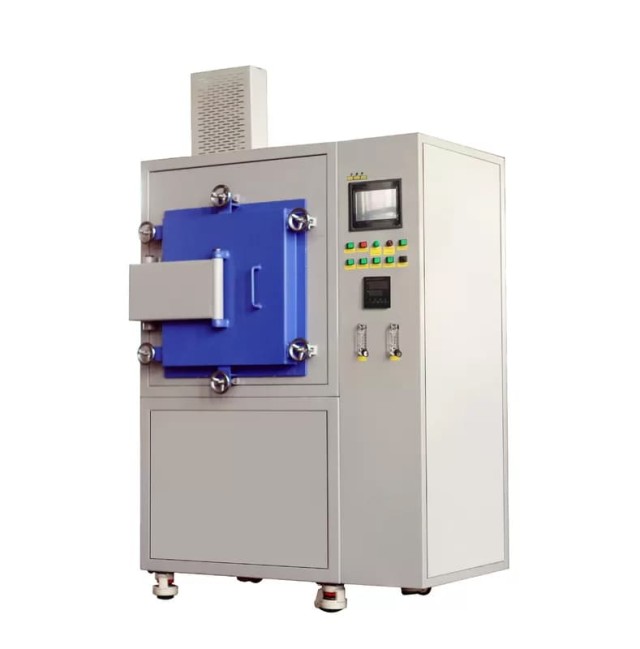
Atmosphere Furnace
Controlled Nitrogen Inert Hydrogen Atmosphere Furnace
Item Number : KT-16AH
Price varies based on specs and customizations
- Max. temperature
- 1600 ℃
- Constant work temperature
- 1500 ℃
- Vacuum pressure
- 0.1 Mpa
- Effective volume
- 4.5-64 L
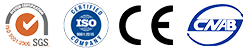
Shipping:
Contact us to get shipping details Enjoy On-time Dispatch Guarantee.
Why Choose Us
Reliable PartnerEasy ordering process, quality products, and dedicated support for your business success.
Introduction
The Hydrogen Atmosphere Furnace is a specialized heating device designed for sintering or annealing materials in a controlled hydrogen or inert gas environment, adjustable up to 1600°C. It features a double-shell structure with air and water cooling systems, high-purity molybdenum wire heating elements, and advanced safety mechanisms including automatic hydrogen tail gas ignition and pressure control systems. Ideal for processing materials like optical materials and titanium alloys, this furnace ensures precise and safe operation in reducing or inert gas atmospheres.
Applications
The Hydrogen Atmosphere Furnace is a specialized equipment designed for various high-temperature processes that require a controlled environment, particularly in the presence of hydrogen or inert gases. This furnace is ideal for applications where the prevention of oxidation or other chemical reactions is crucial, ensuring the integrity and quality of the materials being processed. Below are the main application areas of this product:
- Sintering of Advanced Materials: Ideal for the consolidation of powders into solid materials, especially for high-performance ceramics and metals that require a specific atmosphere to prevent oxidation.
- Annealing Processes: Used for the controlled heating and cooling of materials, particularly metals, to remove internal stresses, soften materials, or alter electrical properties.
- Heat Treatment of Titanium Alloys: Essential for the thermal processing of titanium and its alloys in a controlled hydrogen or inert gas environment to enhance mechanical properties and prevent surface contamination.
- Processing of Optical Materials: Particularly useful for the sintering and annealing of optical materials like phosphors and other luminescent materials that require a clean, controlled atmosphere to maintain optical clarity and performance.
- Research and Development: Widely used in laboratories and research facilities for experiments involving high-temperature reactions in controlled atmospheres, aiding in the development of new materials and processes.
- Manufacturing of Electronic Components: Critical for the production of semiconductors and other electronic components that require precise temperature control and a clean environment to ensure high performance and reliability.
