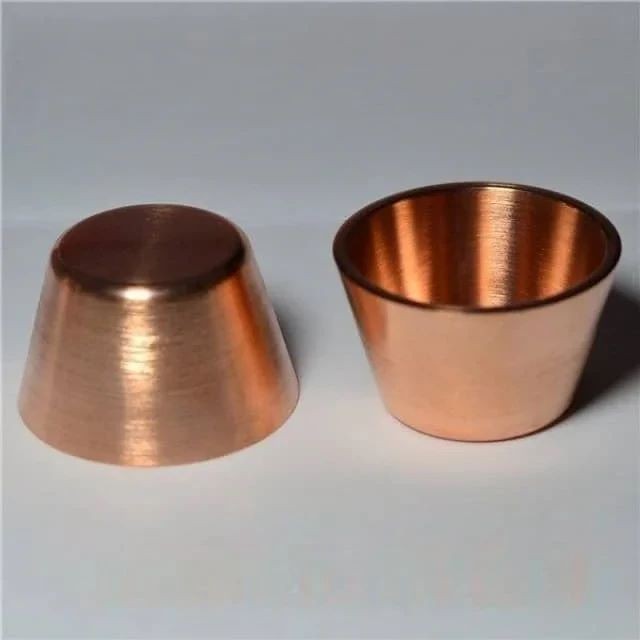
Thin Film Deposition Parts
Electron Beam Evaporation Coating Oxygen-Free Copper Crucible and Evaporation Boat
Item Number : KMS06
Price varies based on specs and customizations
- Material
- Oxygen-free copper
- Specification
- 35-50*17-25mm
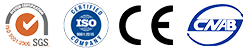
Shipping:
Contact us to get shipping details Enjoy On-time Dispatch Guarantee.
Why Choose Us
Reliable PartnerEasy ordering process, quality products, and dedicated support for your business success.
Introduction
Electron Beam Evaporation Coating Oxygen-Free Copper Crucible is a type of laboratory equipment used for the deposition of thin films. It uses an electron beam to vaporize a material, which is then deposited on a substrate. This process is used to create thin films of metals, dielectrics, and other materials.
The Electron Beam Evaporation Coating Oxygen-Free Copper Crucible is made of oxygen-free copper, which has a high thermal conductivity and is resistant to oxidation. This makes it ideal for use in high-temperature applications. The crucible is also water-cooled to prevent it from overheating.
The Electron Beam Evaporation Coating Oxygen-Free Copper Crucible is a versatile piece of equipment that can be used for a variety of applications. It is commonly used in the semiconductor industry, but it can also be used in other industries, such as the optical and medical industries.
Application
Electron beam evaporation coating refers to the process of using electron beams to evaporate materials in the process of thin film deposition, and then condense them on the substrate to form a thin film. When using electron beam evaporation techniques, use oxygen-free copper crucibles to maintain an oxygen-free or oxygen-depleted environment to minimize the risk of oxygen contamination during evaporation. This helps ensure that high-quality films are deposited without unwanted chemical reactions or oxidation. Oxygen-free copper crucibles are often preferred when handling sensitive materials or depositing thin films where high purity is required.
- Semiconductor Industry: Manufacture of integrated circuits, semiconductor devices and microelectronics.
- Optics and Photonics: Optical coatings and films for lenses, mirrors, filters, waveguides and other optical components.
- Solar energy: Electron beam evaporation is used to make thin film solar cells such as CIGS (copper indium gallium selenide) and CdTe (cadmium telluride) solar cells.
- Display technology: E-beam evaporation is used to produce thin films for various types of displays, including LCD (Liquid Crystal Display), OLED (Organic Light Emitting Diode) and microdisplay technologies.
- Manufacturing of sensors and electronics: Electron beam evaporation is used to produce thin films for sensors, electronics and integrated circuits.
Technical specifications
Outer diameter & High | 35*17mm | 40*17mm | 45*22mm | 50*25mm |
The crucibles we show are available in different sizes and custom sizes are available on request.
Features
Electron Beam Evaporation Coating Oxygen-Free Copper Crucible features a four-pocket hearth that can contain up to four source materials, allowing for the sequential deposition of four material layers without breaking the vacuum. This makes it easy to apply several different layers of coating from different target materials, adapting easily to a variety of lift-off masking techniques.
The crucible is water-cooled to prevent it from heating through thermal energy, and directly heating the source materials eliminates the risk of heat damage to the substrate. This makes E-Beam Evaporation ideal for applications where high temperatures and wear resistance are key, such as in the aerospace, automotive, and cutting tool industries.
