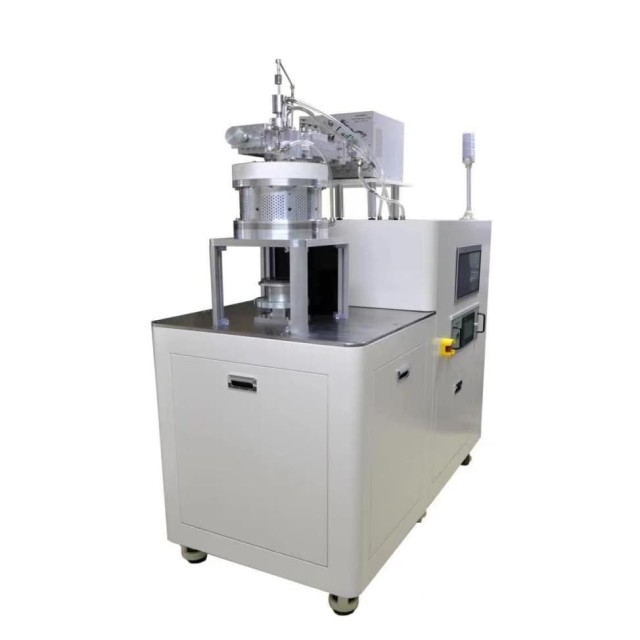
MPCVD
Microwave Plasma Chemical Vapor Deposition MPCVD Machine System Reactor for Lab and Diamond Growth
Item Number : KTMP315
Price varies based on specs and customizations
- Microwave Power
- Microwave frequency 2450±15MHZ
- Output power
- 1~10 KW continuously adjustable
- Microwave leakage
- ≤2MW/cm2
- Output wave guide interface
- WR340, 430 with FD-340, 430 standard flange
- Sample holder
- Diameter of sample table≥70mm, effective use area≥64 mm
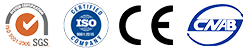
Shipping:
Contact us to get shipping details Enjoy On-time Dispatch Guarantee.
Why Choose Us
Reliable PartnerEasy ordering process, quality products, and dedicated support for your business success.
MPCVD means Microwave Plasma Chemical Vapor Deposition. It grows quality diamond films in labs using carbon gas and microwave plasma.
MPCVD System
MPCVD is a system for depositing thin films onto a substrate using a vacuum chamber, microwave generator, and gas delivery system. A plasma is generated inside the chamber by a magnetron or klystron generating microwaves