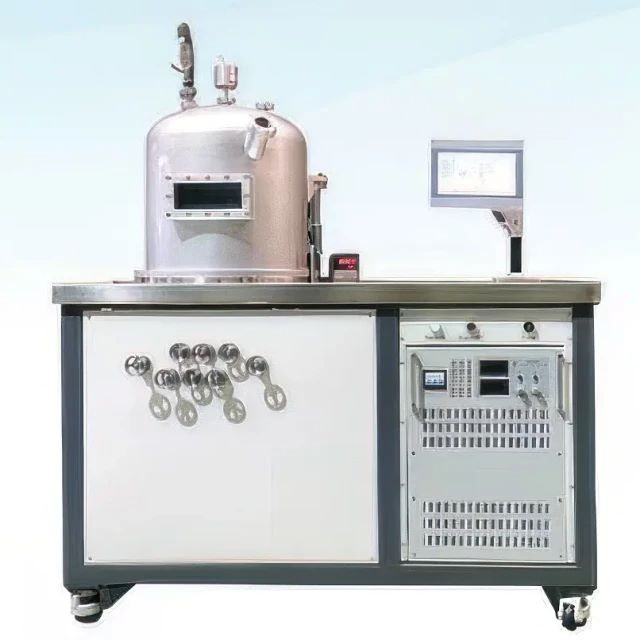
MPCVD
HFCVD Machine System Equipment for Drawing Die Nano-Diamond Coating
Item Number : MP-CVD-100
Price varies based on specs and customizations
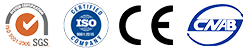
Shipping:
Contact us to get shipping details Enjoy On-time Dispatch Guarantee.
Why Choose Us
Reliable PartnerEasy ordering process, quality products, and dedicated support for your business success.
Application
HFCVD chemical vapor deposition of diamond working principle is: mix a carbon-containing atmosphere with supersaturated hydrogen, activate it in a certain way, and then pass it through a certain atmosphere composition, activation energy, substrate temperature, and the distance between the substrate and the activation source, etc. Under these conditions, a diamond film is deposited on the bottom surface. It is generally believed that the nucleation and growth of diamond films can be divided into three stages:
- Carbon-containing gas and radon gas decompose into carbon, hydrogen atoms and other active free groups at a certain temperature. They combine with the matrix to first form a very thin carbide transition layer.
- Carbon atoms deposit diamond nuclei on the transition layer formed on the substrate.
- The formed diamond crystal nucleus grows into a diamond micro-item under a suitable environment, and then grows into a diamond film.
Detail & Parts
Technical specifications
HFCVD technical composition | ||
Technical Parameters | Equipment composition | System Configuration |
Bell Jar: Dia. 500mm, Height 550mm, SUS304 stainless steel chamber; inner stainless steel skin insulation, lifting height is 350mm; | A set of vacuum chamber (bell jar) main body (jacketed water-cooling structure) | Vacuum chamber (bell jar) main body;The cavity is made of high-quality 304 stainless steel; Vertical bell jar: the jacketed water-cooling jacket is installed on the overall periphery of the bell jar. The inner wall of the bell jar is insulated with stainless steel skin, and the bell jar is fixed on the side . Accurate and stable positioning ; Observation window: horizontally arranged in the middle of the vacuum chamber 200mm Observation window, water cooling, baffle, side and upper configuration 45 Degree bevel angle, 50° observation window (observe the same point as the horizontal observation window, and the sample supporting platform); the two observation windows maintain the existing position and size.Bell jar bottom is 20mm higher than the plane of the bench , set cooling; the holes reserved on the plane, such as large valves, air release valves, air pressure measurement, bypass valves, etc., are sealed with metal mesh and reserved for installing electrodes Interface; |
Equipment table: L1550* W900*H1100mm | One set of drag sample table device (adopting double-axis drive ) | Sample holder device: Stainless steel sample holder (welding water cooling ) 6- position device; it can be adjusted separately, only up and down adjustment, the up and down adjustment range is 25mm, and the left and right shaking is required to be less than 3% when going up and down ( that is, the left and right shaking of rising or falling by 1mm is less than 0.03mm ) , and the sample stage does not rotate when rising or falling. |
Ultimate vacuum degree: 2.0×10-1Pa ; | A set of vacuum system | Vacuum system: Vacuum system configuration: mechanical pump + vacuum valve + physical bleed valve + main exhaust pipe + bypass; (provided by the vacuum pump supplier), the vacuum valve uses a pneumatic valve; Vacuum system measurement: Membrane pressure. |
