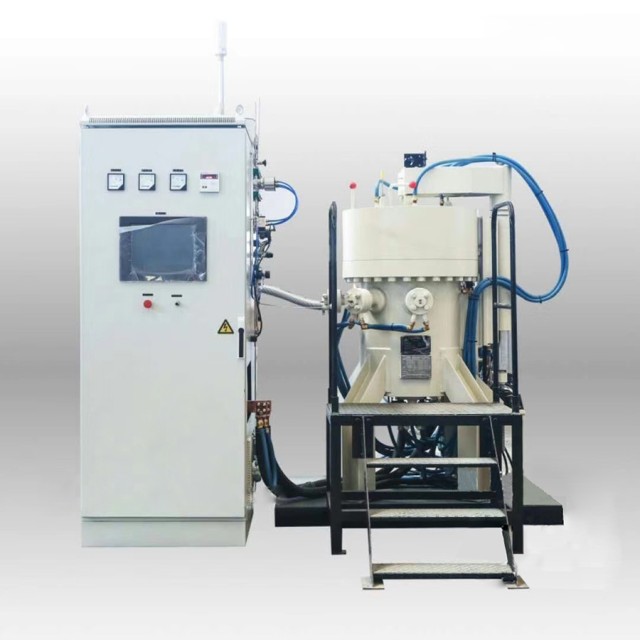
Vacuum Furnace
Vacuum Heat Treat and Sintering Furnace with 9MPa Air Pressure
Item Number : KT-APS
Price varies based on specs and customizations
- Specification
- Please refer to the icon below for details
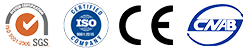
Shipping:
Contact us to get shipping details Enjoy On-time Dispatch Guarantee.
Why Choose Us
Reliable PartnerEasy ordering process, quality products, and dedicated support for your business success.
Introduction
The air pressure sintering furnace is a high-tech equipment commonly used for the sintering of advanced ceramic materials. It combines vacuum sintering and pressure sintering techniques to achieve high-density and high-strength ceramics. Key features of this furnace include:
- High Pressure Capability: Operates at pressures up to 9MPa, enabling effective densification of ceramic materials.
- Temperature Control: Precise temperature regulation up to 2200℃, ensuring accurate and uniform heating.
- Vacuum System: Achieves a cold vacuum degree of 10-3Pa, creating an oxygen-free environment for sintering.
- Atmosphere Control: Allows for the introduction of specific gases to control the sintering atmosphere.
- Versatile Structures: Available in vertical, horizontal, and bottom-up configurations, accommodating different sample sizes and shapes.
Details & Part
Applications
- Vacuum sintering and pressure sintering of SiC and Si3N4 ceramic parts
- Aerospace and automotive industries
- Medical and dental applications
- Research and development laboratories
Features
- Enhanced Temperature Uniformity: Equipped with multiple independent heaters and optimized power distribution, this furnace ensures consistent temperature throughout the high-pressure heating zone, promoting uniform sintering.
- Comprehensive Safety Protection: Advanced safety measures are incorporated, including automatic locking systems for door operations, temperature control, and pressure regulation. Emergency and power failure scenarios are addressed with pressure release valves, ensuring safe operation.
- Cooling System Monitoring: The cooling water system is meticulously monitored for pressure, temperature, and flow. Flow monitoring for each cooling water circuit safeguards against equipment damage due to water shortage failures.
Principle
The air pressure sintering furnace utilizes a combination of high temperature and pressure to densify ceramic materials. The furnace consists of a heating chamber, pressure vessel, gas supply system, and temperature control system. During operation, the furnace is heated to a predetermined temperature, and a high-pressure gas (typically nitrogen or argon) is introduced into the pressure vessel. The high pressure compresses the ceramic powder, promoting grain growth and densification. This process results in improved mechanical properties, such as increased strength and hardness, and reduced porosity. The furnace can be used for a variety of ceramic materials, including silicon carbide (SiC), silicon nitride (Si3N4), and zirconia (ZrO2).
