Introduction to PECVD Coatings
PECVD (Plasma Enhanced Chemical Vapor Deposition) is a type of thin film deposition process that is widely used for creating coatings on various substrates. In this process, a plasma is used to deposit thin films of various materials onto a substrate. PECVD is a variation of the CVD (Chemical Vapor Deposition) process that uses plasma to enhance the chemical reactions that take place during the deposition process. PECVD coatings offer several advantages over traditional CVD coatings, including better control over film properties, higher deposition rates, and the ability to deposit a wider range of materials. PECVD coatings are used in a variety of applications, including semiconductors, solar cells, and optical coatings.
Table of Contents
Advantages of PECVD over CVD
PECVD (Plasma-Enhanced Chemical Vapor Deposition) has become more popular than CVD (Chemical Vapor Deposition) in the field of thin film deposition due to its numerous advantages. In this section, we will discuss these advantages in detail.
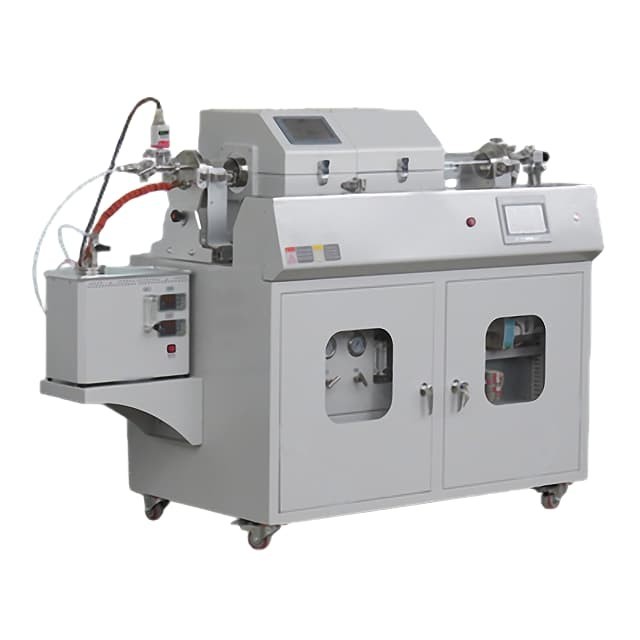
Lower Deposition Temperatures
One of the main advantages of PECVD over CVD is that it can be performed at lower temperatures, making it more suitable for temperature-sensitive materials. PECVD temperatures range from room temperature to 350°C, while standard CVD temperatures are usually conducted in 600°C to 800°C. This feature enables successful applications in situations where the higher CVD temperatures could potentially damage the device or substrate being coated.
Better Coverage and Uniformity
Because CVD is a diffusive gas-driven process, it allows for better coverage on uneven surfaces such as trenches or walls with relatively high conformity. Alternatively, PVD (Physical Vapor Deposition) coatings are a line-of-sight deposition and, therefore, can result in more variance in thin film depth if irregularities shield areas from coating. To a great extent, PECVD reduces the line-of-site issue for high conformity of thin films because the plasma stream can surround the substrate.
PECVD also allows for a greater degree of control over the deposition process, resulting in more uniform and precise coatings. By varying the parameters of the plasma, excellent control of the material properties can be achieved, including density and hardness, purity, roughness, or the refractive index of optical films. PECVD yields some of the fastest deposition rates while still maintaining high film quality.
Unique Coatings with Special Characteristics
The use of plasma in PECVD also allows for the creation of coatings with unique properties, such as increased hardness, adhesion, and resistance to corrosion. PECVD can produce unique compounds and films that cannot be created by common CVD techniques alone and can produce films that demonstrate a very high solvent and corrosion resistance with chemical and thermal stability.
Versatile Applications
In addition to its advantages over CVD, PECVD has numerous applications in a variety of industries, including electronics, optics, and biomedicine. PECVD is widely used in the semiconductor industry to fabricate integrated circuits and is a key deposition technique used in the manufacture of solar cells and photovoltaics. Its versatility allows it to be applied evenly on relatively wide surface areas like solar panels or optical glass, where the refractive quality of the optical coatings can be very finely tuned by altering the plasma for an extremely high degree of process control.
How Plasma Treatments Change Surface Properties
Plasma treatments are widely used to modify the surface properties of various substrates. These treatments involve the use of a plasma generated by applying an electric field to a gas mixture in a vacuum chamber. The plasma plays a crucial role in altering the surface properties of the substrate, making it more suitable for the deposition of thin coatings. In this section, we will discuss how plasma treatments change the surface properties of substrates in the context of PECVD coatings.
Surface Energy Modification
Plasma treatments can modify the surface energy of the substrate, which is an important factor in determining the adhesion between the substrate and the coating. The plasma can increase or decrease the surface energy of the substrate depending on the type of gas used and the plasma parameters. A high surface energy promotes wetting, which results in better adhesion between the substrate and the coating.
Surface Roughness Enhancement
Plasma treatments can also increase the surface roughness of the substrate. This can be beneficial for certain applications, such as enhancing the performance of solar cells. The increased surface roughness can also improve the adhesion between the substrate and the coating. The plasma can etch the surface of the substrate, creating microstructures that increase surface area and promote better adhesion.
