Introduction
Table of Contents
When it comes to high-performance parts manufacturing, one proven process that stands out is Cold Isostatic Pressing (CIP). This technology offers a range of benefits, from achieving exceptional density for ceramics to compressing various materials like metal and graphite. In this blog post, we will delve into the basics of CIP, explore its applications in different industries, and discuss how it has expanded into new areas, such as telecommunications and automotive sectors. So, if you're curious about this innovative manufacturing process, keep reading to learn more about the power of Cold Isostatic Pressing.
The Basics of Cold Isostatic Pressing (CIP)
Understanding the CIP technology
Cold Isostatic Pressing (CIP) is a method of processing materials through the application of pressure. It is similar to metal mold processing and is based on Pascal's law, which states that pressure applied in an enclosed fluid is transmitted uniformly in all directions without any change in magnitude.
In CIP, powders are compacted by enclosing them in an elastomer mold, which has low resistance to deformation. Liquid pressure is then applied uniformly to the mold, compressing the powders and resulting in a highly compact solid. This process can be used for various materials, including plastics, graphite, powdered metallurgy, ceramics, and sputtering targets.
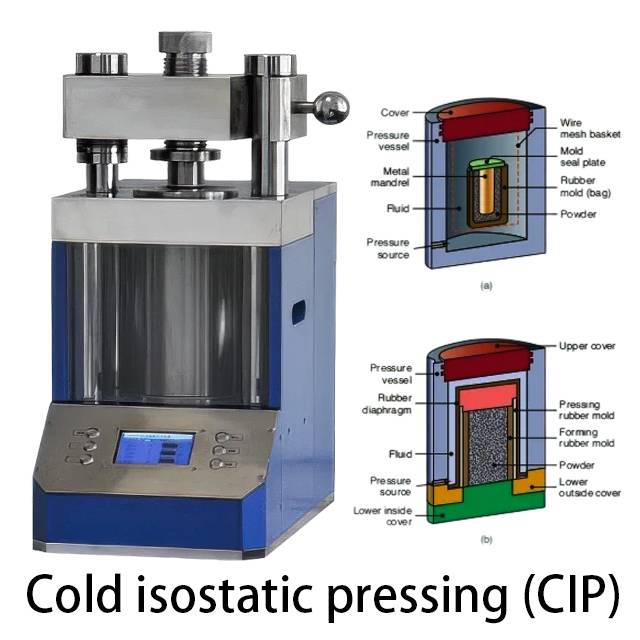
The process of consolidating metal and ceramic powders
Cold Isostatic Pressing (CIP) is a powder-compacting process that achieves 60 to 80% theoretically dense parts ready for sintering. It offers the advantage of good green strength, allowing for premachining before sintering without causing breakage.
CIP is particularly useful for producing parts where the high initial cost of pressing dies cannot be justified or when very large or complex compacts are needed. It can be applied to a variety of powders, including metals, ceramics, plastics, and composites. Pressures required for compacting range from less than 5,000 psi to more than 100,000 psi. Powders are compacted in elastomeric molds using either a wet or dry bag process.
Achievement of 95% theoretical density for ceramics
CIP can achieve 95% of theoretical density for ceramics. With typical pressures ranging from 15,000 to 60,000 psi and ambient temperatures up to 200°F, CIP is able to consolidate ceramic powders to a high density. This makes it a proven process for producing high-performance ceramic parts.
Typical pressures and ambient temperature involved in CIP
Typical pressures for Cold Isostatic Pressing (CIP) range from 15,000 to 60,000 psi, with ambient temperatures up to 200°F. These pressures and temperatures are applied uniformly to the elastomer mold containing the powders, resulting in the consolidation of the materials into a solid homogeneous mass.
CIP is widely used in various industries, including medical, aerospace, automotive, and telecommunications. It is particularly useful for the consolidation of ceramic powders, compressing graphite, refractories, and electrical insulators, as well as for producing sputtering targets and coatings for valve parts.
In conclusion, Cold Isostatic Pressing (CIP) is a versatile powder-compacting process that achieves high-density parts ready for further treatment or sintering. It offers advantages such as solid-state processing, shape complexity, low tooling cost, and minimal material waste. CIP is a proven technology used in various industries for the production of high-performance components.
