Introduction to Furnace Atmospheres
Furnace atmospheres play an essential role in the heat treatment process of materials. The atmosphere inside a furnace can significantly impact the final product's properties, such as strength and durability. An atmosphere is a gas or a mixture of gases surrounding the material being treated in a furnace. The most commonly used furnace atmospheres include air, nitrogen, hydrogen, and argon. Understanding the properties of each atmosphere and their effects on the material is crucial in producing high-quality products. The use of inert atmospheres, such as nitrogen and argon, is important in preventing unwanted reactions and oxidation during the heat treatment process.
Table of Contents
- Introduction to Furnace Atmospheres
- What is an Inert Atmosphere?
- Why is it important to use inert atmospheres?
- Common Gases in Furnace Atmospheres
- Heat Treatment Processes Requiring Inert Atmospheres
- How to Measure Furnace Atmosphere
- Tools for Measuring and Sampling
- Conclusion on the Importance of Inert Atmospheres
What is an Inert Atmosphere?
In laboratory work, it is essential to create a controlled environment for certain reactions or processes. One such environment is an inert atmosphere, which is characterized by the absence of reactive gases that could interfere with the desired outcome. Inert gases such as nitrogen, argon, and helium are commonly used to create this environment, which can be achieved through techniques such as purging, blanketing, or the use of glove boxes.
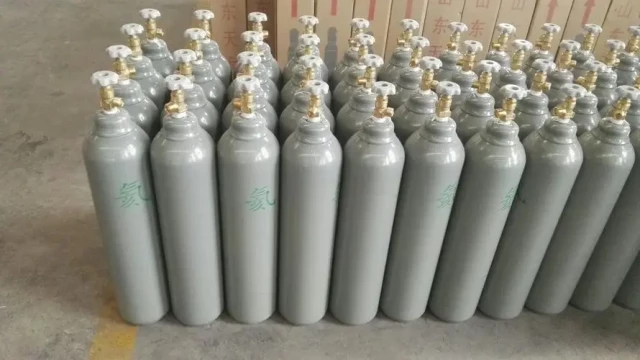
Inert Atmosphere Definition
An inert atmosphere is a controlled environment used for various laboratory and industrial applications, in which the atmosphere is free from reactive gases that could cause unwanted chemical reactions. Inert gases, such as nitrogen, argon, and helium, are commonly used to create such an environment. These gases are considered inert as they do not chemically react with other substances, making them ideal for creating a controlled environment.
Creating an Inert Atmosphere
There are several ways to create an inert atmosphere, including purging, blanketing, and the use of glove boxes. Purging involves removing all the air from a container or system and replacing it with an inert gas. Blanketing involves filling a container with an inert gas to create a layer of gas that prevents air or other reactive gases from entering. Glove boxes are enclosed workspaces that use an inert gas atmosphere to create a controlled environment.
Uses of Inert Atmospheres
Inert atmospheres are used in various laboratory and industrial applications, including heat treatment processes such as sintering, bright annealing, and carbonitriding. These processes require highly controlled atmospheres to produce quality parts for industries such as aerospace, automotive, and petrochemicals. Inert atmospheres are also used in the production of semiconductors, where purity is critical.
Common Inert Gases
The most commonly used inert gases for creating an inert atmosphere are nitrogen, argon, and helium. Nitrogen is the most affordable and widely used inert gas and is often used in applications where moisture and oxygen need to be removed. Argon is a denser gas and is commonly used in applications that require a more substantial inert gas barrier. Helium is the lightest inert gas and is used in applications where low density and high thermal conductivity are required.
In conclusion, an inert atmosphere is a controlled environment in which the atmosphere is free from reactive gases that could interfere with the desired outcome. This environment is crucial in laboratory and industrial applications where precision and control are essential. The use of inert atmosphere gases, such as nitrogen, argon, and helium, is critical in creating this environment and ensuring the quality, reliability, and reproducibility of laboratory experiments and industrial processes.
Why is it important to use inert atmospheres?
Inert atmosphere gases are essential for many heat treatment processes due to their ability to create a controlled environment that prevents undesirable chemical reactions, oxidation, and contamination of the product. In this section, we will discuss the reasons why it is important to use inert atmospheres in furnace atmospheres.
Preventing Undesirable Chemical Reactions
When working with heat treatment, sintering, or brazing, the presence of certain gases such as oxygen or water vapor can cause oxidation or other unwanted chemical reactions. Inert gases, such as nitrogen, argon, and helium, are used to displace the oxygen and water vapor from the furnace chamber, creating an atmosphere that is devoid of reactive gases. This ensures that the process is controlled and that the desired outcome is achieved.
Improving Product Quality
Using inert gases can increase the efficiency of the process by reducing the amount of energy required to achieve the desired temperature and by speeding up the cooling process. Additionally, the inert atmosphere helps to prevent oxidation and contamination of the product, resulting in a higher quality end result. This is especially important for industries such as aerospace, automotive, or petrochemical, where mission-critical parts are manufactured.
