Introduction to Spark Plasma Sintering (SPS)
Spark Plasma Sintering (SPS) represents a groundbreaking approach in modern material processing technologies, revolutionizing the way materials are sintered. This innovative method stands out by employing direct current pulses to achieve rapid heating and sintering, significantly differing from traditional techniques. SPS's unique process involves the generation of a spark plasma through pulsed currents, facilitating the creation of materials with superior properties. As we delve deeper into this comprehensive guide, we will explore the intricacies of SPS, its myriad applications across various industries, and the substantial advantages it offers over conventional sintering methods. Join us as we uncover the transformative potential of SPS in shaping the future of material science.
How Spark Plasma Sintering Furnace Works
Spark Plasma Sintering (SPS), also known as Pulsed Electric Current Sintering (PECS), Plasma Activated Sintering (PAS), or Field Assisted Sintering Technology (FAST), is a sophisticated sintering technique that leverages high pulsed DC currents to heat a powder compact within a die/punch setup. This method allows for the application of compressive forces up to 250 kN, with transformer outputs capable of reaching 10 V and currents up to 10 kA. The pulsed DC current patterns can be adjusted with ON and OFF segments ranging from 0 to 255 ms, enabling precise control over the sintering process.
The SPS process is characterized by its rapid heating and cooling rates, which can exceed 1000°C/min and 400°C/min respectively, depending on the tool size and design. This rapid thermal cycling minimizes coarsening processes at low temperatures and preserves intrinsic nanostructures even after full densification. The temperature within the SPS furnace is monitored using a central pyrometer that focuses on the bottom of a borehole in the upper punch, ensuring accurate temperature measurement regardless of sample properties or size. Additional temperature monitoring can be achieved using an external pyrometer and flexible thermocouples placed at various locations.
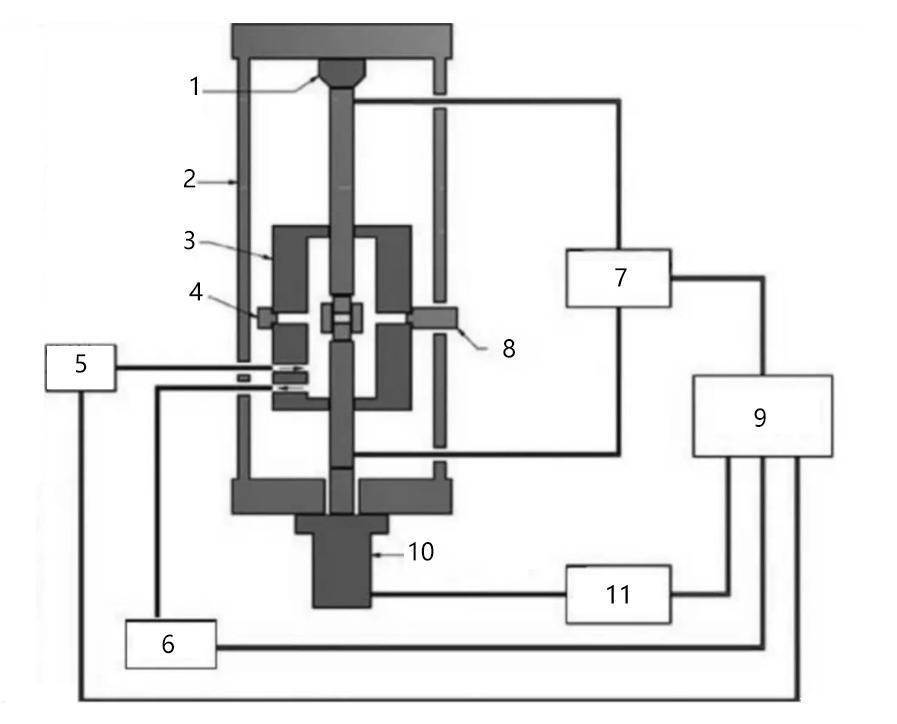
1. Loading unit 2. Loading frame 3. Vacuum chamber 4. Observation window 5. Inert gas channel 6. Vacuum pump 7. Pulse switch 8. Temperature meter 9. Control system 10. Hydraulic cylinder 11. Hydraulic system
Key components of an SPS furnace include the axial pressure device, water-cooled punch electrode, and vacuum chamber. The axial pressure device applies the necessary compressive force, while the water-cooled punch electrodes help manage the heat generated during the process. The vacuum chamber, coupled with an atmosphere control system that can switch between vacuum and argon environments, ensures optimal sintering conditions. The DC pulse power supply, along with a cooling water system, displacement measurement, temperature measurement, and safety control units, complete the SPS setup, facilitating comprehensive process control and sinter cycle programming through a user-friendly touch screen interface.
