Introduction to Electric Heating Systems
Electric heating systems are pivotal in modern heating solutions, employing a variety of resistance-based electric heaters to uphold furnace atmosphere and thermal efficiencies. These systems boast versatility, accommodating different furnace applications and atmospheres through a range of heating elements, from standard open resistance wire types to bayonet/radiant tube styles. Standard features often include SCR power controllers with diagnostic displays, with optional integrations for advanced control systems. Rigorous adherence to NEC and NFPA standards ensures safety, while factory prewiring and testing guarantee reliability. In this article, we delve into the workings and advantages of electric heating systems, focusing particularly on electric furnaces.
How Electric Furnaces Work
Electric furnaces operate similarly to gas furnaces but use electricity to produce heat instead of gas. They contain electric heating elements, which warm the air as it passes through a heat exchanger. The heated air is then distributed throughout the home via ductwork. Unlike gas furnaces, electric furnaces do not require flues, chimneys, or structures for smoke and gas ventilation.
Heating Elements
Heating elements play a crucial role in generating heat within the furnace. These elements, such as electric resistance heaters or gas burners, ensure precise and uniform heating throughout the chamber. This uniform heating is essential for maintaining a consistent temperature required for various heat treatment processes.
Temperature Control System
An electric furnace incorporates a sophisticated temperature control system to monitor and regulate the heat within the chamber. This system ensures that the desired temperature profile is achieved and maintained accurately throughout the entire process. It helps in optimizing energy efficiency and ensures the quality of the heat treatment.
Direct vs. Indirect Heating Furnaces
Direct Heating Furnaces
Direct heating furnaces apply electric power directly to the material itself. Due to the low resistivity of the material, a large current is usually required to meet the heating demand. These furnaces are efficient for specific applications where direct heat transfer is necessary.
Indirect Heating Furnaces
Indirect heating furnaces, on the other hand, connect the power supply to the heating element or other conductive medium, generating heat. The furnace material is then heated indirectly through heat conduction, convection, and radiation. Most of the resistance furnaces available are indirect heating furnaces, offering versatility and controlled heating processes.
Types of Aluminum Melting Furnaces
Aluminum melting furnaces are vital for various industrial applications. One of the popular types is the Induction Furnace:
Induction Furnace
An induction furnace utilizes the induction electrothermal effect of materials to heat or melt substances. Its components include an inductor, furnace body, power supply, capacitor, and control system. Induction furnaces are efficient and widely used in metal melting processes.
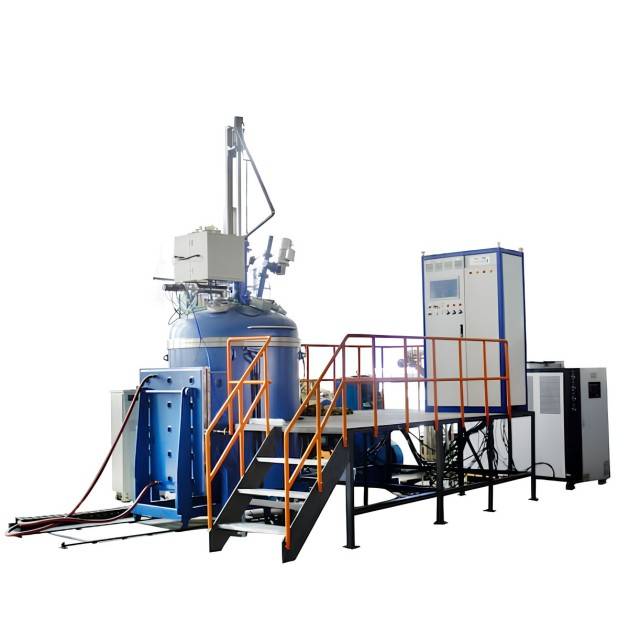
Diverse Applications of Furnaces
Furnaces serve diverse purposes in industries, particularly in heating substances like metals, ores, and alloys for reshaping or modeling. Common types of furnaces include natural gas, oil, electric, and propane furnaces. However, there are numerous specialized furnaces such as electric arc furnaces, vacuum furnaces, and induction furnaces, each designed for specific applications.
Advantages of Electric Furnaces
Electric furnaces offer several advantages over other types:
-
High Temperature Capability: Electric furnaces can reach temperatures exceeding 1800°C in industrial settings and over 3000°C in laboratory units, making them suitable for melting alloys and conducting high-temperature processes.
-
Energy Efficiency: They are energy-efficient as they directly convert electricity into heat without combustion, reducing energy waste and environmental impact.
-
No Ventilation Requirements: Unlike gas furnaces, electric furnaces do not require flues, chimneys, or ventilation structures, simplifying installation and maintenance.
In conclusion, electric furnaces provide reliable and efficient heating solutions for various industrial and laboratory applications, offering precise temperature control and environmental advantages. Their versatility and high-temperature capabilities make them indispensable in modern manufacturing processes.
Advantages of Electric Furnaces
Electric furnaces offer several advantages over other heating systems. Firstly, they are highly efficient, as they do not experience heat loss associated with flues and chimneys. Additionally, they are simple to install and maintain, making them a convenient option for homeowners. Furthermore, electric furnaces do not produce harmful emissions, making them environmentally friendly.
