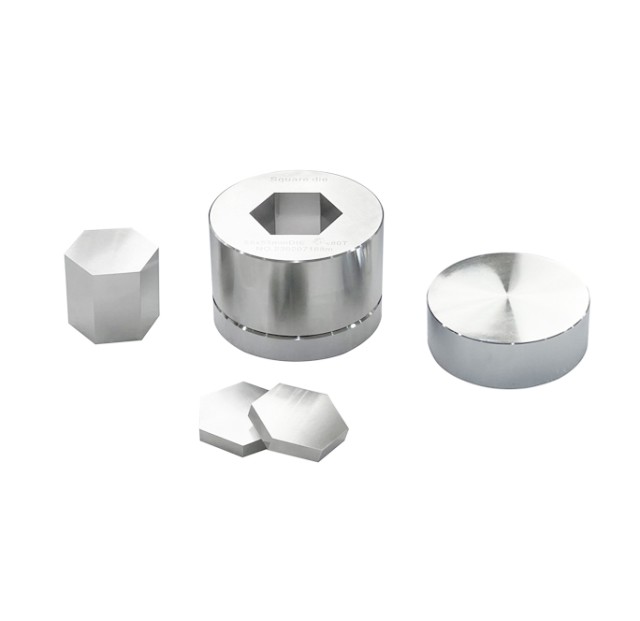
Molds & Accessories
Polygon Press Mold for Lab
Item Number : PMPD
Price varies based on specs and customizations
- Die heating
- Alloy tool steel :Cr12MoV
- Indenter hardness
- HRC60-HRC62
- Sample size
- 5*5、10*10、15*15、20*20 mm (M)
- Cavity depth
- 40mm (N)
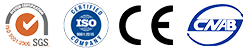
Shipping:
Contact us to get shipping details Enjoy On-time Dispatch Guarantee.
Why Choose Us
Reliable PartnerEasy ordering process, quality products, and dedicated support for your business success.
Introduction
The Polygon Press Mold is a versatile tool designed for compacting metal powders into various shapes using high pressure and optional electric heating. It accommodates molds of different geometries, including round, square, and hexagonal, to produce pellets with precise dimensions. This equipment is crucial in material testing and manufacturing processes, ensuring uniformity and stability in the final product.
Applications
The Polygon press mold is versatile and finds applications in various industries where precise shaping and compaction of materials are required. This equipment is particularly useful for creating samples for material testing, manufacturing components with specific dimensions, and producing items with long aspect ratios. Below are the main application areas:
- Material Testing: Used to create test substances for analyzing material performance during manufacturing.
- Industrial Component Manufacturing: Suitable for producing components with specific shapes and sizes, ensuring uniformity and stability.
- Spark Plug Production: Ideal for cold isostatic pressing of items like spark plugs, which require long aspect ratio pellets.
- Research and Development: Employed in R&D settings to experiment with different material compositions and shapes under controlled conditions.
- Quality Control: Helps in maintaining high standards of product quality by ensuring repeatable and precise compaction processes.
These applications highlight the Polygon press mold's capability to handle diverse materials and shapes, making it a valuable tool in both industrial and research environments.
Detail & Parts
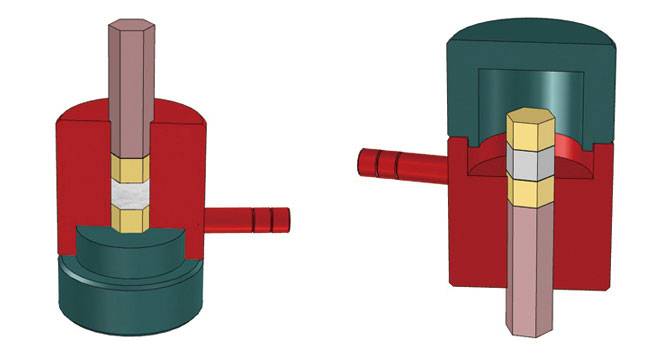
Technical specifications
Instrument model | PMPD |
---|---|
Sample shape | ![]() |
Die heating | Alloy tool steel :Cr12MoV |
Indenter hardness | HRC60-HRC62 |
Sample size | 5*5、10*10、15*15、20*20 mm (M) |
Cavity depth | 40mm (N) |
Dimensions | Φ53*120mm(L*H) |
Weight | 1.4Kg |
Diagram of hydraulic powder press size | ![]() |
Operation steps
Polygonal molds can be made into various special shapes, such as triangles, hexagons, and semicircle.
