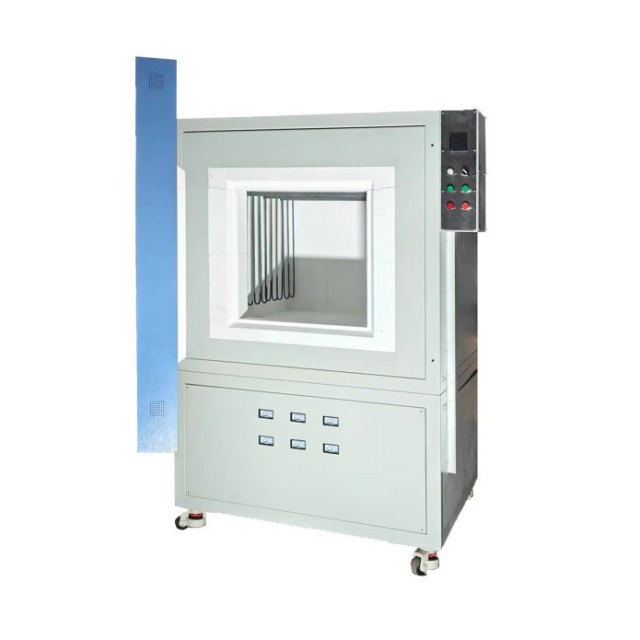
Muffle Furnace
High Temperature Muffle Oven Furnace for Laboratory Debinding and Pre Sintering
Item Number : KT-MD
Price varies based on specs and customizations
- Constant work temperature
- 1100/1300 ℃
- Heating rate
- 0-20 ℃/min
- Effective volume
- 27-512 L
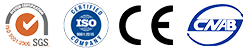
Shipping:
Contact us to get shipping details Enjoy On-time Dispatch Guarantee.
Why Choose Us
Reliable PartnerEasy ordering process, quality products, and dedicated support for your business success.
Applications
KT-MD Debinding and pre sintering integrated furnace is widely used for debinding and pre sintering of ceramic materials with various molding processes, such as fine ceramic components of aluminum nitride, silicon nitride, aluminum oxide, zirconia and dielectric ceramics, as well as for the debinding, pre sintering and sintering integrated process of ceramic powder materials, magnetic materials, LTCC, MLCC, NTC, NFC, ceramic core and other electronic components.
Features
- Furnace body design; the furnace body adopts a stepped assembly structure, and the furnace door and furnace door frame adopt an integral design. This effectively keeps the roof from collapsing. The close fit between the furnace door and the furnace door frame makes it difficult to lose heat energy and increases the service life of the furnace door components. The furnace body is equipped with a furnace rack, which can realize hierarchical management and place materials according to the user's production needs. And the material can be fully burned.
- Temperature control system; the heating element adopts molybdenum resistance wire and is heated on all sides. The control system adopts microcomputer artificial intelligence adjustment technology. With PID adjustment, automatic control, self-tuning function, multi-level programming. And can program various heating, keeping warm and Coolina Proarams with hiah temperature control accuracy Integrated module SCR control nhase-shift trigger protection system independent over-temperature protection, over-voltage, over-current, leakage, short-circuit protection, etc.
- Trolley device; there is a trolley outside the furnace, and a material rack inside the car, which is convenient for taking out and placing materials after completion of production. The frame inside the furnace is made of 310S high temperature resistant stainless steel, and the frame outside the furnace is made of metal materials.
