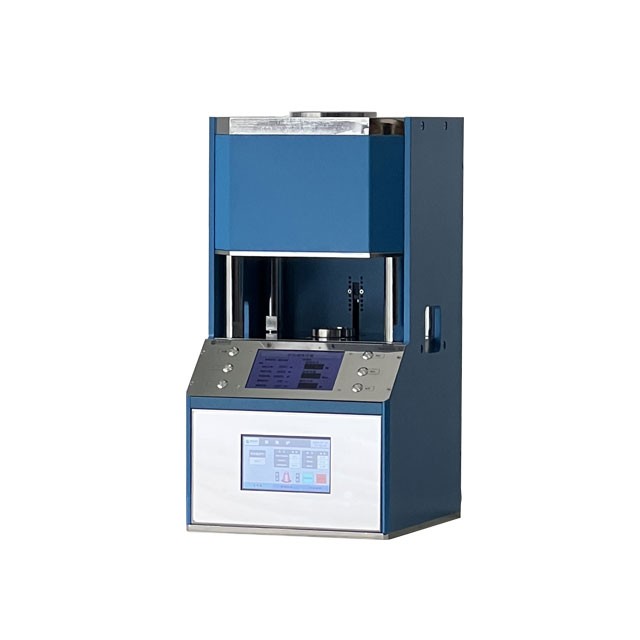
Customer-made Press
Automatic High Temperature Heated Hydraulic Press Machine with Heated Plates for Lab
Item Number : PHA
Price varies based on specs and customizations
- Pressure process
- Program pressurization-program pressure maintenance-timed pressure release
- Pressure holding time
- 1 second ~ ∞ seconds
- Cylinder stroke
- 80mm
- Heating temperature
- Maximum 1000℃
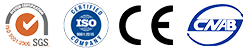
Shipping:
Contact us to get shipping details Enjoy On-time Dispatch Guarantee.
Why Choose Us
Reliable PartnerEasy ordering process, quality products, and dedicated support for your business success.
Introduction
The High Temperature Hot Press is a machine specifically designed for pressing, sintering and processing materials in a high temperature environment. It is capable of operating in the range of hundreds of degrees Celsius to thousands of degrees Celsius for a variety of high temperature process requirements.
Applications
High temperature hot presses are widely used in the following areas:
High-temperature alloy manufacturing: used to manufacture aero-engine components, spacecraft materials, etc.
Powder metallurgy: used for manufacturing precision parts and metal products with complex structure.
Ceramic materials: used for sintering and processing of high temperature ceramics.
Electronic materials: for manufacturing semiconductor materials and magnetic materials.
Detail&part
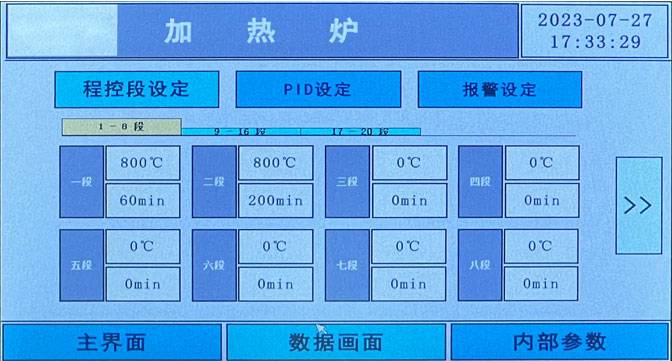
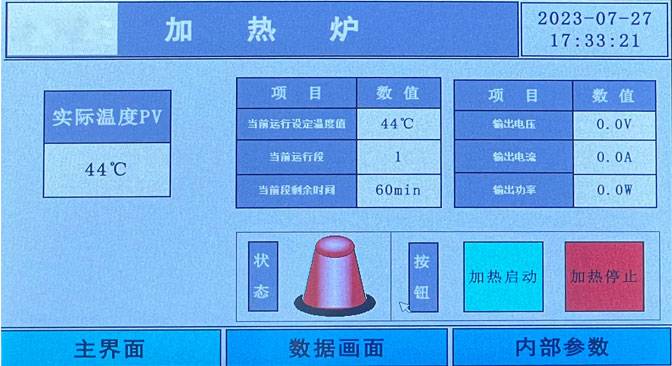
- Step 1: Select the data screen and enter the setting interface
- Step 2: Select "Programmable segment setting"
- Step 3: There are 20 temperature rise control programs in the program, select the first segment
- Step 4: According to the experimental requirements, set the temperature and heating speed of the first segment
- Step 5: If multiple temperature rise programs are required, you can set the 20 segments
- Step 6: After setting, press the main interface to return to the operation interface
- Step 7: On the main interface, press "Heating Start".