Pressure rise rate : ≤5Pa/h; | Two channels mass flow meter gas supply system | Gas supply system: The mass flow meter is configured by Party B, two-way air intake, the flow rate is controlled by the mass flow meter, after the two-way meeting, it enters the vacuum chamber from the top , and the inside of the air intake pipe is 50mm |
Sample table movement: up and down range is ± 25m; it is required to shake left and right ratio when up and down by ± 3%; | One set of electrode device (2 channels) | Electrode device: The length direction of the four electrode holes is parallel to the length direction of the support platform, and the length direction is facing the main observation window with a diameter of 200mm . |
Working pressure: use membrane gauge pressure gauge, measuring range: 0 ~ 10kPa; work constant at 1kPa ~5kPa,the constant pressure value changes plus or minus 0.1kPa; | A set of cooling water system | Cooling water system: The bell jar, electrodes, and bottom plate are all equipped with circulating water cooling pipelines, and are equipped with insufficient water flow alarm device 3.7: control system. Switches, instruments, instruments and power supply for bell lifting, deflation, vacuum pump, main road, bypass, alarm, flow, air pressure, etc. are set on the side of the stand, and are controlled by a 14 -inch touch screen; the equipment has a fully automatic control program without manual intervention, and can store data and call data |
Air intake position: air intake at the top of the bell jar, and the position of the exhaust port is located directly below the sample holder; | Control system | |
Control System: PLC controller + 10-inch touch screen | A set of automatic pressure control system (original pressure control valve imported from Germany ) | |
Inflation system: 2 channels mass flow meter, flow range: 0-2000sccm and 0-200sccm; Pneumatic valve valve | Resistance Vacuum Gauge | |
3.1.10 Vacuum pump: D16C vacuum pump |
Advantages
The nano-diamond composite coating drawing die uses cemented carbide (WC-Co) as the substrate, and uses the chemical vapor phase method ( CVD method for short ) to coat the conventional diamond and nano-diamond composite coating on the surface of the inner hole of the mold. And a brand new product obtained after grinding and polishing the coating . The nano-diamond composite coating coated on the surface of the inner hole not only has the characteristics of strong adhesion and wear resistance of the conventional diamond coating, but also has the advantages of flat and smooth surface of the nano-diamond coating, small friction coefficient and easy grinding and polishing. Coating technology not only solves the technical problem of coating adhesion, but also breaks through the bottleneck that the surface of diamond coating is not easy to polish, and removes the obstacles to the industrialization of CVD diamond film.
Technical indicators |
Traditional drawing die |
Nano-diamond coated drawing die |
Coating Surface Grain Size |
none |
20~80nm |
Coating diamond content |
none |
≥99% |
Diamond Coating Thickness |
none |
10 ~ 15mm |
Surface roughness |
Ra≤0.1mm |
Class A: Ra≤0.1mm Class B: Ra≤0.05mm |
Coating drawing die inner hole diameter range |
Ф3 ~ Ф70mm |
Ф3 ~ Ф70mm |
Service life span |
Life span depends on working conditions |
6-10 times longer |
Surface friction coefficient |
0.8 |
0.1 |
- For the parallelism and straightness of the mold lifting platform of the equipment, our company has specially produced special tooling. The biaxial lifting method is enough to allow the two ends to be raised and lowered by about ±2 wires, so that smaller molds can be made.
- For the tooling of the equipment, our company integrates the location of each company on the tooling, aiming at the tooling and process of the mold. Good tooling and clamping, stable and reliable, high precision, easy to operate.