Advantages
- 1100℃ and 1300℃ Two working temperature models are available
- Working chamber size can be customized according to the products requirement
- Scientific exhaust emission air ventilating design,harmful emission can be collected safely for further processing
- Independent fresh air preheating and circulating system, ensure a better temperature uniformity and energy saving
- PID programmable temperature control,excellent control accuracy and stable heating performance, support remote control and centralized control
- Ceramic polycrystalline fiber insulation liner, less heat loss and superior energy saving efficiency
- Professional heating elements configuration to optimize heat radiation properties, and ensure a longest service life
Technical specifications
Furnace model | KT-MD | ||
---|---|---|---|
Constant work temperature | 1100/1300 ℃ | ||
Chamber material | Japan alumina fiber | ||
Heating element | Cr2Al2Mo2 wire coil/Silicon Carbide | ||
Heating rate | 0-20℃/min | ||
Temperature sensor | K/S type thermal couple | ||
Temperature controller | Digital PID controller/Touch screen PID controller | ||
Temperature control accuracy | ±1℃ | ||
Electric power supply | AC200-440V,50/60HZ | ||
Standard Chamber Sizes Stocks | |||
Chamber size (mm) | Effective volume (L) | Chamber size (mm) | Effective volume (L) |
300x300x300 | 27 | 300x300x400 | 36 |
400x400x400 | 64 | 500x500x500 | 125 |
600x600x600 | 216 | 800x800x800 | 512 |
Other sizes and volume can be customized |
Standard Package
No. | Description | Quantity |
---|---|---|
1 | Furnace | 1 |
2 | Thermal block | 1 |
3 | Crucible tong | 1 |
4 | Heat resistant glove | 1 |
5 | Operation manual | 1 |
Optional Setup
- Independent furnace temperature monitoring and recording
- RS 485 communication port for PC remote control and data exporting
- Automatic and accurate control for fresh air purge and exhaust emission ventilating system
Warnings
Operator safety is the top important issue! Please operate the equipment with cautions. Working with inflammable& explosive or toxic gases is very dangerous, operators must take all necessary precautions before starting the equipment. Working with positive pressure inside the reactors or chambers is dangerous, operator must fellow the safety procedures strictly. Extra caution must also be taken when operating with air-reactive materials, especially under vacuum. A leak can draw air into the apparatus and cause a violent reaction to occur.
Designed for You
KinTek provide deep custom made service and equipment to worldwide customers, our specialized teamwork and rich experienced engineers are capable to undertake the custom tailoring hardware and software equipment requirements, and help our customer to build up the exclusive and personalized equipment and solution!
Would you please drop your ideas to us, our engineers are ready for you now!
FAQ
What Are Muffle Furnace Used For?
What Are The Types Of Muffle Furnace?
What Is Muffle Furnace In Chemistry?
What Is The Use Of Muffle Furnace For Ash?
What Is The Temperature Of Muffle Furnace?
4.9
out of
5
KT-MD furnace is a game-changer! It's incredibly efficient and precise, saving us time and resources.
4.7
out of
5
The furnace's customizable chamber size and precise temperature control make it perfect for our research projects.
4.8
out of
5
KT-MD's integrated design streamlines our debinding and pre-sintering processes, improving productivity.
4.9
out of
5
The furnace's advanced safety features give us peace of mind during high-temperature operations.
4.7
out of
5
Excellent customer service from KINTEK SOLUTION. They answered all our queries promptly and helped us choose the right furnace.
4.8
out of
5
The furnace's durability and low maintenance requirements make it a cost-effective investment.
4.9
out of
5
KT-MD's user-friendly interface and remote control capabilities enhance our lab's efficiency.
4.7
out of
5
The furnace's ability to handle various materials makes it versatile for our diverse research needs.
4.8
out of
5
KINTEK SOLUTION's customization options allowed us to tailor the furnace to our specific requirements.
4.9
out of
5
The furnace's energy-saving features help us reduce our lab's carbon footprint.
4.7
out of
5
The furnace's compact design saves valuable lab space, making it ideal for our small research facility.
4.8
out of
5
KT-MD's fast heating and cooling rates accelerate our research processes, allowing us to achieve more in less time.
Products
High Temperature Muffle Oven Furnace for Laboratory Debinding and Pre Sintering
REQUEST A QUOTE
Our professional team will reply to you within one business day. Please feel free to contact us!
Related Products
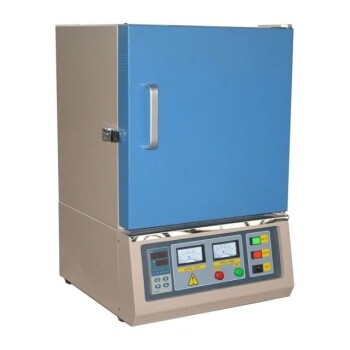
1400℃ Muffle Oven Furnace for Laboratory
Get precise high-temperature control up to 1500℃ with KT-14M Muffle furnace. Equipped with a smart touch screen controller and advanced insulation materials.
