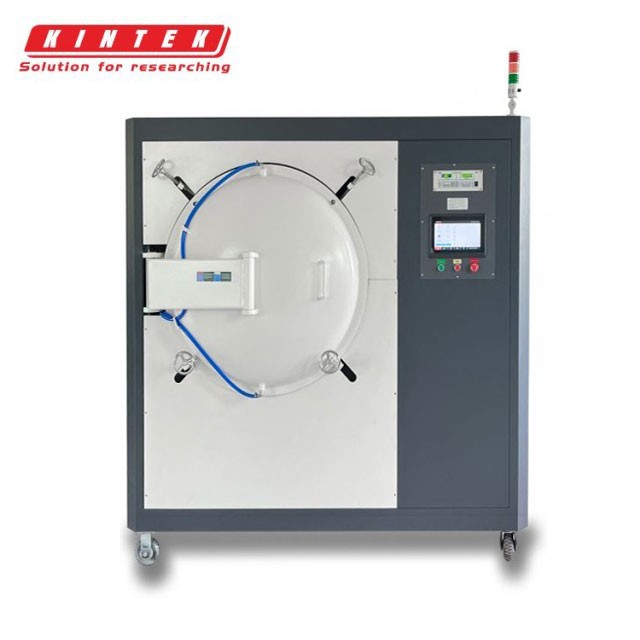
Vacuum Furnace
Vacuum Heat Treat Furnace with Ceramic Fiber Liner
Item Number : KT-VF
Price varies based on specs and customizations
- Max. temperature
- 1200 / 1700℃
- Constant work temperature
- 1100 / 1600℃
- Heating rate
- 0-20 ℃/min
- Effective volume
- 1-512 L
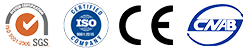
Shipping:
Contact us to get shipping details Enjoy On-time Dispatch Guarantee.
Why Choose Us
Reliable PartnerEasy ordering process, quality products, and dedicated support for your business success.
Introduction
A vacuum furnace with ceramic fiber lining is a type of vacuum furnace that uses ceramic fiber as its insulation liner. Ceramic fiber is a lightweight, porous material with excellent thermal insulation properties. This makes it an ideal material for use in vacuum furnaces, where it helps to reduce heat loss and improve temperature uniformity.
Vacuum furnace with ceramic fiber liner has 2 working temperature range, one is 1200℃ max. Working temperature,which applies Cr2Al2Mo2 resistance wire coil heating elements and polycrystalline ceramic fiber liners; one is 1700℃ max. Working temperature, which applies Molybdenum Disilicide heating elements and polycrystalline ceramic fiber liners.
Vacuum furnaces with ceramic fiber lining are used in a variety of applications, including:
- Vacuum heat treatment
- Vacuum brazing
- Sintering
- Degassing
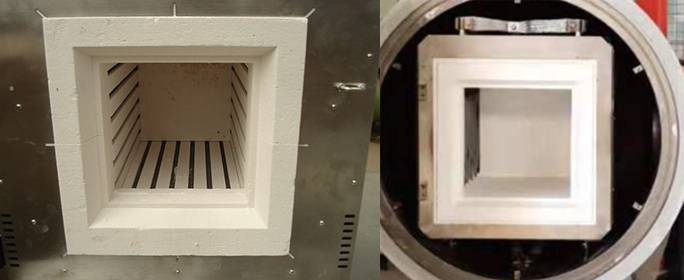
Furnace chamber adopts high-density light alumina ceramic fiber, stable structure, thermal shock performance and thermal stability;Good performance, low heat capacity, low thermal conductivity, energy saving of more than 50% compared with traditional silicon carbide furnace.
