Introduction to Thin Film Deposition
Thin film deposition is a process of applying a thin layer of material onto a substrate surface. This is an essential process used in the semiconductor industry to manufacture microelectronic devices. There are several techniques involved in thin film deposition, including physical vapor deposition (PVD), chemical vapor deposition (CVD), and atomic layer deposition (ALD). In this blog post, we will focus on CVD machines, which are widely used in the semiconductor industry due to their numerous advantages.
Table of Contents
What is CVD?
Chemical Vapor Deposition (CVD) is a widely used technique for deposition of thin films on various substrates. In this process, the substrate is exposed to one or more volatile precursors that react or decompose on the substrate surface to produce the desired thin film deposit.
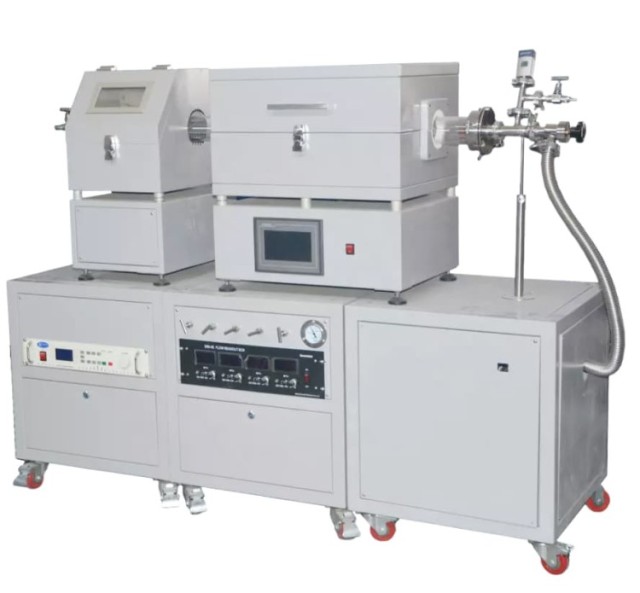
How does CVD work?
CVD machines are used to create thin films using chemical reactions of reactive gases on the substrate surface. The process involves the introduction of a precursor gas into a reaction chamber, where it is heated to a high temperature. The precursor gas reacts with the substrate to form a thin film layer.
What are the advantages of CVD?
CVD offers many benefits not provided by Physical Vapor Deposition (PVD), mainly since the reactive materials are gaseous. This means that the process doesn’t need a line of sight between the target material and substrate, and it’s possible to coat multiple parts in one reaction. CVD machines are used to deposit a wide range of materials, including metals, semiconductors, and ceramics, and are widely used in the production of microelectronic devices, optical coatings, and solar cells.
What are the different types of CVD?
CVD machines are available in a variety of configurations, including low-pressure CVD, plasma-enhanced CVD, and atomic layer deposition (ALD). Each configuration has its advantages and disadvantages, depending on the specific application.
What are the applications of CVD?
CVD processes are used for a broad spectrum of applications. These range from patterning films to insulation materials in transistor structures and between the layers of conducting metal that form the electrical circuit. CVD processes are also important in strain engineering that uses compressive or tensile stress films to enhance transistor performance through improved conductivity. Thin-film deposition also plays a critical role in many sustainable technologies, including solar power and energy storage.
In summary, CVD is a process in which a substrate is exposed to one or more volatile precursors that react or decompose on the substrate surface to produce the desired thin film deposit. CVD processes are used for a broad spectrum of applications, and the machines are available in a variety of configurations, each having its advantages and disadvantages, depending on the specific application.
Advantages of CVD Machines
Chemical Vapor Deposition (CVD) machines are widely used in thin film deposition for a variety of applications. These machines offer many advantages over other methods of thin film deposition.
Versatility in Material Deposition
The first advantage of CVD machines is the ability to deposit a wide range of materials including metals, semiconductors, and insulators. This versatility makes CVD machines an indispensable tool in the manufacturing of electronic devices such as microchips and solar cells.
