Table of Contents
Introduction: Vacuum Induction Melting Furnace
Vacuum Induction Melting (VIM) furnaces are specialized equipment that leverage vacuum and induction heating to refine metals and alloys with exceptional precision and purity. VIM technology offers significant advantages over traditional melting methods, including the ability to prevent oxidation and contamination, ensuring the production of high-quality materials. This comprehensive guide explores the principle, advantages, components, and diverse applications of VIM furnaces, highlighting their crucial role in industries demanding high-performance materials and precise control over alloy composition.
Principle of Operation
Medium Frequency Induction Heating
Medium frequency induction heating is a process that uses an alternating electromagnetic field to generate heat within a conductive material. In the context of vacuum induction melting furnaces, an induction coil surrounds the crucible containing the metal or alloy to be melted. When an alternating current flows through the coil, it creates a magnetic field that induces eddy currents in the metal. These eddy currents cause the metal to heat up rapidly and melt.
The frequency of the alternating current used in medium frequency induction heating furnaces typically ranges from 1 kHz to 10 kHz. This frequency range is high enough to generate sufficient eddy currents for efficient heating but low enough to minimize energy losses due to skin effect.
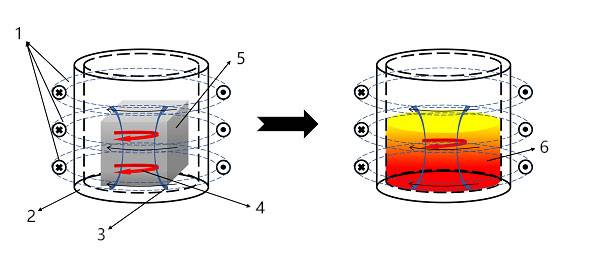
Role of Vacuum Environment
The vacuum environment in a vacuum induction melting furnace is essential for preventing oxidation and contamination of the molten metal. Oxidation occurs when the molten metal reacts with oxygen in the atmosphere, forming metal oxides that can compromise the material's properties. Similarly, contamination can occur when the molten metal comes into contact with impurities in the atmosphere.
By creating a vacuum environment, the furnace prevents these reactions from occurring. The vacuum also allows for the removal of dissolved gases from the molten metal, which can further improve its properties.
Overall, the combination of medium frequency induction heating and a vacuum environment provides a controlled and efficient method for melting metals and alloys, resulting in high-purity and high-quality materials.
Advantages of Vacuum Induction Melting
High Purity and Quality
Vacuum Induction Melting (VIM) offers superior purity and quality in melted materials. The vacuum environment prevents contamination from oxygen, nitrogen, and other atmospheric gases. This results in a cleaner, more homogeneous melt, devoid of harmful inclusions and impurities that could compromise mechanical properties.
Precise Temperature Control
VIM allows for precise temperature control during the melting process. The induction heating system ensures consistent and repeatable results, crucial for producing materials with specific properties and compositions.
Versatile Material Compatibility
VIM furnaces can handle a wide range of materials, including metals, alloys, and even ceramics. This versatility makes it suitable for various applications, from aerospace components to high-temperature alloys and magnet materials.
Energy Efficiency
The induction heating system in VIM furnaces is highly energy-efficient. This reduces operating costs and minimizes environmental impact.
Compact Design
VIM furnaces are relatively compact compared to other melting methods. This makes them suitable for space-constrained environments or mobile applications.
Ease of Operation
VIM furnaces are designed for ease of use, with intuitive controls and automated features that simplify operation.
Safety Features
VIM furnaces incorporate safety features such as over-temperature protection and emergency shutdown mechanisms to ensure safe operation.
Additional Advantages
- Vacuum environment: Prevents oxidation and degassing.
- High-temperature capability: Suitable for melting high-melting-point alloys.
- Electromagnetic stirring: Minimizes element segregation during melting.
- Removal of volatile trace elements: Harmful elements like antimony and bismuth can be removed by controlling the vacuum environment.
