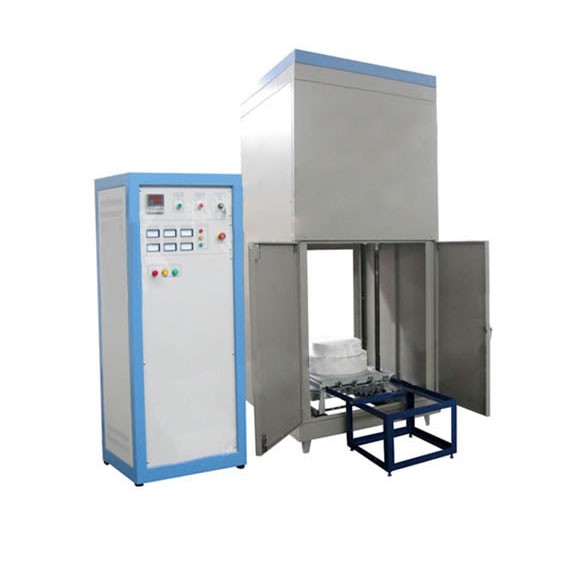
Muffle Furnace
Laboratory Muffle Oven Furnace Bottom Lifting Muffle Furnace
Item Number : KT-BL
Price varies based on specs and customizations
- Working temperature range
- 1100 / 1300 / 1600 ℃
- Heating rate
- 0-20℃/min
- Effective volume
- 12-512 L
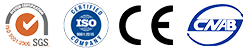
Shipping:
Contact us to get shipping details Enjoy On-time Dispatch Guarantee.
Why Choose Us
Reliable PartnerEasy ordering process, quality products, and dedicated support for your business success.
Introduction
KT-BL Bottom lifting furnace features excellent temperature uniformity and convenient products batch production, its heating elements are placed in the 4 sides of the furnace chamber,which create an excellent heating radiation field;Bottom lifting furnace can work with 2 electric lifting product loading stages, operator can load the product on the second stage when the other one stage is in the heating chamber, so the production efficiency can be greatly improved.
Bottom lifting furnace applies Al2O3 polycrystalline fiber material,which is light weight,low thermal conductivity and high temperature resistance; Temperature controller applies PID intelligent temperature microprocessor, high temperature control accuracy and excellent temperature uniformity; Bottom lifting furnace working temperature is up to 1600℃.
Applications
Bottom lifting furnaces, also known as elevator-type furnaces, are versatile tools used in various scientific and industrial processes. These furnaces are designed with a bottom floor that can be manually or automatically lifted into the heated chamber, facilitating easy loading and unloading of samples. The uniform thermal distribution and the ability to handle large and heavy loads make them suitable for a range of applications. Here are the main application areas of bottom lifting furnaces:
- Material Science and Testing: Used for high-temperature tests and treatments of materials, including annealing, hardening, and stress-relieving.
- Chemical Analysis: Ideal for processes that require precise temperature control and uniform heating, such as calcination and sintering.
- Quality Control in Manufacturing: Ensures consistent heat treatment of components, enhancing product quality and reliability.
- Research and Development: Supports experiments and processes that demand accurate temperature regulation and efficient sample handling.
- Industrial Heat Treatments: Suitable for large-scale operations, including the treatment of bulky and heavy components in industries like aerospace and automotive.
Detail&Parts
Feature
- Appearance design: The electric furnace adopts humanized design, beautiful and generous, easy to operate, and the outer paint layer uses plastic spraying high-temperature baking process. It has high temperature resistance, oxidation resistance, acid and alkali resistance. The color is selected as an anti-aging tone, and the appearance color will not fade due to long-term use.
- Shell design: The shell of the electric furnace adopts a double-layer forced air-cooled structure, so that the external temperature of the shell is close to room temperature when the electric furnace is working at high temperature, and accidental damage is avoided.
- Temperature control method: adopt Yudian advanced temperature controller: with 30-50 programmable PID self-tuning, automatic temperature rise, automatic temperature drop, no need to be on duty. RS-485 communication interface can also be selected (connected to a common computer to start, stop, suspend heating, set heating curve, storage of heating curve, historical curve recording and other functions)
- Temperature control system: The electric furnace adopts integrated circuit, module control, double-circuit protection (protection functions such as partial temperature protection, ultra-high temperature protection, burnout protection, over-current protection, over-pressure protection, etc.) to make the electric furnace work stably and reliably.
