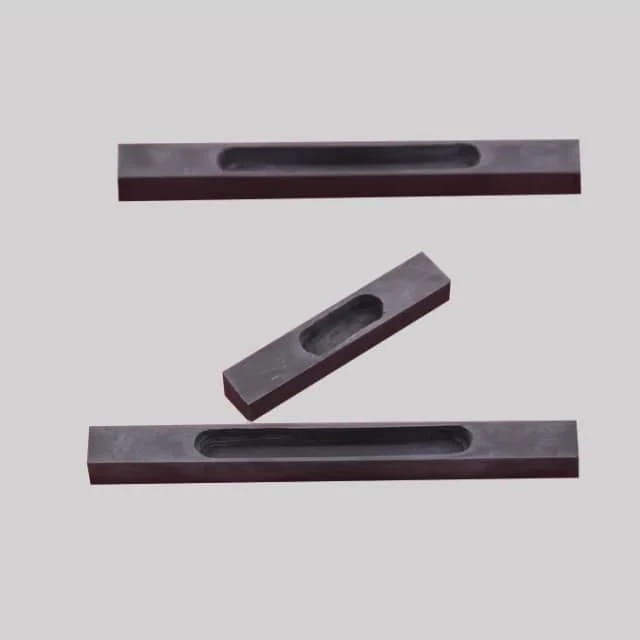
Thin Film Deposition Parts
High Purity Pure Graphite Crucible for Evaporation
Item Number : KME07
Price varies based on specs and customizations
- Material
- Graphite
- Accessories
- optional (Ceramic Evaporation Boat Electrode Chuck)
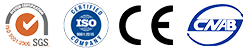
Shipping:
Contact us to get shipping details Enjoy On-time Dispatch Guarantee.
Why Choose Us
Reliable PartnerEasy ordering process, quality products, and dedicated support for your business success.
Application
Graphite evaporation crucibles are specialized vessels for high temperature applications, especially thin film deposition. These crucibles efficiently hold and evaporate materials at extreme temperatures, facilitating thin film deposition onto substrates. Graphite, known for its high thermal stability and excellent electrical conductivity, is the primary material used to manufacture these crucibles. Its thermal conductivity ensures efficient and uniform heating, resulting in a consistent vaporization rate.
- Semiconductor manufacturing, optics, materials research.
- Thermal evaporation, electron beam evaporation coating.
- Physical vapor deposition (PVD), chemical vapor deposition (CVD).
- Form thin films of metals, alloys, oxides and other materials on the substrate, plate germanium, and plate silicon.
- Optical coating, aluminum coating of polyester film, vacuum coating.
- Production of microelectronics, production of solar cells, wires and packaging materials, application of tube furnaces.
Detail & Parts
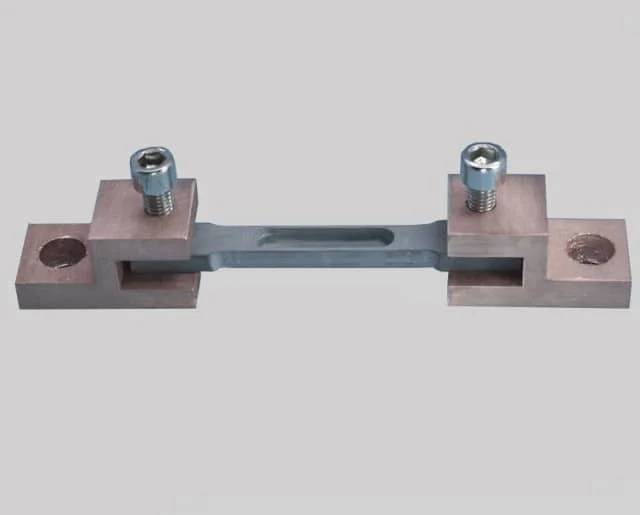
The crucibles we show are available in different sizes and custom sizes are available on request.
Advantage
- High temperature resistance, good thermal shock resistance, high thermal conductivity.
- Polished surface, anti-oxidation, high purity, no pollution to the evaporation film.