Applications
Vacuum furnaces lined with ceramic fiber are widely used in various industries for a range of applications, including:
- Heat Treatment:** Hardening, tempering, annealing
- Brazing:** Joining of metal components in a vacuum environment
- Sintering:** Bonding of powder materials under controlled temperature and pressure
- Degassing:** Removal of gases from materials, such as metals and ceramics
- High-temperature processing:** Vacuum furnaces enable precise temperature control and a clean, safe environment for processing materials at high temperatures
Features
KinTek vacuum furnaces offer precise temperature control, excellent temperature uniformity, and a wide range of applications for labs, universities, and any small-scale production application using industrial furnace models. Each standard and customized vacuum furnace offers the following features and benefits:
- Excellent temperature accuracy and uniformity
- Energy efficient ceramic fiber insulation
- Auto shut-off safety feature
These furnaces offer a number of advantages over traditional vacuum furnaces, including:
- No surface oxidation or discoloration
- Minimal distortion
- Flux free brazing
- Repeatable quality
- Clean, safe, quiet and efficient
Principle
The vacuum furnace with ceramic fiber lining uses a heating element made of resistance wire or molybdenum disilicide to heat the furnace chamber. The ceramic fiber lining insulates the furnace chamber, minimizing heat loss. The furnace is equipped with a vacuum pump that evacuates the air from the furnace chamber, creating a vacuum environment. This vacuum environment prevents the oxidation of the materials being heated and allows for precise temperature control. The furnace is also equipped with a temperature controller that regulates the temperature of the furnace chamber.
Advantages
- No surface oxidation or discoloration: The vacuum environment prevents oxygen from reaching the workpiece, eliminating oxidation and discoloration.
- Minimal distortion:The uniform heating and cooling rates minimize thermal stresses, reducing distortion.
- Flux free brazing:Vacuum furnaces allow for fluxless brazing, eliminating the need for post-brazing cleaning.
- Repeatable quality: The controlled atmosphere and precise temperature control ensure consistent and repeatable results.
- Clean, safe, quiet and efficient:Vacuum furnaces operate in a closed environment, minimizing noise and emissions. They also offer improved energy efficiency due to the reduced heat loss.
- Excellent heat insulating property:Polycrystalline ceramic fiber liners provide excellent thermal insulation, resulting in reduced heat loss and energy savings.
- Outstanding uniformity of temperature field:The ceramic fiber lining promotes uniform temperature distribution throughout the furnace chamber.
- High vacuum performance:Vacuum levels up to 6*10-3Pa ensure effective removal of gases and contaminants.
- Excellent vacuum pressure maintaining performance:** The low vacuum pressure rise rate (0.67Pa/h) maintains a stable vacuum environment.
- PID programmable microprocessor temperature control system:Precise temperature control ensures accurate and reliable heating.
- Safety interlock system:Automatic power shut-off in case of door opening, over temperature, or sensor failure ensures safe operation.
Vacuum Furnace Safety Advantage
- Kindle Tech vacuum furnace owns over current protection, over temperature alarming function, furnace will turn off the power automatically
- Furnace build in thermal couple detecting function, furnace will stop heating and alarm will be on once broken or failure detected
- Power failure restarting function,furnace will resume the furnace heating program when power is incoming after failure
Technical specifications
Furnace model | KT-VF12/KT-VF17 |
---|---|
Max. temperature | 1200/1700℃ |
Constant work temperature | 1100/1600℃ |
Chamber material | Ceramic polycrystalline fiber |
Heating element | Cr2Al2Mo2 wire coil/Molybdenum Disilicide |
Heating rate | 0-20℃/min |
Temperature sensor | Build in K/B type thermal couple |
Temperature controller | Touch screen PID controller with PLC |
Temperature control accuracy | ±1℃ |
Temperature uniformity | ±5℃ |
Electric power supply | AC110-440V,50/60HZ |
Standard Chamber Sizes Stocks | |||
---|---|---|---|
Chamber size (mm) | Effective volume (L) | Chamber size (mm) | Effective volume (L) |
100x100x100 | 1 | 400x400x500 | 80 |
150x150x200 | 4.5 | 500x500x600 | 125 |
200x200x300 | 12 | 600x600x700 | 253 |
300x300x400 | 36 | 800x800x800 | 512 |
Customer design sizes and volume is accepted |
Optional Setup
- Independent furnace temperature monitoring and recording
- RS 485 communication port for PC remote control and data exporting
- Optional pneumatic vacuum valve linkage with temperature controller
- Touch screen temperature controller with versatile operator friendly functions
- Cold water circulation cooling machine for furnace shell jacket cooling system
Warnings
Operator safety is the top important issue! Please operate the equipment with cautions. Working with inflammable& explosive or toxic gases is very dangerous, operators must take all necessary precautions before starting the equipment. Working with positive pressure inside the reactors or chambers is dangerous, operator must fellow the safety procedures strictly. Extra caution must also be taken when operating with air-reactive materials, especially under vacuum. A leak can draw air into the apparatus and cause a violent reaction to occur.
