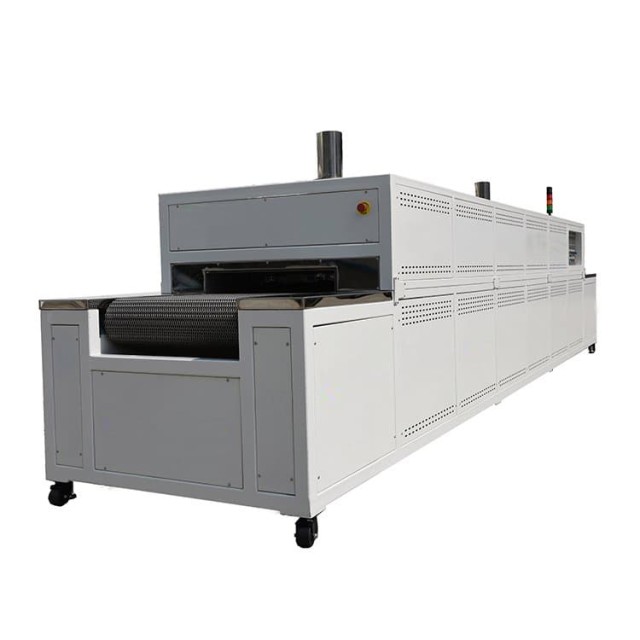
Atmosphere Furnace
Mesh belt controlled atmosphere furnace
Item Number : KT-MB
Price varies based on specs and customizations
- Working temperature
- RT-1000℃
- Mesh belt width
- 200-650 mm
- Effective height
- 50-80 mm
- Hot zone quantity
- 7-12
- Overall length
- 7200-13380 mm
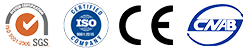
Shipping:
Contact us to get shipping details Enjoy On-time Dispatch Guarantee.
Why Choose Us
Reliable PartnerEasy ordering process, quality products, and dedicated support for your business success.
Introduction
Mesh Belt Controlled Atmosphere Furnace is a continuous production furnace that can operate in both open air and controlled atmosphere environments. It is primarily used in the high-temperature sintering process of electronic components such as thick film circuits, resistors, capacitors, and inductors. The furnace features a selected ceramic fiber heater for rapid response and uniform temperature, a lightweight ceramic fiber insulation for low energy consumption, a mesh belt drive system for stable transmission, and multi independent temperature hot zone control for flexible adjustment. It also offers optional mesh belt ultrasonic cleaning system and center computer control unit. The furnace can be customized to meet specific process requirements, including atmosphere, temperature, and throughput.
Applications
The Mesh Belt Controlled Atmosphere Furnace is a specialized heat treatment system designed for the thermo-chemical processing of small elements. This technology ensures consistent and repeatable results, making it an essential tool in various industrial processes. The furnace operates within a controlled atmosphere, which prevents oxidation and supports surface treatment, enhancing the quality and efficiency of the production process. Here are the main application areas of this product:
- Heat Treatment of Fasteners: Ideal for processing small parts like screws, nuts, bolts, and other elements from the Fasteners group. It is particularly effective for controlled atmosphere hardening, carbonitriding, and carburizing.
- Thermo-chemical Treatment: Suitable for processes that require precise temperature control and a protective atmosphere, such as in the treatment of metal components to enhance their durability and performance.
- Continuous Production Lines: Used in manufacturing settings where continuous processing of materials is required, with capacities ranging from 200 kg to 500 kg per hour, customizable for higher production needs.
- Alternative to Vacuum Furnaces: Offers a lower-cost alternative for materials that can be processed outside of a vacuum, utilizing non-reactive gases to prevent oxidation during the heating process.