E-Beam Evaporation is also used for optical thin films ranging from laser optics, solar panels, eye glasses and architectural glass to give them the desired conductive, reflective and transmissive qualities.
FAQ
What Is Physical Vapor Deposition (PVD)?
What Is Magnetron Sputtering?
What Are The Methods Used To Deposit Thin Films?
Why Magnetron Sputtering?
What Is Thin Film Deposition Equipment?
What Are The Advantages Of Using Evaporation Boats?
What Are The Common Materials Used For Evaporating Crucibles?
What Are The Materials Used In Thin Film Deposition?
Thin film deposition commonly utilizes metals, oxides, and compounds as materials, each with its unique advantages and disadvantages. Metals are preferred for their durability and ease of deposition but are relatively expensive. Oxides are highly durable, can withstand high temperatures, and can be deposited at low temperatures, but can be brittle and challenging to work with. Compounds offer strength and durability, can be deposited at low temperatures and tailored to exhibit specific properties.
The selection of material for a thin film coating is dependent on the application requirements. Metals are ideal for thermal and electrical conduction, while oxides are effective in offering protection. Compounds can be tailored to suit specific needs. Ultimately, the best material for a particular project will depend on the specific needs of the application.
What Is Thin-film Deposition Technology?
What Is The Typical Lifespan Of An Evaporation Boat?
What Are The Advantages Of Using Evaporating Crucibles?
What Are The Methods To Achieve Optimal Thin Film Deposition?
To achieve thin films with desirable properties, high-quality sputtering targets and evaporation materials are essential. The quality of these materials can be influenced by various factors, such as purity, grain size, and surface condition.
The purity of sputtering targets or evaporation materials plays a crucial role, as impurities can cause defects in the resulting thin film. Grain size also affects the quality of the thin film, with larger grains leading to poor film properties. Additionally, the surface condition is crucial, since rough surfaces can result in defects in the film.
To attain the highest quality sputtering targets and evaporation materials, it is crucial to select materials that possess high purity, small grain size, and smooth surfaces.
Uses Of Thin Film Deposition
Zinc Oxide-Based Thin Films
ZnO thin films find applications in several industries such as thermal, optical, magnetic, and electrical, but their primary use is in coatings and semiconductor devices.
Thin-Film Resistors
Thin-film resistors are crucial for modern technology and are used in radio receivers, circuit boards, computers, radiofrequency devices, monitors, wireless routers, Bluetooth modules, and cell phone receivers.
Magnetic Thin Films
Magnetic thin films are used in electronics, data storage, radio-frequency identification, microwave devices, displays, circuit boards, and optoelectronics as key components.
Optical Thin Films
Optical coatings and optoelectronics are standard applications of optical thin films. Molecular beam epitaxy can produce optoelectronic thin-film devices (semiconductors), where epitaxial films are deposited one atom at a time onto the substrate.
Polymer Thin Films
Polymer thin films are used in memory chips, solar cells, and electronic devices. Chemical deposition techniques (CVD) offer precise control of polymer film coatings, including conformance and coating thickness.
Thin-Film Batteries
Thin-film batteries power electronic devices such as implantable medical devices, and the lithium-ion battery has advanced significantly thanks to the use of thin films.
Thin-Film Coatings
Thin-film coatings enhance the chemical and mechanical characteristics of target materials in various industries and technological fields. Anti-reflective coatings, anti-ultraviolet or anti-infrared coatings, anti-scratch coatings, and lens polarization are some common examples.
Thin-Film Solar Cells
Thin-film solar cells are essential to the solar energy industry, enabling the production of relatively cheap and clean electricity. Photovoltaic systems and thermal energy are the two main applicable technologies.
What Are The Advantages Of Using Thin Film Deposition Equipment?
Can Evaporation Boats Be Reused?
How Should Evaporating Crucibles Be Handled And Maintained?
Factors And Parameters That Influence Deposition Of Thin Films
Deposition Rate:
The rate at which the film is produced, typically measured in thickness divided by time, is crucial for selecting a technology suitable for the application. Moderate deposition rates are sufficient for thin films, while quick deposition rates are necessary for thick films. It is important to strike a balance between speed and precise film thickness control.
Uniformity:
The consistency of the film across the substrate is known as uniformity, which usually refers to film thickness but can also relate to other properties such as the index of refraction. It is important to have a good understanding of the application to avoid under- or over-specifying uniformity.