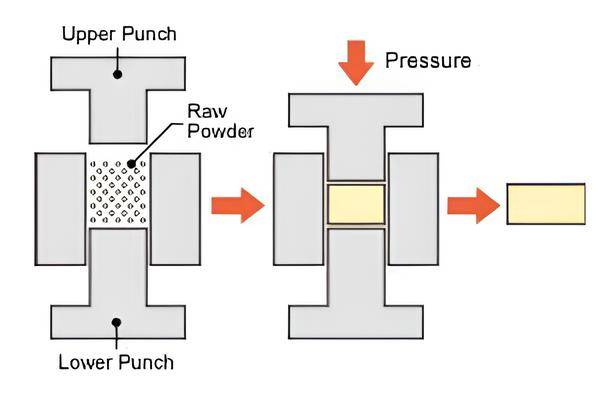
Applications of Cold Isostatic Pressing
Consolidation of ceramic powders
Cold isostatic pressing (CIP) is commonly used for the consolidation of ceramic powders. This process involves compacting a powder in an elastomeric container submerged in a fluid at a pressure of 20 to 400 MPa. CIP allows for the production of simple-shaped small or large powder compacts with a uniform green density. It is particularly useful for powders that are difficult to press, such as hard metals. The range of ceramic products produced by the isostatic process is extensive and includes balls, tubes, rods, nozzles, fuse tubes, teeming tubes, lighting tubes, grinding wheels, and more.
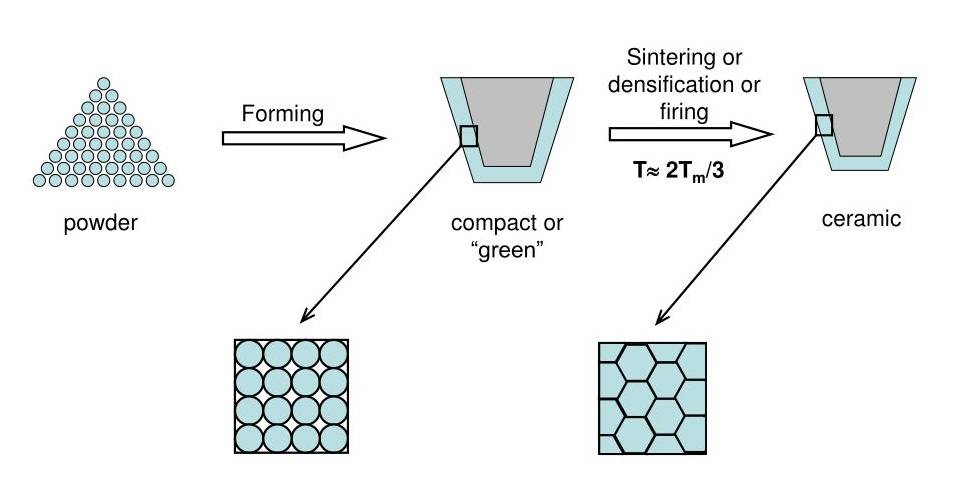
Compressing of graphite, refractories, and electrical insulators
Cold isostatic pressing is also widely used for compressing graphite, refractory materials, and electrical insulators. Materials such as silicon nitride, silicon carbide, boron nitride, boron carbide, titanium boride, and spinel can be effectively compacted using CIP. This technology allows for the production of high-quality parts with a uniform green density, even for complex shapes. However, it is important to note that cold isostatic pressing may sacrifice pressing speed and dimensional control, often requiring subsequent machining of the green compact.
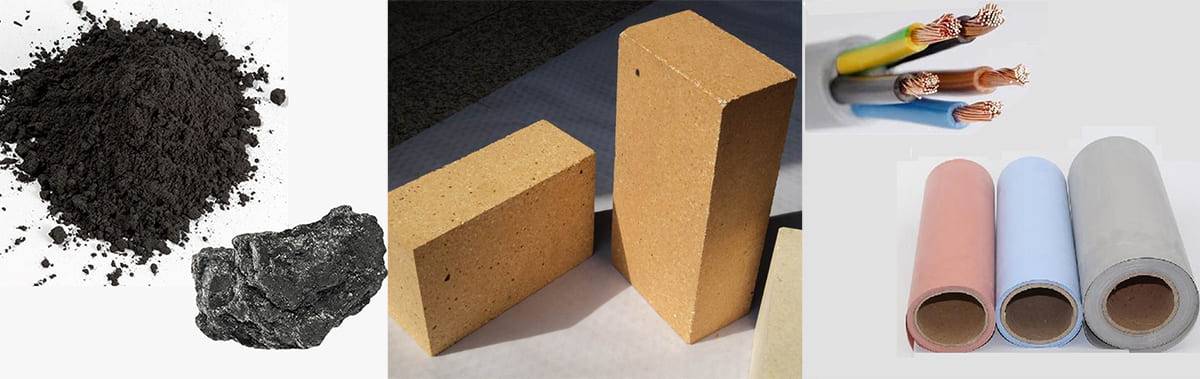
Applications in dental and medical fields
Cold isostatic pressing has found applications in the dental and medical fields as well. It is commonly used for compressing advanced ceramics used in dental implants, prosthetics, and medical devices. The high-pressure process ensures the production of dense and durable ceramic components that meet the stringent requirements of the healthcare industry. The technology is expanding into new applications, including the compression of sputtering targets, the coating of valve components to reduce cylinder wear in engines, and various applications in telecommunications, electronics, aerospace, and automotive industries.