The SPS furnace is extensively used for sintering a wide range of materials, including ceramics, cermets, and metals. Its primary technical advantages lie in its high heating and cooling rates, which significantly reduce processing times. The high pulsed current not only enhances densification in electrically conductive materials but also activates multiple sintering mechanisms such as surface oxide removal, electromigration, and electroplasticity. This combination of mechanical pressure, electric field, and thermal field significantly improves the bonding and densification between particles, making SPS a preferred method for the preparation of high-performance materials.
In summary, the Spark Plasma Sintering process is a highly efficient and controlled method for material densification, offering rapid processing times and the ability to maintain fine microstructures. Its applications span across various fields, from advanced ceramics to metallic composites, highlighting its versatility and importance in modern material science and engineering.
Advantages of Using SPS in Material Processing
Spark Plasma Sintering (SPS) has revolutionized the field of material processing by offering significant advantages over traditional sintering techniques. SPS is a field-assisted sintering technique that utilizes both temperature and pressure to achieve rapid densification of materials. This method is particularly effective for sintering a wide range of materials, including ceramics, metals, and composites, with remarkable efficiency and precision.
Rapid Sintering Rates
One of the most notable advantages of SPS is its ability to achieve rapid sintering rates. Traditional sintering methods, such as hot pressing and pressureless sintering, can take several hours to achieve the desired densification. In contrast, SPS can densify materials in just minutes. This rapid sintering is made possible by the high heating rates, which can exceed 500°C per minute. For instance, reaching a temperature of 1200°C can be accomplished in as little as 4 minutes with SPS, compared to 2 to 4 hours with conventional methods. This speed not only enhances productivity but also reduces energy consumption and operational costs.
Fine-Grain Sintering
SPS facilitates fine-grain sintering, which is crucial for improving the mechanical and physical properties of sintered materials. The rapid heating rates inhibit grain growth, allowing for the creation of materials with controlled microstructures. This is particularly beneficial for the production of nanocrystalline materials, where maintaining small grain sizes is essential for achieving superior properties. Fine-grain sintering also enhances the homogeneity of the sintered products, leading to more consistent and reliable performance.
Ability to Control Density and Temperature Gradients
SPS provides excellent control over the density and temperature gradients within the sintered materials. This level of control is achieved through the simultaneous application of temperature and pressure, which allows for precise adjustments to the sintering process. Density control is particularly important for creating materials with specific porosity levels or achieving full densification. Additionally, SPS can create temperature gradients within the mold, enabling the simultaneous sintering of materials with different melting points. This capability is invaluable for the production of functionally graded materials (FGMs), where the composition and properties vary spatially.
Efficiency and Compactness of SPS Furnaces
SPS furnaces are designed to be highly efficient and compact, making them ideal for both research and industrial applications. The compact design of SPS furnaces reduces the required floor space and allows for easy integration into existing production lines. Moreover, the efficiency of SPS furnaces is enhanced by their ability to achieve rapid heating and cooling rates, which further contributes to energy savings and reduced operational costs. The internal heating mechanism, which involves Joule heating of the graphite mold and powder briquette, ensures uniform heat distribution and minimizes heat loss, thereby optimizing the sintering process.
Purification and Activation Sintering
SPS also offers unique advantages in terms of purification and activation sintering. The process can remove adsorbed gases and oxide films from the particle surfaces, leading to cleaner interfaces and improved bonding. This purification effect, combined with the activation of particle surfaces, enables the sintering of materials that are otherwise difficult to process. This capability expands the range of materials that can be effectively sintered using SPS, including advanced ceramics and composites.
