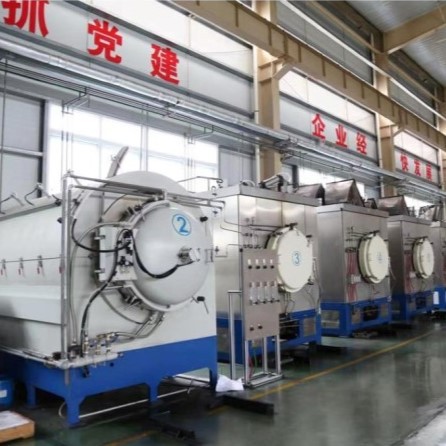
Vacuum Furnace
Vacuum Heat Treat Sintering Brazing Furnace
Item Number : KT-BF
Price varies based on specs and customizations
- Specifications
- Please refer to the chart below for detailed parameters.
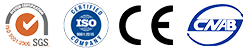
Shipping:
Contact us to get shipping details Enjoy On-time Dispatch Guarantee.
Why Choose Us
Reliable PartnerEasy ordering process, quality products, and dedicated support for your business success.
Introduction
A vacuum brazing furnace is a type of industrial furnace used for brazing, a metalworking process that joins two pieces of metal using a filler metal that melts at a lower temperature than the base metals. Vacuum brazing furnaces are typically used for high-quality applications where a strong, clean joint is required.
Vacuum brazing furnaces operate by creating a vacuum inside the furnace chamber, which removes oxygen and other gases that can interfere with the brazing process. This creates a clean environment that promotes strong, reliable joints. Vacuum brazing furnaces are also capable of achieving very high temperatures, which allows for the brazing of a wide variety of metals, including stainless steel, titanium, and aluminum.
Details & Part
Applications
Vacuum brazing furnaces are widely used in various industries and applications due to their ability to create strong and leak-proof joints. Some of the main application areas include:
- Heating and cooling assemblies
- Micro-channel heat exchangers
- Aircraft components
- Sensors
- Medical devices
- Structural components
- Other thermal products
Features
The vacuum brazing furnace offers numerous benefits that enhance its functionality and value for customers:
- Exceptional temperature uniformity: The furnace's design ensures uniform heating throughout the chamber, resulting in consistent and precise brazing results.
- Efficient heating system: The furnace utilizes a high-performance heating system that rapidly reaches and maintains the desired temperature, reducing cycle times and increasing productivity.
- Advanced vacuum system: The furnace is equipped with a sophisticated vacuum system that effectively removes oxygen and other contaminants from the chamber, ensuring a clean and controlled brazing environment.
- User-friendly interface: The furnace features an intuitive and easy-to-use interface that simplifies operation and monitoring, minimizing the need for extensive training.
- Robust construction: The furnace is constructed from durable materials and components, ensuring longevity and reliability in demanding laboratory environments.
Principle
The vacuum brazing furnace is a horizontal furnace body, composed of a furnace shell, furnace lining, heating element, furnace tank, material tray, vacuum system, and electronic control system. The furnace shell is welded from carbon steel plates and section steel. It is lined with high-quality insulation bricks and refractory bricks and is constructed in three zones. The heating elements are made of iron-chromium-aluminum wire and are arranged in a spiral shape on the wire bricks on both sides and bottom of the furnace. The vacuum system uses a three-stage vacuum pump, which is composed of a vacuum unit, an oil diffusion pump, a Roots pump, a mechanical pump, a pneumatic baffle valve, and a manual butterfly valve.
Advantages
- High-quality joints with minimal voids and excellent mechanical properties
- No need for flux, which eliminates potential contamination and post-brazing cleaning
- Reduced oxidation and scaling, resulting in cleaner joints
- Precise temperature control, which allows for the joining of materials with different melting points
- Suitable for joining complex components and assemblies
- The environmentally friendly process with minimal waste generation
Technical specification
Rated power | 100 Kw |
Rated temperature | 700 ℃ |
Power supply | 380 V, 50 Hz |
Working area size | Φ820×1700㎜ |
Cold ultimate vacuum | 6.67×10-3Pa |
Pressure rise rate | 2pa/h |
Temperature control accuracy | ±1℃ |
FAQ
What Is A Vacuum Furnace Used For?
