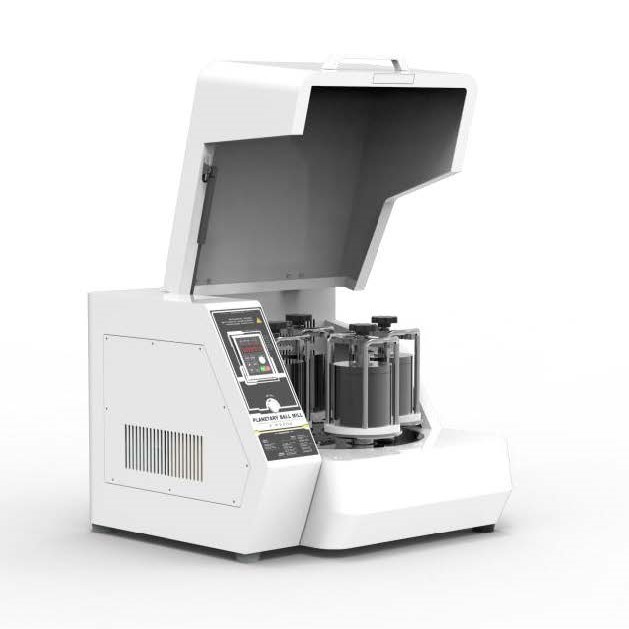
Milling Equipment
High Energy Planetary Ball Mill Milling Machine for Laboratory
Item Number : KT-P2000
Price varies based on specs and customizations
- Maximum injection size
- < 10 mm
- Maximum speed of ball mill tank
- 800 r/min
- Ball mill tank volume
- 500 ml
- Electrical description
- 100-120V/200-240VAC,50-60Hz,750W
- Dimensions (length, width and height)
- 570*570*420 mm
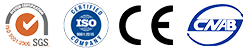
Shipping:
Contact us to get shipping details Enjoy On-time Dispatch Guarantee.
Why Choose Us
Reliable PartnerEasy ordering process, quality products, and dedicated support for your business success.
Introduction
The high-energy planetary ball mill is renowned for its rapid and efficient processing capabilities along with its extensive application range. Through extensive technological advancements and user feedback, this product has undergone significant enhancements in dynamic efficiency, noise reduction, operational safety, and user comfort. Its dimensions of 575mm width, 570mm depth, and 420mm height align with ergonomic requirements for laboratory desktop operation, offering a compact and user-friendly design.
Featuring up to four ball mill tanks with a volume of 500ml or less, the P2000 provides various material options and utilizes variable frequency control for enhanced functionality. Notably, its 304 stainless steel planetary disk ensures balanced and safe operation, reducing the risk of sample contamination.
Operating on the principle of high-frequency collisions, shearing, and friction, this mill achieves rapid sample processing with consistent particle size distribution. Key features include self-lubricating polymer gears for reduced noise, dual rear fans for efficient heat dissipation, and a separated design for heat and dust management.
The instrument offers one-click start, automatic processing, and a range of control options such as grinding time and movement direction. Additionally, it supports liquid nitrogen cooling for low-temperature grinding and can accommodate vacuum ball mill tanks for anti-oxidation processes, enhancing its versatility and reproducibility in laboratory settings.
Detail & Parts
Applications
- Grinding and pulverizing of ores
- Sample preparation for minerals analysis
- Ferroalloys processing
- Ceramic material grinding
- Soil and aggregate testing
- Chemical sample preparation
- High-energy milling for research purposes
- Grinding of refractory materials
- Preparation of pharmaceutical compounds
- Grinding and mixing of various materials in laboratories
Features
- Effective for Mohs 1-10 hard material: Provides efficient grinding for a wide range of materials, ensuring thorough size reduction.
- No moving parts – utilizes compressed air: Ensures minimal maintenance and reduces the risk of mechanical failures, enhancing reliability and longevity.
- Size reduction to 2 microns and below: Offers precise and fine grinding capabilities, ideal for achieving desired particle sizes.