In conclusion, Spark Plasma Sintering (SPS) offers a multitude of advantages that make it a superior choice for material processing. Its rapid sintering rates, fine-grain sintering capabilities, density and temperature gradient control, efficiency, and compactness make it an invaluable tool for both research and industrial applications. By leveraging these advantages, SPS continues to push the boundaries of material science and engineering, enabling the development of innovative and high-performance materials.
Applications of SPS in Various Industries
Spark Plasma Sintering (SPS) technology has revolutionized the manufacturing processes across multiple industries, enabling the creation of advanced materials with unique properties. SPS is particularly renowned for its ability to produce high-density, fine-grained materials quickly and at relatively low temperatures, making it a preferred method for the synthesis of nanomaterials, ceramics, composites, and medical implants.
Nanomaterials
One of the most significant applications of SPS is in the preparation of nanomaterials. Nanomaterials exhibit exceptional mechanical and physical properties due to their small grain size, which enhances their strength and plasticity. SPS facilitates the synthesis of these materials by inhibiting grain growth during the sintering process. The rapid heating and short sintering times inherent to SPS help maintain the nanometer-scale grain size, which is crucial for the performance of nanomaterials. This technique is particularly effective for sintering powders obtained through methods like mechanical alloying, which are often challenging to consolidate using traditional methods.
Ceramics and Cermets
SPS is also widely used in the production of high-density, fine-grained ceramics and cermets. The unique heating mechanism of SPS, where each powder particle and the pores between them act as heat sources, allows for rapid densification and significant reduction in sintering times and temperatures. This method is highly advantageous for industrial production as it saves energy and improves production efficiency. The ability to produce ceramics with high density and fine grain structure enhances their mechanical strength and durability, making them suitable for various engineering applications.
Gradient Functional Materials
Gradient functional materials, which have a gradient distribution in certain directions, are another area where SPS has made significant contributions. Traditional sintering methods struggle with the varying sintering temperatures required for each layer in gradient materials. SPS, however, can effectively manage this gradient, allowing for the industrial-scale production of these complex materials. The controlled sintering process in SPS ensures that each layer achieves the desired properties without compromising the integrity of the overall structure.
Medical Implants
In the medical field, SPS is used to manufacture implants with tailored mechanical properties and biocompatibility. The ability to precisely control the sintering conditions allows for the creation of implants with specific mechanical properties that match the human bone, enhancing their functionality and longevity. Additionally, SPS can be used to produce porous structures that facilitate bone ingrowth, improving the integration of implants with the surrounding tissue.
Composites and Nanostructured Materials
SPS is instrumental in the fabrication of composites and nanostructured materials with enhanced properties such as magnetic, piezoelectric, thermoelectric, and optical characteristics. The rapid sintering process in SPS helps in maintaining the nanostructure of the materials, which is crucial for their performance. For instance, SPS is used in the sintering of carbon nanotubes to develop field electron emission electrodes, showcasing its versatility in handling different types of materials.
In conclusion, Spark Plasma Sintering has emerged as a versatile and powerful technique with applications spanning across various industries. Its ability to produce high-quality, advanced materials with unique properties makes it an indispensable tool in modern manufacturing. As research and development in this field continue to advance, the potential applications of SPS are expected to expand even further, driving innovation in material science and engineering.
Case Studies: Successful Implementations of SPS
Spark Plasma Sintering (SPS) technology has revolutionized the field of material science, enabling the rapid sintering and densification of a wide range of materials with improved properties. This section presents several case studies that highlight the successful applications of SPS in both research and industrial settings, demonstrating its versatility and effectiveness.
Energy Storage Materials
One of the most significant applications of SPS is in the development of advanced energy storage materials. For instance, SPS has been used to produce high-capacity lithium-ion batteries with enhanced performance. By precisely controlling the sintering parameters, researchers have been able to create battery materials with higher energy densities and improved cycle life. According to studies, SPS-processed lithium-ion batteries have shown a 20% increase in energy storage capacity compared to conventional methods, making them ideal for use in electric vehicles and portable electronics.