What Are The Advantages Of Vacuum Brazing?
What Materials Can Be Vacuum Brazed?
What Is The Difference Between A Cold-walled And Hot-walled Vacuum Furnace?
What Is The Process Of A Vacuum Furnace?
What Is The Purpose Of A Vacuum Hot Press Furnace?
How Does A Vacuum Induction Melting Furnace Work?
What Gas Is Used In A Vacuum Furnace?
What Are The Advantages Of A Vacuum Hot Press Furnace?
What Are The Advantages Of Vacuum Induction Melting?
What Is The Heating Element Used In A Vacuum Furnace?
How Does A Vacuum Hot Press Furnace Work?
How Does Vacuum Help In Induction Melting Furnace?
What Are The Common Applications Of Vacuum Hot Press Furnaces?
What Is Vacuum Induction Melting Furnace?
What Factors Should Be Considered When Selecting A Vacuum Hot Press Furnace?
4.9
out of
5
This vacuum brazing furnace is a game-changer for our laboratory. The speed of delivery was exceptional, and the quality of the product is top-notch.
4.8
out of
5
I'm impressed with the value for money I got with this vacuum brazing furnace. It's a durable and technologically advanced piece of equipment that has significantly improved our research capabilities.
4.7
out of
5
The vacuum brazing furnace from KINTEK SOLUTION is a valuable asset to our laboratory. Its user-friendly interface and efficient heating system make it a delight to use.
4.6
out of
5
The vacuum brazing furnace has exceeded our expectations. The exceptional temperature uniformity ensures consistent and precise brazing results.
4.8
out of
5
Thank you, KINTEK SOLUTION, for providing us with such an exceptional vacuum brazing furnace. The advanced vacuum system guarantees a clean and controlled brazing environment, leading to high-quality joints.
4.7
out of
5
The vacuum brazing furnace is a lifesaver for our laboratory. Its ability to join complex components and assemblies has opened up new possibilities for our research.
4.9
out of
5
I highly recommend the vacuum brazing furnace from KINTEK SOLUTION. The precise temperature control allows us to join materials with different melting points with ease.
4.8
out of
5
The vacuum brazing furnace has transformed our laboratory. The reduced oxidation and scaling result in cleaner joints, saving us valuable time and resources.
4.7
out of
5
The environmentally friendly process of the vacuum brazing furnace aligns perfectly with our laboratory's sustainability goals. Minimal waste generation is a major plus.
4.6
out of
5
The vacuum brazing furnace has proven to be a reliable and durable workhorse in our laboratory. Its robust construction ensures longevity and peace of mind.
4.8
out of
5
The vacuum brazing furnace is an indispensable tool for our laboratory. Its exceptional performance and technological advancements have taken our research to the next level.
4.7
out of
5
The vacuum brazing furnace from KINTEK SOLUTION is a valuable investment for any laboratory. Its high-quality joints and minimal voids ensure the integrity of our research.
4.6
out of
5
The vacuum brazing furnace has streamlined our laboratory processes. Its efficient heating system reduces cycle times, allowing us to maximize our productivity.
4.8
out of
5
The vacuum brazing furnace is a testament to KINTEK SOLUTION's commitment to innovation. Its user-friendly interface and robust construction make it an exceptional choice for any laboratory.
Products
Vacuum Heat Treat Sintering Brazing Furnace
REQUEST A QUOTE
Our professional team will reply to you within one business day. Please feel free to contact us!