- Interchangeable liners in Polyurethane, Stainless Steel, Nylon, PTFE available on select models: Allows for versatile usage with different materials and easy maintenance.
- Personalized design to solve the affairs on grinding and classification: Customizable design options cater to specific needs, optimizing performance for various applications.
- Automatic control system: Enhances operational convenience and efficiency by automating processes and maintaining consistent performance.
Principle
The high-energy planetary ball mill F-P2000 utilizes superimposed rotational movements, creating Coriolis forces between grinding jars and balls. This interaction releases dynamic energies, achieving fast and effective size reduction. Its unique geometric structure and movement mode ensure high-frequency collision, shearing, and friction for excellent grinding results.
Advantages
- Easy to disassemble and clean with quick coupling installed
- Small footprint for efficient space utilization
- No risk of contamination during the grinding process
- Improved dynamic efficiency, noise reduction, operation safety, comfort, and convenience
- Good crushing ability for samples with larger particle sizes and hardness
- Up to four ball mill tanks with a volume of 500ml or less
- Variable frequency control interface for multiple functions
- 304 stainless steel planetary disk with higher balance and safety
- Fast processing speed with small, uniform, and consistent sample particle size
- Low noise with self-lubricating polymer gears and press-in grease noise reduction system
- Double fans at the rear for better heat dissipation
- Completely separated grinding chamber and control room for heat and dust isolation
- Edge-free 304 stainless steel planetary position for safety and balanced operation
- Low power consumption and low failure rate for long-term experiments
- Strong impact energy with finer particle size and faster processing speed
- Frequency conversion control for precise grinding parameters adjustment
- Liquid nitrogen cooling system option for low-temperature protection grinding
Parameters
Product name | High energy planetary ball mill |
Model | F-P2000 |
Processing principle | impact force friction |
Application sample characteristics | fine | medium to low hardness | brittle | dry or low viscosity |
Processing type | crush|grind|mix |
Maximum injection size | 10mm |
Sample particle size range | 0.1-20um |
Maximum processing volume | 2000ml |
Maximum speed of ball mill tank | 800r/min |
Transmission mode | European standard |
Space movement mode | X-axis planetary motion |
Function | Continuous and intermittent operation | Emergency stop | Timing | Power outage memory | Overload and hazardous operation protection |
Additional features | LED Lighting|Heat Dissipation |
Ball mill tank material | Tungsten carbide zirconia | agate | stainless steel | MC nylon and other optional |
Number of ball mill tanks | 4个 |
Ball mill tank volume | 500ml |
Grinding ball material | Tungsten carbide | zirconia | agate | stainless steel, etc. optional |
Grinding method | Dry grinding|Wet grinding |
Electrical Description | 100-120V/200-240VAC,50-60Hz,750W |
Power port | National Standard | European Standard | American Standard | British Standard, etc. |
Net weight | 92kg |
Dimensions (length, width and height) | 570*570*420mm |
Protection level | IP650 |
Standard | CE |
Additional configurations available | Ultra-low temperature liquid nitrogen cooling touch operating system |
Accessory parameters
Main accessories | Recommended standard configuration volume: 500ml | √: means it can be configured | ×: indicates that it cannot be matched | ||
Ball mill tank | Material: | Type | 100ml | 250ml | 500ml |
Tungsten carbide | Classic | √ | √ | √ | |
Vacuum type | √ | √ | × | ||
Zirconia | Classic | √ | √ | √ | |
Vacuum type | √ | √ | × | ||
Agate | Classic | √ | √ | √ | |
Vacuum type | √ | √ | × | ||
MC nylon | Classic | √ | √ | √ | |
Vacuum type | √ | √ | |||
Stainless steel | Classic | √ | √ | √ | |
Vacuum type | √ | √ | √ | ||
Polyurethane | Classic | √ | √ | √ | |
Vacuum type | √ | √ | × | ||
PTFE | Classic | √ | √ | √ | |
Vacuum type | √ | √ | × | ||
Corundum | Classic | √ | √ | √ | |
Vacuum type | √ | √ | × | ||
Grinding ball | Diameter(mm) | Material | |||
3/5/10/15/20 | Tungsten carbide | Zirconia | Agate | Stainless steel | Corundum |
FAQ
What Is A Planetary Ball Mill?