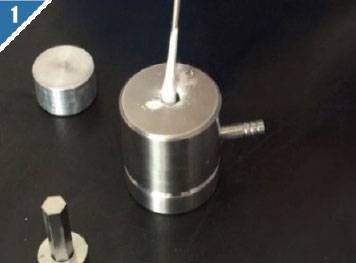
1.Assemble the die according to the operation diagram and install the sample in the cavity.

2.Put the die in the center of the hydraulic press and pressurize to required pressure.
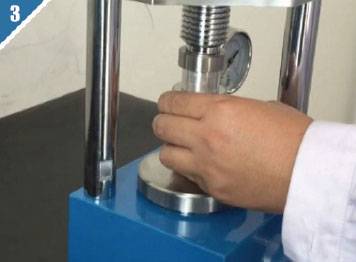
3.Assemble the die according to the release diagram , eject the sample out of the die bushing with the screw rod.
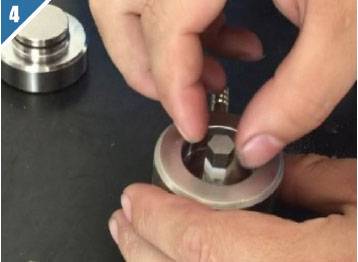
4.Take out the die from the hydraulic press , and remove the sample gently.
Features
The Polygon Press Mold is a versatile and efficient tool designed for various sintering and molding processes, offering several benefits that enhance productivity and reduce costs. This mold is particularly advantageous in industries requiring precise and repeatable shaping of materials, such as automotive parts, spark plugs, and other components. Here are the key features and their benefits:
-
Customizable Pressing Tonnages: The mold allows for adjustable pressing tonnages to fit the size of the parts, ensuring optimal pressure is applied. This customization helps in achieving the desired shape and density of the final product, reducing the need for multiple molds and increasing efficiency.
-
Dual Pressure Application: The pressure is applied from both above and below, providing more stability and uniformity to the compacted sample. This dual-directional pressure ensures consistent results and reduces the likelihood of defects in the final product.
-
Simplified Mold Design: The mold used in sintering processes is simpler and cheaper compared to those used in other manufacturing processes like M.I.M, plastic injection, and die casting. This simplicity reduces the initial investment and maintenance costs, making it more economical for small to medium-scale productions.
-
Repeatable Process: Once the initial trial and error adjustments are made, the process becomes highly repeatable. This repeatability is crucial for mass production, ensuring that each piece meets the exact specifications without requiring extensive manual intervention.
-
Versatility in Material Shaping: The Polygon Press Mold can handle a wide variety of materials, including metals, plastics, and rubber. This versatility makes it suitable for a range of applications, from automotive interior components to industrial spark plugs, enhancing its utility across different industries.
-
Reduced Material Waste and Labor Costs: The molding process using a hydraulic press is fast and efficient, reducing material waste and labor costs. This efficiency is particularly beneficial for large-scale productions, where minimizing waste and labor expenses are critical for profitability.
In summary, the Polygon Press Mold offers a combination of customization, simplicity, repeatability, and versatility, making it an ideal choice for various sintering and molding applications. Its ability to reduce costs and enhance productivity makes it a valuable asset in the manufacturing industry.