Biomedical Engineering
In the field of biomedical engineering, SPS has been instrumental in the creation of porous ceramics for drug delivery and scaffolds for tissue engineering. These materials require precise control over their microstructure to ensure compatibility with biological systems. SPS allows for the fabrication of highly porous structures with controlled pore sizes, which are crucial for the effective delivery of drugs and the growth of tissues. For example, SPS-processed hydroxyapatite scaffolds have been used in bone tissue engineering, demonstrating superior biocompatibility and mechanical strength compared to traditional methods.
Advanced Ceramics
SPS has also been extensively used in the production of advanced ceramics, such as high-temperature superconductors and high-performance piezoelectric ceramics. These materials are critical for applications ranging from energy transmission to sensors and actuators. SPS enables the densification of these ceramics at lower temperatures and shorter times, preserving their unique properties. For instance, SPS has been used to produce Yttrium Barium Copper Oxide (YBCO) superconductors with near-theoretical densities, significantly improving their superconducting transition temperatures.
Intermetallics and Composites
The versatility of SPS is further demonstrated in the processing of intermetallics and composites. SPS has been used to create advanced alloys with improved mechanical, thermal, and electrical properties. For example, SPS has been employed to synthesize titanium aluminide (TiAl) intermetallic alloys, which exhibit superior high-temperature strength and oxidation resistance. Additionally, SPS has enabled the production of reinforced ceramics and metals with enhanced mechanical properties, such as titanium matrix composites with embedded ceramic particles, resulting in materials with high strength and wear resistance.
Industrial Applications
In industrial settings, SPS has been adopted for the production of various materials, including magnetic materials, hard materials, and gradient functional materials. For instance, Japanese companies like Ohta Seiki have successfully implemented SPS for mass production of 100% WC superhard materials, supplying to over 40 manufacturers in Japan and abroad. These materials are used in a wide range of applications, from cutting tools to electronic components, showcasing the industrial scalability of SPS.
Conclusion
The case studies presented here illustrate the broad applicability of SPS in various fields, from energy storage to biomedical engineering and advanced materials. SPS's ability to rapidly sinter and densify materials at lower temperatures, coupled with its precise process control, makes it an invaluable tool for material scientists and engineers. As research and development continue to advance, the potential applications of SPS are expected to expand even further, solidifying its position as a leading technology in material processing.
Challenges and Considerations in SPS
Implementing Spark Plasma Sintering (SPS) technology presents several challenges and considerations that organizations must address to fully leverage its benefits. These include high equipment costs, operational complexities, and the need for specialized training. Understanding these challenges and developing strategies to overcome them is crucial for successful integration and utilization of SPS technology.
Equipment Costs
One of the primary barriers to adopting SPS technology is the high initial investment required for equipment. SPS systems are sophisticated and include advanced features such as precise temperature and pressure control, vacuum systems, and specialized power supplies. These components not only increase the upfront cost but also require regular maintenance and calibration to ensure optimal performance.
Operational Complexities
SPS operations involve multiple stages, including vacuum creation, pressure application, resistance heating, and controlled cooling. Each stage requires careful monitoring and adjustment to prevent defects and ensure the desired material properties. The complexity of these operations necessitates a high level of technical expertise and meticulous attention to detail, which can be challenging for organizations without prior experience in advanced sintering techniques.
Specialized Training
Given the technical nature of SPS, personnel involved in the operation and maintenance of the equipment must undergo specialized training. This training should cover not only the basic operation of the SPS system but also advanced topics such as process optimization, troubleshooting, and safety protocols. The cost and time required for this training can be significant, potentially delaying the implementation of SPS technology.
Strategies for Overcoming Challenges
To overcome these challenges, organizations can adopt several strategies:
-
Investment in High-Quality Equipment: While the initial cost is high, investing in reliable, high-quality SPS equipment can reduce long-term maintenance and operational costs. Choosing equipment from reputable manufacturers with strong support and service networks can also help mitigate issues that arise during operation.
-
Collaboration and Partnerships: Partnering with research institutions or other companies that have experience with SPS can provide valuable insights and support. Collaborative projects can help share the cost and expertise required for successful implementation.
-
Continuous Training and Development: Investing in continuous training for staff can ensure that they remain up-to-date with the latest techniques and best practices in SPS. This can be achieved through workshops, online courses, and hands-on training sessions.