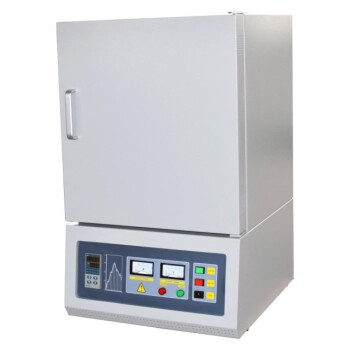
1700℃ Muffle Oven Furnace for Laboratory
Get superior heat control with our 1700℃ Muffle Furnace. Equipped with intelligent temperature microprocessor, TFT touch screen controller & advanced insulation materials for precise heating up to 1700C. Order now!
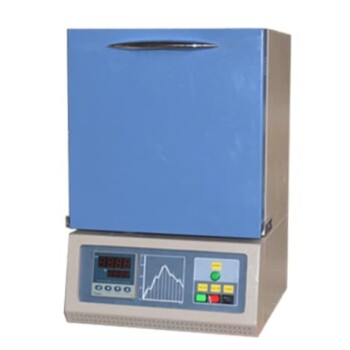
1200℃ Muffle Furnace Oven for Laboratory
Upgrade your lab with our 1200℃ Muffle Furnace. Achieve fast, precise heating with Japan alumina fibers and Molybdenum coils. Features TFT touch screen controller for easy programming and data analysis. Order now!
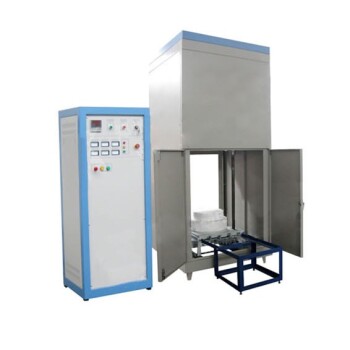
Laboratory Muffle Oven Furnace Bottom Lifting Muffle Furnace
Efficiently produce batches with excellent temperature uniformity using our Bottom Lifting Furnace. Features two electric lifting stages and advanced temperature control up to 1600℃.
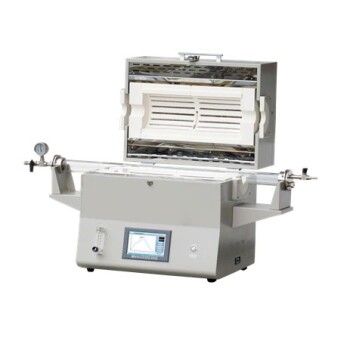
1400℃ Laboratory Quartz Tube Furnace with Alumina Tube Tubular Furnace
Looking for a tube furnace for high-temperature applications? Our 1400℃ Tube Furnace with Alumina Tube is perfect for research and industrial use.
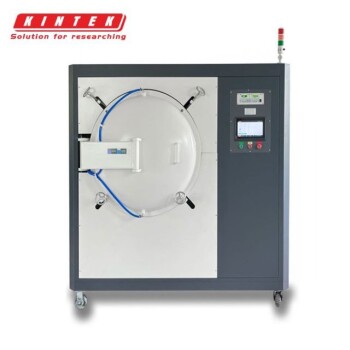
Vacuum Heat Treat Furnace with Ceramic Fiber Liner
Vacuum furnace with polycrystalline ceramic fiber insulation liner for excellent heat insulation and uniform temperature field. Choose from 1200℃ or 1700℃ max. working temperature with high vacuum performance and precise temperature control.
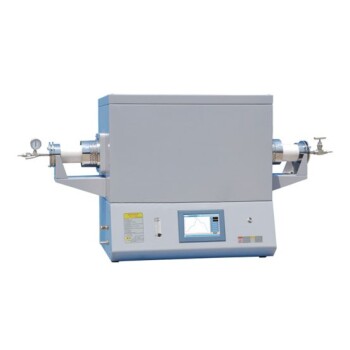
1700℃ Laboratory Quartz Tube Furnace with Alumina Tube Tubular Furnace
Looking for a high-temperature tube furnace? Check out our 1700℃ Tube Furnace with Alumina Tube. Perfect for research and industrial applications up to 1700C.