Principle
The polygon press mold operates by applying pressure from both above and below to compact materials into desired shapes. The mold consists of a die with a through cavity matching the outer shape of the part, such as pentagonal or hexagonal, and upper and lower punches connected to the press cylinders. This setup allows for precise shaping and uniformity, making it suitable for various industrial applications like spark plug production. The process involves adjusting the strokes of the punches to vary the height of the molded piece, ensuring dimensional accuracy and stability.
FAQ
What Is A Polygon Press Mold Used For?
How Does The Polygon Press Mold Work?
Can The Height Of The Molded Part Be Adjusted?
What Are The Design Considerations For A Polygon Press Mold?
What Materials Are Suitable For Polygon Press Molding?
What Is A Press Mold?
What Is Press Mould In Ceramics?
How Are Pellet Molds Used?
What Types Of Materials Can Be Pelletized Using Pellet Molds?
How Can One Select The Appropriate Pellet Mold For Their Specific Application?
4.7
out of
5
Exceptional quality and durability. Perfect for our lab's needs!
4.8
out of
5
Fast delivery and great value for money. Highly recommend!
4.9
out of
5
Technologically advanced and user-friendly. A game-changer in our research!
4.7
out of
5
Impressive build quality and consistent performance. Very satisfied!
4.8
out of
5
Efficient and reliable. Simplifies our material testing process significantly!
4.9
out of
5
Outstanding customer service and product support. A pleasure to work with!
4.7
out of
5
Versatile and adaptable. Handles all our mold needs effortlessly!
4.8
out of
5
Durable and long-lasting. A wise investment for our lab!
4.9
out of
5
Innovative design and excellent functionality. Highly impressed!
4.7
out of
5
Speedy delivery and top-notch quality. Couldn't ask for more!
4.8
out of
5
Reliable and efficient. A key component in our manufacturing process!
4.9
out of
5
Exceptional performance and durability. A must-have for any lab!
4.7
out of
5
Highly satisfied with the product's versatility and ease of use!
4.8
out of
5
Excellent value for money. Simplifies our research tasks significantly!
4.9
out of
5
Innovative and robust. A standout product in its category!
4.7
out of
5
Durable and efficient. A great addition to our lab equipment!
4.8
out of
5
Reliable and user-friendly. Highly recommend for any research lab!
4.9
out of
5
Outstanding quality and performance. A top-tier product!
4.7
out of
5
Efficient and cost-effective. A great investment for our lab!
4.8
out of
5
Highly versatile and durable. Simplifies our material testing process!
REQUEST A QUOTE
Our professional team will reply to you within one business day. Please feel free to contact us!
Related Products

Special Shape Press Mold for Lab
Discover high-pressure special shape press molds for diverse applications, from ceramics to automotive parts. Ideal for precise, efficient molding of various shapes and sizes.
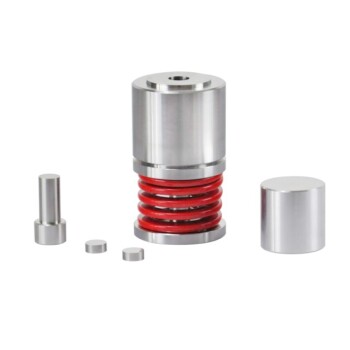
Round Bidirectional Press Mold for Lab
The round bidirectional press mold is a specialized tool used in high-pressure molding processes, particularly for creating intricate shapes from metal powders.
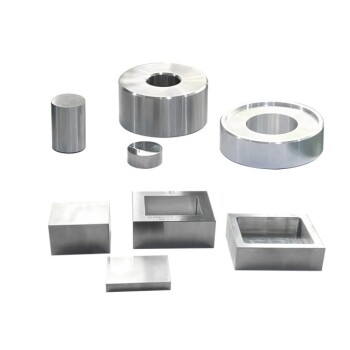
Special Heat Press Mold for Lab Use
Square, round and flat plate forming dies for hot presses.
