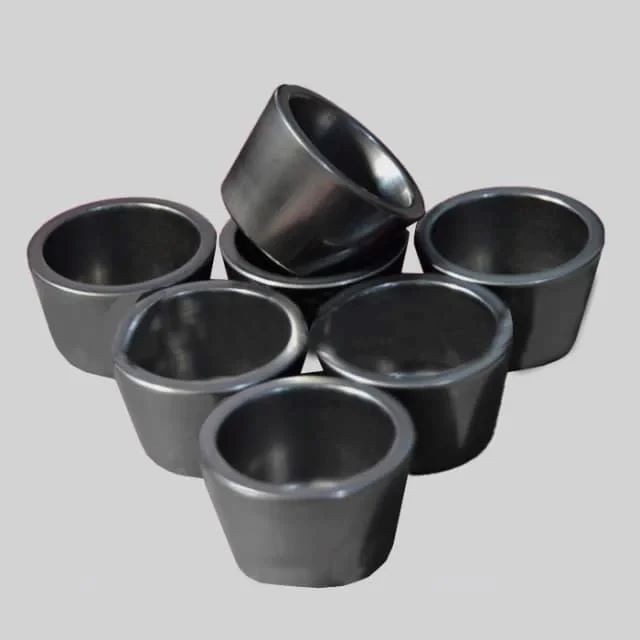
Thin Film Deposition Parts
High Purity Pure Graphite Crucible for Electron Beam Evaporation
Item Number : KMS02
Price varies based on specs and customizations
- Material
- Graphite
- Specification
- Ф35-65*17-30mm
- cover
- optional
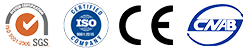
Shipping:
Contact us to get shipping details Enjoy On-time Dispatch Guarantee.
Why Choose Us
Reliable PartnerEasy ordering process, quality products, and dedicated support for your business success.
Applications
Electron beam evaporation graphite crucible is a technology that uses electron beams to create flexible and rough graphite films. Its key parameters include carbon source supply, electron beam irradiation energy, applied voltage, evaporation temperature, and evaporation time. The applied voltage modulates the adhesion between the graphite layer and the bottom layer of the crucible. To ensure a flat graphite layer, the flow rate and particle size of the carbon source feed should be controlled to achieve uniform deposition and evaporation.
In the field of power electronics, electron beam evaporation graphite crucible technology is widely used. It involves depositing a carbon source material using an electron beam to form a thin film of graphite. The graphite crucible manufactured by this process has low resistance, low corona and high yield strength. It is widely used in heat dissipation, withstand voltage manufacturing and testing of electronic equipment.
Detail & Parts
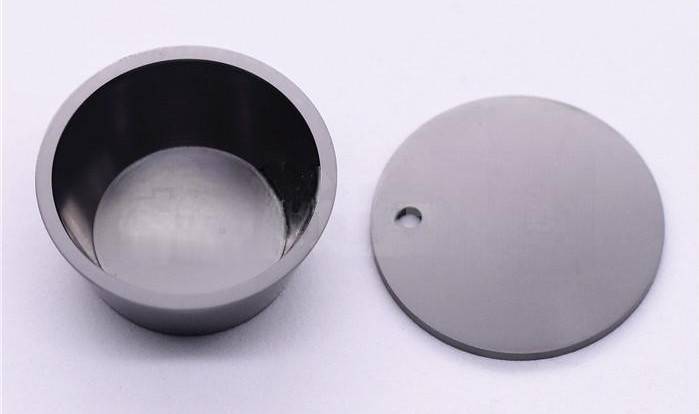
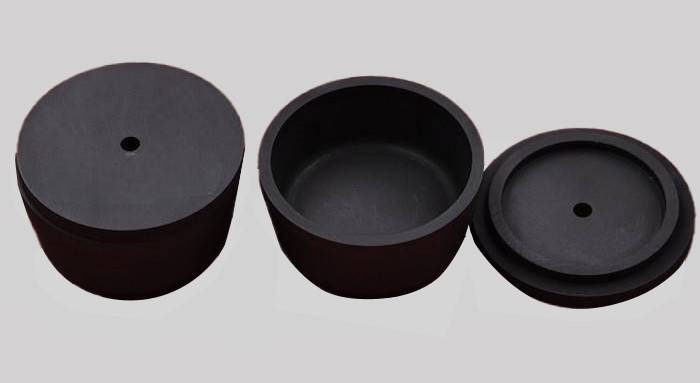
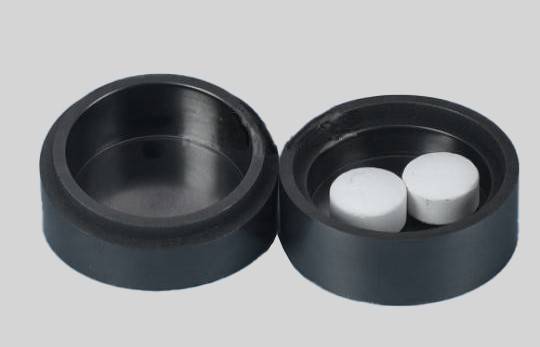
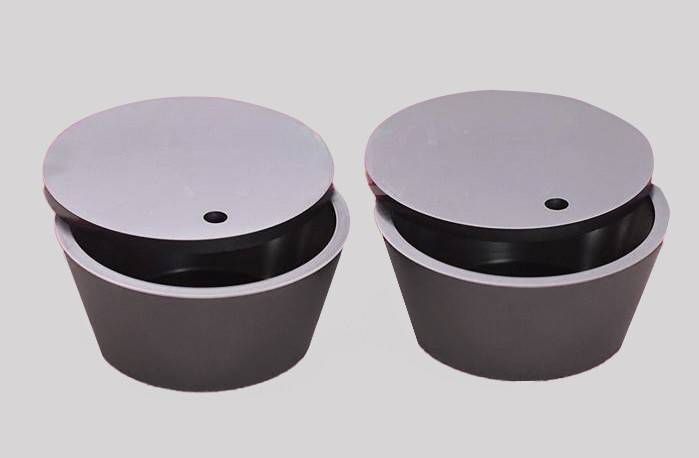
Technical specifications
Graphite Crucible Dimensions | 35*17mm | 35*22mm | 40*20mm | 42.5*19.5mm | 45*22.5mm | 50*25mm | 65*30mm |
The crucibles we show are available in different sizes and custom sizes are available on request.
Advantage
- Preparation accuracy: Electron beam evaporation technology can precisely control the deposition process, resulting in high-precision and consistent graphite crucibles.
- Thermal shock resistance: Graphite films formed by electron beam evaporation have excellent thermal shock resistance and are suitable for applications with rapid temperature changes.