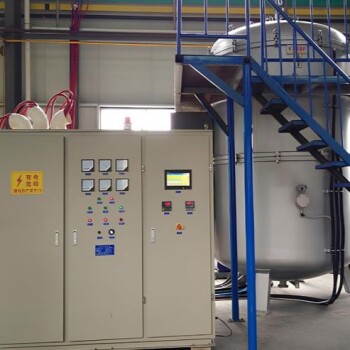
Large Vertical Graphite Vacuum Graphitization Furnace
A large vertical high-temperature graphitization furnace is a type of industrial furnace used for the graphitization of carbon materials, such as carbon fiber and carbon black. It is a high-temperature furnace that can reach temperatures of up to 3100°C.
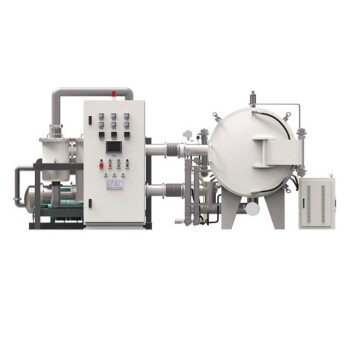
Horizontal High Temperature Graphite Vacuum Graphitization Furnace
Horizontal Graphitization Furnace: This type of furnace is designed with the heating elements placed horizontally, allowing for uniform heating of the sample. It's well-suited for graphitizing large or bulky samples that require precise temperature control and uniformity.
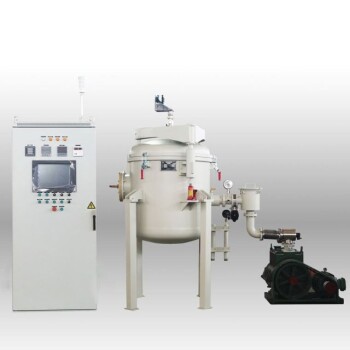
Ultra-High Temperature Graphite Vacuum Graphitization Furnace
The ultra-high temperature graphitization furnace utilizes medium frequency induction heating in a vacuum or inert gas environment. The induction coil generates an alternating magnetic field, inducing eddy currents in the graphite crucible, which heats up and radiates heat to the workpiece, bringing it to the desired temperature. This furnace is primarily used for graphitization and sintering of carbon materials, carbon fiber materials, and other composite materials.
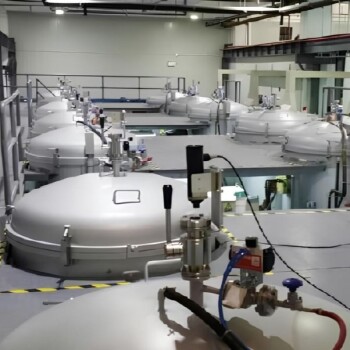
Graphite Vacuum Furnace High Thermal Conductivity Film Graphitization Furnace
The high thermal conductivity film graphitization furnace has uniform temperature, low energy consumption and can operate continuously.
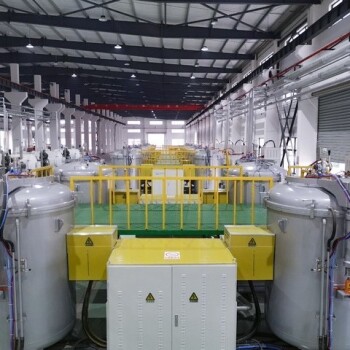
Vertical High Temperature Graphite Vacuum Graphitization Furnace
Vertical high temperature graphitization furnace for carbonization and graphitization of carbon materials up to 3100℃.Suitable for shaped graphitization of carbon fiber filaments and other materials sintered in a carbon environment.Applications in metallurgy, electronics, and aerospace for producing high-quality graphite products like electrodes and crucibles.
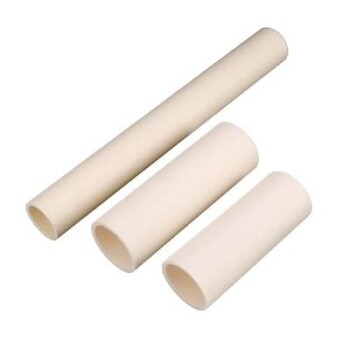
High Temperature Alumina (Al2O3) Furnace Tube for Engineering Advanced Fine Ceramics
High temperature alumina furnace tube combines the advantages of high hardness of alumina, good chemical inertness and steel, and has excellent wear resistance, thermal shock resistance and mechanical shock resistance.
