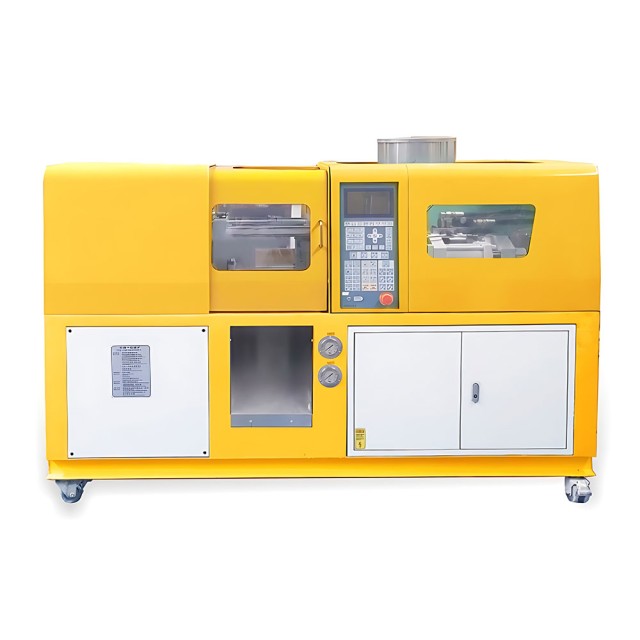
Rubber processing machine
Small Injection Molding Machine for Lab Use
Item Number : RPM-09
Price varies based on specs and customizations
- Control Mode
- PID control or PLC program control
- Calendering rollers
- 2-4 (or customized)
- Diameter of roller
- 120mm、160mm、200mm(or customized)
- Installation method of calender roller
- Vertical or parallel
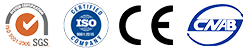
Shipping:
Contact us to get shipping details Enjoy On-time Dispatch Guarantee.
Why Choose Us
Reliable PartnerEasy ordering process, quality products, and dedicated support for your business success.
Introduction
The small injection molding machinehas fast and stable movements; good controllability and repeatability, super energy saving; the product can be automatically dropped and formed; the machine body is low, convenient for feeding, easy to maintain, and no height restrictions on the installation site.
Applicable materials for small injection molding machines: PP, PC, PVC, ABS, PE, PA6, PS, PEI, PMMA, POM, TPU, TPE, etc.
Detail & Parts
Applications
- Precision Parts Manufacturing: Ideal for producing small, intricate plastic parts used in electronics, medical devices, and automotive components.
- Rapid Prototyping: Suitable for quickly producing prototypes to test designs before moving to large-scale production.
- Small Batch Production: Efficient for producing smaller quantities of parts, which is cost-effective for low-volume manufacturing needs.
- Repair and Maintenance: Used for repairing or replacing small plastic parts in various equipment and machinery.
Features
- Compact Size: Smaller footprint compared to larger machines, making them suitable for smaller workspaces or laboratories.
- Energy Efficiency: Typically consume less energy due to their smaller size and lower injection capacities.
- Flexibility: Capable of molding a wide range of plastic materials and producing parts with varying complexities.
- Cost-Effectiveness: Lower initial investment and operational costs make them attractive for small businesses and startups.
- Ease of Operation: Often equipped with user-friendly interfaces, making them easier to operate and maintain.
- Quick Cycle Times: Can achieve fast cycle times, which is beneficial for high-turnover, small-part production.
- Small injection molding machines are a valuable tool in industries requiring precision, flexibility, and efficiency in plastic part production.
Technical specifications
Model No. | RPM-09 |
---|---|
Control Mode | PID control or PLC program control |
Calendering rollers | 2-4 (or customized) |
Diameter of roller | 120mm、160mm、200mm(or customized) |
Installation method of calender roller | Vertical or parallel |
Range of film thickness | 0.1mm~5mm (or customized) |
Roller speed | 0-30r/min(adjustable) |
Motor power | 4kw(or customized) |
Unwinding device | Friction roll |
Winding device | Friction winding |
Volume (W*D*H) | 1300*950*1600mm |
Weight(kg) | About 900kg About 900kgs |
Power Supply | 3f,AC380V |
FAQ
What Materials Does This Small Injection Molding Machine Support?
How Does A Small Injection Molding Machine Ensure Product Quality During The Production Process?
What Are The Environmental Protection Considerations For Small Injection Molding Machines?
What Industries Are Small Injection Molding Machines Mainly Used In?
How Difficult Is It To Operate A Small Injection Molding Machine?
What Are The Advantages Of Small Injection Molding Machines Compared To Large Injection Molding Machines?
4.7
out of
5
Incredible precision and stability, perfect for our lab's needs!
4.8
out of
5
Super quiet operation, a game-changer for our research environment.
4.9
out of
5
Efficient and durable, best value for our small batch productions.
4.7
out of
5
Quick delivery and easy setup, highly recommend for labs!