Related Products
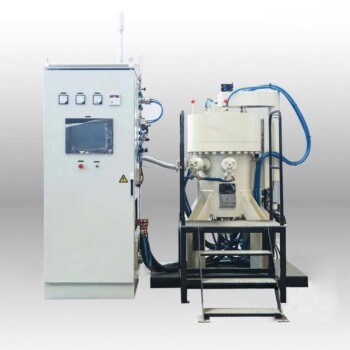
Vacuum Heat Treat and Sintering Furnace with 9MPa Air Pressure
The air pressure sintering furnace is a high-tech equipment commonly used for the sintering of advanced ceramic materials. It combines vacuum sintering and pressure sintering techniques to achieve high-density and high-strength ceramics.
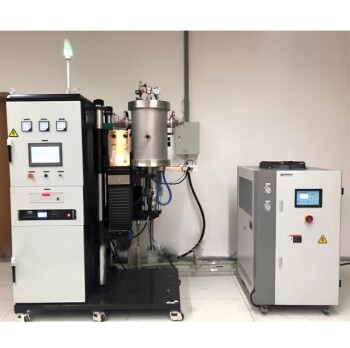
Vacuum Heat Treat and Molybdenum Wire Sintering Furnace for Vacuum Sintering
A vacuum molybdenum wire sintering furnace is a vertical or bedroom structure, which is suitable for withdrawal, brazing, sintering and degassing of metal materials under high vacuum and high temperature conditions. It is also suitable for dehydroxylation treatment of quartz materials.
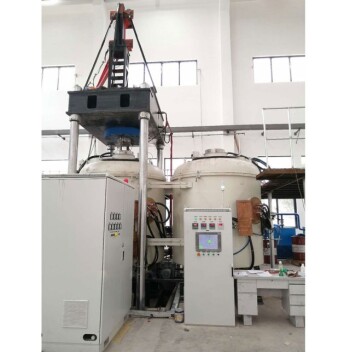
600T Vacuum Induction Hot Press Furnace for Heat Treat and Sintering
Discover the 600T Vacuum Induction Hot Press Furnace, designed for high-temperature sintering experiments in vacuum or protected atmospheres. Its precise temperature and pressure control, adjustable working pressure, and advanced safety features make it ideal for nonmetal materials, carbon composites, ceramics, and metal powders.
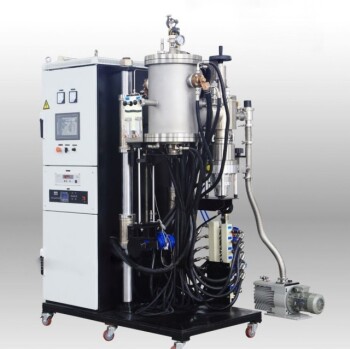
Small Vacuum Heat Treat and Tungsten Wire Sintering Furnace
The small vacuum tungsten wire sintering furnace is a compact experimental vacuum furnace specially designed for universities and scientific research institutes. The furnace features a CNC welded shell and vacuum piping to ensure leak-free operation. Quick-connect electrical connections facilitate relocation and debugging, and the standard electrical control cabinet is safe and convenient to operate.
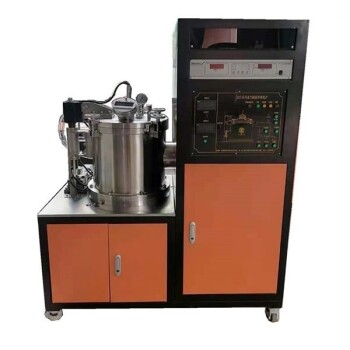
Vacuum Heat Treat Furnace and Levitation Induction Melting Furnace
Experience precise melting with our Vacuum Levitation Melting Furnace. Ideal for high melting point metals or alloys, with advanced technology for effective smelting. Order now for high-quality results.
