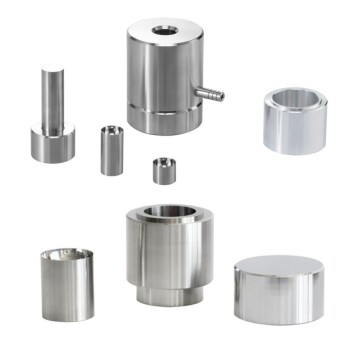
Explore versatile Hydraulic Hot Press molds for precise compression molding. Ideal for creating various shapes and sizes with uniform stability.
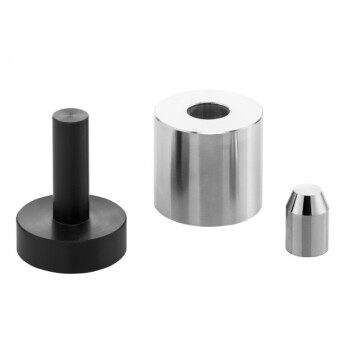
Button Battery Tablet Press Sealing Mold for Lab Use
The sealing die is essential for assembling button batteries, ensuring components like the anode, cathode, and electrolyte are securely enclosed.
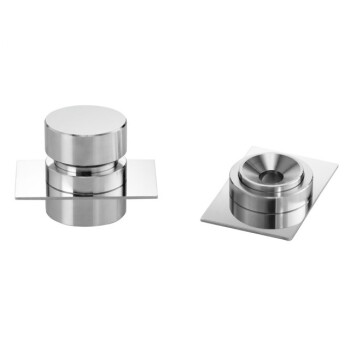
No Demolding Lab Infrared Press Mold for Laboratory Applications
Effortlessly test your samples with no demolding required using our lab infrared press mold. Enjoy high transmittance and customizable sizes for your convenience.
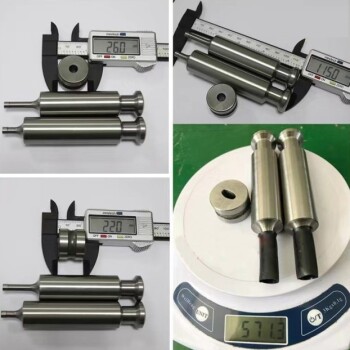
Multi-Punch Rotary Tablet Press Mold Ring for Rotating Oval and Square Molds
The multi-punch rotary tablet press mold stands as a pivotal component in pharmaceutical and manufacturing industries, revolutionizing the process of tablet production. This intricate mold system comprises multiple punches and dies arranged in a circular fashion, facilitating rapid and efficient tablet formation.
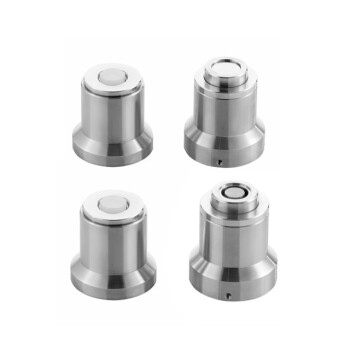
Button Battery Disassembly and Sealing Mold for Lab Use
The simple sealing and disassembly mold can be directly used on ordinary tablet presses, which can save costs, is convenient and fast, and can be used to encapsulate and disassemble button batteries. Other specifications can be customized.
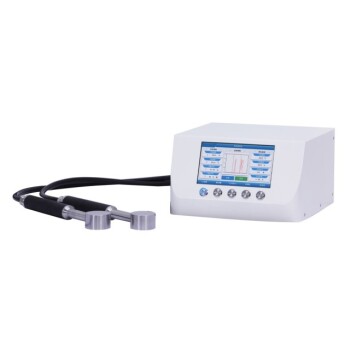
Infrared Heating Quantitative Flat Plate Press Mold
Discover advanced infrared heating solutions with high-density insulation and precise PID control for uniform thermal performance in various applications.