- Heating rate: The heating rate is 30°C/min, 20°C/min is recommended.
- Furnace material: Lightweight alumina ceramic fiber is used, which has excellent thermal insulation effect, light weight, high temperature resistance, rapid cooling and rapid heating resistance, no cracks, no crystallization, no slag drop, and no need to worry about polluting the fired products. The energy-saving effect is 60%-80% of the old electric furnace.
- Furnace design: The furnace adopts a stepped assembly structure, which integrates the laws of mechanics, effectively ensures that the furnace is evenly stressed during the heating process, ensures that the heat energy is not easily lost, and prolongs the service life of the furnace.
Advantages
Bottom Lifting Furnaces offer a range of advantages that enhance laboratory operations and efficiency. These furnaces are designed with a lifting platform located under the furnace, which can be operated manually or automatically, providing a convenient and ergonomic solution for lifting and unloading samples. The bottom loading feature ensures easy access to the chamber, optimizing the workflow and reducing the risk of accidents or strain during sample handling.
One of the key benefits of these furnaces is their uniform thermal distribution. The electrical heating elements are uniformly assembled around the heating chamber, ensuring consistent heating and optimal performance. This uniform heating is crucial for precise and reproducible results, making these furnaces ideal for applications requiring high temperature uniformity.
The Vertical Bottom Loading Vacuum Furnaces come with an integrated heavy-duty support structure, enhancing their durability and stability. The bottom head is motorized, allowing for smooth and controlled movement in and out, as well as up and down, facilitating easy and unobstructed loading and unloading of workloads and fixtures. This design feature not only improves efficiency but also enhances operator safety through remote control operation.
Additionally, these furnaces are equipped with a fully automated and programmable industrial controls package, which allows for precise temperature control and operation. This automation reduces the need for manual intervention, minimizing the potential for human error and increasing the reliability of experimental outcomes.
Maintenance is also made easier with these furnaces, as they are designed to allow for quick and efficient servicing, thereby minimizing downtime. This is particularly beneficial in busy laboratory environments where equipment availability is critical.
In comparison to conventional fixed axis furnaces, Bottom Lifting Furnaces offer a more efficient and user-friendly solution, particularly in terms of loading and unloading processes. The reduction in off-gas volumes and the overall simplification of operations make these furnaces a cost-effective choice for both small and large production units.
Safety Advantage
- Kindle Tech tube furnace owns over current protection, over temperature alarming function, furnace will turn off the power automatically
- Furnace build in thermal couple detecting function, furnace will stop heating and alarm will be on once broken or failure detected
- Up and down lifting function failure interlock protection,once failure detected,heating will be shut off,alarm will be on
Technical specifications
Furnace model | KT-BL | ||
---|---|---|---|
Working temperature range | 1100/1300/1600℃ | ||
Chamber material | Al2O3 polycrystalline fiber | ||
Heating element | Silicon Carbide/Molybdenum Disilicide | ||
Heating rate | 0-20℃/min | ||
Temperature sensor | K/S/B type thermal couple | ||
Temperature controller | Touch screen PID controller | ||
Temperature control accuracy | ±1℃ | ||
Temperature uniformity | ±5℃ | ||
Electric power supply | AC110-220V,50/60HZ | ||
Standard Chamber Sizes Stocks | |||
Chamber size (mm) | Effective volume (L) | Chamber size (mm) | Effective volume (L) |
200x200x300 | 12 | 400x400x500 | 80 |
300x300x300 | 27 | 500x500x500 | 125 |
300x400x300 | 36 | 600x600x600 | 216 |
400x400x400 | 64 | 800x800x800 | 512 |
Customer design sizes and volume is accepted |
Standard Package
No. | Description | Quantity |
---|---|---|
1 | Furnace | 1 |
2 | Thermal block | 1 |
3 | Crucible tong | 1 |
4 | Heat resistant glove | 1 |
5 | Operation manual | 1 |
Optional Setup
- Independent furnace temperature monitoring and recording
- RS 485 communication port for PC remote control and data exporting
- Insert gases port,exhaust output port,observation window port
Warnings
Operator safety is the top important issue! Please operate the equipment with cautions. Working with inflammable& explosive or toxic gases is very dangerous, operators must take all necessary precautions before starting the equipment. Working with positive pressure inside the reactors or chambers is dangerous, operator must fellow the safety procedures strictly. Extra caution must also be taken when operating with air-reactive materials, especially under vacuum. A leak can draw air into the apparatus and cause a violent reaction to occur.