Advantages
- High temperature uniformity: The air pressure sintering furnace adopts a unique heating element design, which ensures high temperature uniformity in the furnace chamber. This is important for achieving consistent sintering results.
- Fast heating and cooling rates: The air pressure sintering furnace has a high heating rate and cooling rate, which can significantly reduce the sintering time. This can save energy and improve productivity.
- Precise temperature control: Theair pressure sintering furnace has a precise temperature control system, which can accurately control the temperature in the furnace chamber. This is important for achieving the desired sintering results.
- Wide range of applications: The air pressure sintering furnace can be used for a wide range of materials, including metals, ceramics, and composites. This makes it a versatile tool for various applications.
- Easy to operate: The air pressure sintering furnace is easy to operate, with a user-friendly interface. This makes it accessible to users of all skill levels.
Technical specification
Air pressure sintering furnace | Vertical structure |
The working area | Φ100×90mm, Φ200×220mm, etc. |
The bottom-lift type | Φ300×400mm, etc. |
The horizontal type | 250×250×400mm, 375×375×475mm, etc. |
Cold vacuum degree | 10-3Pa, 10Pa, etc |
Maximum pressure | 1.2MPa, 2MPa, 6MPa, 9MPa |
Temperature | 2000℃-2200℃ |
FAQ
What Is A Vacuum Furnace Used For?
What Are Advanced Ceramics?
What Are The Benefits Of A Air Pressure Sintering Furnace?
What Are The Applications Of A Air Pressure Sintering Furnace?
What Are The Factors To Consider When Choosing A Air Pressure Sintering Furnace?
What Is The Process Of A Vacuum Furnace?
What Are The Main Types Of Advanced Ceramics?
What Gas Is Used In A Vacuum Furnace?
What Are The Applications Of Advanced Ceramics?
What Is The Heating Element Used In A Vacuum Furnace?
How Are Advanced Ceramics Manufactured?
What Are The Advantages Of Using Advanced Ceramics?
What Is The Difference Between Alumina And Zirconia Ceramics?
Why Are Silicon Carbide Ceramics Used In High-temperature Applications?
What Makes Boron Nitride Ceramics Unique?
How Do Advanced Ceramics Contribute To Energy Efficiency?
4.8
out of
5
The 9.8MPa air pressure sintering furnace from KINTEK SOLUTION is a game-changer for our laboratory. It delivers exceptional sintering results with remarkable speed and efficiency.
4.9
out of
5
I'm thoroughly impressed with the value for money offered by this pressure sintering furnace. It provides outstanding performance at a competitive price, making it an excellent investment for our research facility.
4.7
out of
5
The quality and durability of this furnace are top-notch. It has consistently exceeded our expectations, delivering flawless sintering results for our demanding applications.
4.8
out of
5
KINTEK SOLUTION's pressure sintering furnace is a testament to their technological advancement. It incorporates cutting-edge features that enable us to achieve unprecedented levels of material densification.
4.9
out of
5
This furnace has revolutionized our workflow. Its user-friendly interface and automated controls have significantly reduced the time and effort required for our sintering processes.
4.7
out of
5
The pressure sintering furnace from KINTEK SOLUTION has exceeded all our expectations. Its precise temperature control and uniform heating ensure consistent and reliable results every time.
4.8
out of
5
We've been using this pressure sintering furnace for several months now, and it has proven to be an indispensable tool in our laboratory. Its high-pressure capability and versatile configurations allow us to tackle a wide range of research projects.
4.9
out of
5
The technical specifications of this furnace are truly impressive. It delivers exceptional performance and meets the highest industry standards, making it an ideal choice for our demanding applications.
4.7
out of
5
KINTEK SOLUTION has once again delivered an innovative solution with this pressure sintering furnace. It's a game-changer for our research, enabling us to explore new materials and applications.
4.8
out of
5
The speed and efficiency of this furnace are remarkable. It has significantly reduced our turnaround time for sintering processes, allowing us to meet project deadlines with ease.
4.9
out of
5
I highly recommend this pressure sintering furnace to any laboratory looking for a reliable and high-performing solution. It's a valuable asset to our research team.