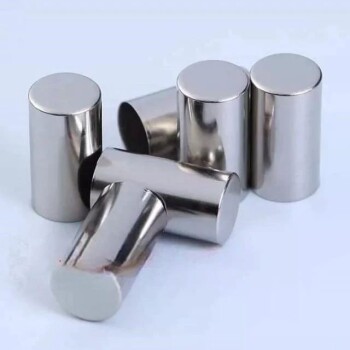
Cylindrical Battery Steel Case for Battery Lab
Lithium-ion battery casing suppresses battery polarization, reduces thermal effects, and improves rate performance.
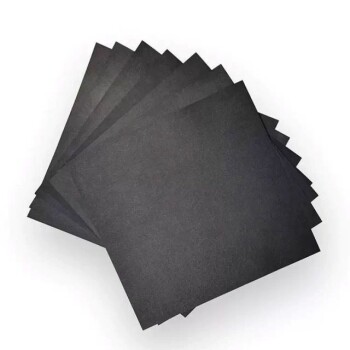
Hydrophilic Carbon Paper TGPH060 for Battery Lab Applications
Toray carbon paper is a porous C/C composite material product (composite material of carbon fiber and carbon) that has undergone high-temperature heat treatment.
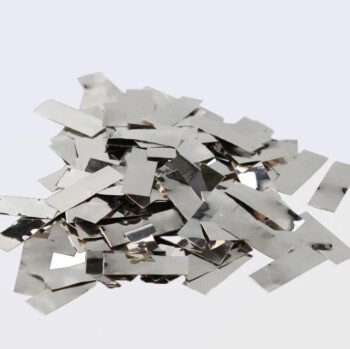
Platinum Sheet Electrode for Battery Lab Applications
Platinum sheet is composed of platinum, which is also one of the refractory metals. It is soft and can be forged, rolled and drawn into rod, wire, plate, tube and wire.
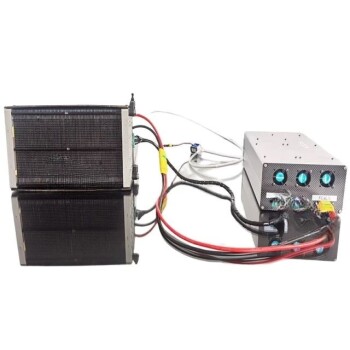
Hydrogen Fuel Cell Stack Battery Lab Equipment
A fuel cell stack is a modular, highly efficient way to generate electricity using hydrogen and oxygen through an electrochemical process. It can be used in various stationary and mobile applications as a clean and renewable energy source.
Related Articles
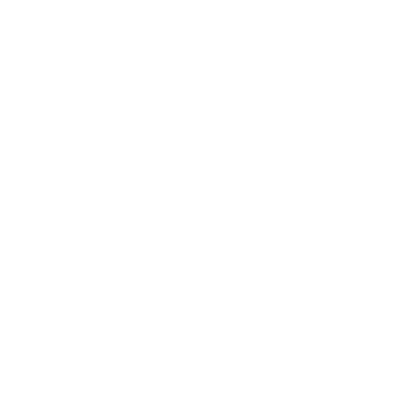
Ceramic Isostatic Pressing Mold Technology
Exploring the design and factors affecting ceramic isostatic pressing molds.
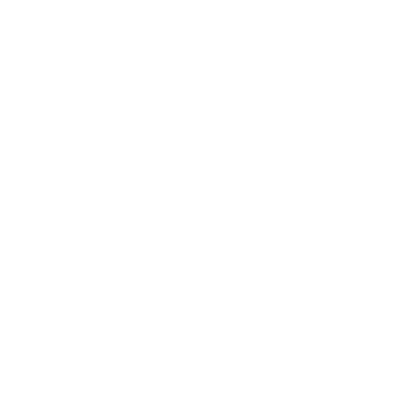
Comprehensive Guide to Cylindrical Lab Electric Heating Press Mold: Technology and Applications
Explore the advanced features and applications of cylindrical lab electric heating press molds. Learn about their working principles, types of heating technologies, and key benefits for precise sample preparation.