Detail & Parts
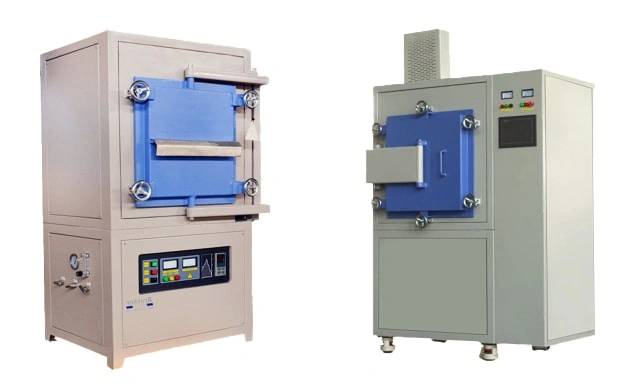
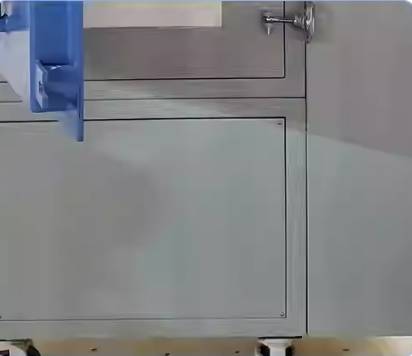
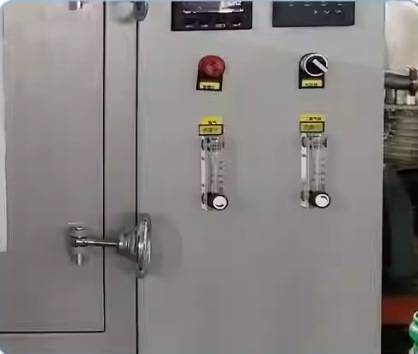
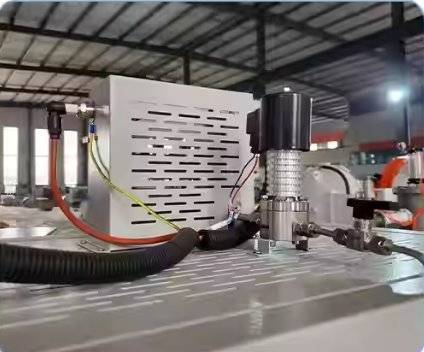
Features
The Hydrogen Atmosphere Furnace is a specialized heating device designed to provide precise control over the environment during sintering or annealing processes. This furnace is particularly beneficial for materials that require processing in a hydrogen or inert gas environment, such as optical materials and titanium alloys. Here are the key features that enhance its functionality and safety:
- Double-Shell Structure with Advanced Cooling Systems: The furnace features a double-layer shell design that incorporates both air and water cooling systems. This setup ensures a stable internal pressure ranging from 0.02MPa positive to -0.1MPa negative, maintaining optimal conditions for the materials being processed.
- High Precision Flow Meters: Equipped with two large-range flow meters for nitrogen and hydrogen (each ranging from 0 to 3.5L/min), the furnace allows for precise control over the gas flow rates. This feature is crucial for maintaining the desired atmosphere composition and ensuring consistent results.
- Comprehensive Hydrogen Safety Mechanism: Safety is paramount in environments involving hydrogen. The furnace includes a hydrogen safety device that automatically ignites hydrogen tail gas. In case of ignition failure, the system is designed to cut off the hydrogen supply, open the nitrogen valve, and force nitrogen into the furnace, thereby preventing any hazardous situations.
- High Purity Molybdenum Heating Element: Utilizing a high purity molybdenum wire (99.99% molybdenum content), the heating element ensures uniform and efficient heating, which is essential for achieving high-quality sintering and annealing results.
- Temperature Flexibility: With an adjustable working temperature range from 0 to 1600°C, this furnace accommodates a wide variety of materials and processes, making it a versatile tool in the laboratory or industrial setting.
Principle
Hydrogen atmosphere furnaces utilize a ceramic tube with leak-tight flanges to enable heat treatment up to 1600 °C in a hydrogen atmosphere. Prior to introducing hydrogen gas, the tube is flooded with inert gas for safety. The flooding tank system, pressurized with inert gas, purges remaining oxygen from the tube before heat treatment. The gas outlet system connects to an afterburner to combust outgoing hydrogen. Exothermic hydrogen atmospheres reduce surface oxides, improving the wetting properties and flow of filler material during brazing.
