Introduction to Electrodeposition
Electrodeposition is a process of depositing a metal or a non-metallic material onto a surface by applying an electric current. This process is widely used in various industries such as electronics, automotive, and aerospace. Electrodeposition can be carried out using different types of electrochemical electrodes such as anode and cathode. The selection of the electrode depends on the type of material to be deposited and the desired properties of the coating. The electrolyte plays a crucial role in this process as it provides the necessary ions for electrodeposition. Electrodeposition has various applications such as electrowinning, electroplating, and battery production. Understanding the basics of electrodeposition is important for anyone working with electrochemical electrodes.
Table of Contents
- Introduction to Electrodeposition
- Importance of Electrochemical Electrodes
- Working electrode: role and preparation
- Electrode Selection Criteria
- Electrolyte and its role in electrodeposition
- Anode and Cathode: Functions and Reactions
- Electroplating and Electrowinning Applications
- Conclusion on Electrodeposition and Electrochemical Electrodes
Importance of Electrochemical Electrodes
Electrodeposition is a process that involves the deposition of a metal or a non-metal onto a substrate by means of an electric current. Electrochemical electrodes play a vital role in this process. These electrodes are used to apply an electric current to the substrate, which in turn triggers the deposition process.
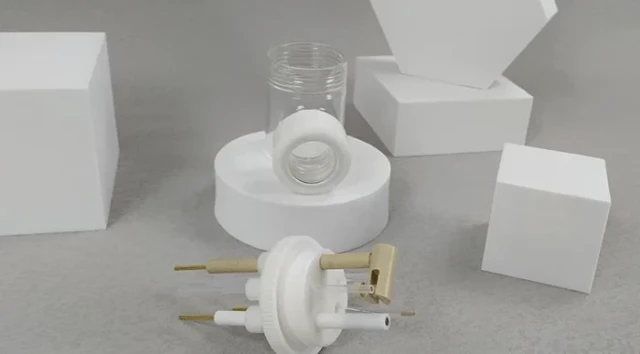
The Role of Electrochemical Electrodes in Electrodeposition
Electrochemical electrodes are made from a variety of materials, including platinum, gold, and graphite. They are designed to be highly conductive and to resist corrosion, which makes them ideal for use in electroplating and other electrochemical processes. Electrodeposition is used in a wide range of applications, including the production of metal coatings, the manufacture of electronic components, and the purification of metals.
Why Electrochemical Electrodes are Important?
The importance of electrochemical electrodes in this process cannot be overstated. They are essential components of the electroplating process, and without them, it would be impossible to achieve the level of precision and control that is required for many applications. As such, understanding the role of electrochemical electrodes in electrodeposition is crucial for anyone involved in the field of laboratory equipment.
Applications of Electrochemical Electrodes
Electrodeposition is used in a wide range of applications, including the production of metal coatings, the manufacture of electronic components, and the purification of metals. In the production of metal coatings, electrochemical electrodes are used to deposit a thin layer of metal onto a substrate, providing protection against corrosion and wear. In the manufacture of electronic components, electrochemical electrodes are used to deposit thin films of metal onto a substrate, creating the necessary electrical connections.
Conclusion
In conclusion, electrochemical electrodes play a crucial role in the process of electrodeposition. They are essential components of the electroplating process and are used in a wide range of applications. Understanding the principles of electrochemical electrodes is crucial for anyone involved in the field of laboratory equipment. By developing new and innovative processes for the electrochemical deposition of metals and other materials, scientists and researchers can ultimately lead to the development of new technologies and applications in a wide range of industries.
Working electrode: role and preparation
In electrodeposition, a metal is deposited onto a surface by applying an electric current. The working electrode is the electrode where the reduction or oxidation reaction takes place. It is usually made of a conductive material, such as platinum or gold, and is coated with the metal being deposited.
Role of the Working Electrode
The working electrode plays a crucial role in electrodeposition by serving as the electrode where the reduction or oxidation reaction takes place. The current that passes to or from this electrode is what is recorded by the potentiostat. In most cyclic voltammetry experiments, there are three electrodes, and the working electrode is the electrode being studied. In corrosion experiments, this is probably the material that is corroding. In physical-electrochemistry experiments, this is most often an inert material—commonly gold, platinum or carbon—which passes current to other species without being affected by that current.
Preparation of the Working Electrode
The preparation of the working electrode is a crucial step in electrodeposition. The surface of the electrode must be clean and free of any contaminants that could interfere with the electrochemical reaction. Polishing the electrode with a fine abrasive material and cleaning it with a solvent, such as acetone or ethanol, can achieve this. This ensures that there are no undesired species on the electrode surface that may inhibit electron transfer to or from the electrode.
It is crucial to ensure that the geometric area of the electrode is close to the true surface area to make sure that the electrode is well polished with no jagged edges or grooves. Common methods of polishing are described in detail in the next section.