at 2.45 GHz. The gas delivery system has MFCs calibrated in sccm to control gas flow. The substrate temperature is controlled by the plasma and measured by a thermocouple. The plasma heats the substrate and the temperature is monitored during deposition.
Applications
MPCVD shows promise for producing large, high-quality diamonds at a low cost.
Diamond's unique properties, such as hardness, stiffness, high thermal conductivity, low thermal expansion, radiation-hardness, and chemical inertness, make it a valuable material. However, the high cost, limited size, and difficulty controlling impurities of natural and synthetic high-pressure, high-temperature diamonds have limited their applications.
MPCVD is the primary equipment for growing diamond gemstones and films, which can be either monocrystal or poly-crystalline. The semi-conductor industry uses diamond film growth extensively for large-size diamond substrates, as well as the diamond cutting or drilling tools industry.
Compared to the HPHT method for lab-grown diamonds, the microwave CVD method is advantageous for large-sized diamond growth at a lower cost, making it an ideal solution for semi-conductor diamonds, optics diamond growth, and the large jewelry diamond market.
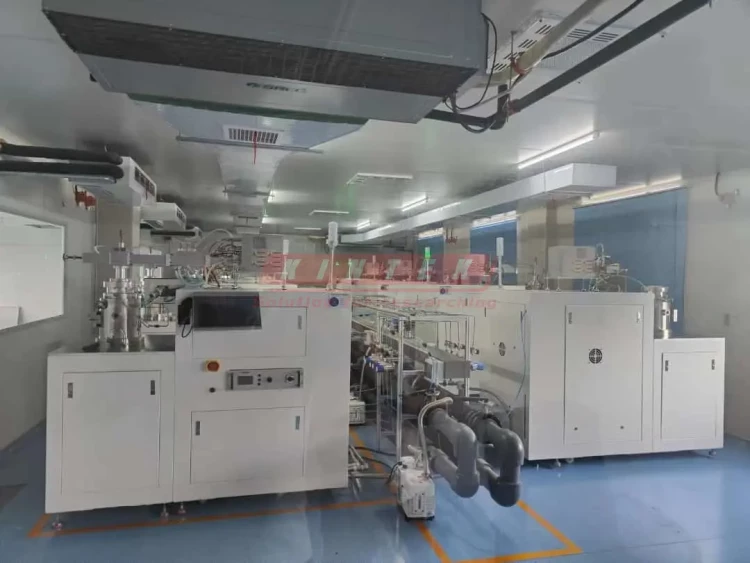
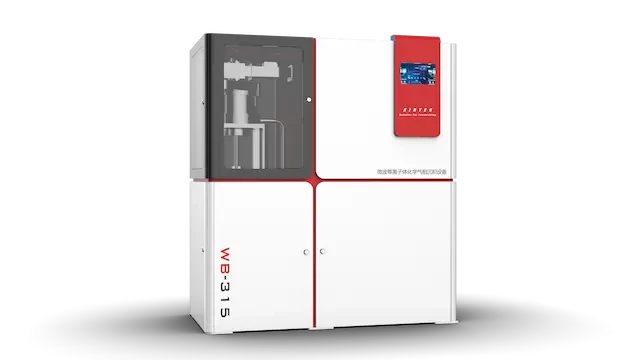
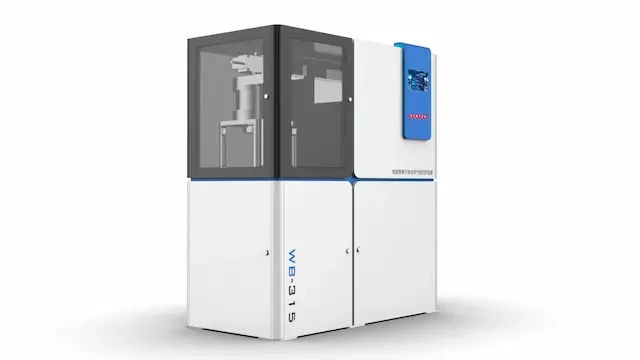
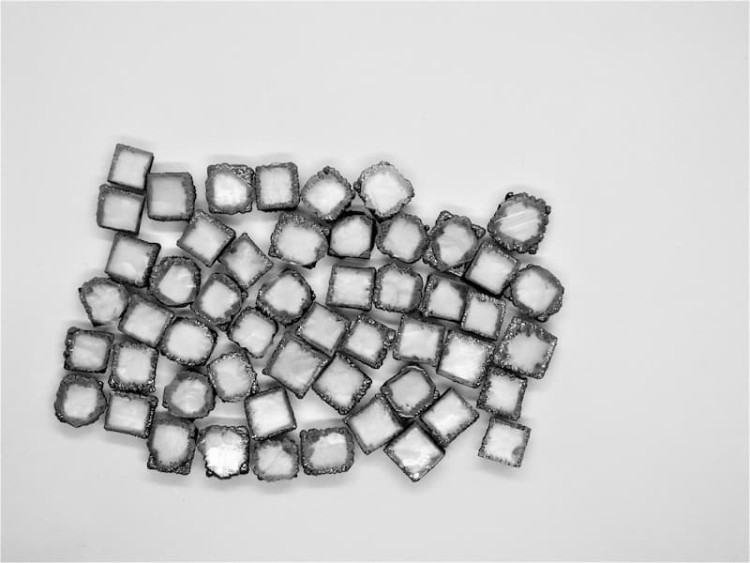
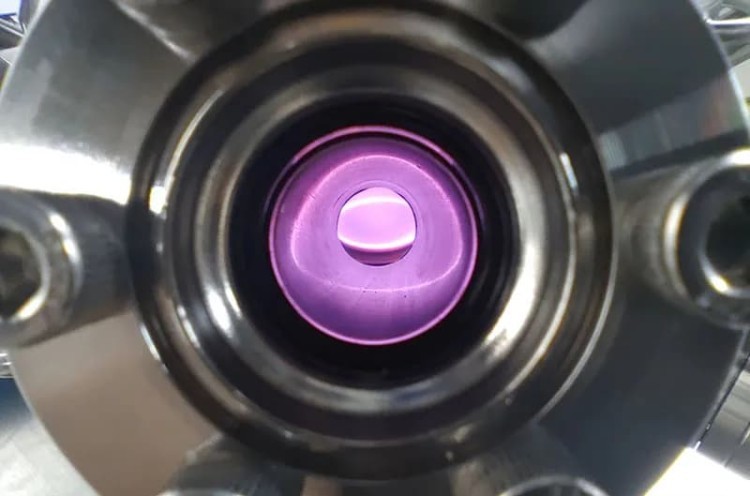
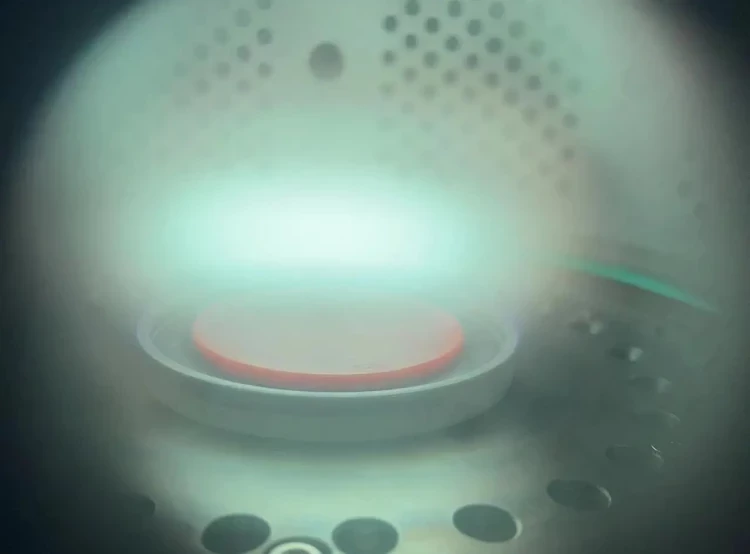
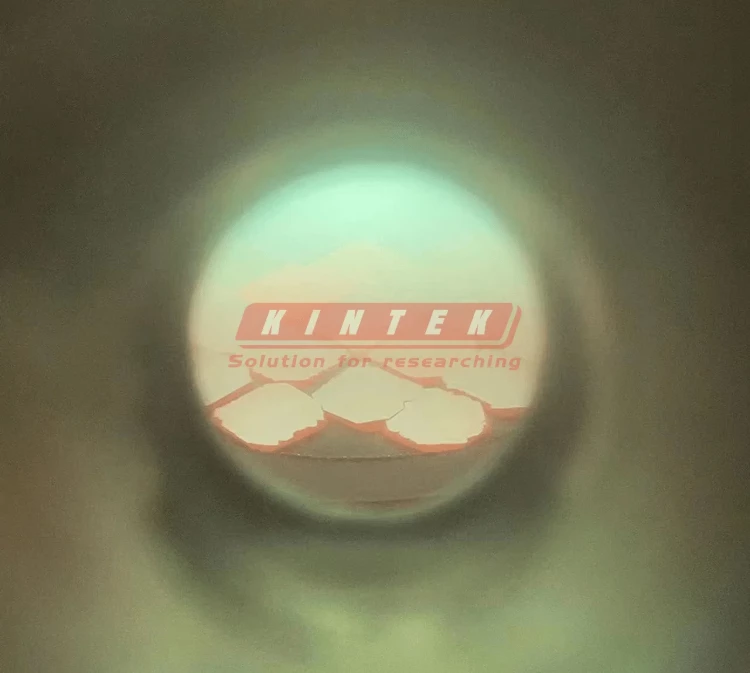
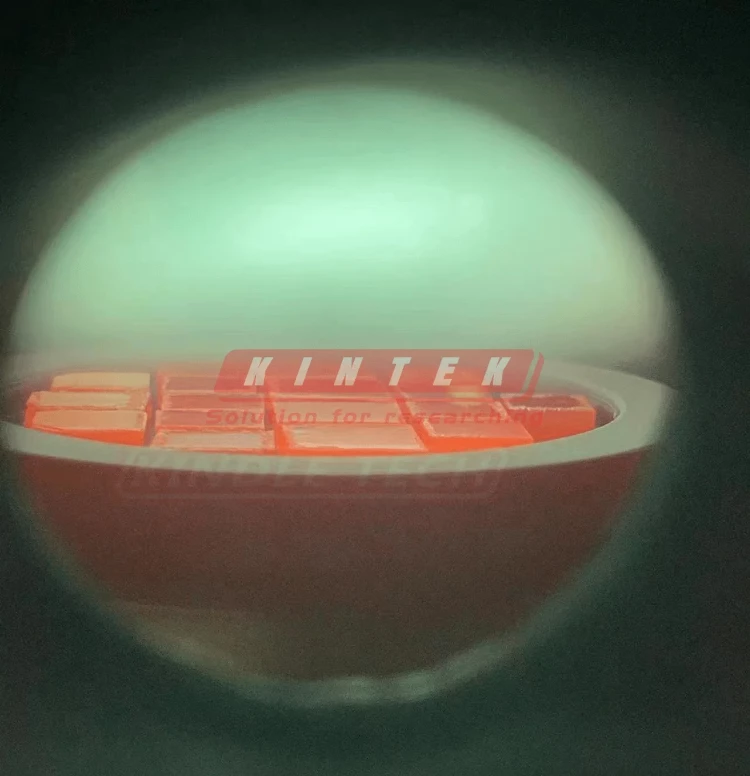
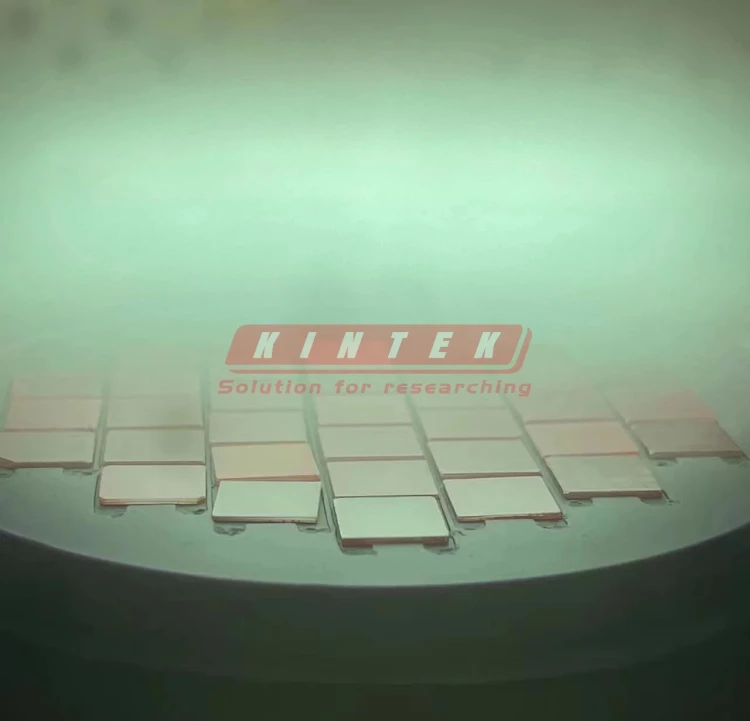
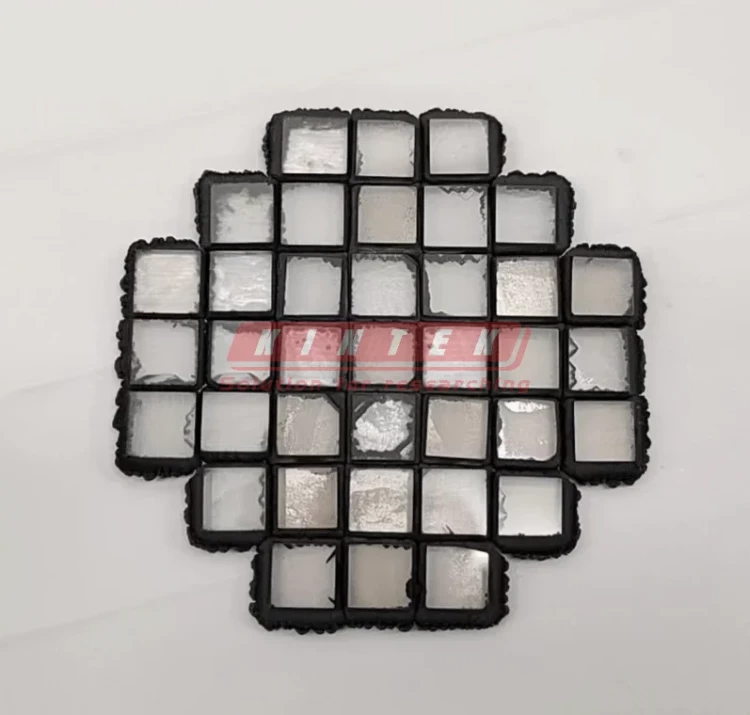
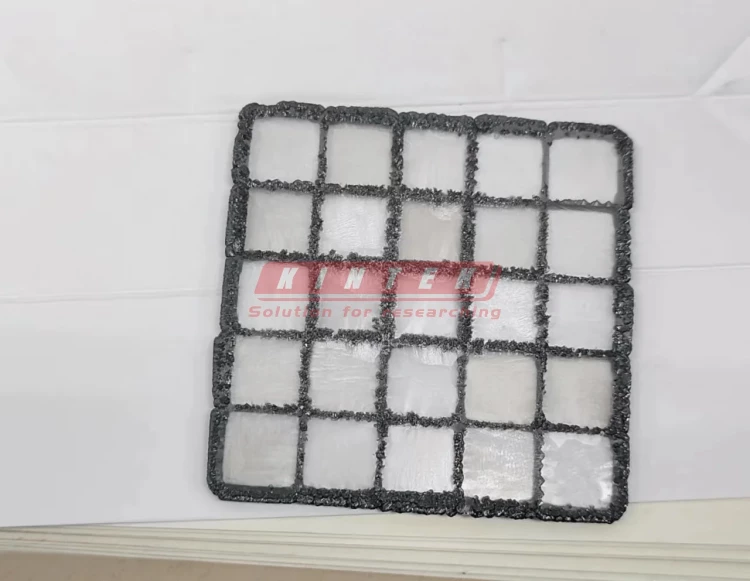
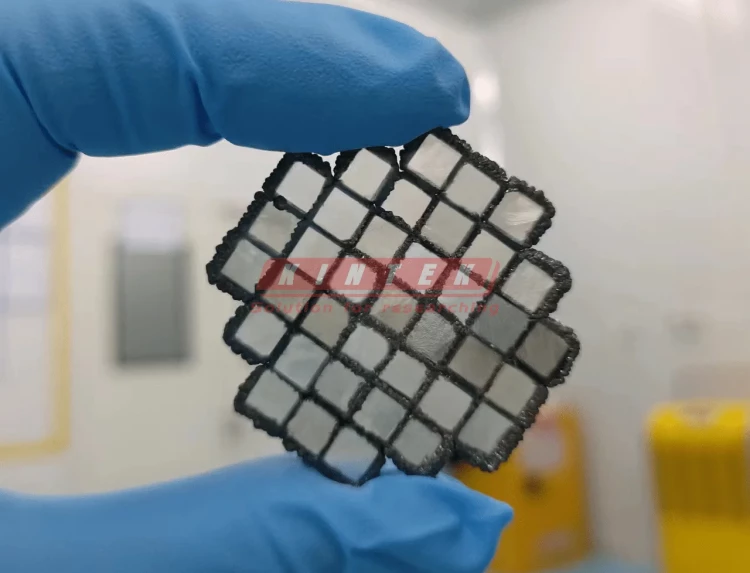
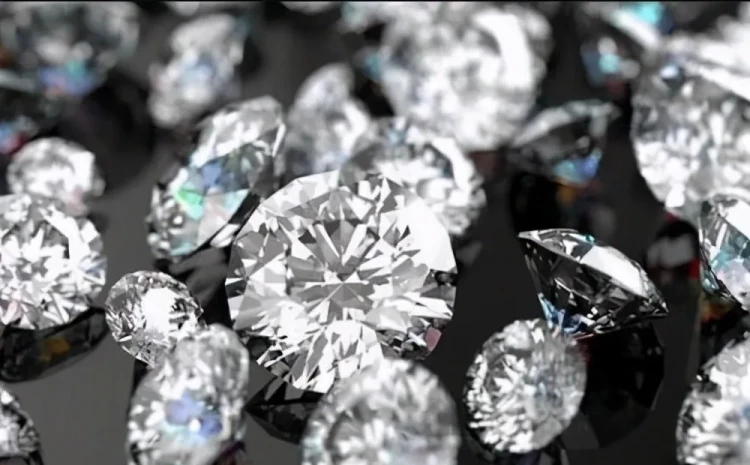
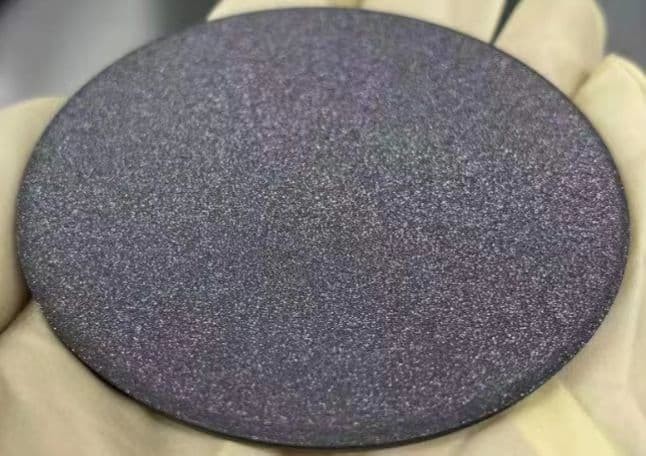
Advantages of MPCVD
MPCVD is a diamond synthesis method with advantages over HFCVD and DC-PJ CVD. It avoids contamination and allows for multiple gases. It offers smooth microwave power adjustment and stable temperature control, avoiding seed crystal loss. MPCVD is promising for industrial applications due to a large, stable plasma area.
MPCVD produces purer diamonds using less energy than HPHT. It also enables production of larger diamonds.
Advantages of Our MPCVD System
We have been deeply involved in the industry for many years, and as a result, we have a vast customer base who trust and use our equipment. Our MPCVD equipment has been running steadily for over 40,000 hours, demonstrating exceptional stability, reliability, repeatability, and cost-effectiveness. More advantages of our MPCVD system include:
- 3 inches substrate growing area, max. batch load up to 45 pieces diamonds
- 1-10Kw adjustable output microwave power for less electricity consumption
- Rich experienced researching team with frontier diamond growing recipe support
- Exclusive technical support program for Zero diamond growing experience team
By leveraging our accumulated advanced technology, we have implemented multiple rounds of upgrades and improvements to our MPCVD system, resulting in significantly improved efficiency and reduced equipment costs. As a result, our MPCVD equipment is at the forefront of technological advancements and offered at a competitive price. Welcome to consult with us.