Advantages
Hydrogen Atmosphere Furnaces offer a range of benefits that make them a superior choice for high-temperature processes. Here are some of the key advantages:
- Enhanced Oxygen Exclusion: The pressurized environment of the furnace ensures that oxygen cannot enter under any circumstances, providing a completely controlled atmosphere for sensitive processes.
- Maximized Reductive Power: With more reactive hydrogen molecules available compared to partial pressure atmospheres, these furnaces maximize the reductive power, crucial for processes requiring a strong reducing environment.
- Versatility with Hydrogen Mixtures: The ability to use mixtures of inert gases like nitrogen or argon with hydrogen offers a valuable alternative. These mixtures retain some of the reducing capabilities of pure hydrogen atmospheres while potentially reducing operating and investment costs.
- Advanced Safety Features: Equipped with a fully automated flow controller and devices adhering to SIL2 standards, the system ensures safety and reliability. A hydrogen sensor at the top of the furnace immediately responds to any leaks, triggering a switch to inert gas and securing the system.
- User-Friendly Interface: The intuitive touch panel interface simplifies operation and control, making it accessible for users of varying technical backgrounds.
- Flexibility in Temperature and Space: These furnaces can be adapted to different usable spaces and temperatures, with options like cold wall furnaces available for requirements exceeding 1800 °C.
- Sealing Efficiency: The inclusion of a high-temperature-resistant silica gel seal ring on the furnace door ensures excellent sealing, allowing for the creation of a vacuum and various other atmospheres, enhancing the versatility of the furnace.
Technical specifications
Furnace model | KT-16AH | ||
---|---|---|---|
Max. temperature | 1600℃ | ||
Constant work temperature | 1500℃ | ||
Vacuum pressure | 0.1Mpa | ||
Vacuum valve | Needle valve | ||
Chamber material | Japan alumina fiber | ||
Heating element | Molybdenum wire | ||
Heating rate | 0-20℃/min | ||
Temperature sensor | B type thermal couple | ||
Temperature controller | Touch screen PID controller | ||
Temperature control accuracy | ±1℃ | ||
Temperature uniformity | ±5℃ | ||
Electric power supply | AC110-220V,50/60HZ | ||
Standard Chamber Sizes Stocks | |||
Chamber size (mm) | Effective volume (L) | Chamber size (mm) | Effective volume (L) |
150x150x200 | 4.5 | 300x300x400 | 36 |
200x200x300 | 12 | 400x400x400 | 64 |
Customer design sizes and volume is accepted |
Standard Temperature controlling |
|
---|---|
Optional of Temperature controlling |
|
Furnace structure | Double layer steel casing with dual cooling fan, surface temperature below 60℃ |
Furnace door |
|
Warranty |
|
Hydrogen Furnace Using Attentions |
|
Warnings
Operator safety is the top important issue! Please operate the equipment with cautions. Working with inflammable& explosive or toxic gases is very dangerous, operators must take all necessary precautions before starting the equipment. Working with positive pressure inside the reactors or chambers is dangerous, operator must fellow the safety procedures strictly. Extra caution must also be taken when operating with air-reactive materials, especially under vacuum. A leak can draw air into the apparatus and cause a violent reaction to occur.
Designed for You
KinTek provide deep custom made service and equipment to worldwide customers, our specialized teamwork and rich experienced engineers are capable to undertake the custom tailoring hardware and software equipment requirements, and help our customer to build up the exclusive and personalized equipment and solution!
Would you please drop your ideas to us, our engineers are ready for you now!
4.8
out of
5
I'm very satisfied with this Hydrogen atmosphere furnace. It's a high-quality product with a reasonable price. The delivery was fast and the customer service was excellent.
4.9
out of
5
This furnace is a lifesaver for our lab. It's easy to use and maintain, and it provides consistent results. We've been using it for over a year now and it's still going strong.
4.7
out of
5
I highly recommend this Hydrogen atmosphere furnace. It's a great value for the money and it's made with high-quality materials. We've been using it for several months now and we've had no problems with it.
5.0
out of
5
This furnace is a game-changer for our lab. It's so easy to use and it produces consistent results. We've been using it for a few months now and we're very happy with it.
4.6
out of
5
I'm really impressed with this Hydrogen atmosphere furnace. It's well-made and it works great. I've been using it for a few weeks now and I've had no problems with it.