Fill Capability:
Fill capability or step coverage refers to how well the deposition process covers the substrate's topography. The deposition method used (e.g., CVD, PVD, IBD, or ALD) has a significant impact on step coverage and fill.
Film Characteristics:
The characteristics of the film depend on the application's requirements, which can be categorized as photonic, optical, electronic, mechanical, or chemical. Most films must meet requirements in more than one category.
Process Temperature:
Film characteristics are significantly affected by process temperature, which may be limited by the application.
Damage:
Each deposition technology has the potential to damage the material being deposited upon, with smaller features being more susceptible to process damage. Pollution, UV radiation, and ion bombardment are among the potential sources of damage. It is crucial to understand the limitations of the materials and tools.
What Factors Should Be Considered When Selecting Thin Film Deposition Equipment?
How Do You Select The Appropriate Evaporation Boat Material?
What Safety Considerations Are Associated With Operating Thin Film Deposition Equipment?
4.8
out of
5
Prompt delivery. Well-packaged and protected.
4.9
out of
5
Amazing quality, works like a charm. Worth every penny!
4.7
out of
5
Durable and long-lasting. Highly recommended!
4.6
out of
5
Great value for money. Exceeded my expectations.
4.8
out of
5
Top-notch quality. Highly satisfied with my purchase.
4.9
out of
5
State-of-the-art technology. Works flawlessly.
4.7
out of
5
Easy to use and maintain. Made my work so much easier.
4.6
out of
5
Reliable and efficient. Highly recommend it to others.
4.8
out of
5
Great addition to my lab. Highly satisfied with the results.
4.9
out of
5
Excellent product. Meets all my requirements.
4.7
out of
5
User-friendly interface. Makes my work more efficient.
Products
Electron Beam Evaporation Coating Oxygen-Free Copper Crucible and Evaporation Boat
REQUEST A QUOTE
Our professional team will reply to you within one business day. Please feel free to contact us!
Related Products
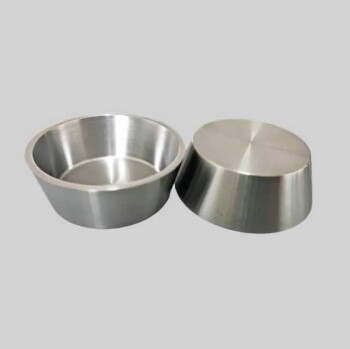
E Beam Crucibles Electron Gun Beam Crucible for Evaporation
In the context of electron gun beam evaporation, a crucible is a container or source holder used to contain and evaporate the material to be deposited onto a substrate.
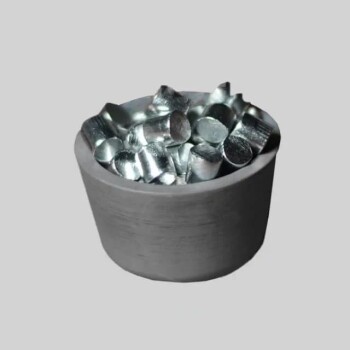
Electron Beam Evaporation Coating Conductive Boron Nitride Crucible BN Crucible
High-purity and smooth conductive boron nitride crucible for electron beam evaporation coating, with high temperature and thermal cycling performance.
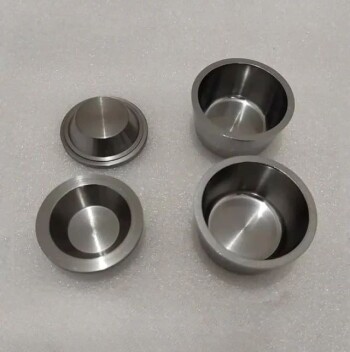
Tungsten and molybdenum crucibles are commonly used in electron beam evaporation processes due to their excellent thermal and mechanical properties.
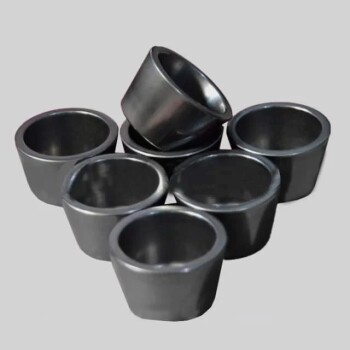
High Purity Pure Graphite Crucible for Electron Beam Evaporation
A technology mainly used in the field of power electronics. It is a graphite film made of carbon source material by material deposition using electron beam technology.