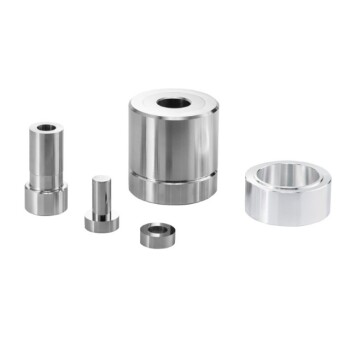
Ring Press Mold for Lab Applications
Ring Press Dies, also known as Circular Pellet Press Die Sets, are integral components in various industrial and laboratory processes.
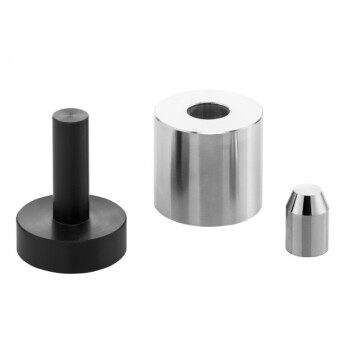
Button Battery Tablet Press Sealing Mold for Lab Use
The sealing die is essential for assembling button batteries, ensuring components like the anode, cathode, and electrolyte are securely enclosed.
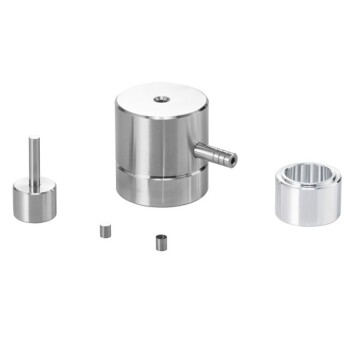
Cylindrical Press Mold for Lab Applications
Efficiently form and test most samples with Cylindrical Press Molds in a range of sizes. Made of Japanese high-speed steel, with long service life and customizable sizes.
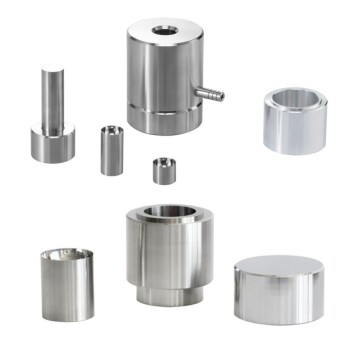
Explore versatile Hydraulic Hot Press molds for precise compression molding. Ideal for creating various shapes and sizes with uniform stability.
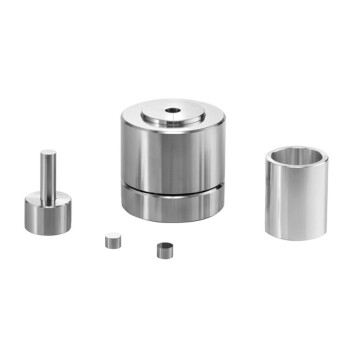
Assemble Lab Cylindrical Press Mold
Get reliable and precise molding with Assemble Lab Cylindrical Press Mold. Perfect for ultra-fine powder or delicate samples, widely used in material research and development.
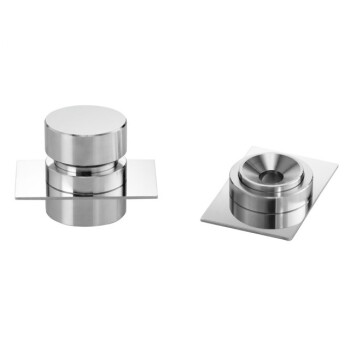
No Demolding Lab Infrared Press Mold for Laboratory Applications
Effortlessly test your samples with no demolding required using our lab infrared press mold. Enjoy high transmittance and customizable sizes for your convenience.
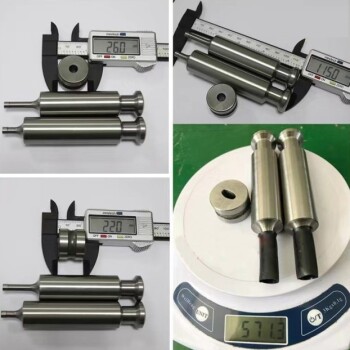
Multi-Punch Rotary Tablet Press Mold Ring for Rotating Oval and Square Molds
The multi-punch rotary tablet press mold stands as a pivotal component in pharmaceutical and manufacturing industries, revolutionizing the process of tablet production. This intricate mold system comprises multiple punches and dies arranged in a circular fashion, facilitating rapid and efficient tablet formation.