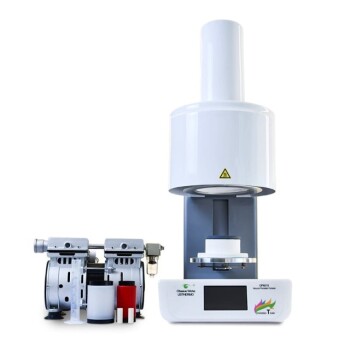
Dental Porcelain Zirconia Sintering Ceramic Vacuum Press Furnace
Get precise dental results with Dental Vacuum Press Furnace. Automatic temperature calibration, low noise tray, and touch screen operation. Order now!

Graphite Vacuum Furnace Bottom Discharge Graphitization Furnace for Carbon Materials
Bottom-out graphitization furnace for carbon materials, ultra-high temperature furnace up to 3100°C, suitable for graphitization and sintering of carbon rods and carbon blocks. Vertical design, bottom discharging, convenient feeding and discharging, high temperature uniformity, low energy consumption, good stability, hydraulic lifting system, convenient loading and unloading.
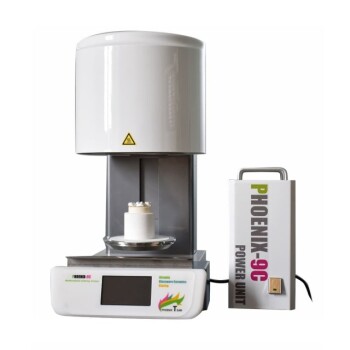
Dental Porcelain Zirconia Sintering Ceramic Furnace Chairside with Transformer
Experience top-notch sintering with Chairside Sintering Furnace with Transformer. Easy to operate, noise-free pallet, and automatic temperature calibration. Order now!
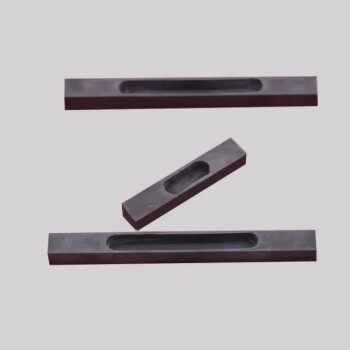
High Purity Pure Graphite Crucible for Evaporation
Vessels for high temperature applications, where materials are kept at extremely high temperatures to evaporate, allowing thin films to be deposited on substrates.
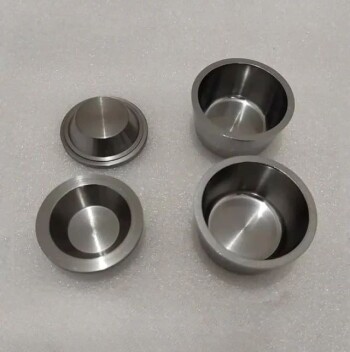
Tungsten and molybdenum crucibles are commonly used in electron beam evaporation processes due to their excellent thermal and mechanical properties.
Related Articles
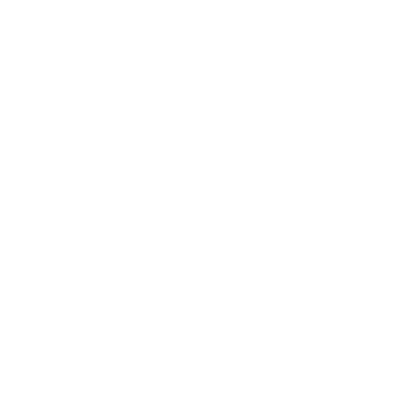
Rotary Furnaces: Advanced Materials Processing and Applications
Rotary furnaces are versatile and efficient thermal processing systems used in various industries. This comprehensive guide explores the basics of rotary furnaces, their applications, advantages, and key components. Discover how rotary furnaces contribute to advanced materials processing and enhance productivity.
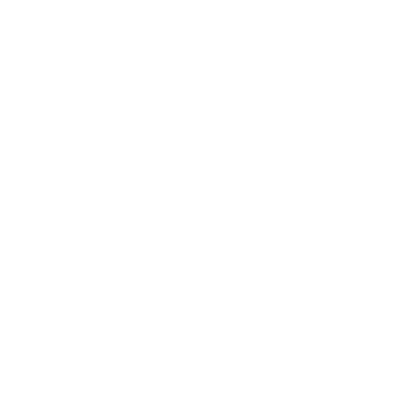
Top 5 Features of a High-Quality Zirconia Sintering Oven
Investing in a high-quality sintering oven is crucial for dental laboratories that want to produce high-quality zirconia restorations consistently.
