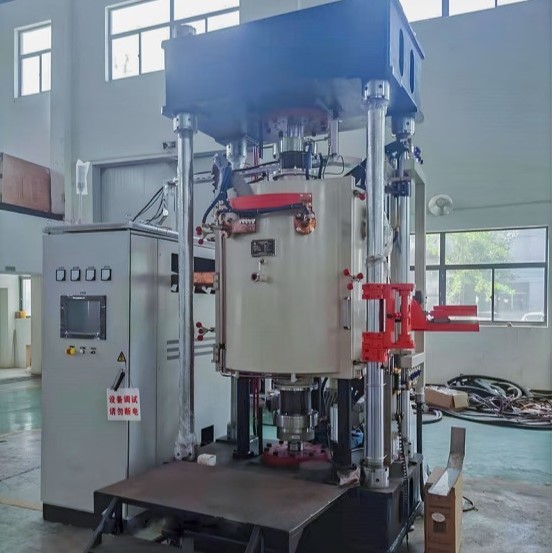
Vacuum Furnace
Vacuum Heat Treat and Pressure Sintering Furnace for High Temperature Applications
Item Number : KT-VPS
Price varies based on specs and customizations
- Maximum temperature
- 2100℃
- Pressure range
- 10-800T
- Heating method
- Graphite
- Vacuum degree
- 6×10-3Pa
- Effective workspace
- Customizable
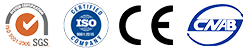
Shipping:
Contact us to get shipping details Enjoy On-time Dispatch Guarantee.
Why Choose Us
Reliable PartnerEasy ordering process, quality products, and dedicated support for your business success.
Introduction
A vacuum pressure sintering furnace is a high-temperature, high-pressure, and low-pressure sintering device primarily used to prepare high-performance ceramics, metals, and composite materials. It consists of a furnace body, heating device, vacuum system, and control system. The furnace operates by sintering powder or lump material under high temperature, vacuum, or inert gas environment, promoting material reorganization and recrystallization to form a dense structure with excellent performance. Vacuum pressure sintering furnaces prevent oxidation and pollution, ensuring material quality.
Details & Part
Applications
- Vacuum sintering:
- Sintering of metal powder, inorganic non-metallic materials, and high-temperature materials in a vacuum environment.
- Densification of materials to prevent deformation and grain coarsening.
- Pressure sintering:
- Sintering of materials under high pressure to enhance their mechanical properties.
- Production of ceramic parts, such as SiC and Si3N4, with improved strength and density.
- Hard alloy sintering:
- Sintering of hard alloys, such as tungsten carbide, to create wear-resistant and durable cutting tools.
- Ceramic materials sintering:
- Sintering of ceramic materials to achieve high purity, density, and electrical conductivity.
- Carbon fiber graphitization:
- Graphitization of carbon fibers to improve their electrical and thermal conductivity.
- Carbon and carbon composites sintering:
- Sintering of carbon and carbon composites to enhance their strength, thermal stability, and electrical properties.
- Silicon carbide products sintering:
- Sintering of silicon carbide products to produce high-strength, wear-resistant, and chemically inert materials.
- Photoelectric coating materials sintering:
- Sintering of photoelectric coating materials to create high-efficiency solar cells and other optoelectronic devices.
- Refractory metals sintering:
- Sintering of refractory metals, such as tungsten, molybdenum, and tungsten-copper alloys, to produce high-temperature resistant materials for aerospace and industrial applications.
- Alloy materials sintering:
- Sintering of alloy materials in a vacuum or atmosphere to achieve specific properties, such as corrosion resistance, high strength, and thermal stability.
Features
- Enhanced Sintering Quality: By providing a vacuum or protective atmosphere, the furnace inhibits oxidation and contamination, resulting in high-quality sintered materials.
- Versatile Sintering: The furnace accommodates a wide range of materials, including metal powders, inorganic non-metallic materials, and nanopowders, ensuring versatility in sintering applications.
- Precise Temperature Control: The advanced PLC and temperature transmitter ensure accurate temperature regulation, enabling precise sintering processes.
