Principles and Components
Hydraulic System
The hydraulic system is the backbone of the hydraulic hot press, delivering the necessary pressure and control force to ensure precise and efficient operation. This system comprises several key components, each playing a vital role in maintaining the machine's functionality.
-
Hydraulic Pump: The heart of the hydraulic system, the pump generates the fluid pressure required to power the entire system. It converts mechanical energy into hydraulic energy, ensuring a steady flow of pressurized fluid.
-
Hydraulic Cylinder: Acting as the actuator, the hydraulic cylinder converts the fluid pressure from the pump into mechanical force. This force is then used to move the press's components, such as the upper and lower platens, with precision.
-
Hydraulic Pipeline: The pipelines are the veins of the system, transporting the pressurized fluid from the pump to the cylinders and other components. They must be robust and leak-proof to maintain the system's integrity.
-
Hydraulic Valve: The valves in the system control the direction, pressure, and flow rate of the hydraulic fluid. They ensure that the fluid is distributed correctly to the various parts of the system, enabling smooth and controlled movements.
Together, these components form a cohesive unit that provides the hydraulic hot press with the strength and precision needed for various industrial applications.
Heating System
The heating system in a hydraulic hot press is a critical component responsible for maintaining the required heating temperature. This system is composed of several key elements, each playing a vital role in ensuring efficient and precise thermal control.
-
Electric Heater: The electric heater is the primary source of heat, converting electrical energy into thermal energy. It is strategically placed to ensure uniform heat distribution across the heating plate.
-
Heating Plate: The heating plate is a crucial interface that transfers the generated heat to the material being processed. It is typically made from high-quality, thermally conductive materials to ensure rapid and even heat transfer.
-
Heating Pipeline: The heating pipeline facilitates the circulation of heat transfer media, such as oil or water, to maintain a consistent temperature throughout the system. This network of pipes ensures that the heat is evenly distributed, preventing hotspots and ensuring optimal processing conditions.
The integration of these components allows the heating system to provide the necessary thermal environment for various processes, from bonding electronic components to shaping metal products. The precise control of temperature is essential for achieving high-quality outcomes in the manufacturing of diverse products.
Pressure Control System
The pressure control system in a hydraulic hot press is a critical subsystem designed to maintain and adjust the pressure levels within the machine. This system ensures that the pressure applied during the pressing process is consistent and precise, which is essential for achieving high-quality end products.
Key components of the pressure control system include:
- Pressure Sensor: Monitors the current pressure in real-time, providing feedback to the control system.
- Pressure Regulating Valve: Adjusts the pressure to the desired level, ensuring that the pressure remains within the specified range.
- Pressure Gauge: Displays the current pressure for operator visibility and control.
Component | Function |
---|---|
Pressure Sensor | Monitors and transmits pressure data to the control system. |
Pressure Regulating Valve | Adjusts and maintains the pressure at the desired level. |
Pressure Gauge | Provides a visual display of the current pressure for operator control. |
The interaction between these components allows for dynamic pressure control, enabling the hydraulic hot press to adapt to varying material properties and pressing requirements. This flexibility is crucial for the machine's versatility and effectiveness in different applications.
Temperature Control System
The temperature control system in a hydraulic hot press is a critical subsystem designed to maintain precise heating conditions, ensuring optimal performance and product quality. This system is composed of several key components, each playing a vital role in the overall temperature regulation process.
-
Temperature Sensor: This component continuously monitors the temperature within the heating system, providing real-time data to the control unit. The sensor's accuracy is crucial, as it directly influences the precision of the temperature adjustments.
-
Temperature Regulator: Acting on the data from the temperature sensor, the regulator is responsible for adjusting the heating elements to maintain the desired temperature. This component ensures that any deviations from the set point are promptly corrected, thereby maintaining a stable heating environment.
-
Temperature Display: For operator convenience and process transparency, the temperature display provides a visual readout of the current temperature. This interface allows operators to monitor and adjust the heating process easily, ensuring that the system operates within the specified parameters.
The seamless integration of these components ensures that the hydraulic hot press can achieve and maintain the precise temperatures required for various applications, from electronic product bonding to metal product radiator shaping.
Product Features
Hydraulic Circuit
The hydraulic circuit of the hydraulic hot press is designed to deliver rapid and efficient operation, making it a cornerstone of the machine's performance. This system employs a sophisticated mother-child cylinder configuration that is engineered for both speed and stability. The hydraulic circuit operates at low oil temperatures, which not only extends the life of the hydraulic components but also ensures consistent performance over time.