- For the shut-off valve of the equipment, other manufacturers use baffle valves, which cannot be adjusted linearly (that is, the gap increases quickly as soon as it is opened). Our company designs it according to the principle of the shut-off valve and stable pressure control, so that the shut-off gap can be linearly adjusted to achieve Stable pressure control;
- The fully automatic control system automatically controls the pressure according to computer algorithms; it can reduce the operator's randomness and make the process more confidential. It saves labor, and the consistency of mold quality of the same specifications is more ideal;
- For the stability of the lifting bell jar, our company uses self-lubricating bearings, which make the rotation more flexible and free of jamming. Basic process, diamond coating can be made according to each customer's diamond coating process.
Warnings
Operator safety is the top important issue! Please operate the equipment with cautions. Working with inflammable& explosive or toxic gases is very dangerous, operators must take all necessary precautions before starting the equipment. Working with positive pressure inside the reactors or chambers is dangerous, operator must fellow the safety procedures strictly. Extra caution must also be taken when operating with air-reactive materials, especially under vacuum. A leak can draw air into the apparatus and cause a violent reaction to occur.
Designed for You
KinTek provide deep custom made service and equipment to worldwide customers, our specialized teamwork and rich experienced engineers are capable to undertake the custom tailoring hardware and software equipment requirements, and help our customer to build up the exclusive and personalized equipment and solution!
Would you please drop your ideas to us, our engineers are ready for you now!
4.8
out of
5
The HFCVD Equipment is a game-changer in diamond coating technology. It's efficient, precise, and delivers superior results. Highly recommended!
4.9
out of
5
I'm thoroughly impressed with the quality and performance of the HFCVD Equipment. It has significantly improved our diamond coating process, resulting in exceptional results. A must-have for any lab!
4.7
out of
5
The HFCVD Equipment has exceeded my expectations. It's user-friendly, reliable, and produces high-quality diamond coatings consistently. A valuable addition to our laboratory.
4.9
out of
5
The HFCVD Equipment is a technological marvel. It has revolutionized our diamond coating research, enabling us to achieve remarkable results. Highly recommended for advanced materials research.
4.8
out of
5
The HFCVD Equipment has transformed our laboratory's capabilities. It delivers exceptional diamond coatings with remarkable precision and efficiency. A valuable investment for any research institution.
4.7
out of
5
I'm highly satisfied with the HFCVD Equipment. It has significantly improved our diamond coating process, resulting in enhanced product quality and reduced production time. Highly recommended!
4.9
out of
5
The HFCVD Equipment is a testament to cutting-edge technology. It has enabled us to achieve unprecedented results in diamond coating, opening up new possibilities for research and innovation.
4.8
out of
5
The HFCVD Equipment has proven to be an invaluable asset to our laboratory. It delivers consistent, high-quality diamond coatings, making it an essential tool for our research.
4.7
out of
5
I'm thoroughly impressed with the HFCVD Equipment. It's user-friendly, efficient, and produces exceptional diamond coatings. A must-have for any laboratory involved in materials research.
4.9
out of
5
The HFCVD Equipment is a remarkable piece of technology. It has enabled us to achieve breakthrough results in diamond coating, pushing the boundaries of materials science.
Products
HFCVD Machine System Equipment for Drawing Die Nano-Diamond Coating
REQUEST A QUOTE
Our professional team will reply to you within one business day. Please feel free to contact us!
Related Products
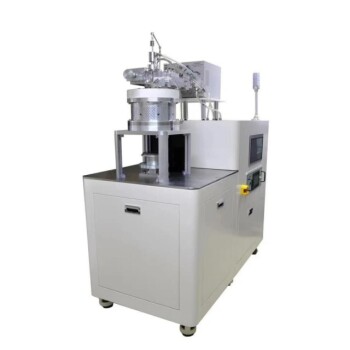
Microwave Plasma Chemical Vapor Deposition MPCVD Machine System Reactor for Lab and Diamond Growth
Get high-quality diamond films with our Bell-jar Resonator MPCVD machine designed for lab and diamond growth. Discover how Microwave Plasma Chemical Vapor Deposition works for growing diamonds using carbon gas and plasma.
