Introduction to Dental Ceramic Furnaces
Dental ceramic furnaces are specialized equipment used in the dental laboratory to create high-quality dental restorations, such as crowns, bridges, and veneers. These furnaces are designed to handle the high temperatures needed to fire and sinter dental ceramics, which are used to create durable and esthetically pleasing restorations. Dental ceramic furnaces come in various types, including conventional, vacuum, and microwave furnaces, and they are essential tools for any dental laboratory. In the next sections, we will explore the various functions of dental ceramic furnaces, the firing and sintering processes, and the factors to consider when selecting a furnace.
Table of Contents
Types of Dental Furnaces
Dental ceramic furnaces are essential equipment in the field of dentistry, and there are mainly three types of dental furnaces available: ceramic furnaces, combination furnaces, and sintering furnaces.
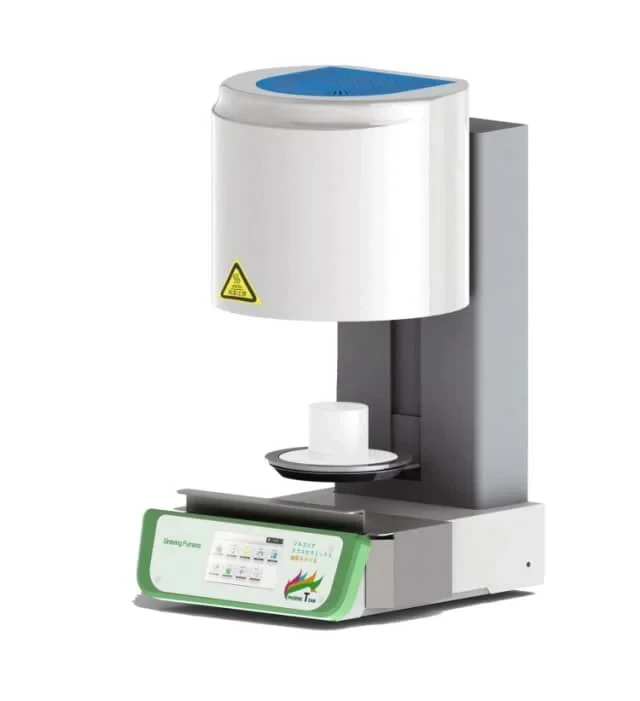
Ceramic Furnaces
Ceramic dental furnaces are designed to process conventional ceramics, making them suitable for all-metal-free and porcelain-fused-to-metal crowns. These furnaces are fully automated and allow for exceptional productivity. They use a heating element made of Kanthal or Nichrome and have a lower temperature range as compared to sintering furnaces.
Combination Furnaces
Combination dental furnaces are designed to handle both pressing ceramics and firing ceramic restorations. They can work with various dental materials and are suitable for different laboratory workflows. Combination furnaces are more versatile than ceramic furnaces and are capable of operating under the pressure necessary to work with pressable ceramics.
Sintering Furnaces
Sintering furnaces are used primarily to process dental zirconia material and mill it into a bridge, crown, framework, or other forms of restoration. These furnaces can reach high temperatures, which is necessary for zirconia to achieve hardness. Sintering furnaces use molybdenum disilicide heating elements and have a higher temperature range compared to ceramic furnaces. During the sintering process, zirconia undergoes significant shrinkage.
In addition to the above types of dental furnaces, there are also glazing furnaces, which are used for setting certain stains and glazes that add the final shade details to a restoration. These furnaces are not as common as the other three types and are not used as frequently in dental laboratories.
When selecting a dental furnace, it is essential to choose one that is capable of processing the materials used in your practice or lab. Make sure the furnaces you use are easy to clean and properly maintained between uses. Invest in a furnace from a reputable manufacturer that offers excellent customer support and training to ensure that you have access to the resources you need to use the equipment correctly.
Understanding the different types of dental furnaces available and their functions is crucial for dental professionals to produce high-quality dental restorations. By choosing the right equipment and properly maintaining it, dental professionals can ensure the accuracy and consistency of the final product.
Firing and Sintering Processes
Dental ceramic furnaces play a crucial role in the creation of dental restorations. The firing and sintering processes are two essential aspects of the furnace's function that are used to ensure the strength, stability, and aesthetics of the ceramic material used in the restoration.
Firing Process
During the firing process, the ceramic material is heated to a specific temperature to remove any organic materials and create a porous structure. This process is necessary to ensure the strength and stability of the ceramic material. The temperature and duration of the firing process are critical factors that determine the quality of the final product.
Sintering Process
After firing, the sintering process begins, which involves heating the ceramic to an even higher temperature to solidify the material and eliminate any remaining pores. This process is vital for ensuring the ceramic's durability and aesthetics. Sintering also involves pressure as well as heat, which reduces the porosity and increases the density of the ceramic material, such as zirconia.
Importance of Understanding Firing and Sintering Processes
Understanding the firing and sintering processes is essential for dental technicians and clinicians alike. Proper use of the dental ceramic furnace is critical for ensuring the quality and longevity of dental restorations. The sintering process is what gives zirconia restorations their strength and structural integrity.
Choosing the Right Dental Furnace
When choosing a dental furnace, it is essential to consider its capacity, pre-programmed cycles, and automation features. The furnace should be capable of processing the materials you plan to work with, and it should be easy to clean to keep your operation running for years.
Conclusion
In conclusion, dental ceramic furnaces are specialized laboratory equipment that plays a critical role in the creation of dental restorations. The firing and sintering processes are two essential aspects of the furnace's function that are necessary to ensure the strength, stability, and aesthetics of the ceramic material used in the restoration. Understanding these processes is essential for dental technicians and clinicians alike to ensure the quality and longevity of dental restorations.