Designed for You
KinTek provide deep custom made service and equipment to worldwide customers, our specialized teamwork and rich experienced engineers are capable to undertake the custom tailoring hardware and software equipment requirements, and help our customer to build up the exclusive and personalized equipment and solution!
Would you please drop your ideas to us, our engineers are ready for you now!
FAQ
What Are Muffle Furnace Used For?
What Are The Types Of Muffle Furnace?
What Is Muffle Furnace In Chemistry?
What Is The Use Of Muffle Furnace For Ash?
What Is The Temperature Of Muffle Furnace?
4.9
out of
5
KT-BL Bottom lifting furnace has been a game-changer for our research lab. The uniform temperature distribution and bottom loading feature have enabled us to conduct experiments with greater precision and efficiency.
4.8
out of
5
I appreciate the ease of use and the rapid heating rate of the Bottom lifting furnace. It has significantly streamlined our sample preparation process and improved our productivity.
4.8
out of
5
The safety features of the Bottom lifting furnace provide peace of mind during high-temperature experiments. The automatic shut-off and alarm systems ensure a safe working environment for our lab personnel.
4.9
out of
5
The energy efficiency of the Bottom lifting furnace is commendable. The Al2O3 polycrystalline fiber insulation effectively minimizes heat loss, resulting in reduced energy consumption and cost savings.
4.7
out of
5
The technical support team at KINTEK SOLUTION is exceptional. They promptly responded to our queries and provided valuable guidance during the installation and operation of the Bottom lifting furnace. Their expertise ensured a smooth integration into our laboratory.
4.7
out of
5
The durability of the Bottom lifting furnace is impressive. Despite continuous usage in our demanding research environment, the furnace has maintained its performance and reliability. KINTEK SOLUTION's commitment to quality is evident in this product.
4.6
out of
5
The Bottom lifting furnace's versatility is a major advantage. Its ability to handle a wide range of materials and applications makes it an indispensable tool in our laboratory. We can confidently rely on it for various experimental needs.
4.7
out of
5
The value for money offered by the Bottom lifting furnace is unbeatable. Its exceptional performance, coupled with its competitive pricing, makes it an excellent investment for any research laboratory. KINTEK SOLUTION has struck the perfect balance between quality and affordability.
4.8
out of
5
The speed of delivery from KINTEK SOLUTION was exceptional. We received the Bottom lifting furnace within a week of placing the order. Their efficient logistics ensured timely arrival and minimized any disruptions to our research schedule.
Products
Laboratory Muffle Oven Furnace Bottom Lifting Muffle Furnace
REQUEST A QUOTE
Our professional team will reply to you within one business day. Please feel free to contact us!
Related Products
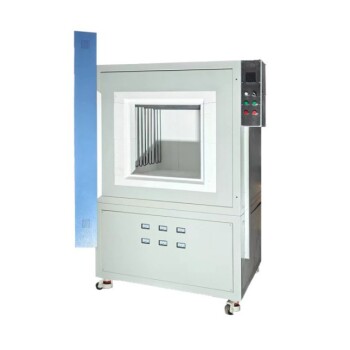
High Temperature Muffle Oven Furnace for Laboratory Debinding and Pre Sintering
KT-MD High temperature debinding and pre-sintering furnace for ceramic materials with various molding processes. Ideal for electronic components such as MLCC and NFC.
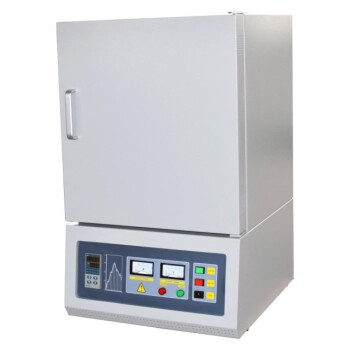
1700℃ Muffle Oven Furnace for Laboratory
Get superior heat control with our 1700℃ Muffle Furnace. Equipped with intelligent temperature microprocessor, TFT touch screen controller & advanced insulation materials for precise heating up to 1700C. Order now!
