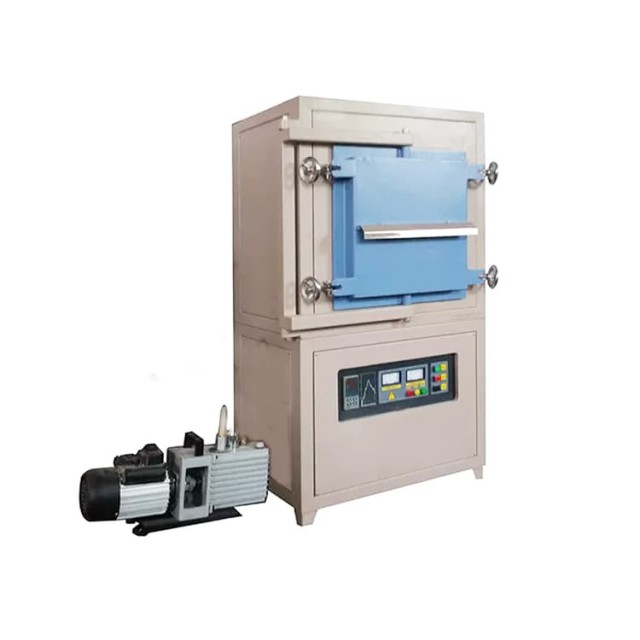
Atmosphere Furnace
1700℃ Controlled Atmosphere Furnace Nitrogen Inert Atmosphere Furnace
Item Number : KT-17A
Price varies based on specs and customizations
- Max. temperature
- 1700 ℃
- Constant work temperature
- 1600 ℃
- Vacuum pressure
- 0.1 Mpa
- Heating rate
- 0-20 ℃/min
- Effective volume
- 1-512 L
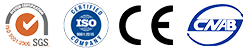
Shipping:
Contact us to get shipping details Enjoy On-time Dispatch Guarantee.
Why Choose Us
Reliable PartnerEasy ordering process, quality products, and dedicated support for your business success.
Introduction
The KT-17A Controlled Atmosphere Furnace is a versatile furnace designed for both laboratory and industrial applications. It features a heavy-duty vacuum chamber structure and scientific united control panel for vacuum suction and inert gas pressure and flow. The double furnace shell design with forced air flow cooling controls the furnace surface temperature, while the PID programmable temperature control ensures excellent control accuracy. The furnace is equipped with a ceramic polycrystalline fiber insulation liner for less heat loss and superior energy-saving efficiency. Professional heating elements optimize heat radiation properties and ensure a long service life. The safety interlock system automatically shuts off power when the furnace door is open, the temperature is too high, or a sensor is broken. The KT-17A Pro model features a 7-inch TFT smart touch screen controller for friendly program setting and history data analysis.
Applications
The Controlled Atmosphere Furnace is a versatile and efficient tool designed for various high-temperature processes requiring precise atmosphere control. This furnace, equipped with advanced features such as temperature controller and a polycrystalline alumina fibre chamber, is ideal for applications in industrial settings, scientific research institutes, and universities. Its ability to pre-vacuum and handle gases like H2, Ar, N2, O2, CO, and NH3 makes it suitable for a range of specialized processes.
- Atmosphere Protection Sintering: Ideal for sintering materials under controlled atmospheres to prevent oxidation and enhance material properties.
- Atmosphere Reducing Processes: Used in processes that require a reduction in the presence of oxygen, such as in the production of certain alloys or ceramics.
- Material Research and Development: Essential for researchers studying the effects of controlled atmospheres on material properties and behaviors.
- Small Batch Production: Particularly useful in the production of semiconductors, silicon nitride, and other sensitive materials where atmosphere control is critical.
- Educational Purposes: Provides hands-on experience for students in materials science and engineering, demonstrating the practical aspects of controlled atmosphere furnaces.
Principle
KT-17A Controlled Atmosphere Furnace employs an airtight vacuum-sealed heating chamber. The insulation chamber and heating element reside within a robust vacuum chamber, akin to a vacuum glove box. An operator utilizes a vacuum pump to evacuate the chamber to a negative pressure of -0.1Mpa. Subsequently, inert gas is introduced to establish a controlled atmosphere environment. The furnace incorporates vacuum pressure gauges, vacuum suction ports with valves, gas purging ports with valves, and float flowmeters, making it suitable for both laboratory and industrial applications.