- It has strong corrosion resistance to acid and alkali liquids.
- Good conductivity and thermal efficiency, chemical stability.
- Resistance to mechanical shock, small coefficient of thermal expansion, long service life.
- High strength, as the temperature increases, the strength of graphite increases.
FAQ
What Are Thermal Evaporation Sources?
How Are High-purity Graphite Crucibles Made?
What Are The Main Types Of Thermal Evaporation Sources?
What Are The Common Applications Of High-purity Graphite Crucibles?
How Do Thermal Evaporation Sources Work?
What Are The Common Materials Used For Evaporating Crucibles?
What Factors Should Be Considered When Selecting High-purity Graphite Crucibles?
What Are The Advantages Of Using Thermal Evaporation Sources?
What Are The Advantages Of Using Evaporating Crucibles?
What Applications Are Thermal Evaporation Sources Used For?
How Should Evaporating Crucibles Be Handled And Maintained?
4.7
out of
5
The crucibles deliver prompt results and are cost-effective. Strongly recommended!
4.8
out of
5
The superb quality of these crucibles is worth every penny. Definitely a must-buy!
4.9
out of
5
The durability and technological advancement of these crucibles are truly impressive, ensuring reliable performance.
4.6
out of
5
These crucibles are an excellent investment for any laboratory, offering great value for money.
4.7
out of
5
The prompt delivery and exceptional quality of these crucibles have greatly enhanced our laboratory's efficiency.
4.8
out of
5
The crucibles' resistance to erosion and acid is remarkable, ensuring longevity and consistent performance.
4.9
out of
5
These crucibles are a testament to KINTEK SOLUTION's commitment to innovation and quality, making them an indispensable tool in our lab.
4.6
out of
5
The impact resistance and high thermal conductivity of these crucibles make them an excellent choice for demanding applications.
Products
High Purity Pure Graphite Crucible for Evaporation
REQUEST A QUOTE
Our professional team will reply to you within one business day. Please feel free to contact us!
Related Products
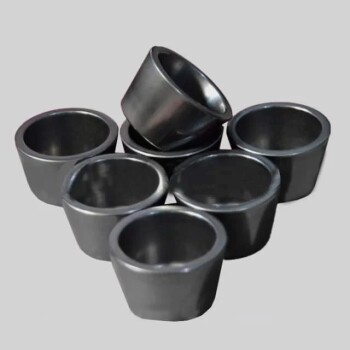
High Purity Pure Graphite Crucible for Electron Beam Evaporation
A technology mainly used in the field of power electronics. It is a graphite film made of carbon source material by material deposition using electron beam technology.
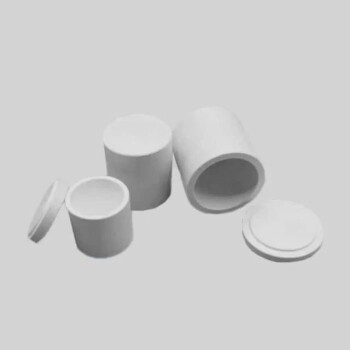
Evaporation Crucible for Organic Matter
An evaporation crucible for organic matter, referred to as an evaporation crucible, is a container for evaporating organic solvents in a laboratory environment.
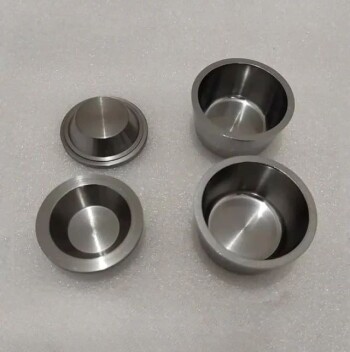
Tungsten and molybdenum crucibles are commonly used in electron beam evaporation processes due to their excellent thermal and mechanical properties.