Polishing Methods
Polishing the electrode with a fine abrasive material is necessary to ensure that there are no undesired species on the electrode surface that may inhibit electron transfer to or from the electrode. The most common abrasive material used is alumina powder, which is available in various sizes ranging from 0.05 to 5 microns. The polishing process usually involves applying the abrasive powder to a polishing cloth or pad and then rubbing the electrode against the pad in a circular motion. The process is repeated with progressively finer abrasive powders until the desired surface finish is achieved.
Positioning the Working Electrode
The working electrode must also be properly positioned in relation to the other electrodes in the electrochemical cell. The distance between the working electrode and the counter electrode, which completes the circuit, must be carefully controlled to ensure the proper flow of current. The physical setup for two-electrode mode has the current and sense leads connected together: working and working sense are connected to a (working) electrode and reference and counter are connected to a second (aux, counter, or quasi-/pseudo-reference) electrode.
Understanding the role and preparation of the working electrode is essential for successful electrodeposition. The working electrode is where the reduction or oxidation reaction takes place, and it must be properly prepared to ensure that there are no contaminants that could interfere with the electrochemical reaction. Proper positioning of the working electrode in relation to the other electrodes in the electrochemical cell is also crucial to ensure the proper flow of current.
Electrode Selection Criteria
Electrode selection is crucial in electrodeposition as it determines the quality and characteristics of the deposited layer. The choice of electrode material depends on various factors such as the type of electrolyte used, the deposition current density, the desired thickness, and the substrate material.
Electrode Material
Electrodes can be made of different materials such as platinum, gold, stainless steel, and graphite. The choice of electrode material determines the stability, reactivity, and conductivity of the electrode. For instance, platinum electrodes are preferred for electrodeposition in acidic solutions, while graphite electrodes are commonly used in alkaline solutions.
Electrode Size and Shape
The size and shape of the electrode also play an important role in electrodeposition as they determine the efficiency and uniformity of the deposition process. The larger the electrode surface area, the higher the deposition rate, and the more uniform the deposition. The shape of the electrode can also affect the deposition rate and uniformity.
Electrode Stability
The stability of the electrode is important for ensuring longevity of use. However, the stability of the substrate or the intermediates produced on the electrode is also important for ensuring high yields of product. A compound can irreversibly bind and decompose on the surface, leading to a decreased mass balance and yield of product.
Electrode Efficiency
The physical properties of electrodes are mainly determined by the material of the electrode and the topology of the electrode. The properties required depend on the application, and therefore, there are many kinds of electrodes in circulation. The defining property for a material to be used as an electrode is that it be conductive. Any conducting material such as metals, semiconductors, graphite or conductive polymers can, therefore, be used as an electrode. Often electrodes consist of a combination of materials, each with a specific task.
Surface Effects
The surface topology of the electrode plays an important factor in determining the efficiency of an electrode. The efficiency of the electrode can be reduced due to contact resistance. To create an efficient electrode, it is, therefore, important to design it such that it minimizes the contact resistance.
In summary, selecting the right electrode is critical for achieving a successful electrodeposition process, and careful consideration should be given to the selection criteria. The electrode material, size and shape, stability, and efficiency, as well as surface effects, should be taken into account when choosing an electrode for a specific application.
Electrolyte and its role in electrodeposition
Electrolytes play a crucial role in the electrodeposition process. During electrodeposition, the metal ions in the electrolyte are reduced at the conductive surface, forming a thin layer of metal. The properties of the electrolyte, such as pH, temperature, and concentration, affect the rate and quality of the electrodeposition process.
What is an Electrolyte?
An electrolyte is a substance that contains mobile ions when molten or in an aqueous solution to conduct electricity. Examples of electrolytes include molten sodium chloride, copper(II) sulfate solution, and acids such as dilute hydrochloric acid.
The Role of Electrolyte in Electrodeposition
The concentration of metal ions in the electrolyte affects the thickness and quality of the deposited layer. The pH of the electrolyte affects the charge on the metal ions. The temperature affects the rate at which the metal ions move towards the conductive surface. Electrolytes are solutions that contain metal ions and are used to carry the electric current.
pH of Electrolyte
The pH of the electrolyte is an essential factor in determining the quality of the electrodeposited layer. The pH of the electrolyte affects the charge on the metal ions. If the pH of the electrolyte is too high or too low, it can cause the metal ions to either repel or attract the conductive surface, resulting in an uneven deposition layer.
Temperature of Electrolyte
The temperature of the electrolyte also plays a crucial role in the electrodeposition process. The temperature affects the rate at which the metal ions move towards the conductive surface. A higher temperature increases the rate of deposition, while a lower temperature slows down the deposition process.
Concentration of Electrolyte
The concentration of the electrolyte affects the thickness and quality of the deposited layer. If the concentration of the electrolyte is too low, the deposited layer may be thin and uneven. On the other hand, if the concentration is too high, it can result in a thicker layer that is not uniform.