Detail & Parts
Features
The Controlled Atmosphere Muffle Furnace is a sophisticated piece of equipment designed for advanced heat treatment processes in industrial and research settings. This furnace offers a range of features that not only enhance its functionality but also ensure efficient and safe operation. Key benefits include precise temperature control, rapid heating and cooling capabilities, and the ability to handle various atmospheres, making it ideal for sintering and reducing processes under controlled conditions.
- Double Layer Housing and Wind Cooling System: The furnace features a double-layer housing with a wind cooling system, facilitating rapid heating and cooling. This design not only improves efficiency but also maintains low surface temperatures, ensuring safety during operation.
- Sealed Housing and Atmosphere Control: With a sealed housing, silicon gel sealed cover, and a door equipped with a silicon gel gasket, the furnace maintains a tight seal, crucial for controlled atmosphere processes. The inclusion of a water cooling system and gas flow management through flow meters ensures precise control over the atmosphere inside the chamber.
- Versatile Atmosphere Handling: The furnace is capable of pre-vacuuming and handling a variety of gases including H2, Ar, N2, O2, CO, and NH3. Multiple gas inlets and outlets, along with a burning mouth, allow for complex atmosphere manipulations, essential for advanced materials processing.
- Advanced Insulation and Heating Elements: Utilizing Kantal resistance wire heating elements and polycrystalline alumina fibre chamber, the furnace ensures optimal temperature uniformity and energy efficiency. This setup supports high-temperature applications up to 1700°C, making it suitable for a wide range of industrial and research applications.
Advantages
The Controlled Atmosphere Furnace offers a range of benefits that make it a superior choice for various applications in industries and research settings. Key advantages include:
- Uniform Temperature Field: The furnace ensures a consistent temperature distribution throughout the chamber, which is crucial for precise and uniform heat treatment processes. This feature is particularly beneficial for sintering and reducing atmospheres where temperature uniformity is critical.
- Low Surface Temperature: Despite operating at high temperatures, the exterior of the furnace remains relatively cool, enhancing safety and reducing the risk of burns or accidental fires. This is achieved through a double-layer housing design with a wind cooling system.
- Rapid Heating and Cooling: The integrated wind cooling system and high-quality heating elements allow for quick adjustments in temperature, optimizing the efficiency of the sintering process and reducing downtime between operations.
- Advanced Temperature Control: Equipped with a Shimaden FP93 controller, the furnace supports 40 programmable segments, providing precise control over the heating process. This advanced control system allows for complex, segmented heating profiles tailored to specific material requirements.
- Versatile Atmosphere Control: The furnace is designed to handle multiple gases including H2, Ar, N2, O2, CO, and NH3, and can be pre-vacuumed to minimize oxygen content. This versatility enables it to support a wide range of heat treatment processes in inert, reducing, or oxidizing atmospheres.
- Sealed and Safe Design: Features such as a silicon gel sealed cover, sealed door with a silicon gel gasket, and a water cooling system ensure that the furnace maintains a tight seal, preventing atmosphere leakage and ensuring the integrity of the heat treatment process.
- Durable and High-Quality Materials: The chamber is constructed from polycrystalline alumina fibre, which is resistant to high temperatures and thermal shock, ensuring longevity and reliability of the furnace.