Designed for You
KinTek provide deep custom made service and equipment to worldwide customers, our specialized teamwork and rich experienced engineers are capable to undertake the custom tailoring hardware and software equipment requirements, and help our customer to build up the exclusive and personalized equipment and solution!
Would you please drop your ideas to us, our engineers are ready for you now!
FAQ
What Is A Vacuum Furnace Used For?
What Is The Process Of A Vacuum Furnace?
What Is The Purpose Of A Vacuum Hot Press Furnace?
What Gas Is Used In A Vacuum Furnace?
What Are The Advantages Of A Vacuum Hot Press Furnace?
What Is The Heating Element Used In A Vacuum Furnace?
How Does A Vacuum Hot Press Furnace Work?
What Are The Common Applications Of Vacuum Hot Press Furnaces?
What Factors Should Be Considered When Selecting A Vacuum Hot Press Furnace?
4.8
out of
5
I love the quality and durability of this vacuum furnace. It's a great value for the money.
4.7
out of
5
This vacuum furnace is a game-changer for our laboratory. It's fast, efficient, and easy to use.
4.9
out of
5
The vacuum furnace from KINTEK SOLUTION is a must-have for any lab. It's reliable, accurate, and has a wide range of features.
4.6
out of
5
I'm very impressed with the performance of this vacuum furnace. It's a great addition to our lab.
4.8
out of
5
This vacuum furnace is a great investment. It's well-made, easy to use, and delivers consistent results.
4.7
out of
5
I highly recommend this vacuum furnace. It's a great value for the money and has a lot of features that make it easy to use.
4.9
out of
5
This vacuum furnace is a must-have for any laboratory. It's accurate, reliable, and has a wide range of features.
4.6
out of
5
I'm very impressed with the performance of this vacuum furnace. It's a great addition to our lab.
4.8
out of
5
This vacuum furnace is a great investment. It's well-made, easy to use, and delivers consistent results.
4.7
out of
5
I highly recommend this vacuum furnace. It's a great value for the money and has a lot of features that make it easy to use.
4.9
out of
5
This vacuum furnace is a must-have for any laboratory. It's accurate, reliable, and has a wide range of features.
4.6
out of
5
I'm very impressed with the performance of this vacuum furnace. It's a great addition to our lab.
4.8
out of
5
This vacuum furnace is a great investment. It's well-made, easy to use, and delivers consistent results.
4.7
out of
5
I highly recommend this vacuum furnace. It's a great value for the money and has a lot of features that make it easy to use.
4.9
out of
5
This vacuum furnace is a must-have for any laboratory. It's accurate, reliable, and has a wide range of features.
4.6
out of
5
I'm very impressed with the performance of this vacuum furnace. It's a great addition to our lab.
4.8
out of
5
This vacuum furnace is a great investment. It's well-made, easy to use, and delivers consistent results.
4.7
out of
5
I highly recommend this vacuum furnace. It's a great value for the money and has a lot of features that make it easy to use.
4.9
out of
5
This vacuum furnace is a must-have for any laboratory. It's accurate, reliable, and has a wide range of features.
Products
Vacuum Heat Treat Furnace with Ceramic Fiber Liner
REQUEST A QUOTE
Our professional team will reply to you within one business day. Please feel free to contact us!
Related Products
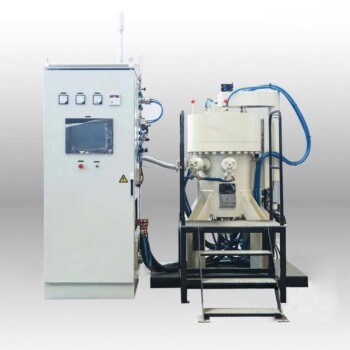
Vacuum Heat Treat and Sintering Furnace with 9MPa Air Pressure
The air pressure sintering furnace is a high-tech equipment commonly used for the sintering of advanced ceramic materials. It combines vacuum sintering and pressure sintering techniques to achieve high-density and high-strength ceramics.