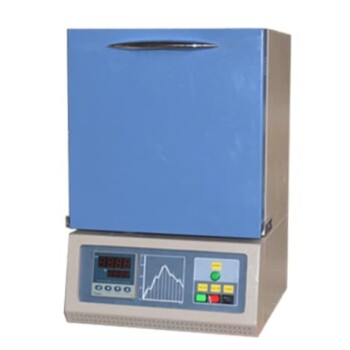
1200℃ Muffle Furnace Oven for Laboratory
Upgrade your lab with our 1200℃ Muffle Furnace. Achieve fast, precise heating with Japan alumina fibers and Molybdenum coils. Features TFT touch screen controller for easy programming and data analysis. Order now!
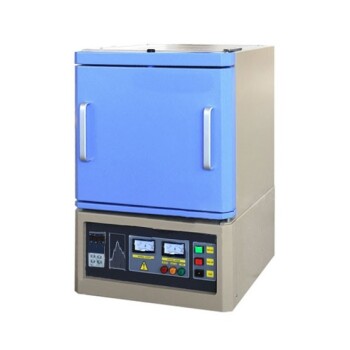
1800℃ Muffle Oven Furnace for Laboratory
KT-18 muffle furnace with Japan Al2O3 polycrystalline fibe and Silicon Molybdenum heating element, up to 1900℃, PID temperature control and 7" smart touch screen. Compact design, low heat loss, and high energy efficiency. Safety interlock system and versatile functions.
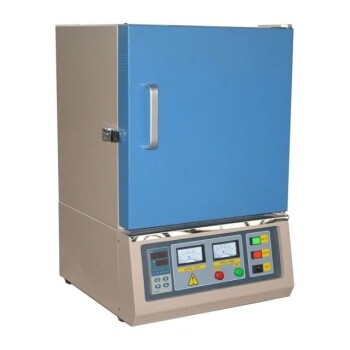
1400℃ Muffle Oven Furnace for Laboratory
Get precise high-temperature control up to 1500℃ with KT-14M Muffle furnace. Equipped with a smart touch screen controller and advanced insulation materials.

Graphite Vacuum Furnace Bottom Discharge Graphitization Furnace for Carbon Materials
Bottom-out graphitization furnace for carbon materials, ultra-high temperature furnace up to 3100°C, suitable for graphitization and sintering of carbon rods and carbon blocks. Vertical design, bottom discharging, convenient feeding and discharging, high temperature uniformity, low energy consumption, good stability, hydraulic lifting system, convenient loading and unloading.
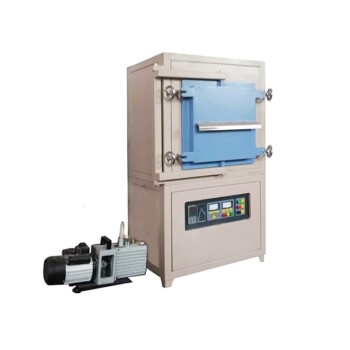
1700℃ Controlled Atmosphere Furnace Nitrogen Inert Atmosphere Furnace
KT-17A Controlled atmosphere furnace: 1700℃ heating, vacuum sealing technology, PID temperature control, and versatile TFT smart touch screen controller for laboratory and industrial use.
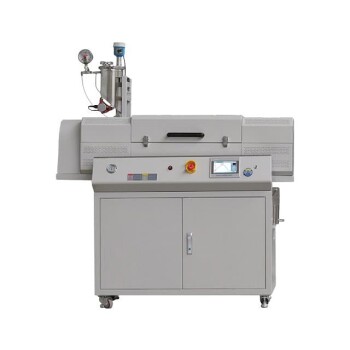
Laboratory Vacuum Tilt Rotary Tube Furnace Rotating Tube Furnace
Discover the versatility of Laboratory Rotary Furnace: Ideal for calcination, drying, sintering, and high-temperature reactions. Adjustable rotating and tilting functions for optimal heating. Suitable for vacuum and controlled atmosphere environments. Learn more now!