- Wear resistance: Electron beam evaporated graphite crucible has good wear resistance, making it durable and able to withstand harsh conditions.
- Chemical Resistance: These crucibles are resistant to acids, alkalis and chemical contamination, ensuring their reliability and longevity in chemically aggressive environments.
- Flexibility and roughness: The graphite film formed by this technique has a certain degree of flexibility and roughness, making it effective for various applications.
In conclusion, e-beam evaporated graphite crucibles have precise preparation, thermal shock resistance, abrasion resistance, chemical resistance, flexibility and roughness. They are widely used in power electronics, molecular binding testing, laser technology, batteries, high voltage capacitors and medical device applications.
FAQ
What Are Thermal Evaporation Sources?
Comparison Of Electron Beam Evaporation Graphite Crucible Technology And Traditional Technology.
How Are High-purity Graphite Crucibles Made?
What Are The Main Types Of Thermal Evaporation Sources?
What Are The Common Applications Of High-purity Graphite Crucibles?
How Do Thermal Evaporation Sources Work?
What Are The Common Materials Used For Evaporating Crucibles?
What Factors Should Be Considered When Selecting High-purity Graphite Crucibles?
What Are The Advantages Of Using Thermal Evaporation Sources?
What Are The Advantages Of Using Evaporating Crucibles?
What Applications Are Thermal Evaporation Sources Used For?
How Should Evaporating Crucibles Be Handled And Maintained?
4.8
out of
5
Speedy shipping and well-packaged. The crucible is of remarkable quality.
4.7
out of
5
Excellent value for the price. Highly recommend this crucible for lab use.
4.9
out of
5
Impeccable quality and construction. Meets all our lab requirements.
4.6
out of
5
Durable and long-lasting. Withstands high temperatures and rigorous use.
4.8
out of
5
Cutting-edge technology. The crucible's performance is outstanding.
4.7
out of
5
Highly recommend. The crucible's features are impressive.
4.9
out of
5
Meticulously crafted. The crucible is a testament to precision engineering.
4.6
out of
5
Sturdy and resilient. Withstands demanding lab conditions effortlessly.
4.8
out of
5
State-of-the-art technology. The crucible's capabilities are remarkable.