4.8
out of
5
Technologically advanced, saves us time and energy in prototyping.
4.9
out of
5
Compact yet powerful, ideal for our limited workspace.
4.7
out of
5
Excellent customer service and support, very satisfied.
4.8
out of
5
Highly reliable, our go-to machine for precision molding.
4.9
out of
5
Outstanding quality and performance, worth every penny.
4.7
out of
5
User-friendly interface, makes operation a breeze.
4.8
out of
5
Energy-efficient and eco-friendly, aligns perfectly with our lab's values.
Products
Small Injection Molding Machine for Lab Use
REQUEST A QUOTE
Our professional team will reply to you within one business day. Please feel free to contact us!
Related Products
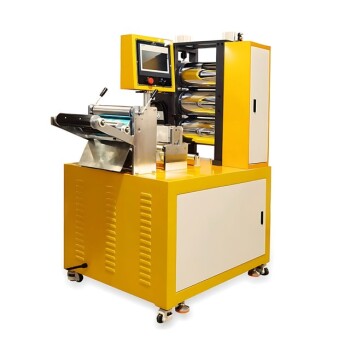
Small Lab Rubber Calendering Machine
Small lab rubber calendering machine is used for producing thin, continuous sheets of plastic or rubber materials. It is commonly employed in laboratories, small-scale production facilities, and prototyping environments to create films, coatings, and laminates with precise thickness and surface finish.
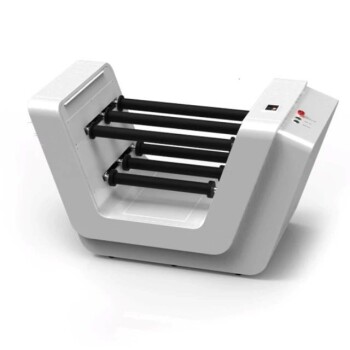
Laboratory Ten-Body Horizontal Jar Mill for Lab Use
The Ten-body horizontal jar mill is for 10 ball mill pots (3000ml or less). It has frequency conversion control, rubber roller movement, and PE protective cover.
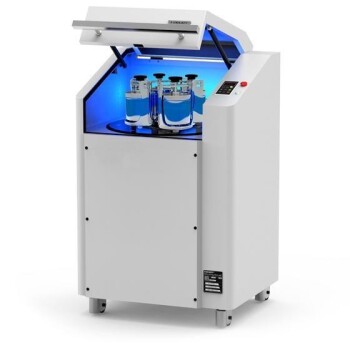
Laboratory Planetary Ball Mill Cabinet Planetary Ball Milling Machine
The vertical cabinet structure combined with ergonomic design enables users to obtain the best comfortable experience in standing operation. The maximum processing capacity is 2000ml, and the speed is 1200 revolutions per minute.
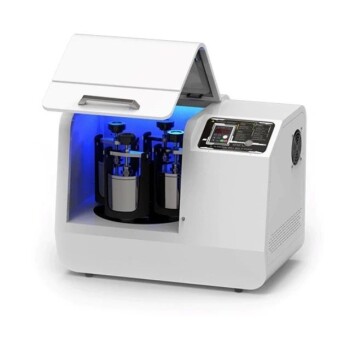
High Energy Planetary Ball Mill Milling Machine for Laboratory
The biggest feature is that the high energy planetary ball mill can not only perform fast and effective grinding, but also has good crushing ability
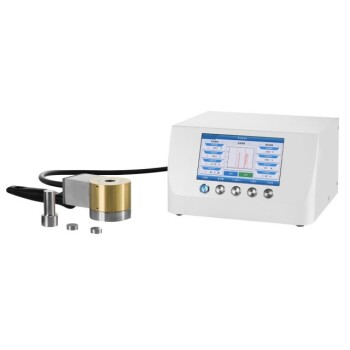
Cylindrical Lab Electric Heating Press Mold for Laboratory Applications
Efficiently prepare samples with Cylindrical Lab Electric Heating Press Mold. Fast heating, high temp & easy operation. Custom sizes available. Perfect for battery, ceramic & biochemical research.
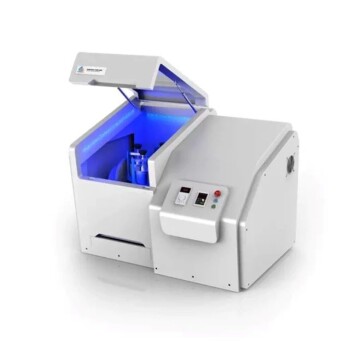
High-Energy Omnidirectional Planetary Ball Mill Machine for Laboratory
The KT-P2000E is a new product derived from the vertical high-energy planetary ball mill with a 360°rotation function. The product not only has the characteristics of the vertical high-energy ball mill, but also has a unique 360°rotation function for the planetary body.