- Convenient Installation and Maintenance: Quick-connect electrical connections facilitate easy installation and relocation, while the standard-made electric control cabinet provides user-friendly operation and maintenance.
- Reliable Pressurization: The imported pressure regulator ensures stable pressurization, preventing deformation and grain coarsening during sintering.
- Comprehensive Safety Features: The classified sound and light alarm function, along with the use of Omron or Schneider electrical components, guarantees safe and reliable operation.
Principle
Vacuum pressure sintering furnace is a high-temperature, high-pressure sintering device. It is mainly used for the preparation of high-performance ceramics, metals, and composite materials. The basic principle of vacuum pressure sintering furnace is to sinter powder or lump material under high temperature, vacuum, or inert gas environment. Under high temperature diffusion, thermal cracking, chemical reaction, and other processes, the material undergoes microscopic reorganization and recrystallization to form a dense structure with excellent performance. This process avoids oxidation, pollution, and other undesirable effects on the material.
Advantages
-
Reduced contamination: Vacuum sintering reduces the contamination of harmful substances (such as water, oxygen, nitrogen, and other impurities) in the atmosphere that may affect the material, thus avoiding a series of adverse reactions such as decarburization, carburization, reduction, oxidation, nitriding, and so on.
-
Consistent, bright parts: Vacuum sintering produces consistent, bright parts with no seams, joints, or fillers.
-
Incredible design flexibility: Vacuum sintering is an efficient way to join parts with minimal waste. Components that require sintering are often delicate, intricate, and easy to botch. Vacuum sintering is an efficient way to join parts with minimal waste.
-
Quick turnaround: Vacuum sintering offers a quick turnaround time, making it an ideal solution for projects with tight deadlines.
-
Superior quality: Vacuum sintering produces parts with superior quality and fewer defects.
-
Easy maintenance: Vacuum sintering furnaces are easy to maintain, ensuring minimal downtime and maximum productivity.
-
Maximum productivity: Vacuum sintering furnaces offer maximum productivity, making them an ideal choice for high-volume production.
Technical specifications
Maximum temperature | 2100℃ |
Pressure range | 10-800T |
Heating method | Graphite |
Vacuum degree | 6×10-3Pa |
Effective workspace | Customizable |
4.8
out of
5
Exceptional quality and craftsmanship. The vacuum pressure sintering furnace has exceeded our expectations, delivering remarkable results.
4.9
out of
5
Highly recommended for its outstanding performance and durability. The furnace has proven to be a valuable asset in our laboratory.
4.7
out of
5
Impeccable design and user-friendly interface. The vacuum pressure sintering furnace has streamlined our workflow, saving us both time and effort.
4.8
out of
5
Exceptional value for money. The furnace's cost-effectiveness has allowed us to expand our research capabilities significantly.
4.9
out of
5
Unparalleled technological advancement. The vacuum pressure sintering furnace has pushed the boundaries of our research, enabling us to achieve groundbreaking results.
4.7
out of
5
Lightning-fast delivery and impeccable packaging. The furnace arrived in perfect condition, ready to use immediately.
4.8
out of
5
Outstanding customer support. The team at KINTEK SOLUTION has been incredibly responsive and helpful, ensuring a seamless experience.
4.9
out of
5
Highly customizable to meet our specific research needs. The vacuum pressure sintering furnace has become an indispensable tool in our laboratory.
4.7
out of
5
Intuitive software and comprehensive documentation. The furnace is easy to operate and maintain, saving us valuable time.
4.8
out of
5
Excellent energy efficiency and low operating costs. The vacuum pressure sintering furnace has reduced our energy consumption significantly.
4.9
out of
5
Compact design and space-saving footprint. The furnace fits perfectly in our laboratory, maximizing our research space.
4.7
out of
5
Highly reliable and consistent performance. The vacuum pressure sintering furnace has proven to be a workhorse in our laboratory, delivering exceptional results every time.
4.8
out of
5
Exceptional safety features and compliance with industry standards. The vacuum pressure sintering furnace provides peace of mind while conducting our research.