One of the standout features of this hydraulic circuit is its rapid operational speed. The fast response time of the hydraulic system allows for quick cycle times, significantly enhancing productivity. This speed is achieved without compromising the stability of the operation, thanks to the robust design of the hydraulic components. The mother-child cylinder setup provides a balanced force distribution, which is crucial for maintaining precise control over the pressing process.
In addition to speed and stability, the hydraulic circuit is also designed with energy efficiency in mind. By minimizing oil temperature fluctuations, the system reduces energy consumption and operational costs. This efficiency is particularly important in industrial settings where continuous operation is the norm.
The hydraulic circuit's design also includes a range of safety and control features. For instance, the system is equipped with pressure sensors and regulating valves that ensure the hydraulic pressure remains within safe and optimal limits. This not only protects the machine from damage but also ensures the quality of the finished product by maintaining consistent pressure throughout the pressing cycle.
Overall, the hydraulic circuit of the hydraulic hot press is a testament to advanced engineering, offering a combination of speed, stability, and efficiency that is essential for high-performance industrial applications.
Structural Precision
The hydraulic hot press is distinguished by its four-column and three-plate structure, which is meticulously engineered for optimal performance and durability. This design incorporates a parallel movable plate and worktable, ensuring that the press operates smoothly and efficiently. The structural integrity is further enhanced by the use of precision linear self-lubricating guide sleeves, which reduce friction and wear, thereby extending the lifespan of the machine.
Key Structural Components:
- Four-Column Structure: Provides robust support and stability, crucial for maintaining alignment during high-pressure operations.
- Three-Plate Design: Includes a fixed lower plate, a movable upper plate, and a middle plate that facilitates precise movement and alignment.
- Parallel Movable Plate and Worktable: Ensures consistent pressure distribution across the work surface, minimizing the risk of deformation or misalignment.
- Precision Linear Self-Lubricating Guide Sleeves: These components are integral to the machine's longevity, offering smooth operation and reduced maintenance needs.
This combination of structural elements not only enhances the precision and reliability of the hydraulic hot press but also contributes to its overall efficiency and ease of operation.
Component Quality
The hydraulic hot press is engineered to deliver exceptional performance and durability, primarily through the integration of imported high-quality hydraulic and electrical components. These components are meticulously selected to ensure low noise operation, high performance, and an extended service life. The hydraulic system, which includes the hydraulic pump, hydraulic cylinder, hydraulic pipeline, and hydraulic valve, is designed to provide the necessary pressure and control force with minimal operational noise. Similarly, the electrical components, such as the electric heater and temperature regulator, are chosen for their reliability and precision in maintaining optimal operating conditions.
Component Type | Key Features |
---|---|
Hydraulic Components | - Low Noise: Operates quietly to minimize disturbance. |
- High Performance: Delivers consistent pressure and control. | |
- Long Service Life: Built to withstand prolonged use without degradation. | |
Electrical Components | - Precision Control: Ensures accurate temperature and pressure settings. |
- Reliability: Designed for consistent performance over time. |
This focus on component quality not only enhances the overall efficiency and reliability of the hydraulic hot press but also contributes to its adaptability across various industrial applications, from electronic product bonding to metal product radiators and membrane switch thermoforming.
Temperature Control
The temperature control system in a hydraulic hot press is designed to regulate and maintain precise heating temperatures, ensuring optimal performance and consistency in the manufacturing process. This system is particularly crucial for applications requiring high precision, such as the bonding of electronic components or the shaping of metal products.
Key Components:
- Temperature Sensor: Monitors the temperature in real-time, providing accurate data to the controller.
- Temperature Regulator: Uses the data from the sensor to adjust the heating elements, ensuring the desired temperature is maintained.
- Temperature Display: Provides a visual readout of the current temperature, allowing for immediate adjustments if necessary.
Operational Precision: The system controls the temperature of both the upper and lower heating plates independently, facilitated by an advanced intelligent temperature controller. This dual control mechanism allows for the precise maintenance of a temperature difference of ±1°C, ensuring uniform heating and preventing thermal inconsistencies that could affect the quality of the final product.
Benefits:
- Consistency: By maintaining a tight temperature range, the system ensures uniform heating, which is essential for processes like bonding and molding.
- Efficiency: The intelligent controller optimizes energy usage, reducing waste and operational costs.
- Adaptability: The system's precision makes it adaptable to various materials and processes, enhancing the flexibility of the hot press.
In summary, the temperature control system is a critical component of the hydraulic hot press, providing the precision and reliability needed for high-quality manufacturing across a range of industries.