Safety Advantage
- Kindle Tech controlled atmosphere furnace owns over current protection, over temperature alarming function, furnace will turn off the power automatically
- Furnace build in thermal couple detecting function, furnace will stop heating and alarm will be on once broken or failure detected
- KT-12M Pro support power failure restarting function,furnace will resume the furnace heating program when power is incoming after failure
Technical specifications
Furnace model | KT-17A | ||
---|---|---|---|
Max. temperature | 1700℃ | ||
Constant work temperature | 1600℃ | ||
Vacuum pressure | 0.1Mpa | ||
Vacuum valve | Needle valve | ||
Chamber material | Japan alumina fiber | ||
Heating element | Molybdenum Disilicide | ||
Heating rate | 0-20℃/min | ||
Temperature sensor | B type thermal couple | ||
Temperature controller | Digital PID controller/Touch screen PID controller | ||
Temperature control accuracy | ±1℃ | ||
Temperature uniformity | ±5℃ | ||
Electric power supply | AC110-220V,50/60HZ | ||
Standard Chamber Sizes Stocks | |||
Chamber size (mm) | Effective volume (L) | Chamber size (mm) | Effective volume (L) |
100x100x100 | 1 | 300x300x400 | 36 |
120x120x130 | 2 | 400x400x400 | 64 |
150x150x200 | 4.5 | 500x500x500 | 125 |
200x200x200 | 8 | 600x600x600 | 216 |
200x200x300 | 12 | 800x800x800 | 512 |
Customer design sizes and volume is accepted |
Standard Package
No. | Description | Quantity |
---|---|---|
1 | Furnace | 1 |
2 | Thermal block | 1 |
3 | Crucible tong | 1 |
4 | Heat resistant glove | 1 |
5 | Operation manual | 1 |
Optional Setup
- Independent furnace temperature monitoring and recording
- RS 485 communication port for PC remote control and data exporting
- Insert gases port,exhaust output port,observation window port
- Touch screen temperature controller with versatile operator friendly functions
Warnings
Operator safety is the top important issue! Please operate the equipment with cautions. Working with inflammable& explosive or toxic gases is very dangerous, operators must take all necessary precautions before starting the equipment. Working with positive pressure inside the reactors or chambers is dangerous, operator must fellow the safety procedures strictly. Extra caution must also be taken when operating with air-reactive materials, especially under vacuum. A leak can draw air into the apparatus and cause a violent reaction to occur.
Designed for You
KinTek provide deep custom made service and equipment to worldwide customers, our specialized teamwork and rich experienced engineers are capable to undertake the custom tailoring hardware and software equipment requirements, and help our customer to build up the exclusive and personalized equipment and solution!
Would you please drop your ideas to us, our engineers are ready for you now!
FAQ
What Is A Atmospheric Furnace?
What Is The Use Of Atmosphere Furnace?
How Does An Atmosphere Furnace Work?
What Are The Advantages Of Using Atmosphere Furnaces?
What Factors Should Be Considered When Selecting An Atmosphere Furnace?
5
out of
5
Exceeded expectations! This controlled atmosphere furnace is a lifesaver in our lab. Highly recommend!
4.8
out of
5
Great value for the price. Easy to use and maintain. Definitely worth the investment.
4.9
out of
5
Outstanding craftsmanship. The quality of this furnace is unmatched. Highly satisfied with my purchase.
4.7
out of
5
Fast shipping and well-packaged. Impressed with the durability and performance of this furnace.
4.8
out of
5
A game-changer for our lab. The technological advancements in this furnace have improved our efficiency tremendously.
5
out of
5
The accuracy and precision of this furnace are remarkable. A must-have for any laboratory.
4.9
out of
5
User-friendly interface and exceptional customer service. Highly recommend this product.
4.7
out of
5
This furnace has exceeded our expectations. The temperature uniformity is impressive.
5
out of
5
The controlled atmosphere feature is a lifesaver. It has improved the quality of our research significantly.
Products
1700℃ Controlled Atmosphere Furnace Nitrogen Inert Atmosphere Furnace
REQUEST A QUOTE
Our professional team will reply to you within one business day. Please feel free to contact us!
Related Products
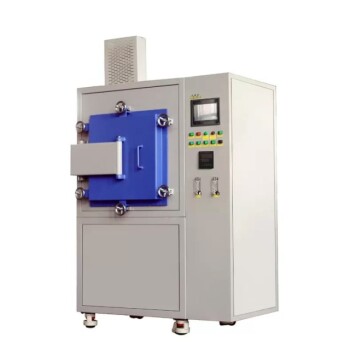
Controlled Nitrogen Inert Hydrogen Atmosphere Furnace
KT-AH Hydrogen atmosphere furnace - induction gas furnace for sintering/annealing with built-in safety features, dual housing design, and energy-saving efficiency. Ideal for lab and industrial use.
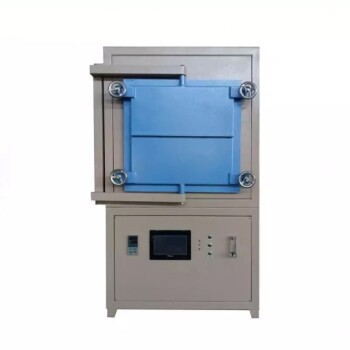
1400℃ Controlled Atmosphere Furnace with Nitrogen and Inert Atmosphere
Achieve precise heat treatment with KT-14A controlled atmosphere furnace. Vacuum sealed with a smart controller, it's ideal for lab and industrial use up to 1400℃.