4.7
out of
5
Great value for money. The crucible's performance exceeds expectations.
4.9
out of
5
Unparalleled quality. The crucible is a game-changer in our lab.
4.6
out of
5
Durable and reliable. The crucible withstands rigorous use remarkably.
4.8
out of
5
Cutting-edge technology. The crucible's capabilities are astounding.
4.7
out of
5
Excellent value for the price. The crucible's performance is impressive.
4.9
out of
5
Meticulously crafted. The crucible's precision is remarkable.
4.6
out of
5
Sturdy and resilient. Withstands demanding lab conditions effortlessly.
4.8
out of
5
State-of-the-art technology. The crucible's capabilities are remarkable.
4.7
out of
5
Great value for money. The crucible's performance exceeds expectations.
Products
High Purity Pure Graphite Crucible for Electron Beam Evaporation
REQUEST A QUOTE
Our professional team will reply to you within one business day. Please feel free to contact us!
Related Products
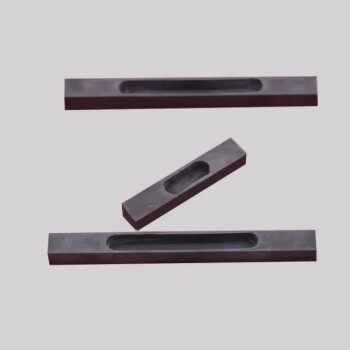
High Purity Pure Graphite Crucible for Evaporation
Vessels for high temperature applications, where materials are kept at extremely high temperatures to evaporate, allowing thin films to be deposited on substrates.
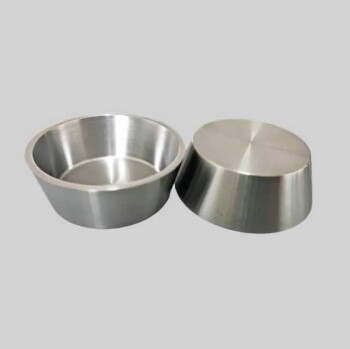
E Beam Crucibles Electron Gun Beam Crucible for Evaporation
In the context of electron gun beam evaporation, a crucible is a container or source holder used to contain and evaporate the material to be deposited onto a substrate.
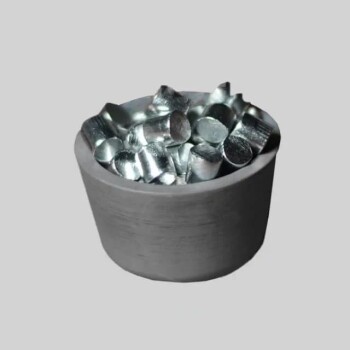
Electron Beam Evaporation Coating Conductive Boron Nitride Crucible BN Crucible
High-purity and smooth conductive boron nitride crucible for electron beam evaporation coating, with high temperature and thermal cycling performance.
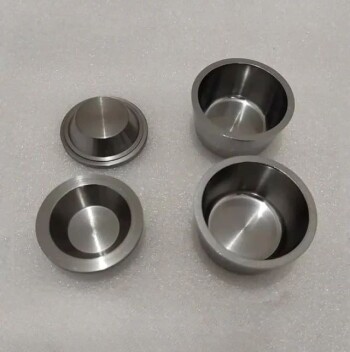
Tungsten and molybdenum crucibles are commonly used in electron beam evaporation processes due to their excellent thermal and mechanical properties.
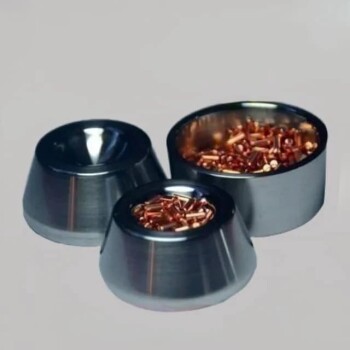
Electron Beam Evaporation Coating Gold Plating Tungsten Molybdenum Crucible for Evaporation
These crucibles act as containers for the gold material evaporated by the electron evaporation beam while precisely directing the electron beam for precise deposition.
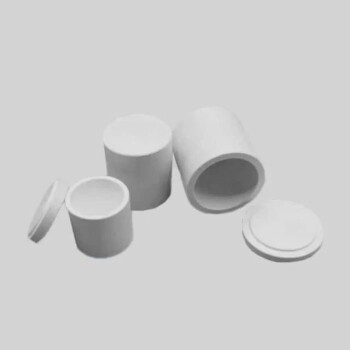
Evaporation Crucible for Organic Matter
An evaporation crucible for organic matter, referred to as an evaporation crucible, is a container for evaporating organic solvents in a laboratory environment.