Components of a Vacuum Induction Melting Furnace
Furnace Body
- Water-cooled interlayer to maintain low surface temperatures
- Side door for easy access (optional)
- Alloy feeder and observation window on the furnace cover
Inductor
- Spiral coil made from thick-walled copper tubes
- Ceramic coating for insulation and extended service life
Furnace Tilting Mechanism
- Manual, electric, or hydraulic options
- 105-degree forward and 10-degree backward tilt angle
- Adjustable tilting speed
Vacuum System
- Consists of mechanical pump, roots pump, diffusion pump (or booster diffusion pump), vacuum valve, damping elastic sleeve, and vacuum pipeline
- Configured according to the properties and process of the materials being smelted
Medium Frequency Power Supply
- IGBT medium frequency power unit
- Maximum temperature: 2000°C
Electrical Control
- Touch screen controller with PLC
- Vacuum measuring instrument, temperature measuring instrument, operation buttons, indicator lights
- Controls for pneumatic system, vacuum system, furnace cover lifting, and furnace tilting
Safety Features
- Precise temperature control
- Vacuum environment prevents oxidation and degassing
- Electromagnetic stirring avoids element segregation
- Removal of harmful trace elements
Applications of Vacuum Induction Melting Furnaces
Vacuum induction melting furnaces are widely used in various research and production fields, including:
Aerospace Components Casting Vacuum induction melting furnaces are used to cast aerospace components due to their ability to produce high-purity, homogeneous metal ingots. These ingots are then used to manufacture critical components for aircraft, missiles, and satellites.
Complex Valves for Extreme Conditions These furnaces are employed to manufacture complex valves designed to withstand extreme conditions encountered in industries such as oil and gas, aerospace, and chemical processing. The vacuum environment ensures the production of high-quality valves with precise dimensions and corrosion resistance.
Refining High-Purity Metals and Alloys Vacuum induction melting furnaces play a crucial role in refining metals and alloys, removing impurities and achieving high levels of purity. This process is essential for applications in industries such as electronics, medical devices, and aerospace.
Production of Electrodes for Remelting Vacuum induction melting furnaces are used to produce electrodes for remelting processes, particularly in the production of high-quality steel and superalloys. The electrodes are melted in a vacuum environment, resulting in high-purity material with minimal contamination.
Nickel and Special Steel Production These furnaces are widely used in the production of nickel and special steels due to their ability to control the composition and properties of the molten metal precisely. The vacuum environment prevents oxidation and contamination, ensuring the production of high-quality alloys.
Precision Alloy Fabrication Vacuum induction melting furnaces are essential for fabricating precision alloys used in various industries, including aerospace, electronics, and medical devices. These alloys require precise control over composition and properties, which can be achieved through vacuum induction melting.
Active Metal Processing Active metals, such as titanium and zirconium, are highly reactive and require specialized melting techniques. Vacuum induction melting furnaces provide a controlled environment that prevents oxidation and contamination, allowing for the safe and efficient processing of these metals.
High-Temperature Alloy Development Vacuum induction melting furnaces are used to develop and produce high-temperature alloys for applications in aerospace, power generation, and other industries. These alloys require precise control over composition and properties to withstand extreme temperatures and harsh environments.
Magnet Material Creation Vacuum induction melting furnaces are employed in the creation of magnet materials, such as neodymium magnets and samarium-cobalt magnets. The vacuum environment ensures the production of high-purity materials with the desired magnetic properties.
Safety Advantages of Vacuum Induction Melting
Vacuum induction melting furnaces offer numerous safety advantages over traditional melting methods, making them a preferred choice for various industrial applications. These advantages include:
-
Precise control of alloy composition: The ability to precisely control the atmosphere inside the vacuum chamber allows for accurate and consistent alloying. This is crucial for producing high-performance materials with specific properties.
-
Inhibition of non-metallic oxide inclusions: The vacuum environment inhibits the formation of non-metallic oxide inclusions, which can significantly degrade the quality of castings. This results in high-quality castings with improved strength and durability.
-
Electromagnetic stirring: Electromagnetic stirring is a unique feature of vacuum induction melting furnaces that prevents element segregation during alloy smelting. This ensures a homogeneous melt and improves the overall quality of the material.
-
Removal of harmful volatile trace elements: Vacuum induction melting can selectively remove harmful volatile trace elements, such as antimony, tellurium, and selenium, through controlled evaporation. This process purifies the molten metal and enhances the material's properties.
CONTACT US FOR A FREE CONSULTATION
KINTEK LAB SOLUTION's products and services have been recognized by customers around the world. Our staff will be happy to assist with any inquiry you might have. Contact us for a free consultation and talk to a product specialist to find the most suitable solution for your application needs!