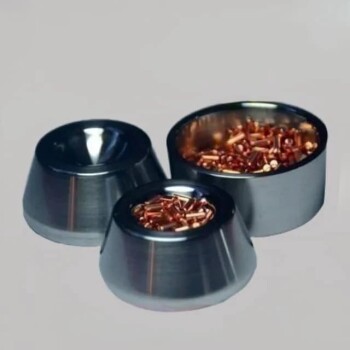
Electron Beam Evaporation Coating Gold Plating Tungsten Molybdenum Crucible for Evaporation
These crucibles act as containers for the gold material evaporated by the electron evaporation beam while precisely directing the electron beam for precise deposition.
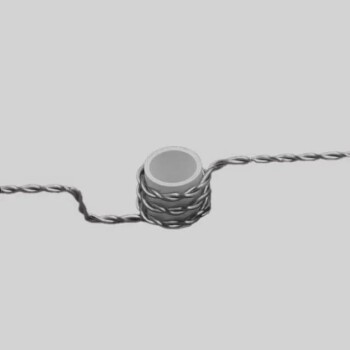
Ceramic Evaporation Boat Set Alumina Crucible for Laboratory Use
It can be used for vapor deposition of various metals and alloys. Most metals can be evaporated completely without loss. Evaporation baskets are reusable.1
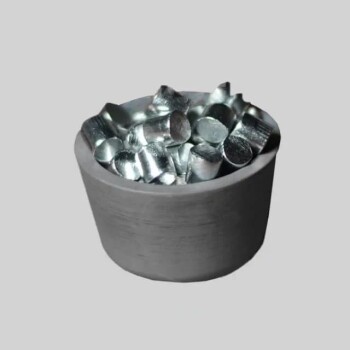
Electron Beam Evaporation Coating Conductive Boron Nitride Crucible BN Crucible
High-purity and smooth conductive boron nitride crucible for electron beam evaporation coating, with high temperature and thermal cycling performance.
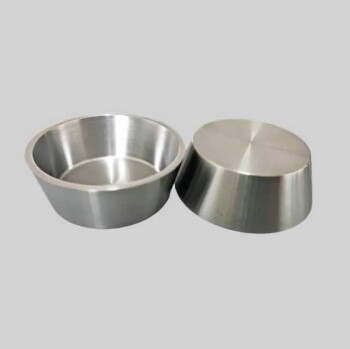
E Beam Crucibles Electron Gun Beam Crucible for Evaporation
In the context of electron gun beam evaporation, a crucible is a container or source holder used to contain and evaporate the material to be deposited onto a substrate.
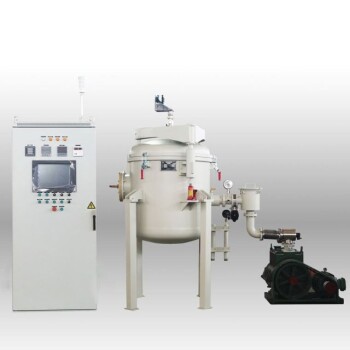
Ultra-High Temperature Graphite Vacuum Graphitization Furnace
The ultra-high temperature graphitization furnace utilizes medium frequency induction heating in a vacuum or inert gas environment. The induction coil generates an alternating magnetic field, inducing eddy currents in the graphite crucible, which heats up and radiates heat to the workpiece, bringing it to the desired temperature. This furnace is primarily used for graphitization and sintering of carbon materials, carbon fiber materials, and other composite materials.
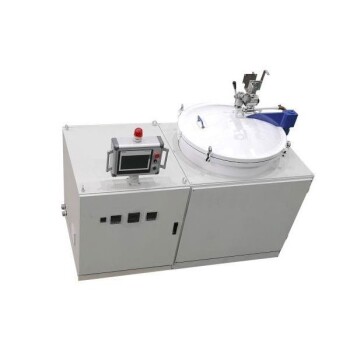
Graphite Vacuum Furnace IGBT Experimental Graphitization Furnace
IGBT experimental graphitization furnace, a tailored solution for universities and research institutions, with high heating efficiency, user-friendliness, and precise temperature control.