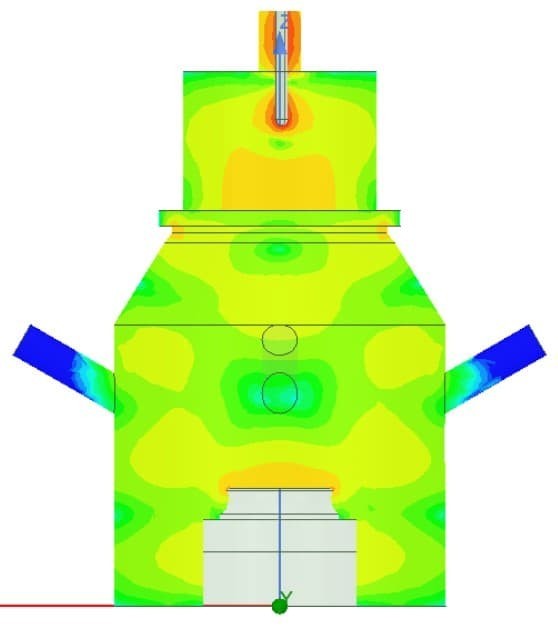
Working Processing
The MPCVD machine controls the flow of each gas path and cavity pressure while introducing reactant gases (such as CH4, H2, Ar, O2, N2, etc.) into the cavity under specific pressure. After stabilizing the airflow, the 6KW solid-state microwave generator generates microwaves that are then introduced into the cavity through the waveguide.
The reaction gas transforms into a plasma state under the microwave field, forming a plasma ball that hovers above the diamond substrate. The high temperature of the plasma heats the substrate to a specific temperature. Excess heat produced in the cavity is dissipated by the water cooling unit.
To ensure optimal growth conditions during the MPCVD single crystal diamond growth process, we adjust factors such as power, gas source composition, and cavity pressure. Furthermore, since the plasma ball doesn't contact the cavity wall, the diamond growth process is free from impurities, thereby enhancing the diamond's quality.
Detail & Parts
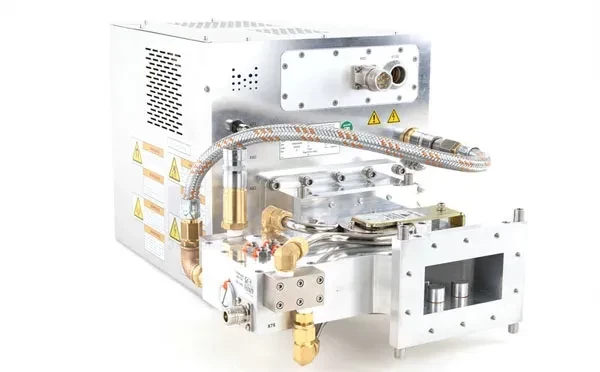
Microwave system
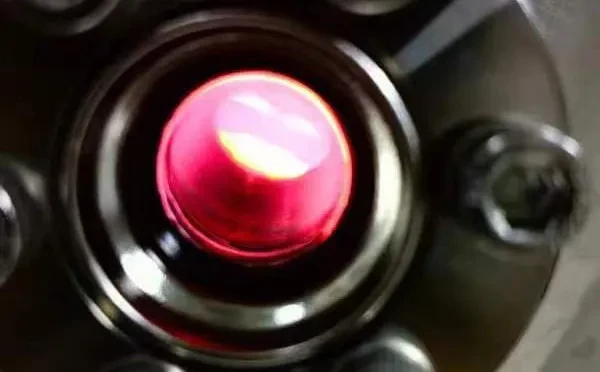
Reaction chamber
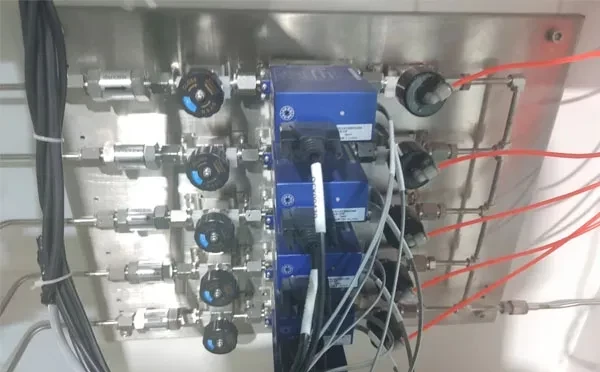
Gas flow system
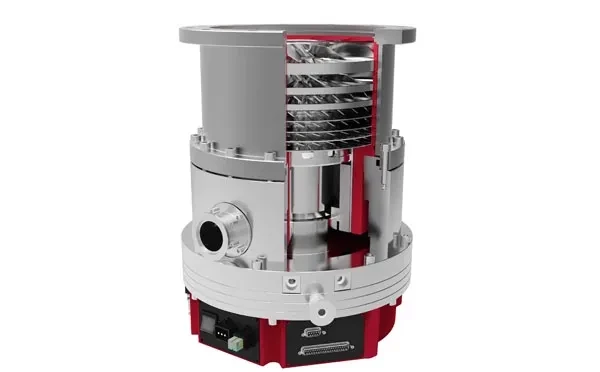
Vacuum and sensor system
Technical specifications
Microwave system |
|
Reaction chamber |
|
Sample holder |
|
Gas flow system |
|
Cooling system |
|
Temperature sensor |
|
Control system |
|
Optional function |
|
Warnings
Operator safety is the top important issue! Please operate the equipment with cautions. Working with inflammable& explosive or toxic gases is very dangerous, operators must take all necessary precautions before starting the equipment. Working with positive pressure inside the reactors or chambers is dangerous, operator must fellow the safety procedures strictly. Extra caution must also be taken when operating with air-reactive materials, especially under vacuum. A leak can draw air into the apparatus and cause a violent reaction to occur.