4.9
out of
5
Unmatched precision and accuracy. The vacuum pressure sintering furnace has enabled us to achieve unparalleled results in our research, pushing the boundaries of scientific discovery.
Products
Vacuum Heat Treat and Pressure Sintering Furnace for High Temperature Applications
REQUEST A QUOTE
Our professional team will reply to you within one business day. Please feel free to contact us!
Related Products
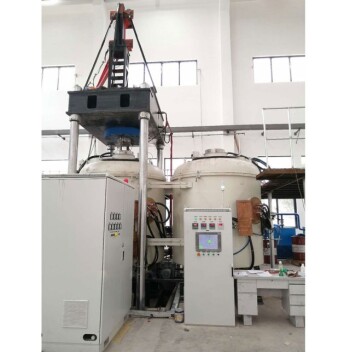
600T Vacuum Induction Hot Press Furnace for Heat Treat and Sintering
Discover the 600T Vacuum Induction Hot Press Furnace, designed for high-temperature sintering experiments in vacuum or protected atmospheres. Its precise temperature and pressure control, adjustable working pressure, and advanced safety features make it ideal for nonmetal materials, carbon composites, ceramics, and metal powders.
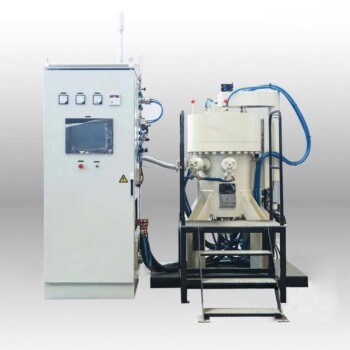
Vacuum Heat Treat and Sintering Furnace with 9MPa Air Pressure
The air pressure sintering furnace is a high-tech equipment commonly used for the sintering of advanced ceramic materials. It combines vacuum sintering and pressure sintering techniques to achieve high-density and high-strength ceramics.
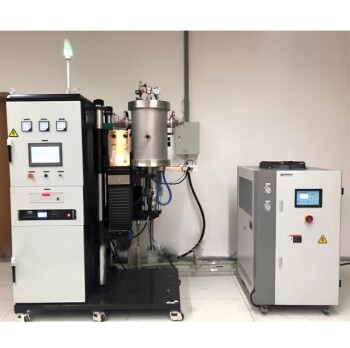
Vacuum Heat Treat and Molybdenum Wire Sintering Furnace for Vacuum Sintering
A vacuum molybdenum wire sintering furnace is a vertical or bedroom structure, which is suitable for withdrawal, brazing, sintering and degassing of metal materials under high vacuum and high temperature conditions. It is also suitable for dehydroxylation treatment of quartz materials.
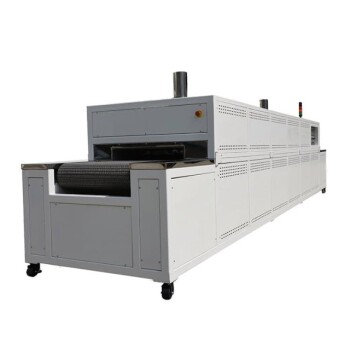
Mesh belt controlled atmosphere furnace
Discover our KT-MB mesh belt sintering furnace - perfect for high-temperature sintering of electronic components & glass insulators. Available for open air or controlled atmosphere environments.
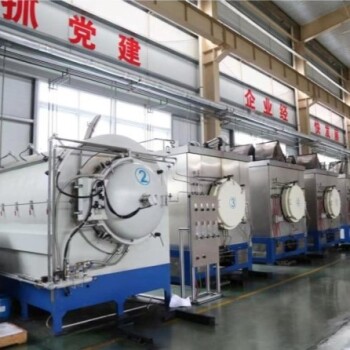
Vacuum Heat Treat Sintering Brazing Furnace
A vacuum brazing furnace is a type of industrial furnace used for brazing, a metalworking process that joins two pieces of metal using a filler metal that melts at a lower temperature than the base metals. Vacuum brazing furnaces are typically used for high-quality applications where a strong, clean joint is required.