4.7
out of
5
The user-friendly interface and comprehensive safety features of this furnace make it a joy to operate. It's a testament to KINTEK SOLUTION's commitment to customer satisfaction.
4.8
out of
5
The versatility of this pressure sintering furnace is truly impressive. It accommodates a wide range of materials and sample sizes, making it an indispensable tool for our research.
4.9
out of
5
KINTEK SOLUTION's pressure sintering furnace is a valuable investment for any laboratory. It's a powerful and reliable tool that has transformed our research capabilities.
4.7
out of
5
The exceptional quality and durability of this pressure sintering furnace make it a worthwhile investment. It's a long-lasting solution that will support our research for years to come.
Products
Vacuum Heat Treat and Sintering Furnace with 9MPa Air Pressure
REQUEST A QUOTE
Our professional team will reply to you within one business day. Please feel free to contact us!
Related Products
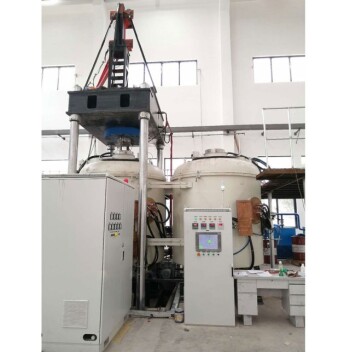
600T Vacuum Induction Hot Press Furnace for Heat Treat and Sintering
Discover the 600T Vacuum Induction Hot Press Furnace, designed for high-temperature sintering experiments in vacuum or protected atmospheres. Its precise temperature and pressure control, adjustable working pressure, and advanced safety features make it ideal for nonmetal materials, carbon composites, ceramics, and metal powders.
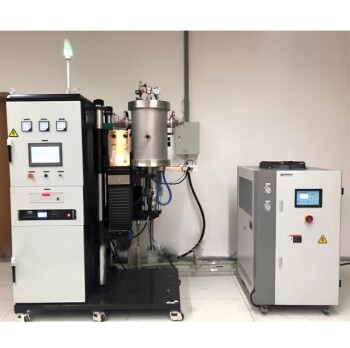
Vacuum Heat Treat and Molybdenum Wire Sintering Furnace for Vacuum Sintering
A vacuum molybdenum wire sintering furnace is a vertical or bedroom structure, which is suitable for withdrawal, brazing, sintering and degassing of metal materials under high vacuum and high temperature conditions. It is also suitable for dehydroxylation treatment of quartz materials.
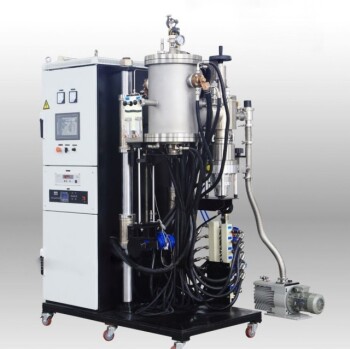
Small Vacuum Heat Treat and Tungsten Wire Sintering Furnace
The small vacuum tungsten wire sintering furnace is a compact experimental vacuum furnace specially designed for universities and scientific research institutes. The furnace features a CNC welded shell and vacuum piping to ensure leak-free operation. Quick-connect electrical connections facilitate relocation and debugging, and the standard electrical control cabinet is safe and convenient to operate.
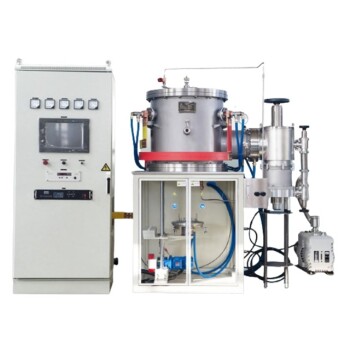
2200 ℃ Tungsten Vacuum Heat Treat and Sintering Furnace
Experience the ultimate refractory metal furnace with our Tungsten vacuum furnace. Capable of reaching 2200℃, perfect for sintering advanced ceramics and refractory metals. Order now for high-quality results.