- Step 8: The equipment starts to heat up according to the program.
- Step 9: The equipment stops automatically after heating. If the setting is wrong, such as the set temperature is not reached within the specified time, the equipment will automatically terminate.
Principle
High-temperature hot presses utilize the physical and chemical effects of high-temperature and high-pressure environments to press, sinter, and process materials by applying high pressure and temperature to the materials, prompting the rearrangement or crystallization of the material molecules. Under high temperature conditions, the material atoms can cross the energy barriers more easily, which is conducive to chemical reactions, grain growth and material densification, and thus improve the mechanical properties and heat resistance of the materials, as well as the manufacture of complex structural materials.
Characteristics
High-temperature operating capability: Capable of stable operation at extremely high temperatures, up to thousands of degrees Celsius.
Precise control: Equipped with precise temperature control and pressure control systems to ensure accurate and repeatable processing.
Adaptation to diverse materials: capable of handling various types of materials, including metals, ceramics, composites, etc.
High performance: equipment design and process optimization allow for high productivity and the ability to produce high quality products in large quantities.
Advantages
Customized processing: Ability to tailor processes and production solutions to specific needs.
Innovative material development: supports the development and research of new materials and promotes the advancement of material science and engineering technology.
Enhancement of product performance: Improvement of mechanical properties, heat resistance and corrosion resistance of materials through high temperature hot pressing treatment.
Energy saving and environmental protection: optimize design and high-efficiency operation to reduce energy consumption and environmental impact.
Technical specifications
Instrument model | PHA |
---|---|
Pressure range | 0-10T |
Pressure process | Program pressurization-Program pressure maintenance-timed pressure release |