Operational Flexibility
The hydraulic hot press is designed with a high degree of operational flexibility, enabling operators to fine-tune several critical parameters to meet specific pressing process requirements. These adjustments include:
-
Pressure Adjustment: The system allows for precise control over the applied pressure, ensuring that the material being pressed receives the optimal force for the desired outcome.
-
Stroke Control: Operators can modify the stroke length, which is the distance the press moves during the pressing cycle. This flexibility is crucial for accommodating materials of varying thicknesses and for achieving the correct pressing depth.
-
Closing Height: The press can be adjusted to achieve the perfect closing height, which is essential for maintaining consistent product quality and for ensuring that the heating plates make full contact with the material.
-
Holding Time: The holding time, or the duration for which the press maintains pressure on the material, can be precisely set. This is particularly important in processes that require a specific dwell time to achieve the desired bonding or molding effect.
This level of operational flexibility ensures that the hydraulic hot press can be tailored to a wide range of applications, from electronic component bonding to complex metal shaping, without the need for extensive reconfiguration.
Safety Features
The hydraulic hot press is equipped with a comprehensive safety system to ensure operator safety and machine reliability. The core of this system is a PLC control system that integrates multiple safety features. One of the primary safety mechanisms is the two-hand operation requirement, which mandates that both hands of the operator must be engaged on the control panel simultaneously to initiate the pressing process. This dual-hand operation significantly reduces the risk of accidental initiation and ensures that the operator is in a safe position.
In addition to the two-hand operation, the system includes an emergency stop button that can halt all operations instantly in case of an unforeseen event. This feature is crucial for preventing accidents and minimizing potential damage. The inching function allows for precise, controlled movements of the press, enabling operators to position materials accurately without the risk of sudden, uncontrolled movements.
Physical barriers such as sheet metal guardrails are strategically placed around the machine to create a protective enclosure, preventing unauthorized access and reducing the likelihood of contact with moving parts. Furthermore, infrared grating protection devices are employed to detect any intrusion into the hazardous area. These devices immediately trigger the machine to stop if an object or person breaks the infrared beam, providing an additional layer of safety.
These safety features collectively ensure that the hydraulic hot press operates in a manner that prioritizes the safety of both the operators and the integrity of the equipment.
Customization
The hydraulic hot press offers extensive customization options to meet diverse industrial needs. Users can tailor the opening height, stroke, and worktable size to fit specific production requirements. Beyond these standard adjustments, the press can be equipped with additional features such as a multi-station turntable, which enhances operational efficiency by allowing multiple parts to be processed simultaneously. The inclusion of a top cylinder ejection system ensures smooth and controlled part removal, reducing the risk of damage.
For more complex operations, options like material receiving devices and side cylinder slide telescopic systems are available. These features facilitate the seamless integration of material handling and positioning, optimizing the workflow. Furthermore, the press can be outfitted with a cooling system to expedite the cooling process, crucial for certain materials and applications. The pressure holding function and pressure relay provide precise control over the pressing force, ensuring consistent product quality.
Advanced features such as force measurement display and human-machine interface (HMI) elevate the press's capabilities. The force measurement display offers real-time data on the applied force, aiding in process optimization and quality control. The HMI, with its intuitive graphical interface, simplifies operator interaction, making the press more user-friendly and efficient. These customization options collectively enable the hydraulic hot press to adapt to a wide range of applications, from electronic product bonding to metal product shaping, ensuring optimal performance in each scenario.
Advantages
Efficiency and Reliability
The hydraulic hot press is engineered for both efficiency and reliability, primarily driven by its advanced hydraulic system. This system is not only capable of delivering rapid working speeds but also boasts a remarkably low maintenance cost. The hydraulic system's design ensures a stable operation, which is crucial for maintaining consistent productivity and minimizing downtime.
Key components of the hydraulic system, such as the hydraulic pump, cylinder, and valves, work in harmony to provide the necessary pressure and control force. This integrated approach ensures that the system operates smoothly and efficiently, reducing the frequency and cost of maintenance interventions. The use of high-quality hydraulic and electrical components further enhances the system's durability and performance, contributing to its overall reliability.
In addition to the hydraulic system, the press incorporates a sophisticated temperature control system that maintains precise temperature settings, ensuring optimal heating conditions for various materials. This dual-system approach—combining hydraulic efficiency with temperature precision—underscores the hydraulic hot press's capability to handle demanding industrial applications with ease and dependability.