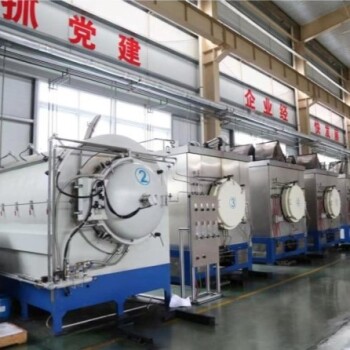
Vacuum Heat Treat Sintering Brazing Furnace
A vacuum brazing furnace is a type of industrial furnace used for brazing, a metalworking process that joins two pieces of metal using a filler metal that melts at a lower temperature than the base metals. Vacuum brazing furnaces are typically used for high-quality applications where a strong, clean joint is required.
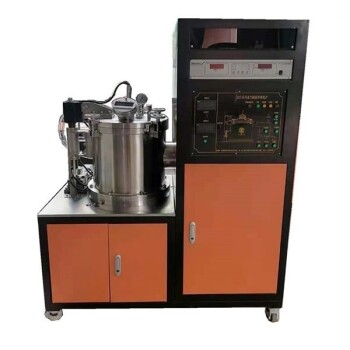
Vacuum Heat Treat Furnace and Levitation Induction Melting Furnace
Experience precise melting with our Vacuum Levitation Melting Furnace. Ideal for high melting point metals or alloys, with advanced technology for effective smelting. Order now for high-quality results.
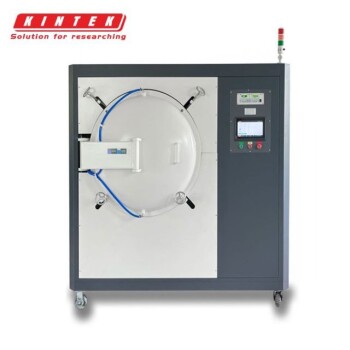
Vacuum Heat Treat Furnace with Ceramic Fiber Liner
Vacuum furnace with polycrystalline ceramic fiber insulation liner for excellent heat insulation and uniform temperature field. Choose from 1200℃ or 1700℃ max. working temperature with high vacuum performance and precise temperature control.
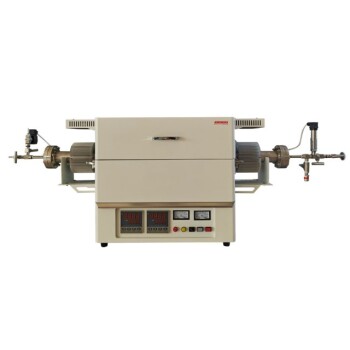
High Pressure Laboratory Vacuum Tube Furnace Quartz Tubular Furnace
KT-PTF High Pressure Tube Furnace: Compact split tube furnace with strong positive pressure resistance. Working temp up to 1100°C and pressure up to 15Mpa. Also works under controller atmosphere or high vacuum.
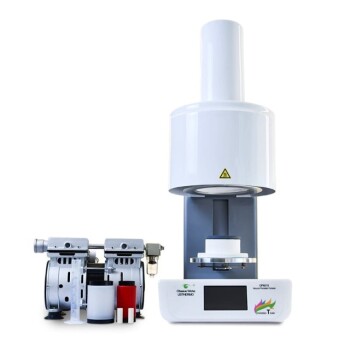
Dental Porcelain Zirconia Sintering Ceramic Vacuum Press Furnace
Get precise dental results with Dental Vacuum Press Furnace. Automatic temperature calibration, low noise tray, and touch screen operation. Order now!
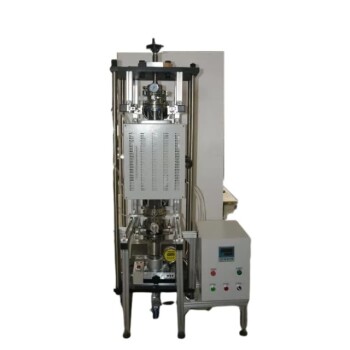
Vacuum Hot Press Furnace Heated Vacuum Press Machine Tube Furnace
Reduce forming pressure & shorten sintering time with Vacuum Tube Hot Press Furnace for high-density, fine-grain materials. Ideal for refractory metals.