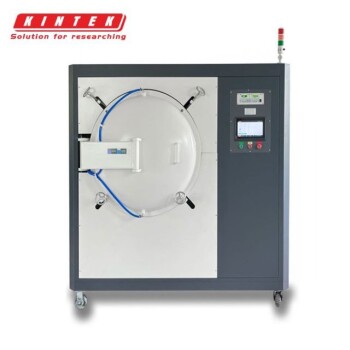
Vacuum Heat Treat Furnace with Ceramic Fiber Liner
Vacuum furnace with polycrystalline ceramic fiber insulation liner for excellent heat insulation and uniform temperature field. Choose from 1200℃ or 1700℃ max. working temperature with high vacuum performance and precise temperature control.
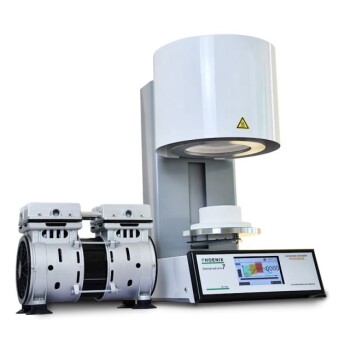
Vacuum Dental Porcelain Sintering Furnace
Get precise and reliable results with KinTek's Vacuum Porcelain Furnace. Suitable for all porcelain powders, it features hyperbolic ceramic furnace function, voice prompt, and automatic temperature calibration.
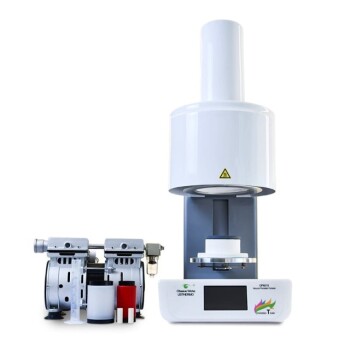
Dental Porcelain Zirconia Sintering Ceramic Vacuum Press Furnace
Get precise dental results with Dental Vacuum Press Furnace. Automatic temperature calibration, low noise tray, and touch screen operation. Order now!
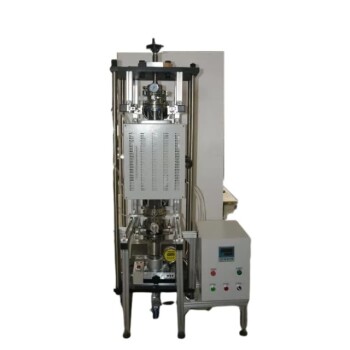
Vacuum Hot Press Furnace Heated Vacuum Press Machine Tube Furnace
Reduce forming pressure & shorten sintering time with Vacuum Tube Hot Press Furnace for high-density, fine-grain materials. Ideal for refractory metals.
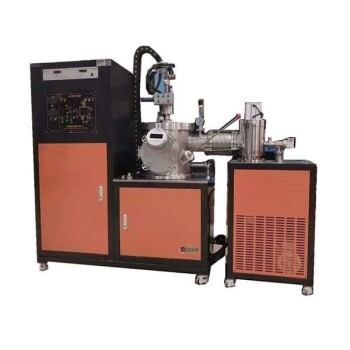
Vacuum Arc Induction Melting Furnace
Discover the power of Vacuum Arc Furnace for melting active & refractory metals. High-speed, remarkable degassing effect, and free of contamination. Learn more now!
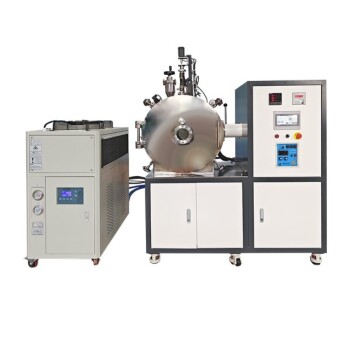
Lab-Scale Vacuum Induction Melting Furnace
Get precise alloy composition with our Vacuum Induction Melting Furnace. Ideal for aerospace, nuclear energy, and electronic industries. Order now for effective smelting and casting of metals and alloys.