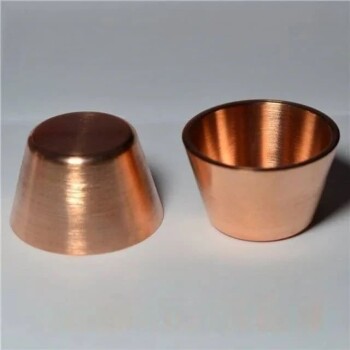
Electron Beam Evaporation Coating Oxygen-Free Copper Crucible and Evaporation Boat
Electron Beam Evaporation Coating Oxygen-Free Copper Crucible enables precise co-deposition of various materials. Its controlled temperature and water-cooled design ensure pure and efficient thin film deposition.
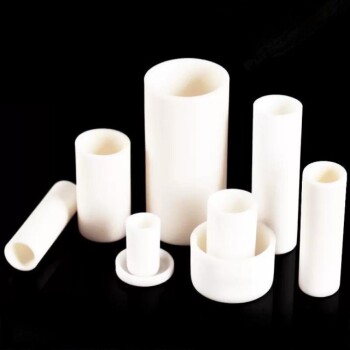
Engineering Advanced Fine Ceramics Alumina Al2O3 Crucible With Lid Cylindrical Laboratory Crucible
Cylindrical Crucibles Cylindrical crucibles are one of the most common crucible shapes, suitable for melting and processing a wide variety of materials, and are easy to handle and clean.
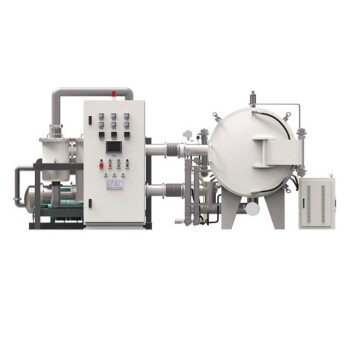
Horizontal High Temperature Graphite Vacuum Graphitization Furnace
Horizontal Graphitization Furnace: This type of furnace is designed with the heating elements placed horizontally, allowing for uniform heating of the sample. It's well-suited for graphitizing large or bulky samples that require precise temperature control and uniformity.
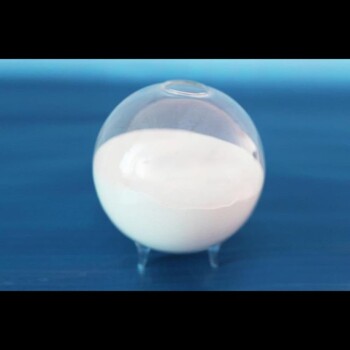
High Purity Alumina Granulated Powder for Engineering Advanced Fine Ceramics
Ordinary alumina granulated powder is alumina particles prepared by traditional processes, with a wide range of applications and good market adaptability. This material is known for its high purity, excellent thermal stability and chemical stability, and is suitable for a variety of high-temperature and conventional applications.
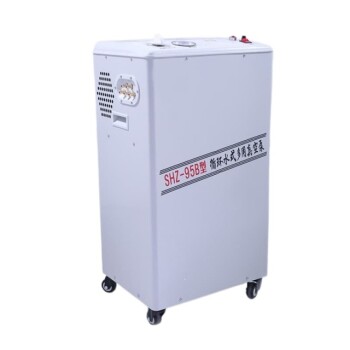
Laboratory Vertical Water Circulating Vacuum Pump for Lab Use
Looking for a reliable water circulating vacuum pump for your lab or small-scale industry? Check out our Vertical Water Circulating Vacuum Pump with five taps and a larger air sucking amount, perfect for evaporation, distillation, and more.
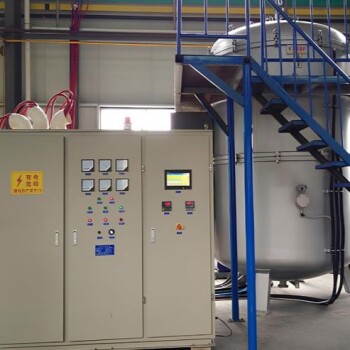
Large Vertical Graphite Vacuum Graphitization Furnace
A large vertical high-temperature graphitization furnace is a type of industrial furnace used for the graphitization of carbon materials, such as carbon fiber and carbon black. It is a high-temperature furnace that can reach temperatures of up to 3100°C.