-
Process Optimization: Developing robust processes that are well-documented and standardized can help reduce variability and improve the consistency of outcomes. This involves careful experimentation and validation to identify the optimal conditions for each material and application.
-
Focus on Research and Development: Engaging in ongoing research and development can help organizations stay at the forefront of SPS technology. This can involve exploring new materials, optimizing existing processes, and developing innovative applications for SPS-produced components.
Conclusion
While the implementation of SPS technology presents several challenges, these can be effectively managed with the right strategies and investments. By addressing the high costs, operational complexities, and training requirements, organizations can unlock the full potential of SPS, leading to significant advancements in material science and manufacturing.
Future Trends in Spark Plasma Sintering
Spark Plasma Sintering (SPS) technology, known for its rapid sintering capabilities at relatively low temperatures, continues to evolve, offering significant advancements in efficiency, scalability, and application diversity. As the demand for new materials and efficient manufacturing processes grows, SPS stands at the forefront of technological innovation in material science.
Efficiency Improvements
One of the primary areas of focus in SPS technology is enhancing its efficiency. Traditional sintering methods can be time-consuming and energy-intensive, whereas SPS significantly reduces both processing time and energy consumption. Future developments aim to further optimize these aspects by refining the pulse current techniques and improving the control systems of SPS devices. For instance, advancements in power supply and control systems could enable more precise temperature and pressure control, leading to more efficient sintering processes.
Scalability Enhancements
Scalability is another critical aspect of SPS technology. Currently, SPS is predominantly used in laboratory settings and small-scale production. However, to meet industrial demands, future SPS systems will need to handle larger volumes and more complex shapes. Researchers are exploring new mold materials and designs that can withstand higher pressures and temperatures, ensuring the integrity and reusability of the molds. Additionally, the integration of advanced robotics and automation in SPS equipment could facilitate the production of larger and more intricate parts, making SPS a viable option for high-volume manufacturing.
Expansion into New Material Types and Industries
SPS technology has traditionally been used for sintering metals and ceramics. However, its unique capabilities offer potential for expanding into new material types and industries. Future research is likely to focus on applying SPS to a broader range of materials, including polymers, composites, and nanomaterials. This expansion could open up new applications in sectors such as electronics, aerospace, and biomedical engineering, where the precise control of material properties is crucial.
Environmental and Economic Benefits
The environmental and economic benefits of SPS are also driving its future development. SPS's energy-efficient and low-waste production process aligns with global sustainability goals. As industries increasingly seek eco-friendly manufacturing solutions, SPS could become a preferred method for producing high-performance materials. Moreover, the reduced processing times and lower energy costs associated with SPS can lead to significant economic savings, making it an attractive option for manufacturers.
Technological Integration and Collaboration
Finally, the future of SPS technology will likely involve greater integration with other advanced manufacturing technologies and collaborative efforts across different fields. For example, combining SPS with additive manufacturing techniques could lead to the creation of hybrid manufacturing processes that leverage the strengths of both technologies. Additionally, interdisciplinary research involving materials science, electrical engineering, and mechanical engineering could lead to breakthroughs in understanding and optimizing the SPS process.
In conclusion, the future of Spark Plasma Sintering is promising, with potential advancements poised to make it a more efficient, scalable, and versatile technology. As research and development continue, SPS could revolutionize the way we produce advanced materials, contributing to innovations across various industries and promoting sustainable manufacturing practices.
Conclusion: The Role of SPS in Shaping Material Science
In conclusion, the Spark Plasma Sintering (SPS) technique stands out as a transformative technology in the field of material science. Its ability to rapidly sinter materials at fine-grain levels, coupled with its efficiency and versatility, positions SPS as a cornerstone in modern material processing. As we look to the future, SPS is poised to drive significant innovations, expanding its applications across various industries and paving the way for the development of advanced, high-performance materials. The continued evolution and adoption of SPS technology will undoubtedly shape the future of material science, offering new possibilities and solutions to complex material challenges.
CONTACT US FOR A FREE CONSULTATION
KINTEK LAB SOLUTION's products and services have been recognized by customers around the world. Our staff will be happy to assist with any inquiry you might have. Contact us for a free consultation and talk to a product specialist to find the most suitable solution for your application needs!