Pressure holding time | 1 second~∞ seconds |
Cylinder stroke | 80mm |
Heating temperature | Maximum 1000℃ |
Mold material | Nickel-based alloy (high temperature resistant material) |
Sample size | Medium 10-30mm |
Mold shape | Medium 50*90mm |
Furnace diameter | Medium 60mm |
Complete machine size | 400*380*780 (L*W*H) |
Power supply | 220V 50Hz |
Powder tablet press size diagram | ![]() |
Operation steps
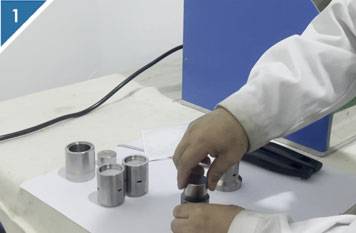
1. Place the sample in the mold.
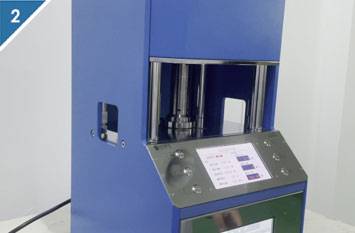
2. Place the mold in the hot press.
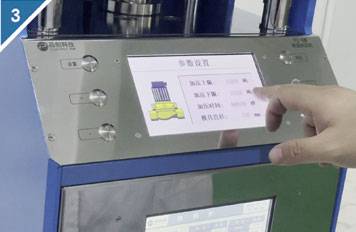
3. Set the required pressure and holding time.
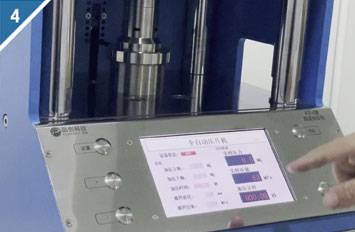
4. Pre-press the sample.
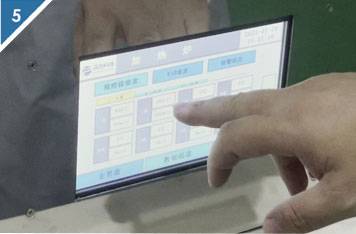
5. Enter the data screen, set the heating temperature and heating time, and you can set up to 20 heating programs.
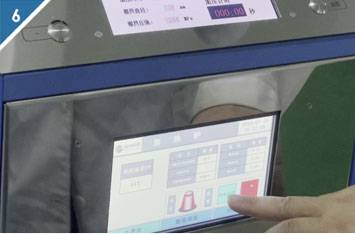
6. Return to the main interface, click Heating, and start heating.
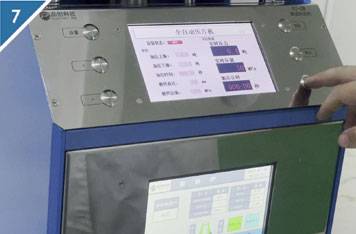
7. When the temperature reaches the set temperature, start pressurizing.
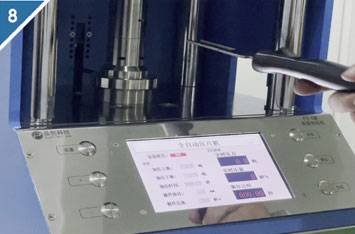
8. Take out the sample
FAQ
What Are Laboratory Hydraulic Machines?
What Are The Advantages Of Using Laboratory Hydraulic Machines?
What Are The Advantages Of Using A Hydraulically Heated Laboratory Press?
What Are The Applications Of Laboratory Hydraulic Machines?
What Does A Hydraulic Lab Heat Press Do?
What Are The Main Components Of A Laboratory Hydraulic Machine?
What Types Of Samples Or Materials Can Be Processed In A Hydraulically Heated Laboratory Press?
What Considerations Should Be Taken When Selecting A Laboratory Hydraulic Machine?
How Does A Hydraulically Heated Laboratory Press Work?
How Can The Performance Of A Hydraulically Heated Laboratory Press Be Optimized?
4.7
out of
5
Incredible precision and durability, a game-changer for our lab!
4.8
out of
5
Efficient and user-friendly, saves us so much time!
4.9
out of
5
Top-notch quality and performance, highly recommend!
4.7
out of
5
Fast delivery and excellent customer service!
4.8
out of
5
Value for money, this machine is a steal!
4.9
out of
5
Technologically advanced, perfect for our needs!
4.7
out of
5
Robust and reliable, handles high-volume tasks effortlessly!
4.8
out of
5
Ergonomic design makes operation a breeze!
4.9
out of
5
Impressive heat distribution, consistent results every time!
4.7
out of
5
Quick setup and easy to use, very satisfied!
4.8
out of
5
Highly durable, stands the test of time!
4.9
out of
5
Advanced features make it a leader in its class!
4.7
out of
5
Outstanding value, exceeded our expectations!
4.8
out of
5
Speedy delivery and excellent packaging!
4.9
out of
5
Superior quality, a must-have for any lab!
4.7
out of
5
Innovative design, simplifies our workflow!
4.8
out of
5
Reliable and efficient, a true asset to our team!
Products
Automatic High Temperature Heated Hydraulic Press Machine with Heated Plates for Lab
REQUEST A QUOTE
Our professional team will reply to you within one business day. Please feel free to contact us!
Related Products
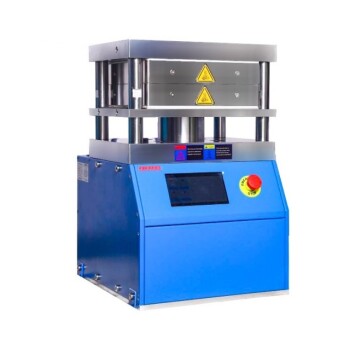
Automatic Heated Hydraulic Press Machine with Heated Plates for Laboratory Hot Press 25T 30T 50T
Efficiently prepare your samples with our Automatic Heated Lab Press. With a pressure range up to 50T and precise control, it's perfect for various industries.