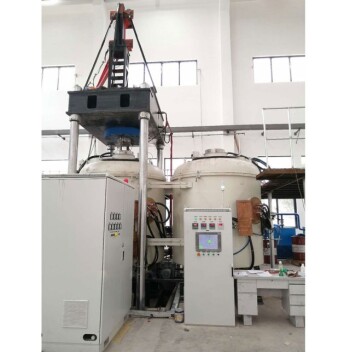
600T Vacuum Induction Hot Press Furnace for Heat Treat and Sintering
Discover the 600T Vacuum Induction Hot Press Furnace, designed for high-temperature sintering experiments in vacuum or protected atmospheres. Its precise temperature and pressure control, adjustable working pressure, and advanced safety features make it ideal for nonmetal materials, carbon composites, ceramics, and metal powders.
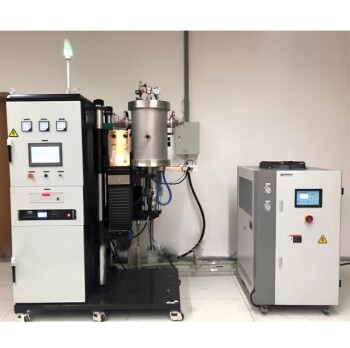
Vacuum Heat Treat and Molybdenum Wire Sintering Furnace for Vacuum Sintering
A vacuum molybdenum wire sintering furnace is a vertical or bedroom structure, which is suitable for withdrawal, brazing, sintering and degassing of metal materials under high vacuum and high temperature conditions. It is also suitable for dehydroxylation treatment of quartz materials.
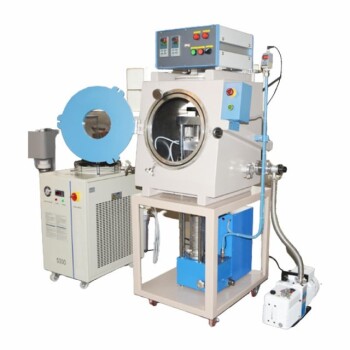
Vacuum Hot Press Furnace Machine for Lamination and Heating
Experience clean and precise lamination with Vacuum Lamination Press. Perfect for wafer bonding, thin-film transformations, and LCP lamination. Order now!
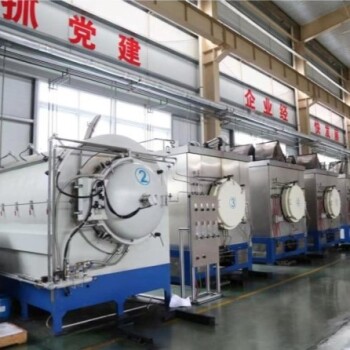
Vacuum Heat Treat Sintering Brazing Furnace
A vacuum brazing furnace is a type of industrial furnace used for brazing, a metalworking process that joins two pieces of metal using a filler metal that melts at a lower temperature than the base metals. Vacuum brazing furnaces are typically used for high-quality applications where a strong, clean joint is required.
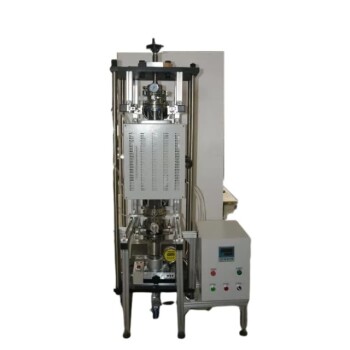
Vacuum Hot Press Furnace Heated Vacuum Press Machine Tube Furnace
Reduce forming pressure & shorten sintering time with Vacuum Tube Hot Press Furnace for high-density, fine-grain materials. Ideal for refractory metals.
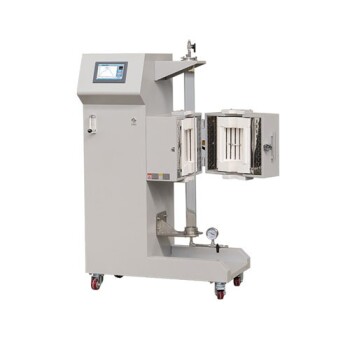
Vertical Laboratory Quartz Tube Furnace Tubular Furnace
Elevate your experiments with our Vertical Tube Furnace. Versatile design allows for operation under various environments and heat treatment applications. Order now for precise results!
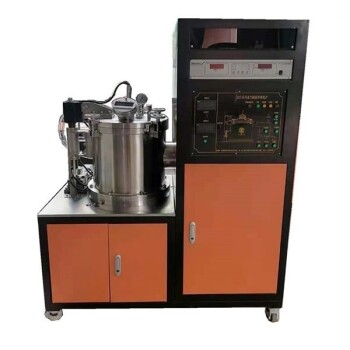
Vacuum Heat Treat Furnace and Levitation Induction Melting Furnace
Experience precise melting with our Vacuum Levitation Melting Furnace. Ideal for high melting point metals or alloys, with advanced technology for effective smelting. Order now for high-quality results.