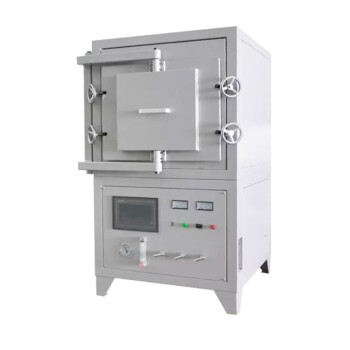
1200℃ Controlled Atmosphere Furnace Nitrogen Inert Atmosphere Furnace
Discover our KT-12A Pro Controlled atmosphere furnace - high precision, heavy duty vacuum chamber, versatile smart touch screen controller, and excellent temperature uniformity up to 1200C. Ideal for both laboratory and industrial application.
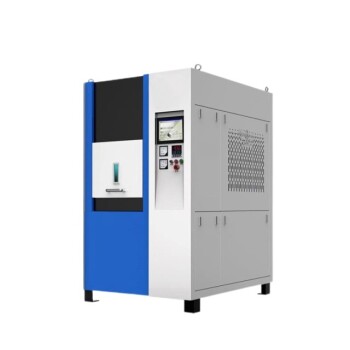
Spark Plasma Sintering Furnace SPS Furnace
Discover the benefits of Spark Plasma Sintering Furnaces for rapid, low-temperature material preparation. Uniform heating, low cost & eco-friendly.
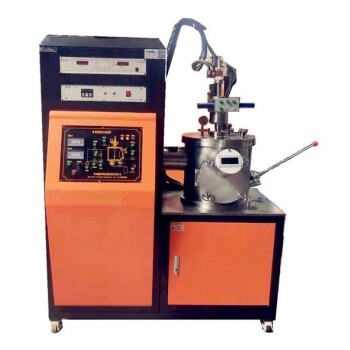
Non Consumable Vacuum Arc Induction Melting Furnace
Explore the benefits of Non-Consumable Vacuum Arc Furnace with high melting point electrodes. Small, easy to operate & eco-friendly. Ideal for laboratory research on refractory metals & carbides.
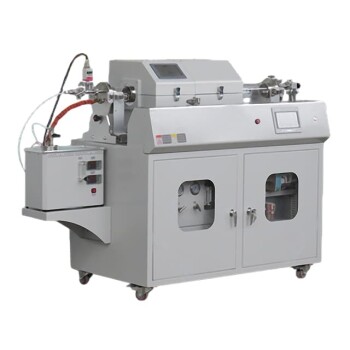
KT-PE12 Slide PECVD System: Wide power range, programmable temp control, fast heating/cooling with sliding system, MFC mass flow control & vacuum pump.
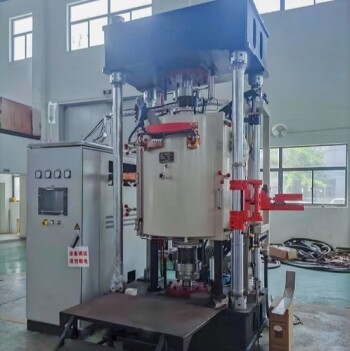
Vacuum Heat Treat and Pressure Sintering Furnace for High Temperature Applications
Vacuum pressure sintering furnaces are designed for high temperature hot pressing applications in metal and ceramic sintering. Its advanced features ensure precise temperature control, reliable pressure maintenance, and a robust design for seamless operation.
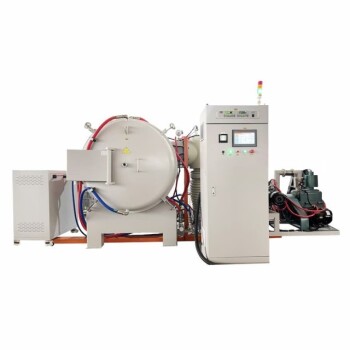
Molybdenum Vacuum Heat Treat Furnace
Discover the benefits of a high-configuration molybdenum vacuum furnace with heat shield insulation. Ideal for high-purity, vacuum environments like sapphire crystal growth and heat treatment.