Designed for You
KinTek provide deep custom made service and equipment to worldwide customers, our specialized teamwork and rich experienced engineers are capable to undertake the custom tailoring hardware and software equipment requirements, and help our customer to build up the exclusive and personalized equipment and solution!
Would you please drop your ideas to us, our engineers are ready for you now!
FAQ
What Is CVD Diamond Machine?
What Types Of Diamond Growth Machines Are Available?
What Is The Basic Principle Of CVD?
How Does A CVD Diamond Machine Work?
What Are The Advantages Of Lab Grown Diamonds?
What Are The Different Types Of CVD Method?
What Are The Advantages Of Using CVD Diamond Machines?
What Is The Price Of CVD Growing Machine?
What Are The Advantages Of Using Chemical Vapor Deposition Machines?
What Considerations Should Be Made When Selecting A CVD Diamond Machine?
What Are The Applications Of Chemical Vapor Deposition Machines?
What Are The Common Applications Of Diamonds Produced By CVD Diamond Machines?
What Factors Should Be Considered When Selecting A Chemical Vapor Deposition Machine?
Can Chemical Vapor Deposition Machines Be Used For Multi-layered Thin Film Deposition?
4.7
out of
5
The speed of delivery was great, and the equipment arrived in perfect condition. It's been a pleasure working with KINTEK SOLUTION.
4.8
out of
5
The value for money is unbeatable. KINTEK SOLUTION provides high-quality equipment at a reasonable price.
4.9
out of
5
The quality of the equipment is top-notch. It's clear that KINTEK SOLUTION uses only the best materials and construction methods.
4.9
out of
5
The durability of the equipment is exceptional. It's built to last and withstand the rigors of daily use in a lab setting.
4.8
out of
5
The technological advancement of the equipment is impressive. KINTEK SOLUTION is always at the forefront of innovation, providing cutting-edge solutions.
4.7
out of
5
The speed of delivery was exceptional. The equipment arrived well before the estimated delivery date.
4.9
out of
5
The value for money is outstanding. The equipment is worth every penny, and it's clear that KINTEK SOLUTION cares about providing customers with a great deal.
4.8
out of
5
The quality of the equipment is superb. It's evident that KINTEK SOLUTION uses only the highest quality materials and construction methods.
4.7
out of
5
The durability of the equipment is remarkable. It's built to withstand the rigors of daily use in a lab setting and shows no signs of wear or tear.
4.9
out of
5
The technological advancement of the equipment is groundbreaking. KINTEK SOLUTION is always pushing the boundaries of innovation, and their equipment is a testament to their commitment to excellence.
4.8
out of
5
The speed of delivery was lightning fast. The equipment arrived within days of placing the order, which was incredibly convenient.
4.9
out of
5
The value for money is exceptional. The equipment is incredibly affordable, especially considering the high quality and advanced features it offers.
4.7
out of
5
The quality of the equipment is impeccable. It's clear that KINTEK SOLUTION takes pride in their craftsmanship, and the equipment is built to the highest standards.
4.8
out of
5
The durability of the equipment is outstanding. It's built to last, and I'm confident that it will provide years of reliable service.
4.9
out of
5
The technological advancement of the equipment is awe-inspiring. KINTEK SOLUTION is at the forefront of innovation, and their equipment is a testament to their commitment to pushing the boundaries of technology.
4.8
out of
5
The speed of delivery was commendable. The equipment arrived within the promised timeframe, which allowed us to start using it right away.
4.9
out of
5
The value for money is unbeatable. The equipment is incredibly affordable, especially considering the advanced features and high quality it offers.
4.7
out of
5
The quality of the equipment is exceptional. It's clear that KINTEK SOLUTION uses only the best materials and construction methods, resulting in a durable and reliable product.
4.8
out of
5
The durability of the equipment is impressive. It's built to withstand the rigors of daily use in a lab setting, and I'm confident that it will last for many years to come.
4.9
out of
5
The technological advancement of the equipment is remarkable. KINTEK SOLUTION is constantly innovating and pushing the boundaries of technology, and their equipment is a testament to their commitment to excellence.
Products
Microwave Plasma Chemical Vapor Deposition MPCVD Machine System Reactor for Lab and Diamond Growth
REQUEST A QUOTE
Our professional team will reply to you within one business day. Please feel free to contact us!
Related Products
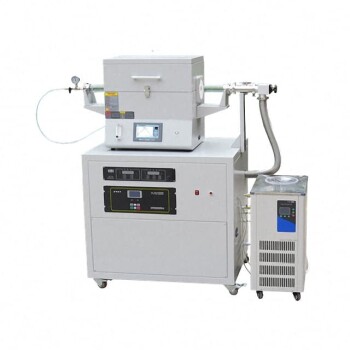
Efficient split chamber CVD furnace with vacuum station for intuitive sample checking and quick cooling. Up to 1200℃ max temperature with accurate MFC mass flowmeter control.
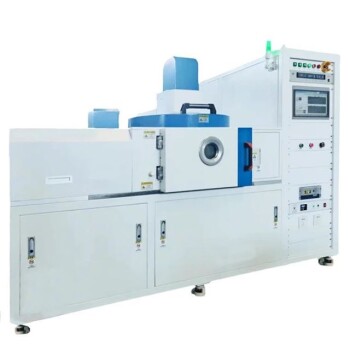
RF PECVD System Radio Frequency Plasma-Enhanced Chemical Vapor Deposition RF PECVD
RF-PECVD is an acronym for "Radio Frequency Plasma-Enhanced Chemical Vapor Deposition." It deposits DLC (Diamond-like carbon film) on germanium and silicon substrates. It is utilized in the 3-12um infrared wavelength range.