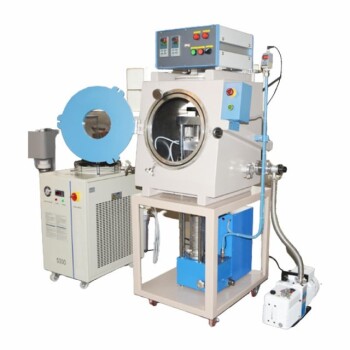
Vacuum Hot Press Furnace Machine for Lamination and Heating
Experience clean and precise lamination with Vacuum Lamination Press. Perfect for wafer bonding, thin-film transformations, and LCP lamination. Order now!
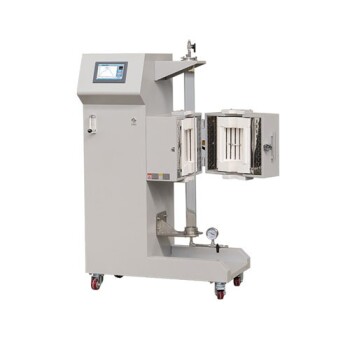
Vertical Laboratory Quartz Tube Furnace Tubular Furnace
Elevate your experiments with our Vertical Tube Furnace. Versatile design allows for operation under various environments and heat treatment applications. Order now for precise results!
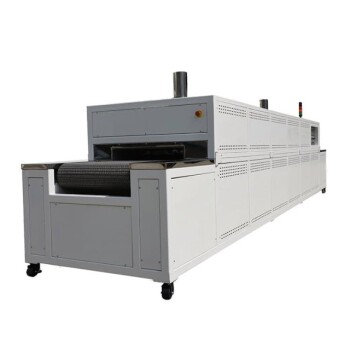
Mesh belt controlled atmosphere furnace
Discover our KT-MB mesh belt sintering furnace - perfect for high-temperature sintering of electronic components & glass insulators. Available for open air or controlled atmosphere environments.
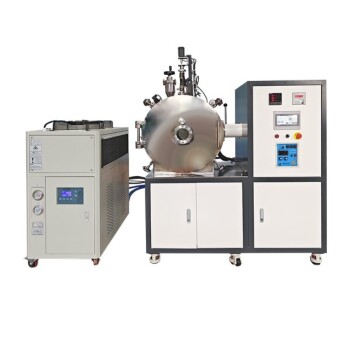
Lab-Scale Vacuum Induction Melting Furnace
Get precise alloy composition with our Vacuum Induction Melting Furnace. Ideal for aerospace, nuclear energy, and electronic industries. Order now for effective smelting and casting of metals and alloys.
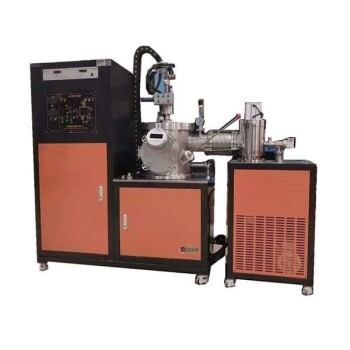
Vacuum Arc Induction Melting Furnace
Discover the power of Vacuum Arc Furnace for melting active & refractory metals. High-speed, remarkable degassing effect, and free of contamination. Learn more now!
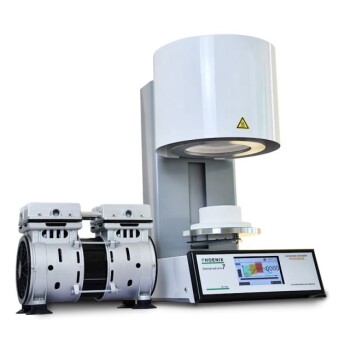
Vacuum Dental Porcelain Sintering Furnace
Get precise and reliable results with KinTek's Vacuum Porcelain Furnace. Suitable for all porcelain powders, it features hyperbolic ceramic furnace function, voice prompt, and automatic temperature calibration.