What Is A Laboratory Ball Mill?
What Are The Main Applications Of Planetary Ball Mills?
What Are The Applications Of A Laboratory Ball Mill?
What Is Milling Equipment Used For?
What Are The Key Features Of Planetary Ball Mills?
What Are The Main Types Of Laboratory Ball Mills?
What Are The Different Types Of Milling Equipment?
What Are The Advantages Of Using A Planetary Ball Mill?
What Is The Working Principle Of A Laboratory Ball Mill?
What Materials Can Be Processed Using Milling Equipment?
What Types Of Planetary Ball Mills Are Available?
What Are The Advantages Of Using A Laboratory Ball Mill?
How Does Milling Equipment Work?
How Does The Automatic Reversal Mechanism In Planetary Ball Mills Work?
What Materials Can Be Processed Using A Laboratory Ball Mill?
What Are The Advantages Of Using Milling Equipment?
What Makes Planetary Ball Mills Suitable For Small Particle Samples?
What Are The Key Features Of A High-energy Planetary Ball Mill?
What Factors Should Be Considered When Selecting Milling Equipment?
What Is The Difference Between A Planetary Ball Mill And A Vibratory Ball Mill?
4.8
out of
5
Efficient processing, minimal contamination risk, and compact design. Highly recommend!
4.7
out of
5
Superb grinding ability with precise size reduction. Excellent for research purposes.
4.9
out of
5
Versatile, easy to clean, and low noise. Perfect for diverse lab applications.
4.8
out of
5
Impressive speed and uniformity in particle size. Great value for money.
4.7
out of
5
Safe operation, efficient heat dissipation, and customizable options. Top-notch!
4.9
out of
5
Convenient controls, rapid processing, and low power consumption. Fantastic!
4.8
out of
5
Robust build, precise grinding parameters, and excellent customer support.
4.7
out of
5
Outstanding efficiency in size reduction, ideal for various materials. Impressed!
4.9
out of
5
Reliable and versatile, with a wide range of grinding options. Highly satisfied!
4.8
out of
5
Effortless operation, precise results, and durable construction. Worth every penny!
4.7
out of
5
Exceptional performance, easy maintenance, and consistent particle size. Impressive!
4.9
out of
5
Sleek design, efficient cooling system, and precise grinding control. Love it!
4.8
out of
5
Great for sample preparation, reliable operation, and compact footprint. Highly recommended!
4.7
out of
5
Excellent versatility, minimal noise, and efficient space utilization. Very pleased!
4.9
out of
5
User-friendly interface, rapid processing speed, and precise control. Excellent product!
Products
High Energy Planetary Ball Mill Milling Machine for Laboratory
REQUEST A QUOTE
Our professional team will reply to you within one business day. Please feel free to contact us!
Related Products
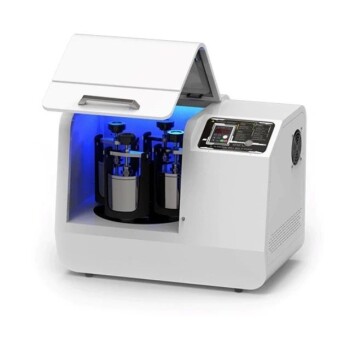
High Energy Planetary Ball Mill Milling Machine for Laboratory
The biggest feature is that the high energy planetary ball mill can not only perform fast and effective grinding, but also has good crushing ability
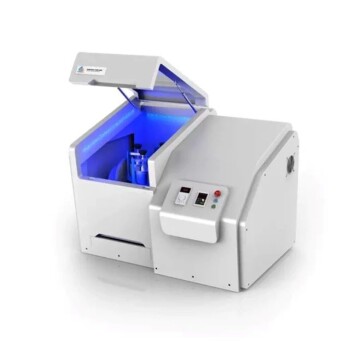
High-Energy Omnidirectional Planetary Ball Mill Machine for Laboratory
The KT-P2000E is a new product derived from the vertical high-energy planetary ball mill with a 360°rotation function. The product not only has the characteristics of the vertical high-energy ball mill, but also has a unique 360°rotation function for the planetary body.