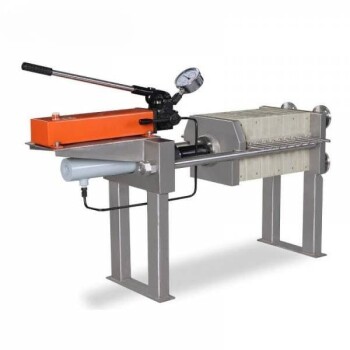
Hydraulic Diaphragm Lab Filter Press for Laboratory Filtration
Hydraulic diaphragm lab press filter is one type lab scale filter press, it takes small footprint, and higher pressing power.
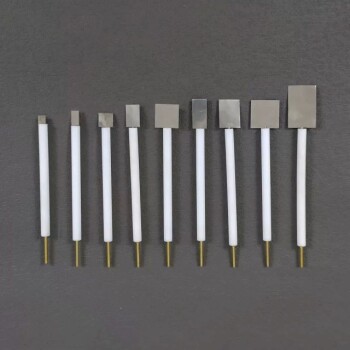
Platinum Sheet Electrode for Laboratory and Industrial Applications
Elevate your experiments with our Platinum Sheet Electrode. Crafted with quality materials, our safe and durable models can be tailored to fit your needs.
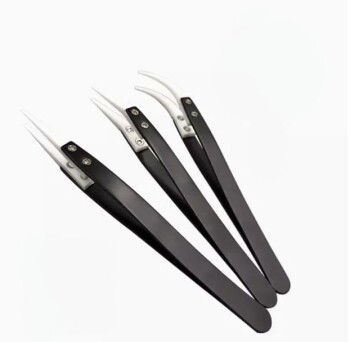
Engineering Advanced Fine Ceramics Head Tweezers with Pointed Elbow Zirconia Ceramic Tip
Zirconia ceramic tweezers are a high-precision tool made of advanced ceramic materials, especially suitable for operating environments that require high precision and corrosion resistance. This type of tweezers not only has excellent physical properties, but is also popular in the medical and laboratory fields because of its biocompatibility.
Related Articles
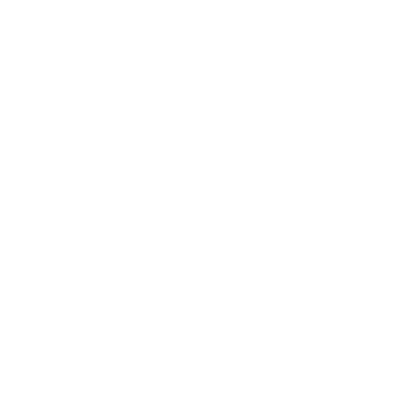
Ceramic Isostatic Pressing Mold Technology
Exploring the design and factors affecting ceramic isostatic pressing molds.
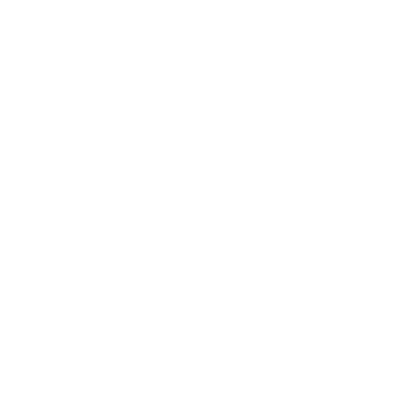
Comprehensive Guide to Metal Mold Pressing: Techniques, Equipment, and Applications
Explore the detailed process of metal mold pressing, including equipment, techniques, and applications. Learn how hydraulic presses shape materials like metal and rubber efficiently.