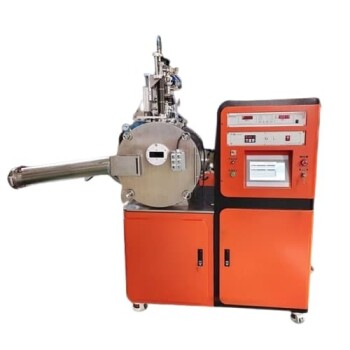
Vacuum Induction Melting Spinning System Arc Melting Furnace
Develop metastable materials with ease using our Vacuum Melt Spinning System. Ideal for research and experimental work with amorphous and microcrystalline materials. Order now for effective results.
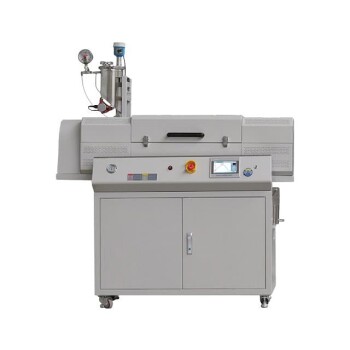
Laboratory Vacuum Tilt Rotary Tube Furnace Rotating Tube Furnace
Discover the versatility of Laboratory Rotary Furnace: Ideal for calcination, drying, sintering, and high-temperature reactions. Adjustable rotating and tilting functions for optimal heating. Suitable for vacuum and controlled atmosphere environments. Learn more now!
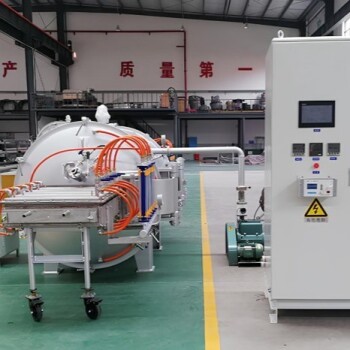
Graphite Vacuum Continuous Graphitization Furnace
High-temperature graphitization furnace is a professional equipment for graphitization treatment of carbon materials. It is a key equipment for the production of high-quality graphite products. It has high temperature, high efficiency and uniform heating. It is suitable for various high-temperature treatments and graphitization treatments. It is widely used in metallurgy, electronics, aerospace, etc. industry.
Related Articles
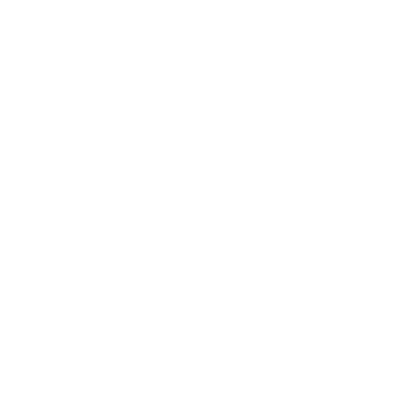
Exploring the Advanced Capabilities of Spark Plasma Sintering (SPS) Furnaces
Dive into the world of Spark Plasma Sintering (SPS) furnaces, their innovative technology, and applications in material science. Learn how SPS furnaces revolutionize the sintering process with high-speed, efficiency, and precision.
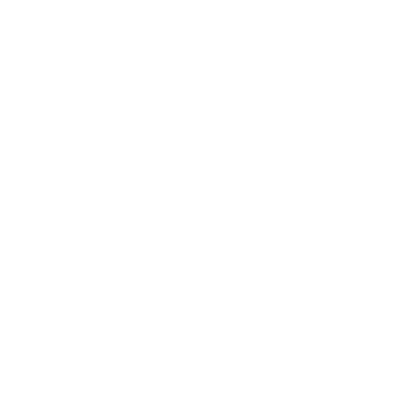
The Ultimate Guide to Vacuum Pressure Sintering Furnace: Benefits, Applications, and Working Principle
Discover the benefits, applications, and working principle of vacuum pressure sintering furnace. Learn how vacuum sintering produces clean, bright parts with incredible design flexibility and quick turnaround, and its applications in teaching, scientific research, and production. Explore the precise setting and monitoring of process parameters, and the advantages of sintering under vacuum and pressure. Find out how vacuum sintering furnace is perfect for higher temperature sintering applications and for sintering extremely reactive materials.