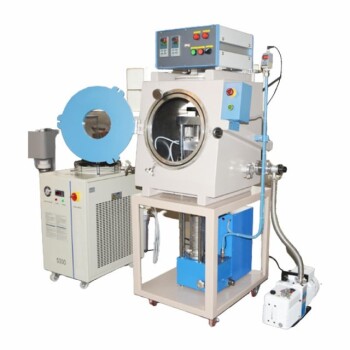
Vacuum Hot Press Furnace Machine for Lamination and Heating
Experience clean and precise lamination with Vacuum Lamination Press. Perfect for wafer bonding, thin-film transformations, and LCP lamination. Order now!
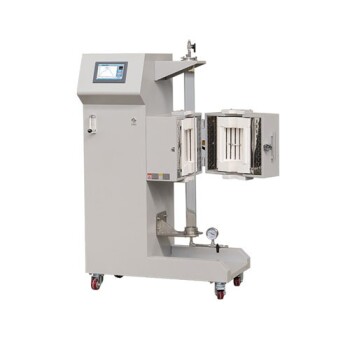
Vertical Laboratory Quartz Tube Furnace Tubular Furnace
Elevate your experiments with our Vertical Tube Furnace. Versatile design allows for operation under various environments and heat treatment applications. Order now for precise results!
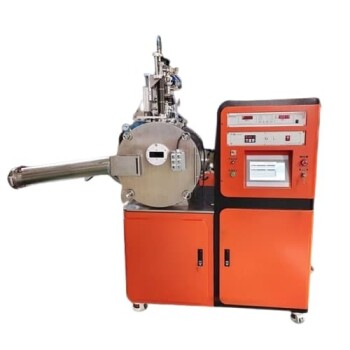
Vacuum Induction Melting Spinning System Arc Melting Furnace
Develop metastable materials with ease using our Vacuum Melt Spinning System. Ideal for research and experimental work with amorphous and microcrystalline materials. Order now for effective results.
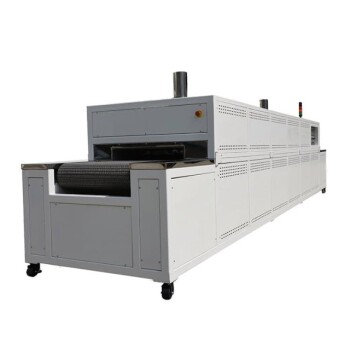
Mesh belt controlled atmosphere furnace
Discover our KT-MB mesh belt sintering furnace - perfect for high-temperature sintering of electronic components & glass insulators. Available for open air or controlled atmosphere environments.
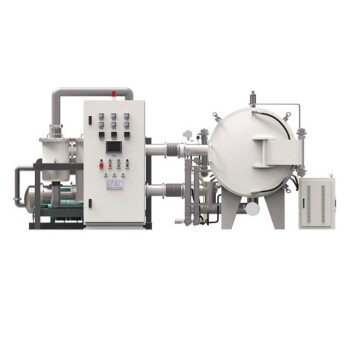
Horizontal High Temperature Graphite Vacuum Graphitization Furnace
Horizontal Graphitization Furnace: This type of furnace is designed with the heating elements placed horizontally, allowing for uniform heating of the sample. It's well-suited for graphitizing large or bulky samples that require precise temperature control and uniformity.
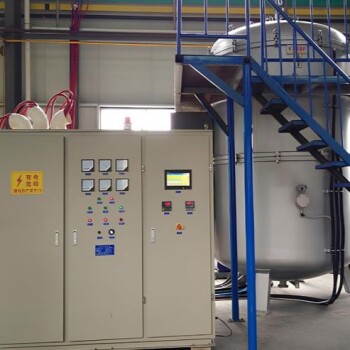
Large Vertical Graphite Vacuum Graphitization Furnace
A large vertical high-temperature graphitization furnace is a type of industrial furnace used for the graphitization of carbon materials, such as carbon fiber and carbon black. It is a high-temperature furnace that can reach temperatures of up to 3100°C.