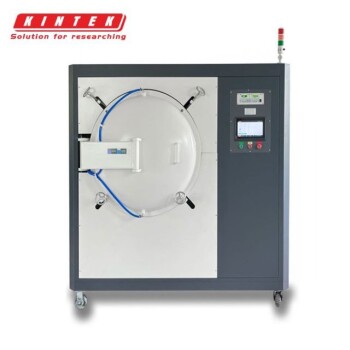
Vacuum Heat Treat Furnace with Ceramic Fiber Liner
Vacuum furnace with polycrystalline ceramic fiber insulation liner for excellent heat insulation and uniform temperature field. Choose from 1200℃ or 1700℃ max. working temperature with high vacuum performance and precise temperature control.
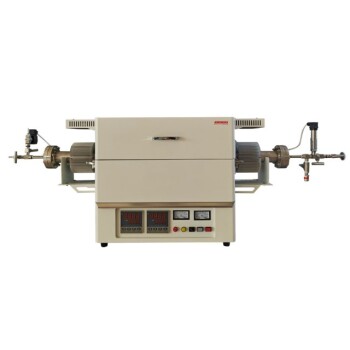
High Pressure Laboratory Vacuum Tube Furnace Quartz Tubular Furnace
KT-PTF High Pressure Tube Furnace: Compact split tube furnace with strong positive pressure resistance. Working temp up to 1100°C and pressure up to 15Mpa. Also works under controller atmosphere or high vacuum.
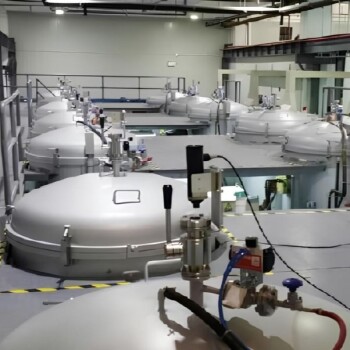
Graphite Vacuum Furnace High Thermal Conductivity Film Graphitization Furnace
The high thermal conductivity film graphitization furnace has uniform temperature, low energy consumption and can operate continuously.
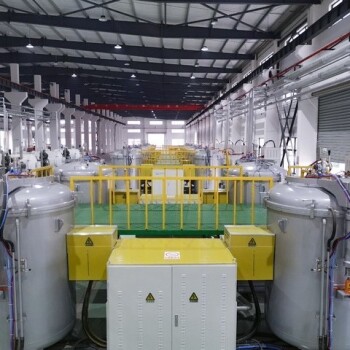
Vertical High Temperature Graphite Vacuum Graphitization Furnace
Vertical high temperature graphitization furnace for carbonization and graphitization of carbon materials up to 3100℃.Suitable for shaped graphitization of carbon fiber filaments and other materials sintered in a carbon environment.Applications in metallurgy, electronics, and aerospace for producing high-quality graphite products like electrodes and crucibles.
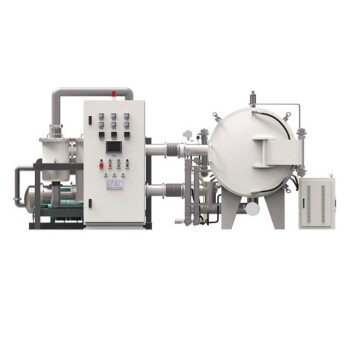
Horizontal High Temperature Graphite Vacuum Graphitization Furnace
Horizontal Graphitization Furnace: This type of furnace is designed with the heating elements placed horizontally, allowing for uniform heating of the sample. It's well-suited for graphitizing large or bulky samples that require precise temperature control and uniformity.
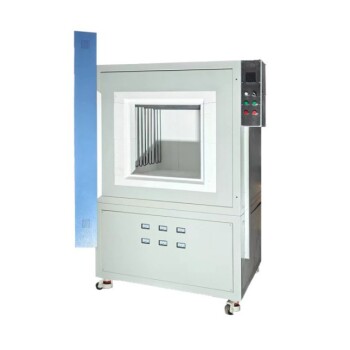
High Temperature Muffle Oven Furnace for Laboratory Debinding and Pre Sintering
KT-MD High temperature debinding and pre-sintering furnace for ceramic materials with various molding processes. Ideal for electronic components such as MLCC and NFC.