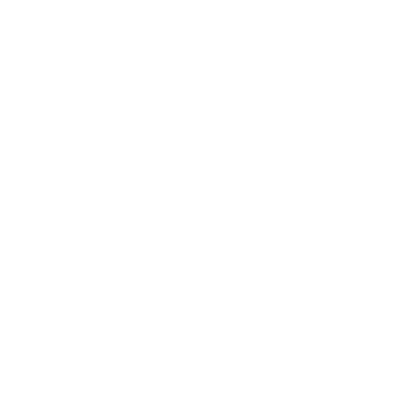
Infrared Heating Quantitative Flat Plate Mold: Design, Applications, and Benefits
Explore the advanced design and applications of infrared heating quantitative flat plate molds. Learn about their benefits in achieving uniform heat distribution and efficient processing.
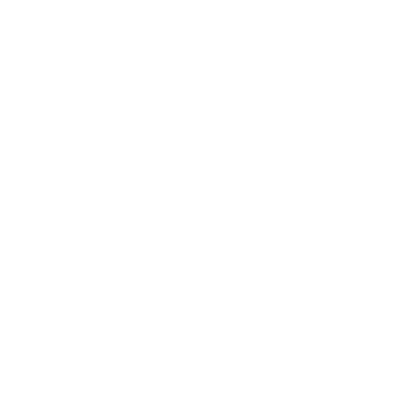
Understanding the Design and Functionality of Industrial Furnaces
Industrial furnaces are heating devices used in various industrial processes, including soldering, heat treatment of steels and alloys, and ceramics sintering.
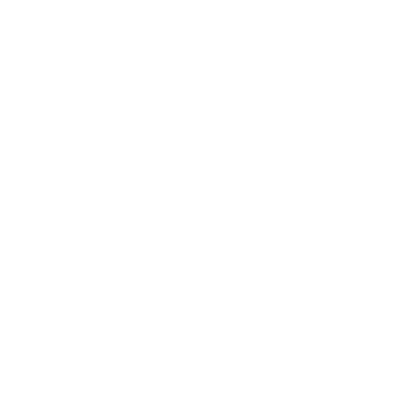
Understanding the Dry Bag Cold Isostatic Press Machine by KinTek
Powder metallurgy is a manufacturing route that allows for the production of specific materials, especially for high-performance applications. It reduces material waste and produces parts that are close to the final shape. KinTek's CIP equipment has been successfully used to consolidate most common metals, and there is a growing interest in using it for metal powder processing in a wider range of applications.
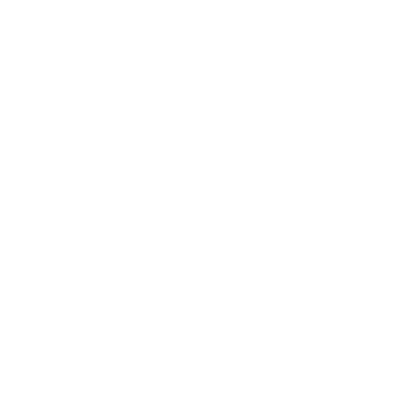
Comprehensive Guide to Muffle Furnaces: Applications, Types, and Maintenance
Explore the world of muffle furnaces with our detailed guide. Learn about their applications in various industries, types available, and essential maintenance tips to ensure optimal performance.
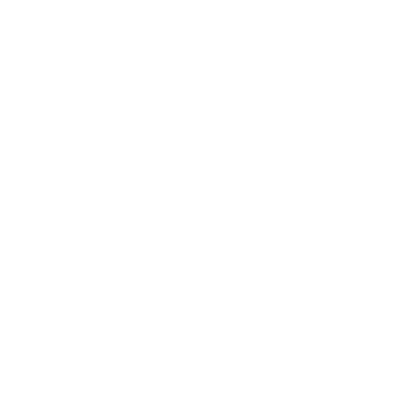
Dental Furnaces The Perfect Solution for Porcelain Processing
The dental furnaces are designed explicitly for the firing process of dental porcelain, which is a crucial step in the dental restoration process.