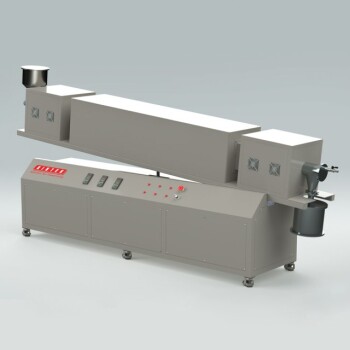
Vacuum Sealed Continuous Working Rotary Tube Furnace Rotating Tube Furnace
Experience efficient material processing with our vacuum-sealed rotary tube furnace. Perfect for experiments or industrial production, equipped with optional features for controlled feeding and optimized results. Order now.
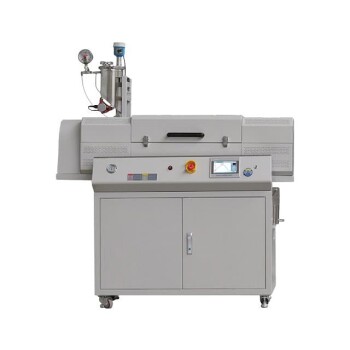
Laboratory Vacuum Tilt Rotary Tube Furnace Rotating Tube Furnace
Discover the versatility of Laboratory Rotary Furnace: Ideal for calcination, drying, sintering, and high-temperature reactions. Adjustable rotating and tilting functions for optimal heating. Suitable for vacuum and controlled atmosphere environments. Learn more now!
Related Articles
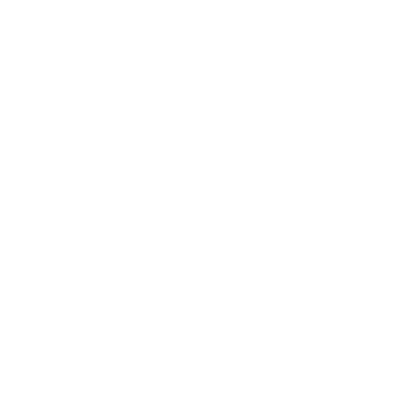
Mastering Vacuum Furnace Brazing: Techniques, Applications, and Advantages
Unlock the full potential of vacuum furnace brazing with our comprehensive guide. Learn about its technology, advantages, applications, and how brazing ovens are used. Explore the principles behind vacuum brazing furnaces and their exceptional features.
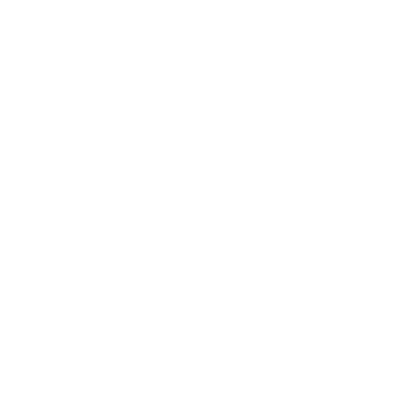
Vacuum Induction Furnace Fault Inspection: Essential Procedures and Solutions
Discover the essential procedures for inspecting and troubleshooting common faults in vacuum induction furnace. Learn how to troubleshoot electrical failures, conduct post-operation inspections, maintain records, and monitor the furnace's operation. Take corrective actions to ensure the furnace's optimal performance. Find expert solutions for temperature abnormalities, vacuum level deviations, and furnace chamber inspections.
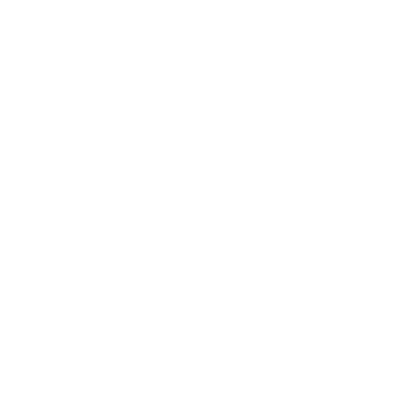
Materials Science with the Lab Vacuum Furnace
A vacuum furnace is a specialized type of furnace that is designed to operate in a vacuum environment. This means that the furnace is sealed and the air inside is pumped out, creating a low pressure or vacuum inside.