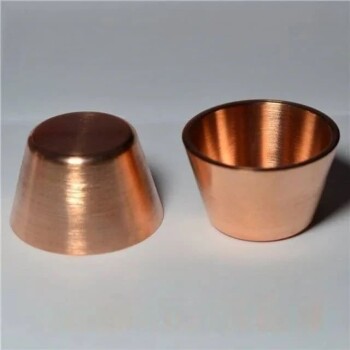
Electron Beam Evaporation Coating Oxygen-Free Copper Crucible and Evaporation Boat
Electron Beam Evaporation Coating Oxygen-Free Copper Crucible enables precise co-deposition of various materials. Its controlled temperature and water-cooled design ensure pure and efficient thin film deposition.
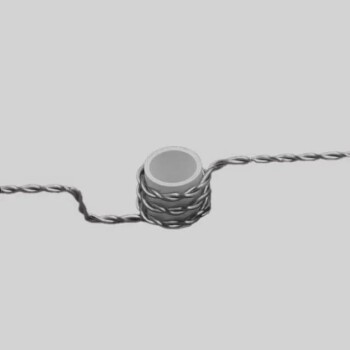
Ceramic Evaporation Boat Set Alumina Crucible for Laboratory Use
It can be used for vapor deposition of various metals and alloys. Most metals can be evaporated completely without loss. Evaporation baskets are reusable.1
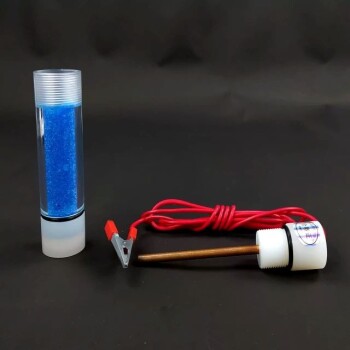
Copper Sulfate Reference Electrode for Laboratory Use
Looking for a Copper Sulfate Reference Electrode? Our complete models are made of high-quality materials, ensuring durability and safety. Customization options available.
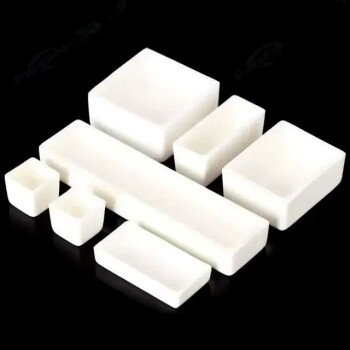
Engineering Advanced Fine Alumina Al2O3 Ceramic Crucible for Laboratory Muffle Furnace
Alumina ceramic crucibles are used in some materials and metal melting tools, and flat-bottomed crucibles are suitable for melting and processing larger batches of materials with better stability and uniformity.
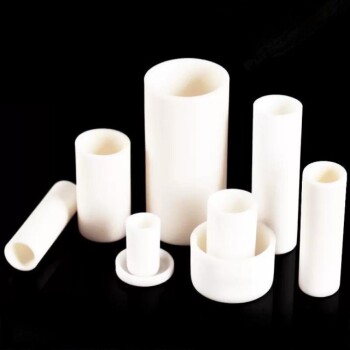
Engineering Advanced Fine Ceramics Alumina Al2O3 Crucible With Lid Cylindrical Laboratory Crucible
Cylindrical Crucibles Cylindrical crucibles are one of the most common crucible shapes, suitable for melting and processing a wide variety of materials, and are easy to handle and clean.
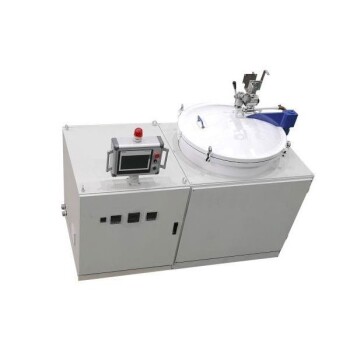
Graphite Vacuum Furnace IGBT Experimental Graphitization Furnace
IGBT experimental graphitization furnace, a tailored solution for universities and research institutions, with high heating efficiency, user-friendliness, and precise temperature control.