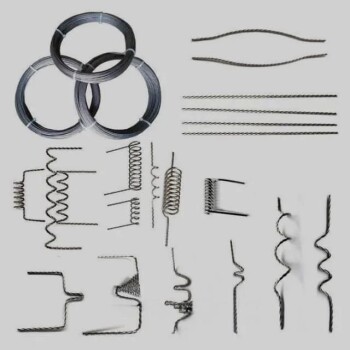
Thermally Evaporated Tungsten Wire for High Temperature Applications
It has a high melting point, thermal and electrical conductivity, and corrosion resistance. It is a valuable material for high temperature, vacuum and other industries.
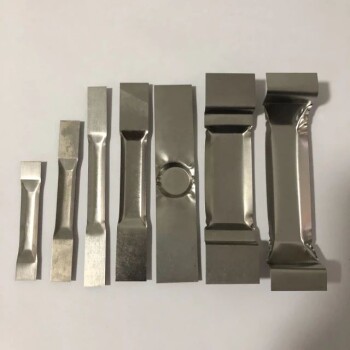
Tungsten Evaporation Boat for Thin Film Deposition
Learn about tungsten boats, also known as evaporated or coated tungsten boats. With a high tungsten content of 99.95%, these boats are ideal for high-temperature environments and widely used in various industries. Discover their properties and applications here.
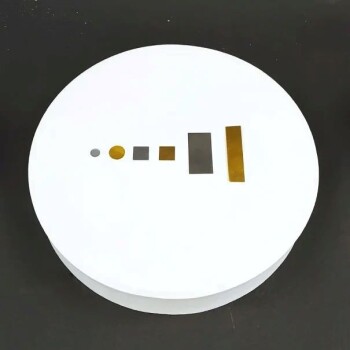
High Purity Gold Platinum Copper Iron Metal Sheets
Elevate your experiments with our high-purity sheet metal. Gold, platinum, copper, iron, and more. Perfect for electrochemistry and other fields.
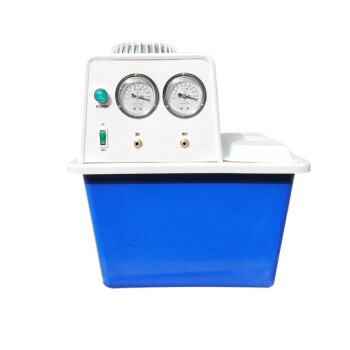
Laboratory Benchtop Water Circulating Vacuum Pump for Lab Use
Need a water circulating vacuum pump for your lab or small-scale industry? Our Benchtop Water Circulating Vacuum Pump is perfect for evaporation, distillation, crystallization, and more.
Related Articles
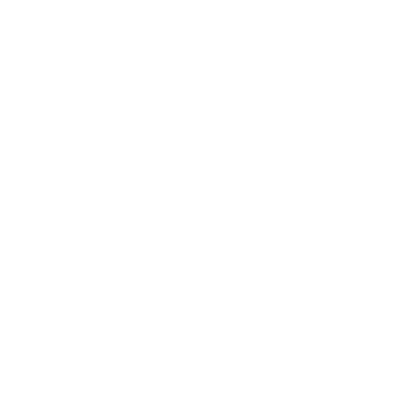
Chemical Vapor Deposition (CVD) of Graphene Challenges and Solutions
Chemical Vapor Deposition (CVD) is a widely adopted method for the production of high-quality graphene.
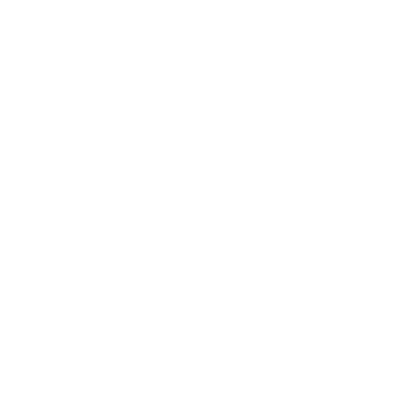
How CVD Coating Can Help You Achieve High Purity and Density
The CVD process offers several advantages over other coating techniques, such as high purity, uniformity, and the ability to deposit coatings with high-density.
