Kinds of atmosphere
Atmosphere furnaces are specialized pieces of equipment used in a variety of industries for applications such as heat treatment, ceramics, and metallurgy. These furnaces are classified according to the atmosphere within the furnace, which can have a significant impact on the performance and efficiency of the furnace.
Other types of atmosphere furnaces include those used for ammonia preparation, charcoal, and ammonia. The choice of atmosphere in the furnace depends on the specific application and the materials being processed. Overall, the performance characteristics of an atmosphere furnace depend on the type of atmosphere used and the specific requirements of the application (exothermic, endothermic, organic liquid cracking, nitrogen, ammonia preparation, charcoal, ammonia).
Table of Contents
The structure of the atmosphere furnace
The atmosphere furnace is a specialized piece of equipment that is used for a variety of applications such as heat treatment, ceramics, and metallurgy. The furnace consists of several key components that work together to achieve the desired results.
- The feeding mechanism is responsible for introducing the materials into the furnace. This may involve manual loading or the use of an automated system to move the materials into the furnace.
- The heating furnace is the component of the atmosphere furnace where the materials are heated to the desired temperature. This may be done using heating elements or burners, and the furnace may also include insulation to reduce heat loss and controls to regulate the temperature and atmosphere within the furnace.
- The quenching tank is used to rapidly cool the materials after they have been heated in the heating furnace. This is often done in order to harden or strengthen the material. The quenching tank may include a cooling medium, such as water or oil, to cool the materials as they are transferred from the heating furnace.
- The washing machine is used to clean the materials after they have been processed in the furnace. This may involve rinsing the materials with water or using a cleaning solution to remove any contaminants or residue.
- The tempering furnace is used to reheat the materials after they have been quenched in order to reduce their brittleness and improve their toughness. This is often done at a lower temperature than the initial heating process.
Overall, these components work together to achieve the desired results in the atmosphere furnace.
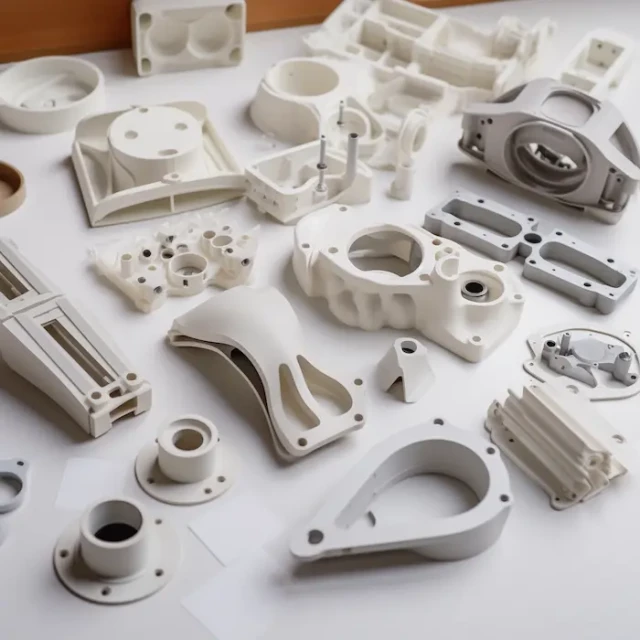
Quenching tank structure
The quenching tank is an important component of the atmosphere furnace, and its structure plays a key role in the performance of the furnace.
A frequency conversion speed regulating oil agitator can be used to greatly increase the quenching deformation of the workpiece, which can be beneficial for certain applications. A high power cooling air-cooled heat exchanger can improve the safety of the equipment by helping to dissipate heat and prevent overheating.
Blocked leakage can increase the oxidation and decarburization of the workpiece, so it is important to design the quenching tank to minimize this issue. An oil curtain can be used to increase the smoke entering the heating chamber, which can be beneficial for certain applications.
The design of the quenching tank is an important consideration in the performance of the atmosphere furnace, and the specific features included in the tank can have a significant impact on the efficiency and effectiveness of the furnace.
Heating furnace structure
The heating furnace is an important component of the atmosphere furnace, and its structural features can have a significant impact on the performance and efficiency of the furnace.
Radiant tube heating and complete double-sided heating of the workpiece can greatly improve the heating efficiency and average furnace temperature. Using a light anti-seepage full fiber lining can save energy compared to an impermeable brick lining.
A heat-resistant steel wire mesh belt that is driven by a rotating roller can increase wear resistance and improve the service life of the furnace. Using import products for key control components can improve the overall reliability of the equipment.
In order to improve safety, a safety alarm system and mechanical interlocking device may be added to the heating furnace. A dialogue operation interface can provide information about the operation modes of the equipment and allow for the processing and correction of various process parameters.
Main features of atmosphere furnace
Refractory material
When using a reducing atmosphere in the furnace, it is important to use refractory material that is resistant to carburization in order to maintain the integrity of the furnace and the stability of the atmosphere within the furnace.
Carburization is a process in which carbon is introduced into the surface of a material, often causing it to become harder and more brittle. This can be a problem in an atmosphere furnace that uses a reducing atmosphere, as the carbon in the atmosphere can react with the refractory material, causing it to break down or degrade over time.
To prevent this issue, it is important to use refractory material that is resistant to carburization, also known as anti-carburizing refractory. This type of refractory material is designed to withstand the reducing atmosphere without breaking down or degrading, ensuring the long-term stability and performance of the furnace.