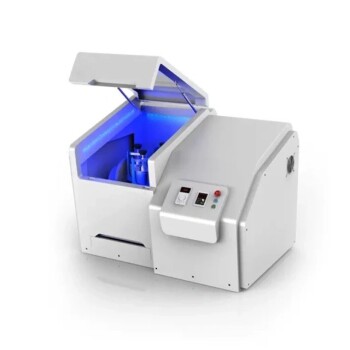
High-Energy Omnidirectional Planetary Ball Mill Milling Machine for Laboratory
The KT-P4000E is a new product derived from the vertical high-energy planetary ball mill with a 360° swivel function. Experience faster, uniform, and smaller sample output results with 4 ≤1000ml ball mill jars.
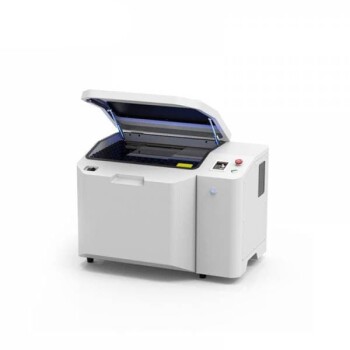
Laboratory Planetary Ball Mill Rotating Ball Milling Machine
KT-P400E is a desktop multi-directional planetary ball mill with unique grinding and mixing capabilities. It offers continuous and intermittent operation, timing, and overload protection, making it ideal for various applications.
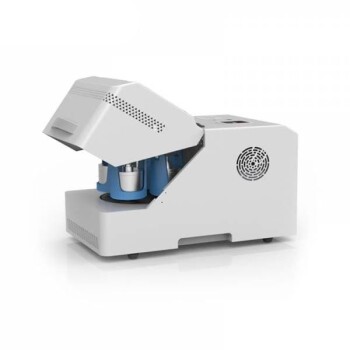
Mini Planetary Ball Mill Machine for Laboratory Milling
Discover the KT-P400 desktop planetary ball mill, ideal for grinding and mixing small samples in the lab. Enjoy stable performance, long service life, and practicality. Functions include timing and overload protection.
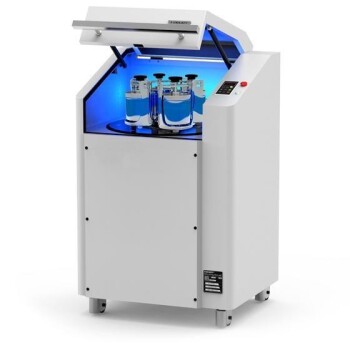
Laboratory Planetary Ball Mill Cabinet Planetary Ball Milling Machine
The vertical cabinet structure combined with ergonomic design enables users to obtain the best comfortable experience in standing operation. The maximum processing capacity is 2000ml, and the speed is 1200 revolutions per minute.
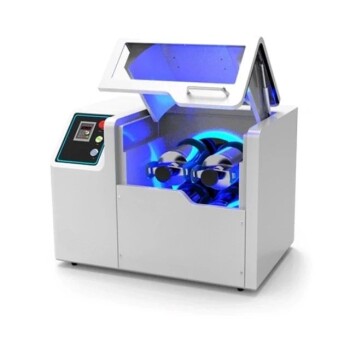
High Energy Planetary Ball Mill for Laboratory Horizontal Tank Type Milling Machine
KT-P4000H uses the unique Y-axis planetary motion trajectory, and utilizes the collision, friction and gravity between the sample and the grinding ball to have a certain anti-sinking ability, which can obtain better grinding or mixing effects and further improve the sample output.