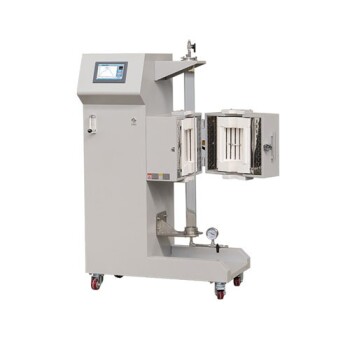
Vertical Laboratory Quartz Tube Furnace Tubular Furnace
Elevate your experiments with our Vertical Tube Furnace. Versatile design allows for operation under various environments and heat treatment applications. Order now for precise results!
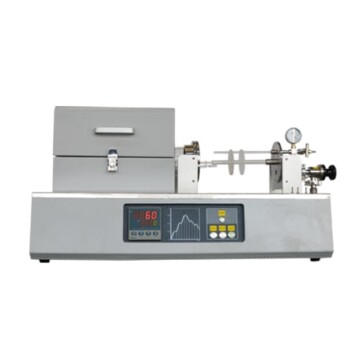
Laboratory Quartz Tube Furnace Tubular RTP Heating Furnace
Get lightning-fast heating with our RTP Rapid Heating Tube Furnace. Designed for precise, high-speed heating and cooling with convenient sliding rail and TFT touch screen controller. Order now for ideal thermal processing!
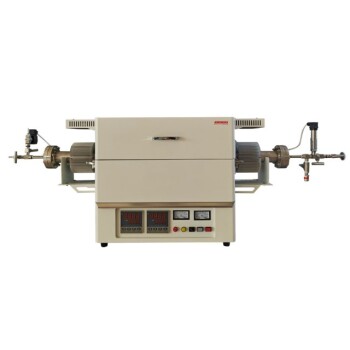
High Pressure Laboratory Vacuum Tube Furnace Quartz Tubular Furnace
KT-PTF High Pressure Tube Furnace: Compact split tube furnace with strong positive pressure resistance. Working temp up to 1100°C and pressure up to 15Mpa. Also works under controller atmosphere or high vacuum.
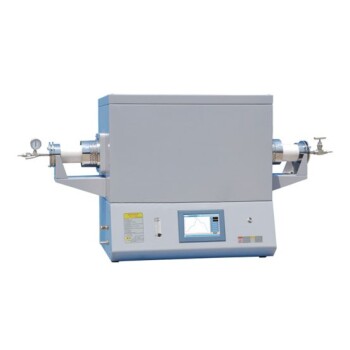
1700℃ Laboratory Quartz Tube Furnace with Alumina Tube Tubular Furnace
Looking for a high-temperature tube furnace? Check out our 1700℃ Tube Furnace with Alumina Tube. Perfect for research and industrial applications up to 1700C.
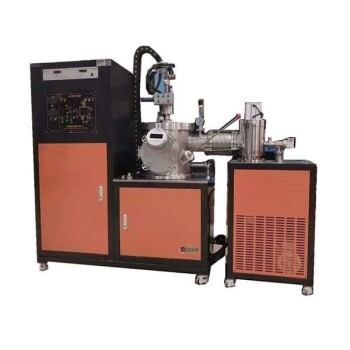
Vacuum Arc Induction Melting Furnace
Discover the power of Vacuum Arc Furnace for melting active & refractory metals. High-speed, remarkable degassing effect, and free of contamination. Learn more now!
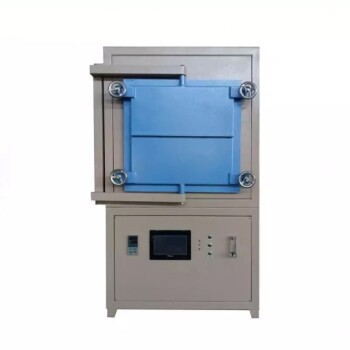
1400℃ Controlled Atmosphere Furnace with Nitrogen and Inert Atmosphere
Achieve precise heat treatment with KT-14A controlled atmosphere furnace. Vacuum sealed with a smart controller, it's ideal for lab and industrial use up to 1400℃.
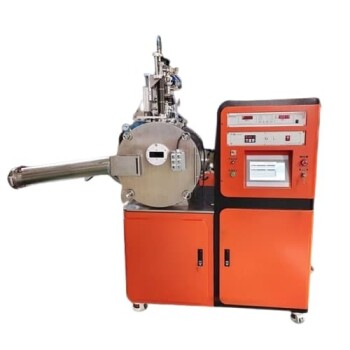
Vacuum Induction Melting Spinning System Arc Melting Furnace
Develop metastable materials with ease using our Vacuum Melt Spinning System. Ideal for research and experimental work with amorphous and microcrystalline materials. Order now for effective results.