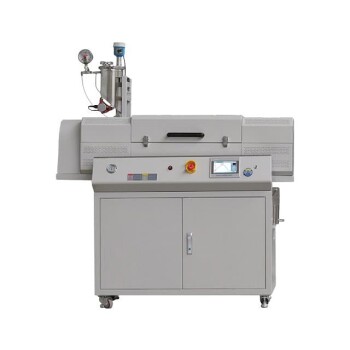
Laboratory Vacuum Tilt Rotary Tube Furnace Rotating Tube Furnace
Discover the versatility of Laboratory Rotary Furnace: Ideal for calcination, drying, sintering, and high-temperature reactions. Adjustable rotating and tilting functions for optimal heating. Suitable for vacuum and controlled atmosphere environments. Learn more now!
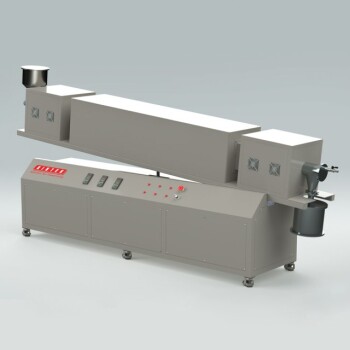
Vacuum Sealed Continuous Working Rotary Tube Furnace Rotating Tube Furnace
Experience efficient material processing with our vacuum-sealed rotary tube furnace. Perfect for experiments or industrial production, equipped with optional features for controlled feeding and optimized results. Order now.
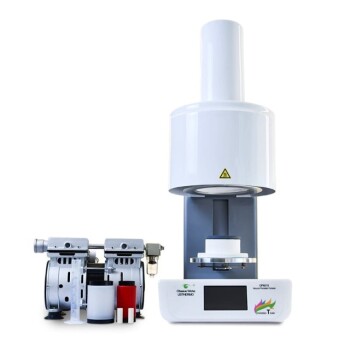
Dental Porcelain Zirconia Sintering Ceramic Vacuum Press Furnace
Get precise dental results with Dental Vacuum Press Furnace. Automatic temperature calibration, low noise tray, and touch screen operation. Order now!
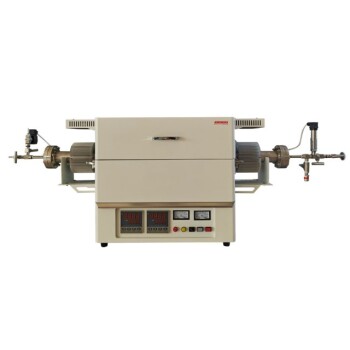
High Pressure Laboratory Vacuum Tube Furnace Quartz Tubular Furnace
KT-PTF High Pressure Tube Furnace: Compact split tube furnace with strong positive pressure resistance. Working temp up to 1100°C and pressure up to 15Mpa. Also works under controller atmosphere or high vacuum.
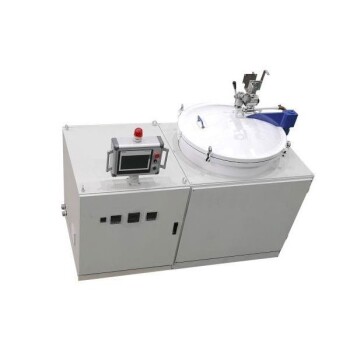
Graphite Vacuum Furnace IGBT Experimental Graphitization Furnace
IGBT experimental graphitization furnace, a tailored solution for universities and research institutions, with high heating efficiency, user-friendliness, and precise temperature control.
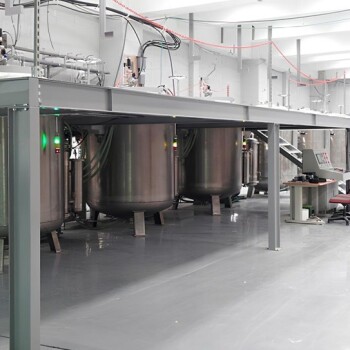
Graphite Vacuum Furnace Negative Material Graphitization Furnace
Graphitization furnace for battery production has uniform temperature and low energy consumption. Graphitization furnace for negative electrode materials: an efficient graphitization solution for battery production and advanced functions to enhance battery performance.