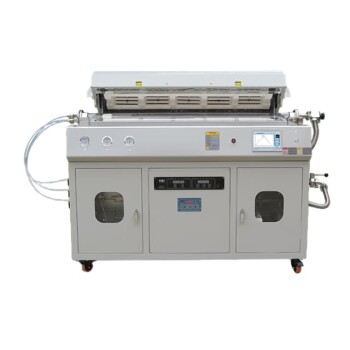
Multi Heating Zones CVD Tube Furnace Machine Chemical Vapor Deposition Chamber System Equipment
KT-CTF14 Multi Heating Zones CVD Furnace - Precise Temperature Control and Gas Flow for Advanced Applications. Max temp up to 1200℃, 4 channels MFC mass flow meter, and 7" TFT touch screen controller.
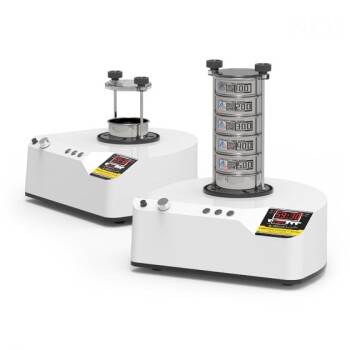
Three-dimensional electromagnetic sieving instrument
KT-VT150 is a desktop sample processing instrument for both sieving and grinding. Grinding and sieving can be used both dry and wet. The vibration amplitude is 5mm and the vibration frequency is 3000-3600 times/min.
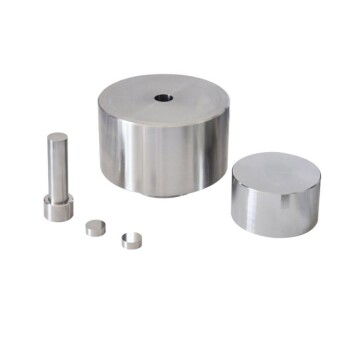
Anti-Cracking Press Mold for Lab Use
The anti-cracking press mold is a specialized equipment designed for molding various shapes and sizes of film using high pressure and electric heating.
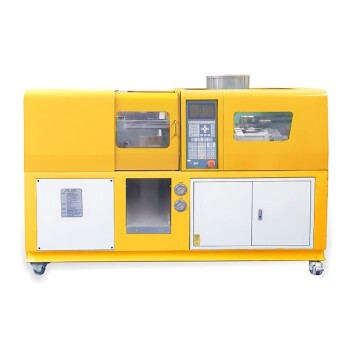
Small Injection Molding Machine for Lab Use
The small injection molding machinehas fast and stable movements; good controllability and repeatability, super energy saving; the product can be automatically dropped and formed; the machine body is low, convenient for feeding, easy to maintain, and no height restrictions on the installation site.
Related Articles
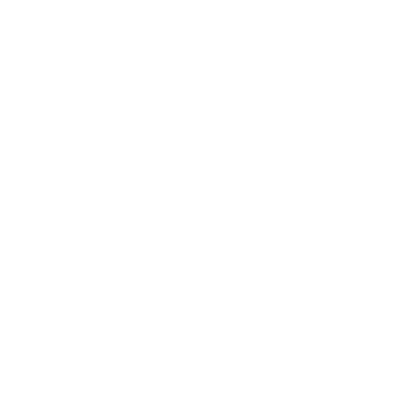
Mastering Handheld Coating Thickness Gauges: A Comprehensive Guide for Industrial and Automotive Applications
Explore the intricacies of handheld coating thickness gauges, their applications in electroplating, automotive paint, and powder coatings. Learn how to choose and use these instruments effectively for quality control and cost efficiency.
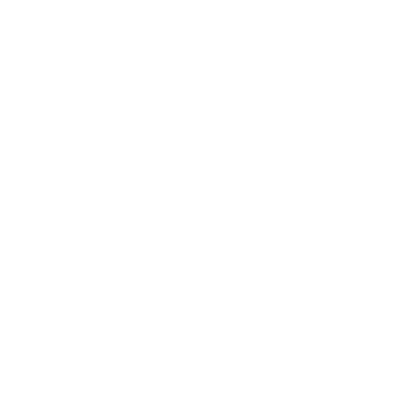
An Introduction to Chemical Vapor Deposition (CVD)
Chemical vapor deposition, or CVD, is a coating process that involves the use of gaseous reactants to produce thin films and coatings of high quality.