Cold isostatic pressing, also known as CIP, is performed at room temperature using an elastomer mold and a fluid, typically oil or water. The fluid pressure during the operation can range from 60,000 lbs/in2 (400 MPa) to 150,000 lbs/in2 (1000 MPa). One disadvantage of this manufacturing process is the lower geometric accuracy due to the flexible mold. However, CIP remains a proven process for producing high-performance parts. After cold isostatic pressing, the green compact is usually conventionally sintered to achieve the desired final part.
Expansion into New Applications
Pressing of sputtering targets
Sputtering targets are widely used in various industries for their ability to deposit thin films of materials onto a variety of substrates with high precision and uniformity. One of the new applications for sputtering targets is the pressing of these targets. This process involves using high pressure to compact the powdered materials into a solid target shape. Pressing ensures that the target has the desired density and mechanical properties for efficient sputtering.
The pressing of sputtering targets has gained popularity due to the increasing demand for thin film coatings in industries such as telecommunications, electronics, aerospace, and automotive. These coatings serve various purposes, including improving the function and durability of high-performance engine components in the automotive industry and creating visually appealing and durable finishes on items like watches and jewelry.
Coating of valve parts in engines
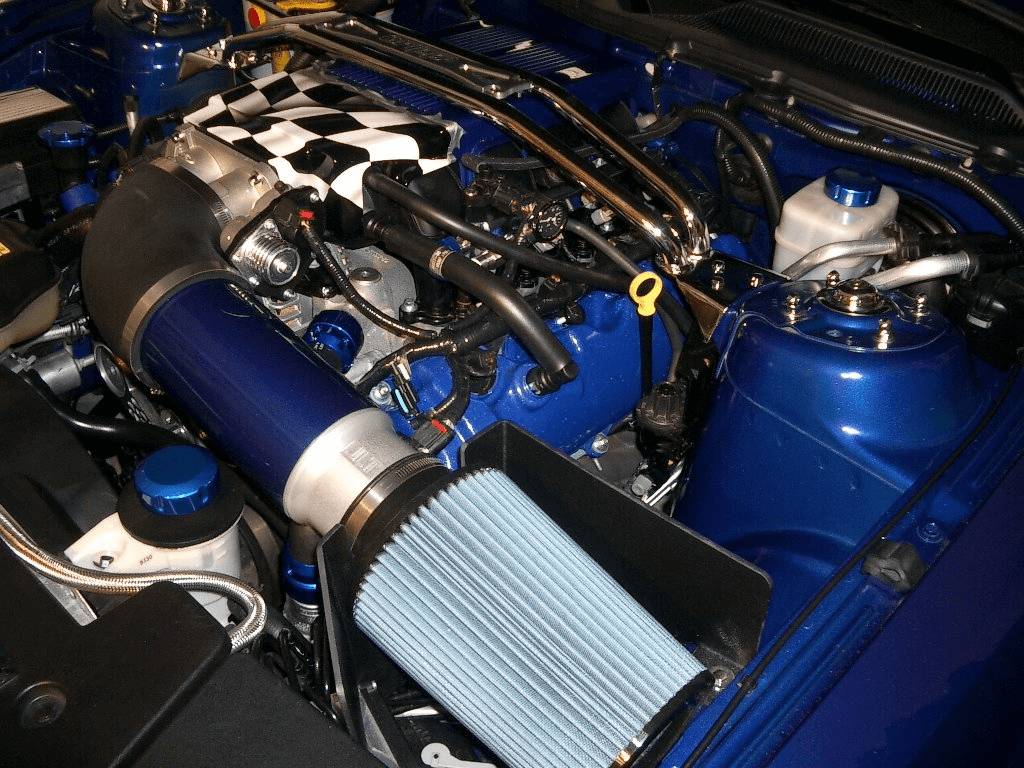
Another emerging application for sputtering targets is the coating of valve parts in engines. Engine valves play a crucial role in the performance and efficiency of an engine. Coating these valves with thin films can enhance their wear resistance, reduce friction, and improve overall engine performance.
By using sputtering targets, manufacturers can deposit thin films of materials onto valve parts with high precision and control. These coatings provide a protective layer that can withstand high temperatures, resist corrosion, and prolong the lifespan of the valves. As a result, engines can operate more efficiently and have a longer service life.
Applications in telecommunications, electronics, aerospace, and automotive industries
Sputtering targets have a wide range of applications in various industries due to their versatility and effectiveness in depositing thin films. Some of the key industries that benefit from sputtering target technology include:
-
Telecommunications: Sputtering targets are used to deposit thin films of materials onto substrates, creating transparent conductive coatings for LCD displays and touch screens. These coatings are essential for the functionality and performance of electronic devices in the telecommunications industry.