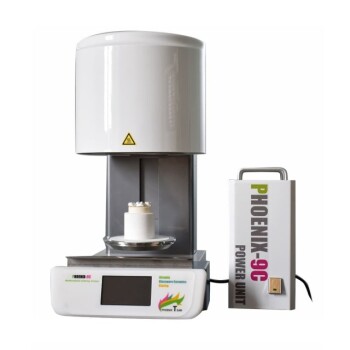
Dental Porcelain Zirconia Sintering Ceramic Furnace Chairside with Transformer
Experience top-notch sintering with Chairside Sintering Furnace with Transformer. Easy to operate, noise-free pallet, and automatic temperature calibration. Order now!
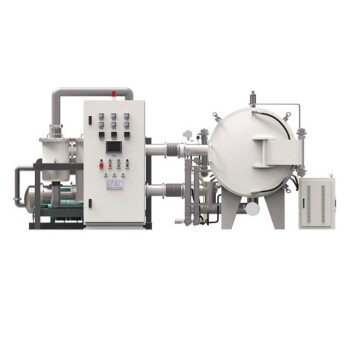
Horizontal High Temperature Graphite Vacuum Graphitization Furnace
Horizontal Graphitization Furnace: This type of furnace is designed with the heating elements placed horizontally, allowing for uniform heating of the sample. It's well-suited for graphitizing large or bulky samples that require precise temperature control and uniformity.
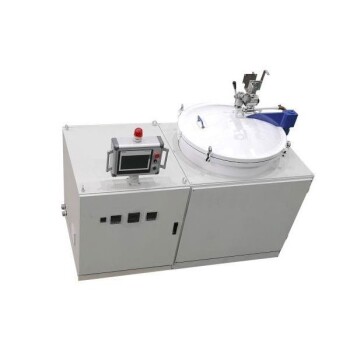
Graphite Vacuum Furnace IGBT Experimental Graphitization Furnace
IGBT experimental graphitization furnace, a tailored solution for universities and research institutions, with high heating efficiency, user-friendliness, and precise temperature control.
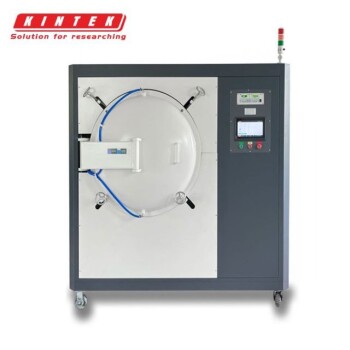
Vacuum Heat Treat Furnace with Ceramic Fiber Liner
Vacuum furnace with polycrystalline ceramic fiber insulation liner for excellent heat insulation and uniform temperature field. Choose from 1200℃ or 1700℃ max. working temperature with high vacuum performance and precise temperature control.
Related Articles
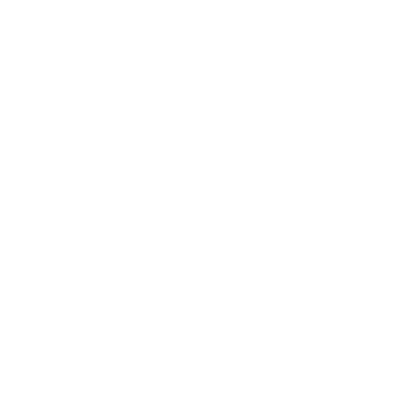
Guide to Bottom Loading Furnace
A bottom loading furnace is a type of industrial furnace that is designed for the efficient processing of materials by heating them to high temperatures.
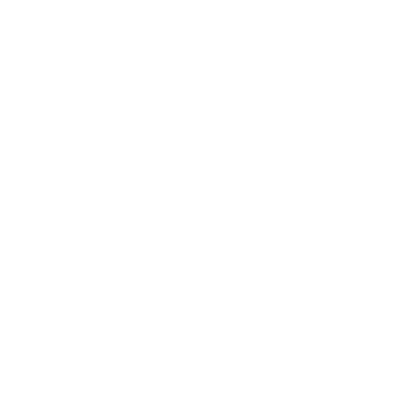
Electric Heating Systems(3): Understanding, Benefits, and Applications
Explore the world of electric heating systems, including electric furnaces, heating elements, and their benefits. Learn about the advantages, disadvantages, and applications of electric heating technology. Discover how electric heating systems work and their role in modern heating solutions.