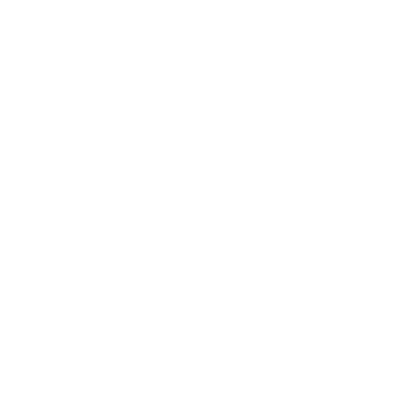
Comprehensive Guide to Vacuum Hot Press Furnace Application
The Vacuum Hot Press Furnace is a versatile tool especially suited for sintering experiments involving non-metallic materials, carbon composites, ceramic materials and metal powder materials.
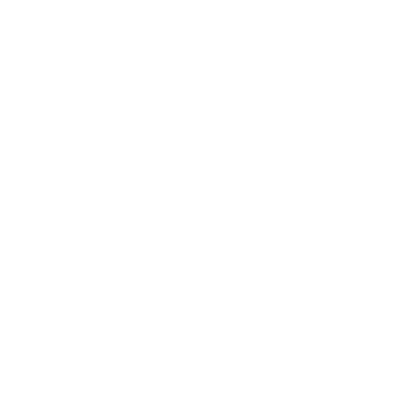
Spark Plasma Sintering Furnace: The Ultimate Guide to SPS Furnaces
Discover the world of Spark Plasma Sintering Furnaces (SPS). This comprehensive guide covers everything from its advantages and applications to its process and equipment. Learn how SPS furnaces can revolutionize your sintering operations.
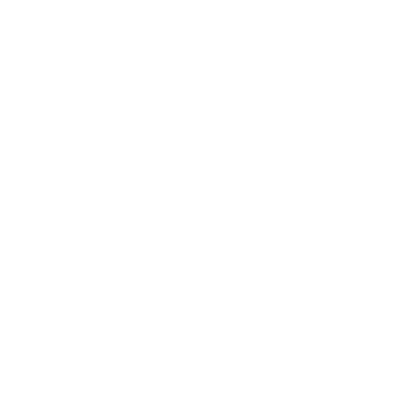
Comprehensive Guide to Muffle Furnaces: Types, Uses, and Maintenance
Explore the world of muffle furnaces with our detailed guide. Learn about their types, applications in various industries, and essential maintenance tips to ensure optimal performance.
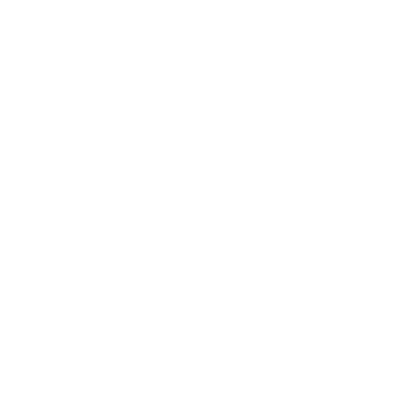
Understanding the Warm Isostatic Press: Operating Temperatures and Their Impact on Molding Quality and Efficiency
Warm isostatic pressing (WIP) is a variant of cold isostatic pressing (CIP) that includes a heating element. It employs warm water or a similar medium to apply uniform pressure to powdered products from all directions. WIP is a cutting-edge technology that enables isostatic pressing at a temperature that does not exceed the boiling point of the liquid medium. This process typically involves utilizing flexible materials as a jacket mold and hydraulic pressure as a pressure medium to shape and press the powder material.
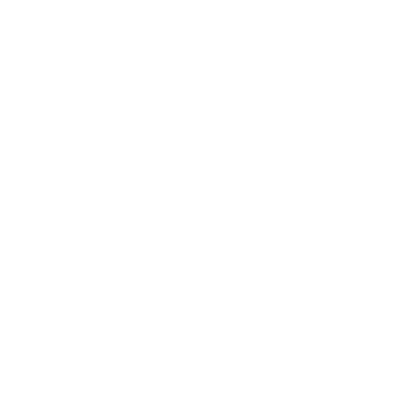
Analysis of the Isostatic Pressing Market
Isostatic pressing, is a manufacturing process that involves applying high-pressure gas to a material in order to shape and consolidate it. This technique is widely used in various industries, including aerospace, automotive, and medical, due to its ability to produce high-quality, defect-free components.