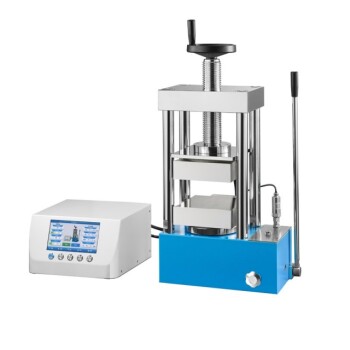
24T 30T 60T Heated Hydraulic Press Machine with Heated Plates for Laboratory Hot Press
Looking for a reliable Hydraulic Heated Lab Press? Our 24T / 40T model is perfect for material research labs, pharmacy, ceramics, and more. With a small footprint and the ability to work inside a vacuum glove box, it's the efficient and versatile solution for your sample preparation needs.
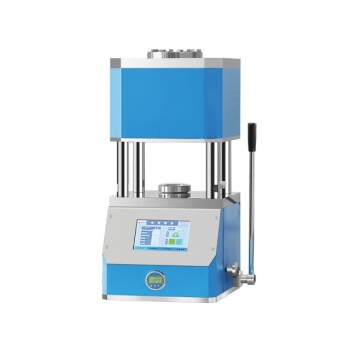
Manual High Temperature Heated Hydraulic Press Machine with Heated Plates for Lab
The High Temperature Hot Press is a machine specifically designed for pressing, sintering and processing materials in a high temperature environment. It is capable of operating in the range of hundreds of degrees Celsius to thousands of degrees Celsius for a variety of high temperature process requirements.
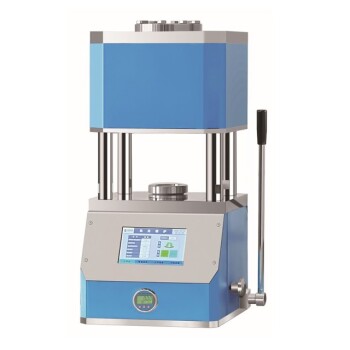
Manual Heated Hydraulic Press Machine with Heated Plates for Laboratory Hot Press
The Manual Heat Press is a versatile piece of equipment suitable for a variety of applications, operated by a manual hydraulic system that applies controlled pressure and heat to the material placed on the piston.
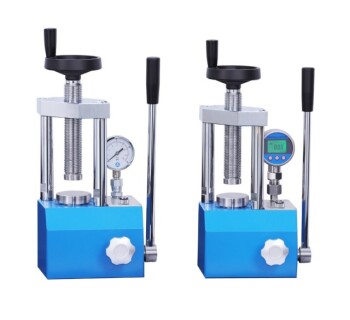
Laboratory Manual Hydraulic Pellet Press for Lab Use
Efficient sample preparation with small footprint Manual Lab Hydraulic Press. Ideal for material researching labs, pharmacy, catalytic reaction, and ceramics.
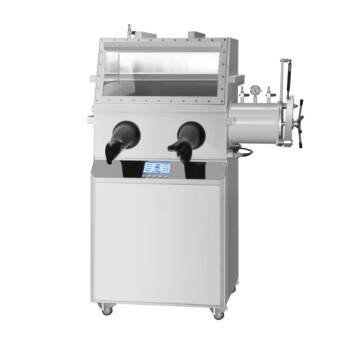
Laboratory Hydraulic Press Lab Pellet Press Machine for Glove Box
Controlled environment lab press machine for glove box. Specialized equipment for material pressing and shaping with high precision digital pressure gauge.