Graphite Vacuum Furnace Bottom Discharge Graphitization Furnace for Carbon Materials
Bottom-out graphitization furnace for carbon materials, ultra-high temperature furnace up to 3100°C, suitable for graphitization and sintering of carbon rods and carbon blocks. Vertical design, bottom discharging, convenient feeding and discharging, high temperature uniformity, low energy consumption, good stability, hydraulic lifting system, convenient loading and unloading.
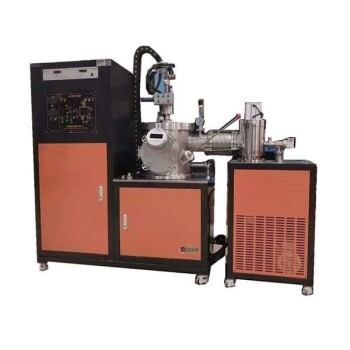
Vacuum Arc Induction Melting Furnace
Discover the power of Vacuum Arc Furnace for melting active & refractory metals. High-speed, remarkable degassing effect, and free of contamination. Learn more now!
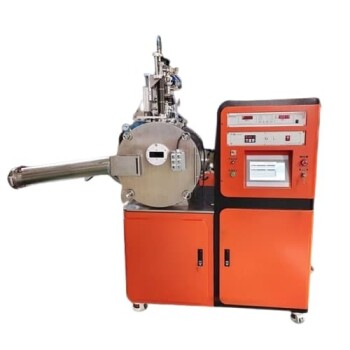
Vacuum Induction Melting Spinning System Arc Melting Furnace
Develop metastable materials with ease using our Vacuum Melt Spinning System. Ideal for research and experimental work with amorphous and microcrystalline materials. Order now for effective results.
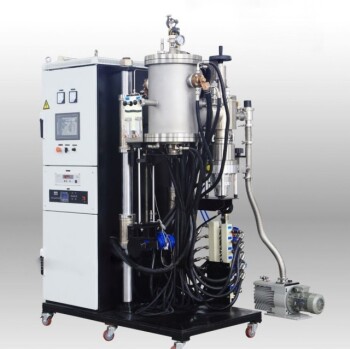
Small Vacuum Heat Treat and Tungsten Wire Sintering Furnace
The small vacuum tungsten wire sintering furnace is a compact experimental vacuum furnace specially designed for universities and scientific research institutes. The furnace features a CNC welded shell and vacuum piping to ensure leak-free operation. Quick-connect electrical connections facilitate relocation and debugging, and the standard electrical control cabinet is safe and convenient to operate.
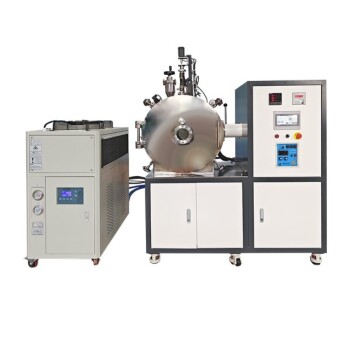
Lab-Scale Vacuum Induction Melting Furnace
Get precise alloy composition with our Vacuum Induction Melting Furnace. Ideal for aerospace, nuclear energy, and electronic industries. Order now for effective smelting and casting of metals and alloys.
Related Articles
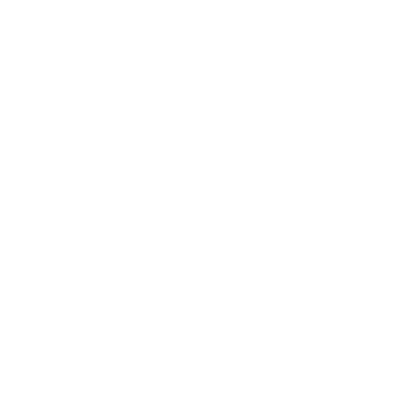
Materials Science with the Lab Vacuum Furnace
A vacuum furnace is a specialized type of furnace that is designed to operate in a vacuum environment. This means that the furnace is sealed and the air inside is pumped out, creating a low pressure or vacuum inside.