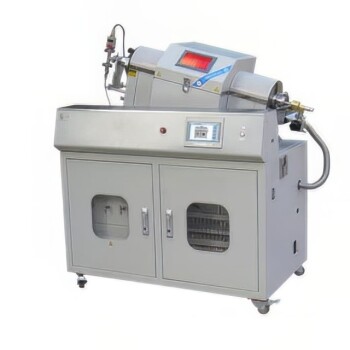
Inclined Rotary Plasma Enhanced Chemical Vapor Deposition PECVD Equipment Tube Furnace Machine
Introducing our inclined rotary PECVD furnace for precise thin film deposition. Enjoy automatic matching source, PID programmable temperature control, and high accuracy MFC mass flowmeter control. Built-in safety features for peace of mind.
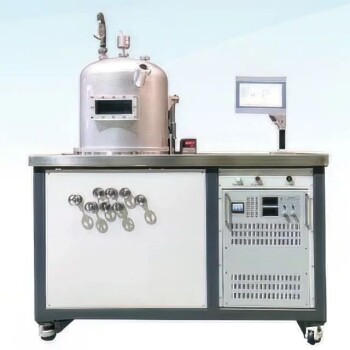
HFCVD Machine System Equipment for Drawing Die Nano-Diamond Coating
The nano-diamond composite coating drawing die uses cemented carbide (WC-Co) as the substrate, and uses the chemical vapor phase method ( CVD method for short ) to coat the conventional diamond and nano-diamond composite coating on the surface of the inner hole of the mold.
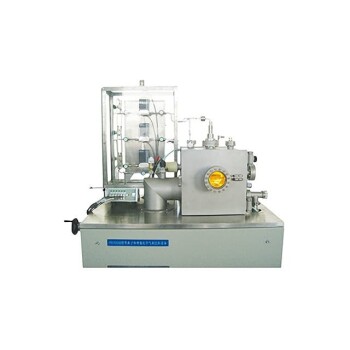
Inclined Rotary Plasma Enhanced Chemical Vapor Deposition PECVD Equipment Tube Furnace Machine
Upgrade your coating process with PECVD coating equipment. Ideal for LED, power semiconductors, MEMS and more. Deposits high-quality solid films at low temps.
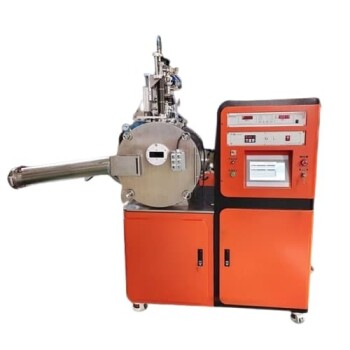
Vacuum Induction Melting Spinning System Arc Melting Furnace
Develop metastable materials with ease using our Vacuum Melt Spinning System. Ideal for research and experimental work with amorphous and microcrystalline materials. Order now for effective results.
Related Articles
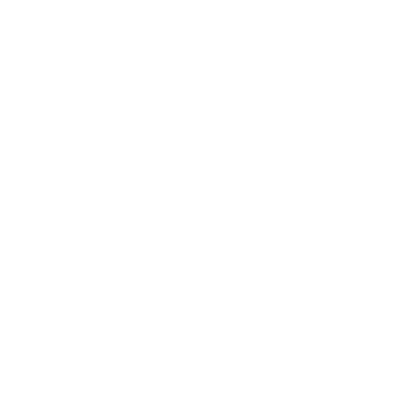
How to Achieve High Quality Single-Crystal Diamond with MPCVD
Microwave plasma chemical vapor deposition (MPCVD) is a popular technique for producing high-quality single-crystal diamond.
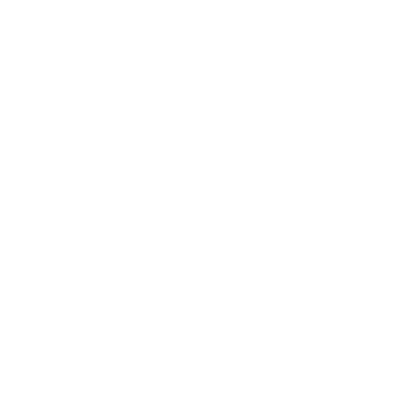
The Process of Fabricating a CVD Diamond By MPCVD Machine
CVD diamond machines have gained significant importance in various industries and scientific research.
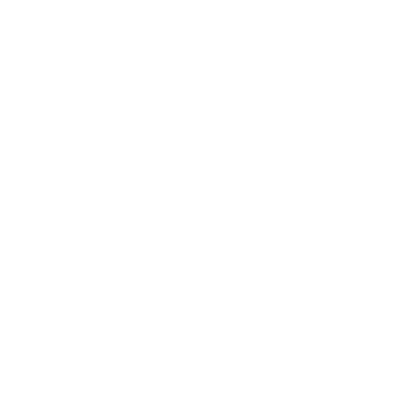
The Advancements in MPCVD Systems for Large Size Single Crystal Diamonds
Advancements in MPCVD systems have enabled the production of larger and higher quality single-crystal diamonds, offering promising potential for future applications.
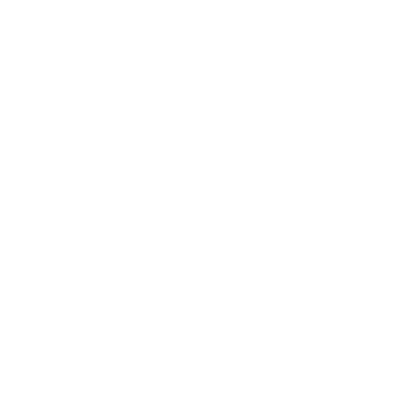
CVD furnace for the growth of carbon nanotubes
Chemical vapor deposition (CVD) furnace technology is a widely used method for growing carbon nanotubes.