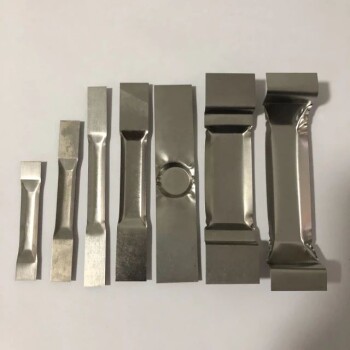
Tungsten Evaporation Boat for Thin Film Deposition
Learn about tungsten boats, also known as evaporated or coated tungsten boats. With a high tungsten content of 99.95%, these boats are ideal for high-temperature environments and widely used in various industries. Discover their properties and applications here.
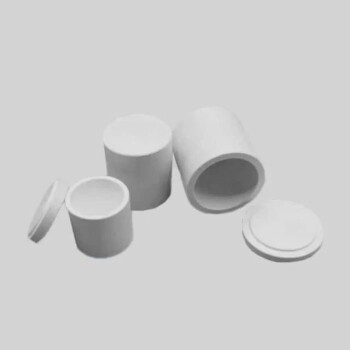
Evaporation Crucible for Organic Matter
An evaporation crucible for organic matter, referred to as an evaporation crucible, is a container for evaporating organic solvents in a laboratory environment.
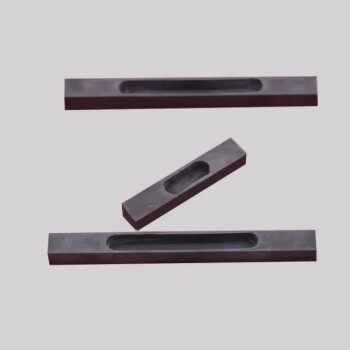
High Purity Pure Graphite Crucible for Evaporation
Vessels for high temperature applications, where materials are kept at extremely high temperatures to evaporate, allowing thin films to be deposited on substrates.
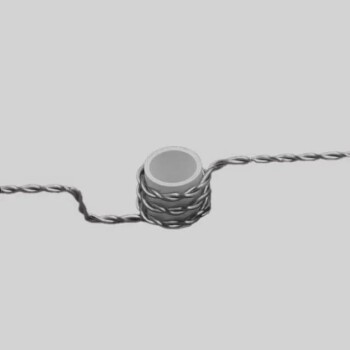
Ceramic Evaporation Boat Set Alumina Crucible for Laboratory Use
It can be used for vapor deposition of various metals and alloys. Most metals can be evaporated completely without loss. Evaporation baskets are reusable.1
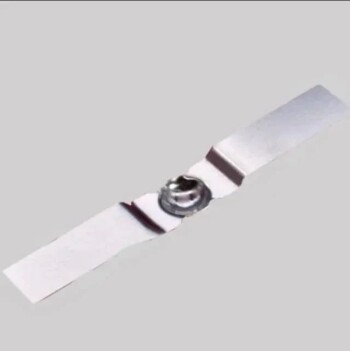
Hemispherical Bottom Tungsten Molybdenum Evaporation Boat
Used for gold plating, silver plating, platinum, palladium, suitable for a small amount of thin film materials. Reduce the waste of film materials and reduce heat dissipation.
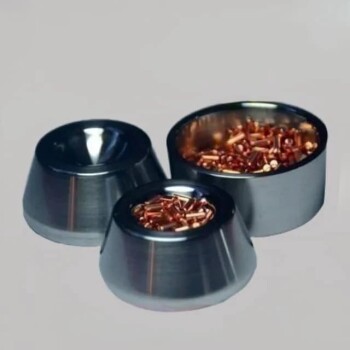
Electron Beam Evaporation Coating Gold Plating Tungsten Molybdenum Crucible for Evaporation
These crucibles act as containers for the gold material evaporated by the electron evaporation beam while precisely directing the electron beam for precise deposition.
Related Articles
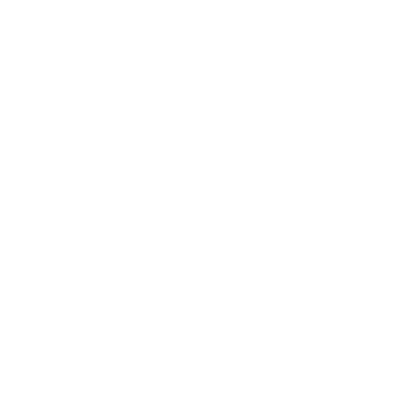
A Comparative Study of Evaporation and Sputtering Techniques in Thin Film Deposition
The two most common techniques used for thin film deposition are evaporation and sputtering.