-
Electronics: Sputtering targets are used in the production of integrated circuits, semiconductors, and display screens. The deposition of thin films onto these electronic components enhances their performance, reliability, and durability.
-
Aerospace: The aerospace industry relies on sputtering targets for various applications, including the coating of engine components, architectural ironmongery, panels, and sheets. These coatings provide improved corrosion resistance, wear resistance, and thermal stability, ensuring the safety and efficiency of aerospace systems.
-
Automotive: Sputtering targets are extensively used in the automotive industry for coating engine components, decorative trim, wheels, and other parts. These coatings enhance the durability, functionality, and aesthetic appeal of automotive products.
In conclusion, the expansion of sputtering targets into new applications is driven by the increasing demand for thin film coatings in industries such as telecommunications, electronics, aerospace, and automotive. The pressing of sputtering targets and the coating of valve parts in engines are emerging applications that offer improved performance, durability, and functionality. With their ability to deposit thin films onto a variety of substrates with high precision, sputtering targets continue to revolutionize various industries and contribute to technological advancements.
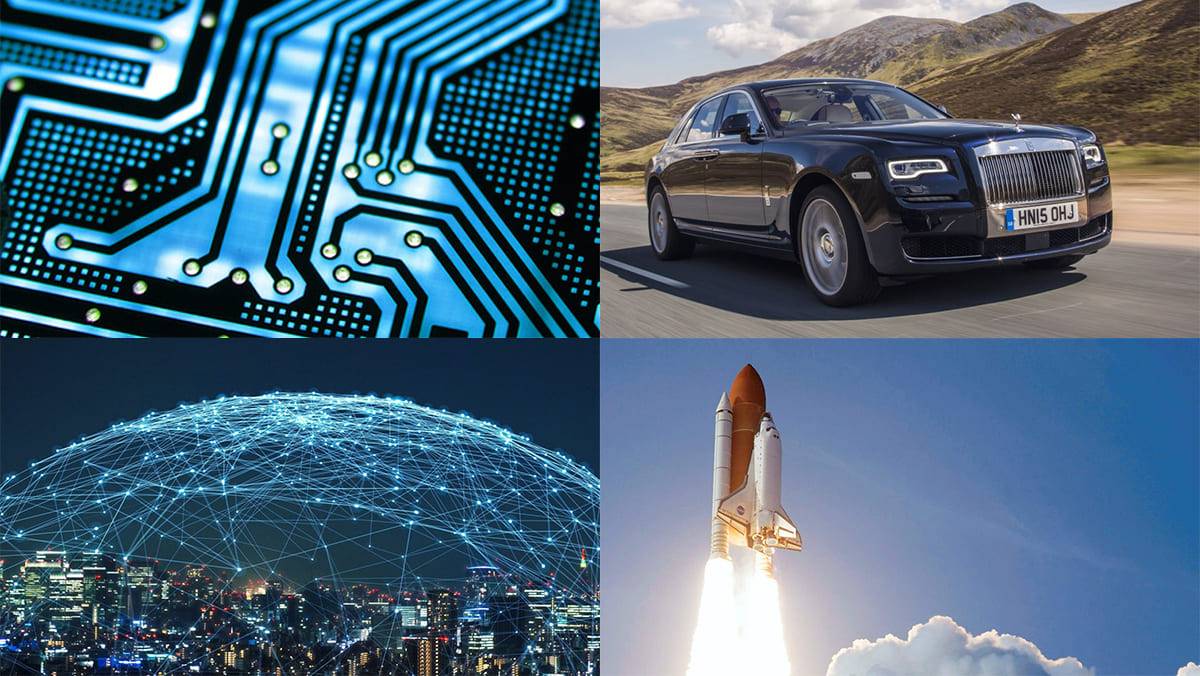
Conclusion
Cold Isostatic Pressing (CIP) is a proven and reliable process for manufacturing high-performance parts. With its ability to achieve 95% theoretical density for ceramics and consolidate metal and ceramic powders, CIP offers excellent results. This technology finds applications in various industries, including dental, medical, telecommunications, electronics, aerospace, and automotive. It is used for compressing graphite, refractories, electrical insulators, and even for pressing sputtering targets and coating valve parts in engines. CIP has consistently demonstrated its effectiveness in producing durable and high-quality components, making it a valuable technique in the manufacturing world.
CONTACT US FOR A FREE CONSULTATION
KINTEK LAB SOLUTION's products and services have been recognized by customers around the world. Our staff will be happy to assist with any inquiry you might have. Contact us for a free consultation and talk to a product specialist to find the most suitable solution for your application needs!