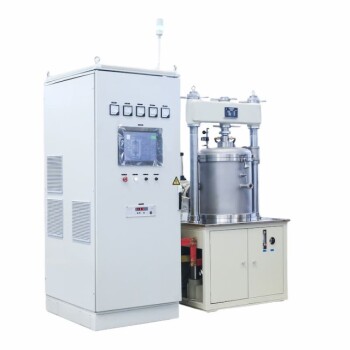
Vacuum Hot Press Furnace Machine Heated Vacuum Press
Discover the advantages of Vacuum Hot Press Furnace! Manufacture dense refractory metals & compounds, ceramics, and composites under high temp and pressure.
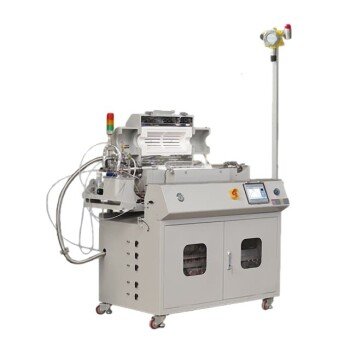
Customer Made Versatile CVD Tube Furnace Chemical Vapor Deposition Chamber System Equipment
Get your exclusive CVD furnace with KT-CTF16 Customer Made Versatile Furnace. Customizable sliding, rotating, and tilting functions for precise reactions. Order now!
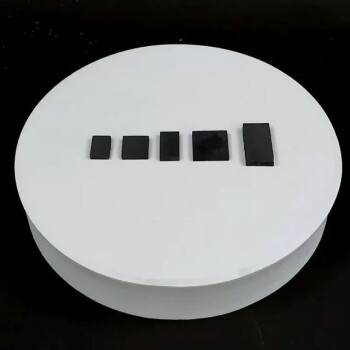
Glassy Carbon Sheet RVC for Electrochemical Experiments
Discover our Glassy Carbon Sheet - RVC. Perfect for your experiments, this high-quality material will elevate your research to the next level.
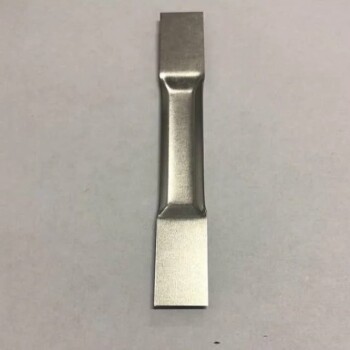
Molybdenum Tungsten Tantalum Evaporation Boat for High Temperature Applications
Evaporation boat sources are used in thermal evaporation systems and are suitable for depositing various metals, alloys and materials. Evaporation boat sources are available in different thicknesses of tungsten, tantalum and molybdenum to ensure compatibility with a variety of power sources. As a container, it is used for vacuum evaporation of materials. They can be used for thin film deposition of various materials, or designed to be compatible with techniques such as electron beam fabrication.
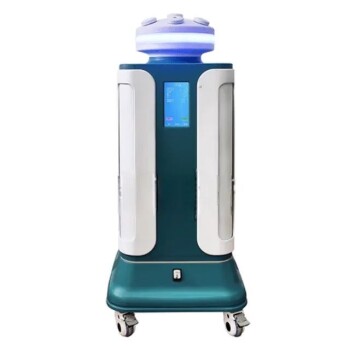
VHP Sterilization Equipment Hydrogen Peroxide H2O2 Space Sterilizer
A hydrogen peroxide space sterilizer is a device that uses vaporized hydrogen peroxide to decontaminate enclosed spaces. It kills microorganisms by damaging their cellular components and genetic material.
Related Articles
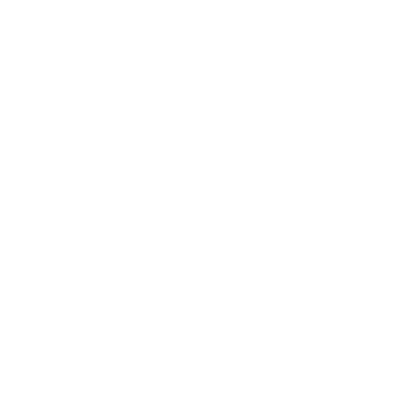
Controlled Atmosphere Furnace: Comprehensive Guide to Advanced Heat Treatment
Explore the advanced features and applications of controlled atmosphere furnaces in heat treatment processes. Learn about key components, operational techniques, and benefits for precise material processing.