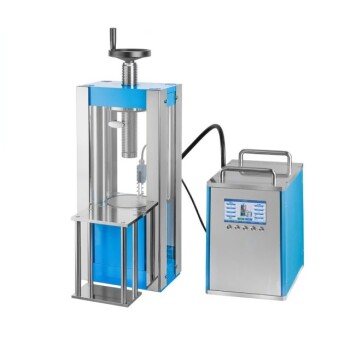
Laboratory Hydraulic Press Split Electric Lab Pellet Press
Efficiently prepare samples with a split electric lab press - available in various sizes and ideal for material research, pharmacy, and ceramics. Enjoy greater versatility and higher pressure with this portable and programmable option.
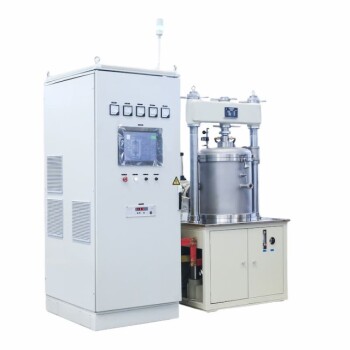
Vacuum Hot Press Furnace Machine Heated Vacuum Press
Discover the advantages of Vacuum Hot Press Furnace! Manufacture dense refractory metals & compounds, ceramics, and composites under high temp and pressure.
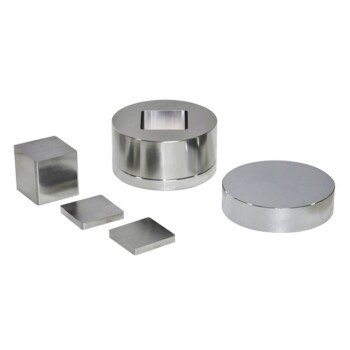
Square Lab Press Mold for Laboratory Applications
Create uniform samples easily with Square Lab Press Mold - available in various sizes. Ideal for battery, cement, ceramics, and more. Custom sizes available.
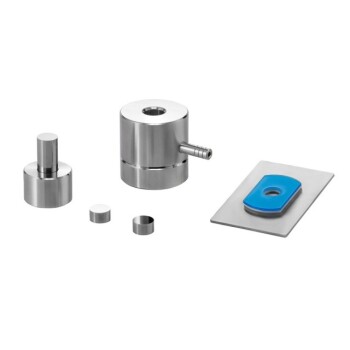
Easily release samples from our lab infrared press mold for accurate testing. Ideal for battery, cement, ceramics, and other sample preparation research. Customizable sizes available.
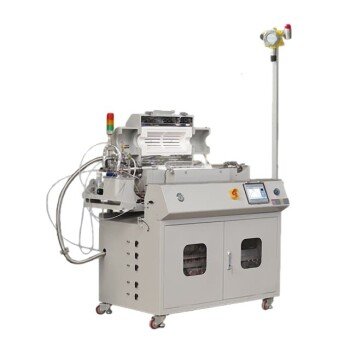
Customer Made Versatile CVD Tube Furnace Chemical Vapor Deposition Chamber System Equipment
Get your exclusive CVD furnace with KT-CTF16 Customer Made Versatile Furnace. Customizable sliding, rotating, and tilting functions for precise reactions. Order now!
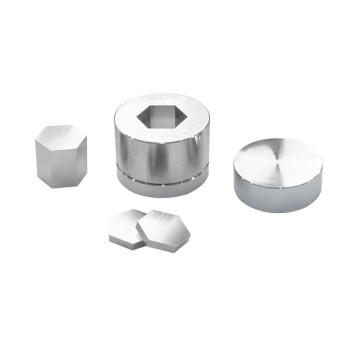
Discover precision polygon press molds for sintering. Ideal for pentagon-shaped parts, our molds ensure uniform pressure and stability. Perfect for repeatable, high-quality production.
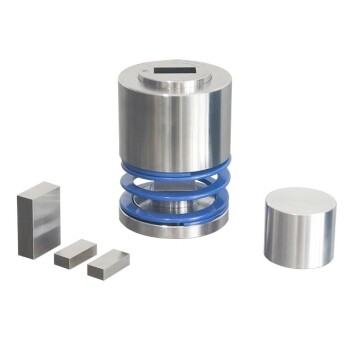
Square Bidirectional Pressure Mold for Lab Use
Discover precision in molding with our Square Bidirectional Pressure Mold. Ideal for creating diverse shapes and sizes, from squares to hexagons, under high pressure and uniform heating. Perfect for advanced material processing.