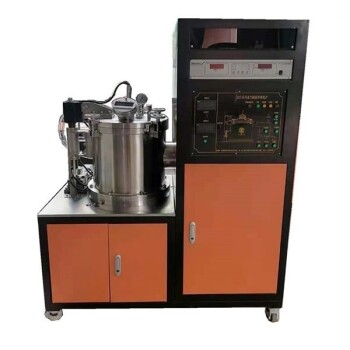
Vacuum Heat Treat Furnace and Levitation Induction Melting Furnace
Experience precise melting with our Vacuum Levitation Melting Furnace. Ideal for high melting point metals or alloys, with advanced technology for effective smelting. Order now for high-quality results.

Graphite Vacuum Furnace Bottom Discharge Graphitization Furnace for Carbon Materials
Bottom-out graphitization furnace for carbon materials, ultra-high temperature furnace up to 3100°C, suitable for graphitization and sintering of carbon rods and carbon blocks. Vertical design, bottom discharging, convenient feeding and discharging, high temperature uniformity, low energy consumption, good stability, hydraulic lifting system, convenient loading and unloading.
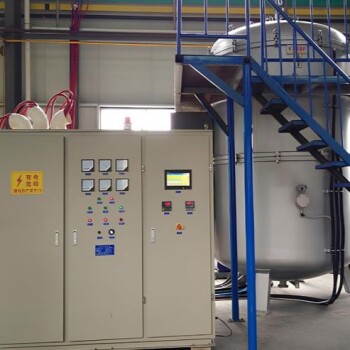
Large Vertical Graphite Vacuum Graphitization Furnace
A large vertical high-temperature graphitization furnace is a type of industrial furnace used for the graphitization of carbon materials, such as carbon fiber and carbon black. It is a high-temperature furnace that can reach temperatures of up to 3100°C.
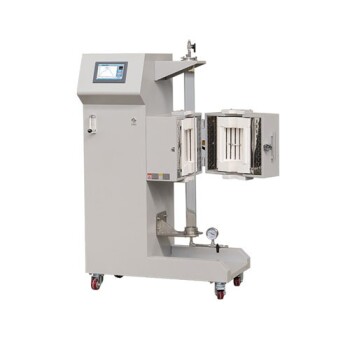
Vertical Laboratory Quartz Tube Furnace Tubular Furnace
Elevate your experiments with our Vertical Tube Furnace. Versatile design allows for operation under various environments and heat treatment applications. Order now for precise results!
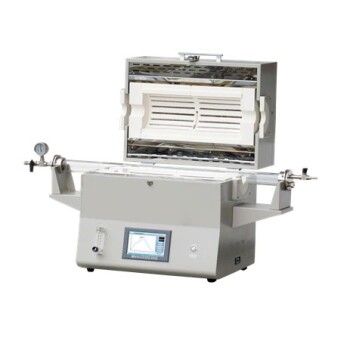
1400℃ Laboratory Quartz Tube Furnace with Alumina Tube Tubular Furnace
Looking for a tube furnace for high-temperature applications? Our 1400℃ Tube Furnace with Alumina Tube is perfect for research and industrial use.
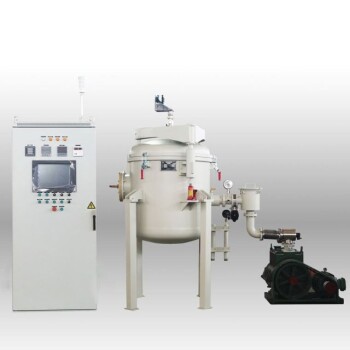
Ultra-High Temperature Graphite Vacuum Graphitization Furnace
The ultra-high temperature graphitization furnace utilizes medium frequency induction heating in a vacuum or inert gas environment. The induction coil generates an alternating magnetic field, inducing eddy currents in the graphite crucible, which heats up and radiates heat to the workpiece, bringing it to the desired temperature. This furnace is primarily used for graphitization and sintering of carbon materials, carbon fiber materials, and other composite materials.