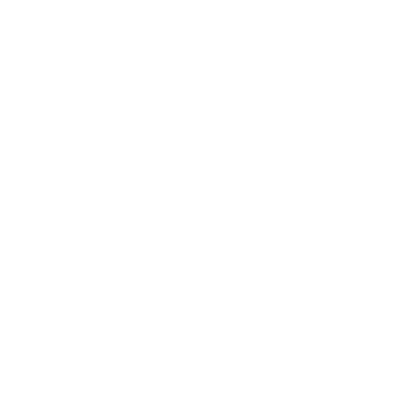
Advantages and Disadvantages of Chemical Vapor Deposition (CVD)
Chemical vapor deposition (CVD) is a versatile thin-film deposition technique widely used in various industries. Explore its advantages, disadvantages, and potential new applications.
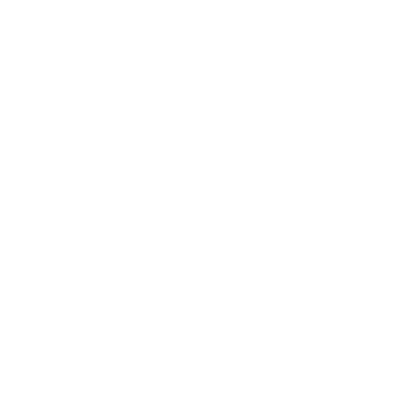
The Process of Fabricating a CVD Diamond By MPCVD Machine
CVD diamond machines have gained significant importance in various industries and scientific research.
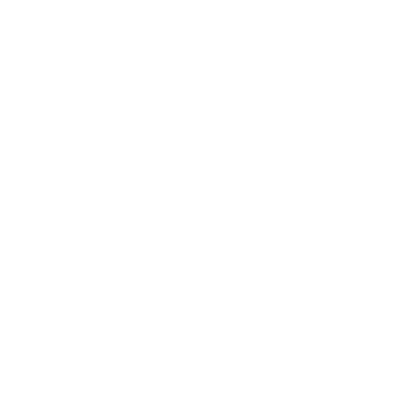
Handheld Coating Thickness Gauges: Accurate Measurement for Electroplating and Industrial Coatings
Discover the best practices and technologies for measuring coating thickness using handheld gauges. Ideal for electroplating, automotive paint, and powder coatings.
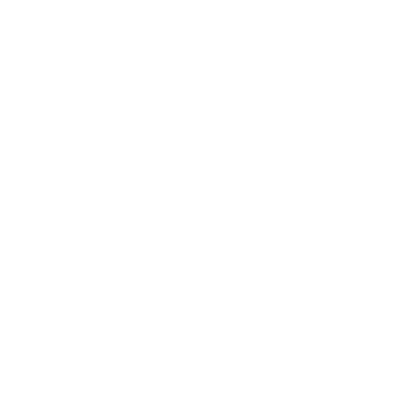
CVD furnace for the growth of carbon nanotubes
Chemical vapor deposition (CVD) furnace technology is a widely used method for growing carbon nanotubes.
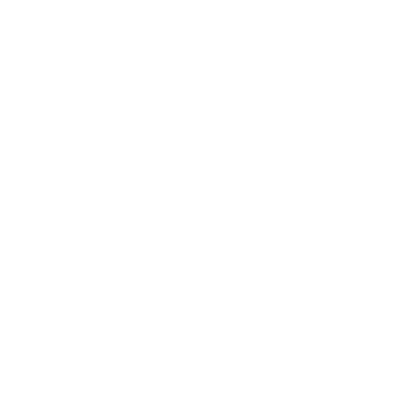
Plasma Enhanced Chemical Vapor Deposition (PECVD): A Comprehensive Guide
Learn everything you need to know about Plasma Enhanced Chemical Vapor Deposition (PECVD), a thin film deposition technique used in the semiconductor industry. Explore its principles, applications, and benefits.