4.9
out of
5
This furnace is a great addition to our lab. It's easy to use and it provides consistent results. We've been using it for a few months now and we're very happy with it.
5.0
out of
5
I'm so glad I bought this Hydrogen atmosphere furnace. It's made my work so much easier. It's easy to use and it produces consistent results. I highly recommend it.
4.8
out of
5
This furnace is a great value for the money. It's well-made and it works great. I've been using it for a few months now and I've had no problems with it.
4.7
out of
5
I'm very happy with this Hydrogen atmosphere furnace. It's a great product and it's made my work so much easier. I highly recommend it.
4.6
out of
5
This furnace is a great addition to our lab. It's easy to use and it provides consistent results. We've been using it for a few months now and we're very happy with it.
5.0
out of
5
I'm so glad I bought this Hydrogen atmosphere furnace. It's made my work so much easier. It's easy to use and it produces consistent results. I highly recommend it.
Products
Controlled Nitrogen Inert Hydrogen Atmosphere Furnace
REQUEST A QUOTE
Our professional team will reply to you within one business day. Please feel free to contact us!
Related Products
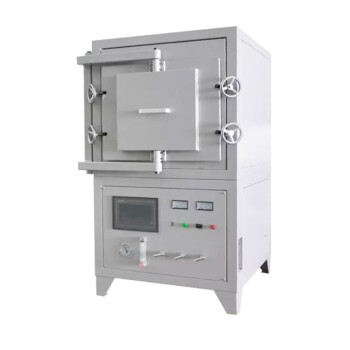
1200℃ Controlled Atmosphere Furnace Nitrogen Inert Atmosphere Furnace
Discover our KT-12A Pro Controlled atmosphere furnace - high precision, heavy duty vacuum chamber, versatile smart touch screen controller, and excellent temperature uniformity up to 1200C. Ideal for both laboratory and industrial application.
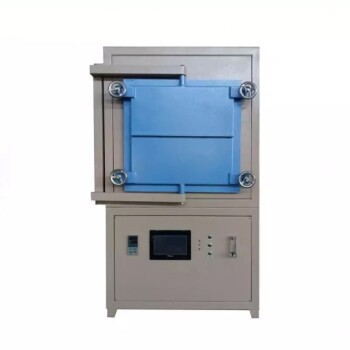
1400℃ Controlled Atmosphere Furnace with Nitrogen and Inert Atmosphere
Achieve precise heat treatment with KT-14A controlled atmosphere furnace. Vacuum sealed with a smart controller, it's ideal for lab and industrial use up to 1400℃.
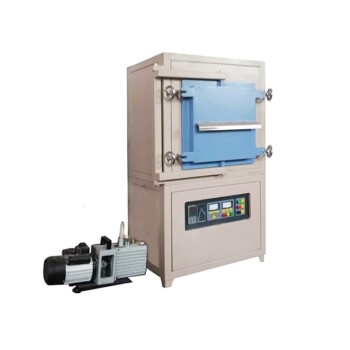
1700℃ Controlled Atmosphere Furnace Nitrogen Inert Atmosphere Furnace
KT-17A Controlled atmosphere furnace: 1700℃ heating, vacuum sealing technology, PID temperature control, and versatile TFT smart touch screen controller for laboratory and industrial use.
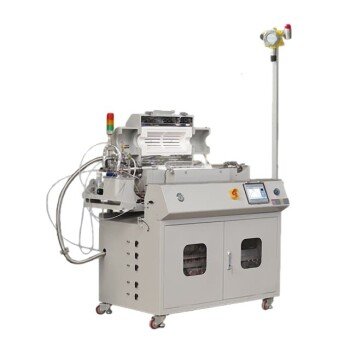
Customer Made Versatile CVD Tube Furnace Chemical Vapor Deposition Chamber System Equipment
Get your exclusive CVD furnace with KT-CTF16 Customer Made Versatile Furnace. Customizable sliding, rotating, and tilting functions for precise reactions. Order now!