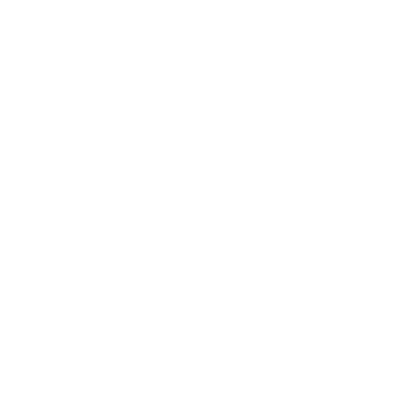
Comprehensive Guide to Isostatic Pressing Molds: Types, Processes, and Applications
Explore the detailed world of isostatic pressing molds, including types like wet bag and dry bag, their processes, and applications. Learn how these molds ensure uniform density and high-strength products.
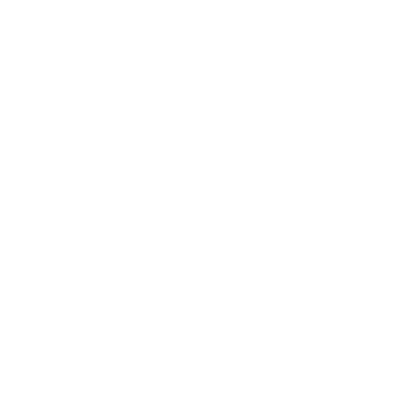
Manual Pellet Press: A Comprehensive Guide to Efficient Lab Pelletizing
Explore the intricacies of manual pellet presses, including operation, safety, and maintenance tips. Learn how to choose the right press, understand force gauges, and optimize pellet quality for your lab experiments.
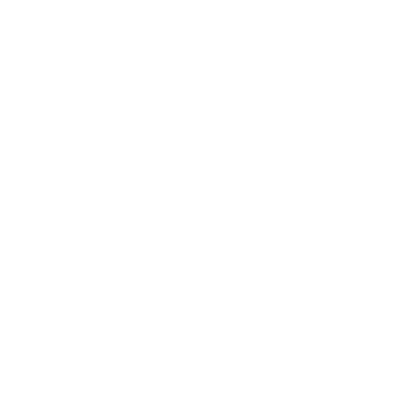
Exploring Spark Plasma Sintering Furnace (SPS): Technology, Applications, and Advantages
Dive into the comprehensive guide on Spark Plasma Sintering Furnace (SPS), covering its technology, applications in materials science, and significant advantages over traditional sintering methods.
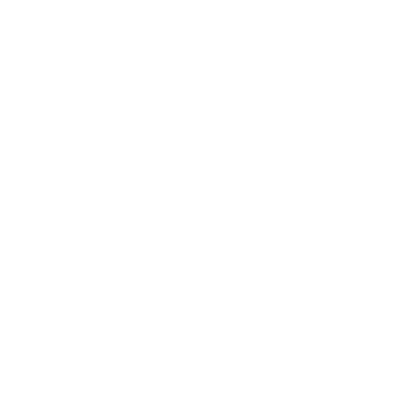
Infrared Press Mold Techniques for Non-Demolding Applications
Explore advanced infrared press mold techniques without demolding. Learn about the benefits, applications, and best practices for non-demolding lab processes.
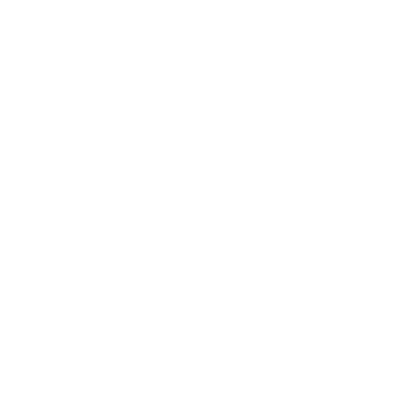
Infrared Heating Quantitative Flat Plate Mold: Design, Applications, and Benefits
Explore the advanced design and applications of infrared heating quantitative flat plate molds. Learn about their benefits in achieving uniform heat distribution and efficient processing.