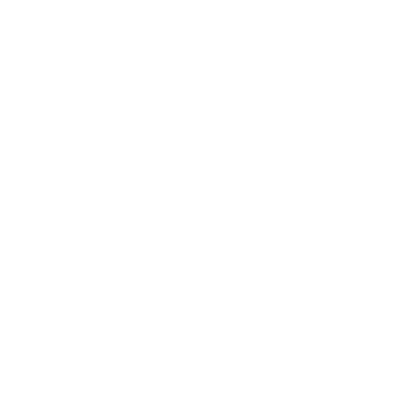
PECVD Furnace A Low-Power and Low-Temperature Solution for Soft Matter
PECVD (Plasma Enhanced Chemical Vapor Deposition) furnaces have become a popular solution for the deposition of thin films on soft matter surfaces.
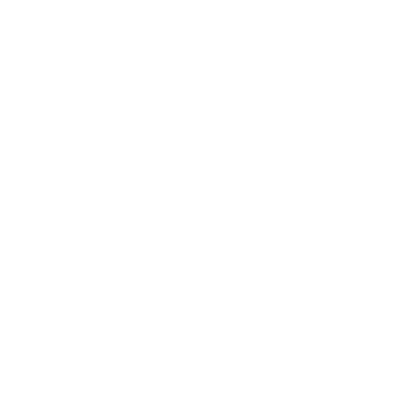
Unveiling Vacuum Graphite Furnaces: Performance, Applications, and Expert Insights
Delve into the world of vacuum graphite furnaces, exploring their exceptional performance, diverse applications, and crucial considerations. Our expert insights empower you to make informed decisions for your laboratory's high-temperature material treatment needs.
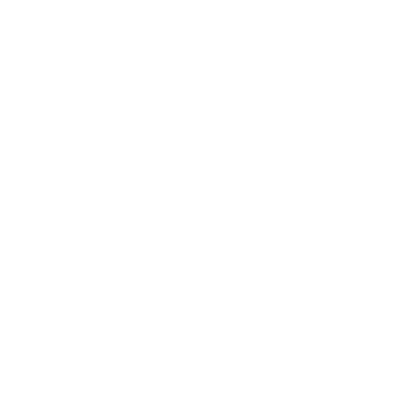
Comparing Chemical Vapor Deposition and Physical Vapor Deposition
Chemical Vapor Deposition (CVD) VS Physical Vapor Deposition (PVD)
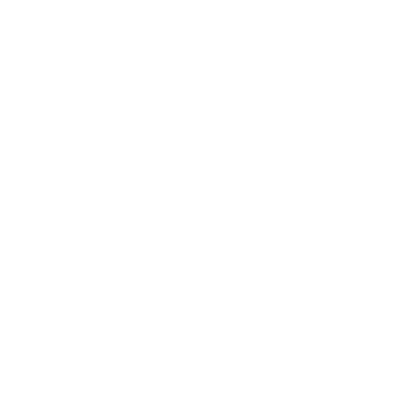
How CVD is Used in the Semiconductor Industry
CVD has revolutionized the semiconductor industry, enabling the production of high-performance electronic devices with enhanced functionality and reliability.
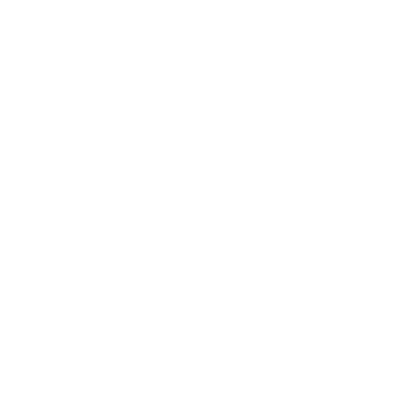
Advantages of Using CVD Tube Furnace for Coating
CVD coatings have several advantages over other coating methods, such as high purity, density, and uniformity, making them ideal for many applications in various industries.