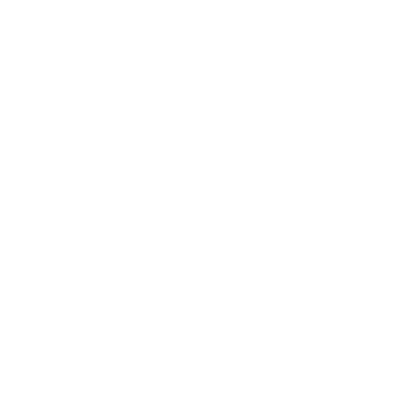
Understanding Electrodeposition with Electrochemical Electrodes
Electrodeposition is a process of depositing a metal or a non-metallic material onto a surface by applying an electric current.
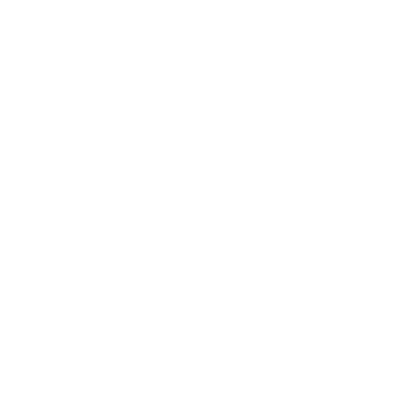
Electron Beam Evaporation Coating Technology and Material Selection
An in-depth look at the principles and applications of electron beam evaporation coating technology, including material selection and various fields of application.
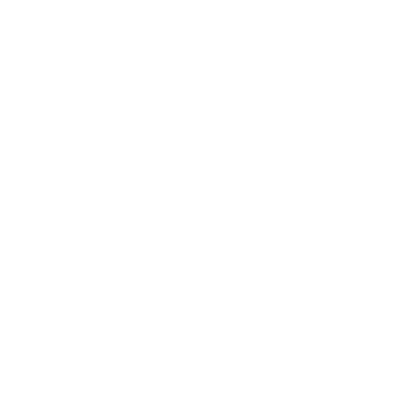
Understanding Electrolytic Cells and Their Role in Copper Purification and Electroplating
Electrolytic cells play a crucial role in various industrial processes, including copper purification and electroplating. These cells utilize an external power source to drive chemical reactions, resulting in the decomposition of substances. Through the process of electrolysis, an electric current is passed through a liquid or solution containing ions, causing them to break down.
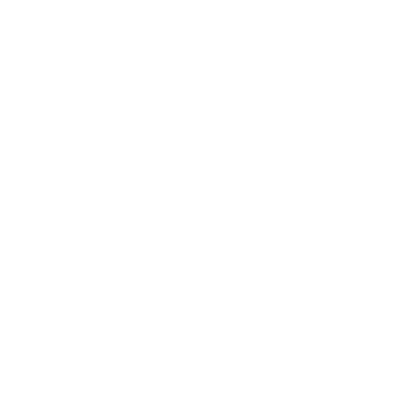
Advanced Techniques in Coating Evaluation Using Electrolytic Cells
Explore the comprehensive guide on coating evaluation using electrolytic cells, covering electroplating, sol-gel methods, and wet chemical techniques. Enhance your understanding of metal coating properties and applications.
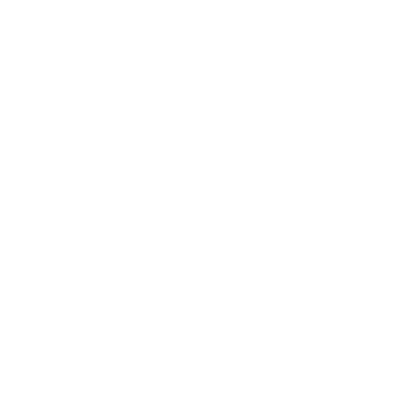
Electron Beam Evaporation Technology in Vacuum Coating
An in-depth look at electron beam evaporation, its types, advantages, and disadvantages in vacuum coating processes.