Achieving Precision and Repeatability
For heat treatment processes that require a highly controlled atmosphere, such as bright annealing, sintering, and carbonitriding, achieving precision and repeatability is essential. The furnaces used in these processes must support a controlled atmosphere in order to achieve successful, high precision, repeatable results for these parts. Inert atmospheres are used to ensure that the process is controlled, and that the desired outcome is achieved.
Reducing Furnace Damage and Employee Injuries
An improperly controlled atmosphere could lead to a damaged furnace or, worse yet, injured employees. Inert gases are used to prevent chemical reactions on the surface of a part that would compromise its quality and performance, leading to rejected parts. This, in turn, leads to financial loss, wasted time, and potentially dangerous repercussions for those using the part if its issues were not detected.
In conclusion, using inert atmosphere gases in furnace atmospheres is essential to ensure a controlled and efficient process, prevent undesirable chemical reactions, and produce high-quality products. It is important to understand why we use them and what the best atmosphere is for a specific application to achieve successful, high precision, and repeatable results.
Common Gases in Furnace Atmospheres
Inert atmosphere gases play a crucial role in furnace atmospheres to prevent unwanted chemical reactions or oxidation of materials during high-temperature processing. The most common gases used for inert atmosphere applications include nitrogen, argon, and helium.
Nitrogen
Nitrogen is the most commonly used gas due to its availability and affordability. It is an unreactive gas that provides a protective atmosphere. Its contents of carbon, oxygen, and nitrogen do not react with steel, making it an ideal gas for furnace atmospheres. Nitrogen is used to prevent oxidation in heat treatment applications and is effective at displacing oxygen from the atmosphere.
Argon
Argon is often used for processes that require a higher level of purity or an extended period of high-temperature processing. Argon is a completely inert “noble” gas and will not react with any material it comes into contact with. It displaces oxygen, making it an ideal gas for applications where oxidation is undesirable. Argon is more expensive than nitrogen but has the benefit of being able to be used at temperatures above 1800°C without any risk of reaction.
Helium
Helium is used when low solubility is required, as it is the least reactive gas. Its low density and high thermal conductivity make it an ideal gas for certain applications. Helium is often used in gas chromatography, leak detection, and cooling applications.
In summary, these gases create an oxygen-free environment that protects the materials being processed and ensures consistent and accurate results. Without the use of inert atmosphere gases, unwanted reactions can occur, leading to product defects, decreased product quality, and even equipment damage. The choice of gas depends on the specific requirements of the heat treatment process, and the type of atmosphere required will determine the type of furnace needed to perform it.
Heat Treatment Processes Requiring Inert Atmospheres
Heat treatment processes that require high temperatures and controlled atmospheres often rely on inert atmosphere gases such as nitrogen, argon, and helium. These gases play a crucial role in creating an environment that is free from oxygen and other reactive gases that could cause chemical reactions or oxidation of the materials being treated.
Why Inert Atmospheres are Essential
The absence of oxygen and other reactive gases in the furnace atmosphere helps to maintain the purity of the materials and prevent contamination or unwanted reactions. Inert atmospheres are essential for a wide range of applications, including heat treating metals, annealing glass, and sintering ceramics. The use of inert atmosphere gases in furnace atmospheres is critical for ensuring the quality and consistency of the end products. Any deviations in the furnace atmosphere can have a significant impact on the final product properties, making it essential to maintain strict control over the furnace environment.
Inert Gases Used in Heat Treatment Processes
Argon, helium, and nitrogen are the inert gases most commonly used in heat treatment processes. The choice of inert gas depends on the type of material being treated and the specific requirements of the heat treatment process. In general, argon and helium are more inert than hydrogen. A pure nitrogen atmosphere provides blanketing of the part being heat treated and can be used to purge the existing atmosphere or be used as a carrier gas for carbon-controlled atmospheres.
Heat Treatment Processes That Use Inert Atmospheres
Inert atmospheres are used in a wide range of heat treatment processes, including:
- Annealing (non-ferrous metals, alloy steel, and decarburization)
- Neutral hardening
- Tempering
- Nitriding (alloy steels, stainless steels, and nitriding steels)
- Sintering
- Brazing (nitrogen acts as the carrier gas)
- Vacuum processes
Inert Gas Combinations
In some cases, a combination of inert gases may be used in heat treatment processes. For example, an atmosphere of hydrogen + nitrogen works well for bright annealing; annealing of stainless steel, alloy steel, and non-iron; neutral hardening; and sintering. Using an atmosphere of hydrogen + argon works with bright annealing; annealing of stainless steel, alloy steel, and non-iron; and sintering.