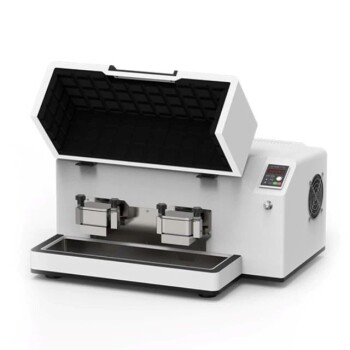
High Energy Vibratory Ball Mill for Lab Use
The high-energy vibrating ball mill is a high-energy oscillating and impacting multifunctional laboratory ball mill. The table-top type is easy to operate, small in size, comfortable and safe.
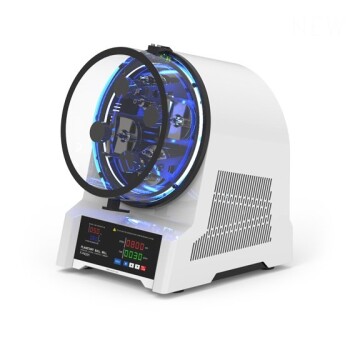
Laboratory Horizontal Planetary Ball Mill Milling Machine
Improve sample uniformity with our Horizontal Planetary Ball Mills. KT-P400H reduces sample deposition and KT-P400E has multi-directional capabilities. Safe, convenient and efficient with overload protection.
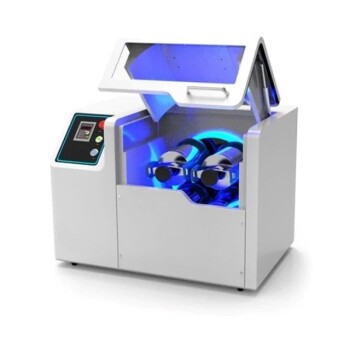
High Energy Planetary Ball Mill Machine for Laboratory Horizontal Tank Type
The KT-P2000H uses a unique Y-axis planetary trajectory, and utilizes the collision, friction and gravity between the sample and the grinding ball.
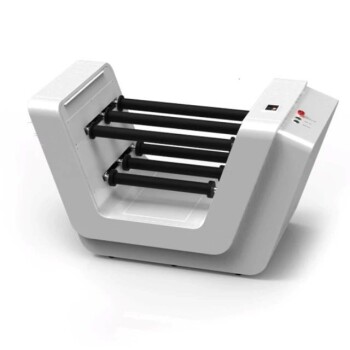
Laboratory Ten-Body Horizontal Jar Mill for Lab Use
The Ten-body horizontal jar mill is for 10 ball mill pots (3000ml or less). It has frequency conversion control, rubber roller movement, and PE protective cover.
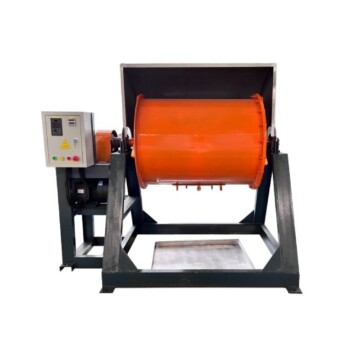
Stainless Steel Laboratory Ball Mill for Dry Powder and Liquid with Ceramic Polyurethane Lining
Discover the versatile stainless steel dry powder/liquid horizontal ball mill with ceramic/polyurethane lining. Ideal for ceramic, chemical, metallurgical, and building materials industries. High grinding efficiency and uniform particle size.
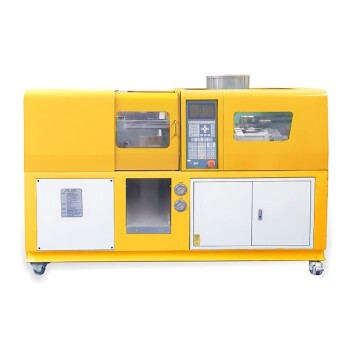
Small Injection Molding Machine for Lab Use
The small injection molding machinehas fast and stable movements; good controllability and repeatability, super energy saving; the product can be automatically dropped and formed; the machine body is low, convenient for feeding, easy to maintain, and no height restrictions on the installation site.