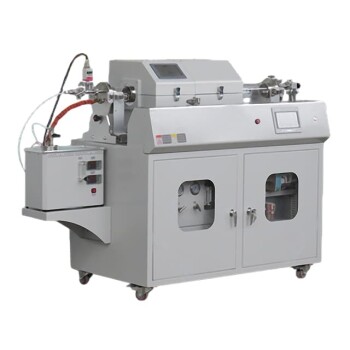
KT-PE12 Slide PECVD System: Wide power range, programmable temp control, fast heating/cooling with sliding system, MFC mass flow control & vacuum pump.
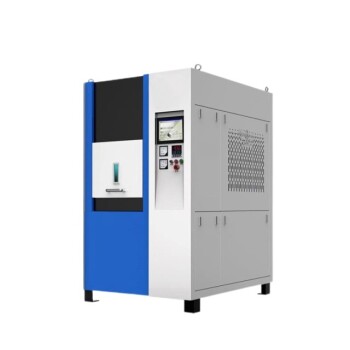
Spark Plasma Sintering Furnace SPS Furnace
Discover the benefits of Spark Plasma Sintering Furnaces for rapid, low-temperature material preparation. Uniform heating, low cost & eco-friendly.
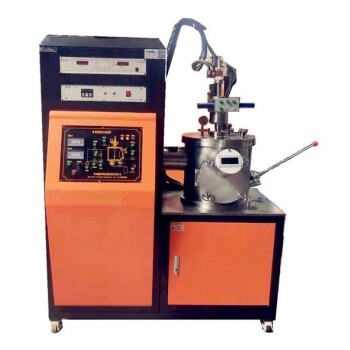
Non Consumable Vacuum Arc Induction Melting Furnace
Explore the benefits of Non-Consumable Vacuum Arc Furnace with high melting point electrodes. Small, easy to operate & eco-friendly. Ideal for laboratory research on refractory metals & carbides.
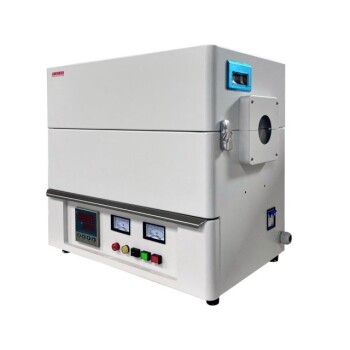
1200℃ Split Tube Furnace with Quartz Tube Laboratory Tubular Furnace
KT-TF12 split tube furnace: high-purity insulation, embedded heating wire coils, and max. 1200C. Widely used for new materials and chemical vapour deposition.
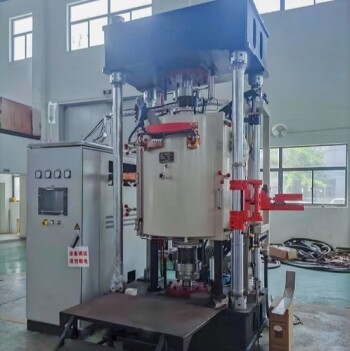
Vacuum Heat Treat and Pressure Sintering Furnace for High Temperature Applications
Vacuum pressure sintering furnaces are designed for high temperature hot pressing applications in metal and ceramic sintering. Its advanced features ensure precise temperature control, reliable pressure maintenance, and a robust design for seamless operation.
Related Articles
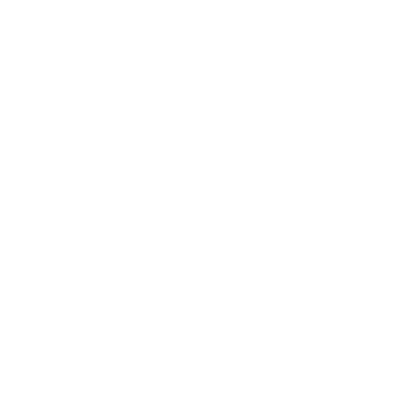
Atmosphere Furnaces: Comprehensive Guide to Controlled Heat Treatment
Explore the advanced world of atmosphere furnaces with our detailed guide. Learn about their operation, applications, and benefits in various industries. Perfect for those seeking in-depth knowledge on controlled heat treatment.