Related Articles
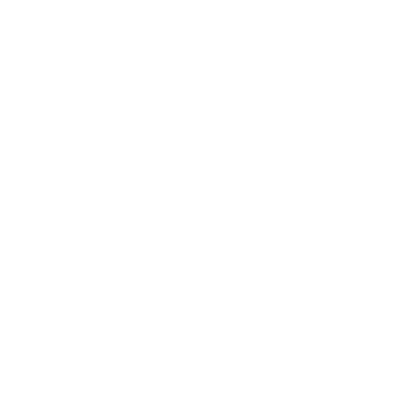
A Comparative Study of Evaporation and Sputtering Techniques in Thin Film Deposition
The two most common techniques used for thin film deposition are evaporation and sputtering.
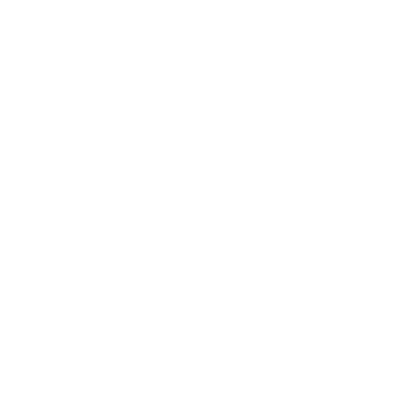
The Future of Electrochemical Electrodes
The latest trends and developments in electrode materials and their implications for the future of electrochemistry.
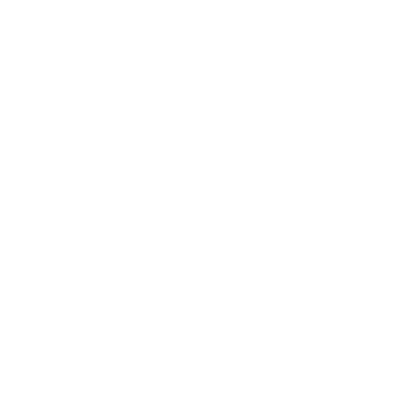
Understanding Electrodeposition with Electrochemical Electrodes
Electrodeposition is a process of depositing a metal or a non-metallic material onto a surface by applying an electric current.
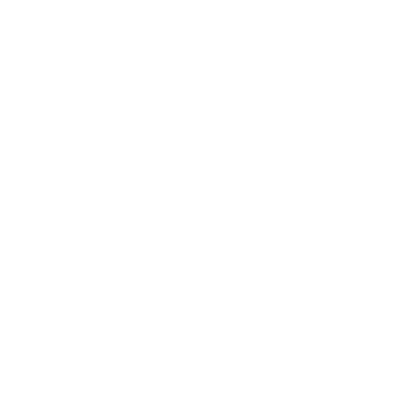
Chemical Vapor Deposition (CVD) of Graphene Challenges and Solutions
Chemical Vapor Deposition (CVD) is a widely adopted method for the production of high-quality graphene.
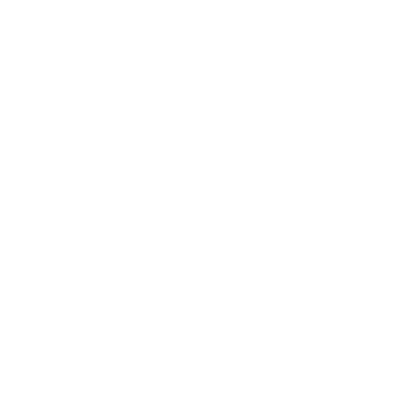
Understanding Saturated Calomel Reference Electrodes: Composition, Uses, and Considerations
Explore the detailed guide on saturated calomel reference electrodes, including their composition, advantages, disadvantages, and applications. Ideal for researchers and lab technicians.
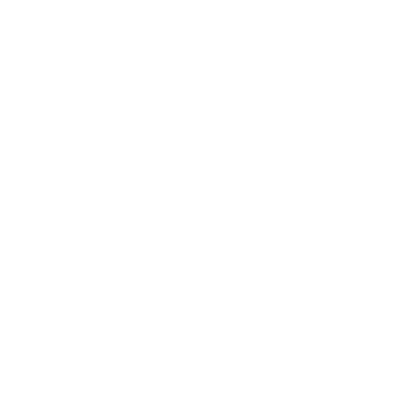
6 Ways To activated carbon regeneration
Activated Carbon Regeneration: Thermal Regeneration Method, Biological Regeneration Method, Wet Oxidation Regeneration Method, Solvent Regeneration Method, Electrochemical Regeneration Method, Catalytic Wet Oxidation Method
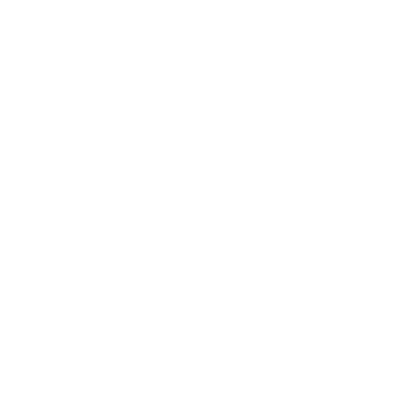
Electrochemical Cells: Generating Electricity and Driving Reactions
Electrochemical cells, like batteries, play a vital role in energy storage by converting chemical energy to electrical energy and vice versa. Explore the workings, types, and significance of these cells.