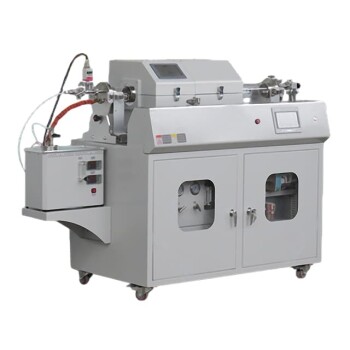
KT-PE12 Slide PECVD System: Wide power range, programmable temp control, fast heating/cooling with sliding system, MFC mass flow control & vacuum pump.
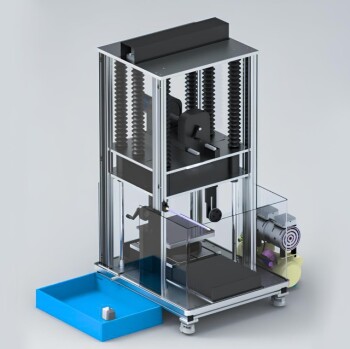
The high precision automatic diamond wire cutting machine is a versatile cutting tool that uses a diamond wire to cut through a wide range of materials, including conductive and non-conductive materials, ceramics, glass, rocks, gems, jade, meteorites, monocrystalline silicon, silicon carbide, polycrystalline silicon, refractory bricks, epoxy boards, and ferrite bodies. It is especially suitable for cutting various brittle crystals with high hardness, high value, and easy to break.
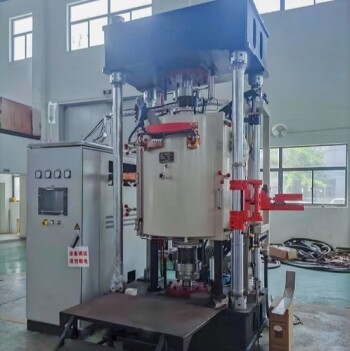
Vacuum Heat Treat and Pressure Sintering Furnace for High Temperature Applications
Vacuum pressure sintering furnaces are designed for high temperature hot pressing applications in metal and ceramic sintering. Its advanced features ensure precise temperature control, reliable pressure maintenance, and a robust design for seamless operation.
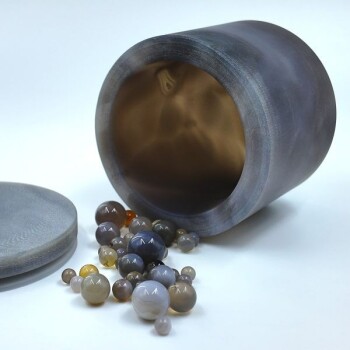
Laboratory Jar Mill with Agate Grinding Jar and Balls
Grind your materials with ease using Agate Grinding Jars with Balls. Sizes from 50ml to 3000ml, perfect for planetary and vibration mills.
Related Articles
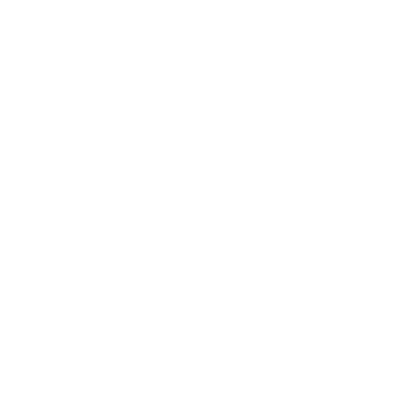
Comprehensive Guide to Spark Plasma Sintering Furnaces: Applications, Features, and Benefits
Explore the advanced features and applications of Spark Plasma Sintering Furnaces (SPS) in material science. Learn how SPS technology offers rapid, efficient, and versatile sintering for various materials.