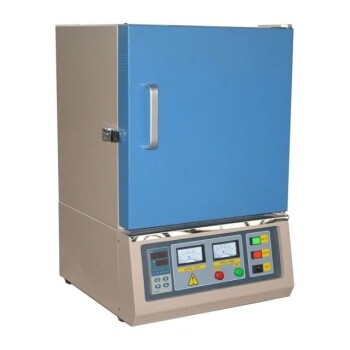
1400℃ Muffle Oven Furnace for Laboratory
Get precise high-temperature control up to 1500℃ with KT-14M Muffle furnace. Equipped with a smart touch screen controller and advanced insulation materials.
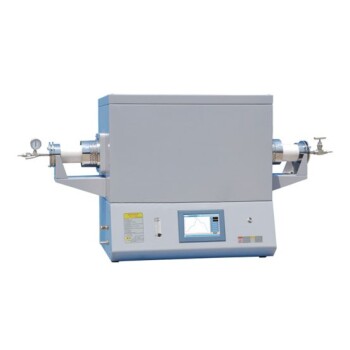
1700℃ Laboratory Quartz Tube Furnace with Alumina Tube Tubular Furnace
Looking for a high-temperature tube furnace? Check out our 1700℃ Tube Furnace with Alumina Tube. Perfect for research and industrial applications up to 1700C.
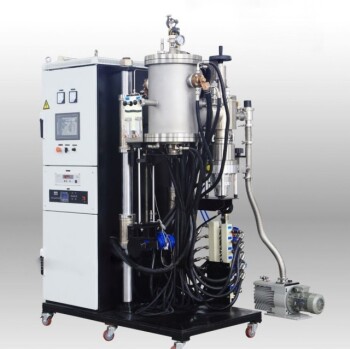
Small Vacuum Heat Treat and Tungsten Wire Sintering Furnace
The small vacuum tungsten wire sintering furnace is a compact experimental vacuum furnace specially designed for universities and scientific research institutes. The furnace features a CNC welded shell and vacuum piping to ensure leak-free operation. Quick-connect electrical connections facilitate relocation and debugging, and the standard electrical control cabinet is safe and convenient to operate.
Related Articles
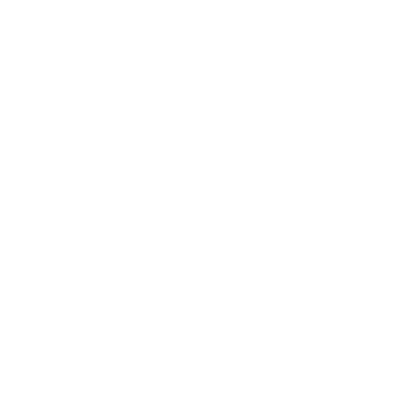
How Vacuum Induction Melting Powers Superior Material Performance in Critical Industries
Discover how Vacuum Induction Melting (VIM) ensures 99.99% pure alloys for aerospace and medical industries, boosting performance and compliance.
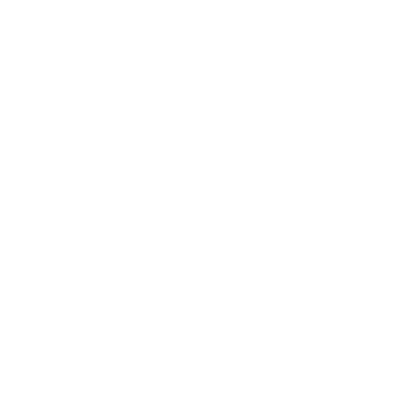
How Vacuum Induction Melting Ensures Unmatched Reliability in Critical Industries
Vacuum induction melting (VIM) ensures metallurgical purity, durability, and efficiency in aerospace, nuclear, and critical industries. Learn why VIM outperforms traditional methods.