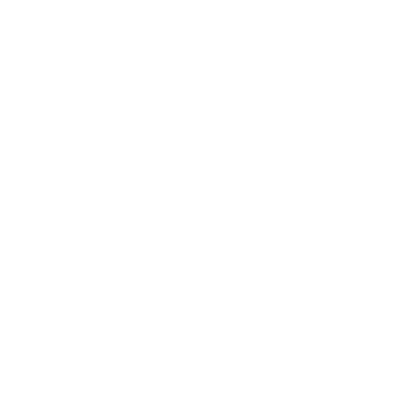
Molybdenum Vacuum Furnace: High-Temperature Sintering and Heat Treatment
Explore the advanced features and applications of molybdenum vacuum furnaces in high-temperature sintering and heat treatment. Learn about their construction, control systems, and maintenance tips.
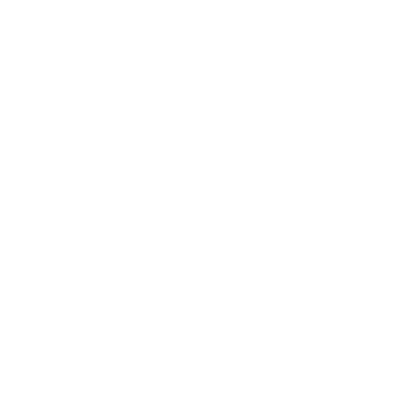
Dental Ceramic Furnaces The Science Behind It
Dental ceramic furnaces play a crucial role in the production of dental restorations such as crowns, bridges, and veneers.
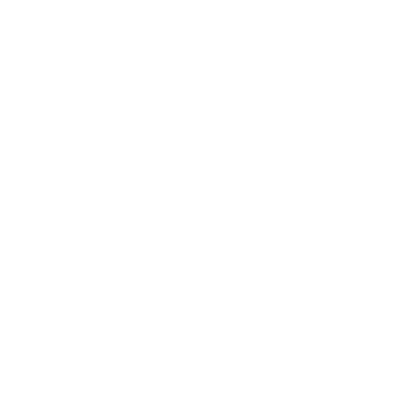
Understanding the Function of a Dental Ceramic Furnace
Dental ceramic furnaces are specialized equipment used in the dental laboratory to create high-quality dental restorations, such as crowns, bridges, and veneers.
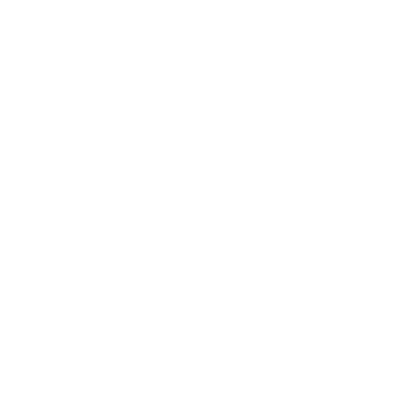
The Future of Porcelain Furnaces in Dental Laboratories
Porcelain furnaces play a crucial role in the dental laboratory industry as they are used for firing ceramic materials that are commonly used for restorations.
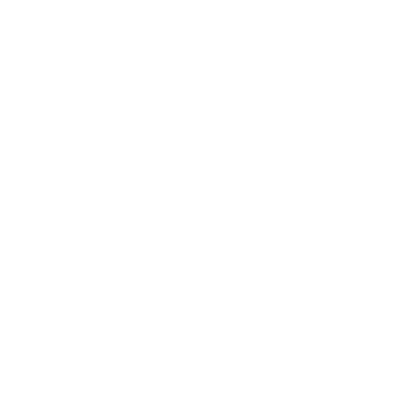
Mastering Vacuum Furnace Brazing: Techniques, Applications, and Advantages
Unlock the full potential of vacuum furnace brazing with our comprehensive guide. Learn about its technology, advantages, applications, and how brazing ovens are used. Explore the principles behind vacuum brazing furnaces and their exceptional features.
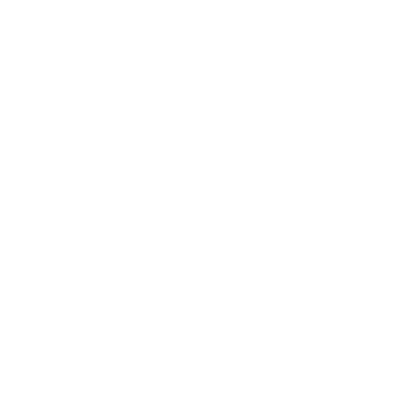
Muffle Furnace: Unraveling the Secrets of Uniform Heating and Controlled Atmosphere
Discover the intricacies of a muffle furnace, an indispensable tool for material processing and analysis. Learn about its working principle, applications, types, features, and benefits, empowering you to make informed decisions for your laboratory or industrial needs.