Precision
The hydraulic hot press excels in precision, particularly in its ability to deliver high pressure and maintain precise temperature control. This dual capability is crucial for optimizing the heating process of materials such as metals and plastics. The pressure control system, which includes components like the pressure sensor, pressure regulating valve, and pressure gauge, ensures that the applied force is consistently accurate. Similarly, the temperature control system, featuring the temperature sensor, temperature regulator, and temperature display, maintains the heating temperature with a precision of ±1°C, ensuring uniform heating across the workpiece.
This level of precision is not just a technical advantage but a functional necessity, especially in industries where dimensional accuracy and material consistency are critical. For instance, in the production of electronic components, even minor deviations in pressure or temperature can lead to significant quality issues. The hydraulic hot press's ability to deliver and control these parameters with such precision makes it an indispensable tool in high-precision manufacturing processes.
Moreover, the precision of the hydraulic hot press extends beyond just pressure and temperature control. The structural design, which includes a four-column and three-plate structure with parallel movable plate and worktable, and precision linear self-lubricating guide sleeves, ensures that the press operates smoothly and consistently. This structural precision, combined with the high-quality components such as imported hydraulic and electrical parts, results in a machine that not only performs with high accuracy but also offers long-term reliability and durability.
In summary, the precision of the hydraulic hot press is a multifaceted attribute that encompasses pressure and temperature control, structural design, and the quality of its components. This precision is what enables the machine to excel in a wide range of applications, from electronic product manufacturing to metal and plastic processing, ensuring that each product meets the highest standards of quality and consistency.
Flexibility
The hydraulic hot press demonstrates remarkable flexibility, primarily through its ability to accommodate a wide range of molds and materials. This adaptability is crucial for manufacturers who need to produce diverse product shapes and sizes. The press can easily switch between different molds, allowing for the production of various components without significant downtime or the need for extensive reconfiguration.
Moreover, the press is designed to handle a variety of metal and plastic blanks, ensuring that it can meet the specific requirements of different manufacturing processes. This versatility is achieved through the integration of advanced pressure and temperature control systems, which can be fine-tuned to suit the unique demands of each material type.
Feature | Description |
---|---|
Mold Replacement | Easy and quick replacement of molds for different product shapes. |
Material Adaptability | Capability to process various metal and plastic blanks. |
Pressure Control | Precise regulation of pressure to suit different material properties. |
Temperature Control | Fine-tuning of heating temperature for optimal material response. |
This operational flexibility not only enhances production efficiency but also reduces costs associated with machine downtime and setup time. It allows manufacturers to respond swiftly to market demands and adapt their production lines to new product designs with minimal disruption.
Applications
Electronic Products
The hydraulic hot press excels in applications involving electronic products, where precision is paramount. This machine is adept at precise bonding of intricate electronic components, ensuring that each connection is secure and reliable. The hot pressing process, facilitated by the hydraulic system's controlled pressure and the heating system's precise temperature management, guarantees the integrity of the bond.
Moreover, the hydraulic hot press is instrumental in the hot pressing of composite materials used in electronic devices. These materials often require a delicate balance of pressure and temperature to achieve the desired properties. The machine's ability to maintain a temperature difference of ±1°C and regulate pressure with high accuracy makes it an ideal choice for such applications. This ensures that the composite materials are pressed to perfection, without compromising their structural integrity or performance.
In summary, the hydraulic hot press's capabilities in precise bonding and composite material hot pressing make it an indispensable tool in the manufacturing of high-quality electronic products.
Metal Product Radiators
In the realm of metal product radiators, the hydraulic hot press plays a pivotal role in the manufacturing process. Specifically, it is instrumental in shaping heat pipes and flattening copper tubes, which are critical components in the thermal management systems of various electronic devices. The hydraulic hot press ensures that these components are formed with precision, enhancing their thermal conductivity and overall efficiency.
The process begins with the precise application of pressure and heat, controlled by the hydraulic and heating systems respectively. The hydraulic system provides the necessary force, while the heating system ensures the optimal temperature is maintained for shaping. This dual control mechanism allows for the creation of heat pipes and copper tubes that are not only structurally sound but also highly efficient in transferring heat away from sensitive electronic components.
Moreover, the pressure control system fine-tunes the application of force, ensuring that the metal components are shaped without any deformation or loss of material integrity. The temperature control system, on the other hand, guarantees that the heating plates are maintained at the exact temperature required for the process, minimizing any temperature-related inconsistencies.