Uniform Thin Film Deposition
Another advantage of CVD machines is the ability to deposit uniform thin films with high precision and accuracy. CVD machines offer excellent control over the thickness, composition, and uniformity of the deposited films. This precision and accuracy are critical in the manufacturing of electronic devices where even small variations in the deposited films can have a significant impact on the performance and reliability of the devices.
High Deposition Rate
Additionally, CVD machines offer a high deposition rate, enabling the production of large quantities of thin films in a short amount of time. This is particularly useful in industrial-scale production where the speed of production is essential.
Efficiency and Scalability
CVD machines are also a highly efficient method of thin film deposition, with minimal waste and low energy consumption. Finally, CVD machines offer excellent scalability, making them suitable for both small-scale laboratory research and large-scale industrial production.
Applications
The advantages of CVD machines have made them an essential tool in various industries such as electronics, solar cells, and even water filtration systems. For example, CVD has enabled the production of large-scale sheets of graphene, which are atomically thin sheets of hybridized carbon atoms arranged in a honeycomb structure used for a very wide range of applications from large screen TV displays to water filtration systems.
In conclusion, CVD machines are a versatile, precise, efficient, and scalable method of thin film deposition with many advantages over other methods. These machines offer a high level of control over the deposition process, which is critical in the manufacturing of electronic devices where even small variations in the deposited films can have a significant impact on the performance and reliability of the devices.
Applications of CVD Machines
CVD machines are widely used in various industries such as electronics, optics, and aerospace. The applications of CVD machines are numerous and varied.
Electronics
In the electronics industry, CVD machines are used to deposit thin films of silicon on substrates to create microchips. Silicon is the most commonly used material in the semiconductor industry, and CVD machines are crucial to the production of high-quality silicon thin films. CVD machines are also used to deposit thin films of other materials such as titanium nitride and tungsten for use in interconnects and circuitry.
Optics
In the optics industry, CVD machines are used to deposit thin films of materials such as titanium dioxide to create anti-reflective coatings on lenses. These coatings reduce glare and improve the efficiency of optical devices. CVD machines are also used to deposit thin films of other materials such as silicon dioxide, aluminum oxide, and zinc oxide for use in mirrors, filters, and waveguides.
Aerospace
In the aerospace industry, CVD machines are used to deposit thin films of materials such as titanium and aluminum to create lightweight and durable coatings on aircraft components. These coatings provide resistance to wear, corrosion, and high temperatures. CVD machines are also used to deposit thin films of other materials such as carbon fiber and ceramic composites for use in aircraft structures and engine components.
Solar Cells
CVD machines are also used in the production of solar cells, where they are used to deposit thin films of materials such as cadmium telluride and copper indium gallium selenide on substrates. These thin films form the basis of thin-film solar cells, which are more flexible and lightweight than traditional solar cells. CVD machines are also used to deposit thin films of other materials such as zinc oxide and titanium dioxide for use in transparent conductive layers and anti-reflective coatings.
Overall, CVD machines play a crucial role in the manufacturing of various products, and their applications are expected to expand in the future. The ability to deposit high-quality thin films in a controlled manner makes CVD machines an essential tool in many industries.
How CVD Machines Work
Chemical vapor deposition (CVD) is a widely used method for depositing thin films. CVD machines work by introducing reactive gases into a reaction chamber, where they react with a substrate surface to form a thin film. The process involves several steps, including gas flow control, substrate heating, and reaction chamber pressure control.
Gas Flow Control
In the gas flow control step, the precursor gases are introduced into the reaction chamber at precise flow rates. The gas flow rate is an important parameter that affects the growth rate and quality of the thin film. The gas flow control system ensures that the gases are introduced to the reaction chamber in a controlled and precise manner.
Substrate Heating
In the substrate heating step, the substrate is heated to a specific temperature to promote the chemical reaction between the precursor gases and the substrate surface. The substrate temperature is an important parameter that affects the growth rate and quality of the thin film. The substrate heating system ensures that the substrate is heated to the desired temperature in a controlled and precise manner.