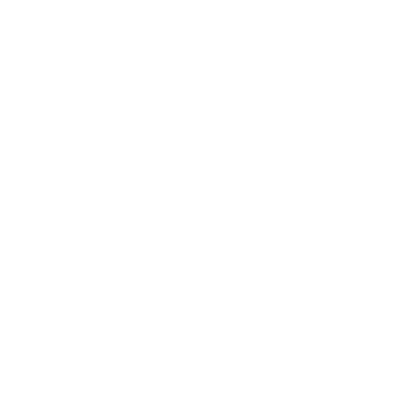
Vacuum Induction Melting Furnace: Principle, Advantages, and Applications
Discover the Vacuum Induction Melting Furnace, a specialized equipment that employs vacuum and induction heating to refine metals and alloys, ensuring high purity and precise composition control. Explore its principle, advantages, applications, and components in this comprehensive guide.
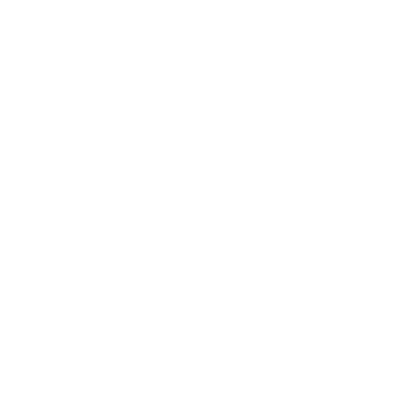
Vacuum Melting Furnace: A Comprehensive Guide to Vacuum Induction Melting
Discover the intricacies of vacuum induction melting furnaces, their components, operation, advantages, and applications. Explore how these furnaces revolutionize metal processing and achieve exceptional material properties.
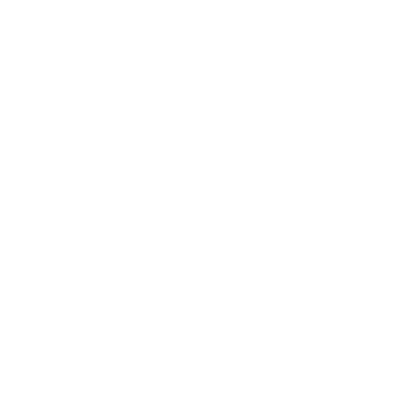
Vacuum Hot Press Furnace: A Comprehensive Guide
Gain in-depth knowledge of Vacuum Hot Press Furnaces, their components, benefits, and applications in various industries. Explore how these furnaces revolutionize material processing and achieve exceptional results.
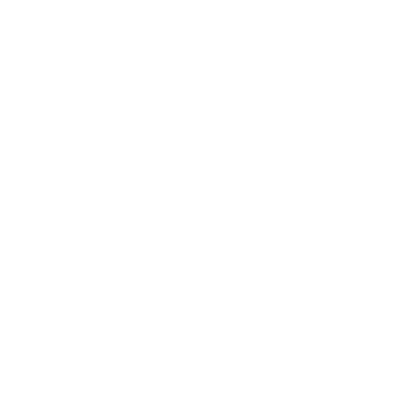
Vacuum Laboratory Furnaces in Advanced Materials Research
In addition to size, there are several other key differences between industrial-scale and laboratory vacuum furnaces
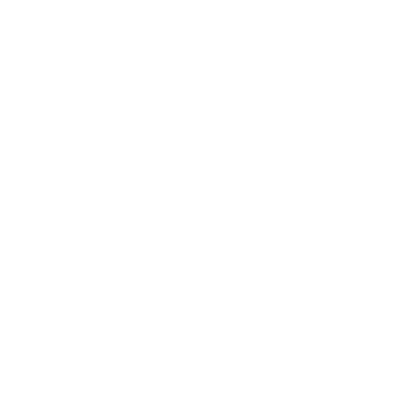
Comprehensive Guide to Vacuum Hot Press Furnace Application
The Vacuum Hot Press Furnace is a versatile tool especially suited for sintering experiments involving non-metallic materials, carbon composites, ceramic materials and metal powder materials.