Principle
The mesh belt controlled atmosphere furnace adopts a mesh belt as the conveying mechanism, and the workpiece is placed on the mesh belt and heated in a controlled atmosphere environment. The controlled atmosphere is generally composed of inert gases such as nitrogen, argon, and hydrogen, which can prevent the workpiece from oxidizing and carburizing during the heating process. The temperature of the furnace is controlled by a temperature controller, and the heating rate can be adjusted according to the process requirements. The mesh belt controlled atmosphere furnace has the advantages of uniform heating, good temperature control, and high production efficiency, and is widely used in the heat treatment of metals, ceramics, and other materials.
Detail & Parts
Features
Mesh Belt Controlled Atmosphere Furnaces are specifically designed for heat treatment and thermo-chemical processes, ensuring consistent and reliable results for small components. These furnaces offer a range of features that enhance productivity and quality in manufacturing processes, particularly for elements like screws, nuts, bolts, and other fasteners. Key features include:
- Versatile Atmosphere Control: These furnaces can operate with an endothermic atmosphere generated by an external generator using natural gas or propane, or alternatively, with an internal or external methanol dissociator to produce a tailored atmosphere. This feature allows for precise control over the environment, preventing oxidation and ensuring the cleanliness and integrity of the treated parts.
- Flexible Heating Options: Available with both electric and gas heating systems, these furnaces can be customized to suit specific operational needs and energy preferences, enhancing efficiency and cost-effectiveness.
- Adjustable Capacity: Standard models are designed for capacities ranging from 200 kg to 500 kg per hour, with the option to customize for higher production demands, ensuring scalability and adaptability to various production volumes.
- Temperature Range: Capable of operating in the temperature range from 840°C to 955°C, these furnaces are ideal for processes such as controlled atmosphere hardening, carbonitriding, and carburizing, ensuring optimal treatment conditions for a variety of materials.
- Non-Vacuum Operation: Instead of operating in a vacuum, these furnaces use non-reactive gases to displace oxygen, preventing oxidation and promoting a controlled environment that is both efficient and cost-effective for materials that do not require vacuum conditions.
These features collectively make Mesh Belt Controlled Atmosphere Furnaces a robust and versatile solution for manufacturers looking to enhance the quality and efficiency of their heat treatment processes.
Advantages
- Selected ceramic fiber heater (FEC) offers rapid response, uniform and stable temperature.
- Lightweight ceramic fiber insulation ensures low energy consumption and fast temperature rise.
- Variable speed regulator on the mesh belt drive system provides stable and reliable transmission.
- Multiple independent temperature hot zone control enables flexible and convenient adjustment.
- Multi gases supply and control system can be tailored to specific process requirements.
- Optional mesh belt ultrasonic cleaning system and center computer control unit enhance productivity and efficiency.
Technical specifications
Model | KT-MB20 | KT-MB30 | KT-MB35 | KT-MB60 | KT-MB65 |
---|---|---|---|---|---|
Working temperature | RT-1000℃ | ||||
Control accuracy | ±1℃ | ||||
Heating element | FEC heater | ||||
Mesh belt width | 200mm | 300mm | 350mm | 600mm | 650mm |
Effective height | 50mm | 60mm | 80mm | 80mm | 80mm |
Hot zone quantity | 7 | 7 | 8 | 9 | 12 |
Overall length | 7200mm | 7200mm | 7200mm | 7650mm | 13380mm |
Customer design sizes and requirement is accepted |
Warnings
Operator safety is the top important issue! Please operate the equipment with cautions. Working with inflammable& explosive or toxic gases is very dangerous, operators must take all necessary precautions before starting the equipment. Working with positive pressure inside the reactors or chambers is dangerous, operator must fellow the safety procedures strictly. Extra caution must also be taken when operating with air-reactive materials, especially under vacuum. A leak can draw air into the apparatus and cause a violent reaction to occur.
Designed for You
KinTek provide deep custom made service and equipment to worldwide customers, our specialized teamwork and rich experienced engineers are capable to undertake the custom tailoring hardware and software equipment requirements, and help our customer to build up the exclusive and personalized equipment and solution!
Would you please drop your ideas to us, our engineers are ready for you now!