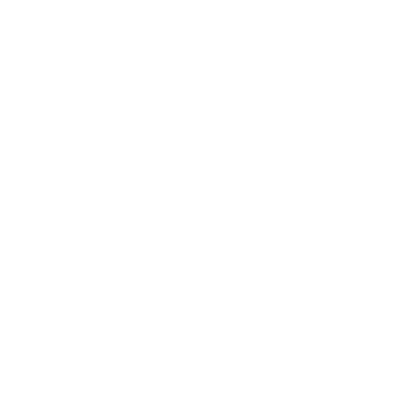
Comprehensive Guide to Atmosphere Furnaces: Types, Applications, and Benefits
Explore the world of atmosphere furnaces with our detailed guide. Learn about their types, applications in metallurgy and beyond, and the benefits they offer for precise material heat treatment.
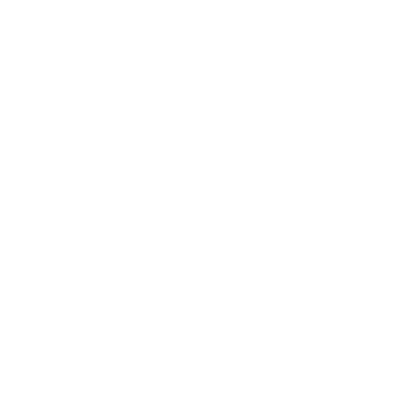
Hydrogen Atmosphere Furnaces: Applications, Safety, and Maintenance
Explore the comprehensive guide on hydrogen atmosphere furnaces, including their applications in high-end alloy sintering, safety measures, and maintenance tips. Learn about the types, components, and operational considerations for optimal performance.
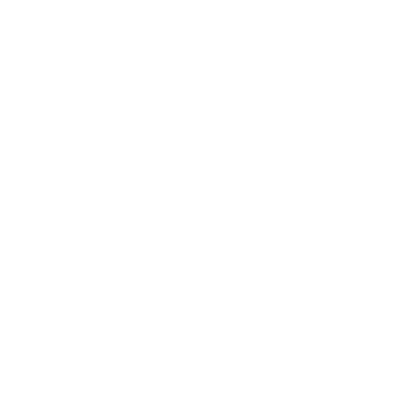
The Benefits of Controlled Atmosphere Furnaces for Sintering and Annealing Processes
They are essential in preventing oxidation, reducing the risk of contamination, and improving the properties of the materials being treated.
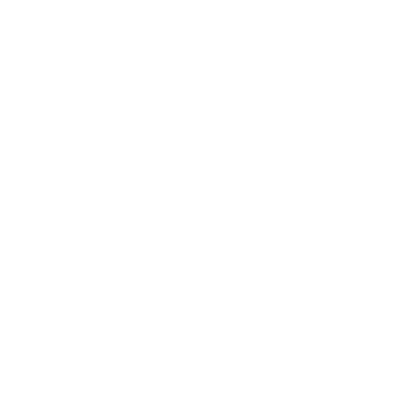
Controlled Atmosphere Furnace: Comprehensive Guide to Advanced Heat Treatment
Explore the advanced features and applications of controlled atmosphere furnaces in heat treatment processes. Learn about key components, operational techniques, and benefits for precise material processing.
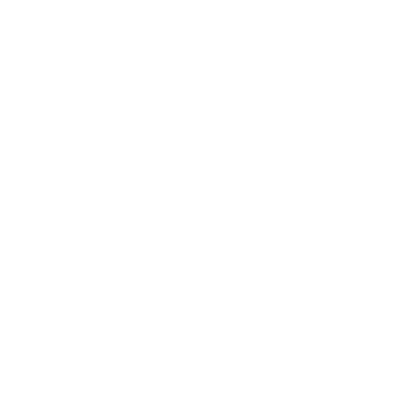
guide to UNIVERSAL TUBE FURNACES
The maximum temperature in a tube furnace can vary depending on the specific model and the materials used in its construction. In general, tube furnaces are designed to operate at high temperatures, with some models capable of reaching temperatures as high as 2600°C.
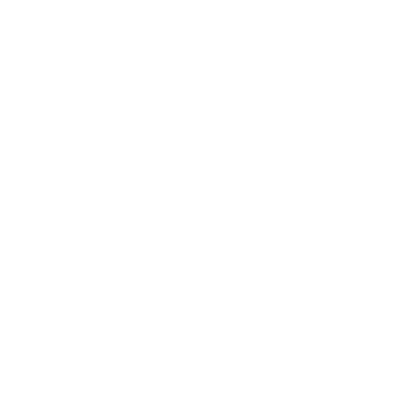
Introducing the Lab Vacuum Tube Furnaces
A vacuum tube furnace is a type of furnace that uses vacuum to isolate the process atmosphere from the external atmosphere.