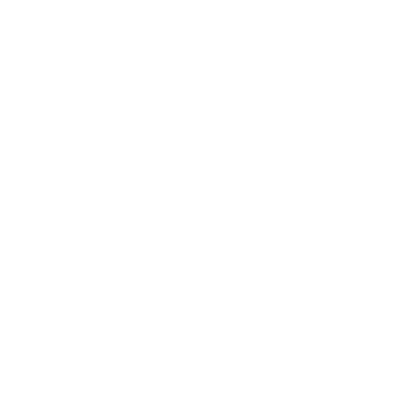
Hydrogen Atmosphere Furnaces: Applications, Safety, and Maintenance
Explore the comprehensive guide on hydrogen atmosphere furnaces, including their applications in high-end alloy sintering, safety measures, and maintenance tips. Learn about the types, components, and operational considerations for optimal performance.
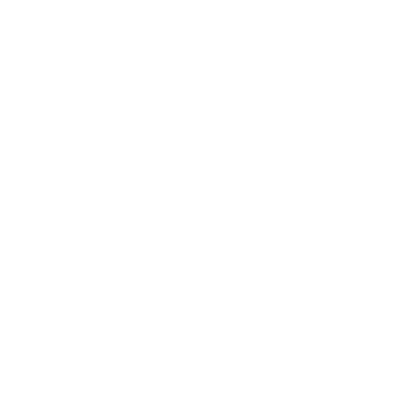
Comprehensive Guide to Atmosphere Furnaces: Types, Applications, and Benefits
Explore the world of atmosphere furnaces with our detailed guide. Learn about their types, applications in metallurgy and beyond, and the benefits they offer for precise material heat treatment.
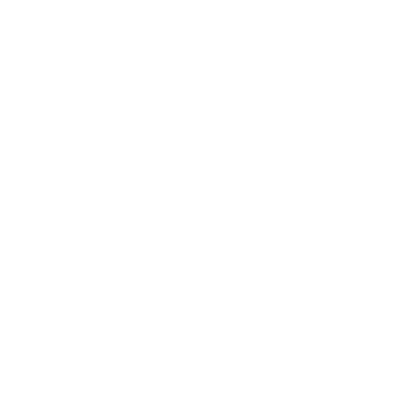
The Benefits of Controlled Atmosphere Furnaces for Sintering and Annealing Processes
They are essential in preventing oxidation, reducing the risk of contamination, and improving the properties of the materials being treated.
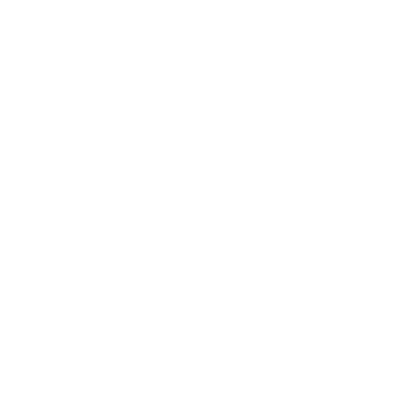
How Controlled Atmosphere Furnaces Improve Quality and Consistency in Heat Treatment
Controlled atmosphere furnaces play a vital role in heat treatment processes.
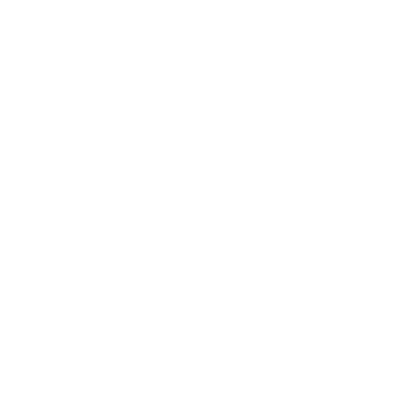
Atmosphere Furnaces: Comprehensive Guide to Controlled Heat Treatment
Explore the advanced world of atmosphere furnaces with our detailed guide. Learn about their operation, applications, and benefits in various industries. Perfect for those seeking in-depth knowledge on controlled heat treatment.