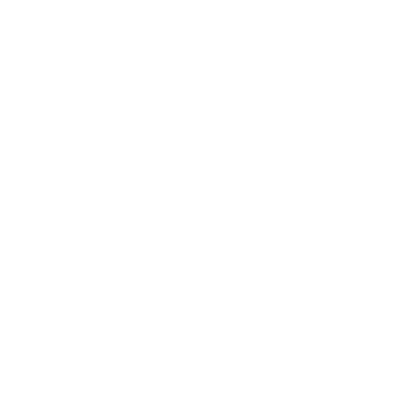
Electron Beam Evaporation Technology in Vacuum Coating
An in-depth look at electron beam evaporation, its types, advantages, and disadvantages in vacuum coating processes.
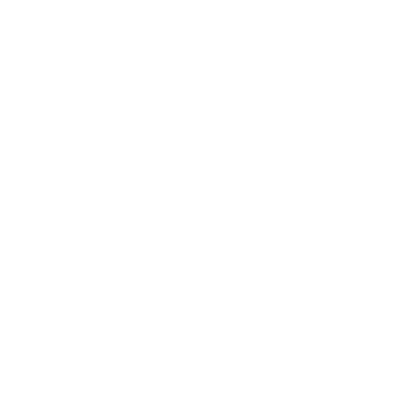
The Role of Plasma in PECVD Coatings
PECVD (Plasma Enhanced Chemical Vapor Deposition) is a type of thin film deposition process that is widely used for creating coatings on various substrates. In this process, a plasma is used to deposit thin films of various materials onto a substrate.
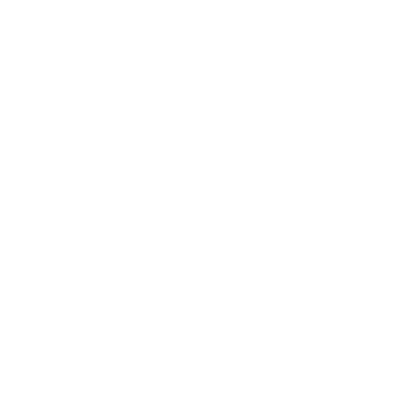
The Importance of Activated Carbon Regeneration in Water Treatment
In water treatment, activated carbon is often used as a means of removing unwanted contaminants, such as chlorine, chloramines, and organic matter, from drinking water and wastewater.
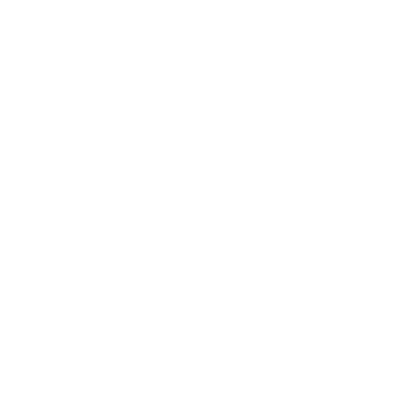
Electron Beam Evaporation Coating Technology and Material Selection
An in-depth look at the principles and applications of electron beam evaporation coating technology, including material selection and various fields of application.
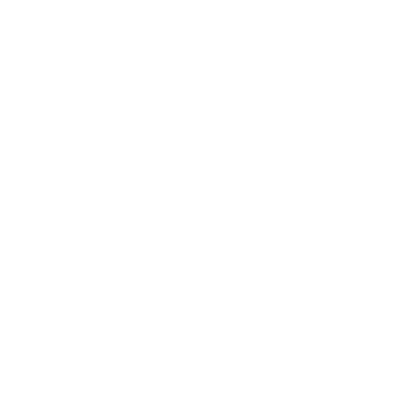
Electron Beam Evaporation Coating: Principles, Characteristics, and Applications
An in-depth analysis of electron beam evaporation coating technology, its advantages, disadvantages, and applications in thin film manufacturing.