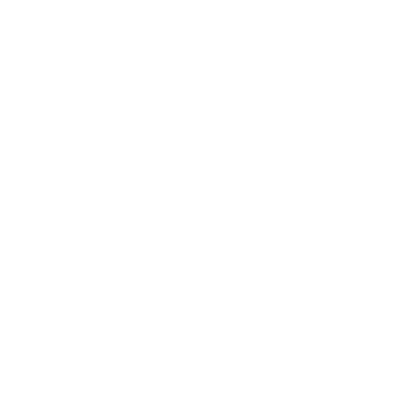
Comparing Laboratory Furnace Features and Specifications: A Guide
A laboratory furnace is a specialized heating equipment that is used in laboratories and research facilities to heat materials to high temperatures.
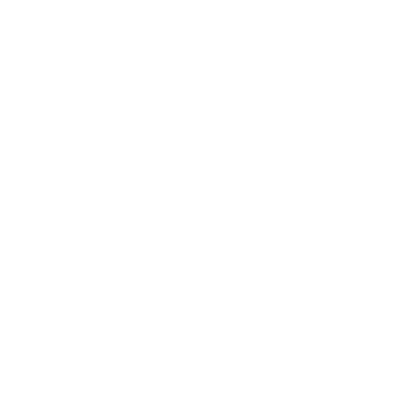
Muffle Furnace: Unraveling the Secrets of Uniform Heating and Controlled Atmosphere
Discover the intricacies of a muffle furnace, an indispensable tool for material processing and analysis. Learn about its working principle, applications, types, features, and benefits, empowering you to make informed decisions for your laboratory or industrial needs.
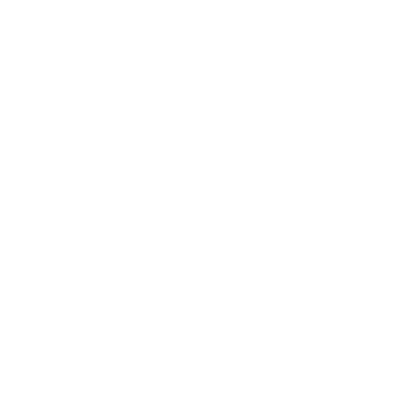
How Controlled Atmosphere Furnaces Improve Quality and Consistency in Heat Treatment
Controlled atmosphere furnaces play a vital role in heat treatment processes.
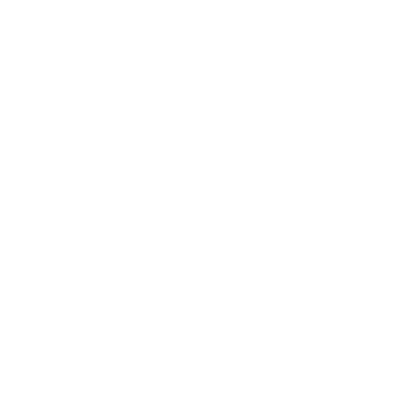
Exploring the Using a Chamber Furnace for Industrial and Laboratory Applications
A laboratory chamber furnace is a type of heating equipment that is specifically designed for use in a laboratory setting. It is typically used for applications that require precise temperature control and uniformity, such as ashing or heat treatment of materials.
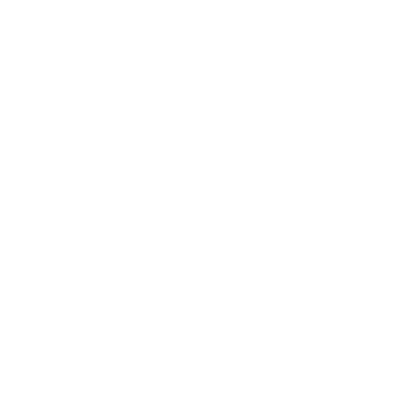
Exploring the Key Characteristics of Tube Heating Furnaces
A tube heating furnace is a specialized type of industrial furnace that is used in various industries to heat substances through the use of fuel combustion.