Conclusion
In summary, inert atmosphere gases play a critical role in heat treatment processes that require high temperatures and controlled atmospheres. The use of these gases helps to maintain the purity of the materials and prevent contamination or unwanted reactions. The choice of inert gas depends on the specific heat treatment process and the type of material being treated. Inert atmospheres are essential for ensuring high-quality end products in the heat treatment industry.
How to Measure Furnace Atmosphere
Measuring the furnace atmosphere is a crucial step in ensuring that the inert atmosphere gases are functioning correctly and that the process is running smoothly. The following are the steps to measure the furnace atmosphere.
Step 1: Determine the type of analyzer
There are several ways to measure furnace atmosphere, including thermal conductivity, infrared, and zirconia analyzers. Each method has its strengths and weaknesses, and the choice of the appropriate analyzer depends on the specific application and the type of gases used.
Step 2: Calibrate the analyzer
Before using the analyzer, it is important to calibrate it to ensure that it is reading accurately. Calibration involves exposing the analyzer to a known gas mixture and adjusting it until it reads the correct values.
Step 3: Install the analyzer
Install the analyzer in the furnace or at the sampling point in the flue gas stream, depending on the type of analyzer.
Step 4: Take the measurement
Once the analyzer is installed, take the measurement. The frequency of measurements will depend on the specific application, but it is important to regularly monitor the furnace atmosphere to maintain its integrity and ensure consistent product quality.
Step 5: Interpret the results
Interpret the results obtained from the analyzer and take corrective actions if necessary. If the results indicate that the furnace atmosphere is not functioning correctly, adjust the inert atmosphere gases to maintain the correct balance.
By following these steps, manufacturers can optimize their processes and produce high-quality products with precision and efficiency.
Tools for Measuring and Sampling
Inert atmosphere gases are crucial components in furnace atmospheres, and ensuring their safety and effectiveness during high-temperature operations is essential. Measuring and sampling these gases is therefore a critical task in laboratory settings.
Gas Analyzers
Gas analyzers are sophisticated tools that perform precise analysis of gas samples, detecting impurities and changes in concentration. They are used to measure a wide range of parameters, including oxygen, carbon dioxide, and water vapor. Gas analyzers are highly sensitive and can detect even the slightest changes in gas composition, making them ideal for monitoring inert atmosphere gases.
Gas Chromatographs
Gas chromatographs are powerful tools that can separate and analyze individual components of a gas sample. They are capable of detecting trace amounts of impurities and can accurately measure the concentrations of various gases. Gas chromatographs are widely used in laboratory settings and can be used to analyze inert atmosphere gases for safety and quality control purposes.
Sampling Equipment
Proper sampling equipment is essential for measuring and monitoring inert atmosphere gases. Gas sampling bags, for example, are used to collect gas samples for analysis, while gas syringes are used to extract samples directly from a gas stream. Other types of sampling equipment include gas detectors, which can detect the presence of specific gases, and gas sensors, which can measure gas concentrations in real-time.
Calibration Equipment
Calibration equipment is essential for ensuring the accuracy of gas analyzers and other gas measurement tools. Calibration gases, such as nitrogen and oxygen, are used to calibrate gas analyzers and ensure accurate readings. Calibration equipment is also used to verify the accuracy of gas sensors and other gas measurement tools.
Benefits of Measuring and Sampling Inert Atmosphere Gases
Measuring and sampling inert atmosphere gases is important for maintaining the safety and quality of heat treatment processes. Regular sampling and analysis of inert atmosphere gases can help identify potential issues in furnace operations and prevent costly equipment damage. It can also help laboratory professionals and engineers to optimize their heat treatment processes, resulting in improved product quality and reduced production costs.
In conclusion, measuring and sampling inert atmosphere gases is a critical task in laboratory settings. Gas analyzers, gas chromatographs, sampling equipment, calibration equipment, and other tools are all essential components of this process. By regularly measuring and monitoring inert atmosphere gases, laboratory professionals can ensure the safety and effectiveness of heat treatment processes and maintain the quality of their products.
Conclusion on the Importance of Inert Atmospheres
Inert atmospheres play a crucial role in the heat treatment process of materials. They help to prevent oxidation, decarburization, or other undesirable reactions that can occur in the presence of oxygen or other reactive gases. By using inert gases, such as nitrogen or argon, in furnace atmospheres, materials can be heated and cooled in a controlled environment, ensuring consistent and reliable results. It is important to measure and monitor the atmosphere in the furnace to ensure that the desired conditions are maintained. Proper use of inert atmospheres can lead to improved product quality, reduced scrap rates, and increased productivity in the heat treatment industry.
CONTACT US FOR A FREE CONSULTATION
KINTEK LAB SOLUTION's products and services have been recognized by customers around the world. Our staff will be happy to assist with any inquiry you might have. Contact us for a free consultation and talk to a product specialist to find the most suitable solution for your application needs!