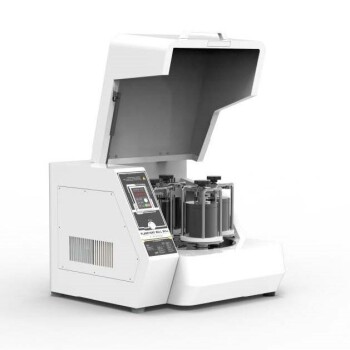
High Energy Planetary Ball Mill Milling Machine for Laboratory
Experience fast and effective sample processing with the F-P2000 high-energy planetary ball mill. This versatile equipment offers precise control and excellent grinding capabilities. Perfect for laboratories, it features multiple grinding bowls for simultaneous testing and high output. Achieve optimal results with its ergonomic design, compact structure, and advanced features. Ideal for a wide range of materials, it ensures consistent particle size reduction and low maintenance.
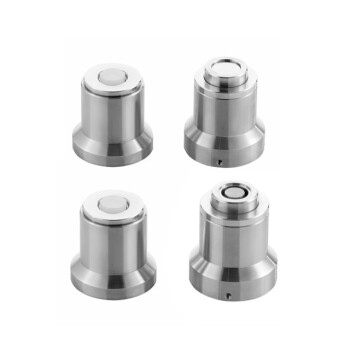
Button Battery Disassembly and Sealing Mold for Lab Use
The simple sealing and disassembly mold can be directly used on ordinary tablet presses, which can save costs, is convenient and fast, and can be used to encapsulate and disassemble button batteries. Other specifications can be customized.
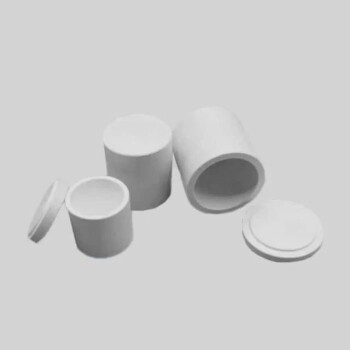
Evaporation Crucible for Organic Matter
An evaporation crucible for organic matter, referred to as an evaporation crucible, is a container for evaporating organic solvents in a laboratory environment.
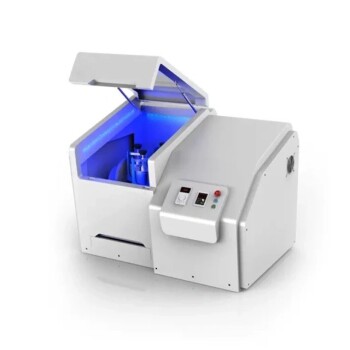
High-Energy Omnidirectional Planetary Ball Mill Milling Machine for Laboratory
The KT-P4000E is a new product derived from the vertical high-energy planetary ball mill with a 360° swivel function. Experience faster, uniform, and smaller sample output results with 4 ≤1000ml ball mill jars.
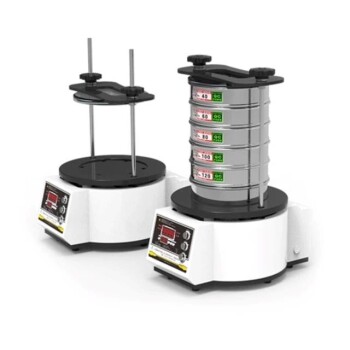
Laboratory Wet Three-Dimensional Vibratory Sieve Shaker Machine
The wet three-dimensional vibrating sieving instrument focuses on solving the sieving tasks of dry and wet samples in the laboratory. It is suitable for sieving 20g - 3kg dry, wet or liquid samples.
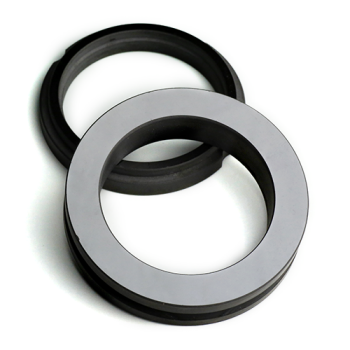
Custom CVD Diamond Coating for Lab Applications
CVD Diamond Coating: Superior Thermal Conductivity, Crystal Quality, and Adhesion for Cutting Tools, Friction, and Acoustic Applications
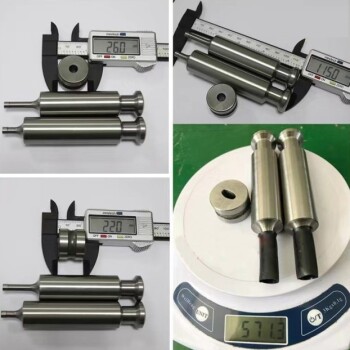
Multi-Punch Rotary Tablet Press Mold Ring for Rotating Oval and Square Molds
The multi-punch rotary tablet press mold stands as a pivotal component in pharmaceutical and manufacturing industries, revolutionizing the process of tablet production. This intricate mold system comprises multiple punches and dies arranged in a circular fashion, facilitating rapid and efficient tablet formation.