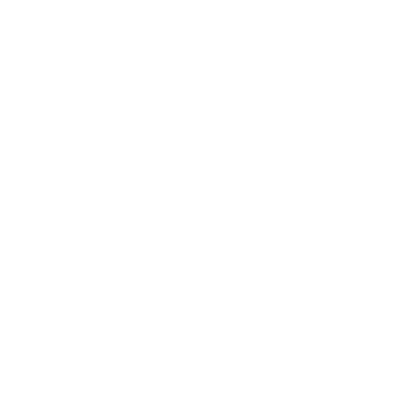
Pressing Powder Samples and Molding Polymer Films: A Comprehensive Guide
Pressing powder samples is done to create a solid material that remains intact even after the load is removed. This process involves pushing the powder grains closer together, closing the gaps between them and forcing them to flow and rearrange themselves into a more compact arrangement. As the available volume reduces, the flow of particles stops, and they undergo plastic and elastic deformations that result in bonding between the grains.
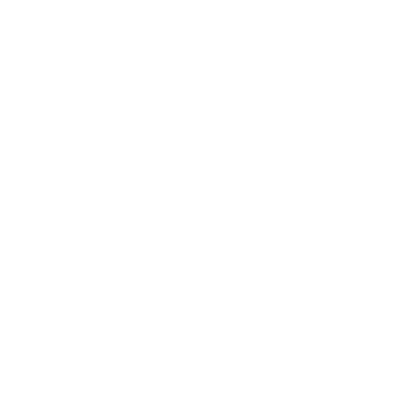
Classification of tablet press molds and precautions for use
During the stamping process.A stamping die is a tablet press die that compresses a sample or tablet during the stamping process. The stamping die is placed on top of the tablet press and the sample is placed on top of the die. The die is then compression molded to the desired shape and size. here are some classification of tablet press molds and precautions for use.
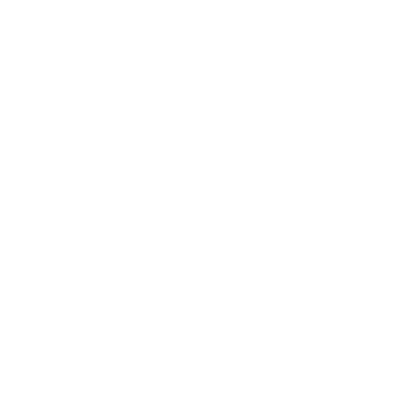
Understanding Isostatic Pressing in Powder Metallurgy
Isostatic pressing is a crucial technique used in powder metallurgy to achieve high-density components with improved mechanical properties. It involves subjecting a powder compact to equal pressure from all directions, resulting in uniform compaction and minimal defects. Isostatic pressing offers several advantages over traditional uniaxial pressing, such as improved density and microstructure control.
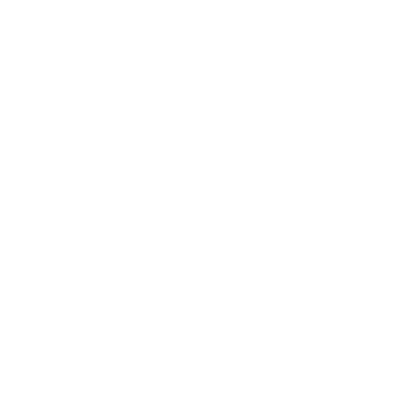
Understanding Isostatic Pressing in Powder Metallurgy
Isostatic pressing is a powder processing technique that uses fluid pressure to compact the part. It involves placing metal powders in a flexible container, which acts as the mold for the part. Fluid pressure is then exerted over the entire outside surface of the container, causing it to press and form the powder into the desired geometry.
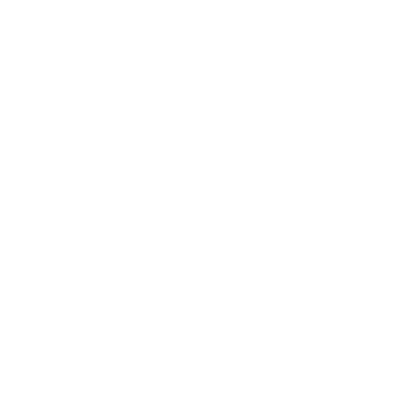
The Role of Isostatic Presses in Powder Metallurgy
Isostatic pressing is a technique used in powder metallurgy to produce high-density components with uniform density and excellent mechanical properties. In this process, a powder material is placed into a flexible mold and subjected to high-pressure isostatic compression from all sides.