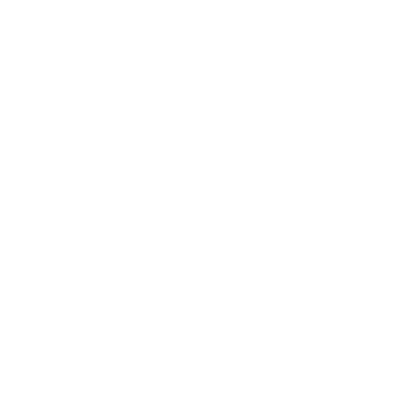
How Vacuum Induction Melting (VIM) Transforms High-Performance Alloy Production
Discover how Vacuum Induction Melting (VIM) enhances alloy purity for aerospace, medical, and nuclear industries, reducing defects and costs.
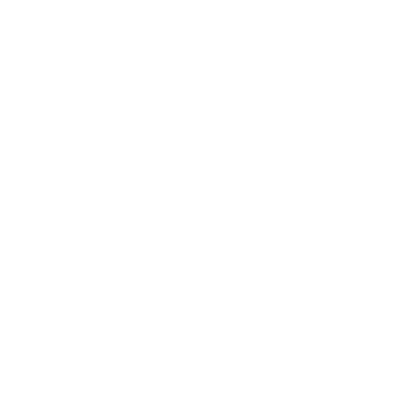
How Vacuum Induction Melting Outperforms Traditional Methods in Advanced Alloy Production
Discover how vacuum induction melting (VIM) outperforms traditional methods in advanced alloy production, offering precision, purity, and cost savings.
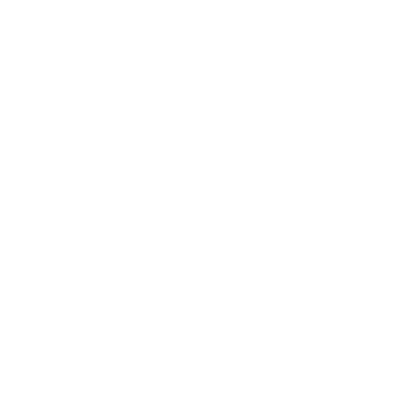
How Vacuum Induction Melting Elevates High-Performance Alloy Production
Discover how Vacuum Induction Melting (VIM) enhances alloy purity, reduces defects, and optimizes costs for aerospace and energy sectors.
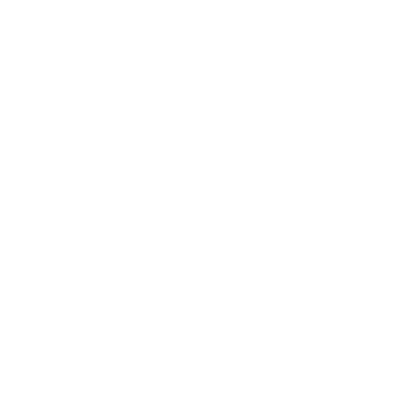
How Vacuum Induction Melting Prevents Catastrophic Material Failures in Critical Components
Discover how Vacuum Induction Melting (VIM) prevents material failures in aerospace, nuclear, and EV components by eliminating atomic-level contamination.
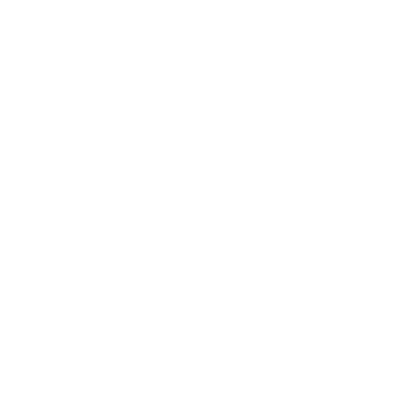
How to Choose Crucible Materials That Prevent Chemical Degradation in Vacuum Induction Melting
Learn how to choose crucible materials for vacuum induction melting to prevent chemical degradation and optimize alloy purity. Essential guide for industrial applications.