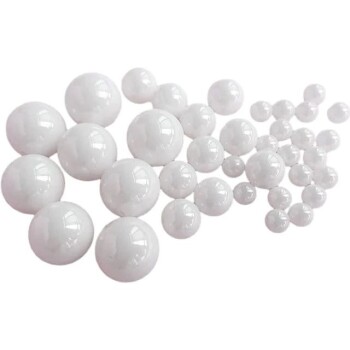
Precision Machined Zirconia Ceramic Ball for Engineering Advanced Fine Ceramics
zirconia ceramic ball have the characteristics of high strength, high hardness, PPM wear level, high fracture toughness, good wear resistance, and high specific gravity.
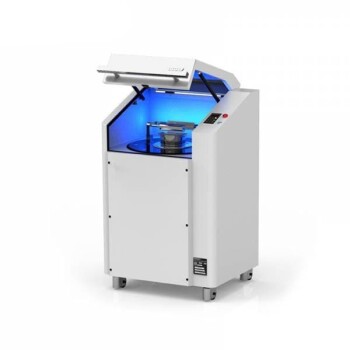
Vibration Mill for Efficient Sample Preparation, Suitable for Crushing and Grinding a Variety of Materials with Analytical Precision. Supports Dry / Wet / Cryogenic Grinding and Vacuum/Inert Gas Protection.
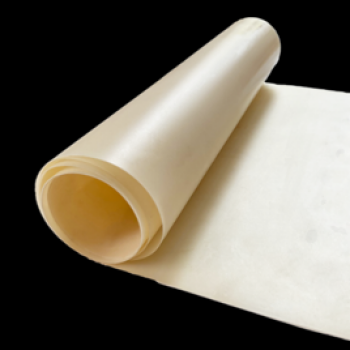
Anion Exchange Membrane for Laboratory Use
Anion exchange membranes (AEMs) are semipermeable membranes, usually made of ionomers, designed to conduct anions but reject gases such as oxygen or hydrogen.
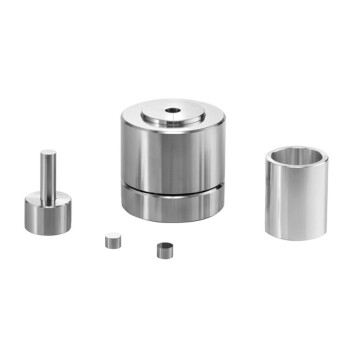
Assemble Lab Cylindrical Press Mold
Get reliable and precise molding with Assemble Lab Cylindrical Press Mold. Perfect for ultra-fine powder or delicate samples, widely used in material research and development.
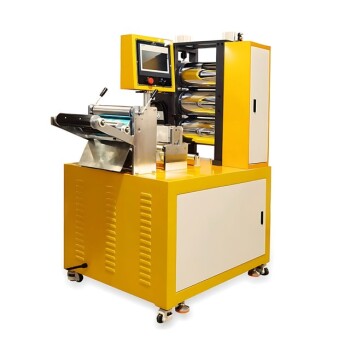
Small Lab Rubber Calendering Machine
Small lab rubber calendering machine is used for producing thin, continuous sheets of plastic or rubber materials. It is commonly employed in laboratories, small-scale production facilities, and prototyping environments to create films, coatings, and laminates with precise thickness and surface finish.
Related Articles
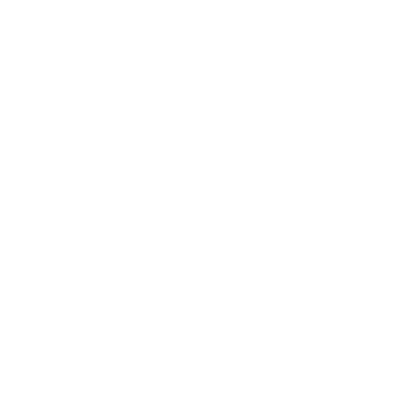
Exploring Spark Plasma Sintering Furnace (SPS): Technology, Applications, and Advantages
Dive into the comprehensive guide on Spark Plasma Sintering Furnace (SPS), covering its technology, applications in materials science, and significant advantages over traditional sintering methods.