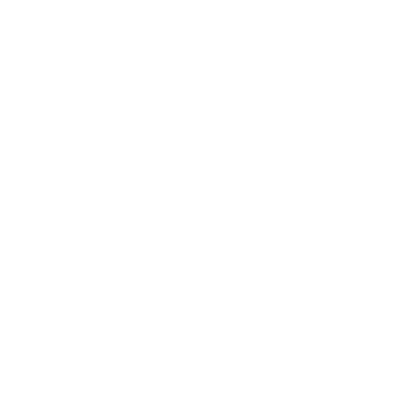
Understanding Hot Presses and Safety Considerations
An overview of hot presses, their applications, advantages, and safety precautions.
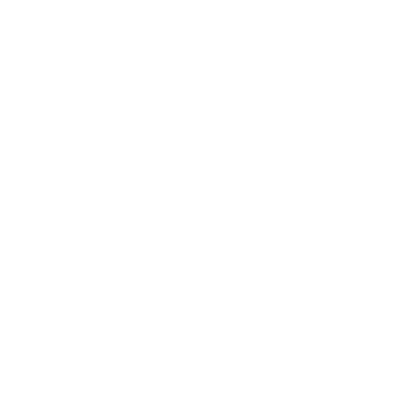
High Pressure Tube Furnace: Applications, Safety, and Maintenance
Explore the advanced applications, safety measures, and maintenance tips for high pressure tube furnaces. Learn how these furnaces are used in various high-temperature processes and ensure optimal performance and safety.
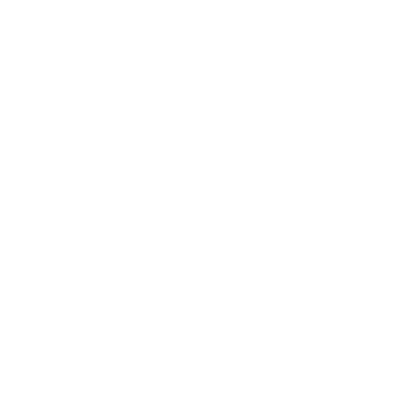
Principles and Applications of Vacuum Hot Press Sintering Equipment
Exploring the principles, classification, and applications of vacuum hot press sintering equipment in materials science.
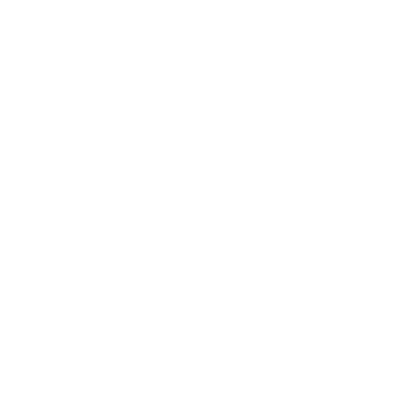
Advanced Ceramics Hot Press Sintering Technology and Equipment
Explores the hot press sintering process for advanced ceramics, its methods, advantages, equipment, and applications.
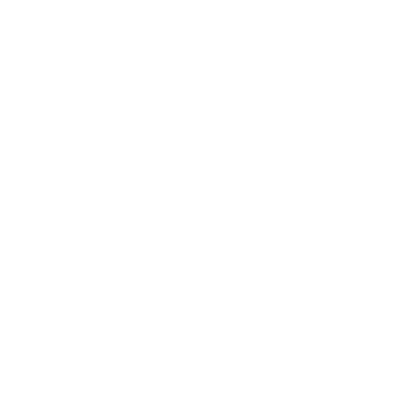
Optimizing Laboratory Analysis with Split Automatic Heated Lab Pellet Press
Explore the advanced features and benefits of split automatic heated lab pellet presses for precise pellet preparation in various analytical applications. Ideal for high-throughput laboratories.
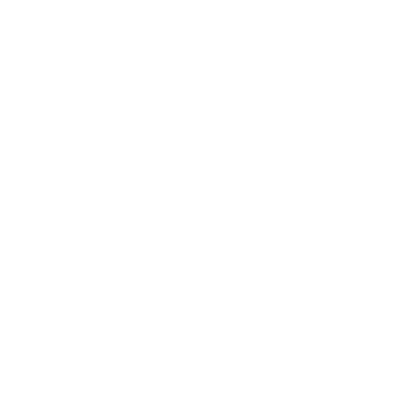
Hydraulic Hot Press: Principles, Components, Features, Advantages, and Applications
An in-depth look at the hydraulic hot press, its components, features, advantages, and applications.