Electric heating systems, including furnaces, employ various styles of resistance type electric heaters to maintain the integrity of the furnace atmosphere and thermal efficiencies. These heaters can be supplied as either standard open resistance wire type or bayonet/radiant tube style based on the specific furnace application, intended atmosphere, and/or customer preference. SCR power controllers with control panel door-mounted diagnostics displays are standard for many electric furnaces, with optional PLC and PC systems integration available. Heating systems are factory prewired to meet NEC and NFPA standards where applicable, and all equipment is factory tested prior to shipment.
Moreover, electric furnaces offer an energy-saving function, benefiting both the environment and the user's wallet. Certain furnaces come equipped with an energy-saving feature that automatically switches to a standby mode, saving up to 40% energy. Users can simply press a button to activate this mode, thereby saving electricity and using other valuable resources efficiently and responsibly. By doing so, they contribute to environmental conservation and reduce electricity bills simultaneously.
Induction furnaces, a subset of electric heating systems, provide additional advantages over conventional electric furnaces. These include:
- Fast Heating: Induction furnaces operate on the principle of electromagnetic induction, which is a quicker process compared to traditional electric or gas heating methods.
- Quick Startup: With an energy-efficient power supply, induction furnaces can provide full power without the need for a warm-up or cooling-down cycle, ensuring a quick startup time.
- Natural Stirring: The medium-frequency electric current created by induction power supplies induces a strong stirring action, resulting in homogeneous mixtures of liquid metal.
- Reduced Refractory Usage: Induction furnaces require less refractory material compared to fuel-fired units, contributing to cost savings and easier maintenance.
- Energy Conservation: Induction furnaces are more efficient than conventional furnaces, capable of reducing power consumption during metal melting processes.
Additionally, it's important to consider the pros and cons of electric furnaces compared to other heating systems:
Pros:
- Environmentally Friendly: Electric furnaces do not produce carbon monoxide emissions, making them environmentally friendly and safe for indoor use without the need for a flue.
- High Efficiency: All electricity used is converted into heat, making electric furnaces 100 percent efficient.
- Simple Installation and Maintenance: Electric furnaces are easy to install and maintain, reducing associated costs and inconvenience.
Cons:
- Higher Operating Costs: Electricity tends to cost more than natural gas, resulting in higher operating costs for electric furnaces over time.
- Dependence on Electricity: Electric furnaces require a stable electricity supply, making them vulnerable to power outages.
In summary, electric furnaces offer numerous advantages, including high efficiency, environmental friendliness, and ease of installation and maintenance. With the additional benefits of energy-saving features and advancements in induction heating technology, electric heating systems continue to be a viable and attractive option for residential and industrial heating needs.
Disadvantages of Electric Furnaces
Despite their advantages, electric furnaces have some drawbacks to consider. One of the main disadvantages is the potentially high cost of electricity compared to other fuel sources. Additionally, electric furnaces may struggle to heat larger spaces efficiently, and they rely on electricity, which can be unreliable during power outages.
Efficient from a heat-loss perspective, electric heating is one of the most efficient sources on the market. An electric heater doesn’t require flues, chimneys, or other structures designed to allow smoke and gasses to escape, since they don’t produce any of these. However, like any other system, there are some caveats that should be considered when opting for an electric furnace.
A second important decision is whether you would like a self-contained unit that requires electricity to operate, or if you are more familiar with using gas than liquid fuels such as propane or natural gas. If you choose the latter, make sure that the equipment can work efficiently without any source of energy other than air and oxygen. Liquid fuel may require an external power supply at times.
Factors to Consider Before Purchasing a Muffle Furnace
-
Business Size and Production:
- Consider the size of your business and how much production you have. This will help determine the furnace size and capacity needed for your operations.
-
Product Requirements:
- What products you make will influence the type of furnace you need. Different products may require different temperature ranges or heating methods.
-
Ease of Use:
- Determine if you can learn to use the furnace properly. Some furnaces may require specialized knowledge or training to operate effectively.
-
Energy Source:
- Consider the energy source required for the furnace. Natural gas is commonly used but electric resistance may be preferred for cost or quality reasons.
-
Cost Analysis:
- Analyze the cost of operating the furnace. Electricity tends to be more expensive than gas in many regions, which can significantly impact operating costs.
-
Technology and Supplier Evaluation:
- Evaluate the specifications of various furnace technologies and suppliers based on your criteria. Rate them accordingly to determine the best-suited option for your needs.
-
Energy Efficiency:
- Consider the energy efficiency of the furnace. Look for energy-saving features or options that can help reduce operating costs.
-
Reliability:
- Evaluate the reliability of the furnace. Consider factors such as maintenance requirements and downtime for repairs.
-
Environmental Impact:
- Consider the environmental impact of the furnace. Look for environmentally friendly options that comply with regulations and standards.
-
Long-Term Costs:
- Consider the long-term costs of operating the furnace. Look for options that offer a good balance between upfront cost and long-term savings.
In conclusion, when choosing a furnace, it's important to consider factors such as business size, production requirements, ease of use, energy source, cost, technology, and reliability. By carefully evaluating these factors, you can select the furnace that best meets your needs and budget.
If you are interested in this product you can browse our company website, as an industry-leading laboratory equipment manufacturer, we are committed to providing the most advanced and high-quality laboratory equipment solutions. Whether you are engaged in scientific research, teaching or industrial production, our products will meet your needs for accurate and reliable laboratory equipment.
CONTACT US FOR A FREE CONSULTATION
KINTEK LAB SOLUTION's products and services have been recognized by customers around the world. Our staff will be happy to assist with any inquiry you might have. Contact us for a free consultation and talk to a product specialist to find the most suitable solution for your application needs!