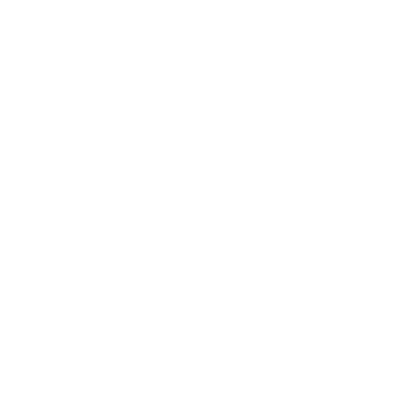
Understanding Electric Heating Systems(1): How Electric Furnaces Work and Their Advantages
Discover how electric heating systems, particularly electric furnaces, work efficiently without the need for flues or chimneys. Explore the benefits and components of electric furnaces, including heating elements, contactors, sequencers, and transformers.
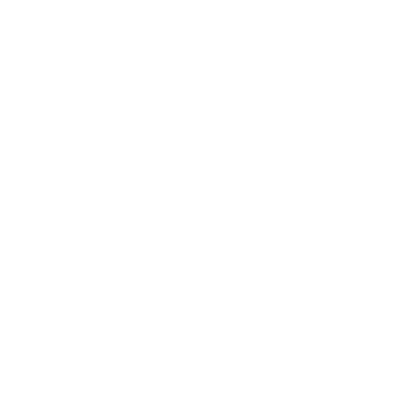
Exploring the Key Performance Indicators of an Atmosphere Furnace
Atmosphere furnaces are specialized pieces of equipment used in a variety of industries for applications such as heat treatment, ceramics, and metallurgy.
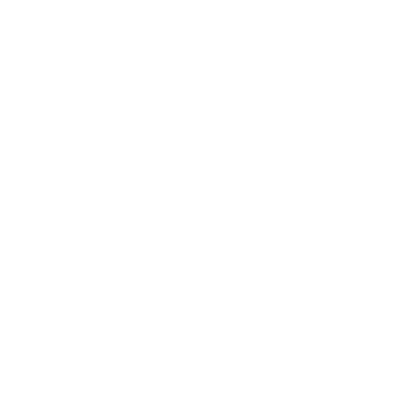
Effective Maintenance Strategies for Vertical Tubular Electric Furnaces
There are several key areas to focus on when it comes to maintaining a multi temperature zone vertical tubular electric furnace.
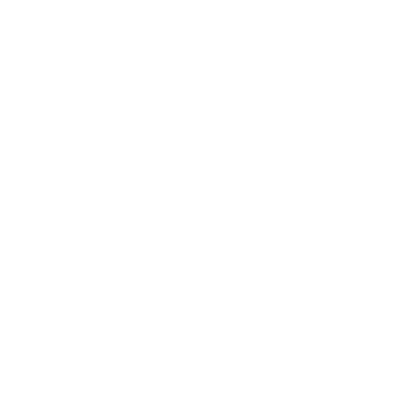
Guide To QUENCHING FURNACE
A quenching furnace is a type of heat treatment furnace that is commonly used in industrial production. It is used to harden or temper materials, and plays an important role in the production process. Quenching furnaces are available in a variety of sizes and configurations, and can be custom-designed to meet the specific needs of the application.
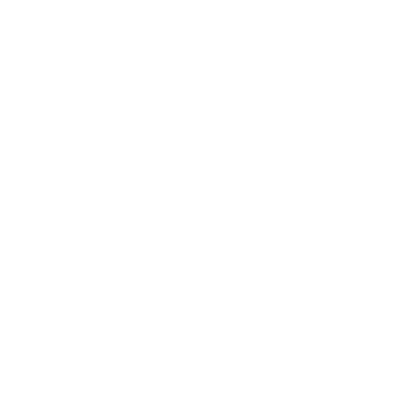
Understanding Electric Heating Systems(2): From Furnaces to Heating Elements
Discover how electric heating systems work, from electric furnaces to heating element basics. Learn about the benefits of electric heating and why it's a viable option for various applications. Find insights on heat treating furnaces and their subassemblies.