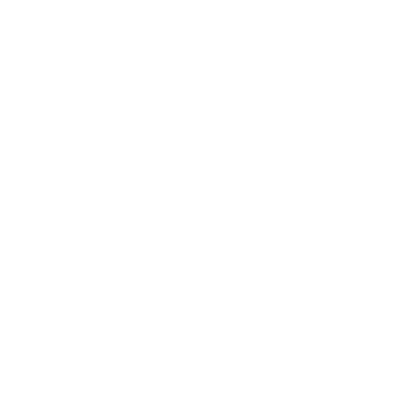
Exploring the Advanced Capabilities of Spark Plasma Sintering (SPS) Furnaces
Dive into the world of Spark Plasma Sintering (SPS) furnaces, their innovative technology, and applications in material science. Learn how SPS furnaces revolutionize the sintering process with high-speed, efficiency, and precision.
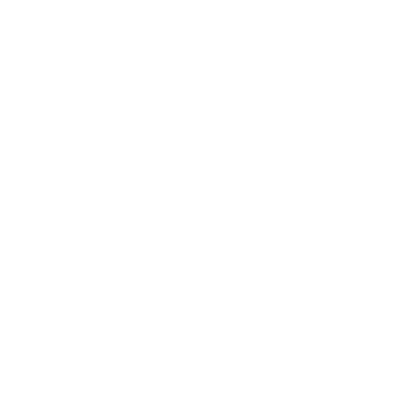
Comprehensive Guide to Cylindrical Lab Electric Heating Press Mold: Technology and Applications
Explore the advanced features and applications of cylindrical lab electric heating press molds. Learn about their working principles, types of heating technologies, and key benefits for precise sample preparation.
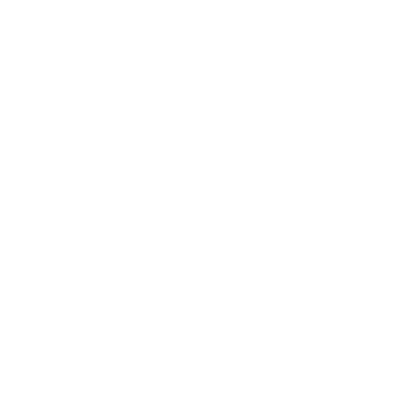
Nine Precision Molding Processes of Zirconia Ceramics
An overview of nine advanced molding processes for zirconia ceramics, including dry and wet methods.
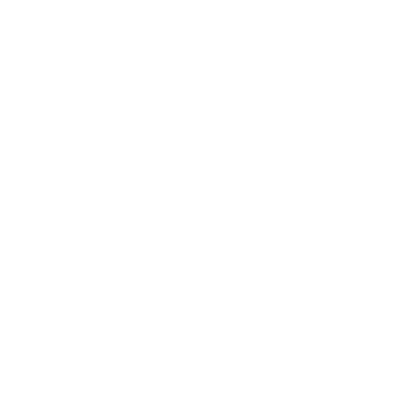
Advanced Ceramics Hot Press Sintering Technology and Equipment
Explores the hot press sintering process for advanced ceramics, its methods, advantages, equipment, and applications.
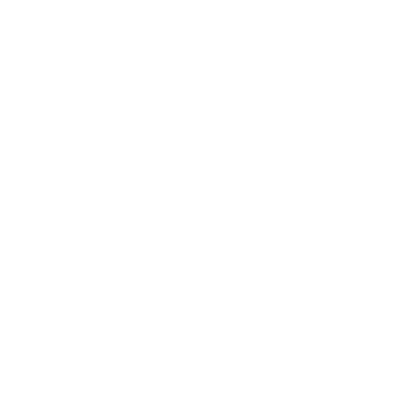
The Art and Craft of Making Porcelain Teeth
A detailed guide on the intricate process of creating porcelain teeth.