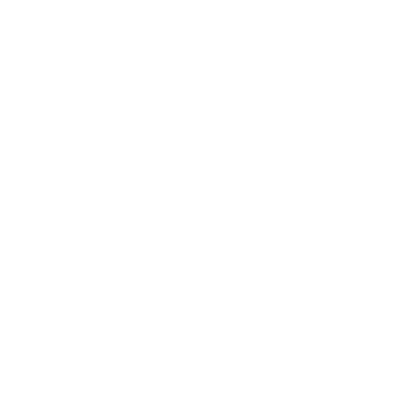
Exploring Spark Plasma Sintering Furnace (SPS): Technology, Applications, and Advantages
Dive into the comprehensive guide on Spark Plasma Sintering Furnace (SPS), covering its technology, applications in materials science, and significant advantages over traditional sintering methods.
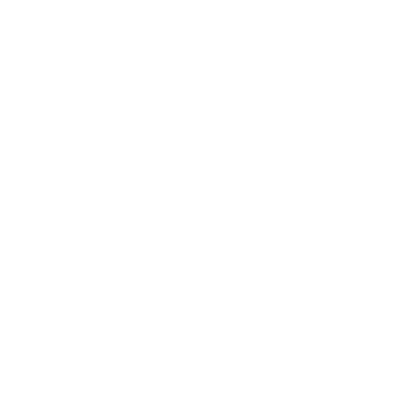
Comprehensive Guide to Spark Plasma Sintering Furnaces: Applications, Features, and Benefits
Explore the advanced features and applications of Spark Plasma Sintering Furnaces (SPS) in material science. Learn how SPS technology offers rapid, efficient, and versatile sintering for various materials.
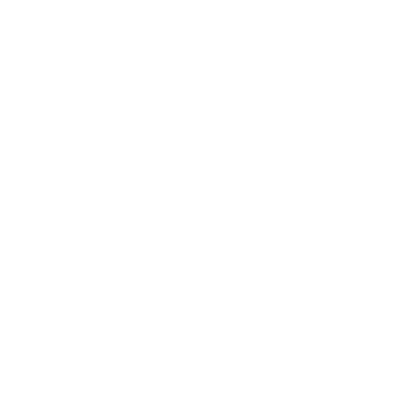
Comprehensive Guide to Vacuum Hot Press Furnace Application
The Vacuum Hot Press Furnace is a versatile tool especially suited for sintering experiments involving non-metallic materials, carbon composites, ceramic materials and metal powder materials.
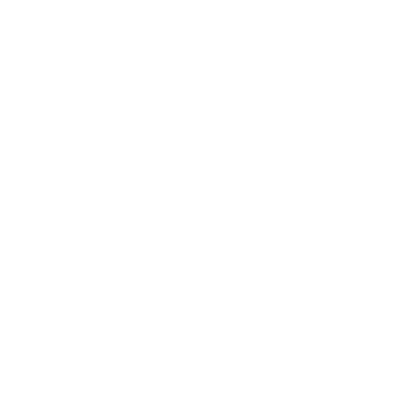
The Latest Advancements in Zirconia Sintering Furnaces for Dental Applications
Zirconia sintering furnaces are designed to give dental professionals the ability to create dental restorations with the highest level of precision and accuracy.
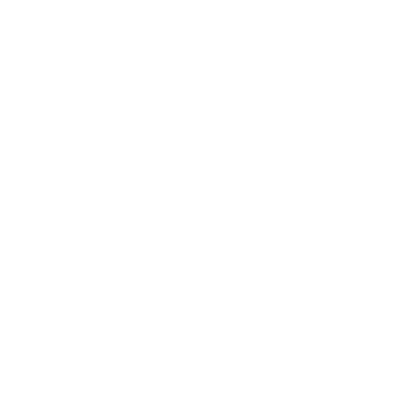
Spark Plasma Sintering Furnace: The Ultimate Guide to SPS Furnaces
Discover the world of Spark Plasma Sintering Furnaces (SPS). This comprehensive guide covers everything from its advantages and applications to its process and equipment. Learn how SPS furnaces can revolutionize your sintering operations.