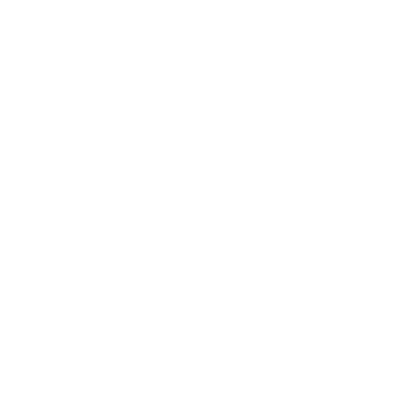
Investigating the Factors Affecting the Slow Temperature Rise in Box Furnaces
Sometimes, the temperature of the furnace may not rise as quickly as expected, or may not be able to reach the desired temperature at all.
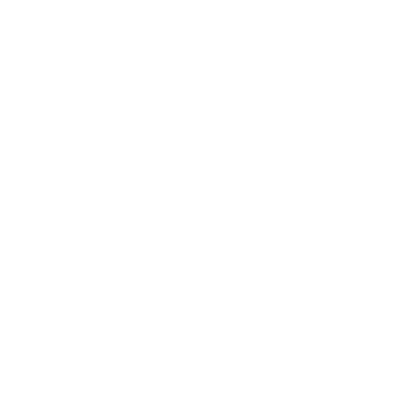
Comprehensive Guide to Atmosphere Furnaces: Types, Applications, and Benefits
Explore the world of atmosphere furnaces with our detailed guide. Learn about their types, applications in metallurgy and beyond, and the benefits they offer for precise material heat treatment.
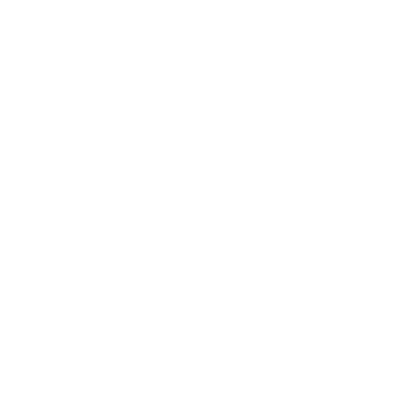
Hydrogen Atmosphere Furnaces: Applications, Safety, and Maintenance
Explore the comprehensive guide on hydrogen atmosphere furnaces, including their applications in high-end alloy sintering, safety measures, and maintenance tips. Learn about the types, components, and operational considerations for optimal performance.
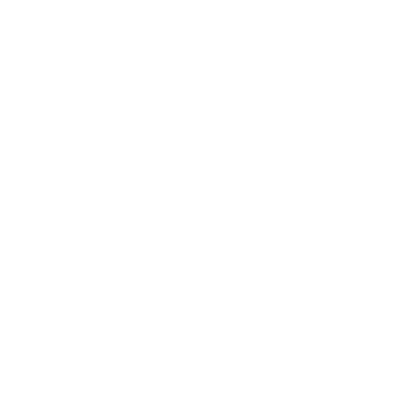
Electric Rotary Kiln Pyrolysis Furnace: Design, Operation, and Applications
Explore the comprehensive guide on electric rotary kiln pyrolysis furnaces, including their design, operation, efficiency factors, and diverse applications in industries like waste processing and biofuel production.
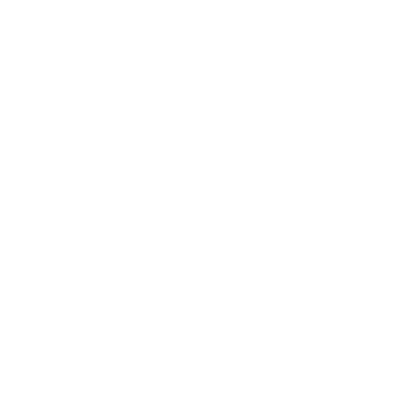
Comprehensive Guide to Hydraulic Hot Press: Function, Features and Applications
Hydraulic hot press is equipped with advanced electronic controls that allow for precise temperature selection and technical control. This enables the machine to automatically carry out processes such as stage temperature adjustment and film pressure control.