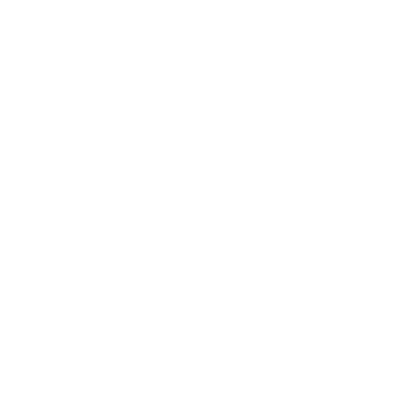
Understanding PECVD: A Guide to Plasma-Enhanced Chemical Vapor Deposition
PECVD is a useful technique for creating thin film coatings because it allows for the deposition of a wide variety of materials, including oxides, nitrides, and carbides.
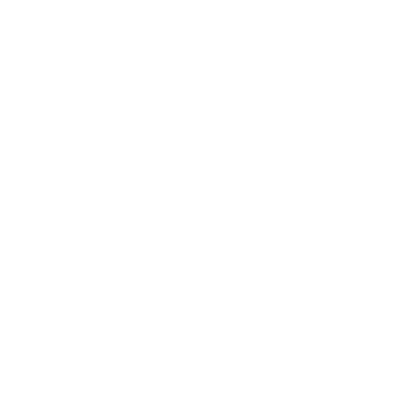
Comparing the Performance of PECVD and HPCVD in Coating Applications
Although both PECVD & HFCVD are used for coating applications, they differ in terms of deposition methods, performance, and suitability for specific applications.
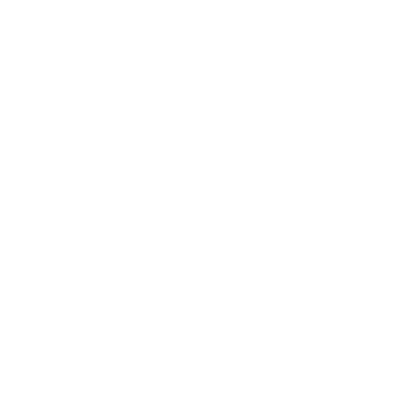
CVD Machines for Thin Film Deposition
Chemical Vapor Deposition (CVD) is a widely used technique for deposition of thin films on various substrates.
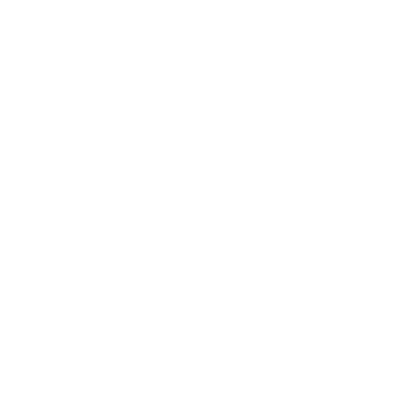
Chemical Vapor Deposition (CVD) of Graphene Challenges and Solutions
Chemical Vapor Deposition (CVD) is a widely adopted method for the production of high-quality graphene.
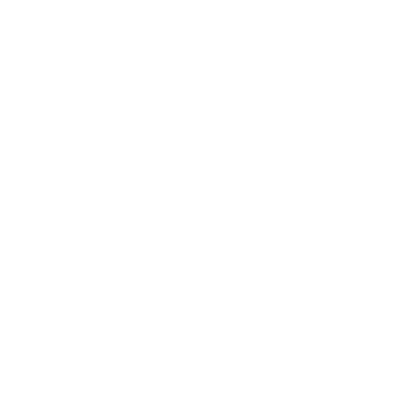
Understanding the CVD Diamond Machine and How It Works
CVD (Chemical Vapor Deposition) diamond creation process involves the deposition of carbon atoms onto a substrate using a gas phase chemical reaction. The process starts with the selection of a high-quality diamond seed, which is then placed in a growth chamber along with a carbon-rich gas mixture.