In conclusion, understanding the role of electrolytes in electrodeposition is essential in optimizing the electrodeposition process and achieving the desired properties of the deposited layer. By controlling the properties of the electrolyte and the parameters of the electrodeposition process, it is possible to achieve highly uniform and precise coatings on a range of materials, making electrodeposition a versatile and widely used technique in a range of industries.
Anode and Cathode: Functions and Reactions
Electrodeposition is a process that involves depositing a thin layer of metal on a conductive surface. This process is carried out using electrochemical electrodes, namely the anode and cathode. The anode and cathode have specific functions and reactions that are crucial to the electrodeposition process.
Anode: Function and Reaction
The anode is the electrode where the oxidation reaction occurs during electrodeposition. During the process, the metal is oxidized at the anode, which results in the release of electrons. These electrons then flow through the external circuit to the cathode, where they are used to reduce the metal ions. The anode, therefore, serves as the source of electrons for the reduction reaction at the cathode.
Cathode: Function and Reaction
The cathode is the electrode where the reduction reaction occurs during electrodeposition. The metal ions are reduced at the cathode, resulting in the deposition of the metal on the surface. The cathode, therefore, serves as the site for the deposition of the metal being plated.
Anode and Cathode: Polarization
The anode and cathode can undergo polarization during the electrodeposition process, which affects the quality of the plated metal. Polarization occurs when the current density at the electrode surface is not uniform, leading to the formation of non-uniform deposits. This can be avoided by ensuring that the anode and cathode are of the correct size and shape to optimize the current distribution.
Anode and Cathode: Material Selection
The choice of material for the anode and cathode is also important in electrodeposition. The anode should be made of a material that is oxidizable and does not dissolve easily in the electrolyte. Common materials used for anodes include platinum, graphite, and lead dioxide. The cathode, on the other hand, should be made of a material that is reducible and can accommodate the deposition of the metal being plated. Common materials used for cathodes include copper, nickel, and zinc.
In conclusion, understanding the functions and reactions of the anode and cathode is essential for optimizing the electrodeposition process and producing high-quality metal coatings. The anode serves as the source of electrons for the reduction reaction at the cathode, while the cathode serves as the site for the deposition of the metal being plated. The selection of the correct materials and ensuring uniform current distribution can help avoid polarization and produce uniform deposits.
Electroplating and Electrowinning Applications
Electrodeposition is an essential process used in electroplating and electrowinning applications. Electroplating involves depositing a metal coating onto a surface to enhance its appearance, durability, or conductivity, while electrowinning involves extracting a metal from a solution using an electric current. Understanding the principles of electrodeposition is crucial to achieving the desired quality and efficiency in these applications.
Electrochemical Electrodes in Electrodeposition
Electrochemical electrodes, such as anodes and cathodes, play a critical role in the electrodeposition process. Anodes release metal ions into the solution, while cathodes attract these ions and deposit them onto the substrate. The choice of electrode material, current density, and electrolyte solution can all affect the quality and efficiency of electrodeposition.
Electroplating Applications
Electroplating is widely used in various industries, including automotive, electronics, and aerospace. It is also an important technique in research and development, allowing for the creation of new materials and improved manufacturing processes. Electroplating is used to deposit a thin layer of metal onto a surface to improve its appearance, durability, or conductivity. For example, chrome plating is used to enhance the appearance and durability of automotive parts, while electroless nickel plating is used to improve the corrosion resistance of electronic components.
Electrowinning Applications
Electrowinning is also widely used in various industries, including mining and metallurgy. It is used to extract metals from solutions containing metal ions. For example, electrowinning is used to extract copper from copper sulfate solutions or nickel from nickel chloride solutions. The choice of electrode material, current density, and electrolyte solution can all affect the quality and efficiency of electrowinning.
Conclusion
In conclusion, electrodeposition is a crucial process in various electroplating and electrowinning applications. Electrochemical electrodes and their choice of material, current density, and electrolyte solution are essential in achieving the desired quality and efficiency. Electroplating and electrowinning have a wide range of applications in various industries, and their use allows for the creation of new materials and improved manufacturing processes.
Conclusion on Electrodeposition and Electrochemical Electrodes
Electrodeposition is a versatile technique used in various applications, such as electrowinning, electroplating, and pH determination. Electrochemical electrodes play a crucial role in electrodeposition by providing a surface for the deposition of the desired material. The selection of an appropriate electrode relies on several factors, such as the chemical composition and the type of electrolyte used. The process of electrodeposition involves the deposition of a material on the surface of the working electrode, which can be an anode or a cathode. The product of electrolysis and electrodeposition can be used for various applications, such as in the production of batteries. Overall, electrodeposition and electrochemical electrodes are essential tools in the field of materials science and engineering, and their importance in various applications cannot be overlooked.
CONTACT US FOR A FREE CONSULTATION
KINTEK LAB SOLUTION's products and services have been recognized by customers around the world. Our staff will be happy to assist with any inquiry you might have. Contact us for a free consultation and talk to a product specialist to find the most suitable solution for your application needs!