FAQ
What Is A Atmospheric Furnace?
What Is The Use Of Atmosphere Furnace?
How Does An Atmosphere Furnace Work?
What Are The Advantages Of Using Atmosphere Furnaces?
What Factors Should Be Considered When Selecting An Atmosphere Furnace?
4.8
out of
5
KINTEK's mesh belt furnace has streamlined our sintering process, resulting in consistent high-quality products.
4.7
out of
5
The AI-based temperature control system ensures precise temperature maintenance, leading to increased efficiency and energy savings.
4.9
out of
5
The thyristor-based controllers have significantly extended the lifespan of our heating elements, reducing maintenance costs and downtime.
4.6
out of
5
The mesh belt drive system operates smoothly and reliably, ensuring consistent product flow and quality.
4.8
out of
5
The multi-independent temperature hot zone control provides excellent flexibility and convenience in adjusting process parameters.
4.7
out of
5
The optional mesh belt ultrasonic cleaning system maintains belt cleanliness, contributing to product quality and reducing maintenance.
4.9
out of
5
KINTEK's customer support is outstanding. They promptly addressed our queries and provided valuable technical guidance.
4.6
out of
5
The mesh belt furnace's compact design and customizable sizes make it an ideal fit for our limited lab space.
Products
Mesh belt controlled atmosphere furnace
REQUEST A QUOTE
Our professional team will reply to you within one business day. Please feel free to contact us!
Related Products
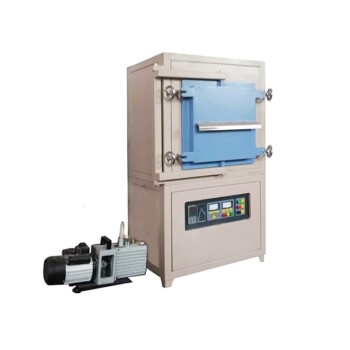
1700℃ Controlled Atmosphere Furnace Nitrogen Inert Atmosphere Furnace
KT-17A Controlled atmosphere furnace: 1700℃ heating, vacuum sealing technology, PID temperature control, and versatile TFT smart touch screen controller for laboratory and industrial use.
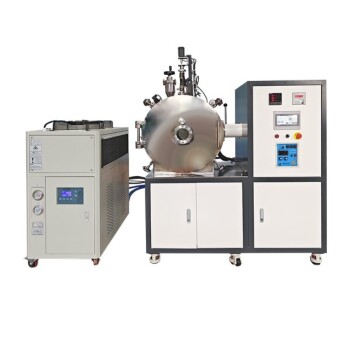
Lab-Scale Vacuum Induction Melting Furnace
Get precise alloy composition with our Vacuum Induction Melting Furnace. Ideal for aerospace, nuclear energy, and electronic industries. Order now for effective smelting and casting of metals and alloys.
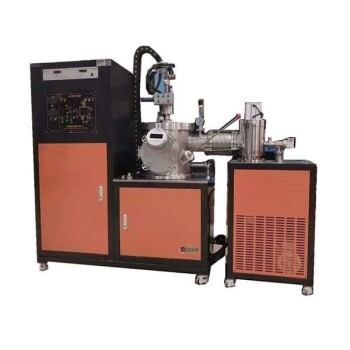
Vacuum Arc Induction Melting Furnace
Discover the power of Vacuum Arc Furnace for melting active & refractory metals. High-speed, remarkable degassing effect, and free of contamination. Learn more now!
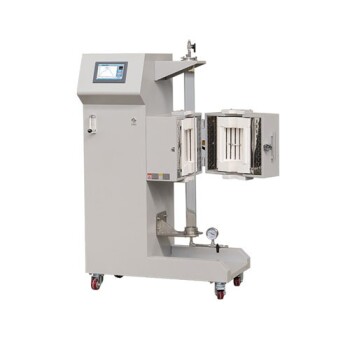
Vertical Laboratory Quartz Tube Furnace Tubular Furnace
Elevate your experiments with our Vertical Tube Furnace. Versatile design allows for operation under various environments and heat treatment applications. Order now for precise results!