Importance of Accurate Temperature Control
Accurate temperature control is highly essential in the production of high-quality dental prosthetics. Dental ceramic furnaces use a high temperature to fire dental ceramic materials to create the final product. It is crucial to ensure that the temperature inside the furnace is accurately controlled to avoid any damage to the ceramic material.
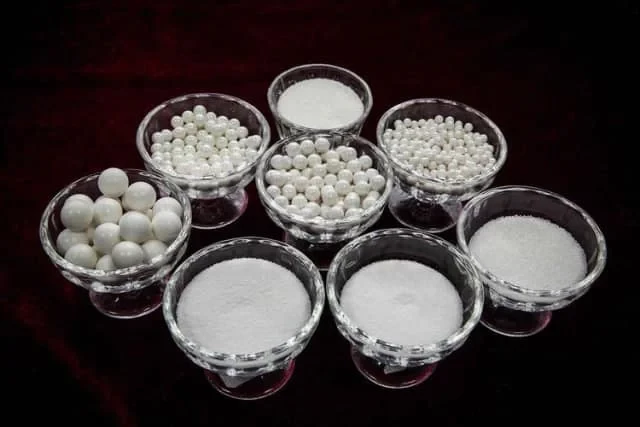
Ensuring Even Firing
The temperature inside the furnace must be carefully controlled to ensure that the ceramic material is fired evenly, preventing any cracks, bubbles, or distortion. The firing process is critical for ensuring that the final product is strong and durable, with proper adhesion to the underlying tooth structure. A well-designed dental ceramic furnace should have a programmable controller that enables precise temperature control.
Automated Temperature Regulation
The controller should provide automated temperature regulation to ensure that the firing process is consistent and repeatable. It is also important to monitor the temperature inside the furnace regularly, using a thermocouple or other temperature-measuring device. This will help detect any temperature variances that could negatively affect the quality of the final product.
Impact of Improper Temperature Control
Improper temperature control can cause soiling and deposits in the furnace, leading to changes over time. The technical components such as the heating wire, stone insulation inserts, and heating muffle can also be affected by wear. Calibration ensures that the temperature control is correct again. If you do not calibrate, this can lead to faulty temperatures in the furnace, which could negatively affect your restorations.
The Impact of Furnace Calibration
Calibration is necessary to ensure that the final product is strong, durable, and has proper adhesion to the underlying tooth structure. Understanding the dynamics of modern furnaces and ceramic materials can positively affect the esthetic outcome of restorations. Proper calibration can help technicians achieve the esthetics and vitality that these ceramic materials inherently possess.
In conclusion, an accurate temperature control system is critical in the production of high-quality dental prosthetics. Without accurate temperature control, the final product may have cracks, bubbles, or distortion, and may not be strong or durable enough to provide proper adhesion to the underlying tooth structure. Furnace calibration is necessary to ensure that the furnace is functioning optimally and can provide the necessary temperature conditions to create high-quality dental prosthetics.
Benefits of Using a Dental Furnace
A dental ceramic furnace is an essential piece of equipment in any dental laboratory. It is used to create high-quality dental restorations such as crowns, bridges, and implants. The benefits of using a dental furnace are numerous, and they include the following:
Precise Temperature and Heating Control
One of the significant benefits of using a dental furnace is that it allows for precise control over the temperature and heating process, ensuring that the ceramic material is not damaged or compromised during the firing process. The firing process is crucial in creating dental restorations that are both functional and aesthetically pleasing. With precise temperature and heating control, the dental restoration can be shaped and molded into the desired form without losing its structural integrity.
Consistent and Predictable Results
Another benefit of using a dental furnace is that it provides consistent and predictable results, which is essential in creating restorations that fit perfectly and match the patient's natural teeth. The uniform heating process ensures that the ceramics are heated evenly and consistently, resulting in a more predictable outcome. This consistency is critical in creating dental restorations that are accurate, durable, and aesthetically pleasing.
Saves Time and Money
A dental furnace saves time and money in the long run by reducing the need for adjustments or remakes, which can be costly and time-consuming. The precise temperature and heating control of a dental furnace ensure that the ceramics are not damaged during the firing process. Therefore, there is less need for adjustments or remakes, which can save both time and money.
Versatile
A dental furnace is versatile and can be used to create a wide range of dental restorations, including crowns, bridges, and implants. The furnace can handle different types of ceramics and materials, making it an essential tool for any dental laboratory.
In conclusion, a dental furnace is a crucial tool in any dental laboratory. The benefits of using a dental furnace include precise temperature and heating control, consistent and predictable results, saving time and money, and versatility. These benefits make a dental furnace an essential tool for any dental lab looking to create high-quality dental restorations that meet the needs of both the dentist and the patient.
Conclusion: How Dental Furnaces Improve Restorations
Dental ceramic furnaces play a vital role in the success of dental restorations. Accurate temperature control during the firing and sintering processes is crucial for achieving optimal restoration results. Using a dental furnace provides many benefits, including predictable and consistent firing results, reduced porosity, and improved strength and durability of restorations. Factors to consider when selecting a furnace include capacity, temperature range, and programming options. Investing in a quality dental furnace is a smart decision for any dental laboratory looking to improve the quality and consistency of their restorations.
CONTACT US FOR A FREE CONSULTATION
KINTEK LAB SOLUTION's products and services have been recognized by customers around the world. Our staff will be happy to assist with any inquiry you might have. Contact us for a free consultation and talk to a product specialist to find the most suitable solution for your application needs!