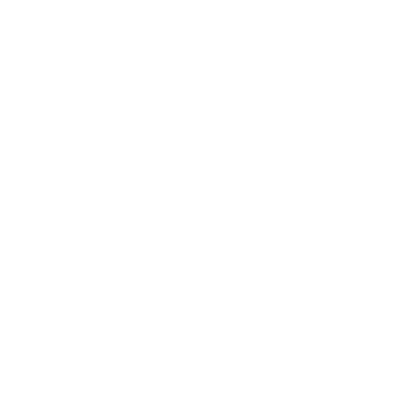
Muffle Furnace: Unraveling the Secrets of Uniform Heating and Controlled Atmosphere
Discover the intricacies of a muffle furnace, an indispensable tool for material processing and analysis. Learn about its working principle, applications, types, features, and benefits, empowering you to make informed decisions for your laboratory or industrial needs.
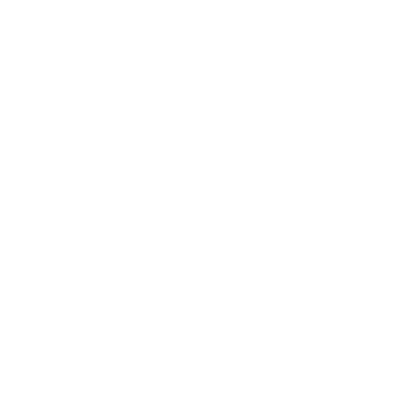
Exploring the Using a Chamber Furnace for Industrial and Laboratory Applications
A laboratory chamber furnace is a type of heating equipment that is specifically designed for use in a laboratory setting. It is typically used for applications that require precise temperature control and uniformity, such as ashing or heat treatment of materials.
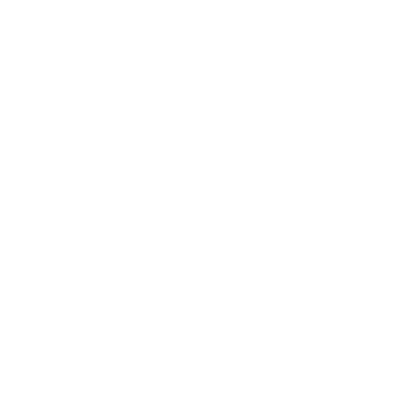
Inert Atmosphere Ovens for Research A Comprehensive Guide
Inert atmosphere ovens are designed to create a controlled environment that is free of oxygen and moisture.
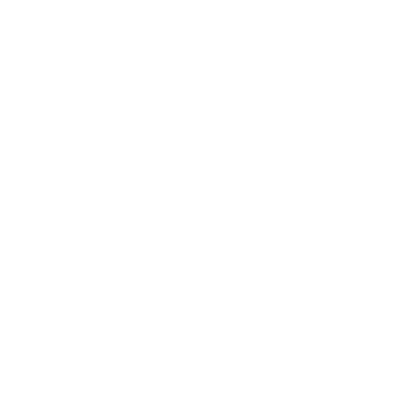
Exploring the Key Performance Indicators of an Atmosphere Furnace
Atmosphere furnaces are specialized pieces of equipment used in a variety of industries for applications such as heat treatment, ceramics, and metallurgy.
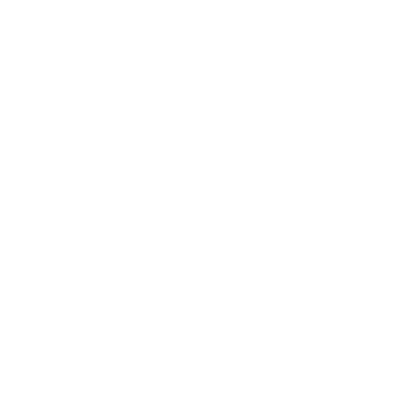
Comparing Laboratory Furnace Features and Specifications: A Guide
A laboratory furnace is a specialized heating equipment that is used in laboratories and research facilities to heat materials to high temperatures.
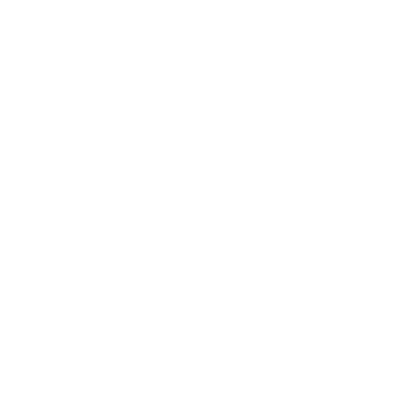
The Importance of Inert Atmosphere Gases in Furnace Atmospheres
Furnace atmospheres play an essential role in the heat treatment process of materials.