Reaction Chamber Pressure Control
In the reaction chamber pressure control step, the pressure inside the reaction chamber is controlled to optimize the chemical reaction between the precursor gases and the substrate surface. The pressure inside the reaction chamber is an important parameter that affects the growth rate and quality of the thin film. The reaction chamber pressure control system ensures that the pressure inside the reaction chamber is maintained at the desired level in a controlled and precise manner.
Thin Film Formation
The gas molecules react with the substrate surface, forming a solid film that adheres to the surface. The CVD process can be used to deposit a variety of materials, including metals, semiconductors, and ceramics. The materials deposited can have a wide range of properties, including electrical conductivity, optical transparency, and hardness.
Applications of CVD Machines
CVD machines are commonly used in the production of microelectronics, such as integrated circuits and solar cells. The machines are also used in the production of coatings for various applications, such as wear resistance and corrosion protection.
In summary, the CVD process is a powerful tool for the deposition of thin films, with applications across a wide range of industries. The gas flow control, substrate heating, and reaction chamber pressure control systems all play important roles in ensuring that the thin films deposited are of high quality and meet the desired specifications.
Types of CVD Machines
Chemical Vapor Deposition (CVD) machines are essential for the production of thin films used in a wide range of applications. These machines come in different types to suit varying requirements. Here are some of the most common types of CVD machines:
Atmospheric Pressure CVD
Atmospheric Pressure CVD is the most commonly used CVD machine for the deposition of thin films on a large scale. This technique operates at atmospheric pressure and is ideal for depositing large-area films. It is fast, cost-effective, and can be used to deposit a wide range of materials.
Low-pressure CVD
Low-pressure CVD operates under subatmospheric pressure and is used for the deposition of high-quality thin films with precise control over the deposition process. It is ideal for depositing thin films with high uniformity and thickness control. This technique is widely used in the semiconductor industry for the production of integrated circuits.
Plasma-Enhanced CVD
Plasma-Enhanced CVD is a type of CVD technique used for the deposition of thin films on temperature-sensitive substrates. This technique uses plasma to enhance the chemical reaction between the precursor gases and the substrate surface, resulting in a higher deposition rate and better film quality. It is widely used in the production of thin films for electronic devices, such as solar cells and displays.
Hot Wire CVD
Hot Wire CVD is a type of CVD technique that uses a hot wire to decompose the precursor gases and deposit the thin film on the substrate surface. It is a low-temperature process and is ideal for the deposition of diamond-like carbon films and other hard materials.
Photo-assisted CVD
Photo-assisted CVD is a type of CVD technique that uses light to enhance the chemical reaction between the precursor gases and the substrate surface. It is ideal for the deposition of thin films with high uniformity and thickness control.
Microwave Plasma CVD
Microwave Plasma CVD is a type of CVD technique that uses microwave energy to generate plasma and enhance the chemical reaction between the precursor gases and the substrate surface. It is ideal for the deposition of thin films on a large scale and can be used to deposit a wide range of materials.
In choosing a CVD machine, it is important to consider factors such as the type of substrate, the required film quality, and the deposition temperature. The type of CVD machine chosen will depend on the specific application and the desired outcome. Overall, CVD machines play an important role in the production of thin films, and the development of new and improved CVD machines is an ongoing area of research in the field of materials science.
Conclusion on CVD machines
In conclusion, CVD machines are highly versatile and efficient tools for thin film deposition. They offer numerous advantages, such as precise control over film thickness and composition, high deposition rates, and compatibility with a wide range of materials. CVD machines have found applications in various fields, including microelectronics, optics, and coatings, among others. Different types of CVD machines are available, each with specific features and capabilities. Overall, CVD machines are essential tools for research and industrial applications that require the deposition of high-quality thin films.
CONTACT US FOR A FREE CONSULTATION
KINTEK LAB SOLUTION's products and services have been recognized by customers around the world. Our staff will be happy to assist with any inquiry you might have. Contact us for a free consultation and talk to a product specialist to find the most suitable solution for your application needs!