The result is a radiator that not only meets the stringent demands of modern electronics but also contributes to the overall performance and longevity of the devices they are integrated into. This application underscores the versatility and precision of hydraulic hot presses in the manufacturing sector, particularly in high-tech industries where thermal management is paramount.
Membrane Switches
The hydraulic hot press is particularly adept at thermoforming both concave and convex surfaces of various materials used in membrane switches, such as Polycarbonate (PC), Polyvinyl Chloride (PVC), and Polyethylene Terephthalate (PET). This application leverages the press's precise temperature and pressure control systems to ensure the integrity and functionality of the membrane switches.
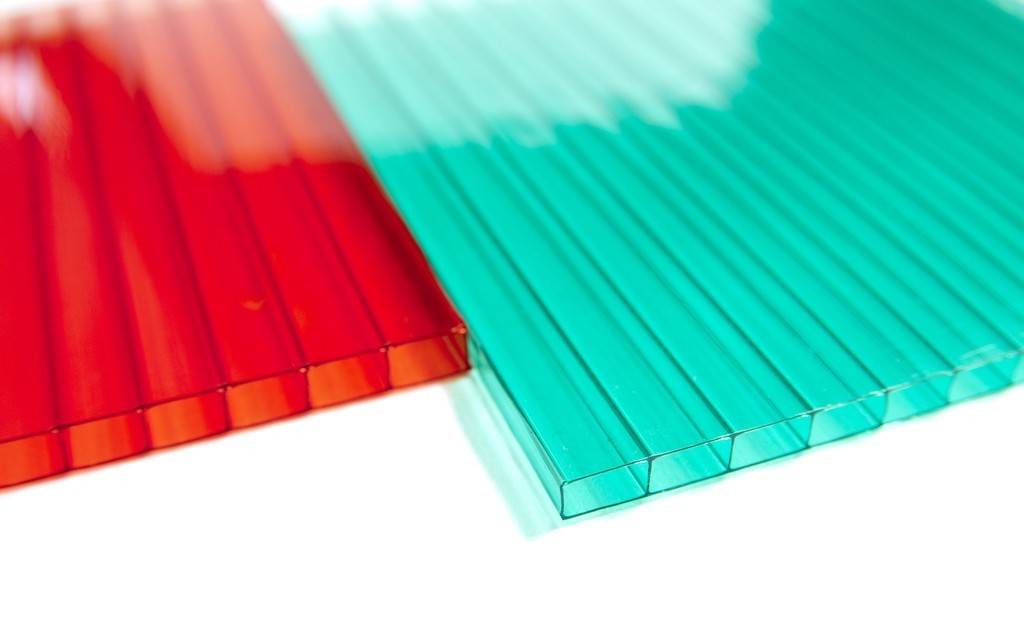
For instance, the heating system, which includes components like the electric heater and heating plate, ensures that the temperature is maintained within a tight range, typically with a temperature difference of ±1°C. This level of precision is crucial for the uniform heating of the membrane materials, preventing any distortion or damage during the thermoforming process.
Additionally, the pressure control system, featuring components such as the pressure sensor and pressure regulating valve, allows for fine-tuning of the pressure applied during thermoforming. This ensures that the membrane switches achieve the desired shape and consistency without compromising their structural integrity or operational reliability.
The hydraulic hot press's flexibility in adjusting parameters such as pressure, stroke, and holding time further enhances its suitability for manufacturing membrane switches. This adaptability ensures that the press can accommodate a wide range of membrane switch designs and specifications, making it a versatile tool in the production process.
EVA Molding
The hydraulic hot press is extensively utilized in the realm of EVA molding, where it excels in creating intricate concave and convex shapes. This process is pivotal for achieving the desired aesthetics and functionality in EVA products. Beyond mere shaping, the hot press facilitates logo font hot stamping and embossing, adding a layer of customization and brand identity to the final product.
For instance, in the production of EVA footwear, the hot press ensures that the soles are not only durable but also visually appealing, thanks to the precise molding and embossing capabilities. Similarly, in the manufacturing of EVA protective cases for electronics, the hot press enables the integration of company logos and intricate designs, enhancing both the product's marketability and its protective features.
The versatility of the hydraulic hot press in EVA molding is further highlighted by its ability to handle various thicknesses and complexities of EVA materials, making it an indispensable tool in industries ranging from footwear to electronics.
CONTACT US FOR A FREE CONSULTATION
KINTEK LAB SOLUTION's products and services have been recognized by customers around the world. Our staff will be happy to assist with any inquiry you might have. Contact us for a free consultation and talk to a product specialist to find the most suitable solution for your application needs!