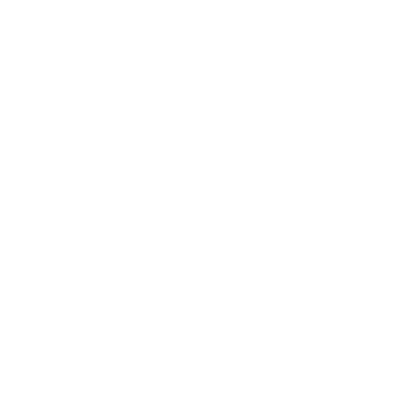
How to Maintain Your Dental Ceramic Furnace
The dental furnaces are expensive and require regular maintenance to ensure they function properly and produce accurate results.
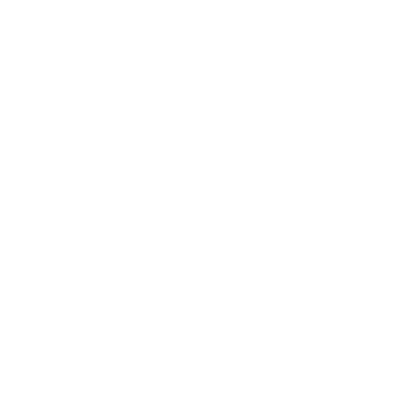
Melting process and maintenance of vacuum induction melting furnace
Melting process and maintenance of vacuum induction melting furnace
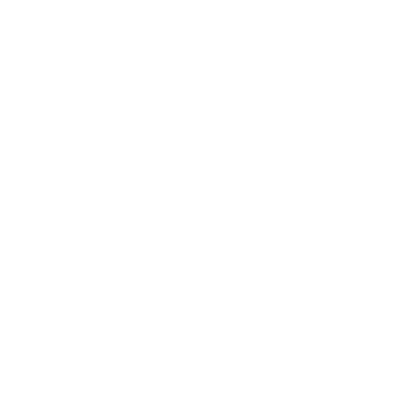
Molybdenum Vacuum Furnace: High-Temperature Sintering and Advanced Applications
Explore the advanced features and applications of molybdenum vacuum furnaces in high-temperature sintering and material treatment. Learn about their construction, control systems, and maintenance tips.
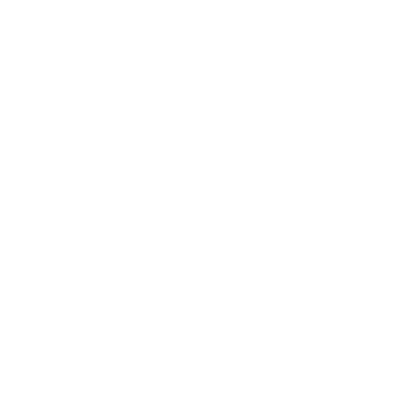
Vacuum Induction Furnace Fault Inspection: Essential Procedures and Solutions
Discover the essential procedures for inspecting and troubleshooting common faults in vacuum induction furnace. Learn how to troubleshoot electrical failures, conduct post-operation inspections, maintain records, and monitor the furnace's operation. Take corrective actions to ensure the furnace's optimal performance. Find expert solutions for temperature abnormalities, vacuum level deviations, and furnace chamber inspections.
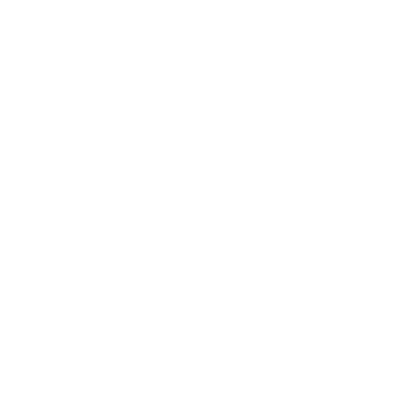
Unlocking the Potential: Vacuum Levitation Induction Melting Furnace Explained
Discover the working principles, applications, and advantages of vacuum levitation induction melting furnaces. Learn how this technology revolutionizes metal smelting, ensuring purity, efficiency, and environmental friendliness.