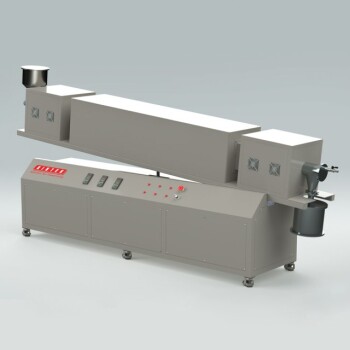
Vacuum Sealed Continuous Working Rotary Tube Furnace Rotating Tube Furnace
Experience efficient material processing with our vacuum-sealed rotary tube furnace. Perfect for experiments or industrial production, equipped with optional features for controlled feeding and optimized results. Order now.
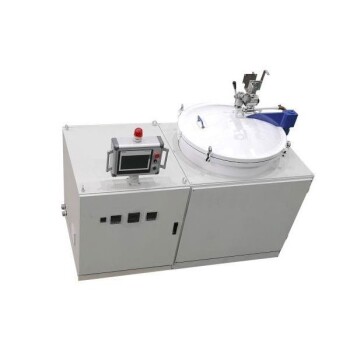
Graphite Vacuum Furnace IGBT Experimental Graphitization Furnace
IGBT experimental graphitization furnace, a tailored solution for universities and research institutions, with high heating efficiency, user-friendliness, and precise temperature control.
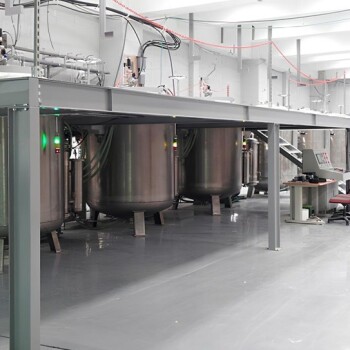
Graphite Vacuum Furnace Negative Material Graphitization Furnace
Graphitization furnace for battery production has uniform temperature and low energy consumption. Graphitization furnace for negative electrode materials: an efficient graphitization solution for battery production and advanced functions to enhance battery performance.
Related Articles
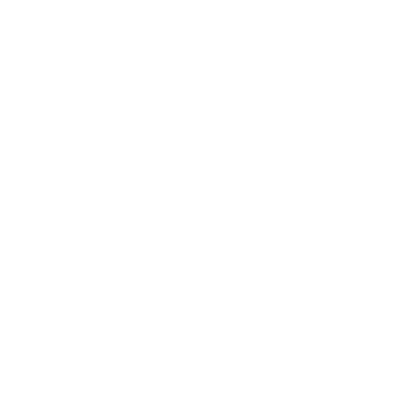
Atmosphere Furnaces: Comprehensive Guide to Controlled Heat Treatment
Explore the advanced world of atmosphere furnaces with our detailed guide. Learn about their operation, applications, and benefits in various industries. Perfect for those seeking in-depth knowledge on controlled heat treatment.
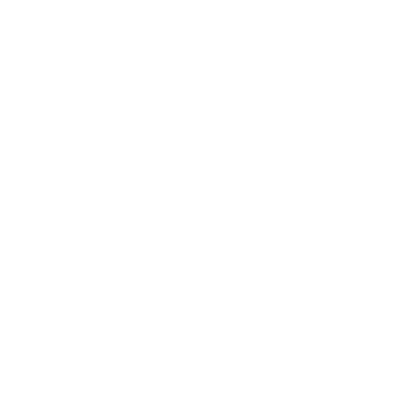
Comprehensive Guide to Atmosphere Furnaces: Types, Applications, and Benefits
Explore the world of atmosphere furnaces with our detailed guide. Learn about their types, applications in metallurgy and beyond, and the benefits they offer for precise material heat treatment.