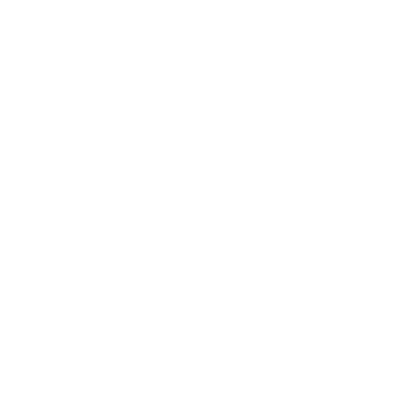
Electron Beam Evaporation Coating: Principles, Characteristics, and Applications
An in-depth analysis of electron beam evaporation coating technology, its advantages, disadvantages, and applications in thin film manufacturing.
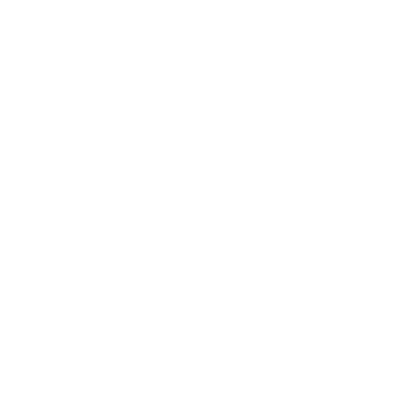
Electron Beam Evaporation: Advanced Thin Film Creation
Explores the technology and applications of electron beam evaporation in thin film production.
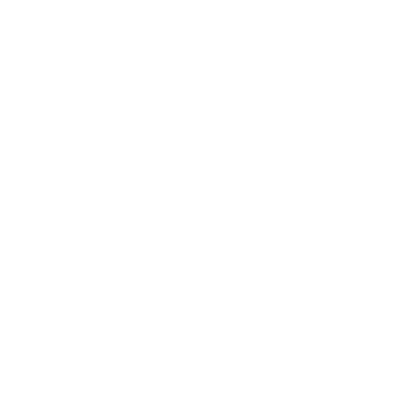
Vacuum Melting Furnace: A Comprehensive Guide to Vacuum Induction Melting
Discover the intricacies of vacuum induction melting furnaces, their components, operation, advantages, and applications. Explore how these furnaces revolutionize metal processing and achieve exceptional material properties.
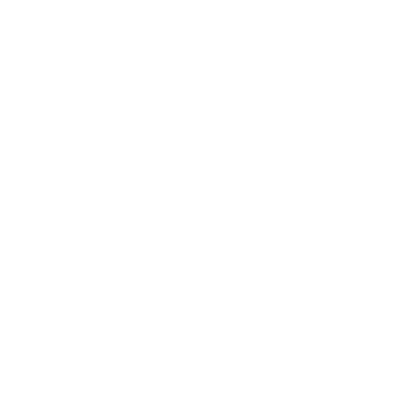
Electron Beam Evaporation Coating: Advantages, Disadvantages, and Applications
An in-depth look at the pros and cons of electron beam evaporation coating and its various applications in industries.
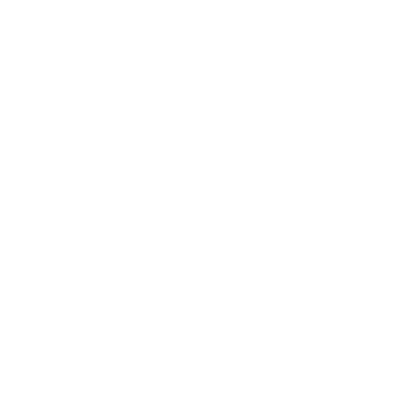
Understanding Electrodes and Electrochemical Cells
An electrode is a point where current enters and leaves the electrolyte. It is a conductor used to make a junction with a nonmetallic part of a circuit. Electrodes can be made of materials such as gold, platinum, carbon, graphite, or metal. They serve as the surface for oxidation-reduction reactions in electrochemical cells. There are different types of electrodes, including anode and cathode.
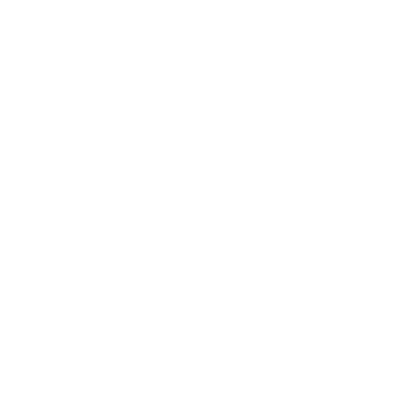
Selecting Vacuum Coating Materials: Key Factors and Considerations
Guidelines on choosing the right vacuum coating materials based on application, material properties, deposition methods, economy, substrate compatibility, and safety.