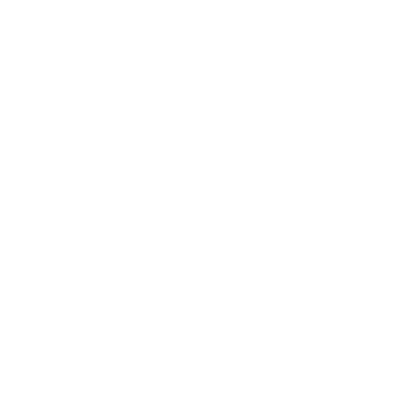
Guidelines for Safe Operation and Procedures of Flat-Plate Hot Press in Lamination Experiments
Detailed safety and operational guidelines for using a flat-plate hot press in lamination experiments, including pre-operation checks, material preparation, heating procedures, and post-processing.
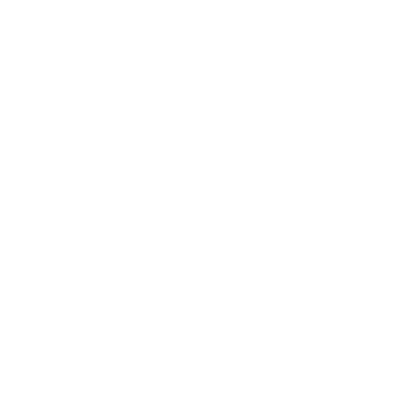
Safety and Operational Guidelines for Flat-Plate Hot Press in Lamination Experiments
Detailed safety measures and operational steps for using a flat-plate hot press in lamination experiments.
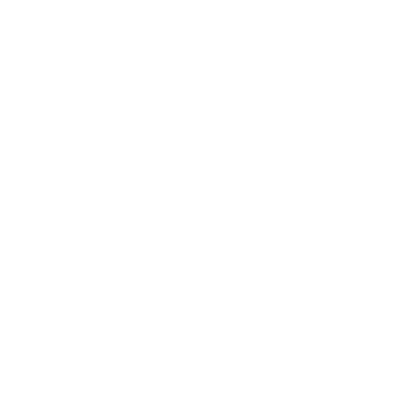
Operation of Vacuum Hot Press Sintering Furnace
An overview of the operation and components of a vacuum hot press sintering furnace, focusing on its application in the preparation of high-temperature wear-resistant ceramics.
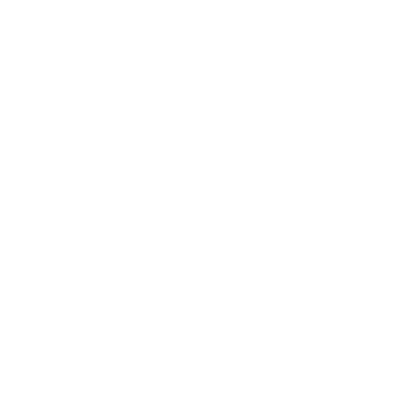
Comprehensive Overview of Commonly Used Heat Treatment Equipment
This article discusses various heat treatment equipment, their classifications, structures, and applications.
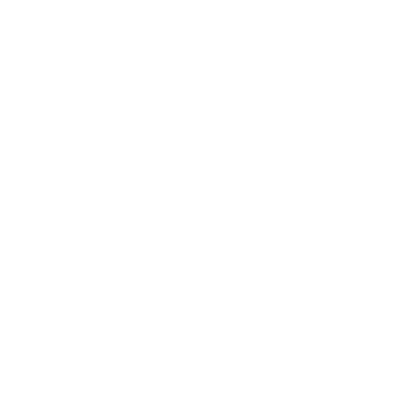
Chip Manufacturing: Comprehensive Guide to the Annealing Process
Detailed exploration of the annealing process in semiconductor fabrication, its types, key parameters, and applications.