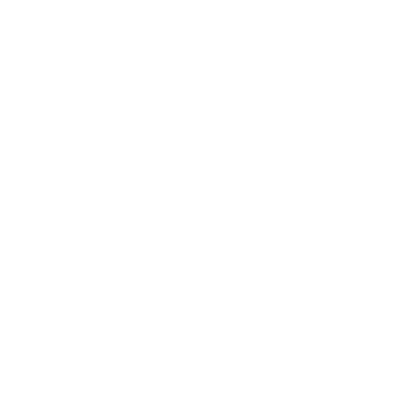
Exploring Tungsten Vacuum Furnaces: Operation, Applications, and Advantages
Discover the operation, applications, and benefits of tungsten vacuum furnaces in laboratory settings. Learn about KinTek's advanced features, control mechanisms, and the use of tungsten in high-temperature environments.
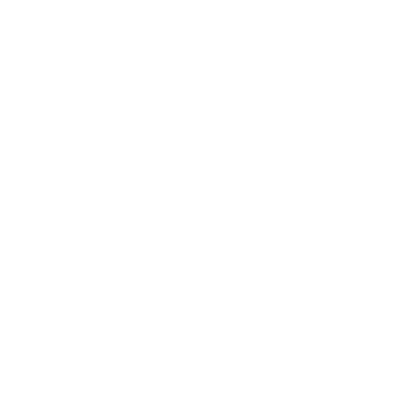
Vacuum Induction Melting Furnace vs Arc Melting Furnace: Choosing the Right Equipment for Your Process
Learn about the key differences between vacuum induction melting furnaces and arc melting furnaces, including their advantages and applications, to help you choose the best equipment for your specific needs.
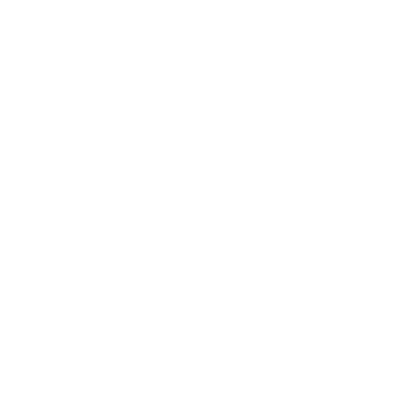
Evaluating the Pros and Cons of External Vacuum Heat Treatment Furnaces
we evaluate the pros and cons of using external vacuum heat treatment furnaces to help manufacturers determine if it is the right choice for their specific process.
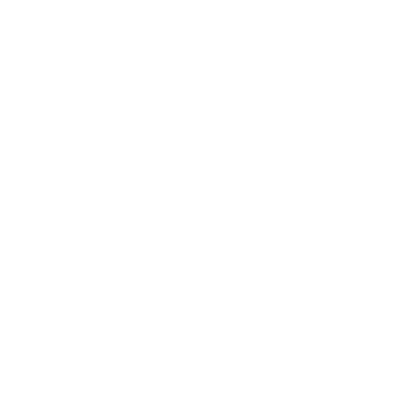
The Ultimate Guide to Vacuum Pressure Sintering Furnace: Benefits, Applications, and Working Principle
Discover the benefits, applications, and working principle of vacuum pressure sintering furnace. Learn how vacuum sintering produces clean, bright parts with incredible design flexibility and quick turnaround, and its applications in teaching, scientific research, and production. Explore the precise setting and monitoring of process parameters, and the advantages of sintering under vacuum and pressure. Find out how vacuum sintering furnace is perfect for higher temperature sintering applications and for sintering extremely reactive materials.