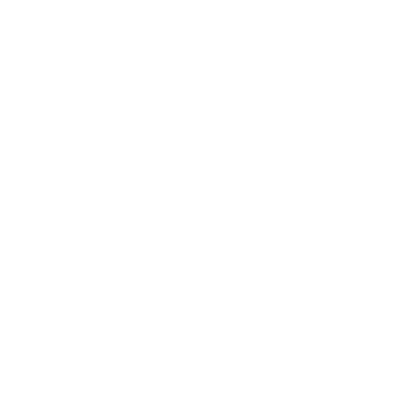
A Comparative Study of Evaporation and Sputtering Techniques in Thin Film Deposition
The two most common techniques used for thin film deposition are evaporation and sputtering.
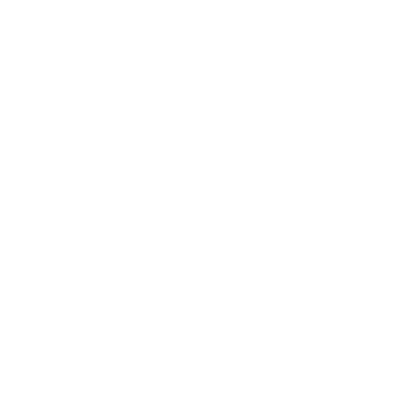
Optimizing Performance with Graphite Vacuum Furnaces: A Comprehensive Guide
Unlock the potential of graphite vacuum furnaces for high-temperature material treatment. Learn about their efficiency, customization options, automation, and key considerations for graphite rod usage.
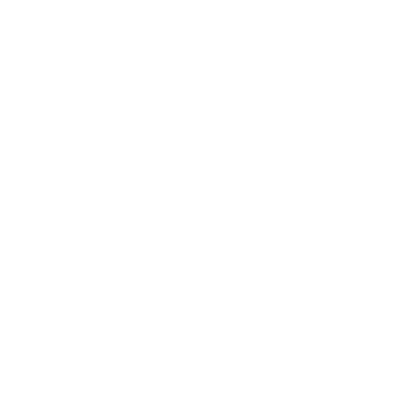
A Comprehensive Guide to Vacuum Coating: Enhancing Performance and Aesthetics
Discover the world of vacuum coating, a process that creates protective and aesthetic layers on metal and plastic surfaces. Explore its types, uses, and benefits, including enhanced performance, extended lifespan, and improved aesthetics.
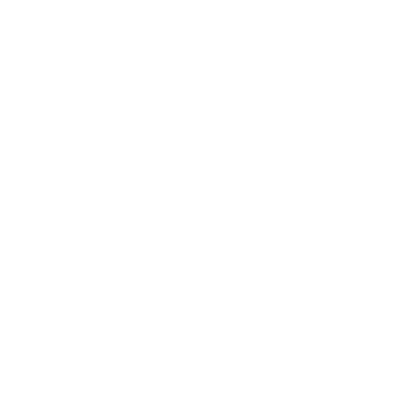
Rotary Furnaces: Advanced Materials Processing and Applications
Rotary furnaces are versatile and efficient thermal processing systems used in various industries. This comprehensive guide explores the basics of rotary furnaces, their applications, advantages, and key components. Discover how rotary furnaces contribute to advanced materials processing and enhance productivity.
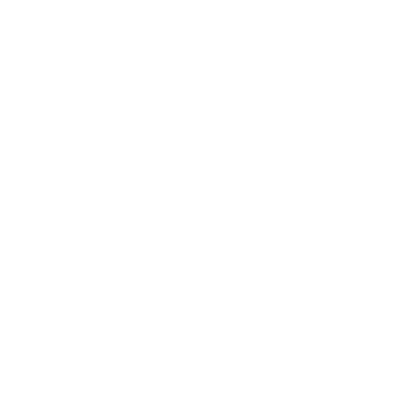
Electrode Fixture Guide: Types, Design, and Applications
Discover the comprehensive guide to electrode fixtures, covering various types, design considerations, and their indispensable role in industries like electroplating, welding, and electrochemical cells.