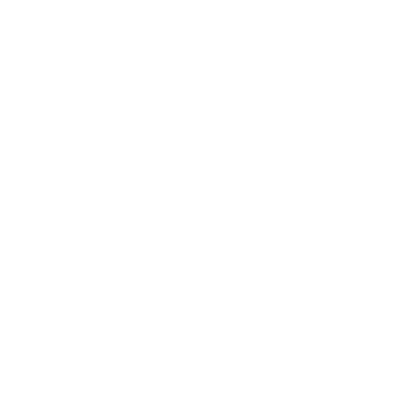
The Ultimate Guide to Vacuum Pressure Sintering Furnace: Benefits, Applications, and Working Principle
Discover the benefits, applications, and working principle of vacuum pressure sintering furnace. Learn how vacuum sintering produces clean, bright parts with incredible design flexibility and quick turnaround, and its applications in teaching, scientific research, and production. Explore the precise setting and monitoring of process parameters, and the advantages of sintering under vacuum and pressure. Find out how vacuum sintering furnace is perfect for higher temperature sintering applications and for sintering extremely reactive materials.
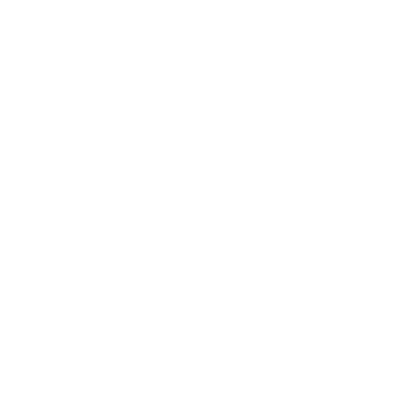
Mastering Vacuum Furnace Brazing: Techniques, Applications, and Advantages
Unlock the full potential of vacuum furnace brazing with our comprehensive guide. Learn about its technology, advantages, applications, and how brazing ovens are used. Explore the principles behind vacuum brazing furnaces and their exceptional features.
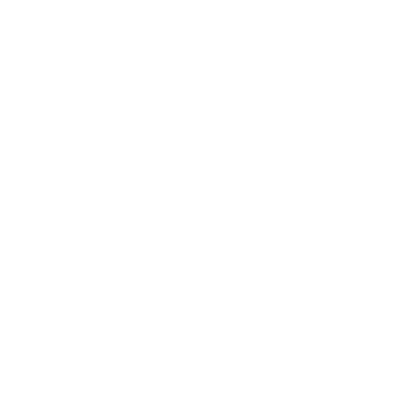
Exploring Spark Plasma Sintering Furnace (SPS): Technology, Applications, and Advantages
Dive into the comprehensive guide on Spark Plasma Sintering Furnace (SPS), covering its technology, applications in materials science, and significant advantages over traditional sintering methods.
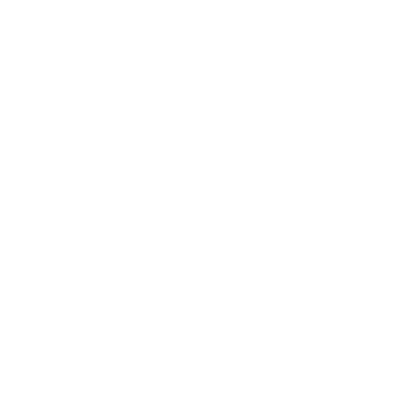
Comprehensive Guide to Spark Plasma Sintering Furnaces: Applications, Features, and Benefits
Explore the advanced features and applications of Spark Plasma Sintering Furnaces (SPS) in material science. Learn how SPS technology offers rapid, efficient, and versatile sintering for various materials.
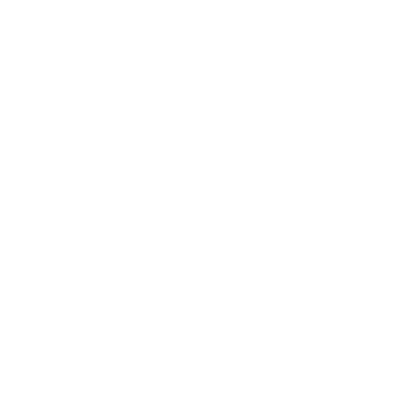
Comprehensive Guide to Vacuum Hot Press Furnace Application
The Vacuum Hot Press Furnace is a versatile tool especially suited for sintering experiments involving non-metallic materials, carbon composites, ceramic materials and metal powder materials.