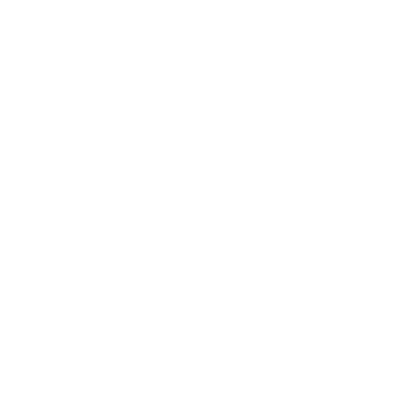
Top 5 Features of a High-Quality Zirconia Sintering Oven
Investing in a high-quality sintering oven is crucial for dental laboratories that want to produce high-quality zirconia restorations consistently.
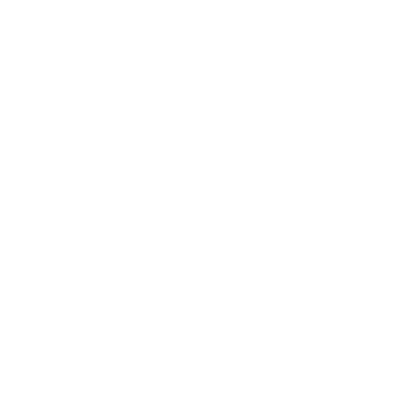
The Benefits of Controlled Atmosphere Furnaces for Sintering and Annealing Processes
They are essential in preventing oxidation, reducing the risk of contamination, and improving the properties of the materials being treated.
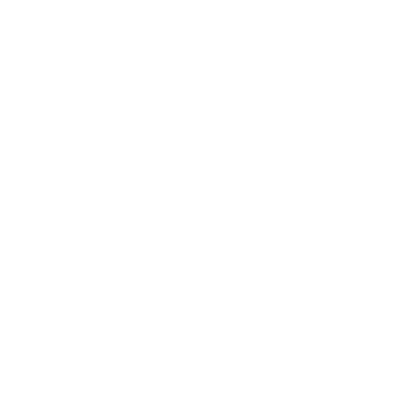
Vacuum Hot Press Furnace: A Comprehensive Guide
Gain in-depth knowledge of Vacuum Hot Press Furnaces, their components, benefits, and applications in various industries. Explore how these furnaces revolutionize material processing and achieve exceptional results.
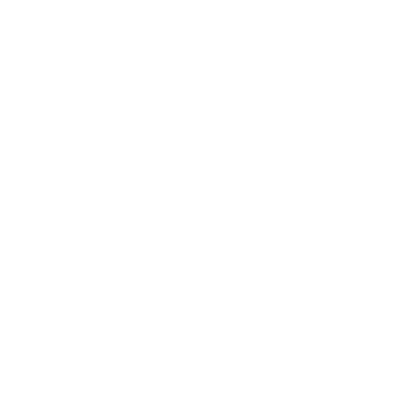
Dental Sintering Furnaces The Impact on Restoration Quality and Durability
Dental sintering furnaces play a crucial role in the manufacturing process of dental crowns and other restorations.
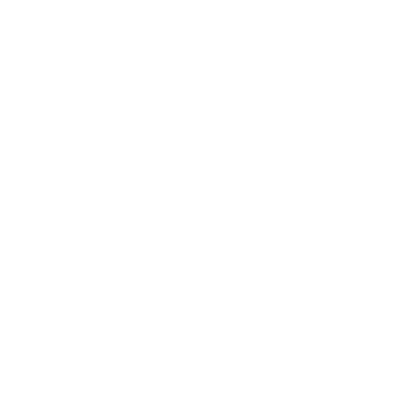
Molybdenum Vacuum Furnace: High-Temperature Sintering and Advanced Applications
Explore the advanced features and applications of molybdenum vacuum furnaces in high-temperature sintering and material treatment. Learn about their construction, control systems, and maintenance tips.