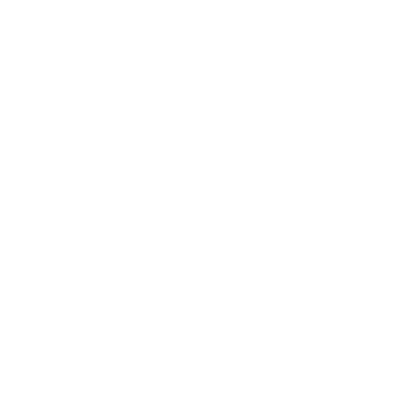
The Benefits of Controlled Atmosphere Furnaces for Sintering and Annealing Processes
They are essential in preventing oxidation, reducing the risk of contamination, and improving the properties of the materials being treated.
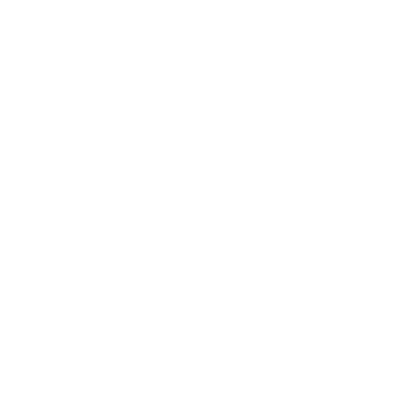
Muffle Furnace: Unraveling the Secrets of Uniform Heating and Controlled Atmosphere
Discover the intricacies of a muffle furnace, an indispensable tool for material processing and analysis. Learn about its working principle, applications, types, features, and benefits, empowering you to make informed decisions for your laboratory or industrial needs.
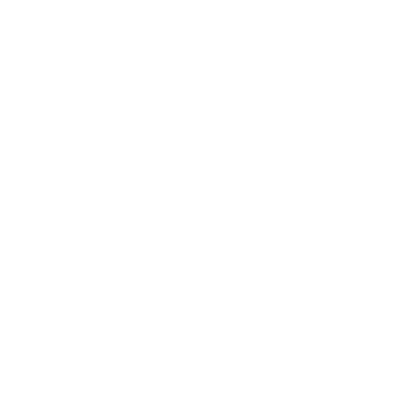
Controlled Atmosphere Furnace: Comprehensive Guide to Advanced Heat Treatment
Explore the advanced features and applications of controlled atmosphere furnaces in heat treatment processes. Learn about key components, operational techniques, and benefits for precise material processing.
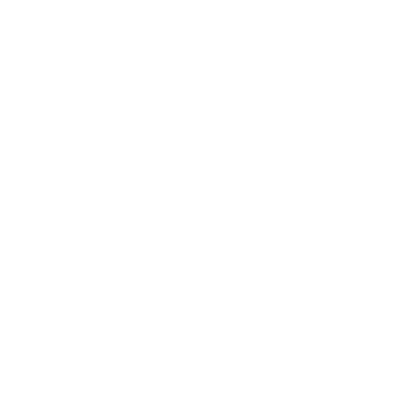
How Controlled Atmosphere Furnaces Improve Quality and Consistency in Heat Treatment
Controlled atmosphere furnaces play a vital role in heat treatment processes.
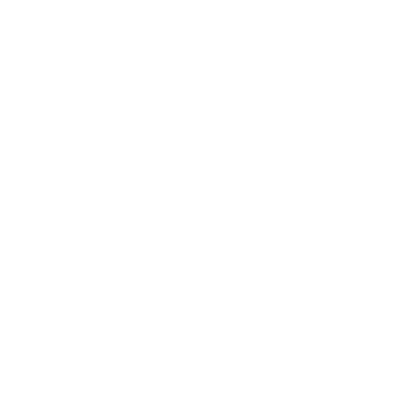
Hydrogen Atmosphere Furnaces: Applications, Safety, and Maintenance
Explore the comprehensive guide on hydrogen atmosphere furnaces, including their applications in high-end alloy sintering, safety measures, and maintenance tips. Learn about the types, components, and operational considerations for optimal performance.