Chemical Composition Modification
Plasma treatments can modify the chemical composition of the substrate surface, leading to changes in the chemical and physical properties of the coating. The plasma can introduce functional groups onto the surface of the substrate, which can be used to control the wettability of the coating. For example, plasma treatments with oxygen gas can introduce hydroxyl groups onto the surface of the substrate, which can make it more hydrophilic.
Dangling Bond Creation
Plasma treatments can also create dangling bonds on the surface of the substrate. These are unpaired electrons that are chemically reactive and can bond with other atoms or molecules. Dangling bonds can be useful for promoting adhesion between the substrate and the coating, as they can react with the coating material to form strong chemical bonds.
In conclusion, plasma treatments are effective in changing the surface properties of substrates, making them more suitable for the deposition of thin coatings. By modifying the surface energy, surface roughness, chemical composition, and introducing dangling bonds, plasma treatments can promote better adhesion and improve the overall quality of PECVD coatings.
Types of coatings produced by PECVD
Plasma-Enhanced Chemical Vapor Deposition (PECVD) is a process that can produce various types of coatings on different surfaces. The coating types that can be produced using PECVD are:
1. Silicon Dioxide Coatings
Silicon dioxide (SiO2) coatings produced by PECVD are widely used in the microelectronics industry as a dielectric material. SiO2 coatings have excellent electrical insulation properties and can withstand high temperatures without degrading. PECVD produces dense, uniform and conformal SiO2 coatings with good adhesion to the substrate.
2. Silicon Nitride Coatings
Silicon nitride (Si3N4) coatings produced by PECVD are also widely used in the microelectronics industry as a dielectric material and a passivation layer. Si3N4 coatings have good mechanical, chemical and thermal stability, making them ideal for harsh environments. PECVD produces Si3N4 coatings with good uniformity, low stress, and high density.
3. Amorphous Carbon Coatings
Amorphous carbon (a-C) coatings produced by PECVD have a wide range of applications. They are used as a protective coating for cutting tools, optical elements, and various mechanical components. a-C coatings have excellent wear resistance, chemical inertness, and low friction coefficient. PECVD produces a-C coatings with good adhesion, high density, and low roughness.
4. DLC Coatings
Diamond-like carbon (DLC) coatings produced by PECVD have unique properties such as high hardness, low friction, and high wear resistance. DLC coatings are used in various applications such as automotive, aerospace, and biomedical industries. PECVD produces DLC coatings with good adhesion, high density, and low hydrogen content.
In conclusion, PECVD is a versatile process that can produce various types of coatings with different properties. The choice of coating type depends on the specific application requirements. Understanding the properties and characteristics of each type of coating is essential for selecting the appropriate coating for a particular application.
How PECVD Creates Coatings
PECVD is a versatile coating technique that can deposit thin films of materials on various substrates through the use of low-pressure plasma. The plasma is a critical component in this process, as it can provide the necessary energy to activate the precursor gases and promote the chemical reactions that form the coating. In this section, we will discuss how PECVD creates coatings step by step.
Step 1: Plasma Generation
The first step in the PECVD process is plasma generation. Plasma is generated by applying a high-frequency electric field to a gas mixture, which dissociates the gas molecules and creates a reactive plasma.
Step 2: Introduction of Precursor Gases
Once the plasma is generated, precursor gases are introduced into the chamber. These gases are typically organic or inorganic compounds that will react with the plasma to form the coating.
Step 3: Activation of Precursor Gases
The reactive species present in the plasma then react with precursor gases to form a thin film on the substrate surface. Plasma provides the necessary energy to activate the precursor gases and promote the chemical reactions that form the coating.
Step 4: Thin Film Deposition
As the precursor gases are activated by the plasma, they begin to deposit on the substrate surface, forming a thin film. The plasma provides the energy necessary to promote the chemical reactions that lead to the deposition of the thin film on the substrate.
Step 5: Control of Film Properties
PECVD coatings can be tailored to meet specific requirements, such as optical and electrical properties. By controlling the deposition parameters, such as the gas flow rate, plasma power, and chamber pressure, the film properties can be optimized to meet the desired specifications.
In summary, PECVD creates coatings through the use of low-pressure plasma. The plasma dissociates the precursor gases, creating reactive species that react with the precursor gases to form a thin film on the substrate surface. The plasma provides the necessary energy to activate the precursor gases and promote the chemical reactions that form the coating. The deposition parameters can be optimized to tailor the film properties to meet specific requirements.
Conclusion: The Wide Applications of PECVD
The Plasma-Enhanced Chemical Vapor Deposition (PECVD) technique has a wide range of applications in various industries, including the semiconductor industry, biomedical engineering, and solar cell manufacturing. PECVD coatings offer superior adhesion, uniformity, and high-quality deposition. These coatings are used in various applications, including optical coatings, semiconductor coatings, anti-corrosion coatings, and barrier coatings. PECVD technology is used to produce various types of coatings, including diamond-like carbon, amorphous silicon, and silicon nitride. With its numerous advantages over conventional CVD techniques, PECVD continues to grow in popularity and is poised to play a significant role in various industries in the future.
CONTACT US FOR A FREE CONSULTATION
KINTEK LAB SOLUTION's products and services have been recognized by customers around the world. Our staff will be happy to assist with any inquiry you might have. Contact us for a free consultation and talk to a product specialist to find the most suitable solution for your application needs!