Automation
The degree of automation of an atmosphere furnace is an important consideration, especially in large-scale production where multiple furnaces may be used in conjunction with one another.
The sealing requirements of various atmosphere furnaces are often high, and the process of loading and unloading materials into the furnace can be complex. In order to improve efficiency and reduce the risk of errors, it is often beneficial to use a furnace with a higher degree of mechanization and automation.
In large-scale production, it is common to use large-scale comprehensive heat treatment units or dual-purpose units that consist of multiple atmosphere furnaces. These units can be designed with a higher degree of mechanization and automation in order to improve efficiency and reduce the risk of errors.
Explosion proof
Explosion proof devices are often necessary in an atmosphere furnace in order to prevent explosions caused by the mixture of gas and air at high temperatures.
When the mixing ratio of gas and air is too high, it can be easy to cause an explosion at a certain temperature. To prevent this, it is necessary to install explosion proof devices in the front and rear chambers of the furnace, as well as in the quenching chamber and slow cooling chamber.
In addition to these measures, the furnace gas supply and exhaust gas control system should also have explosion-proof measures in place to prevent the risk of explosion. These may include valves, pressure relief devices, and other controls to reduce the mixing ratio of gas and air and prevent the risk of explosion.
Explosion proof devices are an important safety feature of an atmosphere furnace, and it is important to ensure that these devices are properly installed and maintained to reduce the risk of explosions.
Good sealing
Good sealing is essential in an atmosphere furnace in order to control the atmosphere within the furnace and maintain the desired pressure.
To achieve good sealing, it is important to isolate the working space within the furnace from external air and prevent air leakage or inhalation. This involves sealing the furnace shell, masonry, furnace door, and all external connecting parts such as fans, thermocouples, radiant tubes, and push-pull feeders.
By maintaining a tight seal on the furnace, it is possible to control the atmosphere within the furnace and maintain the desired pressure, which is important for achieving the desired results in the furnace.
Atmosphere control
Atmosphere control is an important aspect of the operation of an atmosphere furnace. In order to maintain a certain carbon potential within the furnace, it is necessary to control the stability of the atmosphere composition and adjust the amount of gas supplied to the furnace as needed.
To achieve this, various control instruments are used to continuously and periodically measure the atmosphere within the furnace and adjust the flow of gas as needed. This may involve the use of sensors to measure the concentration of gases within the furnace, as well as valves and other control mechanisms to adjust the flow of gas into the furnace.
By maintaining a stable atmosphere within the furnace and controlling the carbon potential, it is possible to achieve the desired results in the furnace.
Heating mode
The heating mode of an atmosphere furnace can have a significant impact on its performance and stability.
One type of atmosphere furnace is the muffle furnace, in which the flame is located outside the muffle furnace and the workpiece is indirectly heated. This can be a good option for maintaining the stability of the atmosphere within the furnace.
Another type of atmosphere furnace is the muffle-free furnace, which uses various flame radiant tubes or electric radiant tubes to separate the flame or electric heater from the furnace gas. This can help to maintain the stability of the atmosphere within the furnace by avoiding the introduction of contaminants or disruptions to the atmosphere.
How to choose atmosphere furnace
There are a number of factors to consider when choosing an atmosphere furnace for a specific application. Some of the key considerations include:
- The type of atmosphere: Different types of atmosphere furnaces are designed for specific atmospheres, such as exothermic, endothermic, organic liquid cracking, nitrogen, ammonia preparation, charcoal, and ammonia. It is important to choose a furnace that is designed for the desired atmosphere.
- The size and capacity of the furnace: The size and capacity of the furnace should be chosen based on the size and volume of the materials being processed. It is important to choose a furnace that is appropriately sized for the application.
- The temperature range: Different atmosphere furnaces are designed to operate at different temperature ranges. It is important to choose a furnace that is capable of reaching the desired temperatures for the application.
- The degree of automation: The degree of automation of the furnace can be an important factor, especially in large-scale production. Higher degrees of automation can improve efficiency and reduce the risk of errors.
- The sealing and atmosphere control: Good sealing and effective atmosphere control are important factors in the performance and efficiency of the furnace. It is important to choose a furnace that is designed with these features in mind.
KINTEK atmosphere furnace
Are you in the market for an atmosphere furnace? Look no further! Kintek atmosphere furnaces are top-of-the-line and designed to meet all of your heat treatment needs.
Our furnaces are available in a variety of types, including exothermic, endothermic, organic liquid cracking, nitrogen, ammonia preparation, charcoal, and ammonia. No matter what your specific atmosphere needs may be, we have a furnace that is right for you.
In addition to our wide selection of atmosphere types, our furnaces are also available in a range of sizes and capacities to suit your needs. Whether you are working with small or large volumes of material, we have a furnace that is perfect for you.
KINTEK furnaces are also designed to operate at a wide range of temperatures, so you can be sure that we have a furnace that is capable of reaching the temperatures you need for your specific application.
And with our high degree of automation, you can trust that our furnaces will be efficient and easy to use. Plus, our attention to sealing and atmosphere control ensures that you will get the best performance possible from our furnaces.
Don't settle for anything less than the best. Choose our atmosphere furnaces for all of your heat treatment needs.
CONTACT US FOR A FREE CONSULTATION
KINTEK LAB SOLUTION's products and services have been recognized by customers around the world. Our staff will be happy to assist with any inquiry you might have. Contact us for a free consultation and talk to a product specialist to find the most suitable solution for your application needs!