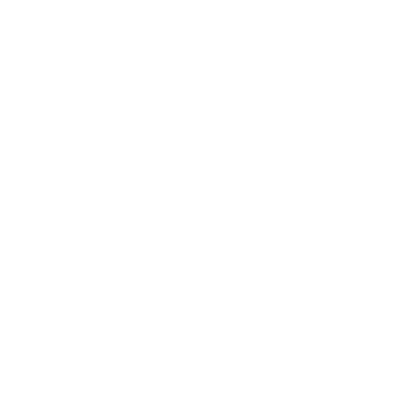
The Importance of Inert Atmosphere Gases in Furnace Atmospheres
Furnace atmospheres play an essential role in the heat treatment process of materials.
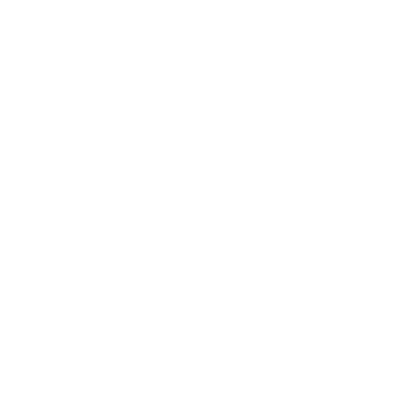
Exploring the Key Performance Indicators of an Atmosphere Furnace
Atmosphere furnaces are specialized pieces of equipment used in a variety of industries for applications such as heat treatment, ceramics, and metallurgy.
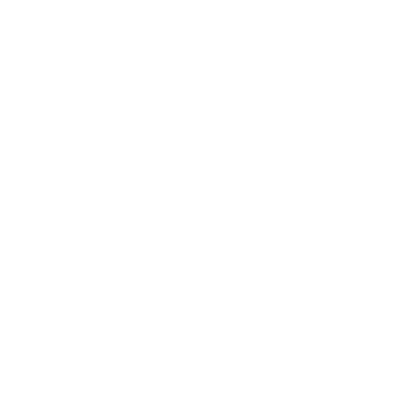
Environmental Benefits of Using an Atmosphere Furnace
Inert atmosphere furnaces are designed to provide a controlled environment for high-temperature processing of materials.
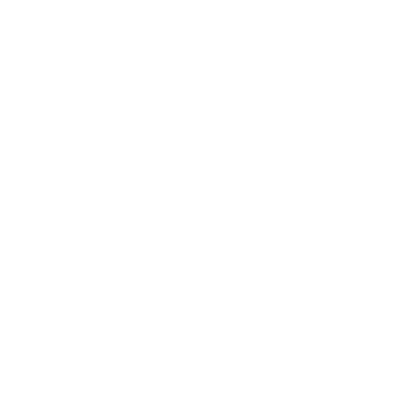
Comprehensive Guide to Muffle Furnaces: Applications, Types, and Maintenance
Explore the world of muffle furnaces with our detailed guide. Learn about their applications in various industries, types available, and essential maintenance tips to ensure optimal performance.
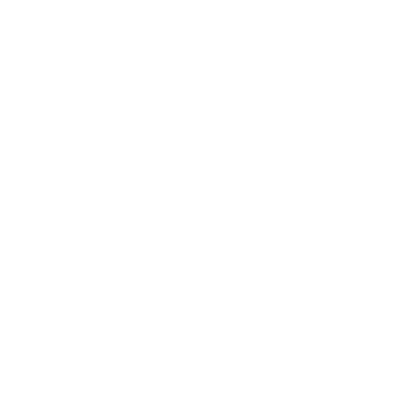
Exploring the Advanced Capabilities of Spark Plasma Sintering (SPS) Furnaces
Dive into the world of Spark Plasma Sintering (SPS) furnaces, their innovative technology, and applications in material science. Learn how SPS furnaces revolutionize the sintering process with high-speed, efficiency, and precision.