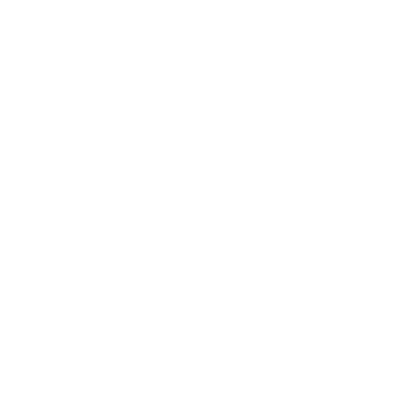
Plasma Enhanced Chemical Vapor Deposition (PECVD): A Comprehensive Guide
Learn everything you need to know about Plasma Enhanced Chemical Vapor Deposition (PECVD), a thin film deposition technique used in the semiconductor industry. Explore its principles, applications, and benefits.
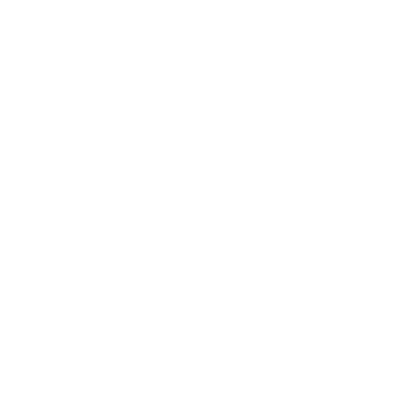
Understanding PECVD: A Guide to Plasma-Enhanced Chemical Vapor Deposition
PECVD is a useful technique for creating thin film coatings because it allows for the deposition of a wide variety of materials, including oxides, nitrides, and carbides.
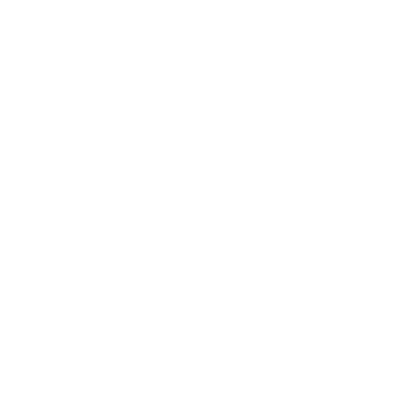
An Introduction to Chemical Vapor Deposition (CVD)
Chemical vapor deposition, or CVD, is a coating process that involves the use of gaseous reactants to produce thin films and coatings of high quality.
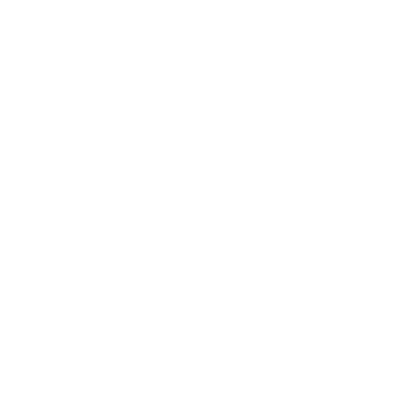
CVD Machines for Thin Film Deposition
Chemical Vapor Deposition (CVD) is a widely used technique for deposition of thin films on various substrates.
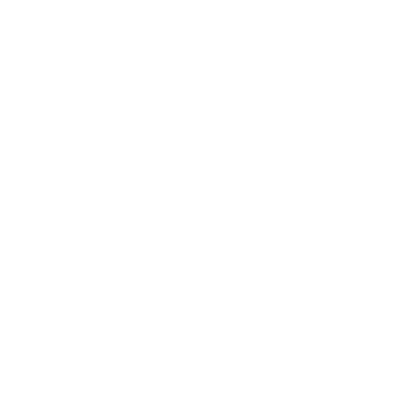
A Comprehensive Guide to MPCVD: Diamond Synthesis and Applications
Explore the fundamentals, advantages, and applications of Microwave Plasma Chemical Vapor Deposition (MPCVD) in diamond synthesis. Learn about its unique capabilities and how it compares to other diamond growth methods.
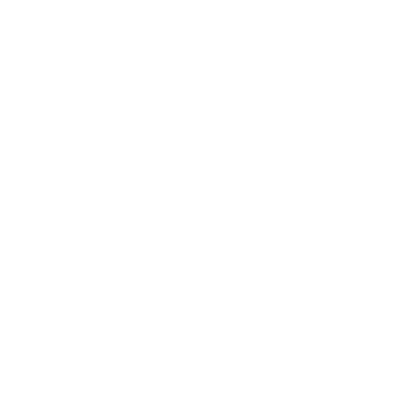
A beginner's guide to MPCVD machines
MPCVD (Microwave Plasma Chemical Vapor Deposition) is a process used to deposit thin films of material onto a substrate using plasma generated by microwaves.
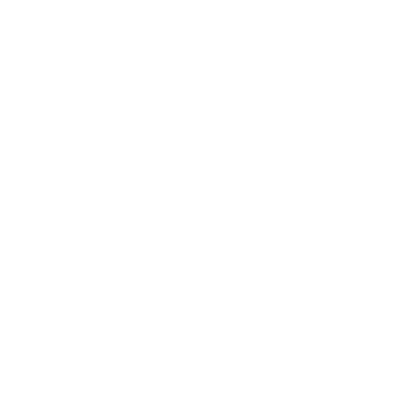
Advantages and Disadvantages of Chemical Vapor Deposition (CVD)
Chemical vapor deposition (CVD) is a versatile thin-film deposition technique widely used in various industries. Explore its advantages, disadvantages, and potential new applications.
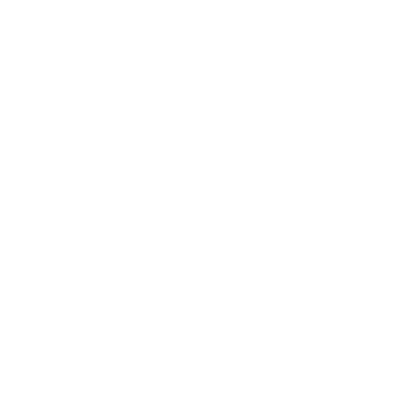
PECVD Furnace A Low-Power and Low-Temperature Solution for Soft Matter
PECVD (Plasma Enhanced Chemical Vapor Deposition) furnaces have become a popular solution for the deposition of thin films on soft matter surfaces.