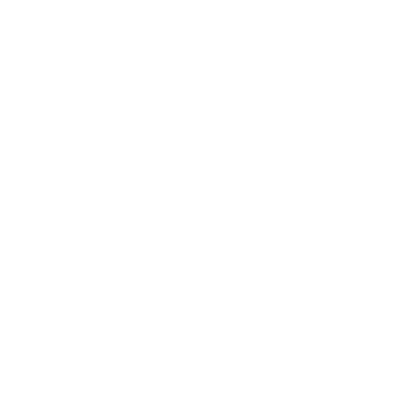
Development and Principles of Frozen Tissue Crushers
Explore the history, classification, and principles of frozen tissue crushers, including grinding ball selection and how to choose the right crusher.
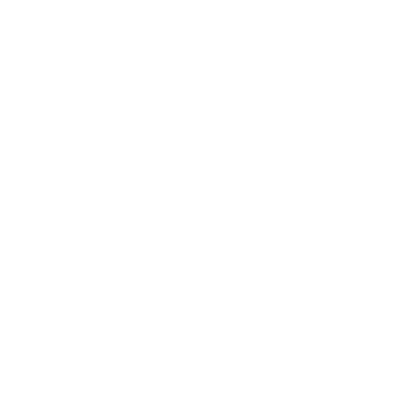
Cryogenic Pulverization Technology and Its Applications
Explores the process, advantages, disadvantages, and applications of cryogenic pulverization in various fields.
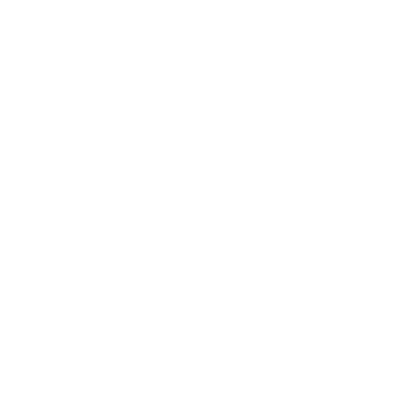
Application of Ultra-Micro Pulverization Technology in the Food Industry
Explores the benefits and applications of ultra-micro pulverization technology in enhancing food processing and nutrient absorption.
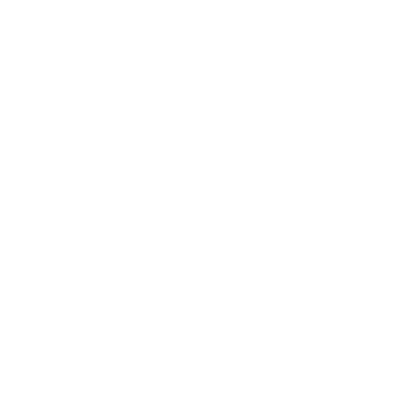
Hydraulic Hot Press: Principles, Components, Features, Advantages, and Applications
An in-depth look at the hydraulic hot press, its components, features, advantages, and applications.
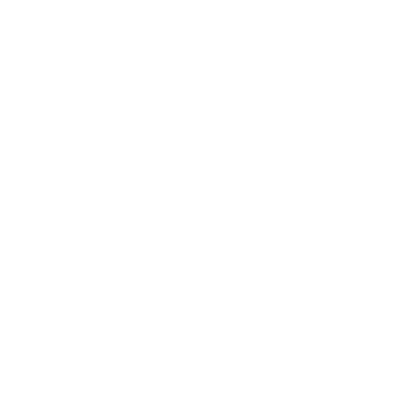
Exploring the Applications of Isostatic Pressing
Isostatic pressing is a powder metallurgy technique that applies equal pressure from all directions to a compacted powder. There are two types of isostatic pressing: cold isostatic pressing (CIP) and hot isostatic pressing (HIP). CIP uses pressure at room temperature, while HIP applies heat and pressure to the powder.