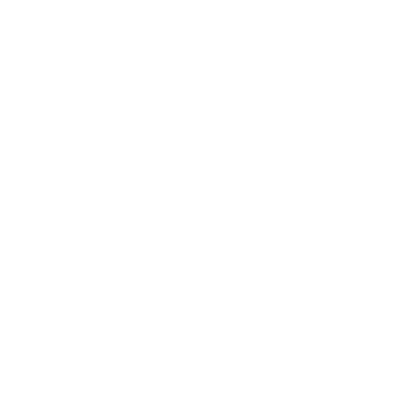
Isostatic Pressing for Producing Parts with Internal Shapes
Isostatic pressing is a manufacturing process that is widely used in the production of complex-shaped parts. It involves applying equal pressure from all directions to a material placed inside a flexible mold.
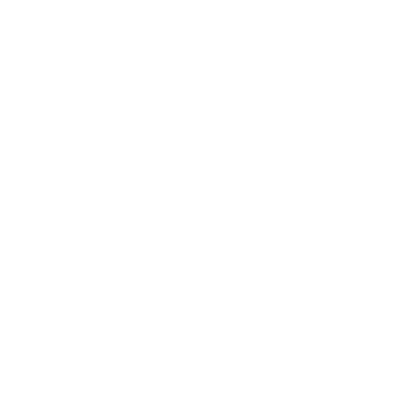
Cold Isostatic Pressing (CIP): A Proven Process for High-Performance Parts Manufacturing
Cold isostatic pressing (CIP) is a proven process that stands out when it comes to high-performance part manufacturing. The technology offers a range of advantages, from achieving superior densities in ceramics to compressing materials as diverse as metals and graphite.
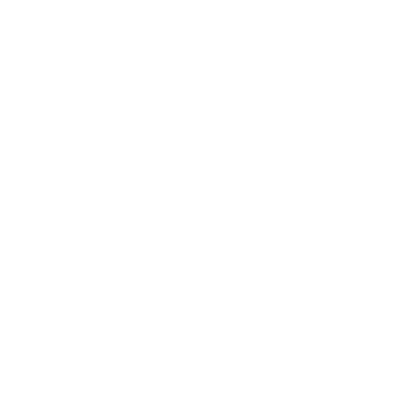
CIP vs. Metal Mold Pressing What's the Difference
CIP and Metal Mold Pressing are used to create high-density components, but they differ in terms of the level of complexity required and the final outcome. Understanding these differences can help manufacturers determine which method is best suited for their needs.
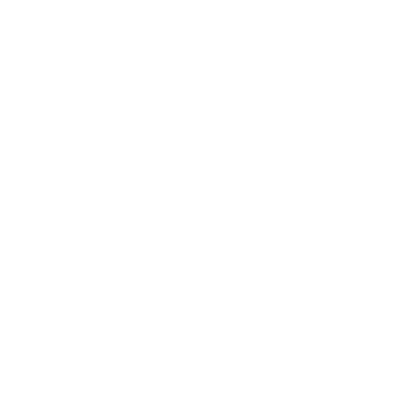
Comprehensive Guide to Isostatic Pressing Molds: Types, Processes, and Applications
Explore the detailed world of isostatic pressing molds, including types like wet bag and dry bag, their processes, and applications. Learn how these molds ensure uniform density and high-strength products.
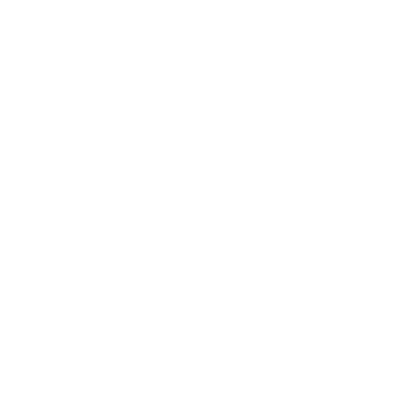
How Isostatically Pressed Products are Made
Isostatic pressing is a manufacturing process used in the production of high-density, high-strength materials and components. Isostatic pressing involves applying pressure uniformly in all directions to a powdered material, which is contained within a flexible or rigid mold.